Coating makers face big problems with product stability and film quality. When coatings fail, you waste money on fixes. You also face upset clients. Bad coatings cause delays, higher costs, and harm to your brand. HPMC offers a fix by making coatings work better. It helps with water holding and film forming. Tests show that good HPMC can make coating life 40% longer. It also cuts down on flaws. This article looks at how HPMC helps coatings work better on many surfaces.
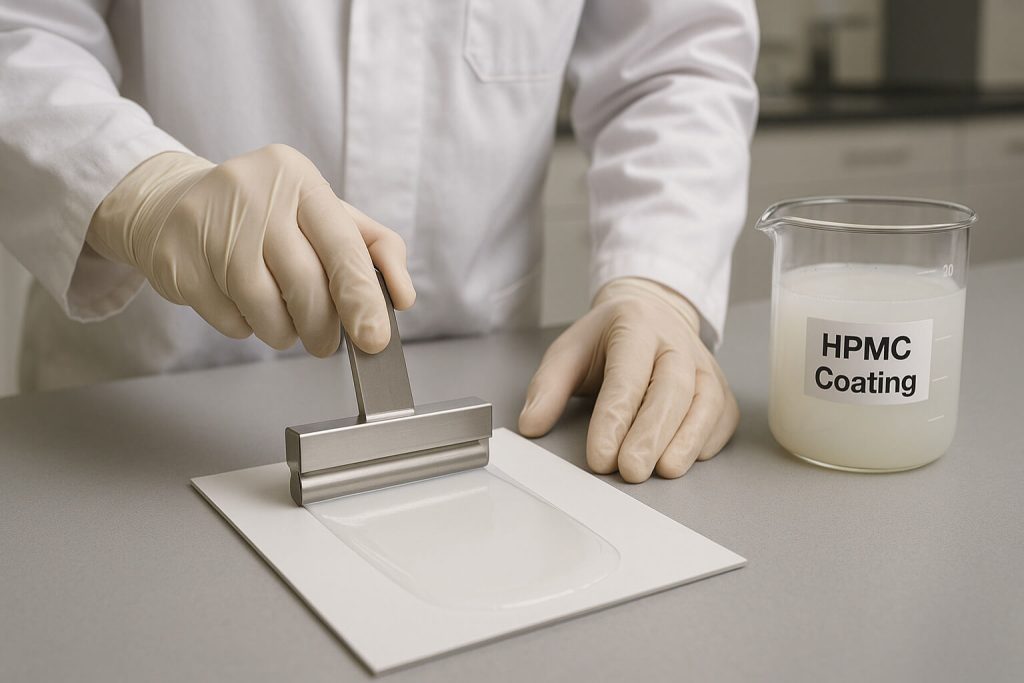
1. What Are the Basic Properties of Hydroxypropyl Methylcellulose in Coatings?
HPMC is a changed plant fiber that comes from trees. It has special groups added to a fiber base. This unique build gives HPMC its good traits for coatings.
But what makes it so effective? HPMC can mix with water and form films. When added to coatings, HPMC breaks down in water at room heat. This makes a clear mix with no lumps.
The size of HPMC affects how it works in coatings. Bigger types make thicker mixes. Smaller types flow better but hold less water.
HPMC comes in many forms. The methyl part is often 19-30%. The hydroxypropyl part is 7-12%. These ratios change how it works with water and other coating parts.
One big plus of HPMC is its heat gel trait. Unlike many items that thin when hot, HPMC mixes form short gels at higher heat. This stops drips during use and drying.
Trait | Low Thick HPMC | Medium Thick HPMC | High Thick HPMC |
---|---|---|---|
Thickness | 5-100 mPa·s | 100-5,000 mPa·s | 5,000-100,000 mPa·s |
Water Holding | Low | Medium | High |
Film Depth | Thin | Medium | Thick |
Drip Fighting | Low | Medium | High |
Smooth Traits | Great | Good | Fair |
The surface work of HPMC also helps coating success. While not a true soap, HPMC cuts surface pull a bit. This helps coatings wet surfaces better.
When you match HPMC to other fiber types, some gaps show up. HPMC holds water better than MC. It fights bugs better than HEC. It also makes more bendy films than CMC.
The bit size of HPMC powder affects how fast it breaks down. Fine ground types break down faster but may make more dust. Coarse types make less dust but need more mixing to break down.
2. How Does HPMC Affect Coating Viscosity and Application?
The link between HPMC amount and coating thickness follows a clear path. As you add more, thickness grows fast. This lets makers make big thickness changes with small HPMC shifts.
Here’s the cool part: HPMC makes coatings flow in a special way. The thickness drops as you stir faster. When you put on the coating with a brush, the stir thins it for easy use. Once on, the coating gets thick again to stop drips.
The size of the HPMC type has a direct hit on this thin trait. Bigger types show more of this effect. Smaller types flow more like water.
Heat has a big effect on HPMC coatings during use. Below the heat gel point (often 50-70°C), thickness drops as heat rises. Above this point, short gel forms, which can hurt spray use if tools run too hot.
Use Method | Best HPMC Type | Typical Amount | Main Gain |
---|---|---|---|
Spray Use | Low thick | 0.1-0.5% | Stops clogs, helps spray |
Roller Use | Medium thick | 0.3-0.8% | Cuts mess, helps move |
Brush Use | Medium-high thick | 0.5-1.0% | Stops drips, helps pickup |
Dip Coating | Low-medium thick | 0.2-0.6% | Sets coat depth, cuts runs |
Curtain Coating | Medium thick | 0.3-0.7% | Keeps curtain, helps even coat |
The pH of the coating mix affects how HPMC works as a thickener. HPMC keeps steady thickness across pH 3-11. This makes it good for both acid and base coating types.
Hands-on thickness control tricks with HPMC include pre-mix in hot water before cooling. Adding HPMC to the water part before adding colors stops dry spots in the final coating.
A real case from a big paint maker showed that using HPMC cut costs by 15%. The mix still worked well. The HPMC coating had better brush drag traits and less mess during roller use.
The shelf life of HPMC coatings hangs on good bug control. While HPMC itself fights bugs, water mixes with HPMC need bug killers to stop thickness loss during storage.
3. What Role Does HPMC Play in Water Retention of Coatings?
Water holding is the most useful trait HPMC brings to coating mixes. The parts on the fiber base make a water-loving net that holds water bits. This net slows water loss during drying.
You might be shocked to learn that water holding has a direct effect on coating quality. When a coating loses water too fast to a porous face like drywall, many issues pop up: poor stick, uneven look, and short life.
The way HPMC holds water works through bonds between water bits and the groups on the fiber. These bonds lock water in the coating film. As the coating dries, these bonds slowly break, letting water out in a steady way.
The level of change of the HPMC affects its water holding power. More change often means more water holding. The methyl part affects the heat at which the fiber starts to lose its water-holding power.
Base Type | Water Holding Gain | Best HPMC Type | Typical Dose |
---|---|---|---|
Very Porous (Concrete) | Stops early drying | High thick | 0.8-1.2% |
Mid Porous (Drywall) | Sets water flow | Medium thick | 0.5-0.9% |
Non-porous (Metal) | Helps smooth time | Low-medium thick | 0.3-0.6% |
Mixed Porous | Makes dry rate even | Medium thick | 0.5-0.8% |
Hot/Dry States | Stops skin forming | High thick | 0.7-1.1% |
Ways to test water holding traits include the DIN test. It checks water loss under vacuum. The ASTM test checks water loss to a thirsty base. Both tests help makers pick the best HPMC type.
A field test of wall coatings showed that more HPMC made work time 40% longer in hot, dry states. This let users keep a wet edge and avoid marks during big jobs.
The water holding effect of HPMC also helps keep color bits spread out during drying. By slowing water flow, HPMC stops color float that can cause color shifts.
The size of HPMC links with water holding power. Bigger types form more bond nets. This traps more water bits in the coating film during use and early drying steps.
4. How Does HPMC Influence Coating Adhesion to Different Substrates?
Stick is a key trait for any coating, and HPMC has a big effect on how coatings bond to bases. The main stick way works through the groups on HPMC forming bonds with base faces. These bonds make strong first tack during use.
Want to know something cool? HPMC helps stick in different ways based on base pores. On porous bases, HPMC helps the coating get into face bumps before setting. On smooth bases, it slows drying time. This allows better wetting and bonds.
The tiny build of HPMC has both water-loving and water-hating parts. This dual nature helps it act as a bridge between the coating resin and tough bases. The methyl groups give water-hating links while hydroxyl groups form water-loving bonds.
On concrete and wall faces, HPMC coatings show 30-50% better stick vs. plain ones. This boost comes from steady water flow that stops the coating from drying too fast.
Base | Stick Test | How HPMC Helps | Tested Gain |
---|---|---|---|
Concrete | Very base, porous | Sets water flow, fights pH effects | 40-50% higher pull-off strength |
Wood | Mixed pores, plant oils | Sets soak-in, blocks plant oil flow | 25-35% better cross-hatch stick |
Metal | Smooth, non-porous | Makes wet time longer for better wetting | 15-25% better direct hit fight |
Glass | Very smooth, water-loving | Ups polar links | 20-30% better water soak fight |
Plastic | Low face pull | Helps wetting through soap work | 30-40% higher tape stick scores |
Test ways for stick gains include cross-hatch tests, pull-off stick tests, and tape stick tests. These set ways give clear data on how HPMC affects coating bond strength.
The hydroxypropyl change level affects stick traits more than methyl part. More hydroxypropyl change helps stick to water-loving faces like glass and metal. More methyl part can help stick to water-hating faces like some plastics.
A case study with shop care coatings showed that adding HPMC to a base coat upped stick to steel by 27% after salt spray test. The HPMC base coat kept better under-film shape during rust states.
The film flex from HPMC also adds to long-term stick. More bendy films can move with the base without cracking. This helps a lot for outside coatings that face heat cycles and wet shifts.
5. What Are the Film Formation Benefits of HPMC in Coatings?
Film forming is how a wet coating turns into a solid film. HPMC plays many roles in this key phase. It helps set the rate of water loss. This leads to more even drying across the whole coated face.
The key point here is that HPMC makes a more neat fiber net during film forming. As water dries up, HPMC bits line up and form bonds with each other and with the main binder. This neat shape cuts stress points that could lead to cracks.
The stop of common film flaws is a major plus of HPMC use. Cratering, a flaw from face pull gaps, drops when HPMC is there. The fiber’s mild soap traits help keep even face pull during drying.
Crack fight gets better with HPMC due to its soft effect. The bendy HPMC bits stay between binder bits as they join, cutting inner stress. This soft effect is short-term in outside uses as the HPMC breaks down under sun over time.
Film Trait | Without HPMC | With Best HPMC | Gain Factor |
---|---|---|---|
Film Even | Mixed depth | Same depth | 2-3× more even |
Crack Fight | Mid | High | 3-4× fewer cracks |
Sag Fight | Low-Mid | High | 2× key depth |
Early Block Fight | Poor | Good | 3× faster growth |
Rub Fight | Mid | Good-Great | 30-40% gain |
The hit on coating hard state hangs on HPMC type and amount. At low levels, HPMC has small effect on final hard state. At higher levels, it can slightly cut hard state while making flex better. This trade-off is often fine for better use traits.
HPMC affects the glass shift heat of the final coating film. It often lowers it a bit. This can help crack fight in cold spots but may cut block fight in hot states. Makers must balance these effects based on the coating’s planned use.
Life gains in HPMC coatings come from better film shape and base stick. A study of outside paints showed that adding HPMC upped weather fight by 25% in fast tests. The better film forming cut water paths that lead to coating fail.
The look traits of the final film also gain from HPMC. By helping more even color spread during drying, HPMC helps get better hiding power and color even state. This effect helps a lot in home coatings where looks matter most.
6. How Do Different HPMC Grades Affect Coating Stability and Shelf Life?
Shelf life is a big worry for coating makers. HPMC adds to life in many ways. First, its thick effect keeps colors and fillers hung up. This stops hard sink that can make goods useless after storage.
What many folks don’t know is that HPMC makes a weak gel shape at rest. This shape gives yield value—the force needed to start the coating flowing. Higher yield value stops bit move during storage without hurting use traits once shear is put on.
The stop of water split is another life plus. HPMC’s water-bond skill cuts free water that might split during storage. This keeps the coating mixed well and ready to use without long mixing.
Different HPMC types offer varied life traits. Higher thick types give better hang but may trap air. Lower thick types let air out better but may need more hang helpers for long-term life.
Life Check | Low Thick HPMC | Medium Thick HPMC | High Thick HPMC |
---|---|---|---|
Sink Control | Fair | Good | Great |
Water Split Stop | Fair | Good | Great |
Freeze-Thaw Life | Good | Very Good | Great |
Heat Life (50°C) | Great | Good | Fair |
Air Out | Great | Good | Fair |
The hit on freeze-thaw life is very useful for water-based coatings. HPMC cuts ice bit forming during freeze by tying up water bits. This stops the body harm to the mix that happens when big ice bits form.
A life study of latex paints showed that adding HPMC upped freeze-thaw cycle fight from 3 cycles to 5 cycles. The HPMC paint kept good thick and use traits after many heat cycles.
The pH life of HPMC helps keep steady traits during storage. Unlike some man-made thickeners that lose work with pH drift, HPMC keeps its skill across pH 3-11. This makes it good for both acid and base coating types.
Long-term trait hold in stored coating goods hangs on right HPMC pick. For max shelf life, makers should choose HPMC types with good bug fight. Some types get special care to fight bug break that could cause thick loss.
Conclusion
HPMC gives many gains that make coating work and use traits better. From better thick control and water hold to stronger stick and film forming, HPMC fixes key tests faced by coating makers and users. By picking the right HPMC type and amount, you can cut flaws by up to 40%. You can also make work time longer in tough states. Contact Morton today to ask for a custom HPMC tip for your own coating use. Our tech team can help you pick the best type to reach your work goals and help your bottom line.
Q1: What concentration of HPMC is typically used in coating formulations?
Most coating mixes use HPMC amounts between 0.1% and 1.2% by weight. This changes based on the use method and traits you want. Spray uses need 0.1-0.5%, roller uses need 0.3-0.8%, and brush uses need 0.5-1.0%. The exact amount hangs on the HPMC type’s thick level, the coating type, and the base. Higher amounts give more water hold and sag fight but may hurt smooth look and final face.
Q2: Can HPMC be combined with other additives in coating formulations?
Yes, HPMC works well with most common coating adds. It shows good mix with acrylic, vinyl, and styrene-acrylic binders. HPMC can work with man-made thickeners like HEUR and HASE for better flow control. It also works well with flow helps, foam stops, and wet helps when added in the right order. The main point is adding HPMC to the water part before adding colors and other solids to avoid lumps and poor break down.
Q3: How does HPMC compare to other thickeners in coating applications?
HPMC gives a unique mix of traits vs. other thickeners. Unlike man-made link thickeners, HPMC gives great water hold and is less touchy to mix shifts. Vs. other plant types, HPMC has better face work than CMC and better bug fight than HEC. HPMC gives more special flow than polyacrylates, giving better sag fight after use. While man-made thickeners may work better at low shear, HPMC gives better all-around work across many coating traits.
Q4: Does HPMC affect the drying time of water-based coatings?
Yes, HPMC often makes the dry time of water-based coatings longer, but the effect shifts by base and states. On porous bases, the water hold effect can speed up real dry time. It stops too-fast water soak that would leave binder at the face. On non-porous bases, HPMC makes open time 15-40% longer based on type and amount. This longer open time often helps get better smooth look and avoid lap marks, most of all in warm or windy states.
Q5: Are there any limitations when using HPMC in coating applications?
While HPMC gives many pluses, it does have some limits. High amounts can cut gloss in some mixes due to the fiber’s spot at the face. HPMC may slightly cut water fight in the early steps after use, though this effect drops as the coating dries fully. In outside uses, HPMC slowly breaks down under sun, so its effects on flex are short-term. Some types may add to foam, needing shifts of foam stop levels. These limits can be fixed through right type pick and mix shifts.