Choosing the right cellulose ether for industrial applications presents a common challenge. Many businesses struggle to differentiate between Hydroxypropyl Methylcellulose (HPMC) and Methylcellulose (MC), leading to suboptimal product performance or increased costs. Misapplication can result in poor binding, inadequate water retention, or unstable formulations, directly impacting product quality and manufacturing efficiency. This article clarifies the distinct properties and applications of HPMC and MC. We will help you make informed decisions for your specific industrial needs.
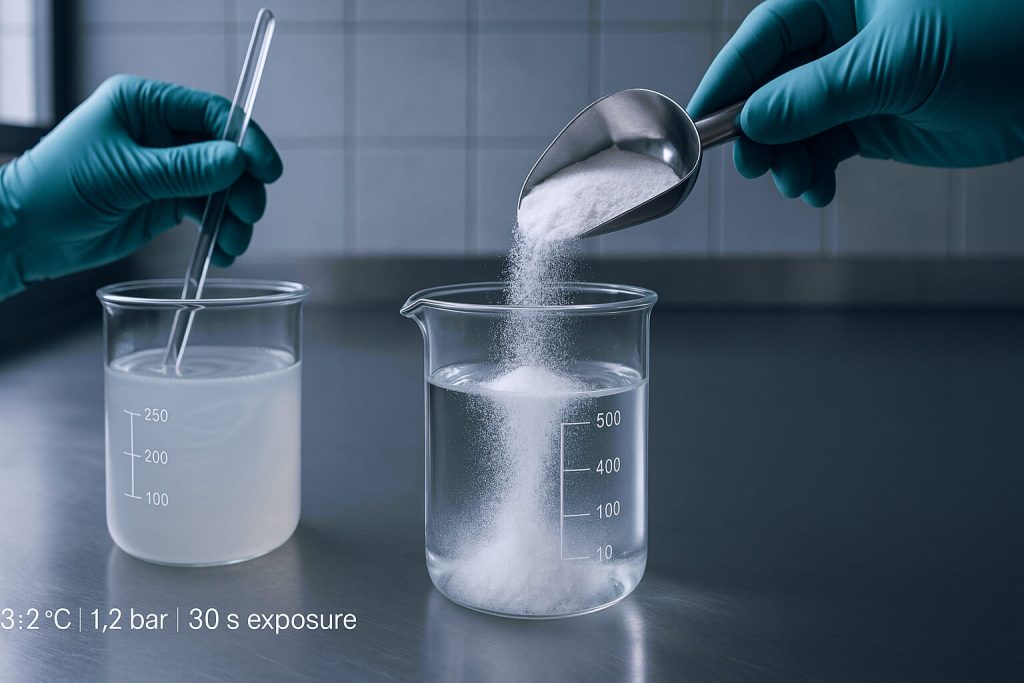
1. What are HPMC and MC, and how do they differ chemically?
HPMC and MC are both cellulose ethers. They come from cellulose, a natural polymer found in plant cell walls. Cellulose itself is a long chain of glucose units. Chemical processes change cellulose into these useful derivatives. This makes them soluble in water.
Methylcellulose (MC) is a simple cellulose ether. Manufacturers create it by reacting cellulose with methyl chloride. This adds methoxy groups to the cellulose backbone. The degree of substitution impacts its properties. Here’s why it matters… These methoxy groups give MC its unique characteristics. It forms a gel when heated.
Hydroxypropyl Methylcellulose (HPMC) is more complex. It has both methoxy and hydroxypropyl groups. Manufacturers add propylene oxide during its creation. This dual substitution gives HPMC different properties. It offers broader application possibilities.
This table shows their basic chemical differences:
Feature | Methylcellulose (MC) | Hydroxypropyl Methylcellulose (HPMC) |
---|---|---|
Chemical Groups | Methoxy groups | Methoxy and hydroxypropyl groups |
Substitution | Methylation | Methylation and hydroxypropylation |
Source | Cellulose | Cellulose |
Structure | Simpler | More complex |
The presence of hydroxypropyl groups in HPMC is key. These groups change how the molecule interacts with water. They also affect its thermal gelation. This leads to differences in solubility and film formation. Understanding these chemical details helps in product selection.
2. How do HPMC and MC behave in water?
Both HPMC and MC are water-soluble. Their behavior in water, however, shows clear differences. These differences impact their use in various products. You must understand these properties.
Methylcellulose dissolves in cold water. It forms a clear solution. When heated, MC solutions gel. This gelling is reversible. It turns back into a solution upon cooling. This unique thermal gelation makes MC useful in many food products. Now, you might be wondering… how does HPMC compare?
HPMC also dissolves in cold water. Its gelation temperature is generally higher than MC. The hydroxypropyl groups reduce the tendency to gel. This provides more flexibility in processing. HPMC solutions also form films. These films are often more flexible and stronger than MC films.
Water retention is another important property. Both HPMC and MC hold water well. This makes them valuable in construction materials. They prevent rapid drying of cement mixes. This allows for better hydration and strength development. HPMC often shows better water retention at higher temperatures.
Here is a comparison of their water behavior:
Property | Methylcellulose (MC) | Hydroxypropyl Methylcellulose (HPMC) |
---|---|---|
Cold Water Solubility | Soluble | Soluble |
Thermal Gelation | Lower temperature | Higher temperature |
Gelation Reversibility | Reversible | Reversible |
Film Strength | Good | Better |
Water Retention | Good | Very good |
Viscosity also varies. Both HPMC and MC come in different viscosity grades. Higher viscosity grades create thicker solutions. This impacts their use as thickeners or binders. The choice depends on the desired end product consistency.
3. Where does HPMC find its main uses?
HPMC is a versatile polymer. It finds use across many industries. Its unique properties make it suitable for diverse applications. These range from pharmaceuticals to construction.
In pharmaceuticals, HPMC acts as a binder. It helps hold tablets together. It also works as a film-forming agent for coatings. HPMC is also key in controlled-release formulations. It allows drugs to release slowly over time. This improves patient compliance. This is important because… it directly impacts drug effectiveness and safety.
Construction is another major area. HPMC improves workability of cement-based products. It enhances water retention in tile adhesives. It also helps in renders and self-leveling compounds. This leads to stronger, more durable building materials. It prevents premature drying.
The food industry uses HPMC as a thickener. It also serves as an emulsifier and stabilizer. You find it in many processed foods. It improves texture and shelf life. In personal care, HPMC is in shampoos and lotions. It provides thickening and film-forming properties. This enhances product feel.
Here are some common applications for HPMC:
Industry | Specific Use | Benefit |
---|---|---|
Pharmaceuticals | Tablet binder, film coating | Improved drug delivery, stability |
Construction | Tile adhesive, renders | Enhanced workability, water retention |
Food | Thickener, emulsifier | Better texture, extended shelf life |
Personal Care | Shampoos, lotions | Thickening, improved feel |
Paints & Coatings | Thickener, rheology modifier | Better application, stability |
HPMC’s ability to form strong films is a big advantage. These films are flexible. They protect surfaces and encapsulate ingredients. This broadens its utility. Its thermal stability also makes it suitable for high-temperature processes.
4. What are the primary applications for MC?
Methylcellulose (MC) also has a wide range of uses. Its unique thermal gelation property makes it stand out. This means it gels when heated and melts when cooled. This makes it very useful in certain food applications.
In the food industry, MC is popular for meat alternatives. It provides a meat-like texture when cooked. It also helps bind ingredients in baked goods. In frozen desserts, MC prevents ice crystal formation. This keeps products smooth. The best part? It offers a clean label solution for many food manufacturers.
Construction materials also use MC. It improves the workability of mortars. It enhances adhesion in plasters. MC helps prevent cracking. It also extends the open time of cement mixes. This gives workers more time to apply the material. It ensures a stronger bond.
MC acts as an adhesive and binder. It is used in paper and textile industries. It provides strength and flexibility. It also helps in ceramics and glazes. MC improves the green strength of ceramic bodies. This reduces breakage during handling. It also helps glazes adhere evenly.
Here are key applications for Methylcellulose:
Industry | Specific Use | Benefit |
---|---|---|
Food | Meat alternatives, baked goods | Texture improvement, binding |
Construction | Mortars, plasters | Workability, crack prevention |
Adhesives | Paper, textiles | Strength, flexibility |
Ceramics | Green strength, glazes | Reduced breakage, even coating |
Pharmaceuticals | Tablet disintegration | Controlled release |
MC is also used in some pharmaceutical applications. It can act as a disintegrant in tablets. This helps the tablet break apart quickly. This releases the active ingredient. Its simpler chemical structure can be an advantage. It offers consistent performance in specific formulations.
5. How do you choose between HPMC and MC for your project?
Selecting between HPMC and MC depends on your specific project needs. Several factors guide this decision. You must consider performance, cost, and regulatory compliance. Each choice impacts your final product.
First, assess the required properties. Do you need high thermal stability? HPMC might be better. Is strong gelation at lower temperatures important? MC could be the answer. Consider water retention needs. HPMC often excels here. Also, think about adhesion. Both offer good adhesion, but HPMC can be more versatile. What does this mean for you? It means matching the polymer to the exact function.
Compatibility with other ingredients is also vital. Some formulations work better with one over the other. Test both options if unsure. Processing conditions play a role. High-temperature processes might favor HPMC. Simpler processes might allow for MC.
Finally, consider the target application environment. Is it a food product? Both are food-grade, but their functional differences matter. Is it a pharmaceutical product? HPMC is widely used. Construction applications can use either, depending on the specific mortar or adhesive.
Here is a decision-making guide:
Factor | Consider HPMC if… | Consider MC if… |
---|---|---|
Thermal Stability | High temperatures are involved | Lower temperatures are sufficient |
Gelation | Higher gelation temperature needed | Strong gelation at lower temperatures |
Film Properties | Flexible, strong films are required | Basic film properties are enough |
Cost | Performance justifies higher cost | Cost-effectiveness is a priority |
Regulatory | Broad pharmaceutical acceptance | Specific food applications |
Always review product specifications. Suppliers provide detailed data sheets. These sheets list viscosity, gelation temperature, and substitution types. This information helps make an informed choice.
6. What are the performance benefits of HPMC over MC?
HPMC offers several performance advantages over MC. These benefits often justify its use in more demanding applications. Understanding these can help you optimize your product formulations.
One key benefit is enhanced thermal stability. HPMC maintains its properties better at higher temperatures. This is crucial in processes involving heat. It also provides improved film flexibility and strength. HPMC films are less brittle. They offer better protection and adhesion. Let me explain… this means HPMC can perform where MC might fail.
HPMC also shows better compatibility with various additives. Its chemical structure allows for broader formulation possibilities. This makes it easier to combine with other ingredients. It offers a wider range of substitution types. This allows for fine-tuning of properties. You can tailor HPMC to specific needs.
In pharmaceuticals, HPMC excels in controlled-release systems. Its consistent performance ensures accurate drug delivery. This is a significant advantage. In construction, HPMC provides superior water retention. This is especially true in hot climates. It helps prevent premature drying of cement mixes.
Here is a summary of HPMC’s benefits:
Benefit | Description | Impact |
---|---|---|
Thermal Stability | Maintains properties at high heat | Reliable performance in hot processes |
Film Flexibility | Less brittle films | Better protection, durability |
Additive Compatibility | Mixes well with many substances | Broader formulation options |
Substitution Range | Customizable properties | Tailored solutions for specific needs |
Water Retention | Holds water effectively | Prevents premature drying in construction |
These benefits make HPMC a preferred choice. It is used in applications where performance is critical. Its versatility allows for innovation in product development. It helps create more robust and reliable products.
7. When might MC be a better choice than HPMC?
While HPMC offers many advantages, Methylcellulose (MC) remains a strong contender. There are specific scenarios where MC is the preferred option. Its unique characteristics make it ideal for certain applications.
Cost-effectiveness is a major factor. MC is generally less expensive than HPMC. For applications where cost is a primary concern, MC can provide a viable solution. This is true if its performance meets the requirements. Its simpler chemical structure can also be an advantage. This leads to more straightforward processing in some cases. Want to know the secret? Sometimes, simpler is better.
MC also exhibits stronger gelation properties at lower temperatures. This is particularly useful in food applications. It creates a firm gel upon heating. This provides structure to products like meat alternatives. HPMC gels at higher temperatures. This makes MC more suitable for specific food processing needs.
Applications requiring high purity or specific rheology might also favor MC. Certain grades of MC offer very consistent viscosity. This is important for precise formulations. Environmental considerations can also play a role. MC production can sometimes have a smaller environmental footprint.
Here are situations where MC excels:
Factor | MC Advantage | Example Application |
---|---|---|
Cost | Lower production cost | Bulk construction materials |
Gelation | Stronger low-temp gelation | Plant-based meat products |
Purity | High purity grades available | Sensitive pharmaceutical formulations |
Rheology | Consistent viscosity | Precision coatings |
Simplicity | Simpler chemical structure | Basic adhesive formulations |
Consider the specific needs of your product. Do not over-engineer solutions. MC can provide excellent performance. It is a reliable choice for many industrial uses. It balances performance with economic considerations.
8. Are there regulatory differences for HPMC and MC?
Regulatory compliance is a critical aspect. Both HPMC and MC are widely accepted. However, their specific applications may fall under different regulations. Understanding these rules is vital for market entry.
In the food industry, both are generally recognized as safe (GRAS). The FDA in the United States approves them. The European Food Safety Authority (EFSA) also approves them. Specific grades and purity levels apply. You must meet these standards. Here’s the deal… regulatory bodies ensure product safety and quality.
For pharmaceutical uses, HPMC is more common. It is listed in major pharmacopeias. These include the United States Pharmacopeia (USP) and the European Pharmacopoeia (EP). MC also has some pharmaceutical applications. However, HPMC has a broader acceptance as an excipient. This is due to its versatility and consistent performance.
Industrial safety standards also apply. These cover handling, storage, and disposal. Manufacturers must follow these guidelines. Global market acceptance varies slightly. Always check local regulations for your target market. Certification and quality control are also important. Reputable suppliers provide these.
Here is a look at regulatory aspects:
Regulatory Body | HPMC Status | MC Status |
---|---|---|
FDA (Food) | GRAS | GRAS |
EFSA (Food) | Approved | Approved |
USP (Pharma) | Listed excipient | Listed excipient (less common) |
EP (Pharma) | Listed excipient | Listed excipient (less common) |
Industrial Safety | Covered by general chemical safety | Covered by general chemical safety |
Always work with suppliers who understand these regulations. They can provide necessary documentation. This ensures your products meet all legal requirements. It also builds consumer trust. Proper regulatory adherence is not optional.
Conclusion
Understanding the differences between HPMC and MC is vital for industrial success. This article highlighted their chemical distinctions, water behavior, and diverse applications. We explored where HPMC excels, such as in controlled-release pharmaceuticals and high-performance construction. We also saw where MC shines, particularly in cost-sensitive food applications and specific gelation needs. Making the right choice directly impacts product quality and efficiency. It ensures your formulations perform as expected, saving time and resources. For expert guidance and to find the perfect cellulose ether for your project, contact Morton today. We offer tailored solutions and technical support to optimize your product development.
FAQ
Q1: What is the main difference between HPMC and MC?
The main difference lies in their chemical structure. HPMC has both methoxy and hydroxypropyl groups. MC only has methoxy groups. This structural difference leads to varied properties. It impacts their water behavior and thermal gelation.
Q2: Can HPMC and MC be used interchangeably?
No, they cannot always be used interchangeably. While both are cellulose ethers, their distinct properties make them suitable for different applications. HPMC offers broader versatility. MC excels in specific uses, like thermal gelation in food.
Q3: Which one is better for food applications?
Both HPMC and MC are used in food applications. MC is often preferred for its strong thermal gelation at lower temperatures. This is useful in meat alternatives. HPMC is also used as a thickener and stabilizer. The choice depends on the specific food product needs.
Q4: Are there any health concerns with HPMC or MC?
Both HPMC and MC are generally recognized as safe (GRAS) by regulatory bodies. These include the FDA and EFSA. They are widely used in food, pharmaceutical, and personal care products. They have a long history of safe use.
Q5: How do HPMC and MC affect product texture?
Both HPMC and MC act as thickeners and gelling agents. They impact product texture by increasing viscosity. MC creates a firm gel upon heating. HPMC can also form gels but often at higher temperatures. They both improve mouthfeel and stability in various products.