Hydroxypropyl methylcellulose, or HPMC, is a versatile polymer. It finds use across many industries. This compound is a cellulose ether. It comes from natural cellulose. HPMC changes the properties of liquids and solids. It acts as a thickener, binder, and film former. Many businesses face challenges with product consistency. They also struggle with material performance. HPMC offers a reliable solution. It improves product quality and process efficiency. This article will explain HPMC. It will cover its properties, production, and main uses. You will learn how HPMC improves construction, pharmaceutical, and food products. We will also discuss safety and selection guidelines.
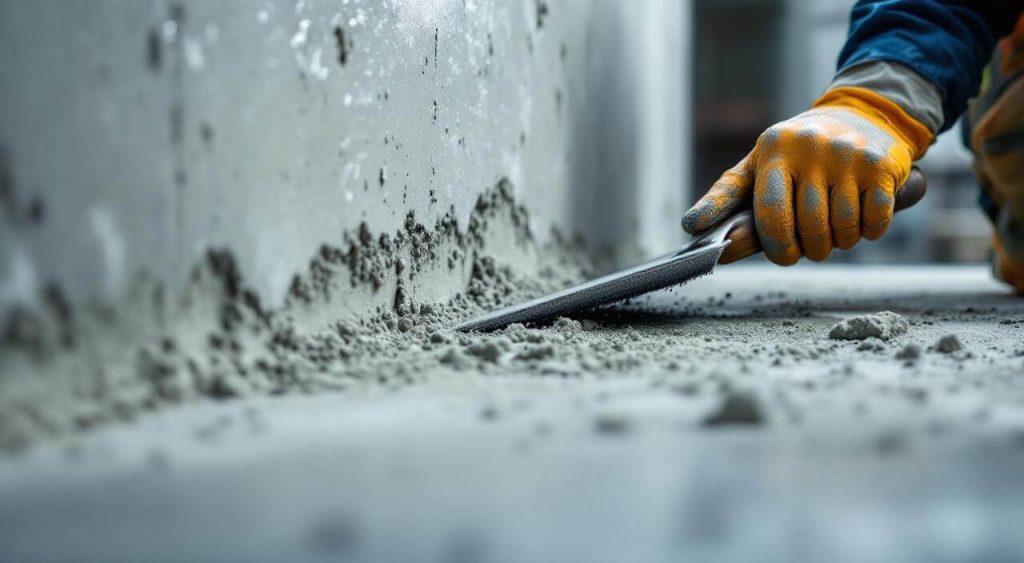
1. What is HPMC and how does it function?
HPMC is a derivative of cellulose. It is a non-ionic cellulose ether. Manufacturers create it from natural wood pulp or cotton linters. The process involves treating cellulose with methyl chloride and propylene oxide. This chemical modification gives HPMC its unique properties. It makes HPMC soluble in cold water. This solubility is a key feature. It allows HPMC to form clear solutions. These solutions can be highly viscous.
Here’s why it matters… HPMC’s ability to thicken and form films makes it useful. It can create a protective layer. It also binds particles together. This makes it valuable in many products. Its viscosity can range widely. This depends on the degree of polymerization. It also depends on the substitution of methyl and hydroxypropyl groups. Gelation is another important property. HPMC solutions can form gels when heated. They return to liquid form upon cooling. This thermal gelation is reversible. It is useful in certain applications. HPMC forms films by drying. The films are flexible and strong. They resist oil and grease. This makes them good for coatings. The thickening action comes from polymer chains. These chains entangle in solution. This increases the resistance to flow.
Property | Description |
---|---|
Solubility | Dissolves in cold water, forms clear solutions |
Viscosity | Adjustable, from low to high |
Gelation | Forms reversible gels when heated |
Film Formation | Creates strong, flexible films |
Water Retention | Holds water in formulations |
2. How is HPMC produced and what are its grades?
HPMC production starts with cellulose. This raw material comes from wood pulp or cotton. The cellulose undergoes a purification process. Then, it reacts with sodium hydroxide. This creates alkali cellulose. This step activates the cellulose. It prepares it for the next reactions. The alkali cellulose then reacts with methyl chloride and propylene oxide. These chemicals attach to the cellulose backbone. This forms the hydroxypropyl methylcellulose polymer. The reaction conditions control the degree of substitution. This affects the final properties of HPMC. After the reaction, the product is purified. It is washed to remove impurities. Then, it is dried and ground into a fine powder.
Now, you might be wondering… what are the different grades? HPMC comes in various grades. These grades differ in viscosity and substitution patterns. Viscosity is a key differentiator. It ranges from low to high. Low viscosity grades are good for thin coatings. High viscosity grades are used for thickening. The substitution pattern refers to the ratio of methyl to hydroxypropyl groups. This affects solubility and gelation temperature. Manufacturers control these factors. They create specific grades for different uses. Quality control is strict. It ensures purity and consistent performance. This includes testing for heavy metals and microbial limits.
Grade Type | Viscosity Range | Common Uses |
---|---|---|
Low Viscosity | 3-50 mPa·s | Film coatings, thin-layer applications |
Medium Viscosity | 50-4,000 mPa·s | Adhesives, paints, general thickening |
High Viscosity | 4,000-200,000 mPa·s | Mortars, renders, controlled release systems |
3. What are the primary industrial applications of HPMC?
HPMC finds wide use across many industries. Its diverse properties make it valuable. In construction, it improves building materials. It is in mortars, renders, and tile adhesives. HPMC enhances workability and water retention. This leads to stronger, more durable structures. In paints and coatings, HPMC acts as a thickener. It also improves stability. It helps form a smooth, even film. This gives a better finish.
This is important because… HPMC helps these products perform better. It makes them easier to use. It also extends their lifespan. Personal care products also use HPMC. It is in cosmetics and detergents. It provides thickening and emulsifying properties. This creates stable and pleasant textures. The food industry uses HPMC as well. It serves as a thickener, stabilizer, and emulsifier. It improves texture and mouthfeel in many food items. It also helps retain moisture.
Industry | Key Application Areas |
---|---|
Construction | Mortars, renders, tile adhesives, grouts |
Paints & Coatings | Water-based paints, primers, sealants |
Personal Care | Shampoos, lotions, creams, hand sanitizers |
Food | Baked goods, dairy products, sauces, dressings |
Pharmaceuticals | Tablets, capsules, ophthalmic solutions |
4. How does HPMC improve construction material performance?
HPMC is a key additive in construction. It significantly improves the performance of building materials. For cementitious systems, HPMC enhances water retention. This means the mixture stays workable longer. It prevents premature drying. This is crucial for proper hydration of cement. It also improves the adhesion of mortars and renders. This leads to stronger bonds. It reduces cracking.
The bottom line? HPMC makes construction materials more reliable. It also makes them easier to apply. For tile adhesives, HPMC extends the open time. This is the time before the adhesive sets. It allows for more precise tile placement. It also improves the bond strength. This prevents tiles from detaching. In renders, HPMC provides sag resistance. This means the render stays in place. It does not slide down vertical surfaces. It also helps prevent cracks. This creates a smoother, more durable finish.
HPMC Benefit | Impact on Construction Materials |
---|---|
Water Retention | Longer workability, better cement hydration |
Adhesion Strength | Stronger bonds, reduced delamination |
Open Time | More time for tile placement, better bonding |
Sag Resistance | Prevents material slump on vertical surfaces |
Crack Prevention | Smoother finishes, increased durability |
5. What role does HPMC play in pharmaceutical formulations?
HPMC is a widely used excipient in pharmaceuticals. It serves multiple functions in drug formulations. As a binder, it helps hold tablet ingredients together. This ensures tablet integrity and strength. It prevents tablets from crumbling. HPMC also acts as a film-forming agent. It creates coatings for tablets and capsules. These coatings can protect the drug. They can also mask taste.
Want to know the secret? HPMC is crucial for controlled release. It forms a gel layer around the tablet. This layer controls how fast the drug dissolves. This allows for sustained drug release over time. This means patients take fewer doses. It also helps maintain steady drug levels. HPMC is also in ophthalmic solutions. It increases the viscosity of eye drops. This extends the contact time of the drug with the eye. It improves drug absorption. It also reduces irritation.
Pharmaceutical Application | HPMC Function |
---|---|
Tablet Binder | Ensures tablet integrity and strength |
Film Coating | Protects drug, masks taste, improves appearance |
Controlled Release | Sustains drug release over time |
Ophthalmic Solutions | Increases viscosity, extends contact time |
Suspensions | Stabilizes particles, prevents settling |
6. How does HPMC contribute to personal care and food products?
HPMC is a valuable ingredient in personal care items. It provides thickening and emulsifying properties. In shampoos and lotions, it creates a desirable texture. It also helps stabilize emulsions. This prevents ingredients from separating. For example, in hand sanitizers, HPMC gives the gel consistency. This makes the product easy to apply. It also ensures even distribution.
What does this mean for you? HPMC improves the user experience. It makes products feel better. In food products, HPMC acts as a thickener and stabilizer. It can improve the texture of sauces and dressings. It prevents syneresis, which is water separation. In baked goods, HPMC helps retain moisture. This keeps products fresh longer. It also improves dough workability. It can replace some fats in certain recipes. This helps create healthier food options. HPMC is also used in vegetarian and vegan products. It provides a plant-based alternative to animal-derived thickeners.
Product Category | HPMC Role |
---|---|
Personal Care | Thickening, emulsifying, texture enhancement |
Food | Thickening, stabilizing, moisture retention |
Beverages | Suspension of solids, mouthfeel improvement |
7. What are the safety and regulatory considerations for HPMC?
HPMC is generally recognized as safe (GRAS) by regulatory bodies. This includes the U.S. Food and Drug Administration (FDA). It is approved for use in food, pharmaceuticals, and cosmetics. This broad approval reflects its safety profile. HPMC is non-toxic and non-allergenic. It does not irritate skin or eyes. It is also metabolically inert. This means the body does not absorb or break it down. It passes through the digestive system unchanged.
Let me explain… proper handling and storage are still important. HPMC should be stored in a cool, dry place. It should be kept away from direct sunlight. This prevents degradation. It also maintains its quality. Always use clean equipment when handling HPMC. This avoids contamination. From an environmental standpoint, HPMC is biodegradable. It breaks down naturally in the environment. This makes it a sustainable choice. It does not accumulate in ecosystems. Its production process also has a low environmental impact. This makes it a responsible choice for manufacturers.
Aspect | Consideration |
---|---|
Regulatory Status | GRAS by FDA, approved for food, pharma, cosmetics |
Safety Profile | Non-toxic, non-allergenic, metabolically inert |
Handling | Store cool, dry; use clean equipment |
Environmental | Biodegradable, low environmental impact |
8. How do you select the right HPMC grade for your application?
Choosing the correct HPMC grade is crucial. It ensures optimal product performance. Several factors influence this selection. Viscosity is a primary consideration. It determines the thickening power. For example, a low viscosity grade works for thin film coatings. A high viscosity grade is better for thick mortars. The substitution type also matters. This refers to the ratio of methyl to hydroxypropyl groups. It affects solubility and gelation temperature. Different substitution types suit different applications.
But here’s the thing… particle size also plays a role. Finer particles dissolve faster. They also disperse more easily. Coarser particles might be better for certain dry mixes. Matching HPMC properties to specific application needs is key. Consider the desired end product characteristics. Think about processing conditions. For instance, a pharmaceutical tablet needs a specific dissolution profile. A construction adhesive needs a certain open time. Testing and validation are essential. Always conduct trials with different HPMC grades. This helps find the best fit. It ensures the HPMC performs as expected. It also helps avoid costly mistakes.
Selection Factor | Impact on HPMC Performance |
---|---|
Viscosity | Thickening power, flow properties |
Substitution Type | Solubility, gelation temperature, film properties |
Particle Size | Dissolution rate, dispersion characteristics |
Purity | Product quality, regulatory compliance |
Application Needs | Desired end product characteristics, processing |
Conclusion
HPMC is a highly versatile polymer. It offers many benefits across diverse industries. We have seen how it improves construction materials. It enhances their workability and durability. In pharmaceuticals, HPMC enables controlled drug release. It also improves tablet integrity. For personal care and food products, it provides essential thickening and stabilizing functions. Its safety profile and regulatory approvals make it a trusted choice. Selecting the right HPMC grade is vital. It ensures optimal performance for your specific application. This choice impacts product quality and efficiency.
By carefully choosing HPMC, you can achieve superior product outcomes. This leads to better market acceptance and reduced production costs. Morton offers a wide range of HPMC grades. We provide expert guidance to help you select the perfect solution. Contact Morton today to discuss your specific needs. We can help you find the ideal HPMC product. Partner with us to enhance your product formulations.
FAQ
- Q1: Is HPMC a natural or synthetic polymer?
HPMC is a semi-synthetic polymer. It is derived from natural cellulose. Cellulose comes from wood pulp or cotton. Chemical modification creates the final HPMC product. - Q2: What is the primary difference between HPMC and other cellulose ethers?
HPMC differs from other cellulose ethers in its substitution groups. It has both methyl and hydroxypropyl groups. This gives it unique properties. These include cold water solubility and thermal gelation. - Q3: Can HPMC be used in organic certified products?
Yes, certain grades of HPMC can be used in organic certified products. This depends on the specific certification standards. Always check with the certifying body. - Q4: How does temperature affect HPMC’s performance?
Temperature significantly affects HPMC. HPMC solutions thicken as temperature decreases. They can form a gel when heated above a certain temperature. This is known as thermal gelation. - Q5: What are the typical dosage levels of HPMC in industrial applications?
Dosage levels vary widely. They depend on the specific application and desired effect. In construction, it can be 0.1% to 0.5% of dry mix weight. In pharmaceuticals, it can be 1% to 10% of tablet weight. Always consult product specifications.
tal. It ensures optimal product performance. Several factors influence this selection. Viscosity is a primary consideration. It determines the thickening power. For example, a low viscosity grade works for thin film coatings. A high viscosity grade is better for thick mortars. The substitution type also matters. This refers to the ratio of methyl to hydroxypropyl groups. It affects solubility and gelation temperature. Different substitution types suit different applications.
But here’s the thing… particle size also plays a role. Finer particles dissolve faster. They also disperse more easily. Coarser particles might be better for certain dry mixes. Matching HPMC properties to specific application needs is key. Consider the desired end product characteristics. Think about processing conditions. For instance, a pharmaceutical tablet needs a specific dissolution profile. A construction adhesive needs a certain open time. Testing and validation are essential. Always conduct trials with different HPMC grades. This helps find the best fit. It ensures the HPMC performs as expected. It also helps avoid costly mistakes.
Selection Factor | Impact on HPMC Performance |
---|---|
Viscosity | Thickening power, flow properties |
Substitution Type | Solubility, gelation temperature, film properties |
Particle Size | Dissolution rate, dispersion characteristics |
Purity | Product quality, regulatory compliance |
Application Needs | Desired end product characteristics, processing |
Conclusion
HPMC is a highly versatile polymer. It offers many benefits across diverse industries. We have seen how it improves construction materials. It enhances their workability and durability. In pharmaceuticals, HPMC enables controlled drug release. It also improves tablet integrity. For personal care and food products, it provides essential thickening and stabilizing functions. Its safety profile and regulatory approvals make it a trusted choice. Selecting the right HPMC grade is vital. It ensures optimal product performance for your specific application. This choice impacts product quality and efficiency.
By carefully choosing HPMC, you can achieve superior product outcomes. This leads to better market acceptance and reduced production costs. Morton offers a wide range of HPMC grades. We provide expert guidance to help you select the perfect solution. Contact Morton today to discuss your specific needs. We can help you find the ideal HPMC product. Partner with us to enhance your product formulations.
FAQ
Q1: Is HPMC a natural or synthetic polymer?
HPMC is a semi-synthetic polymer. It is derived from natural cellulose. Cellulose comes from wood pulp or cotton. Chemical modification creates the final HPMC product.
Q2: What is the primary difference between HPMC and other cellulose ethers?
HPMC differs from other cellulose ethers in its substitution groups. It has both methyl and hydroxypropyl groups. This gives it unique properties. These include cold water solubility and thermal gelation.
Q3: Can HPMC be used in organic certified products?
Yes, certain grades of HPMC can be used in organic certified products. This depends on the specific certification standards. Always check with the certifying body.
Q4: How does temperature affect HPMC’s performance?
Temperature significantly affects HPMC. HPMC solutions thicken as temperature decreases. They can form a gel when heated above a certain temperature. This is known as thermal gelation.
Q5: What are the typical dosage levels of HPMC in industrial applications?
Dosage levels vary widely. They depend on the specific application and desired effect. In construction, it can be 0.1% to 0.5% of dry mix weight. In pharmaceuticals, it can be 1% to 10% of tablet weight. Always consult product specifications.