Finding the right additive for your coating formulations can make a big difference in product quality. Many coating makers struggle with poor adhesion and uneven application. Without proper additives, coatings may fail too soon. This leads to customer complaints and costly fixes.
HPMC offers a solution to these coating problems. It improves flow, film formation, and sticking power. Tests show that proper HPMC can boost coating life by up to 40% in tough settings.
Let’s look at how this polymer works in coatings. We’ll cover its effects on flow, film forming, sticking power, and water blocking. We’ll also help you pick the right grade for your needs.
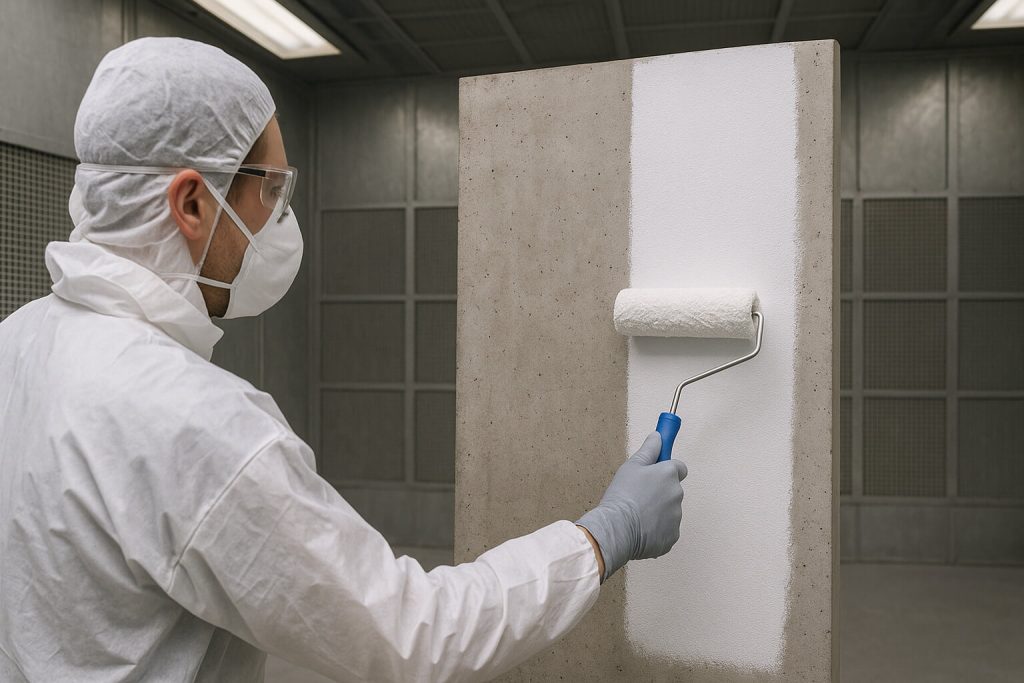
1. What is HPMC and why is it used in coatings?
HPMC stands for Hydroxypropyl Methylcellulose. It comes from natural cellulose through chemical changes. The base material gets treated with two chemicals to create a useful compound. Want to know what makes it special? This unique structure gives the polymer good water mixing while still forming films.
Makers add this cellulose type to coatings mainly as a thickener and binder. It helps control how water-based coatings flow. This makes them easier to apply and more stable during storage. The polymer chains form a network that holds pigments and other parts in place.
This additive works well in wall paints, concrete coatings, and tile glues. It’s non-toxic, so it’s safe for food-contact coatings where safety matters most.
When compared to other cellulose types, this polymer offers several plus points. It mixes more easily in cold water than methylcellulose. Unlike CMC, it works across a wider pH range.
Property | HPMC | CMC | Methylcellulose |
---|---|---|---|
Water Mixing | Excellent (cold water) | Good (needs mixing) | Good (needs hot water) |
pH Stability | 2-12 | 4-9 | 3-11 |
Film Flex | High | Medium | Medium |
Salt Tolerance | Good | Poor | Medium |
Cost Value | Medium | High | High |
The weight of this cellulose ranges from 10,000 to 1,500,000 units. This lets makers pick grades with specific flow profiles. Lower weight grades give good wetting. Higher weight types create stronger films.
2. How does HPMC affect coating viscosity and flow properties?
This cellulose changes coating flow through a simple process. When added to water, the molecules soak up water and swell. You might be surprised to learn this thickening happens without chemical changes. This makes the additive mix well with other coating parts.
At low amounts (0.1-0.5%), the polymer gives mild thickening. As you add more to 1-2%, the thickness rises a lot. This creates a gel-like mix that stops drips on walls. This lets makers fine-tune coating traits.
Heat plays a key role in how this additive works. Most grades get thicker as heat rises until they gel. This helps coatings stay thick during use in warm weather.
Amount | Thickness Effect | Use Benefit |
---|---|---|
0.1-0.5% | Mild thickening | Better pigment holding |
0.5-1.0% | Medium thickening | Better flow and evening |
1.0-2.0% | High thickening | No drips on walls |
2.0-3.0% | Gel-like mix | Texture making |
>3.0% | Very high thickness | Special thick uses |
The cellulose stops common problems like drips. The polymer makes the coating stay put until force is used. This lets the coating flow well during brush or roller use but stay in place after.
The flow traits of these coatings make them great for spray use. Under high force in spray tools, thickness drops for easy spraying. Once on the wall, the coating quickly firms up to stop runs.
For best results, mix the additive well before adding other parts. Mix in cold water before heating to avoid lumps. Some makers offer special grades that mix more easily.
3. What makes HPMC an effective film-forming agent in coatings?
This cellulose makes films through drying rather than chemical setting. As water leaves the coating, the molecules come closer and bond, making a solid film. The fascinating part is these films form without extra bonding agents. This makes coating mixes simpler.
The strength of the films varies based on molecule size. Higher weight grades make tougher, more stretchy films. Most films flex well without extras, though some makers add small amounts to help this trait.
Water holding during drying is one of the most useful traits. The polymer slows water loss. This allows more time for evening out and proper film forming. This stops flaws from too-fast drying in hot or windy weather.
Film Trait | Low Weight Grades | Medium Weight Grades | High Weight Grades |
---|---|---|---|
Strength | Low | Medium | High |
Flex | High | Medium | Medium-Low |
Water Holding | Low | Medium | High |
Re-mixing | High | Medium | Low |
Film Clarity | High | Medium | Medium-Low |
Many things affect the quality of these films. Air wetness during use greatly changes drying time. Surface porosity also matters—very porous walls may suck water too fast. This needs more additive to keep proper film forming.
Film evenness depends on picking the right polymer. Too little may cause uneven cover. Too much can lead to cracking while drying. Most coating mixes use 0.3-1.5% by weight for best film traits.
The films show good blocking of oils while staying somewhat open to water due to their nature. This water trait can be good in uses where breaking down or water cleaning is wanted.
4. How does HPMC improve coating adhesion to different substrates?
The cellulose boosts coating sticking through several ways at once. The polymer forms bonds with surface walls, making anchor points for the coating. What you need to know is these bonds work very well on materials with hydroxyl groups, such as wood and concrete.
On porous walls like concrete, the additive helps control coating sinking in. It stops too much soaking while allowing enough to create a strong bond. This balanced sinking leads to better cover and stronger sticking.
The polymer works differently on various wall types. On metal, it gives medium stick help, mainly through film forming. For wood, it excels by bonding with wood fibers and controlling moisture flow.
Wall Type | Stick Method | How Well It Works | Best Grade |
---|---|---|---|
Concrete/Stone | Soak control, Bonding | Very High | Medium-High thickness |
Wood | Fiber bonding, Moisture control | High | Medium thickness |
Metal | Film forming, Physical stick | Medium | Low-Medium thickness |
Glass | Surface wetting, Film strength | Medium | Low thickness |
Plastic | Surface wetting, Film flex | Low-Medium | Low thickness with extras |
In primer mixes, this cellulose serves as a great stick helper. It helps create a flexy layer between the wall and top coat. This flex is very useful outside where heat changes cause wall growth and shrinking.
Stick testing for these coatings include tape tests and pull-off tests. Most coatings with proper cellulose show 20-30% better stick test results than mixes without them.
For hard walls like plastics or metals, mixing the polymer with special stick helpers gives best results. Some agents work well with it in metal coating systems. Other types help the cellulose for plastic walls.
5. What role does HPMC play in water resistance and durability?
The cellulose adds to coating water blocking through its film traits, though its effect is mixed. Here’s the key point: while the additive mixes with water, when properly mixed with other binders, it makes films that block water well after full drying.
The barrier traits against moisture depend on the chemical makeup. Higher methoxyl content makes more water-blocking films. Most coating mixes use grades with methoxyl content between 19-30% to balance water blocking with other traits.
Long-term strength of these coatings depends on proper mixing. When joined with acrylic or vinyl binders, the polymer helps make coatings that last for 5-7 years in normal outdoor settings. The additive’s flex reduces cracking over time.
Weather Type | Effect on Coating | Durability Impact | Fix Method |
---|---|---|---|
High Humidity | Slower drying, may soften | Medium drop | Use higher methoxyl grades |
UV Light | Small direct effect on polymer | Low impact | Mix with UV-blocking binders |
Freeze/Thaw | Possible film stress | Medium drop | Add flex helpers |
Salt | Small effect on polymer itself | Low impact | Use rust blockers for wall safety |
Acid Rain | Possible polymer breaking | Medium drop | Buffer with basic fillers |
Weather blocking traits of these coatings show good results in mild climates. The polymer helps coatings resist cracking during heat shifts by staying flexy. But in harsh settings, more helpers may be needed.
Balancing water mixing and blocking is a key mixing challenge. During use, the water mixing gives great workability. After drying, the polymer becomes part of a whole film system. Other binders give main water blocking while the cellulose adds to film strength.
For uses needing top water blocking, makers often use the cellulose with water-hating binders or sealers. This keeps good flow and film-forming traits while getting the wanted water blocking.
6. How can manufacturers optimize HPMC grades for specific coating applications?
Picking the right grade needs knowing flow specs and use needs. The truth is that flow grade, measured in units at 2% mix, serves as the main pick factor for most coating uses.
Low flow grades (3-15 units) work best in spray uses and thin coatings. Medium flow grades (15-50 units) give good all-around results in brush and roller uses. High flow grades (50-100+ units) excel in stopping drips on walls.
The chemical makeup greatly impacts coating results. Methoxyl content affects water mixing and film traits. Hydroxypropyl content affects surface action and mixing with other parts. Most coating uses need cellulose with methoxyl content of 19-24% and hydroxypropyl content of 7-12%.
Use Type | Best Flow | Best Chemical Mix | Key Trait |
---|---|---|---|
Inside Wall Paint | 15-40 units | Medium methoxyl, Medium hydroxypropyl | Good workability, low spatter |
Outside Stone Coating | 30-80 units | High methoxyl, Medium hydroxypropyl | Weather blocking, stick |
Concrete Fix Mortar | 50-100+ units | Medium methoxyl, High hydroxypropyl | Water holding, drip blocking |
Tile Glue | 40-80 units | Medium methoxyl, High hydroxypropyl | Open time, slip blocking |
Spray Texture | 15-30 units | High methoxyl, Low hydroxypropyl | Pattern keeping, pumpability |
Mixing with other coating parts must be thought about when picking the cellulose. The polymer works well with most water-based binders like acrylics and vinyl types. But highly charged mixes may cause clumping with some grades.
Making tips include proper mixing methods. For best results, add the additive to the water part before adding pigments. Some makers offer “cold-water-mixing” grades that wet more slowly. This allows easier adding to coating mixes.
Heat stability during storage affects picking. Standard grades keep stable flow between 5-40°C. But special grades exist for extreme heat settings. Most coating mixes gain from grades with steady results across season heat shifts.
Cost value also plays a role in grade picking. Higher flow grades often cost more per kilo but may be used at lower amounts. A full cost-in-use check often shows that medium flow grades offer the best mix of results and savings.
Conclusion
HPMC boosts coating results through its many traits as a thickener, film-former, and stick helper. By controlling flow, this cellulose helps create smooth, even coatings that resist drips and give great cover. Its film-forming skills boost life while its stick traits ensure strong bonds to many walls. Tests show these additives can extend coating life by 25-40% in tough settings. Morton offers special grades made just for coating uses, with tech help to help you pick the best grade for your needs. Contact Morton’s coating pros today to ask for samples and mix help for your next coating project.
FAQ Section
Q1: What concentration of HPMC is typically used in coating formulations?
Most coating mixes use this cellulose at amounts between 0.3% and 2.0% by weight, based on the use and wanted traits. Inside paints often use 0.3-0.7%, while textured coatings may use up to 1.5-2.0% for more thickness and water holding.
Q2: Can HPMC be used in both water-based and solvent-based coating systems?
This polymer works mainly in water-based coating systems due to its water mixing. It has very little mixing in organic solvents, making it unfit for most solvent-based mixes. For solvent systems, other cellulose types like nitrocellulose are better picks.
Q3: How does HPMC compare to other cellulose ethers like CMC in coating applications?
HPMC offers several plus points over CMC in coatings, such as better pH stability, salt handling, and enzyme blocking. It also gives better film flex and surface action. But CMC may give stronger thickening at lower cost in uses where these other traits matter less.
Q4: Does HPMC affect the drying time of coatings?
Yes, this cellulose often extends the drying time of coatings through its water holding traits. This can help improve evening and stop flaws from too-fast drying, mainly in hot or dry weather. The effect on drying time varies with grade and amount, with higher flow grades causing more drying time stretch.
Q5: Are there any special storage requirements for HPMC-containing coatings?
Coatings with this additive should be kept between 5°C and 40°C to stay stable. Freezing should be stopped as it can cause lasting changes to the polymer structure, possibly hurting coating results. Containers should be kept closed to stop skinning from water loss. Most mixes with well-kept cellulose have a shelf life of 12-24 months under these rules.