Die thermischen Eigenschaften von Hydroxypropylmethylcellulose (HPMC) sind für Hersteller in der Pharma-, Bau- und Lebensmittelindustrie von entscheidender Bedeutung. Bei der Formulierung von Produkten mit HPMC hat das Verständnis des genauen Schmelzverhaltens direkten Einfluss auf Verarbeitungsentscheidungen, die Stabilität des Endprodukts und die Anwendungsleistung. Dieser Artikel untersucht die spezifischen Schmelzpunktbereiche von HPMC, untersucht Faktoren, die das thermische Verhalten beeinflussen, und bietet praktische Hinweise zur Optimierung der Verarbeitungstemperaturen. Durch die Beherrschung der thermischen Eigenschaften von HPMC können Sie Fertigungsprobleme vermeiden, die Haltbarkeit von Produkten verlängern und eine gleichbleibende Leistung in allen Anwendungen sicherstellen.
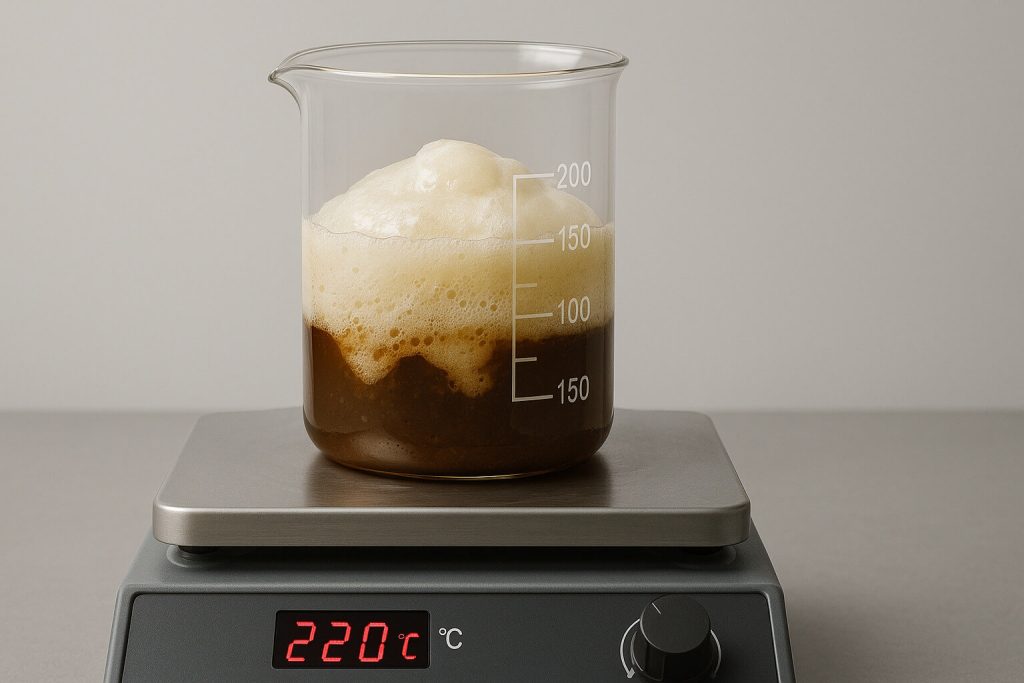
1. Was ist HPMC und warum ist sein Schmelzpunkt wichtig?
Hydroxypropylmethylcellulose (HPMC) ist ein halbsynthetisches, inertes Polymer, das durch chemische Modifizierung aus Cellulose gewonnen wird. Die Cellulose-Grundstruktur wird durch Hydroxypropyl- und Methylgruppen ersetzt, wodurch eine vielseitige Verbindung mit einzigartigen thermischen Eigenschaften entsteht. HPMC erscheint als weißes bis cremefarbenes Pulver, das sich in Wasser löst und klare Lösungen mit je nach Qualität unterschiedlicher Viskosität bildet.
Aber hier ist der kritische Punkt: Das Verständnis des Schmelzverhaltens von HPMC wirkt sich direkt auf Herstellungsprozesse und die Leistung des Endprodukts aus. Im Gegensatz zu kristallinen Materialien mit scharfen Schmelzpunkten weist HPMC aufgrund seiner amorphen Natur und Polymerstruktur ein komplexes thermisches Verhalten auf.
Die Schmelzeigenschaften von HPMC bestimmen die Verarbeitungsparameter in zahlreichen Branchen:
Industrie | Anwendung | Warum der Schmelzpunkt wichtig ist |
---|---|---|
Pharmazeutische | Kontrollierte Freisetzungsmatrizen | Bestimmt die Verarbeitungstemperaturgrenzen bei der Tablettenherstellung |
Konstruktion | Zementzusätze | Beeinflusst die Stabilität beim Mischen mit heißen Zementmischungen |
Essen | Verdickungsmittel | Sorgt für Stabilität beim Koch- und Backvorgang |
Körperpflege | Gelformulierungen | Beeinträchtigt die Produktstabilität während der Herstellung und Lagerung |
Beschichtungen | Filmbildner | Bestimmt die erforderlichen Trocknungs- und Aushärtungstemperaturen |
Die thermische Stabilität von HPMC beeinflusst direkt die Haltbarkeit des Produkts, die Freisetzungskinetik in pharmazeutischen Anwendungen und die strukturelle Integrität von Baumaterialien. Das Polymer beginnt sich bereits lange vor Erreichen seiner Zersetzungstemperatur zu verändern. Daher ist die Kenntnis seines vollständigen thermischen Profils für die ordnungsgemäße Handhabung unerlässlich.
Hersteller müssen bei der Entwicklung von Verarbeitungsprotokollen nicht nur den endgültigen Schmelzpunkt, sondern den gesamten thermischen Übergangsbereich berücksichtigen. Dieses Wissen verhindert Produktfehler, gewährleistet die Konsistenz von Charge zu Charge und optimiert die Fertigungseffizienz.
2. Was ist der tatsächliche Schmelzpunktbereich von HPMC?
HPMC weist im Gegensatz zu kristallinen Substanzen keinen scharfen, klar definierten Schmelzpunkt auf. Stattdessen weist es einen thermischen Übergangsbereich auf, in dem es vor dem vollständigen Schmelzen erweicht. Der konventionelle Schmelzpunktbereich für HPMC in pharmazeutischer Qualität liegt typischerweise zwischen 225 und 230 °C, kann jedoch je nach Qualität und Herstellungsverfahren variieren.
Das sollten Sie wissen HPMC durchläuft mehrere thermische Übergänge, bevor es seinen Schmelzpunkt erreicht. Dazu gehören Wasserverlust, Glasübergang und schließlich Schmelzen, gefolgt von Zersetzung.
In der folgenden Tabelle sind die wichtigsten thermischen Übergangspunkte für Standard-HPMC aufgeführt:
Thermischer Übergang | Temperaturbereich (°C) | Körperliche Veränderungen |
---|---|---|
Wasserverlust | 50-100 | Verdunstung von gebundenem Wasser |
Glasübergang | 170-195 | Erweichung, erhöhte molekulare Mobilität |
Schmelzbereich | 225-230 | Vollständiger Strukturverlust |
Abbaubeginn | 270-290 | Chemischer Abbau, Verfärbung |
Vollständige Degradation | >300 | Verkohlung |
Beim Vergleich von HPMC mit anderen Zellulosederivaten werden seine Schmelzeigenschaften deutlicher:
Cellulosederivat | Schmelzpunktbereich (°C) | Relative thermische Stabilität |
---|---|---|
HPMC | 225-230 | Hoch |
Methylcellulose (MC) | 290-305 | Sehr hoch |
Hydroxyethylcellulose (HEC) | 200-220 | Mäßig |
Carboxymethylcellulose (CMC) | 227-252 | Hoch |
Ethylcellulose (EC) | 160-210 | Mäßig |
Zur Bestimmung der Schmelzpunkte von HPMC wird üblicherweise die Differenzial-Scanning-Kalorimetrie (DSC) verwendet, die den Wärmefluss bei kontrollierten Temperaturerhöhungen misst. Diese Technik zeigt die endothermen Peaks, die mit Schmelzübergängen verbunden sind.
Zu den Faktoren, die die Genauigkeit von Schmelzpunktmessungen beeinflussen, gehören:
- Probenvorbereitungsmethode
- Heizrate während der Analyse
- Bisherige thermische Vorgeschichte der Probe
- Vorhandensein von Zusatzstoffen oder Verunreinigungen
- Feuchtigkeitsgehalt vor der Prüfung
Für praktische Anwendungen betrachten Hersteller häufig den Beginn der Erweichung (ca. 190–200 °C) als praktische Obergrenze für die Verarbeitung und nicht den tatsächlichen Schmelzpunkt, um eine Sicherheitsmarge gegen Abbau zu gewährleisten.
3. Wie wirkt sich die Viskositätsklasse von HPMC auf das Schmelzverhalten aus?
Die Viskositätsklassen von HPMC korrelieren direkt mit dem Molekulargewicht, das die thermischen Eigenschaften, einschließlich des Schmelzverhaltens, maßgeblich beeinflusst. HPMC-Klassen mit höherem Molekulargewicht (höhere Viskosität) weisen im Allgemeinen leicht erhöhte Schmelzpunkte und breitere Schmelzbereiche auf als Sorten mit niedrigerem Molekulargewicht.
Die wichtigste Erkenntnis hier ist Die Wahl der Viskositätsklasse beeinflusst nicht nur die Lösungseigenschaften, sondern auch die thermischen Verarbeitungsparameter. Dieser Zusammenhang ist auf die erhöhte Kettenverschränkung und die intermolekularen Kräfte zurückzuführen, die in HPMC mit höherem Molekulargewicht vorhanden sind.
Die folgende Tabelle veranschaulicht, wie sich unterschiedliche Viskositätsgrade auf die thermischen Eigenschaften auswirken:
HPMC-Viskositätsklasse | Ungefähres Molekulargewicht | Glasübergang (°C) | Schmelzbereich (°C) | Thermische Stabilität |
---|---|---|---|---|
Niedrig (3-15 mPa·s) | 10,000-30,000 | 170-180 | 220-225 | Gut |
Mittel (100-150 mPa·s) | 40,000-60,000 | 175-185 | 225-230 | Besser |
Hoch (4.000–6.000 mPa·s) | 80,000-120,000 | 180-190 | 230-235 | Am besten |
Ultrahoch (>10.000 mPa·s) | >150.000 | 185-195 | 235-240 | Exzellent |
Beim Erhitzen zeigen höhere Viskositätsklassen:
- Höherer Fließwiderstand bei erhöhten Temperaturen
- Höhere Elastizität vor dem Schmelzen
- Langsamere thermische Abbauraten
- Höherer Energiebedarf zum vollständigen Schmelzen
Diese Unterschiede sind besonders wichtig bei Anwendungen wie der Hotmelt-Extrusion, bei der die Verarbeitungstemperaturfenster sorgfältig kontrolliert werden müssen. Niedrigere Viskositätsklassen ermöglichen eine einfachere Verarbeitung bei niedrigeren Temperaturen, weisen in der Endanwendung jedoch möglicherweise eine geringere thermische Stabilität auf.
Bei der Auswahl von HPMC-Typen für thermisch anspruchsvolle Anwendungen müssen Hersteller die Verarbeitbarkeit mit den Anforderungen an die thermische Leistung abwägen. Anwendungen, die längere Zeit hohen Temperaturen ausgesetzt sind, profitieren im Allgemeinen von Typen mit höherer Viskosität. Wer hingegen Wert auf eine einfache Verarbeitbarkeit legt, sollte sich für Alternativen mit niedrigerer Viskosität entscheiden.
4. Was passiert mit HPMC beim Erhitzen?
Beim Erhitzen von HPMC kommt es nicht nur zu einem einfachen Fest-Flüssig-Übergang, sondern zu einer Reihe deutlicher physikalischer und chemischer Veränderungen. Das Verständnis dieses komplexen thermischen Verhaltens ist für die ordnungsgemäße Handhabung und Verarbeitung des Materials unerlässlich.
Was Sie faszinierend finden werden, ist Das einzigartige thermische Gelierungsverhalten unterscheidet HPMC von vielen anderen Polymeren. Dieses Phänomen schafft sowohl Herausforderungen als auch Chancen für verschiedene Anwendungen.
Die thermische Umwandlungssequenz von HPMC läuft wie folgt ab:
Temperaturbereich (°C) | Physischer Zustand | Beobachtbare Änderungen | Molekulare Ereignisse |
---|---|---|---|
25-50 | Festes Pulver | Keine sichtbaren Änderungen | Eingeschränkte Molekularbewegung |
50-100 | Feststoff mit Feuchtigkeitsverlust | Gewichtsreduktion | Wasserverdampfung, Stärkung der Wasserstoffbrücken |
100-170 | Trockener Feststoff | Leichte Verfärbungen beginnen | Anfängliche Kettenentspannung |
170-195 | Glasiger Übergang | Erweichung, erhöhte Klebrigkeit | Deutliche Steigerung der Kettenmobilität |
195-225 | Gummiartiger Zustand | Verformung unter Druck | Die Entwirrung der Kette beginnt |
225-230 | Schmelzen | Strömung unter Druck, Transparenz ändert sich | Vollständiger Verlust der physischen Struktur |
>230 | Geschmolzen/zersetzend | Bräunung, Viskositätsreduzierung | Kettenspaltung, Oxidation |
Beim Erhitzen zeigt HPMC in wässrigen Lösungen einen einzigartigen thermischen Gelierungsmechanismus. Bei niedrigeren Temperaturen löst sich HPMC auf und bildet klare Lösungen. Bei steigender Temperatur (typischerweise etwa 65–80 °C, je nach Qualität) bildet die Lösung aufgrund hydrophober Wechselwirkungen zwischen Methoxygruppen ein Gel. Weiteres Erhitzen führt schließlich zur Ausfällung.
Dieses thermische Gelierungsverhalten schafft ein temperaturempfindliches System, das nützlich ist für:
- Systeme zur kontrollierten Wirkstofffreisetzung
- Temperaturempfindliche Lebensmittelverdicker
- Intelligente Materialien, die auf Umweltveränderungen reagieren
Bei der Verarbeitung müssen Hersteller mehrere kritische Faktoren berücksichtigen:
- Die Glasübergangstemperatur (Tg) stellt den Punkt dar, an dem HPMC von einem starren glasartigen Zustand in einen flexibleren gummiartigen Zustand übergeht
- Das Verarbeitungsfenster liegt typischerweise zwischen Tg und 20-30°C unter dem Beginn der Degradation
- Längere Einwirkung auch unterhalb der Schmelztemperatur kann zu einer allmählichen Zersetzung führen
- Die thermische Vorgeschichte beeinflusst das nachfolgende thermische Verhalten
Durch das Verständnis dieser Übergänge können Verarbeiter die Temperaturprofile während der Herstellung optimieren und so sowohl eine unzureichende Erwärmung (die zu einer unvollständigen Verarbeitung führt) als auch eine übermäßige Erwärmung (die zu einer Verschlechterung führt) vermeiden.
5. Welchen Einfluss haben Substitutionsgrade auf die Schmelzeigenschaften von HPMC?
Das Substitutionsmuster der Hydroxypropyl- und Methoxygruppen am Celluloserückgrat bestimmt maßgeblich die thermischen Eigenschaften von HPMC, einschließlich des Schmelzverhaltens. Diese Substitutionen stören die Wasserstoffbrückenbindung in der nativen Cellulosestruktur und verändern so thermische Übergänge und Löslichkeitseigenschaften.
Das entscheidende Detail, das man verstehen muss, ist Das Verhältnis und die Verteilung dieser Substituenten können präzise angepasst werden, um spezifische thermische Profile für verschiedene Anwendungen zu erreichen. Diese Anpassungsfähigkeit macht HPMC zu einem außergewöhnlich vielseitigen Polymer.
HPMC-Typen werden mithilfe eines vierstelligen USP/NF- oder EP-Bezeichnungssystems klassifiziert, das die Substitutionsgrade angibt:
HPMC-Typ | Methoxylgehalt (%) | Hydroxypropyl-Gehalt (%) | Typischer Schmelzbereich (°C) | Thermische Eigenschaften |
---|---|---|---|---|
1828 | 16.5-20.0 | 23.0-32.0 | 215-225 | Niedriger schmelzend, hydrophiler |
2208 | 19.0-24.0 | 4.0-12.0 | 220-230 | Ausgeglichene thermische Eigenschaften |
2906 | 27.0-30.0 | 4.0-7.5 | 225-235 | Höher schmelzend, weniger hydrophil |
2910 | 28.0-30.0 | 7.0-12.0 | 230-240 | Höchster Schmelzpunkt |
Die Methoxylsubstitution beeinflusst vor allem:
- Thermische Beständigkeit (ein höherer Methoxylgehalt erhöht im Allgemeinen den Schmelzpunkt)
- Löslichkeit in organischen Lösungsmitteln
- Oberflächenaktivität und Grenzflächeneigenschaften
Gleichzeitig beeinflusst die Hydroxypropylsubstitution:
- Wasserlöslichkeit (höherer Hydroxypropylgehalt erhöht die Wasserlöslichkeit)
- Gelierung bei niedrigerer Lösungstemperatur
- Flexibilität der Polymerkette
Das Verteilungsmuster dieser Substituenten entlang der Cellulosekette (blockartig oder zufällig) beeinflusst das thermische Verhalten zusätzlich. Heterogenere Substitutionsmuster führen typischerweise zu breiteren Schmelzbereichen als homogene Substitutionen.
Für Anwendungen, die eine präzise Temperaturregelung erfordern, können Hersteller spezifische HPMC-Typen auswählen oder sogar individuelle Substitutionsmuster von Lieferanten anfordern. Dies ermöglicht eine Feinabstimmung von:
- Verarbeitungstemperaturfenster
- Thermische Gelierungstemperaturen
- Wärmestabilität während der Lagerung
- Schmelzviskositätseigenschaften
Durch das Verständnis dieser Struktur-Eigenschafts-Beziehungen können Formulierer die optimale HPMC-Qualität für spezifische thermische Verarbeitungsanforderungen auswählen und dabei die Leistungsanforderungen mit den Verarbeitungsbeschränkungen in Einklang bringen.
6. Was sind die besten Verarbeitungstemperaturen für HPMC?
Um optimale Verarbeitungstemperaturen für HPMC zu bestimmen, müssen die effektive Materialumwandlung und die Risiken der thermischen Zersetzung abgewogen werden. Der ideale Temperaturbereich variiert erheblich je nach Herstellungsprozess, HPMC-Qualität und den gewünschten Endprodukteigenschaften.
Folgendes ist am wichtigsten: Die Einhaltung des sicheren Verarbeitungsfensters verhindert Qualitäts- und Geräteprobleme und maximiert gleichzeitig die Produktionseffizienz. Dieses Fenster variiert je nach Anwendungsmethode.
In der folgenden Tabelle sind die empfohlenen Temperaturbereiche für gängige HPMC-Verarbeitungsmethoden aufgeführt:
Verarbeitungsmethode | Empfohlener Temperaturbereich (°C) | Kritische Überlegungen | Qualitätsindikatoren |
---|---|---|---|
Hot-Melt-Extrusion | 140-180 | Verweilzeit, Schergeschwindigkeit | Klarheit, Degradationsfarbe |
Sprühtrocknung | Einlass: 170-210, Auslass: 70-100 | Zerstäubungsparameter | Partikelmorphologie, Feuchtigkeitsgehalt |
Filmcasting | 60-90 | Trocknungsrate, Luftstrom | Filmgleichmäßigkeit, Restlösemittel |
Tablettenkompression | 20-30 | Druckkraft | Härte, Zerfallszeit |
Nassgranulierung | 50-70 | Bindemittelkonzentration | Granulatgrößenverteilung |
Beschichtungsanwendungen | 40-60 | Lösungskonzentration | Beschichtungsgleichmäßigkeit, Haftung |
Bei der Hotmelt-Extrusion, einem thermisch besonders anspruchsvollen Verfahren, beeinflussen mehrere Faktoren das optimale Temperaturprofil:
- Schneckendesign und -konfiguration
- Verweilzeit im Extruder
- Vorhandensein von Weichmachern oder anderen Zusatzstoffen
- HPMC-Substitutionstyp und Viskositätsgrad
- Gewünschte Freisetzungseigenschaften des Endprodukts
Um eine thermische Verschlechterung während der Verarbeitung zu vermeiden, sollten Hersteller die folgenden bewährten Verfahren umsetzen:
- Minimieren Sie die Verweilzeit bei erhöhten Temperaturen
- Verwenden Sie Temperaturprofile mit allmählichen Anstiegen statt plötzlichen Sprüngen
- Integrieren Sie bei Bedarf Antioxidantien
- Überwachen Sie Drehmoment und Druck auf Anzeichen von Verschlechterung
- Schnelles Abkühlen nach Hochtemperaturverarbeitung
- Validieren Sie jede Charge mit thermischen Analysetechniken
Die Prozessvalidierung sollte Tests auf Folgendes umfassen:
- Farbveränderungen (Gelbfärbung deutet auf Abbau hin)
- Viskositätsreduzierung (Kettenspaltung)
- Veränderte Auflösungsprofile
- Änderungen der mechanischen Eigenschaften
- Unerwartete Freigabeeigenschaften
Durch sorgfältige Kontrolle der Verarbeitungstemperaturen innerhalb der empfohlenen Bereiche können Hersteller die HPMC-Funktionalität aufrechterhalten und gleichzeitig die gewünschten Produkteigenschaften und Verarbeitungseffizienz erreichen.
7. Wie können Sie die Schmelzeigenschaften von HPMC testen und überprüfen?
Präzise Tests und Überprüfungen der thermischen Eigenschaften von HPMC gewährleisten konsistente Herstellungsprozesse und eine hohe Leistungsfähigkeit des Endprodukts. Verschiedene Analyseverfahren liefern ergänzende Informationen zu Schmelzverhalten, thermischen Übergängen und Stabilität.
Was Sie erkennen müssen, ist Eine umfassende thermische Charakterisierung erfordert mehrere Prüfmethoden, da keine einzelne Technik alle relevanten thermischen Eigenschaften erfasst. Dieser multimethodische Ansatz liefert ein vollständiges thermisches Profil für die Qualitätskontrolle und Fehlerbehebung.
Die folgende Tabelle fasst die wichtigsten Analysemethoden zur thermischen Charakterisierung von HPMC zusammen:
Analytische Methode | Bereitgestellte Informationen | Stichprobengröße | Temperaturbereich (°C) | Hauptvorteile |
---|---|---|---|---|
Differenz-Scanning-Kalorimetrie (DSC) | Glasübergang, Schmelzübergänge, Wärmekapazität | 2-10 mg | -90 bis 550 | Hohe Empfindlichkeit gegenüber thermischen Übergängen |
Thermogravimetrische Analyse (TGA) | Gewichtsverlust, Zersetzungstemperatur, Feuchtigkeitsgehalt | 5-20 mg | 25 bis 1000 | Quantifiziert Abbau und Feuchtigkeit |
Dynamisch-mechanische Analyse (DMA) | Viskoelastische Eigenschaften, Moduländerungen mit der Temperatur | 10-500 mg | -150 bis 500 | Misst Änderungen mechanischer Eigenschaften |
Heiztischmikroskopie | Optische Veränderungen beim Erhitzen | <1 mg | 25 bis 350 | Direkte Beobachtung physikalischer Veränderungen |
Rheometrie | Schmelzviskosität, Gelierungstemperatur | 1-2 g | -20 bis 300 | Misst die Fließeigenschaften während des Erhitzens |
Für die routinemäßige Qualitätskontrolle werden am häufigsten DSC und TGA eingesetzt. Ein Standard-DSC-Protokoll für HPMC umfasst typischerweise:
- Probenäquilibrierung bei 25 °C
- Erster Heizdurchgang auf 250 °C mit 10 °C/min
- Abkühlung auf 25°C mit 20°C/min
- Zweiter Heizscan auf 250 °C bei 10 °C/min (zeigt thermische Verlaufseffekte)
Bei der Interpretation der Ergebnisse der thermischen Analyse müssen folgende Schlüsselparameter ausgewertet werden:
- Glasübergangstemperatur (Tg): Typischerweise 170–195 °C für HPMC
- Beginn des Schmelzens: Normalerweise 10–15 °C unter der maximalen Schmelztemperatur
- Maximale Schmelztemperatur: Typischerweise 225–230 °C für Standardqualitäten
- Schmelzenthalpie: Gibt den Organisationsgrad der Polymerstruktur an
- Beginn der Degradation: Sollte bei hochwertigem Material >270°C sein
Zu den üblichen Fehlerbehebungsszenarien bei inkonsistentem Schmelzverhalten gehören:
- Verschobene Schmelztemperaturen: Deutet oft auf Schwankungen im Feuchtigkeitsgehalt oder unterschiedliche Substitutionsmuster hin
- Verbreiterte Schmelzpeaks: Können auf Veränderungen der Molekulargewichtsverteilung oder teilweisen Abbau hindeuten
- Reduzierte Schmelzenthalpie: Könnte auf eine frühere thermische Vorgeschichte oder Verarbeitungsschäden hinweisen
- Frühzeitiger Abbau: Mögliche Kontaminations- oder Oxidationsprobleme
Durch die Festlegung von Spezifikationsgrenzen für thermische Eigenschaften wird die Konsistenz von Charge zu Charge sichergestellt und potenzielle Herstellungsprobleme werden erkannt, bevor sie die Leistung des Endprodukts beeinträchtigen.
Abschluss
Das Verständnis des genauen Schmelzverhaltens von HPMC – typischerweise im Bereich von 225–230 °C mit frühen thermischen Übergängen ab etwa 170 °C – liefert Herstellern das nötige Wissen für eine optimale Verarbeitung und Anwendungsentwicklung. Indem Sie erkennen, wie sich Viskositätsklassen, Substitutionsmuster und Verarbeitungsbedingungen auf die thermischen Eigenschaften auswirken, können Sie kostspielige Produktionsfehler und Probleme mit der Produktstabilität vermeiden. Die hier beschriebenen umfassenden thermischen Prüfmethoden ermöglichen eine präzise Qualitätskontrolle und Fehlerbehebung. Kontaktieren Sie noch heute das technische Team von Morton, um fachkundige Beratung zur Auswahl und Verarbeitung der richtigen HPMC-Sorte für Ihre spezifischen thermischen Anforderungen zu erhalten. Unsere spezialisierten Polymerwissenschaftler unterstützen Sie bei der Entwicklung maßgeschneiderter HPMC-Formulierungen mit präzise abgestimmten thermischen Profilen, die auch Ihren anspruchsvollsten Anwendungsanforderungen gerecht werden.
FAQ-Bereich
F1: Hält HPMC den Sterilisationstemperaturen im Autoklaven stand?
Standard-HPMC-Typen halten Autoklavenbedingungen (121 °C, Dampfdruck) in der Regel nicht ohne Zersetzung stand. Obwohl das Polymer bei Autoklaventemperaturen nicht vollständig schmilzt, kann eine längere Einwirkung zu teilweiser Zersetzung, reduzierter Viskosität und veränderten Leistungseigenschaften führen. Für Anwendungen, die eine Sterilisation erfordern, sollten Sie Typen mit höherem Methoxylgehalt (2906 oder 2910) oder alternative Sterilisationsmethoden wie Gammabestrahlung oder Ethylenoxidbehandlung in Betracht ziehen.
F2: Ändert sich der Schmelzpunkt von HPMC, wenn es mit anderen Polymeren gemischt wird?
Ja, das Mischen von HPMC mit anderen Polymeren verändert typischerweise dessen Schmelzverhalten. Kompatible Polymere können mischbare Mischungen mit mittleren Schmelzpunkten der beiden Komponenten bilden. Weichmacher wie Polyethylenglykol oder Glycerin senken den Glasübergang und die scheinbare Schmelztemperatur durch Erhöhung der Kettenbeweglichkeit. Inkompatible Polymere bilden phasengetrennte Systeme mit unterschiedlichen thermischen Übergängen für jede Komponente. Diese Wechselwirkungen müssen im Einzelfall durch eine thermische Analyse der spezifischen Mischungszusammensetzung bewertet werden.
F3: Wie wirkt sich der Feuchtigkeitsgehalt auf das Schmelzverhalten von HPMC aus?
Feuchtigkeit beeinflusst das thermische Verhalten von HPMC erheblich, da sie als Weichmacher wirkt. Ein höherer Feuchtigkeitsgehalt senkt die Glasübergangstemperatur und kann den Schmelzpunkt um 10–20 °C senken. Wassermoleküle stören die Wasserstoffbrückenbindung zwischen Polymerketten und erhöhen so die Molekülbeweglichkeit bei niedrigeren Temperaturen. Für eine konsistente thermische Verarbeitung sollte der Feuchtigkeitsgehalt standardisiert sein, typischerweise unter 5%. Eine ordnungsgemäße Trocknung vor der thermischen Analyse oder Verarbeitung gewährleistet reproduzierbare Ergebnisse und verhindert Verarbeitungsprobleme wie Schaumbildung oder unregelmäßiges Schmelzen.
F4: Was passiert, wenn HPMC über seinem Schmelzpunkt verarbeitet wird?
Die Verarbeitung von HPMC oberhalb seines Schmelzpunkts (> 230 °C) führt zu einem schnellen thermischen Abbau durch Kettenspaltung, Oxidation und Verfärbung. Dieser Abbau führt zu reduziertem Molekulargewicht, verringerter Lösungsviskosität, veränderten Auflösungsprofilen und potenziell schädlichen Abbauprodukten. Das Material verfärbt sich von weiß nach gelbbraun und verliert seine funktionellen Eigenschaften. Nach dem Abbau ist eine Wiederherstellung nicht mehr möglich. Halten Sie die Verarbeitungstemperaturen stets mindestens 30–50 °C unter dem Schmelzpunkt und achten Sie auf eine minimale Verweilzeit bei erhöhten Temperaturen, um die HPMC-Funktionalität zu erhalten.
F5: Gibt es signifikante Unterschiede beim Schmelzpunkt zwischen HPMC-Lieferanten?
Ja, HPMC verschiedener Lieferanten kann trotz identischer Sortenbezeichnungen Schmelzpunktunterschiede von 5–15 °C aufweisen. Diese Unterschiede sind auf Unterschiede in den Herstellungsprozessen, der Einheitlichkeit des Substitutionsmusters, der Molekulargewichtsverteilung und den Reinheitsgraden zurückzuführen. Führen Sie bei einem Lieferantenwechsel stets eine vergleichende Thermoanalyse durch, um notwendige Prozessanpassungen zu ermitteln. Etablierte Pharma- oder Lebensmittellieferanten halten in der Regel strengere Spezifikationen und eine höhere Chargenkonsistenz ein als allgemeine Industrielieferanten, was sie für thermisch sensible Anwendungen bevorzugt.