Businesses often struggle to select the correct Hydroxypropyl Methylcellulose (HPMC) grade for their products. Choosing the wrong HPMC can lead to significant issues, including poor product performance, increased production costs, and even regulatory non-compliance. These challenges can delay market entry and reduce profitability, creating frustration for purchasing managers and technical teams alike. A precise HPMC grade selection can prevent these problems, ensuring product stability, functionality, and cost-effectiveness. This article will guide you through HPMC classification, its applications in various industries, and how to select the right grade for your specific needs.
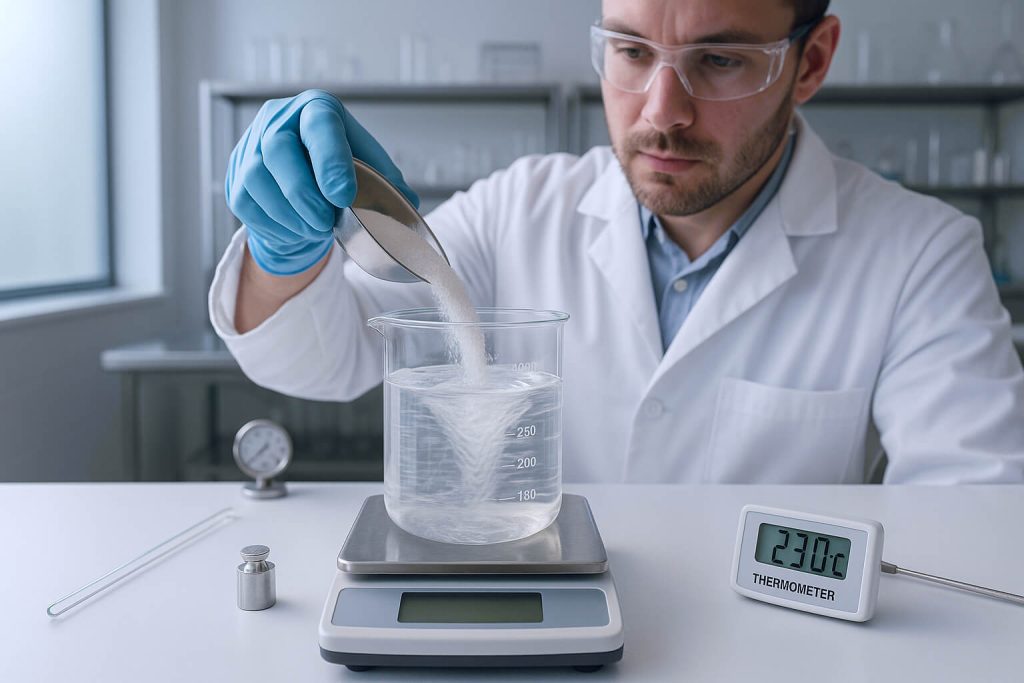
1. What is HPMC and Why is Grade Selection So Important?
Hydroxylpropyl Methylcellulose, or HPMC, is a versatile polymer derived from cellulose. It serves as a crucial ingredient across many industries. You find it in pharmaceuticals, construction, food, and personal care products. Its unique properties make it a preferred choice for thickening, binding, and film-forming. Here’s why it matters… Choosing the right HPMC grade is not just a technical detail; it directly impacts product quality and cost. An incorrect grade can lead to formulation instability, reduced shelf life, or processing difficulties. For example, in pharmaceuticals, the wrong HPMC can affect drug release rates, making the product ineffective or unsafe. In construction, it might compromise the strength or workability of materials. Precise selection ensures product performance, reduces waste, and meets specific application demands. This careful choice saves money and builds trust with customers.
HPMC Property | Impact on Application |
---|---|
Viscosity | Determines thickening power and flow characteristics |
Substitution Type | Affects solubility, gelation temperature, and film properties |
Particle Size | Influences dissolution rate and dispersion in formulations |
Purity | Critical for pharmaceutical and food applications |
pH Stability | Affects performance in acidic or alkaline environments |
2. How Are Different HPMC Grades Classified?
HPMC grades are classified based on several key parameters. These parameters dictate how the HPMC will behave in different applications. The most important factors are viscosity, degree of substitution, and molecular weight. Viscosity refers to the thickness of the HPMC solution. It is often measured in centipoise (cP) and is a primary indicator of its thickening power. Different HPMC grades have specific viscosity ranges, from low to high. The degree of substitution relates to the number of hydroxypropyl and methoxy groups attached to the cellulose backbone. This chemical modification affects properties like solubility, gelation temperature, and surface activity. Now, you might be wondering… How do these classifications translate into practical use? Manufacturers use a specific nomenclature to identify each grade. This naming convention typically includes letters and numbers that indicate the type of substitution and the approximate viscosity. For example, an HPMC grade might be labeled as HPMC K100M, where ‘K’ denotes a specific substitution type and ‘100M’ indicates a high viscosity. Understanding this system helps you choose the right product for your needs. The classification also impacts how HPMC interacts with other ingredients in a formulation, affecting stability and performance.
Classification Parameter | Description | Impact on HPMC Properties |
---|---|---|
Viscosity | Resistance to flow in solution | Thickening, binding, film-forming |
Methoxy Content | Degree of methyl substitution | Solubility, gelation temperature |
Hydroxypropoxy Content | Degree of hydroxypropyl substitution | Water retention, surface activity |
Molecular Weight | Size of the polymer chain | Viscosity, film strength |
Gelation Temperature | Temperature at which solution gels | Thermal stability, processing conditions |
3. Which HPMC Grades Are Used in Pharmaceutical Applications?
In the pharmaceutical industry, HPMC is a widely used excipient. It plays many roles in drug formulations. It acts as a binder in tablets, helping to hold ingredients together. It also serves as a film-forming agent for tablet coatings. These coatings protect the drug, mask taste, and aid in swallowing. For controlled-release formulations, specific HPMC grades are vital. They form a gel matrix that slows down drug release over time. This ensures a steady therapeutic effect. The choice of HPMC grade here depends on the desired release profile. High-viscosity grades typically provide slower release. Low-viscosity grades allow for faster dissolution. Let me explain… Regulatory bodies like the FDA have strict guidelines for pharmaceutical excipients. HPMC used in drugs must meet specific purity and quality standards. Manufacturers must provide detailed documentation, including certificates of analysis. This ensures patient safety and product efficacy. Understanding these requirements is key for pharmaceutical companies. It helps them meet compliance and bring safe products to market.
Pharmaceutical Application | Typical HPMC Grade Characteristics |
---|---|
Tablet Binding | Low to medium viscosity, good compressibility |
Film Coating | Low viscosity, excellent film-forming properties, clear solutions |
Controlled Release | High viscosity, consistent gel formation, pH-independent release |
Ophthalmic Solutions | Low viscosity, good clarity, non-irritating |
Topical Formulations | Medium viscosity, good spreadability, stable emulsions |
4. What HPMC Grades Are Ideal for Construction Materials?
In the construction industry, HPMC plays a vital role in various building materials. It improves workability, water retention, and adhesion. For cement-based products like tile adhesives, grouts, and renders, HPMC acts as a thickener and water-retaining agent. This prevents premature drying and allows for longer open times. It also enhances the bond strength between materials. In gypsum-based products, HPMC improves consistency and prevents cracking. Specific HPMC grades are chosen based on the application. For instance, in tile adhesives, high water retention and good slip resistance are crucial. This means selecting HPMC with higher viscosity and specific substitution patterns. This is important because… The performance of these materials directly impacts construction quality and durability. For self-leveling compounds, HPMC helps control flow and prevents segregation of aggregates. In Exterior Insulation and Finish Systems (EIFS), it contributes to crack resistance and adhesion of the base coat. The right HPMC grade ensures that construction materials perform as expected, even in challenging environmental conditions. This leads to more reliable and long-lasting structures.
Construction Application | Key HPMC Properties Required |
---|---|
Tile Adhesives | High water retention, good open time, slip resistance |
Renders/Plasters | Workability, sag resistance, adhesion |
Self-Leveling Compounds | Flow control, anti-segregation, surface finish |
Grouts | Water retention, reduced shrinkage, improved bond |
EIFS Base Coats | Crack resistance, adhesion, flexibility |
5. How Does HPMC Function in Food and Beverage Products?
HPMC is a widely accepted food additive, valued for its versatility. It acts as a thickener, stabilizer, and emulsifier in many food and beverage products. You find it in sauces, dressings, and dairy alternatives, where it provides desired texture and consistency. In baked goods, HPMC can improve crumb structure and extend shelf life. For gluten-free products, it mimics the properties of gluten, providing elasticity and volume. This makes it a valuable ingredient for consumers with dietary restrictions. The best part? HPMC is plant-derived, making it suitable for vegetarian and vegan products. Regulatory bodies like the FDA and EFSA classify food-grade HPMC as generally recognized as safe (GRAS). This means it is safe for consumption when used within specified limits. Proper labeling is also crucial to inform consumers. The specific HPMC grade chosen for food applications depends on the desired functional properties. For example, a higher viscosity HPMC might be used for thickening sauces, while a lower viscosity grade could be used for film-forming in confectionery. Its ability to form gels upon heating and revert to a liquid upon cooling also makes it useful in certain food processing applications.
Food Application | HPMC Function | Typical HPMC Grade Characteristics |
---|---|---|
Sauces & Dressings | Thickener, stabilizer | Medium to high viscosity, good shear stability |
Dairy Alternatives | Stabilizer, texture enhancer | Medium viscosity, good protein compatibility |
Baked Goods | Volume enhancer, moisture retention | Low to medium viscosity, good film-forming |
Gluten-Free Products | Binder, texture improver | Medium viscosity, heat gelling properties |
Confectionery | Film former, anti-sticking agent | Low viscosity, clear film formation |
6. What Are the Key HPMC Grades for Paints and Coatings?
HPMC is a critical additive in the paints and coatings industry. It primarily functions as a rheology modifier. This means it controls the flow and consistency of paints. In water-based paints, HPMC prevents sagging and improves brushability. It also enhances color development and stability. Different HPMC grades offer varying levels of thickening efficiency. This allows manufacturers to achieve specific paint properties. For example, a high-viscosity HPMC provides excellent anti-sagging properties. A lower viscosity grade might be preferred for spray applications. But here’s the thing… HPMC also affects the open time of paints, allowing for smoother application and better leveling. It reduces spatter during roller application, leading to a cleaner finish. Compatibility with other paint components is also a key consideration. HPMC must disperse well and not react negatively with pigments, binders, or other additives. The right HPMC grade ensures that paints have the desired application properties, appearance, and durability. This leads to high-quality finishes and satisfied customers.
Paint/Coating Application | HPMC Role | Key HPMC Properties |
---|---|---|
Water-based Paints | Thickener, rheology modifier | High viscosity, good water retention, sag resistance |
Latex Paints | Stabilizer, film former | Medium viscosity, improved flow and leveling |
Textured Coatings | Thickener, anti-settling agent | High viscosity, good particle suspension |
Primers | Binder, adhesion promoter | Low to medium viscosity, good film formation |
Industrial Coatings | Rheology control, anti-spatter | Specific viscosity and substitution for desired flow |
7. Which HPMC Grades Are Suited for Personal Care and Cosmetics?
In personal care and cosmetics, HPMC is a popular ingredient. It is used in shampoos, lotions, creams, and gels. Its primary functions include thickening, stabilizing emulsions, and forming films. HPMC provides a smooth, luxurious feel to products. It also helps to suspend insoluble ingredients, like exfoliating beads. Different HPMC grades offer varying textures and sensory properties. For example, a high-viscosity HPMC creates a rich, creamy lotion. A lower viscosity grade might be used for a light, non-greasy serum. Want to know the secret? HPMC is often chosen for its mildness and compatibility with skin. It is generally non-irritating and non-sensitizing. This makes it suitable for sensitive skin formulations. Trends in the personal care industry favor natural and sustainable ingredients. HPMC, being cellulose-derived, fits this demand. It offers a plant-based alternative to synthetic polymers. The right HPMC grade contributes to the product’s stability, appearance, and consumer appeal. This helps brands create effective and desirable cosmetic products.
Personal Care Application | HPMC Function | Typical HPMC Grade Characteristics |
---|---|---|
Shampoos & Conditioners | Thickener, foam stabilizer | Medium to high viscosity, good clarity |
Lotions & Creams | Emulsion stabilizer, texture enhancer | Medium viscosity, smooth feel |
Gels & Serums | Gelling agent, film former | Low to medium viscosity, non-tacky |
Sunscreens | Rheology modifier, pigment suspension | Medium viscosity, good UV filter compatibility |
Hair Styling Products | Film former, hold enhancer | Low to medium viscosity, non-flaking |
8. How Can You Test and Select the Right HPMC Grade?
Selecting the correct HPMC grade involves a systematic approach. It begins with understanding your specific application requirements. Consider factors like desired viscosity, solubility, and thermal properties. Laboratory testing is the first step. This involves evaluating different HPMC grades in small-scale formulations. You measure parameters like viscosity, pH, and stability over time. This helps narrow down the options. Once promising grades are identified, pilot testing is crucial. This involves scaling up the formulation to a larger batch size. It helps identify any processing issues or performance variations that might not appear in lab tests. The bottom line? Always consult supplier specifications and technical data sheets. These documents provide detailed information on each HPMC grade, including its chemical properties, typical applications, and handling instructions. Partnering with experienced HPMC suppliers can also be highly beneficial. They offer technical support and expertise. They can guide you through the selection process and provide samples for testing. This collaborative approach minimizes risks and optimizes product development. It ensures you choose the HPMC grade that delivers consistent performance and meets your quality standards.
Selection Step | Description | Benefit |
---|---|---|
Define Requirements | Clearly outline desired product properties and HPMC functions | Narrows down initial choices |
Lab Testing | Evaluate HPMC grades in small-scale formulations | Identifies promising candidates |
Pilot Testing | Scale up formulation to larger batches | Uncovers processing issues, confirms performance |
Supplier Consultation | Leverage supplier expertise and technical data | Accesses specialized knowledge, ensures compatibility |
Performance Monitoring | Continuously assess HPMC performance in final product | Ensures ongoing quality and consistency |
9. How Does HPMC Affect Product Stability and Shelf Life?
HPMC plays a significant role in enhancing the stability and extending the shelf life of various products. Its ability to form a protective film and retain moisture is key. In many formulations, HPMC acts as a stabilizer, preventing phase separation. This is particularly important in emulsions and suspensions, where ingredients might otherwise separate over time. By increasing the viscosity of the continuous phase, HPMC helps keep particles suspended and prevents settling. This leads to a more uniform and stable product. Here’s the deal… HPMC also helps control moisture migration. In food products, this can prevent staling or drying out. In personal care items, it maintains hydration and prevents product degradation. Its film-forming properties can also create a barrier against oxygen and other environmental factors. This further protects the product from spoilage. For example, in certain pharmaceutical suspensions, HPMC prevents drug particles from settling, ensuring consistent dosing throughout the product’s shelf life. In construction materials, it helps maintain workability and prevents premature drying, contributing to the material’s long-term integrity. The right HPMC grade can significantly improve a product’s longevity and performance.
Stability Factor | HPMC Contribution | Example Application |
---|---|---|
Phase Separation | Viscosity increase, particle suspension | Emulsions, Suspensions |
Moisture Retention | Film formation, water binding | Baked goods, Cosmetics |
Oxidation | Barrier formation | Food products, Pharmaceuticals |
Microbial Growth | Reduced water activity (indirect) | Various formulations |
Sedimentation | Increased viscosity, particle dispersion | Liquid pharmaceuticals |
10. What Are the Future Trends and Innovations in HPMC Use?
The HPMC market is continuously evolving, driven by innovation and changing industry demands. One major trend is the increasing focus on sustainability. Manufacturers are developing more eco-friendly production methods for HPMC. This includes using renewable resources and reducing environmental impact. There is also a growing demand for specialized HPMC grades. These grades are tailored for niche applications. For example, HPMC with enhanced thermal stability for high-temperature processes. Or, grades with specific rheological properties for advanced materials. What does this mean for you? The development of multi-functional HPMC grades is another key area. These grades offer several benefits in a single product. This simplifies formulations and reduces raw material complexity. For instance, an HPMC that acts as both a thickener and a sustained-release agent. Digitalization and data analytics are also influencing HPMC selection. Advanced modeling can predict HPMC behavior in formulations. This speeds up product development and reduces trial-and-error. As industries seek more efficient and sustainable solutions, HPMC will remain a vital ingredient. Its adaptability and diverse functionalities ensure its continued relevance in future innovations.
Trend | Description | Impact on HPMC Development |
---|---|---|
Sustainability | Eco-friendly production, renewable sources | Green chemistry, reduced carbon footprint |
Specialization | Tailored grades for niche applications | Custom properties, enhanced performance |
Multi-functionality | Single HPMC grade with multiple benefits | Simplified formulations, cost savings |
Digitalization | Predictive modeling, data analytics | Faster development, optimized selection |
Bio-based Alternatives | Research into new plant-derived polymers | Diversification of HPMC sources |
Conclusion
Selecting the appropriate HPMC grade is paramount for product success across diverse industries. We have explored how HPMC classification, based on viscosity and substitution, directly influences its performance in pharmaceuticals, construction, food, paints, and personal care. Understanding these nuances helps prevent costly formulation errors and ensures product integrity. The ability of HPMC to enhance stability, extend shelf life, and adapt to emerging trends underscores its value. By carefully testing and selecting the right grade, businesses gain a competitive edge. To refine your HPMC selection and optimize your product formulations, contact Morton today. Our experts provide tailored guidance and high-quality HPMC solutions, helping you achieve superior results and operational efficiency.
FAQ
Q1: What does HPMC stand for?
Hydroxypropyl Methylcellulose. It is a semi-synthetic, inert, viscoelastic polymer used as an excipient, thickener, and emulsifier in various industries.
Q2: Is HPMC safe for consumption?
Food-grade HPMC is generally recognized as safe (GRAS) by regulatory bodies like the FDA when used according to guidelines. Pharmaceutical grades also have stringent safety profiles.
Q3: Can different HPMC grades be blended?
Yes, blending HPMC grades can sometimes achieve specific performance characteristics. However, this requires careful formulation and testing.
Q4: How does temperature affect HPMC viscosity?
HPMC solutions typically exhibit thermo-gelling properties. Their viscosity decreases with increasing temperature up to a certain point. After this point, they may gel. The exact behavior depends on the grade.
Q5: Where can I source high-quality HPMC grades?
Reliable chemical suppliers and manufacturers, like Morton, offer a range of HPMC grades. They also provide detailed specifications and technical support to help you choose the right one for your application.