Für die industriellen Anwendungen von Hydroxypropylmethylcellulose (HPMC) und Hydroxyethylmethylcellulose (HEMC) ist das Verständnis ihrer Wasserlöslichkeit und ihres Lösungsverhaltens entscheidend, um optimale Ergebnisse zu erzielen. Diese beiden Cellulosederivate werden häufig in Branchen wie der Pharma-, Lebensmittel- und Bauindustrie eingesetzt, wo präzise Leistung unerlässlich ist. Doch warum ist die Löslichkeit so wichtig und wie wirken sich diese Eigenschaften auf die Funktionalität von HPMC und HEMC in der Praxis aus? Dieser Artikel untersucht die Löslichkeitseigenschaften dieser Polymere, ihre Auswirkungen auf die Produktleistung und den Einfluss ihres Lösungsverhaltens auf verschiedene industrielle Anwendungen. Am Ende dieses Artikels wissen Sie, wie Sie die Auflösung von HPMC und HEMC für Ihre spezifischen Anforderungen optimieren können.
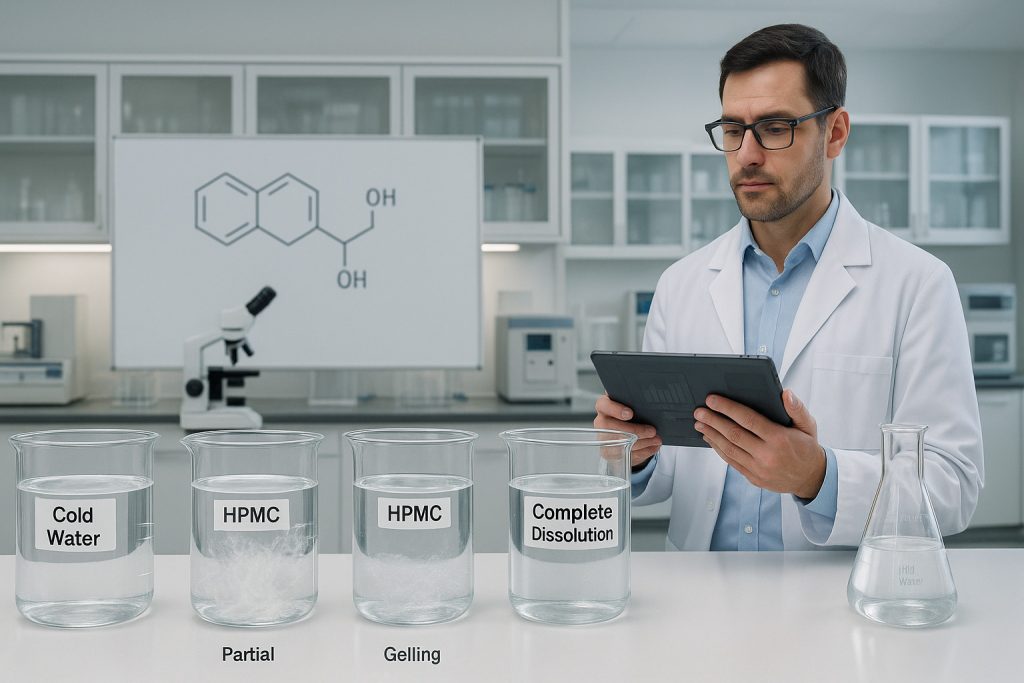
1. Was sind HPMC und HEMC und warum sind ihre Löslichkeitseigenschaften wichtig?
Hydroxypropylmethylcellulose (HPMC) und Hydroxyethylmethylcellulose (HEMC) sind beides Cellulosederivate, die aufgrund ihrer Löslichkeit und ihrer verdickenden Eigenschaften weite Verbreitung gefunden haben. Beide werden häufig als Bindemittel, Stabilisatoren, Emulgatoren und Verdickungsmittel in zahlreichen Branchen eingesetzt.. Sie weisen zwar viele Gemeinsamkeiten auf, beispielsweise ihre Wasserlöslichkeit, unterscheiden sich jedoch in den funktionellen Gruppen, die während ihres chemischen Modifizierungsprozesses hinzugefügt werden.
HPMC wird in der Pharmaindustrie häufig als Bindemittel in Tablettenformulierungen und in der Bauindustrie verwendet, um die Verarbeitbarkeit von Mörtel und Klebstoffen zu verbessern. HEMC, wird dagegen häufiger in der Lebensmittelindustrie und bestimmten Baumaterialien eingesetzt. Der Schlüssel zu ihrer Leistung in diesen Anwendungen liegt in ihrer Wasserlöslichkeit Und Auflösungsmodi.
Der Löslichkeitseigenschaften Die Zusammensetzung von HPMC und HEMC ist entscheidend für die gewünschte Konsistenz, Viskosität und Textur des Endprodukts. Lösen sich diese Polymere nicht richtig in Wasser, kann dies zu inkonsistenter Produktleistung, Verklumpung oder schlechter Textur führen, was die Verwendung in Formulierungen erschwert. Eine unzureichende Auflösung kann beispielsweise in Baumaterialien zu einer schwachen Haftung führen, während sie in Arzneimitteln zu inkonsistenten Wirkstofffreisetzungsraten führen kann.
Durch das Verständnis dieser Löslichkeitseigenschaften können Industrien die Verwendung von HPMC und HEMC in ihren Formulierungen optimieren und so eine gleichbleibende Leistung und Produktqualität sicherstellen.
Polymer | Häufige Anwendungen | Löslichkeit Bedeutung |
---|---|---|
HPMC | Pharma, Bau, Lebensmittel | Beeinflusst die Wirkstofffreisetzung, Haftung und Textur |
HEMC | Lebensmittel, Bau, Farben | Beeinflusst Emulgierung, Viskosität, Stabilität |
2. Wie wirken sich Wasserlöslichkeit und Auflösungsmodus auf HPMC und HEMC aus?
Wasserlöslichkeit und Auflösungsmodus sind entscheidende Faktoren für die Wirksamkeit von HPMC und HEMC in verschiedenen industriellen Anwendungen. Die Wasserlöslichkeit definiert, wie gut sich das Polymer in Wasser auflöst, während sich der Auflösungsmodus darauf bezieht, wie sich das Polymer während des Auflösungsprozesses verhält, was wiederum das Verhalten der endgültigen Lösung oder des Produkts beeinflusst.
Für HPMC und HEMC, der Auflösungsmodus beeinflusst ihre Funktionalität in einem Produkt. Wenn HPMC in Wasser gelöst wird, bildet es eine gelartige Struktur Die Viskosität der Lösung lässt sich steuern. In der Pharmaindustrie ist dies besonders wichtig, da es sicherstellt, dass das Polymer eine gleichmäßige Gelmatrix für eine kontrollierte Wirkstofffreisetzung bildet. Der Auflösungsmodus beeinflusst, wie schnell sich das Polymer auflöst und wie gleichmäßig es sich in die Formulierung integriert. Eine ungleichmäßige Auflösung kann zu einer ungleichmäßigen Wirkstoffabgabe führen, was bei kritischen medizinischen Anwendungen problematisch sein kann.
In Lebensmitteln, der Auflösungsmodus beeinflusst die Textur und das Mundgefühl des Produkts. Wenn HPMC beispielsweise in Soßen oder Dressings verwendet wird, seine Löslichkeit bestimmt die Konsistenz des Endprodukts. Wenn HEMC in einem emulgierten Produkt verwendet wirdDie Auflösungsgeschwindigkeit beeinflusst, wie gut das Produkt seine glatte Textur behält. Eine schlechte Löslichkeit kann zu Klumpen oder ungleichmäßigen Emulsionen führen, was die Produktqualität und das Verbrauchererlebnis beeinträchtigt.
Im Bauwesen ist die Löslichkeit von HPMC spielt eine entscheidende Rolle bei der Formulierung von Mörtel und Klebstoffen. Die Löslichkeit des Polymers sorgt für eine geschmeidige Konsistenz und verhindert Verklumpen, wodurch sich das Verteilen und Auftragen erleichtert. Ohne ausreichende Auflösung kann die Mischung zu dick oder ungleichmäßig werden, was das Auftragen erschwert und die Haftkraft verringert.
Industrie | Polymer | Auswirkungen auf die Löslichkeit |
---|---|---|
Pharmazeutische | HPMC | Kontrolliert die Wirkstofffreisetzung und die Tablettenkonsistenz |
Essen | HEMC | Beeinflusst Textur, Emulgierung und Mundgefühl |
Konstruktion | HPMC | Beeinflusst Verarbeitbarkeit, Haftung und Konsistenz |
3. Welche Faktoren beeinflussen die Löslichkeit und Auflösung von HPMC und HEMC?
Die Löslichkeit und Auflösung von HPMC und HEMC werden von mehreren Faktoren beeinflusst, darunter Temperatur, Wasser-Polymer-Verhältnis und Rührgeschwindigkeit. Die Temperatur ist einer der wichtigsten Faktoren, da es direkten Einfluss darauf hat, wie schnell sich das Polymer in Wasser auflöst. Höhere Temperaturen allgemein den Auflösungsprozess beschleunigen, es muss jedoch darauf geachtet werden, den idealen Bereich nicht zu überschreiten, da zu hohe Temperaturen das Polymer zersetzen können, was zu einer verringerten Löslichkeit und Wirksamkeit führt.
Ein weiterer zu berücksichtigender Faktor ist die Wasser-Polymer-Verhältnis. Zu viel Polymer und zu wenig Wasser können zu einer unvollständigen Auflösung führen, was zu Verklumpungen und einer dickeren, viskoseren Lösung führt. Andererseits zu wenig Polymer führt zu einer dünnflüssigeren Lösung Dies führt möglicherweise nicht zur gewünschten Dicke oder Textur. Daher ist das richtige Verhältnis für eine optimale Auflösung unerlässlich.
Auch die Rührgeschwindigkeit spielt eine entscheidende Rolle um sicherzustellen, dass sich HPMC und HEMC gleichmäßig auflösen. Wenn das Rühren zu schnell ist, kann dadurch Luft in die Lösung gelangen, wodurch Blasen entstehen, die die Viskosität und Konsistenz beeinträchtigen. Zu langsames Rühren kann zu einer unvollständigen Auflösung führen. Idealerweise sollte eine moderate, konstante Rührgeschwindigkeit beibehalten werden, um sicherzustellen, dass die Lösung glatt und gleichmäßig bleibt.
Durch die Kontrolle dieser Faktoren können Hersteller sicherstellen, dass sich HPMC und HEMC richtig auflösen und in ihren Anwendungen die gewünschten Ergebnisse erzielen, sei es in Arzneimitteltabletten, Lebensmitteln oder Baumaterialien.
Faktor | Auswirkungen | Bewährte Vorgehensweise |
---|---|---|
Temperatur | Schnellere Auflösung bei höheren Temperaturen | Halten Sie die Temperatur zwischen 60 °C und 80 °C |
Wasser-Polymer-Verhältnis | Beeinflusst Viskosität und Auflösung | Passen Sie das Verhältnis für eine optimale Lösungsdicke an |
Rührgeschwindigkeit | Zu schnell kann Luftblasen verursachen, zu langsam führt zu unvollständiger Auflösung | Mit gleichmäßiger, mäßiger Geschwindigkeit rühren |
4. Welche Leistung erbringen HPMC und HEMC in verschiedenen industriellen Anwendungen?
HPMC und HEMC werden in zahlreichen Branchen eingesetzt, die jeweils spezifische Anforderungen stellen. In der PharmaindustrieHPMC wird häufig als Bindemittel und Wirkstoff zur kontrollierten Freisetzung in Tablettenformulierungen verwendet. Seine Löslichkeitseigenschaften sind entscheidend für die kontrollierte Freisetzung der Wirkstoffe in Tabletten. In dieser Branche, müssen die Auflösungsraten präzise sein, um sicherzustellen, dass das Arzneimittel dem Patienten wirksam zugeführt wird.
Im Lebensmittelindustrie, HPMC und HEMC dienen als Emulgatoren und Verdickungsmittel. Ihre Wasserlöslichkeit ist entscheidend zur Erhaltung der Konsistenz von Lebensmitteln wie Soßen, Dressings und Eiscreme. Für EmulsionenDie Löslichkeit sorgt dafür, dass die Inhaltsstoffe gleichmäßig verteilt bleiben, eine Trennung verhindert wird und das Endprodukt eine glatte Textur aufweist.
Im BauindustrieHPMC wird hauptsächlich in Trockenmörtel, Putzen und Klebstoffen verwendet. Die Löslichkeit von HPMC sorgt dafür, dass der Mörtel leicht zu mischen, zu verteilen und aufzutragen istDie richtige Auflösung trägt dazu bei, die gewünschte Konsistenz zu erreichen und stellt sicher, dass der Klebstoff bei der Anwendung eine starke Verbindung bildet. Ohne ausreichende Löslichkeit kann die Leistung dieser Materialien beeinträchtigt werden, was zu einer verringerten Wirksamkeit und Haltbarkeit führt.
Industrie | Anwendung | Rolle der Löslichkeit |
---|---|---|
Pharmazeutische | Tablets | Kontrolliert die Wirkstofffreisetzung und sorgt für eine gleichmäßige Bindung |
Essen | Saucen, Dressings, Eis | Erhält die Textur und verhindert die Trennung |
Konstruktion | Mörtel, Klebstoffe | Beeinflusst die Verarbeitbarkeit und die Bindungsstärke |
5. Was sind die besten Methoden, um eine optimale Wasserlöslichkeit in HPMC und HEMC zu erreichen?
Um eine optimale Wasserlöslichkeit in HPMC und HEMC zu erreichen, sind die richtige Methode und die richtigen Bedingungen erforderlich. Auflösung in heißem Wasser wird häufig verwendet, um diese Polymere schnell aufzulösen, insbesondere wenn eine höhere Viskosität erforderlich ist. Durch Erhitzen von Wasser auf den optimalen Bereich (60 °C bis 80 °C) können sich HPMC und HEMC effizient auflösen und bilden eine gelartige Konsistenz, die ideal für Pharmazeutika und Bauanwendungen ist. Auflösung in heißem Wasser ermöglicht einen schnellen Abbau des Polymers, was besonders nützlich ist, wenn eine schnelle, gleichmäßige Lösung benötigt wird.
Auflösung in kaltem Wasser wird in Anwendungen eingesetzt, in denen empfindlichere Formulierungen erforderlich sind, beispielsweise in Lebensmittelprodukten. Bei diesem Verfahren wird das Polymer nach und nach in Wasser bei Raumtemperatur gegeben und vorsichtig gerührt.Es trägt dazu bei, die Integrität des Polymers zu erhalten und gleichzeitig eine glatte, klumpenfreie Lösung zu gewährleisten. Die Auflösung in kaltem Wasser kann zwar länger dauern, sorgt aber dafür, dass das Endprodukt eine glattere Textur aufweist, insbesondere bei Emulsionen und Stabilisatoren.
Für großindustrielle Anwendungen kontinuierliches Rühren und Mischen Stellen Sie sicher, dass sich das Polymer gleichmäßig auflöst. Diese Methode wird häufig in der Pharma- und Lebensmittelherstellung eingesetzt, wo große Mengen schnell und gleichmäßig aufgelöst werden müssen. Mit spezielle Mischgeräte stellt sicher, dass der Auflösungsprozess effizient ist und die endgültige Lösung homogen ist.
Verfahren | Temperatur | Anwendung |
---|---|---|
Auflösung in heißem Wasser | 60 °C bis 80 °C | Pharmazeutika, Bauwesen, hohe Viskosität |
Auflösung in kaltem Wasser | Raumtemperatur | Lebensmittel, empfindliche Formulierungen |
Kontinuierliches Rühren | Variiert | Großindustrielle Produktion |
6. Wie können Sie die Viskosität von Lösungen steuern, die HPMC und HEMC enthalten?
Die Kontrolle der Viskosität von Lösungen, die HPMC und HEMC enthalten, ist in vielen industriellen Anwendungen von entscheidender Bedeutung. Das Wasser-Polymer-Verhältnis beeinflusst direkt die Viskosität der LösungEine Erhöhung der HPMC- oder HEMC-Konzentration führt zu einer dickeren Lösung, eine Verringerung der Konzentration zu einer dünneren Lösung. Durch Anpassung des Wasser-Polymer-Verhältnisses können Hersteller die Viskosität steuern, um die gewünschte Konsistenz zu erreichen.
Auch die Temperatur spielt eine wichtige Rolle bei der Viskositätskontrolle. Höhere Temperaturen neigen dazu, die Viskosität zu verringern, was bei Anwendungen nützlich sein kann, bei denen eine dünnere Lösung benötigt wird. Umgekehrt Abkühlen der Lösung kann die Viskosität erhöhen, wodurch es sich besser für dickere Formulierungen eignet. Es ist wichtig, die Temperatur in einem optimalen Bereich zu halten, um eine konstante Viskosität zu erreichen.
Rührgeschwindigkeit beeinflusst auch die Viskosität. Schnellere Rührgeschwindigkeiten können die Viskosität senken, während langsamere Rührgeschwindigkeiten zu dickeren Lösungen führen. Durch Anpassen der Rührgeschwindigkeit und Aufrechterhaltung eines optimalen Temperatur- und Wasser-Polymer-Verhältnisses können Sie die Viskosität von HPMC- und HEMC-Lösungen präzise steuern.
Faktor | Einfluss auf die Viskosität | Lösung |
---|---|---|
Wasser-Polymer-Verhältnis | Höhere Konzentration erhöht die Viskosität | Passen Sie die gewünschte Dicke an |
Temperatur | Höhere Temperaturen senken die Viskosität | Halten Sie die optimale Temperatur für Konsistenz aufrecht |
Rührgeschwindigkeit | Höhere Geschwindigkeiten, geringere Viskosität | Bei mäßiger Geschwindigkeit rühren, um Luftblasen zu vermeiden |
7. Welche häufigen Fehler sollten beim Auflösen von HPMC und HEMC vermieden werden?
Selbst erfahrenen Formulierern können beim Auflösen von HPMC und HEMC Fehler unterlaufen, die zu einer suboptimalen Leistung führen. Ein häufiger Fehler besteht darin, das Polymer zu schnell zum Wasser hinzuzufügen., was zu Verklumpungen und ungleichmäßiger Auflösung führen kann. Am besten ist es, das Polymer unter ständigem Rühren nach und nach zuzugeben. um eine gleichmäßige Hydratisierung zu gewährleisten.
Ein weiterer Fehler ist die Verwendung falsche Wassertemperatur. Zu heißes oder zu kaltes Wasser kann den Auflösungsprozess behindern, was zu inkonsistenten Ergebnissen führt. Halten Sie die Wassertemperatur im idealen Bereich (60 °C bis 80 °C) um eine optimale Auflösung zu erreichen.
Auch die Rührgeschwindigkeit ist entscheidend. Wenn das Rühren zu schnell istkönnen sich Luftblasen in der Lösung bilden, die ihre Viskosität und Textur beeinträchtigen. Andererseits langsames Rühren kann zu einer unvollständigen Auflösung führenAm besten rührt man mit einer konstanten, moderaten Geschwindigkeit, um Lufteinschlüsse zu vermeiden und eine gleichmäßige Auflösung sicherzustellen.
Fehler | Ursache | Lösung |
---|---|---|
HPMC zu schnell hinzufügen | Verklumpung | Unter ständigem Rühren nach und nach hinzufügen |
Falsche Temperatur | Langsame oder unvollständige Auflösung | Halten Sie die Wassertemperatur zwischen 60 °C und 80 °C |
Hohe Rührgeschwindigkeit | Luftblasen, ungleichmäßige Viskosität | Für eine optimale Auflösung bei mäßiger Geschwindigkeit rühren |
8. Wie beheben Sie Löslichkeitsprobleme in HPMC und HEMC?
Beim Auflösen von HPMC und HEMC können Löslichkeitsprobleme auftreten, insbesondere beim Arbeiten mit großen Chargen. Ein häufiges Problem ist die Verklumpung oder unvollständige Auflösung, was durch zu schnelles Hinzufügen des Polymers oder die Verwendung von zu kaltem Wasser verursacht werden kann. Zur Fehlerbehebung erhöhen Sie die Rührgeschwindigkeit oder erhöhen Sie die Wassertemperatur leicht um eine bessere Auflösung zu fördern.
Die Wasserqualität ist ein weiterer Faktor die die Löslichkeit beeinträchtigen können. Verunreinigungen im Wasser können den Lösungsprozess behindern und zu inkonsistenten Ergebnissen führen. gereinigtes oder destilliertes Wasser wird immer empfohlen, um die besten Ergebnisse zu erzielen.
Wenn die Lösung zu dick oder zu dünn ist, Einstellen des Wasser-Polymer-Verhältnisses kann zur Lösung des Problems beitragen. Eine Erhöhung der Wassermenge verdünnt die Lösung, während die Zugabe von mehr Polymer sie verdickt.Durch kleine Anpassungen können Sie sicherstellen, dass sich HPMC und HEMC richtig auflösen und die gewünschten Spezifikationen erfüllen.
Ausgabe | Ursache | Lösung |
---|---|---|
Klumpenbildung | Schnelle Zugabe, unzureichendes Rühren | HPMC nach und nach hinzufügen und ständig rühren |
Schlechte Auflösung | Wasserverunreinigungen | Verwenden Sie gereinigtes oder destilliertes Wasser |
Falsche Viskosität | Falsches Verhältnis oder falsche Rührgeschwindigkeit | Passen Sie das Verhältnis oder die Rührgeschwindigkeit an |
9. Gibt es Alternativen zu HPMC und HEMC mit ähnlichen Löslichkeitseigenschaften?
Während HPMC und HEMC weit verbreitet sind, können mehrere Alternativen ähnliche Löslichkeitseigenschaften bieten. Methylcellulose (MC) wird häufig anstelle von HPMC verwendet, insbesondere in der Bau- und Pharmaindustrie. Carboxymethylcellulose (CMC) ist eine weitere Alternative, die in Lebensmittel- und Arzneimittelformulierungen verwendet wird, insbesondere wenn Kaltwasserlöslichkeit erforderlich ist.
Ethylcellulose ist eine weitere Option, obwohl es im Vergleich zu HPMC und HEMC weniger wasserlöslich ist. Es wird typischerweise in pharmazeutischen Beschichtungen und anderen Spezialanwendungen verwendet.
Trotz der Verfügbarkeit von Alternativen HPMC und HEMC bleiben beliebte Optionen aufgrund ihrer überlegenen Löslichkeit, Vielseitigkeit und gleichbleibenden Leistung in einem breiten Anwendungsspektrum.
Alternative | Hauptmerkmale | Anwendungen |
---|---|---|
Methylcellulose | Ähnliche Binde- und Verdickungseigenschaften | Pharmazeutika, Bau |
Carboxymethylcellulose | Kaltwasserlöslichkeit, Verdickung | Lebensmittel, Pharmazeutika |
Ethylcellulose | Starke filmbildende Eigenschaften | Pharmazeutika, Beschichtungen |
Abschluss
Zusammenfassend lässt sich sagen, dass die Wasserlöslichkeit und die Auflösungseigenschaften von HPMC und HEMC entscheidend für ihre Wirksamkeit in verschiedenen Branchen sind. Ob für die Freisetzung pharmazeutischer Wirkstoffe, die Kontrolle der Lebensmitteltextur oder die Konsistenz von Baumaterialien – das Verständnis und die Kontrolle dieser Eigenschaften gewährleisten eine optimale Produktleistung. Durch den Einsatz der richtigen Auflösungstechniken, die Kontrolle wichtiger Faktoren wie Temperatur, Wasserverhältnis und Rührgeschwindigkeit sowie die Behebung häufiger Probleme können Branchen das Potenzial von HPMC und HEMC in ihren Formulierungen voll ausschöpfen.
Häufig gestellte Fragen
Frage 1: Was ist HPMC und HEMC?
HPMC und HEMC sind wasserlösliche Cellulosederivate, die in verschiedenen Branchen zum Verdicken, Binden, Stabilisieren und Emulgieren verwendet werden.
Q2: Wie wirkt sich die Wasserlöslichkeit auf die Leistung von HPMC und HEMC aus?
Die Wasserlöslichkeit beeinflusst direkt die Viskosität, Textur und Funktionalität des Endprodukts und stellt sicher, dass es die gewünschten Leistungsstandards erfüllt.
Drittes Quartal: Welche Faktoren beeinflussen die Löslichkeit und Auflösung von HPMC und HEMC?
Faktoren wie Temperatur, Wasser-Polymer-Verhältnis und Rührgeschwindigkeit spielen eine entscheidende Rolle bei der Gewährleistung einer korrekten Auflösung der Polymere.
Viertes Quartal: Welche Fehler sollten beim Auflösen von HPMC und HEMC am häufigsten vermieden werden?
Zu den häufigsten Fehlern zählen das zu schnelle Hinzufügen des Polymers, die Verwendung falscher Wassertemperaturen und zu schnelles Rühren, was den Auflösungsprozess beeinträchtigen kann.
Frage 5: Gibt es Alternativen zu HPMC und HEMC für ähnliche Anwendungen?
Ja, Alternativen wie Methylcellulose und Carboxymethylcellulose bieten ähnliche Eigenschaften, können sich jedoch in Löslichkeit und Anwendungseignung unterscheiden.