Developing new products often presents complex challenges. You face hurdles like ensuring consistent quality, achieving desired performance, and meeting strict regulatory standards. These issues can lead to costly delays, wasted resources, and missed market opportunities if not addressed effectively. A reliable solution is needed to overcome these obstacles and streamline your development process. This article explores the structure, functions, and diverse applications of HPMC E15, providing insights into its role in various industries. We will examine how this versatile polymer can enhance your product formulations.
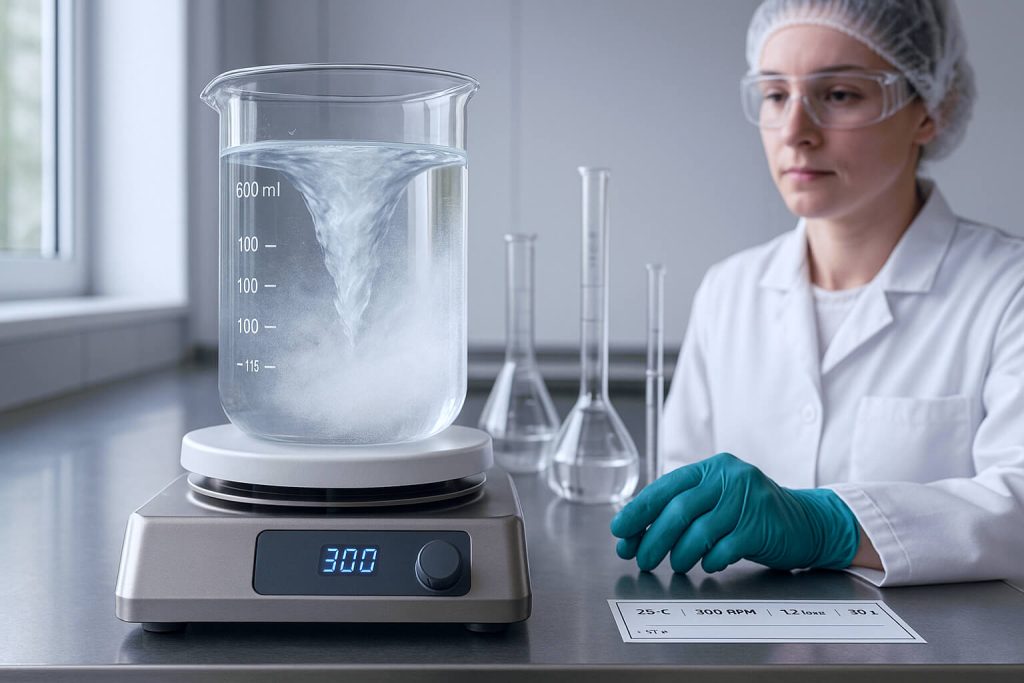
1. What is HPMC E15 and why is it important?
HPMC E15 stands for Hydroxypropyl Methylcellulose, a versatile polymer. It derives from cellulose, a natural plant fiber. This compound is a non-ionic, water-soluble ether. It finds use in many industries.
Its chemical structure includes methoxyl and hydroxypropoxyl groups. These groups replace hydroxyls on the cellulose backbone. This modification gives HPMC E15 its unique properties. Here’s why it matters… It offers excellent film-forming abilities. It also provides good water retention. This makes it highly valuable in diverse applications.
Property | Description |
---|---|
Chemical Type | Non-ionic cellulose ether |
Solubility | Water-soluble |
Origin | Plant-derived (cellulose) |
Key Groups | Methoxyl, Hydroxypropoxyl |
HPMC E15 is crucial for product stability and performance. It acts as a thickener, binder, and emulsifier. Its ability to form clear films is also important. These functions make it indispensable. It helps in creating high-quality products. This polymer ensures consistent results. It meets strict industry standards.
2. How does HPMC E15’s structure affect its properties?
The molecular structure of HPMC E15 directly influences its functional properties. The degree of substitution (DS) of methoxyl and hydroxypropoxyl groups plays a key role. This DS determines the polymer’s solubility and thermal gelation temperature. A higher DS often leads to better solubility.
Molecular weight also impacts viscosity. Higher molecular weight HPMC E15 yields higher viscosity solutions. This relationship is crucial for thickening applications. The distribution of these substituent groups along the cellulose chain also matters. It affects how the polymer interacts with water. But here’s the thing… This interaction dictates its performance in various formulations.
Structural Feature | Impact on Properties |
---|---|
Degree of Substitution | Solubility, Thermal Gelation |
Molecular Weight | Solution Viscosity |
Substituent Distribution | Water Interaction, Performance |
Understanding these structural aspects helps in selecting the right HPMC E15 grade. Different applications require specific property profiles. For example, a high-viscosity grade suits thickeners. A low-viscosity grade works for film coatings. Precise control over these structural elements allows for tailored product development.
3. What are the primary functions of HPMC E15 in various applications?
HPMC E15 performs several critical functions across diverse applications. Its primary role is as a thickening agent. It increases the viscosity of solutions. This property is vital in many liquid and semi-solid formulations. It provides desired consistency and texture.
It also acts as an effective binder. It holds particles together in solid formulations. This is particularly useful in tablets and construction materials. HPMC E15 improves the structural integrity of products. It prevents them from crumbling. Let me explain… Its film-forming capabilities are also significant. It creates strong, flexible films. These films protect surfaces and control release rates.
Function | Description |
---|---|
Thickening | Increases viscosity of liquids |
Binding | Holds particles together in solids |
Film-forming | Creates protective, flexible films |
Water Retention | Prevents moisture loss |
Emulsification | Stabilizes oil-in-water mixtures |
Water retention is another key function. HPMC E15 prevents moisture loss in various products. This extends shelf life and maintains product quality. It also functions as an emulsifier. It helps stabilize mixtures of immiscible liquids. This ensures uniform distribution of ingredients. These combined functions make HPMC E15 a highly versatile additive.
4. Where is HPMC E15 commonly used in different industries?
HPMC E15 finds widespread use across many industries. In pharmaceuticals, it serves as a crucial excipient. It helps in tablet formulation and controlled drug release. Its inert nature makes it safe for medical applications.
Construction materials also benefit from HPMC E15. It improves workability and adhesion in mortars and renders. It enhances water retention in cement-based products. This leads to stronger, more durable structures. Want to know the secret? It helps prevent premature drying.
Industry | Primary Applications |
---|---|
Pharmaceuticals | Tablet binders, film coatings, controlled release |
Construction | Mortars, renders, tile adhesives, self-leveling compounds |
Food | Thickener, stabilizer, emulsifier in various products |
Cosmetics | Thickeners, film formers, emulsifiers in personal care |
In the food industry, HPMC E15 acts as a thickener and stabilizer. It improves texture in dairy products and baked goods. It also extends shelf life. Cosmetics and personal care products use it for thickening and film-forming. It creates smooth textures in lotions and shampoos. This broad applicability highlights its versatility.
5. How does HPMC E15 perform in pharmaceutical formulations?
In pharmaceuticals, HPMC E15 is a key excipient. It plays multiple roles in tablet manufacturing. It acts as a binder, ensuring tablet integrity. It also influences disintegration and dissolution rates. This helps control drug release.
For controlled release, HPMC E15 forms a gel layer around the tablet. This layer regulates water penetration. It slows down drug diffusion. This allows for sustained drug delivery. The best part? It can be tailored for different release profiles.
Role in Pharmaceuticals | Description |
---|---|
Tablet Binder | Ensures tablet cohesion and strength |
Controlled Release | Forms gel layer to regulate drug diffusion |
Film Coating | Provides protection and aesthetic appeal |
Suspension Stabilizer | Prevents particle settling in liquid formulations |
Film coating is another vital application. HPMC E15 creates smooth, durable coatings. These coatings protect the active ingredients. They also improve patient compliance. In liquid formulations, it stabilizes suspensions and emulsions. It prevents particle settling and phase separation. This ensures uniform dosage and product stability.
6. What are the key considerations for using HPMC E15 in construction materials?
Using HPMC E15 in construction materials requires careful consideration. It significantly impacts workability. It improves the spread and flow of mortars. This makes application easier for workers. It also enhances adhesion to various substrates.
Water retention is another critical factor. HPMC E15 prevents rapid water loss from cement mixes. This allows for proper hydration of cement. It leads to stronger, more durable concrete and mortar. This is important because… it reduces cracking and improves overall performance.
Consideration | Impact of HPMC E15 |
---|---|
Workability | Improves spread and flow of mixes |
Adhesion | Enhances bonding to substrates |
Water Retention | Prevents premature drying, aids hydration |
Setting Time | Can influence initial and final set times |
Strength Development | Contributes to higher compressive strength |
HPMC E15 also influences setting time. It can slightly retard the initial set. This provides more time for application. However, it does not negatively affect final strength development. It contributes to higher compressive and flexural strengths. Proper dosage is key to achieving desired properties without adverse effects.
7. How does HPMC E15 contribute to food product quality and stability?
HPMC E15 plays a significant role in enhancing food product quality. It acts as a thickener, stabilizer, and emulsifier. In dairy products, it improves texture and prevents syneresis. It gives a creamy mouthfeel to yogurts and desserts.
In baked goods, it improves dough handling and crumb structure. It also extends freshness. For sauces and dressings, it provides desired consistency. It prevents separation of ingredients. Now, you might be wondering… How does it achieve all this?
Food Application | Contribution of HPMC E15 |
---|---|
Dairy Products | Texture improvement, syneresis prevention |
Baked Goods | Dough workability, crumb structure, freshness |
Sauces/Dressings | Consistency, emulsion stability |
Frozen Foods | Ice crystal control, texture retention |
Confectionery | Gelling, texture modification |
HPMC E15 controls ice crystal formation in frozen foods. This maintains texture during freezing and thawing cycles. It also helps in reducing fat content in some products. It provides a fat-like mouthfeel. Its ability to form gels upon heating and revert to liquid upon cooling is also useful. This property is valuable in many food processing applications.
8. What are the safety and regulatory aspects of HPMC E15?
HPMC E15 is widely recognized as safe for use in various applications. Regulatory bodies worldwide have approved its use. The U.S. Food and Drug Administration (FDA) lists it as Generally Recognized As Safe (GRAS). This designation confirms its safety for food use.
Handling HPMC E15 requires standard industrial hygiene practices. It is a non-toxic, non-irritating powder. Proper ventilation and dust control are advisable during handling. Storage should be in a cool, dry place. Here’s the deal… This prevents moisture absorption and maintains product quality.
Aspect | Detail |
---|---|
Regulatory Status | FDA GRAS, EU approved |
Toxicity | Non-toxic |
Irritation | Non-irritating |
Handling | Standard industrial hygiene |
Storage | Cool, dry place |
Environmentally, HPMC E15 is biodegradable. It poses no significant environmental hazard. Its production process is also relatively sustainable. This makes it an attractive choice for eco-conscious manufacturers. Compliance with local and international regulations is always necessary. This ensures safe and responsible use in all applications.
9. How can you optimize HPMC E15 selection for specific product needs?
Optimizing HPMC E15 selection involves several key steps. First, consider the desired viscosity of your final product. HPMC E15 comes in various viscosity grades. Matching the grade to your application is crucial. A higher viscosity grade suits thickeners. A lower viscosity grade works for film coatings.
Next, determine the optimal concentration level. This depends on the desired effect and other ingredients. Too little may not provide the intended function. Too much can lead to undesirable textures or processing issues. What does this mean for you? Careful experimentation is often needed.
Optimization Factor | Description |
---|---|
Viscosity Grade | Match to desired product consistency |
Concentration Level | Determine optimal dosage for function |
Ingredient Compatibility | Check interactions with other components |
Processing Conditions | Consider temperature, pH, shear during mixing |
Compatibility with other ingredients is also vital. HPMC E15 generally works well with many common excipients and additives. However, some interactions can occur. Always test compatibility in your specific formulation. Finally, consider your processing conditions. Temperature, pH, and shear during mixing can all affect HPMC E15 performance. Adjusting these factors can help achieve optimal results.
10. What are the future trends and innovations involving HPMC E15?
The future of HPMC E15 looks promising, with ongoing research and innovation. Emerging applications are constantly being explored. These include advanced drug delivery systems and sustainable packaging materials. There is also a growing interest in its use in 3D printing for medical devices.
Advancements in production methods aim to improve efficiency and reduce environmental impact. New modification techniques are also being developed. These enhance specific functionalities. For example, researchers are creating HPMC variants with improved thermal stability or targeted release profiles. The bottom line? HPMC E15 remains a dynamic material.
Trend/Innovation | Description |
---|---|
Emerging Applications | 3D printing, advanced drug delivery |
Production Advancements | Improved efficiency, reduced environmental impact |
Functional Enhancements | Improved thermal stability, targeted release |
Sustainability Focus | Eco-friendly solutions, biodegradable materials |
Sustainability is a major focus. Manufacturers are seeking greener alternatives. HPMC E15, being plant-derived and biodegradable, fits this trend well. Innovations also include combining HPMC E15 with other polymers. This creates hybrid materials with synergistic properties. These developments ensure HPMC E15 will continue to be a valuable ingredient in many industries.
Conclusion
HPMC E15 is a highly versatile and indispensable polymer. It offers a wide range of functional properties. We have explored its structure, diverse applications, and critical roles in pharmaceuticals, construction, and food. Its ability to thicken, bind, form films, and retain water makes it invaluable across industries. This understanding empowers you to optimize your product formulations. It helps you achieve superior performance and meet market demands. You gain a competitive edge by leveraging its unique characteristics.
To further enhance your product development and ensure optimal performance, partner with Morton. We provide expert guidance and high-quality HPMC E15 solutions tailored to your specific needs. Contact Morton today to discuss how our specialized HPMC E15 products can elevate your formulations and streamline your processes. We are committed to supporting your success.
FAQ
Q1: What is the main difference between HPMC E15 and other HPMC grades?
HPMC E15 has a specific substitution pattern and viscosity range. This differentiates it from other HPMC grades. These differences affect its solubility, gelation temperature, and performance in various applications. Other grades may have different methoxyl and hydroxypropoxyl content. This leads to varied properties.
Q2: Can HPMC E15 be used in organic or natural products?
Yes, HPMC E15 is derived from natural cellulose. It is often considered suitable for organic or natural products. Its plant-based origin aligns with many natural product standards. Always verify specific certification requirements for your product. This ensures full compliance.
Q3: How does temperature affect HPMC E15’s performance?
Temperature significantly affects HPMC E15. It exhibits thermal gelation. This means it forms a gel when heated above a certain temperature. It reverts to a liquid upon cooling. This property is useful in many applications. It allows for controlled release or texture changes.
Q4: What is the typical shelf life of HPMC E15?
The typical shelf life of HPMC E15 is generally two to three years. This applies when stored in its original, unopened packaging. It must be kept in a cool, dry place. Proper storage conditions prevent moisture absorption. This maintains its quality and performance over time.
Q5: Is HPMC E15 safe for human consumption?
Yes, HPMC E15 is safe for human consumption. Regulatory bodies like the FDA have granted it GRAS status. This means Generally Recognized As Safe. It is widely used in food and pharmaceutical products. It serves as a thickener, stabilizer, and binder. Its safety profile is well-established.