Hydroxypropyl methylcellulose (HPMC) is a versatile polymer. It is used across many industries. However, understanding its complex structure can be a challenge. This lack of clarity often leads to suboptimal product performance. It also causes wasted resources and missed market opportunities. A deep understanding of HPMC structure is vital. It helps you unlock its full potential. This article will explain HPMC, its properties, applications, and how its structure impacts product quality.
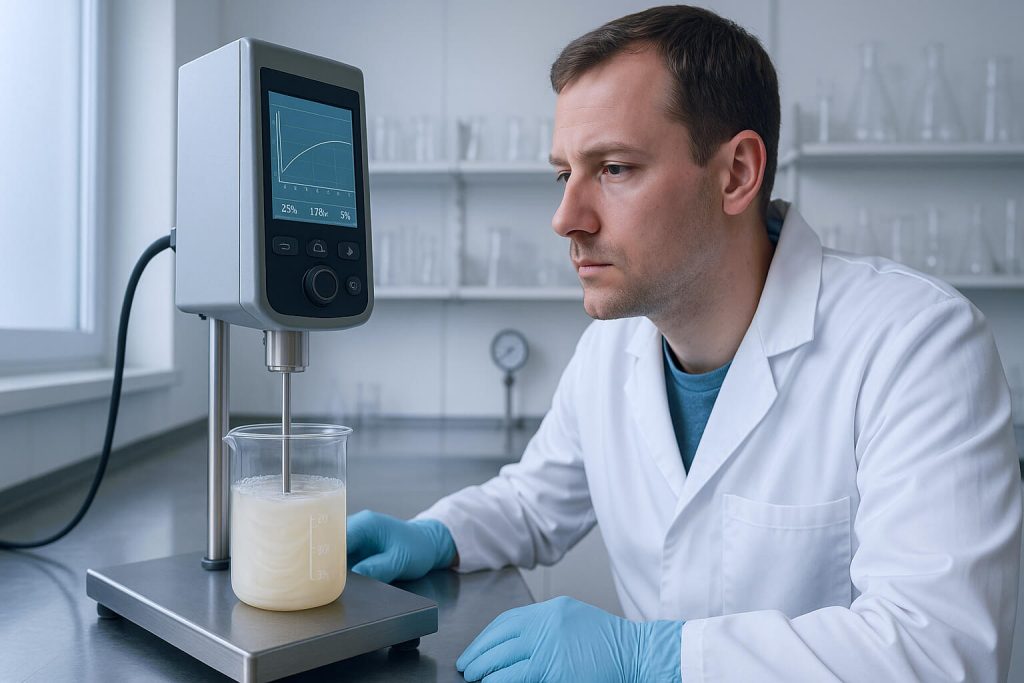
1. What is HPMC and how is it made?
HPMC is a cellulose ether. It is derived from cellulose, a natural polymer. Cellulose comes from wood pulp or cotton. HPMC is made by chemically modifying cellulose. This modification involves adding hydroxypropyl and methoxy groups. These groups change cellulose’s properties. They make it soluble in water. They also give it unique thickening and film-forming abilities. Here’s why it matters… These changes are key to its wide use.
The production process starts with cellulose. It is treated with sodium hydroxide. This creates alkali cellulose. Then, propylene oxide and methyl chloride are added. These react with the alkali cellulose. This reaction forms HPMC. The final product is purified. It is then dried and milled into a powder. This powder is ready for various applications.
Component | Source | Role in HPMC Production |
---|---|---|
Cellulose | Wood pulp, cotton | Primary raw material |
Sodium Hydroxide | Chemical | Activates cellulose |
Propylene Oxide | Chemical | Introduces hydroxypropyl groups |
Methyl Chloride | Chemical | Introduces methoxy groups |
HPMC has several key properties. It is water-soluble. It forms clear solutions. It is also non-toxic and non-ionic. These features make it suitable for many uses. It acts as a thickener. It also works as a binder. It can form films. It helps retain water. These properties are critical for its performance in different products.
2. How do HPMC properties impact its applications?
HPMC properties directly affect its performance. Viscosity is a key property. It measures a fluid’s resistance to flow. In HPMC, viscosity depends on molecular weight. Higher molecular weight means higher viscosity. This property is vital in many uses. For example, in paints, it controls flow. In pharmaceuticals, it affects drug release. But here’s the thing… controlling viscosity is crucial for product consistency.
Gelation temperature is another important property. This is the temperature at which HPMC solutions form a gel. It is influenced by the degree of substitution. Different HPMC grades have different gelation temperatures. This property is important for hot-melt applications. It also matters for sustained-release drug formulations. Knowing this temperature helps in product design.
Property | Description | Impact on Application |
---|---|---|
Viscosity | Resistance to flow | Controls thickness, flow, and spreadability |
Gelation Temperature | Temperature at which gel forms | Affects thermal stability and release profiles |
Water Retention | Ability to hold water | Prevents drying, improves workability |
Water retention is a critical function of HPMC. It can absorb and hold large amounts of water. This prevents premature drying. In construction, it extends working time. It also improves hydration of cement. In cosmetics, it keeps products from drying out. This property also helps in film formation. It creates a protective barrier. This barrier can reduce moisture loss.
3. What are the common uses of HPMC in various industries?
HPMC finds wide use across many industries. In pharmaceuticals, it serves multiple roles. It acts as a binder in tablets. It helps hold ingredients together. It also functions as a film-forming agent for tablet coatings. These coatings protect the drug. They also help with controlled release. HPMC is key for sustained-release formulations. It slows down drug release. This provides a longer therapeutic effect. Now, you might be wondering… how does one material do so much?
In construction, HPMC improves material performance. It is used in mortars. It enhances workability. It also prevents water loss. This leads to stronger, more durable structures. In tile adhesives, HPMC provides better adhesion. It also extends open time. This allows for easier installation. It is also found in renders. It improves consistency and crack resistance.
Industry | Common Applications | Benefits of HPMC |
---|---|---|
Pharmaceuticals | Tablet binders, coatings, sustained release | Controlled drug release, improved stability |
Construction | Mortars, tile adhesives, renders | Enhanced workability, increased adhesion |
Food | Thickeners, stabilizers, emulsifiers | Improved texture, extended shelf life |
Cosmetics | Creams, lotions, shampoos | Thickening, film-forming, moisturizing |
The food industry uses HPMC as a thickener. It stabilizes emulsions. It also improves texture in many products. Examples include sauces, dressings, and dairy items. In cosmetics and personal care, HPMC is a common ingredient. It thickens creams and lotions. It also forms films in shampoos and hair sprays. This provides a smooth feel. It also helps with product delivery.
4. How does HPMC structure influence its performance?
The structure of HPMC directly impacts its performance. The degree of substitution (DS) is a key structural feature. It refers to the average number of hydroxyl groups replaced by methoxy or hydroxypropyl groups. A higher DS means more substituted groups. This affects solubility and gelation temperature. For example, higher methoxy DS leads to lower gelation temperature. Let me explain… this directly influences how HPMC behaves in different solutions.
Molecular weight (MW) is another critical structural factor. It determines the length of the polymer chain. Higher MW HPMC has longer chains. This results in higher viscosity in solutions. It also affects film-forming properties. Longer chains create stronger films. The manufacturing process also plays a role. It influences the distribution of substituents along the cellulose backbone. This distribution affects hydration and dissolution rates.
Structural Feature | Description | Impact on Performance |
---|---|---|
Degree of Substitution (DS) | Average number of substituted hydroxyl groups | Affects solubility, gelation temperature, and film properties |
Molecular Weight (MW) | Length of polymer chain | Influences viscosity, film strength, and water retention |
Substituent Distribution | Placement of methoxy/hydroxypropyl groups | Impacts hydration rate and dissolution behavior |
Understanding these structural details is vital. It allows for precise control over HPMC properties. Manufacturers can tailor HPMC grades. They can meet specific application needs. This ensures optimal product performance. It also helps in troubleshooting issues. For instance, if a formulation is too thick, adjusting the HPMC grade based on its MW can solve the problem.
5. What are the different grades of HPMC and their distinctions?
HPMC is available in various grades. These grades are distinguished by their properties. Viscosity is a primary classification method. Low viscosity grades are used for coatings. They provide good film formation. Medium viscosity grades are common in construction. They offer good workability. High viscosity grades are used as thickeners. They create very viscous solutions. This is important because… choosing the right viscosity grade is critical for product success.
Another classification is by substitution type. This refers to the ratio of methoxy to hydroxypropyl groups. Different ratios lead to different properties. For example, some grades are more hydrophilic. They dissolve faster in water. Others are more hydrophobic. They have better film-forming properties. These distinctions allow for precise application matching.
HPMC Grade Type | Typical Viscosity Range (mPa·s) | Common Applications |
---|---|---|
Low Viscosity | 3 – 50 | Tablet coatings, thin films, paints |
Medium Viscosity | 100 – 4,000 | Mortars, tile adhesives, self-leveling compounds |
High Viscosity | 5,000 – 200,000 | Thickeners for food, pharmaceuticals, personal care |
Selecting the right HPMC grade is essential. It depends on the specific application. Consider the desired viscosity. Think about the required gelation temperature. Also, consider water retention needs. A careful selection ensures optimal product performance. It also helps in achieving desired processing characteristics. Always consult technical data sheets. These sheets provide detailed information on each grade.
6. How can HPMC improve product quality and efficiency?
HPMC significantly improves product quality and efficiency. In construction, it enhances workability. Mortars become easier to mix and apply. This leads to smoother finishes. It also improves consistency. Batches of material behave similarly. This reduces errors on site. It also saves time and labor. Want to know the secret? It is HPMC’s ability to control water movement.
It also improves adhesion and strength. In tile adhesives, HPMC creates a stronger bond. This reduces tile detachment. In renders, it minimizes cracking. This leads to more durable surfaces. HPMC also extends shelf life. In food products, it acts as a stabilizer. It prevents separation. This keeps products fresh longer. In pharmaceuticals, it protects active ingredients. This maintains drug efficacy over time.
Product Quality Improvement | Mechanism | Benefit |
---|---|---|
Enhanced Workability | Controls water, improves flow | Easier application, smoother finish |
Improved Adhesion | Forms strong bonds | Reduced detachment, increased durability |
Extended Shelf Life | Stabilizes, protects ingredients | Maintained freshness, sustained efficacy |
Efficiency gains are also notable. Faster application times are possible. Less material waste occurs. Consistent product performance means fewer reworks. These factors all contribute to cost savings. They also lead to higher customer satisfaction. HPMC is a small addition. Yet, it yields big results in product performance.
7. What are the quality control measures for HPMC?
Quality control for HPMC is crucial. It ensures consistent product performance. Testing methods verify purity and consistency. These tests include viscosity measurements. They also check moisture content. Ash content and pH are also tested. These measures ensure HPMC meets specifications. They prevent variations in final products. The bottom line? Strict quality control means reliable HPMC.
Regulatory standards guide HPMC production. These standards vary by industry. For pharmaceuticals, HPMC must meet pharmacopoeial requirements. These include USP, EP, and JP. For food applications, it must be food-grade. This means it meets FDA or EFSA standards. Compliance with these standards is mandatory. It ensures safety and efficacy.
Quality Control Test | Purpose | Standard |
---|---|---|
Viscosity | Measures flow resistance | Ensures consistent thickening |
Moisture Content | Determines water presence | Affects stability and purity |
Ash Content | Indicates inorganic impurities | Checks purity |
pH | Measures acidity/alkalinity | Affects solubility and stability |
Choosing reliable suppliers is paramount. Reputable suppliers provide quality certificates. They also offer technical support. They ensure traceability of their products. This helps in maintaining product quality. It also aids in regulatory compliance. Partnering with trusted suppliers minimizes risks. It ensures a steady supply of high-quality HPMC.
8. What are the future trends and innovations in HPMC technology?
The field of HPMC technology is always evolving. New applications are constantly emerging. Research focuses on tailoring HPMC for specific needs. For example, in drug delivery, HPMC is being explored for targeted release. This means drugs go directly to where they are needed. In construction, HPMC is being developed for 3D printing. This allows for new building methods. What does this mean for you? It means more specialized and efficient products.
Sustainable production methods are a growing trend. Manufacturers are looking for greener ways to produce HPMC. This includes using renewable resources. It also involves reducing waste. These efforts align with global sustainability goals. They also appeal to environmentally conscious consumers. This focus on sustainability will shape the future of HPMC production.
Trend | Description | Impact |
---|---|---|
Targeted Drug Delivery | HPMC designed for precise drug release | Improved treatment efficacy, reduced side effects |
3D Printing in Construction | HPMC for printable concrete mixes | Faster construction, complex designs |
Sustainable Production | Eco-friendly raw materials and processes | Reduced environmental footprint, market appeal |
Emerging market demands also drive innovation. There is a growing need for natural ingredients. This pushes HPMC manufacturers to ensure their products meet these demands. There is also a demand for high-performance materials. These materials must withstand extreme conditions. HPMC technology will continue to adapt. It will meet these evolving needs. This ensures its continued relevance across industries.
Conclusion
We have explored HPMC, its production, properties, and diverse applications. We also examined how its structure impacts performance. Understanding these aspects is vital for product development. It ensures optimal outcomes. HPMC enhances product quality. It improves efficiency across many sectors. From pharmaceuticals to construction, its benefits are clear. It provides better workability, stronger adhesion, and longer shelf life. This translates to tangible gains for your business. It means more reliable products and reduced operational costs. By leveraging the right HPMC grade, you can achieve superior results. Morton offers a comprehensive range of HPMC solutions. We provide expert guidance to help you select the perfect fit. Partner with Morton today. Let us help you elevate your product performance. We are committed to your success. We provide innovative solutions for your specific needs.
FAQ
Q1: What is the primary function of HPMC in pharmaceuticals?
HPMC primarily functions as a binder, film-forming agent, and sustained-release matrix in pharmaceuticals. It helps hold tablet ingredients together, coats tablets for protection, and controls the release of active drug ingredients over time.
Q2: How does HPMC contribute to the workability of construction materials?
HPMC improves the workability of construction materials by enhancing water retention and consistency. It prevents premature drying, extends open time, and makes mixtures easier to apply and spread smoothly.
Q3: Can HPMC be used in organic food products?
Yes, certain grades of HPMC are approved for use in food products, including some organic applications, depending on regulatory standards and certifications. Always check specific product certifications and local regulations.
Q4: What is the significance of the degree of substitution in HPMC?
The degree of substitution (DS) in HPMC is significant because it directly influences the polymer’s solubility, gelation temperature, and overall performance characteristics. A higher DS affects how HPMC interacts with water and forms gels.
Q5: How does HPMC’s water retention capacity benefit products?
HPMC’s water retention capacity benefits products by preventing premature drying, improving workability, and enhancing stability. In construction, it ensures proper hydration; in cosmetics, it helps maintain product consistency and texture.