Making good pills and tablets needs the right coating. Drug makers often can’t find coatings that both protect the medicine and break down at the right time. Bad coatings lead to pills that taste bitter, break down too fast, or don’t work right. These problems make patients unhappy and can cause trouble with health rules. HPMC coating fixes these issues by adding better protection, controlled release, and a better patient experience. Studies show that coated pills can boost patient use by up to 40% compared to pills without coating. Let’s look at how HPMC coating works and why so many drug makers now use it.
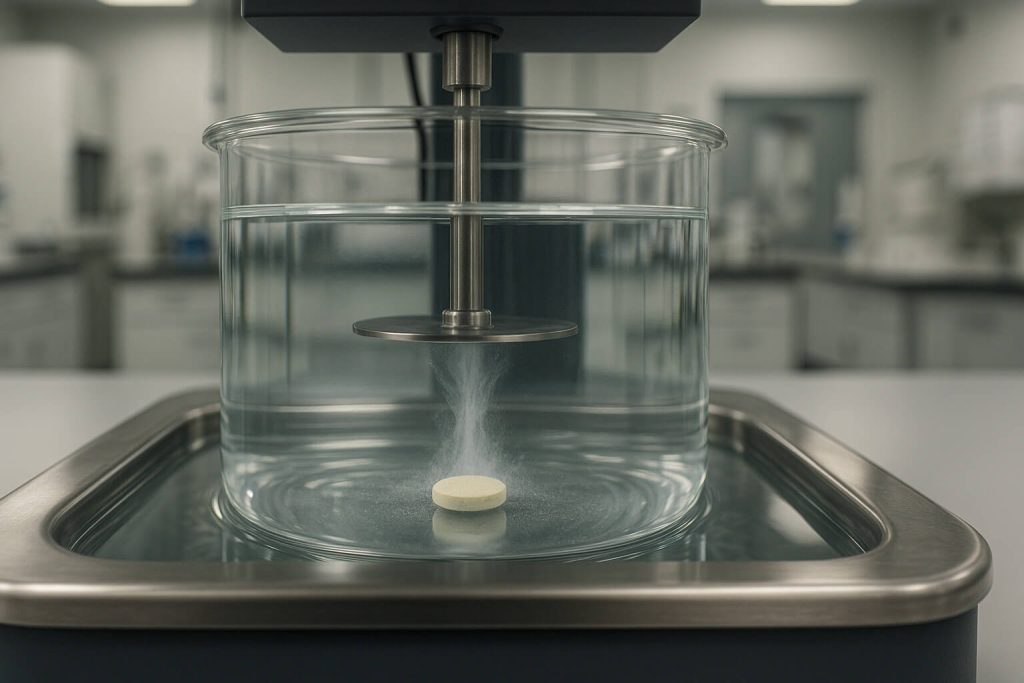
1. What Is HPMC Coating and How Does It Work?
HPMC (Hydroxypropyl Methylcellulose) comes from plant cellulose. It forms a shield around pills while adding useful features.
Want to know what makes HPMC special? It mixes water-friendly and water-repelling parts to create a smooth coating that breaks down just right in your body. The coating sticks to the pill through physical bonds, not chemical ones.
HPMC coating happens through film forming. When sprayed as a liquid onto pills, the water dries up and leaves a thin, even film. This film can be thin (20 microns) for fast-release drugs or thick (100 microns) for slow-release ones.
The coating works best when it matches the drug’s needs. Pills that need to work fast use thin coatings. Pills that should work over many hours use thicker ones.
HPMC Property | Benefit to Coating | Application Example |
---|---|---|
Film-forming ability | Creates smooth surface | Tablet coating |
Water solubility | Controls when drug releases | Fast-acting pain pills |
Thermal setting | Stays stable in heat | Heat-sensitive drugs |
Low oxygen passing | Blocks air damage | Vitamin pills |
UV light blocking | Stops light damage | Light-sensitive drugs |
HPMC comes in different grades based on its makeup. Low-thickness grades (E3, E5, E6) work for basic coating. Medium grades (E15, E50) give better strength and moisture blocking. High-thickness grades (K100M, K4M) excel at slow-release drugs.
The coating process uses spray systems that coat pills as they tumble in a drum or float in air. As the liquid dries, the coating forms a solid film.
2. Why Do Pharmaceutical Companies Choose HPMC Coatings?
Drug makers pick coating materials based on how well they work, what they cost, and if they meet health rules. HPMC has become very popular due to its many benefits.
Did you know that HPMC offers big advantages over old-style coatings? Unlike sugar coatings that need many layers and long drying times, HPMC needs just one step. This cuts making time by up to 75% compared to sugar coating.
HPMC works with water instead of harsh solvents. This makes it safer for workers and better for the earth. It avoids the fire risks that come with solvent-based options like cellulose acetate phthalate.
While HPMC may cost a bit more per pound than some options, the total cost ends up lower. This happens because it needs less time, fewer layers, and simpler machines.
Coating Material | Processing Time | Solvent System | Regulatory Status | Cost Efficiency |
---|---|---|---|---|
HPMC | 2-4 hours | Water-based | Global acceptance | High |
Sugar coating | 8-24 hours | Water-based | Limited use | Low |
Shellac | 4-6 hours | Alcohol-based | Some limits | Medium |
Acrylic polymers | 3-5 hours | Mixed | Widely accepted | Medium |
Ethylcellulose | 4-6 hours | Organic solvents | Widely accepted | Medium |
Health groups worldwide see HPMC as safe. The FDA lists it as GRAS (Generally Recognized As Safe). The European Medicines Agency also approves it. This global okay makes getting new drugs approved easier.
Market trends show strong favor for HPMC. Reports say over 70% of new pill forms use HPMC-based coating systems. This high use has created scale savings, further cutting costs.
3. How Does HPMC Coating Affect Drug Release Rates?
When a drug gets into your body matters a lot. HPMC coatings can be made to release drugs at just the right time based on what the patient needs.
You might be surprised by how flexible HPMC can be for controlling drug release. By changing the weight, pattern, and thickness, makers can create pills that work right away or slowly over 24 hours.
For fast-acting drugs, thin HPMC coatings (20-40 microns) quickly break down in stomach acid. This lets the drug start working in just 15-30 minutes after you take it.
Slow-release pills use thicker HPMC coatings. When these meet your digestive juices, they form a gel layer that controls how fast the drug comes out. As this gel slowly wears away, the drug releases at a steady rate.
Release Profile | HPMC Grade | Coating Thickness | Release Mechanism | Application Example |
---|---|---|---|---|
Immediate | E3, E5 | 20-40 μm | Quick dissolving | Pain relievers |
Delayed | E15 + additives | 40-60 μm | pH-triggered | Stomach protection |
Extended (6-8 hr) | E50, K4M | 60-80 μm | Erosion/diffusion | Blood pressure meds |
Extended (12-24 hr) | K100M | 80-100 μm | Slow erosion | Sleep medications |
Pulsed | Multiple layers | Various | Layer dissolving | Fever reducers |
A real case shows how HPMC coating helped a diabetes drug. By fixing the coating mix, the maker created a pill that kept blood sugar steady all day. This let patients take one pill daily instead of two.
Coating thickness directly affects how fast drugs release. Each 10-micron increase in thickness adds about 1-2 hours to the release time for high-grade HPMC. This lets drug makers design pills with very exact timing.
Heat affects how HPMC forms gels and releases drugs. In hot places, the coating may slow down drug release. Drug makers account for this when making pills for global markets with different climates.
4. What Manufacturing Processes Work Best for HPMC Coating?
Good HPMC coating needs the right tools and careful control. The making method greatly affects coating quality and how even it is.
The truth is that spray coating dominates the HPMC world. Over 90% of drug makers use either pan coating or fluid bed systems. These methods give great control over coating thickness and evenness.
Pan coating tumbles pills in a turning drum while spraying HPMC liquid through nozzles. This old-school method works well for normal pill shapes but may struggle with odd shapes. New pan coaters have auto controls for spray rate, pan speed, and air flow.
Fluid bed coating floats pills in an air stream while spraying coating from above or below. This gives very even coating and works great for small pills and pellets. The high air flow lets coatings dry faster than pan coating.
Process Setting | Good Range | Impact on Coating | How to Check |
---|---|---|---|
Spray rate | 5-15 g/min/kg | Thickness evenness | Flow meters |
Inlet air heat | 50-70°C | Drying speed | Heat sensors |
Product heat | 35-45°C | Film forming | IR sensors |
Pan/bed speed | 10-20 rpm | Pill movement | Speed gauge |
Spray pressure | 1.5-3.0 bar | Droplet size | Pressure gauges |
Coating thickness | 100-500 cP | Even coating | Thickness tool |
Humidity control is a common challenge during HPMC coating. The best relative humidity in the coating room is 40-60%. Too dry causes rough coatings, while too wet makes drying slow and may soften pills.
Quality checks during HPMC coating use several methods. Weight gain tracks coating progress, with goals of 2-4% for fast-release and 5-8% for slow-release pills. Visual checks find flaws like orange peel texture, cracks, or uneven color.
New tech has made HPMC coating more even. Near-infrared tools can check coating thickness in real-time. This allows auto fixes to the process, making each batch more like the last.
5. How Does HPMC Coating Impact Medication Stability?
Drug stability sets how long pills last and work well. HPMC coatings give many kinds of protection that help keep drugs good over time.
Here’s something you should know about stability: HPMC blocks things that can harm drugs. This protection makes pills last longer and stay strong until they expire.
Moisture protection is one of HPMC’s best traits. The coating forms a barrier that controls water movement. For drugs that pull in water, this stops them from breaking down too soon.
Light can harm many drugs, especially those with certain chemical bonds. HPMC coatings can add white pigments like titanium dioxide that block UV and visible light, stopping light damage.
Stability Factor | HPMC Protection Level | Enhancement Options | Testing Method |
---|---|---|---|
Moisture | Medium to High | Water-hating adds | Karl Fischer test |
Light | Low to High (with adds) | TiO₂, iron oxides | Light test chamber |
Oxygen | Medium | Add antioxidants | Oxygen rate test |
Temperature | Medium | Heat stabilizers | Speed aging test |
Microbes | Low to Medium | Add preservatives | Microbe testing |
Tests show HPMC-coated pills last longer than uncoated ones. In speed aging tests (40°C/75% RH), HPMC-coated pills stay good for 3-6 months, equal to 2-3 years at room temp.
Storage needs become less strict with good HPMC coating. While uncoated water-loving drugs might need drying agents and foil packs, HPMC-coated ones often stay stable in simple plastic bottles with normal caps.
Longer shelf life through HPMC coating saves money. Longer dating cuts waste from expired pills and helps stock planning. For seasonal drugs, longer shelf life allows more efficient making schedules.
6. What Are the Patient Benefits of HPMC-Coated Medications?
Beyond making and stability gains, HPMC coatings directly help patients. These benefits can boost how well patients take their meds and get better.
Let me tell you why patients prefer HPMC-coated pills. The smooth, easy-to-swallow surface cuts throat pain and stops pills from sticking when swallowing. This alone can help patients who struggle to take pills.
Taste masking is one of HPMC’s most liked features. Many drug parts taste very bitter. HPMC creates a shield that keeps these parts from touching taste buds during swallowing.
Smell control works like taste masking. HPMC traps smelly parts that create bad odors, making pills nicer to take. This helps with sulfur drugs and some vitamins with strong smells.
Patient Benefit | How It Works | Impact on Use | Patients Most Helped |
---|---|---|---|
Taste masking | Physical barrier | High | Kids, picky adults |
Smell control | Traps smelly parts | Medium | Older folks, sensitive patients |
Easy swallowing | Surface wetting | High | Swallowing problem patients |
Visual ID | Color coding | Medium | Multi-med users |
Allergy-free | Plant-based | Medium | Vegans, religious needs |
Patient use data shows big gains with coated pills. Studies find 15-30% higher use rates for coated vs. uncoated versions of the same drug, especially among kids and older folks.
Look and brand gain from HPMC’s ability to take colors and printing. Same look helps patients ID their pills right, cutting dosing errors. This visual sameness also builds brand trust.
Plant-based traits make HPMC good for patients with food rules. Unlike animal-based gel caps, HPMC comes from plant cellulose. This makes it okay for vegans and those following kosher or halal diets.
Conclusion
HPMC coating makes pills better by fixing many drug delivery and patient problems. From guarding active parts to controlling release rates and hiding bad tastes, HPMC coatings help make drugs work better and patients take them more often. Data shows that well-made HPMC coatings can make pills last 50-100% longer while helping 30% more patients take them as told. For drug makers wanting better pills, Morton offers special HPMC mixes and tech help to get just the right coating for any need. Contact Morton’s team today to ask for a meeting and product samples for your specific needs.
FAQ
Q1: Is HPMC coating safe for all patient populations?
HPMC coatings have a great safety record for most patients. The stuff is non-toxic, non-irritating, and rarely causes allergic reactions. It works well for kids and older folks. Patients with rare cellulose issues should ask their doctor, but such problems are very rare. Health groups worldwide have approved HPMC for drug use across all age groups.
Q2: Can HPMC coating be used with both prescription and over-the-counter medications?
Yes, HPMC coating works just as well for prescription and over-the-counter products. Many OTC pain pills, vitamins, and supplements use HPMC coatings for taste masking and easy swallowing. Prescription drugs often use HPMC for timed release. The flexibility of HPMC makes it good for almost any pill type no matter the rules.
Q3: How does HPMC coating compare to gelatin capsules for drug delivery?
HPMC coatings and gelatin caps serve different roles in drug making. HPMC coatings go right on pill surfaces, while gelatin forms the whole cap shell. HPMC offers better stability in changing humidity and works with more fillers. Gelatin caps break down a bit faster but need stricter storage. HPMC comes from plants, making it good for veggie products, while normal gelatin comes from animals.
Q4: What are the environmental impacts of HPMC coating production?
HPMC making has a fairly low earth impact compared to many drug materials. It comes from wood pulp and uses water-based making. The coating process uses mainly water as a solvent, avoiding harsh chemicals that cause air pollution. Waste from the coating has no toxic parts and can go through normal water treatment.
Q5: Does HPMC coating affect the bioavailability of active ingredients?
HPMC coating typically doesn’t cut bioavailability when made right. For fast-release products, thin HPMC coatings break down quickly in stomach acid, letting the drug out with little delay. Timed-release forms control bioavailability on purpose to get specific blood levels. Drug makers must check through tests that the coating works as planned.