Selecting the right viscosity of Hydroxypropyl Methylcellulose (HPMC) is essential for achieving optimal results in various industrial applications. Whether you’re formulating construction materials, pharmaceuticals, or food products, understanding how viscosity impacts the performance of HPMC is crucial. In this article, we’ll explore the factors that influence HPMC viscosity and how to determine the right viscosity grade for your specific needs.
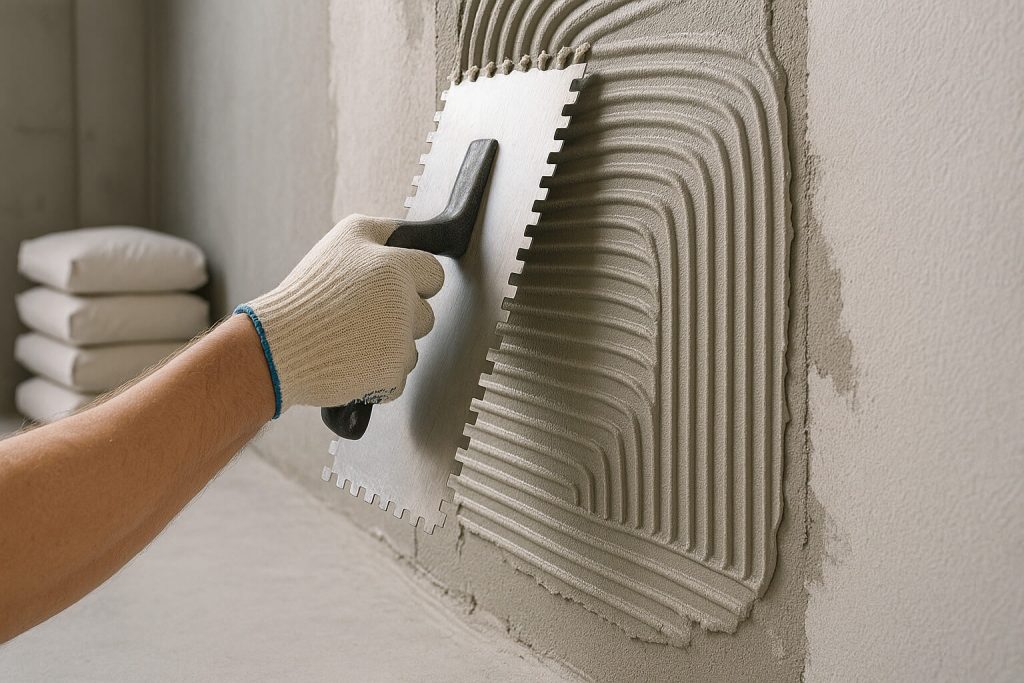
1. What is HPMC and Why is Viscosity Important for Applications?
Hydroxypropyl Methylcellulose (HPMC) is a cellulose-based compound widely used as a thickening agent, binder, stabilizer, and emulsifier in numerous industries. Ready for the good part? Its versatility and effectiveness are largely dependent on its viscosity, which influences the texture, consistency, and performance of products in which it’s used.
In construction, for example, HPMC is a key ingredient in tile adhesives, mortars, and plasters. Its viscosity ensures that the mixture has the right workability, flow, and adhesion properties. The same applies to pharmaceuticals, where HPMC’s viscosity determines how effectively it controls the release of active ingredients in controlled-release formulations. In food production, the right viscosity ensures that HPMC can stabilize emulsions and improve texture, providing products with the desired consistency and mouthfeel.
The viscosity of HPMC can vary greatly, which is why it is essential to choose the appropriate grade for your application. The right viscosity ensures that your product performs as expected, whether it’s a construction adhesive that stays in place or a tablet that releases the active ingredient at the right rate.
صناعة | طلب | Benefit of Viscosity |
---|---|---|
بناء | Mortars, adhesives, plaster | Workability, open time |
المستحضرات الصيدلانية | Tablets, capsules | Consistency, controlled release |
طعام | Emulsions, sauces, dressings | Texture, stability |
2. How Does Viscosity Affect the Performance of HPMC?
Viscosity plays a pivotal role in determining how HPMC behaves in a solution and how it performs in various formulations. But here’s the kicker – viscosity directly impacts the flow and texture of the end product. In construction, for example, higher viscosity HPMC helps prevent materials like mortar and adhesives from running off surfaces, ensuring they stay in place during application.
In pharmaceuticals, the viscosity of HPMC solutions is crucial for controlling the release of active ingredients. HPMC forms a gel in aqueous solutions, and this gel can influence how slowly or quickly the active ingredients are released from tablets or capsules. The right viscosity ensures that the release is controlled and sustained, providing a steady therapeutic effect.
In food, viscosity affects the texture, mouthfeel, and stability of products. For instance, sauces, dressings, and ice creams require specific viscosity levels to ensure they have the right consistency and texture, enhancing consumer experience and product quality.
By adjusting the viscosity, manufacturers can optimize the performance of HPMC in each application, ensuring the right consistency and functionality.
Viscosity Range (mPa·s) | طلب | فائدة |
---|---|---|
50,000 – 100,000 | Mortars, tile adhesives | Improved workability, water retention |
100,000 – 250,000 | أقراص الإطلاق المُتحكم فيه | Steady release, therapeutic effect |
10,000 – 50,000 | Sauces, dressings, beverages | Smooth texture, easy pouring |
3. What are the Different Viscosity Requirements for Various Industries?
Each industry has its own set of viscosity requirements based on the specific needs of the application. What’s the real story here? Different viscosities are required for HPMC to perform optimally in each sector.
In construction, the ideal viscosity for HPMC typically ranges between 50,000 to 150,000 mPa·s. This ensures that the mortar, adhesive, or plaster has the right texture, making it easy to apply while offering excellent bonding strength. Higher viscosity HPMC will prevent materials from running off surfaces, providing better control during application.
In pharmaceuticals, viscosity plays a role in controlling the release of drugs. Low viscosity is often used in fast-dissolving tablets, while high viscosity HPMC is used in controlled-release formulations. Here, viscosity is crucial for ensuring that the active ingredients are released over time, providing prolonged therapeutic effects.
In food production, viscosity is needed to ensure the right texture and consistency in products such as sauces, dressings, and ice cream. The viscosity requirements will vary depending on the desired product texture – for example, thicker products like mayonnaise require higher viscosity HPMC.
صناعة | Viscosity Range (mPa·s) | طلب |
---|---|---|
بناء | 50,000 – 150,000 | Mortars, adhesives, plasters |
المستحضرات الصيدلانية | 50,000 – 250,000 | أقراص وكبسولات ذات إطلاق متحكم |
طعام | 10,000 – 100,000 | الصلصات، والتتبيلات، والآيس كريم |
4. How Do Temperature and pH Influence HPMC Viscosity?
Temperature and pH are two key environmental factors that can significantly influence the viscosity of HPMC. What’s the kicker? As temperature increases, the viscosity of HPMC typically decreases. This is particularly important in industries where temperature fluctuations are common, such as pharmaceuticals and food production.
In pharmaceuticals, HPMC solutions are sensitive to temperature changes. When exposed to high temperatures, the viscosity of the solution may drop, affecting the controlled release of active ingredients in tablets. Conversely, lower temperatures may increase viscosity, which can lead to problems with the flow and mixing of ingredients.
pH is another critical factor. HPMC is non-ionic, meaning it’s generally stable across a wide pH range. However, extreme pH values (either acidic or alkaline) can cause HPMC to lose its viscosity or change its solubility properties. In food applications, pH control is essential for maintaining the right texture and preventing separation in emulsions like salad dressings or sauces.
درجة الحرارة (°م) | تأثير اللزوجة | طلب |
---|---|---|
5 – 25 | Increased viscosity | الأدوية والأغذية |
25 – 45 | Decreased viscosity | Pharmaceuticals, food production |
>45 | Significant reduction in viscosity | الأغذية ومستحضرات التجميل |
5. What Role Does Molecular Weight Play in Determining HPMC Viscosity?
The molecular weight of HPMC directly affects its viscosity and solubility. What’s the real story here? Higher molecular weight HPMC has longer polymer chains, which leads to higher viscosity. This is because the longer chains have more points of interaction with water, resulting in a thicker solution. In contrast, lower molecular weight HPMC has shorter chains, which results in lower viscosity and faster dissolution.
In pharmaceutical applications, higher molecular weight HPMC is often used for controlled-release tablets because it forms a gel matrix that slows the release of active ingredients over time. In contrast, lower molecular weight HPMC is used in formulations that require quicker dissolution or thinner solutions.
In construction, higher molecular weight HPMC provides better stability and adhesion in products like tile adhesives and mortars. It ensures that the product stays intact and doesn’t lose its effectiveness over time.
الوزن الجزيئي | تأثير اللزوجة | التطبيقات |
---|---|---|
الوزن الجزيئي المنخفض | Lower viscosity, quicker dissolution | الأغذية والأدوية |
الوزن الجزيئي العالي | Higher viscosity, controlled release | المستحضرات الصيدلانية والبناء |
6. How Can Concentration of HPMC Impact Its Viscosity?
The concentration of HPMC in a solution directly influences its viscosity. Ready for the good part? As the concentration of HPMC increases, the viscosity of the solution thickens. This is due to the increased number of polymer chains interacting with the solvent, which results in higher resistance to flow.
In construction, a higher concentration of HPMC is used to ensure that the mortar or adhesive has a thick, stable consistency that can be applied without running off the surface. In pharmaceuticals, adjusting the concentration of HPMC allows manufacturers to control the release rate of active ingredients. For food applications, concentration levels determine the desired texture and mouthfeel of products like sauces and dressings.
Concentration (%) | تأثير اللزوجة | طلب |
---|---|---|
1 – 2 | Low viscosity, quick application | الأغذية والأدوية |
2 – 5 | اللزوجة المعتدلة | Mortar, tile adhesives |
5 – 10 | High viscosity, improved stability | أقراص الإطلاق المُتحكم فيه |
7. How Do Additives and Solvents Affect HPMC Viscosity?
Additives and solvents can have a significant impact on the viscosity of HPMC solutions. But here’s the kicker – carefully choosing the right additives and solvents can help you optimize viscosity for specific applications. For example, plasticizers and stabilizers can be added to construction materials to adjust the viscosity and improve their workability.
In pharmaceuticals, certain excipients can be mixed with HPMC to create controlled-release formulations. These additives can affect the gel formation and release rate of the active ingredients. In food, the choice of solvent can determine the viscosity of the product, which is essential for achieving the right texture and consistency in emulsions.
By experimenting with different additives and solvents, manufacturers can fine-tune the viscosity of HPMC to meet the specific requirements of their applications.
نوع المادة المضافة | التأثير على اللزوجة | التطبيقات |
---|---|---|
المواد الملينة | Reduce viscosity, improve workability | Construction, adhesives |
المثبتات | Increase viscosity, improve stability | الأدوية والأغذية |
المذيبات | Adjust viscosity for desired texture | الأغذية ومستحضرات التجميل |
8. How Can HPMC Viscosity Be Measured and Optimized for Applications?
Measuring HPMC viscosity is a critical step in ensuring that it meets the required specifications for each application. What’s the kicker here? Accurate viscosity measurements allow manufacturers to adjust formulations to achieve optimal performance. Viscosity is typically measured using tools like the Brookfield viscometer أو rotational viscometer, which are designed to measure the flow resistance of the solution.
Once the viscosity is measured, it can be adjusted by changing the concentration, molecular weight, or by adding additives to fine-tune the product. Regular testing ensures that the viscosity remains consistent between batches, ensuring the desired product performance every time.
Viscosity Test | طريقة القياس | التطبيقات |
---|---|---|
اختبار اللزوجة | مقياس اللزوجة بروكفيلد | المستحضرات الصيدلانية والبناء |
Shear Rate Testing | مقياس اللزوجة الدوراني | Food, adhesives |
Temperature Testing | Rheometer | R&D, specialized formulations |
9. What Are the Risks of Using Incorrect HPMC Viscosity in Your Formulations?
Using the wrong viscosity of HPMC can have significant consequences on your product’s performance. Ready for the good part? If the viscosity is too low, the product may be too fluid, making it difficult to apply or causing inconsistent results. On the other hand, if the viscosity is too high, it may become too thick, causing issues with processing and application.
In pharmaceuticals, using the wrong viscosity can result in inconsistent drug release, affecting therapeutic outcomes. In construction, incorrect viscosity may lead to poor bonding and reduced effectiveness of adhesives and mortars. In food, the wrong viscosity could lead to texture issues and consumer dissatisfaction.
To mitigate
these risks, it’s essential to measure and adjust the viscosity regularly and ensure that the right viscosity is used for each application.
Viscosity Risk | التأثير المحتمل | Example Application |
---|---|---|
اللزوجة المنخفضة | Poor adhesion, inconsistent performance | Construction, adhesives |
اللزوجة العالية | Difficulty in application, poor flow | الأدوية والأغذية |
10. How Can You Ensure Consistent Viscosity of HPMC Across Batches?
Ensuring consistent viscosity of HPMC across batches is crucial for product quality. But here’s where it gets interesting – manufacturers need to implement strict quality control measures to monitor and adjust viscosity throughout production. Regular viscosity testing using standard methods like the Brookfield viscometer ensures consistency across batches.
Manufacturers can also rely on suppliers that maintain rigorous quality control processes and offer products that meet established viscosity standards. By using reliable suppliers and conducting routine tests, you can ensure that each batch of HPMC performs consistently and meets your specific viscosity requirements.
مقياس مراقبة الجودة | فائدة | طلب |
---|---|---|
Regular Viscosity Testing | Ensures consistency and quality | جميع الصناعات |
Batch Monitoring | Guarantees uniform viscosity | الأدوية والأغذية والبناء |
خاتمة
In conclusion, choosing the right viscosity for HPMC is critical for ensuring product performance across various industries. Whether in construction, pharmaceuticals, or food, viscosity plays a pivotal role in the effectiveness of HPMC-based formulations. By understanding the factors that affect viscosity, such as temperature, concentration, molecular weight, and additives, you can optimize HPMC for your specific application and ensure consistent performance.
قسم الأسئلة الشائعة
س1: ما هو HPMC؟
أ1: HPMC (Hydroxypropyl Methylcellulose) is a cellulose derivative used in various industries for its properties as a binder, thickener, emulsifier, and stabilizer. It’s commonly found in construction materials, pharmaceuticals, and food products.
س2: How does viscosity affect the performance of HPMC?
أ2: Viscosity impacts how HPMC behaves in formulations. It affects flow, consistency, and the overall functionality of the product. In construction, it ensures workability; in pharmaceuticals, it controls drug release; in food, it determines texture and mouthfeel.
س3: What are the ideal viscosity requirements for construction applications?
أ3: In construction, HPMC viscosity typically ranges from 50,000 to 150,000 mPa·s. The viscosity ensures that the mortar or adhesive remains workable, providing the right bonding and spreading properties.
س4: How can temperature influence the viscosity of HPMC?
أ4: Temperature affects HPMC viscosity, with higher temperatures typically decreasing viscosity. This is critical in industries like pharmaceuticals, where temperature fluctuations can impact product consistency and release rates.
س5: What are the risks of using incorrect HPMC viscosity?
أ5: Using incorrect viscosity can lead to poor product performance, such as weak bonding in construction, inconsistent drug release in pharmaceuticals, and undesirable textures in food products. Regular testing is essential to mitigate these risks.