HPMC (hydroxypropyl methylcellulose) is a versatile polymer used across many industries. Its solubility is a critical factor for product performance. Improper dissolution leads to poor product quality, wasted materials, and production delays. This can cause significant financial losses and damage to your brand reputation. Understanding and controlling HPMC solubility helps you avoid these costly issues. This article will discuss HPMC, how temperature and pH affect its solubility, methods to improve dissolution, its impact on product performance, common challenges, different grades, testing methods, selection, and stability.
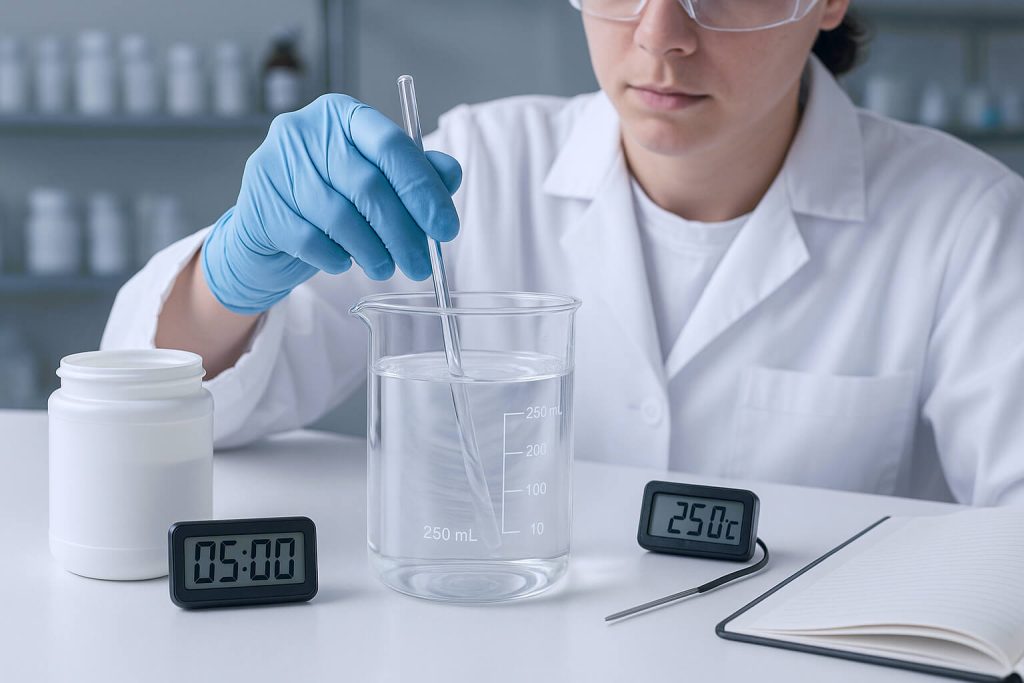
1. What is HPMC and Why is Solubility Important?
HPMC, or hydroxypropyl methylcellulose, is a cellulose ether. It comes from cellulose, a natural polymer found in plant cell walls. Manufacturers chemically modify cellulose to create HPMC. This process makes HPMC soluble in water. The chemical structure of HPMC includes both hydrophilic (water-loving) and hydrophobic (water-fearing) groups. This balance allows it to dissolve and form viscous solutions. Here’s why it matters… HPMC’s unique properties make it valuable in many fields. These include pharmaceuticals, construction, and food. In pharmaceuticals, HPMC acts as a binder, disintegrant, or film-former. In construction, it improves mortar workability and water retention. In food, it serves as a thickener or stabilizer. Proper solubility ensures HPMC performs its intended function. If HPMC does not dissolve correctly, product quality suffers. This can lead to inconsistent batches and failed products. Understanding HPMC solubility is key to successful product development.
Property | Description |
---|---|
Water Solubility | Dissolves in cold water to form clear, viscous solutions. |
Film-Forming | Forms strong, flexible films upon drying. |
Thermal Gelation | Gels when heated above a certain temperature. |
Non-Ionic | Does not carry an electrical charge, making it compatible with many ingredients. |
Biocompatible | Safe for use in pharmaceutical and food applications. |
2. How Do Temperature and pH Impact HPMC Solubility?
Temperature significantly affects HPMC dissolution. HPMC dissolves best in cold water. As water temperature rises, HPMC molecules hydrate slower. Above a certain temperature, HPMC solutions will gel or become turbid. This is known as the cloud point. But here’s the thing… The cloud point is a critical parameter for HPMC. It varies based on the HPMC grade and concentration. Below the cloud point, HPMC remains soluble. Above it, the polymer precipitates. This affects product stability and performance. pH also plays a role in HPMC hydration. HPMC is non-ionic, so its solubility is generally stable across a wide pH range. However, extreme pH values can affect its hydration rate. This is especially true for very acidic or very alkaline conditions. Proper temperature and pH control are vital for consistent HPMC performance.
Factor | Effect on HPMC Solubility |
---|---|
Temperature | |
Cold Water | Faster dissolution, clear solutions |
Warm Water | Slower dissolution, potential for lumping |
Above Cloud Point | Gelation or precipitation |
pH | |
Neutral pH | Stable solubility |
Extreme Acidic pH | Can reduce hydration rate |
Extreme Alkaline pH | Can reduce hydration rate |
3. What Methods Improve HPMC Dissolution?
Achieving proper HPMC dissolution requires specific techniques. Cold water dispersion is a common method. You slowly add HPMC powder to cold water while stirring. This prevents lumping. The HPMC particles hydrate gradually. Another method is the hot water slurry technique. You disperse HPMC in hot water first. This creates a slurry. Then, you add cold water to cool the mixture. This allows the HPMC to dissolve. Want to know the secret? Using wetting agents or co-solvents can also improve dissolution. These additives help the HPMC particles disperse more evenly. Mechanical agitation is also important. High-shear mixers can break up lumps. They help ensure uniform dispersion. Proper mixing speed and duration are key for complete dissolution.
Method | Description | Advantages | Disadvantages |
---|---|---|---|
Cold Water Dispersion | Add HPMC to cold water with stirring. | Prevents lumping, simple. | Can be slow for large batches. |
Hot Water Slurry | Disperse in hot water, then add cold water. | Faster initial dispersion. | Requires temperature control. |
Wetting Agents | Additives that aid dispersion. | Improves uniformity. | Adds cost, potential compatibility issues. |
Mechanical Agitation | Use high-shear mixers. | Breaks lumps, speeds dissolution. | Requires specialized equipment. |
4. How Does HPMC Solubility Affect Product Performance?
HPMC solubility directly impacts product performance. In many applications, HPMC acts as a thickener. Its dissolution determines the final viscosity of a solution. This is crucial for rheology control. For example, in paints, proper viscosity ensures smooth application. In pharmaceuticals, HPMC forms films for tablet coatings. Its solubility affects the film’s integrity and release properties. This is important because… HPMC also plays a role in controlled release drug delivery. The rate at which HPMC dissolves dictates how quickly a drug is released. In construction, HPMC improves water retention in mortars. This affects workability and strength. In all these cases, consistent HPMC solubility means consistent product performance. Inconsistent solubility leads to unpredictable results. This impacts product quality and user satisfaction.
Application | Impact of HPMC Solubility |
---|---|
Pharmaceuticals | |
Tablet Coatings | Film integrity, drug release profile |
Controlled Release | Drug release rate, dissolution kinetics |
Construction | |
Mortars/Renders | Water retention, workability, adhesion |
Tile Adhesives | Open time, sag resistance |
Food | |
Sauces/Dressings | Viscosity, texture, stability |
Baked Goods | Moisture retention, crumb structure |
5. What Are Common Challenges with HPMC Solubility?
Manufacturers often face challenges with HPMC solubility. One common issue is the formation of lumps. These lumps, sometimes called “fish eyes,” occur when HPMC particles hydrate too quickly on the surface. This creates a barrier. It prevents water from reaching the inner particles. This results in incomplete dissolution. Incomplete dissolution leads to inconsistent product quality. It can affect viscosity, clarity, and overall performance. Now, you might be wondering… Variability between HPMC batches also presents a challenge. Even from the same supplier, slight differences can exist. These differences can impact dissolution rates. Proper storage conditions are also vital. HPMC is hygroscopic. It absorbs moisture from the air. High humidity can cause pre-hydration. This makes dissolution more difficult. Always store HPMC in a cool, dry place. This helps maintain its solubility characteristics.
Challenge | Description | Impact on Product |
---|---|---|
Lumping/Fish Eyes | Surface hydration prevents full dissolution. | Inconsistent viscosity, poor clarity. |
Incomplete Dissolution | Not all HPMC dissolves. | Reduced performance, material waste. |
Batch Variability | Differences between HPMC lots. | Inconsistent product quality. |
Improper Storage | Moisture absorption. | Reduced solubility, lumping. |
6. How Do Different HPMC Grades Influence Solubility?
HPMC comes in various grades. These grades differ in molecular weight and degree of substitution. Molecular weight affects dissolution rate. Higher molecular weight HPMC dissolves slower. It also produces higher viscosity solutions. The degree of substitution refers to the number of hydroxypropyl and methoxy groups. These groups replace hydroxyl groups on the cellulose backbone. This affects the polymer’s hydrophilicity. It also impacts its interaction with water. Let me explain… Different degrees of substitution lead to different cloud points. They also affect solubility in various solvents. Viscosity grades are also important. These indicate the viscosity of a 2% solution at a specific temperature. A higher viscosity grade means a higher molecular weight. This generally means slower dissolution. Selecting the correct HPMC grade is vital. It must match the specific requirements of your application. This ensures optimal performance and consistent results.
HPMC Property | Impact on Solubility |
---|---|
Molecular Weight | Higher molecular weight = slower dissolution, higher viscosity. |
Degree of Substitution | Affects hydrophilicity, cloud point, and solvent interaction. |
Viscosity Grade | Higher grade = higher molecular weight, generally slower dissolution. |
7. What Testing Methods Verify HPMC Solubility?
Verifying HPMC solubility is crucial for quality control. Several testing methods help assess dissolution. Viscosity measurement is a primary method. You prepare an HPMC solution. Then, you measure its viscosity using a viscometer. This indicates the extent of dissolution. Higher viscosity suggests better dissolution. Turbidity and clarity assessments also provide insights. A fully dissolved HPMC solution should be clear. Any haziness or particles indicate incomplete dissolution. Particle size analysis of dissolved solutions can also be useful. This confirms the absence of undissolved HPMC particles. The bottom line? Dissolution rate testing measures how quickly HPMC dissolves. This involves monitoring viscosity or clarity over time. These tests help ensure consistent HPMC quality. They also confirm that the HPMC meets product specifications. Regular testing helps prevent production issues. It also ensures product performance.
Testing Method | What it Measures | Indication of Good Solubility |
---|---|---|
Viscosity Measurement | Solution thickness/resistance to flow. | Higher viscosity. |
Turbidity/Clarity | Haze or presence of undissolved particles. | Clear solution, low turbidity. |
Particle Size Analysis | Size of particles in solution. | Absence of large undissolved particles. |
Dissolution Rate Testing | Speed of dissolution over time. | Faster, complete dissolution. |
8. How Can You Select the Right HPMC for Your Application?
Selecting the right HPMC grade is a critical decision. It directly impacts your product’s success. You must match HPMC properties to your application requirements. Consider the desired viscosity. Think about the required gelation temperature. Also, consider the film-forming capabilities. Regulatory compliance is another key factor. Ensure the HPMC grade meets all necessary industry standards. This includes certifications for pharmaceutical or food use. Cost-effectiveness is also important. Balance performance with budget constraints. What does this mean for you? Partnering with reliable suppliers is vital. A good supplier provides consistent quality HPMC. They also offer technical support. They can help you choose the best grade. They can also troubleshoot any solubility issues. A thorough evaluation process helps you make an informed decision. This ensures your product performs as expected. It also helps you avoid costly mistakes.
Selection Criteria | Considerations |
---|---|
Application Requirements | Viscosity, gelation temperature, film-forming, water retention. |
Regulatory Compliance | FDA, GMP, food-grade, pharmaceutical-grade certifications. |
Cost-Effectiveness | Balance performance with budget, long-term value. |
Supplier Reliability | Consistent quality, technical support, supply chain stability. |
9. How Does HPMC Solubility Relate to Product Stability?
HPMC solubility plays a direct role in product stability. Once HPMC dissolves, it forms a stable solution. This solution helps maintain the integrity of your product over time. For example, in liquid formulations, HPMC prevents settling of particles. It also maintains uniform consistency. Long-term stability of HPMC solutions is crucial. Changes in viscosity or clarity can indicate instability. These changes might be due to degradation or microbial growth. Preventing microbial growth in HPMC formulations is important. HPMC itself does not support microbial growth. However, it can provide a medium if contaminants are present. Proper preservation techniques are necessary. Here’s the deal… HPMC also impacts the shelf life of finished products. A stable HPMC solution contributes to a longer shelf life. This means your product remains effective and appealing for a longer period. Storage recommendations for HPMC-containing products are vital. Store them in cool, dry conditions. Protect them from direct sunlight. This helps maintain the HPMC solution’s stability. It also ensures the overall product quality.
Aspect | Impact of HPMC Solubility on Stability |
---|---|
Solution Integrity | Prevents particle settling, maintains consistency. |
Microbial Growth | HPMC does not support growth, but formulations need preservation. |
Shelf Life | Stable HPMC solutions contribute to longer product shelf life. |
Storage Conditions | Proper storage maintains HPMC solution stability. |
Conclusion
Understanding HPMC solubility is fundamental for product success. We have explored its definition, the impact of temperature and pH, and methods to improve dissolution. We also discussed how solubility affects product performance, common challenges, and the influence of different HPMC grades. Finally, we covered testing methods, selection criteria, and the relationship between HPMC solubility and product stability. Mastering these aspects leads to consistent quality and reliable performance. This knowledge helps you avoid costly production issues and ensures your products meet market demands. For expert guidance and high-quality HPMC solutions, contact Morton today. We help you optimize your formulations and achieve superior results.
FAQ
Q1: What is the primary factor affecting HPMC solubility?
Temperature is a primary factor. HPMC dissolves more readily in cold water and forms a gel as temperature rises.
Q2: Can HPMC dissolve in organic solvents?
HPMC is primarily water-soluble. It shows limited solubility or swelling in some polar organic solvents, but water is its main solvent.
Q3: How does HPMC molecular weight impact its solubility?
Higher molecular weight HPMC grades generally dissolve slower and produce higher viscosity solutions compared to lower molecular weight grades.
Q4: What is the ‘cloud point’ of HPMC?
The cloud point is the temperature at which an HPMC solution becomes turbid or cloudy due to polymer precipitation, indicating reduced solubility.
Q5: Why is proper HPMC dissolution important for pharmaceutical products?
Proper dissolution ensures uniform distribution of active ingredients, consistent drug release, and predictable product performance and stability.