Hydroxypropyl Methylcellulose, commonly known as HPMC, is an essential ingredient in various industries, notably pharmaceuticals, food, and cosmetics. Understanding HPMC is vital for professionals in these fields, as it significantly affects product formulations and performance. This article addresses the importance, applications, properties, manufacturing processes, and challenges associated with HPMC, while providing insights into its future potential and best practices for utilization.
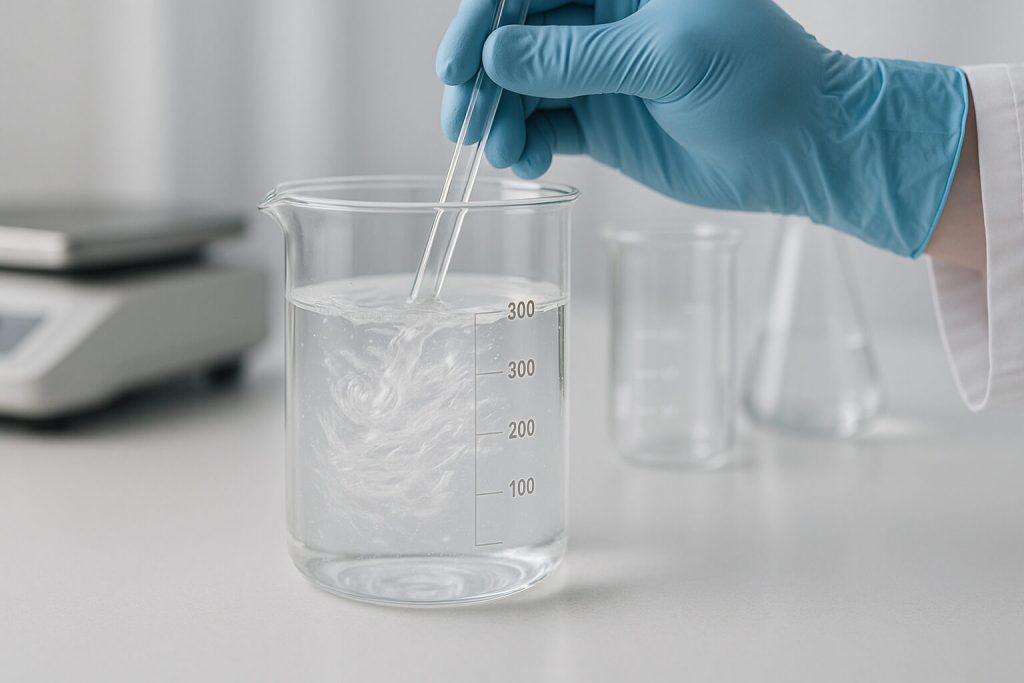
1. ما هو HPMC ولماذا هو مهم؟
HPMC, or Hydroxypropyl Methylcellulose, is a non-ionic cellulose ether widely used as an excipient in pharmaceuticals, a thickener in food products, and a binder in cosmetic formulations. The origin of HPMC dates back to when cellulose was first modified to create new products with enhanced functionalities. This compound has become essential due to its versatile properties and significant applications across various sectors.
But here’s the kicker: HPMC not only offers multiple functionalities but also provides vital characteristics that are highly sought after in product formulations. It acts as a thickener, stabilizer, binder, and film-former, influencing the texture, viscosity, and stability of formulations. Moreover, scientists and formulators often choose HPMC for its non-toxic and hypoallergenic nature, making it suitable for sensitive applications, especially in pharmaceuticals.
Today, HPMC plays a critical role in ensuring that products maintain their integrity and performance. For example, in pharmaceuticals, HPMC is instrumental in controlling drug release rates, thereby improving bioavailability. This property can transform the therapeutic efficacy of medications. In the food industry, HPMC acts as a stabilizer, preventing separation in emulsions and enhancing texture and mouthfeel. This broad applicability solidifies its importance across multiple sectors and encourages ongoing research and development.
وجه | تفاصيل |
---|---|
تعريف | A non-ionic cellulose ether used in multiple industries |
Key Functions | Thickener, stabilizer, binder, film-former |
أهمية | Enhances product integrity and performance |
2. How is HPMC Used in Pharmaceuticals?
In the pharmaceutical world, HPMC serves several critical purposes. Its primary role is as an excipient in drug formulations, notably in oral tablets, capsules, and topical applications. What’s the real story? HPMC is crucial for providing various functionalities that ensure efficacy and usability in medications.
One of the key benefits of HPMC in pharmaceuticals is its ability to control the release of active pharmaceutical ingredients (APIs). This is particularly significant for sustained-release formulations, which are designed to release medication over an extended period. For instance, HPMC can create a gel matrix when it comes in contact with water, moderating the release of the drug and effectively extending its therapeutic effects. This property is vital for managing chronic conditions, where consistent dosing is crucial for maintaining stable drug levels in patients.
Moreover, HPMC is often included in topical formulations such as gels and creams. Its ability to form films enhances the adherence of these products to the skin, improving the delivery of the active ingredients and ensuring that they perform effectively. In addition, HPMC is used to improve the solvency of poorly soluble drugs, enabling better absorption in the gastrointestinal tract.
Historically, one major case highlighting HPMC’s impact is in the formulation of metformin extended-release tablets. Researchers found that incorporating HPMC significantly improved patient compliance by reducing dosing frequency and providing effective blood sugar control through sustained drug release. Such contributions showcase HPMC’s indispensable role in meeting patient and healthcare needs.
نوع التطبيق | Benefits of HPMC |
---|---|
أقراص فموية | Sustained drug release for chronic conditions |
تركيبات موضعية | Enhanced adherence and ingredient delivery |
Solubility Improvement | Increased absorption of poorly soluble drugs |
3. What are the Key Properties of HPMC?
Understanding the key properties of HPMC is essential for its effective utilization in formulations. HPMC is characterized by its unique chemical structure, which can be modified to achieve specific functionalities. This is where it gets interesting. Its solubility profiles, viscosity parameters, and gel-forming abilities are all pivotal for its application in different industries.
HPMC is available in several grades, which differ primarily by their viscosity. This viscosity variation allows formulators to select specific grades tailored for their particular applications. Low-viscosity grades are preferred for applications requiring rapid disintegration and dissolution, while high-viscosity grades are suitable for controlled-release formulations where slower dissolution is desired.
Furthermore, HPMC is soluble in cold water yet forms a gel when it hydrates, which is beneficial for creating stable emulsions and suspensions. This characteristic helps maintain product consistency and prevents separation, particularly in food and cosmetic formulations.
Additionally, HPMC exhibits excellent film-forming properties, enabling it to create a barrier that enhances stability and prolongs the shelf life of products. This ability is vital in pharmaceuticals, where prolonged stability is essential for maintaining the efficacy of active ingredients.
Overall, the unique properties of HPMC, combined with its adaptability for various applications, reinforce its value across pharmaceuticals, food, and cosmetic sectors.
Key Property | وصف |
---|---|
اللزوجة | Variable grades for tailored applications |
الذوبان | Soluble in cold water, forming gels |
Film Forming | Creates stable barriers enhancing shelf life |
4. Where Else is HPMC Applied?
HPMC’s versatility extends well beyond pharmaceuticals. It finds robust applications in several industries, particularly in food production and cosmetics. But here’s the kicker: understanding where HPMC is used can open your eyes to its widespread relevance and importance.
In the food industry, HPMC acts primarily as a thickening agent and stabilizer. It is commonly used in sauces, dressings, and ice creams to help create a desirable texture and improve mouthfeel. For example, HPMC can stabilize emulsions by preventing ingredients from separating, thus enhancing the overall quality and appeal of food products. Its ability to create a creamy texture often leads consumers to perceive these products as more indulgent and satisfying.
In the cosmetics sector, HPMC is utilized for its film-forming properties, enhancing product consistency and performance. It is employed in cosmetic creams, gels, and lotions to provide a smooth application and help active ingredients absorb better into the skin. The film created by HPMC can also provide a barrier against moisture loss and environmental pollutants.
Interestingly, HPMC has applications in the construction industry as well. It is utilized in the formulation of dry-mix mortars and plasters, where it improves the workability and water retention of the mixture. This characteristic allows for easier application and better adhesion, essential for construction durability.
By understanding the diverse applications of HPMC, companies can leverage its benefits across multiple product lines, creating high-quality formulations that meet consumer expectations.
صناعة | تطبيقات HPMC |
---|---|
طعام | Thickener and stabilizer in sauces and dressings |
مستحضرات التجميل | Enhances texture and absorption in creams |
بناء | Improves workability in dry-mix mortars |
5. How is HPMC Manufactured?
Manufacturing HPMC involves a meticulous process that ensures high-quality output. Ready for the good part? The process of synthesizing HPMC generally begins with the selection of pure cellulose, which is derived from wood pulp or cotton linters. The cellulose is then subjected to a series of chemical reactions to modify its structure and introduce hydroxypropyl and methyl groups, creating HPMC.
The first step entails treating cellulose with alkaline solutions, which allows for the substitution of the hydroxyl groups. The treatment breaks the cellulose fibers into smaller pieces, enhancing their accessibility during subsequent steps. After the initial processing, the cellulose undergoes etherification, whereby methylene chloride and propylene oxide are utilized to achieve the desired degree of substitution.
Quality control is a critical step in HPMC manufacturing. Continuous monitoring ensures adherence to regulatory standards and consistency in quality. Various tests are conducted to evaluate the product, including viscosity measurements, solubility assessments, and particle size distribution analyses. This stringency ensures that the HPMC produced meets industry specifications for applications in pharmaceuticals and other sectors.
Once the product is tested and verified, it undergoes drying and milling to obtain the desired granule size. This final step is vital as it impacts how HPMC behaves in formulation contexts. The precise handling and comprehensive quality assurance throughout the manufacturing process showcase the importance of HPMC and its versatile applications.
خطوة التصنيع | وصف |
---|---|
اختيار السليلوز | Use of pure cellulose derived from biomass |
الأثير | Chemical modifications to create HPMC |
ضبط الجودة | Rigorous testing for viscosity and solubility |
6. What are the Benefits of Using HPMC?
The benefits of incorporating HPMC into formulations are numerous and impactful. One primary advantage is its ability to enhance stability in various products. This is where it gets interesting. HPMC contributes to maintaining the integrity of formulations, extending shelf life, and ensuring consistent performance over time.
In pharmaceuticals, HPMC’s role as a controlled release agent significantly improves therapeutic efficacy. By modulating the release rates of active ingredients, HPMC minimizes the frequency of dosing, enhancing patient compliance. This is particularly beneficial in treating chronic conditions, where consistent levels of medication in the bloodstream are critical.
Moreover, HPMC’s non-toxic and hypoallergenic nature makes it a suitable choice for sensitive applications. This characteristic is indispensable in the cosmetic sector, where formulations must be safe and gentle on the skin. Furthermore, HPMC’s versatility allows for multiple applications across different formulation types, enhancing its value as an excipient or ingredient.
Cost-effectiveness is another key benefit of HPMC. Its stable prices in relation to performance metrics ensure that companies can produce high-quality products without overspending. Packaging and distribution of HPMC also tend to be economical, making it an attractive option for manufacturers looking to optimize their operational costs.
Ultimately, the versatility, stability, and efficiency of HPMC render it a invaluable asset across various industries, driving innovation and improving product quality.
فائدة | التأثير على الصيغ |
---|---|
استقرار | Extends shelf life and preserves integrity |
إطلاق مُتحكَّم فيه | Enhances therapeutic efficacy and patient compliance |
فعالية التكلفة | Provides high performance at a competitive price |
7. Are There Any Alternatives to HPMC?
While HPMC is an invaluable component in numerous formulations, it is essential to consider its alternatives. Various other cellulose derivatives and excipients can serve similar functions, depending on the specific needs of a formulation. What’s the real story? Understanding these alternatives can help manufacturers make informed decisions.
Some common alternatives to HPMC include Hydroxyethyl Cellulose (HEC) and Methylcellulose (MC). HEC is primarily utilized as a thickener and emulsifier and is often chosen when gel formation is not required. This no-gel characteristic can be advantageous for certain applications in food and cosmetics where a more fluid product is desired.
Methylcellulose, on the other hand, shares several properties with HPMC, such as hydration and thickening abilities. However, it behaves differently in that it forms gels when heated, making it unsuitable for applications requiring stable emulsions at high temperatures.
Additionally, other synthetic polymers, such as Carbopol and PVP (Polyvinyl Pyrrolidone), can be viable alternatives depending on desired attributes. Carbopol is used as a thickening agent and stabilizer particularly in personal care formulations, while PVP is noted for its solubility and film-forming properties.
However, each alternative presents both advantages and disadvantages. This means that formulators must assess their project requirements carefully and consider the performance differences to choose the most fitting substitute or companion to HPMC in product formulations.
بديل | صفات |
---|---|
Hydroxyethyl Cellulose | Acts as a thickener, ideal for fluid formulations |
ميثيل السليلوز | Gel-forming when heated, not suitable for all applications |
Carbopol | Thickening and stabilizing agent in cosmetics |
8. What Challenges Are Associated with HPMC?
Despite its many advantages, the utilization of HPMC is not without challenges. Manufacturers often face several hurdles when incorporating HPMC into their formulations. But here’s the kicker: addressing these challenges is crucial for maximizing the benefits of HPMC.
One prominent challenge is variability in HPMC quality. Since the source and manufacturing processes can differ, there may be batch-to-batch inconsistencies affecting performance. This necessitates rigorous quality control measures to ensure every batch meets the required specifications.
Another challenge lies in the effective integration of HPMC into formulations. Given its unique properties, improper handling or incorrect formulation techniques can lead to unexpected behavior, such as poor suspension stability or uneven viscosity. Therefore, formulators must possess a deep understanding of HPMC’s properties to use it optimally.
Regulatory considerations also pose challenges, as products containing HPMC must meet stringent guidelines to ensure safety and efficacy. Manufacturers must navigate through complex regulations, especially in the pharmaceuticals sector, where compliance is a necessity.
Additionally, ongoing scientific research may lead to evolving recommendations and standards regarding HPMC, requiring manufacturers to stay updated on the latest findings affecting formulation techniques and usage guidelines.
By recognizing and proactively addressing these challenges, manufacturers can successfully harness the benefits of HPMC while minimizing potential setbacks.
تحدي | التأثير على الاستخدام |
---|---|
تباين الجودة | Inconsistencies affecting performance |
قضايا التكامل | Improper handling leading to formulation problems |
Regulatory Considerations | Navigating complex guidelines for compliance |
9. How is the Future Outlook for HPMC?
The future of HPMC appears promising, with ongoing advancements poised to enhance its relevance across various industries. Ready for the good part? As research continues to unlock the full potential of HPMC, its applications are expected to expand significantly.
With the increasing demand for personalized medicine, HPMC is likely to play a vital role in developing customized drug formulations. These formulations could address individual patient needs more effectively through tailored release profiles and enhanced efficacy. Emerging technologies also promise to enable the development of innovative drug delivery systems that incorporate HPMC’s unique properties.
Moreover, the growing focus on sustainability and eco-friendly practices aligns well with HPMC’s plant-based origins. As consumers and manufacturers continue to prioritize environmentally friendly products, HPMC’s sustainable nature and compatibility with green formulation practices offer a distinct advantage.
Expect to see advances in formulation technologies that leverage HPMC’s properties for enhanced performance in pharmaceuticals, food, and cosmetics. This evolution is supported by ongoing research aimed at optimizing its functionality, performance, and efficiency, thus strengthening its application across various sectors.
Thus, the outlook for HPMC is increasingly optimistic, showcasing its adaptability and continued relevance as industries innovate and evolve.
الاتجاه المستقبلي | التأثير المحتمل |
---|---|
الطب الشخصي | Tailored formulations for improved patient outcomes |
الاستدامة | Alignment with eco-friendly practices |
ابتكار | Advancements in applications and technologies |
10. How Can You Effectively Utilize HPMC in Your Products?
Effectively utilizing HPMC in formulations requires a strategic approach that considers its properties and the specific needs of the product. This is where it gets interesting. First, manufacturers must select the right grade of HPMC based on desired viscosity and functional requirements. Testing different grades can yield insights into which option performs best for a particular application.
Moreover, thorough formulation and processing techniques are critical. Prehydration of HPMC prior to incorporation can lead to better distribution and performance within the mixture. This step ensures that when HPMC is added to formulations, it swells effectively, leading to the desired viscosity and consistency.
Conducting small-scale trials is advisable before full-scale production. These trials provide valuable data about product performance and stability, allowing formulators to refine their processes. Continuous monitoring during production phases helps maintain consistency and quality throughout the manufacturing process.
Lastly, staying informed about emerging trends and innovations regarding HPMC applications allows manufacturers to remain competitive. Attending industry conferences and seminars can provide insights into new research, alternative applications, and formulation advancements, enhancing overall product quality and market readiness.
By embracing a proactive and well-informed strategy for utilizing HPMC, manufacturers can maximize its benefits and ensure superior performance across a range of products.
أفضل الممارسات | وصف |
---|---|
اختيار الصف | Tailor selection to specific application needs |
الترطيب المسبق | Improves HPMC distribution in formulations |
التجارب على نطاق صغير | Allows for functional testing and refinement |
قسم الأسئلة الشائعة
س1: ما هو HPMC؟
HPMC stands for Hydroxypropyl Methylcellulose, a non-ionic cellulose ether widely used in pharmaceuticals, food, and cosmetics for its thickening, binding, and stabilizing properties.
س2: How does HPMC function in pharmaceuticals?
HPMC acts as an excipient that controls the release of active ingredients, enhances solubility, and improves the stability of formulations in drug delivery systems.
س3: Where else is HPMC applied apart from pharmaceuticals?
HPMC is also used in food products as a thickening and stabilizing agent, as well as in cosmetics for enhancing texture and product consistency.
س4: What are the key benefits of using HPMC?
Benefits of HPMC include enhanced stability in formulations, improved bioavailability of pharmaceuticals, and its non-toxic nature, making it suitable for various applications.
س5: ما هي التحديات المرتبطة باستخدام HPMC؟
Challenges include quality variability between batches, integration issues during formulation, and navigating regulatory considerations for compliant manufacturing.