Die Formulierung wirksamer Fliesenkleber stellt für viele Hersteller eine Herausforderung dar. Mangelnde Kompatibilität der Inhaltsstoffe führt zu ungleichmäßigem Abbinden, schwachen Verbindungen und beeinträchtigter Haltbarkeit.
Hydroxypropylmethylcellulose (HPMC) weist eine hervorragende Kompatibilität mit zementbasierten Fliesenklebersystemen auf, indem es stabile Wasserstoffbrücken mit Zementpartikeln bildet und gleichzeitig die Wasserrückhaltung, Verarbeitbarkeit und Hafteigenschaften verbessert, ohne den grundlegenden Hydratisierungsprozess zu beeinträchtigen.
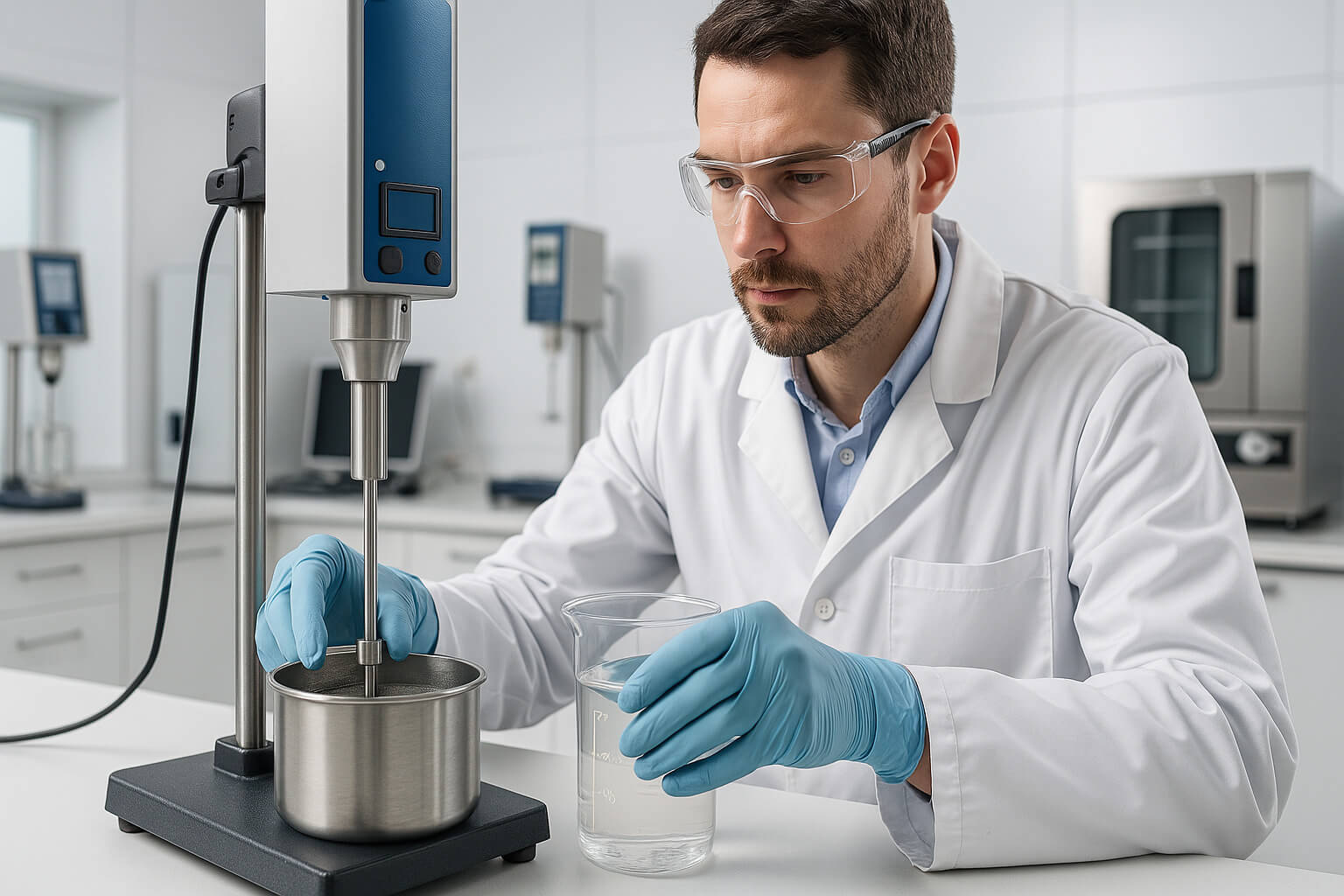
Ein Labortechniker führt Kompatibilitätstests zwischen verschiedenen HPMC-Typen und zementbasierten Klebstoffformulierungen durch, um die Leistungsmerkmale zu optimieren.
Das Verständnis der Kompatibilität zwischen HPMC und Zementsystemen erfordert tiefere technische Kenntnisse, als die meisten Quellen bieten. Untersuchen wir die chemischen und physikalischen Wechselwirkungen, die HPMC zu einer idealen Komponente in modernen Fliesenkleberformulierungen machen.
Welche Rolle spielt HPMC in Fliesenklebersystemen?
Die richtige Balance zwischen Verarbeitbarkeit, Offenzeit und Festigkeit zu finden, ist für viele Klebstoffhersteller ein Frust. Ohne geeignete Additive trocknen Klebstoffe zu schnell oder entwickeln keine ausreichende Haftung.
HPMC fungiert als multifunktionaler Rheologiemodifikator in Fliesenklebersystemen. Es reguliert in erster Linie die Wasserretention, um die offene Zeit zu verlängern, während es gleichzeitig die Standfestigkeit verbessert, die Haftung verbessert und die Konsistenz für eine ordnungsgemäße Flieseneinbettung optimiert.
Wir produzieren HPMC seit über einem Jahrzehnt für Bauanwendungen und verfügen daher über einzigartige Einblicke in seine grundlegende Rolle in zementbasierten Systemen. Die Hauptfunktion konzentriert sich auf das Wassermanagement – eine entscheidende Herausforderung bei der Fliesenverlegung. HPMC bildet ein schützendes kolloidales Netzwerk in der gesamten Klebstoffmatrix, das die Wasserbewegung durch verschiedene Mechanismen physikalisch verlangsamt.
Diese Wasserspeicherfähigkeit behebt die häufigsten Installationsprobleme. Beim Auftragen auf Untergründe verlieren unmodifizierte Zementkleber schnell Feuchtigkeit durch Verdunstung und Absorption in porösen Oberflächen. HPMC unterbricht beide Prozesse, indem es temporäre Wasserstoffbrücken mit Wassermolekülen bildet. Dadurch bleiben diese für die richtige Zementhydratation verfügbar und verlängern gleichzeitig die kritische Verarbeitungszeit.
Neben der Wasserretention verändert HPMC auch die rheologischen Eigenschaften erheblich. Unsere Labortests zeigen immer wieder, dass richtig formulierte HPMC-Zusätze die Klebstoffkonsistenz in drei entscheidenden Punkten verändern:
- Verbessert die Durchhangfestigkeit bei vertikalen Anwendungen
- Verbessert die Streichfähigkeit beim Auftragen mit der Kelle
- Behält die Viskosität auch bei Temperaturschwankungen konstant bei
- Verhindert Wasserabscheidung während der Lagerung und Verwendung
- Erzeugt ein thixotropes Verhalten, das ideal zum Fliesenlegen ist
Diese rheologischen Modifikationen verbessern nicht nur die Verarbeitbarkeit, sondern auch die Bindungsentwicklung grundlegend. Die verbesserte Konsistenz sorgt für eine bessere mechanische Verzahnung zwischen dem Klebstoff und dem Untergrund sowie dem Fliesenträger. Diese mechanische Verbindung ergänzt die chemischer Bindungsprozess ist für die langfristige Haftleistung unerlässlich, wie Forscher im Bereich der Werkstofftechnik dokumentiert haben.
Darüber hinaus trägt HPMC zur Haftfestigkeit bei, indem es ein sekundäres Polymernetzwerk in der gesamten Zementmatrix bildet. Während dieses Netzwerk während der vollständigen Hydratisierung schließlich zerfällt, unterstützt es die sich entwickelnde Mineralstruktur während der kritischen frühen Verstärkungsphase.
Wie interagiert HPMC mit zementbasierten Klebstoffen?
Eine schlechte Additivauswahl führt häufig zu Inkompatibilitäten, die die Klebstoffleistung beeinträchtigen. Chemische Wechselwirkungen zwischen Komponenten können das Aushärten beschleunigen, die Festigkeit verringern oder zu unerwarteten Ausfällen führen.
HPMC interagiert mit Zement durch nichtionische Assoziationen statt durch chemische Bindungen, wobei es Zementpartikel vorübergehend beschichtet, um die Hydratationsrate zu regulieren und gleichzeitig ein kompatibles Gelnetzwerk aufbaut, das die für die Haftfestigkeit wesentliche Bildung der Kristallstruktur unterstützt, anstatt sie zu beeinträchtigen.
Dank unserer langjährigen Erfahrung in der Herstellung haben wir die Wechselwirkungen von HPMC mit verschiedenen Zementkomponenten genau identifiziert. Die Kompatibilität beruht auf der grundsätzlich nicht reaktiven Eigenschaft von HPMC in alkalischen Umgebungen. Im Gegensatz zu einigen Additiven, die die Zementhydratation chemisch verändern, wirkt HPMC über physikalische Mechanismen, die die Leistung modifizieren, ohne die wesentlichen Zementreaktionen zu beeinträchtigen.
Wenn Wasser in ein zementbasiertes System eindringt, löst es sofort Calciumsilikate und -aluminate auf und leitet den Hydratationsprozess ein. HPMC-Moleküle hydratisieren gleichzeitig und bilden ein sekundäres Polymergel in der gesamten Mischung. Diese zeitliche Synchronisierung stellt einen der wichtigsten Kompatibilitätsfaktoren dar – beide Prozesse laufen parallel und ohne Störungen ab.
Die molekulare Wechselwirkung zwischen HPMC und Zementpartikeln beruht hauptsächlich auf einer temporären Oberflächenadsorption. HPMC-Moleküle umhüllen Zementkörner teilweise, ohne dauerhaft an sie gebunden zu sein. Diese Beschichtung mildert den Wasserzugang zur Zementoberfläche und verlangsamt, verhindert aber nicht die wesentlichen Hydratationsreaktionen. Mit fortschreitender Hydratation löst sich die HPMC-Beschichtung allmählich auf und ermöglicht eine vollständige Aushärtung.
In der flüssigen Phase des Klebstoffs bildet HPMC durch Wasserstoffbrückenbindungen ein dreidimensionales Netzwerk. Dieses Netzwerk bindet Wassermoleküle physikalisch und ermöglicht gleichzeitig deren allmähliche Wanderung zu Zementpartikeln. Dadurch bleibt die Verarbeitbarkeit erhalten, ohne die für die vollständige Hydratisierung erforderliche Feuchtigkeit dauerhaft zu binden.
Unsere mikroskopischen Untersuchungen zeigen, dass sich richtig formuliertes HPMC nahtlos in die sich entwickelnde Zementmikrostruktur integriert. Das Polymernetzwerk füllt die Räume zwischen wachsenden Kristallformationen, ohne deren Ausrichtung oder Entwicklung zu stören. Tatsächlich fördert die kontrollierte Wasserumgebung oft eine vollständigere Kristallbildung im Vergleich zu unmodifizierten Systemen. Verbesserung der Langzeithaltbarkeitseigenschaften wie von Baustoffforschern dokumentiert.
Diese Kompatibilität erstreckt sich auch auf die chemische Stabilität. HPMC bleibt in der stark alkalischen Umgebung von frischem Zement (pH 12–13) stabil, ohne dass es zu Zersetzung oder Nebenreaktionen kommt, die die Leistung beeinträchtigen könnten. Diese pH-Stabilität stellt einen erheblichen Vorteil gegenüber einigen alternativen Additiven dar, die unter stark alkalischen Bedingungen zerfallen.
Welche Vorteile bietet HPMC für die Leistung von Fliesenklebern?
Viele Flieseninstallationen scheitern aufgrund mangelnder Klebeleistung. Herkömmliche Formulierungen ohne moderne Zusatzstoffe haben Probleme mit der Offenzeit, der Anpassbarkeit und der Klebkraft.
HPMC verbessert die Leistung des Fliesenklebers, indem es die offene Zeit auf bis zu 30 Minuten verlängert, die vertikale Standfestigkeit verbessert, die Wasserspeicherung auch auf porösen Untergründen gewährleistet, Anpassungszeit für eine präzise Fliesenplatzierung bietet und die Frost-Tau-Beständigkeit erhöht.
Leistungseigenschaft | Ohne HPMC | Mit Optimal HPMC | Verbesserungsfaktor |
---|---|---|---|
Offene Zeit | 5-10 Minuten | 20-30 Minuten | 200-300% |
Vertikale Rutschfestigkeit | < 0,5 mm | < 0,1 mm | 80%-Reduzierung |
Wassereinlagerungen | 60-70% | 95-98% | 40% Erhöhung |
Anpassungsfenster | < 5 Minuten | 15-20 Minuten | 300%-Erweiterung |
Zughaftung nach Frost-Tau-Wechsel | 0,5–0,7 MPa | 1,0–1,2 MPa | 70-100% Erhöhung |
Durch unsere zehnjährige Erfahrung in der Herstellung von HPMC für Bauanwendungen verfügen wir über umfassende Daten zur Leistungssteigerung verschiedener Klebstoffsysteme. Die Vorteile zeigen sich bereits beim Mischen: HPMC verbessert die Pulverbenetzung und -dispersion und sorgt so für glattere, klumpenfreie Mischungen. Diese verbesserte Mischung führt direkt zu einer konstanteren Leistung im Feld.
Die verlängerte Offenzeit stellt den vielleicht größten praktischen Vorteil dar. Unsere technischen Daten zeigen, dass richtig formulierte HPMC-Zusätze die Verarbeitbarkeitszeit des Klebstoffs typischerweise von etwa 10 Minuten (unmodifiziert) auf 20–30 Minuten verlängern. Diese Verlängerung verbessert die Verlegequalität unmittelbar, da sie eine präzisere und schnellere Fliesenverlegung ermöglicht.
Vertikale Anwendungen profitieren besonders von den rheologischen Modifikationen von HPMC. Das Polymernetzwerk erzeugt ein thixotropes Verhalten – der Klebstoff verfließt nicht unter Schwerkraft, verteilt sich aber unter Druck leicht. Diese Eigenschaft verhindert das Verrutschen schwerer Fliesen während der Verlegung und sorgt gleichzeitig für eine hervorragende Deckkraft.
Die Wasserrückhaltefähigkeit löst kritische Probleme der Substratinteraktion. Beim Auftragen auf poröse Materialien wie Beton oder Zementplatten verlieren unmodifizierte Klebstoffe schnell Feuchtigkeit, was die Hydratation beeinträchtigt. Unsere Tests zeigen, dass HPMC-modifizierte Systeme selbst bei Auftragung auf stark saugfähige Untergründe 95–981 TP3T Anmachwasser zurückhalten und so unabhängig von den Einbaubedingungen eine ordnungsgemäße Zementhydratation gewährleisten.
Neben den unmittelbaren Anwendungsvorteilen trägt HPMC maßgeblich zur langfristigen Leistung bei. Die kontrollierte Hydratationsumgebung fördert eine vollständigere Zementaushärtung und führt zu verbesserten Haltbarkeitswerten über mehrere Testparameter hinweg. Abziehhaftungstests zeigen typischerweise eine Verbesserung der Haftfestigkeit um 15-25% im Vergleich zu unveränderten Formulierungen.
Ein weiterer wesentlicher Vorteil ist die Umweltbeständigkeit. HPMC-modifizierte Klebstoffe weisen eine hervorragende Beständigkeit gegen Frost-Tau-Wechsel, Temperaturschocks und Feuchtigkeitsschwankungen auf. Diese verbesserte Haltbarkeit ist besonders wertvoll bei Außenanwendungen, wo Umweltbelastungen die Klebeverbindungen ständig auf die Probe stellen.
Diese umfassende Leistungssteigerung macht HPMC zu einem wesentlichen Bestandteil moderner Konstruktionsklebstoffe gemäß internationalen Baunormorganisationen, die fortschrittliche Baumaterialien untersuchen.
Wie wählen Sie das richtige HPMC für Fliesenkleberformulierungen aus?
Die Wahl ungeeigneter HPMC-Typen führt zu unvorhersehbarem Klebstoffverhalten. Viskositätsabweichungen, schlechte Auflösungseigenschaften und ein falscher Methoxylgehalt führen zu Leistungsproblemen.
Zur Auswahl des optimalen HPMC sind eine passende Viskositätsklasse (typischerweise 15.000–100.000 mPa·s), die Auswahl eines geeigneten Methoxylgehalts (28–30% für Standardsysteme), die Sicherstellung einer geeigneten Hydroxypropylsubstitution (7–12%) und die Überprüfung einer für Trockenmischungsherstellungsprozesse geeigneten Partikelgrößenverteilung erforderlich.
Durch unsere Produktionsabläufe haben wir mehrere kritische Parameter identifiziert, die die Eignung von HPMC für bestimmte Fliesenkleberanwendungen bestimmen. Der Auswahlprozess muss sowohl die chemischen Eigenschaften des HPMC selbst als auch die praktischen Anforderungen der Formulierung und der Anwendungsmethode berücksichtigen.
Die Viskosität ist das wichtigste Auswahlkriterium und beeinflusst direkt die Wasserretention, die offene Zeit und die Verarbeitbarkeit. Unsere Produktionserfahrung zeigt optimale Bereiche für verschiedene Anwendungsarten:
- Niedrige Viskosität (15.000–30.000 mPa·s): Bodenfliesenkleber, bei denen die Fließfähigkeit der Verlegung zugute kommt
- Mittlere Viskosität (40.000–70.000 mPa·s): Allgemeine Wand- und Bodenanwendungen
- Hohe Viskosität (80.000–100.000 mPa·s): Vertikale Anwendungen, die maximale Ablauffestigkeit erfordern
- Sehr hohe Viskosität (>100.000 mPa·s): Spezialanwendungen wie Naturstein oder großformatige Fliesen
Neben der Viskosität beeinflusst der Methoxylgehalt maßgeblich die HPMC-Leistung in Zementsystemen. Höhere Methoxylanteile (29-30%) sorgen im Allgemeinen für eine bessere Zementverträglichkeit und bessere thermische Gelierungseigenschaften. Ein niedrigerer Methoxylgehalt führt manchmal zu einer schlechten Dispersion in der alkalischen Zementumgebung.
Der Hydroxypropylsubstitutionsgrad beeinflusst sowohl die Löslichkeit als auch die Oberflächenaktivität. Unsere Tests zeigen, dass eine moderate Substitution (7-12%) die Leistung von Fliesenklebern optimiert, indem sie die Auflösungsgeschwindigkeit mit der Gelstärke in Einklang bringt. Höhere Substitutionsgrade können die Wasserrückhaltefähigkeit in einigen Formulierungen sogar verringern.
Die Partikelgrößenverteilung spielt eine entscheidende Rolle für den Herstellungs- und Anwendungserfolg. Bei Trockenmischungen muss sich HPMC problemlos in die Pulvermischung einarbeiten lassen, ohne dass es zu Entmischungen oder Agglomerationen kommt. Eine gleichmäßige Partikelgröße gewährleistet zudem eine gleichmäßige Auflösung bei Wasserzugabe vor Ort. Unsere Produktionsprozesse entwickeln speziell abgestimmte Partikelgrößenverteilungen, um diese Integration zu optimieren.
Die Temperaturbedingungen am Installationsort sollten die HPMC-Auswahl beeinflussen. Projekte in heißen, trockenen Umgebungen profitieren von höheren Viskositätsgraden, die die beschleunigte Trocknung kompensieren. Umgekehrt können kühle, feuchte Bedingungen Varianten mit niedrigerer Viskosität erfordern, um die Verarbeitbarkeit ohne übermäßige Abbindeverzögerung aufrechtzuerhalten.
Auch der Substrattyp beeinflusst die Auswahlentscheidung. Hochporöse Substrate erfordern HPMC-Typen mit verbesserter Wasserspeicherfähigkeit, die typischerweise durch höhere Viskosität und optimierte Substitutionsmuster erreicht wird. Nichtporöse Oberflächen ermöglichen eine geringere Wasserspeicherung.
Herstellern, die neue Formulierungen entwickeln, empfehlen wir systematische Evaluierungsprotokolle anstelle von Versuch und Irrtum. Labortests sollten Rheologiemessungen, Wasserretentionsbestimmungen und Haftungstests unter verschiedenen Bedingungen umfassen, um die optimale HPMC-Qualität für spezifische Anwendungen zu ermitteln.
Welche Herausforderungen und Lösungen gibt es häufig bei der Verwendung von HPMC in Fliesenkleber?
Eine unsachgemäße Einarbeitung von HPMC führt zu Anwendungsproblemen für Installateure. Klumpenbildung, verzögerte Auflösung und inkonsistente Leistung frustrieren Fachleute und schädigen den Ruf des Produkts.
Zu den üblichen Herausforderungen zählen eine schlechte Auflösung, die zu Klumpen führt, eine verzögerte Viskositätsentwicklung, Inkompatibilität mit Hochschermischungen, verringerte Wirksamkeit in Regionen mit hartem Wasser und mögliche Schaumbildung während des Mischens – alles lösbar durch die Auswahl der richtigen Qualität, modifizierte Mischverfahren und kleine Zugaben ergänzender Additive.
Unser technisches Supportteam unterstützt Kunden regelmäßig bei der Bewältigung von HPMC-Integrationsproblemen. Die häufigsten Probleme betreffen die Auflösung und Dispersion innerhalb der Klebstoffmatrix. Bei unsachgemäßer Einarbeitung kann HPMC Gelklumpen bilden, die sich nie vollständig integrieren und so zu inkonsistenter Leistung im gesamten Anwendungsbereich führen.
Dieses Klumpenproblem ist häufig auf unsachgemäße Einarbeitung zurückzuführen. Die Lösung besteht darin, HPMC vor der Wasserzugabe sorgfältig mit trockenen Komponenten vorzumischen. Wir empfehlen, HPMC vor der Zugabe von Flüssigkeit gründlich mit Zement und Zuschlagstoffen in Hochleistungsmischern zu dispergieren. Dadurch wird die sofortige Gelbildung verhindert, die bei direktem Kontakt von HPMC-Pulver mit Wasser auftritt.
Ein weiteres häufiges Problem ist die verzögerte Viskositätsentwicklung. Einige Klebstoffhersteller berichten, dass Mischungen zunächst zu dünnflüssig erscheinen, bevor sie plötzlich über die brauchbare Konsistenz hinaus eindicken. Dieses Verhalten deutet typischerweise auf eine falsche HPMC-Sorte oder Probleme beim Mischvorgang hin. Wir lösen dieses Problem mit zwei Ansätzen:
- Auswahl von HPMC-Typen mit optimierten Auflösungsprofilen, die eine vorhersehbarere Viskositätsentwicklung ermöglichen
- Modifizierung der Mischprotokolle, um kurze Ruhepausen einzuschließen, die eine vollständige Hydratisierung ermöglichen
Die Verträglichkeit mit hartem Wasser stellt eine weitere große Herausforderung dar, insbesondere in Regionen mit hohem Mineralgehalt. Calcium- und Magnesiumionen können mit HPMC interagieren und dessen Wirksamkeit verringern. Unsere Lösung umfasst speziell entwickelte HPMC-Typen mit modifizierten Substitutionsmustern, die auch bei hartem Wasser ihre Leistungsfähigkeit erhalten.
Einige Hersteller stellen beim Hochgeschwindigkeitsmischen Schaumbildung fest. Dieser Schaum kann zu Anwendungsproblemen führen und die endgültige Klebstoffdichte verringern. Wir begegnen diesem Problem durch:
- Einarbeitung minimaler Mengen an Entschäumern in die Formulierung
- Empfehlung modifizierter Mischverfahren mit kontrollierten Rührgeschwindigkeiten
- Entwicklung spezieller HPMC-Typen mit reduzierter Schaumneigung
Temperaturabhängigkeit führt manchmal zu Konsistenzunterschieden zwischen Sommer- und Winteranwendungen. Standard-HPMC weist in verschiedenen Temperaturbereichen ein unterschiedliches Auflösungs- und Rheologieverhalten auf. Unsere Produktionsprozesse erzeugen thermisch stabilisierte Sorten, die auch bei saisonalen Temperaturschwankungen eine konsistentere Leistung aufweisen.
Auch die Lagerstabilität kann Herausforderungen mit sich bringen. Unter hohen Luftfeuchtigkeitsbedingungen kann HPMC in Trockenmischungen teilweise hydratisieren, was die Wirksamkeit nach dem Mischen verringert. Unsere Verpackungsempfehlungen umfassen feuchtigkeitsbeständige Liner und spezifische Lagerrichtlinien, um die optimale Leistung während des gesamten Produktlebenszyklus zu gewährleisten.
Herstellern, die Qualitätsabweichungen zwischen Chargen feststellen, bieten wir umfassende Unterstützung bei der Fehlerbehebung. Unsere Laboranalysen identifizieren spezifische Ursachen für Abweichungen, unabhängig davon, ob diese auf Rohstoffe, Herstellungsprozesse oder Anwendungstechniken zurückzuführen sind.
Welche Tests und Zertifizierungen unterstützen den Einsatz von HPMC im Bauwesen?
Die Einhaltung von Bauvorschriften erfordert eine nachgewiesene Leistung. Ohne ordnungsgemäße Prüfung und Zertifizierung werden Produkte von Prüfern und Planern abgelehnt, was den Marktzugang einschränkt.
HPMC-modifizierte Klebstoffe werden strengen Tests gemäß den Normen EN 12004, ANSI A118.4 und ISO 13007 unterzogen, um die Zugfestigkeit der Haftung, die Verlängerung der offenen Zeit, die Rutschfestigkeit und die Verformbarkeit zu überprüfen. Umweltzertifizierungen wie die Einhaltung von VOC-Vorschriften und LEED-Beiträge bestätigen zusätzlich ihre Eignung für den Baubereich.
Rahmen für regulatorische Tests
Durch unsere Mitarbeit in technischen Ausschüssen und Normungsorganisationen haben wir umfassende Kenntnisse über die Prüfanforderungen für Konstruktionsklebstoffe erlangt. Diese standardisierten Bewertungen ermöglichen eine objektive Überprüfung des Beitrags von HPMC zur Klebstoffleistung.
Die europäische Norm EN 12004 legt das am weitesten verbreitete Prüfprotokoll für Keramikfliesenkleber fest. Dieses Rahmenwerk klassifiziert Klebstoffe nach ihren Leistungsmerkmalen. HPMC-modifizierte Systeme erreichen typischerweise die Klassifizierung C2 (verbesserter Zementkleber) mit zusätzlichen Bezeichnungen:
- E (verlängerte offene Zeit): Direkt auf die Wasserretention von HPMC zurückzuführen
- T (reduzierter Schlupf): Bezieht sich auf die rheologische Modifikation von HPMC
- S1/S2 (Verformbarkeit): Teilweise unterstützt durch die Kompatibilität von HPMC mit verformbaren Polymeren
Zu den Tests gemäß dieser Norm gehören Messungen der Zughaftfestigkeit unter verschiedenen Konditionierungsbedingungen, darunter:
- Standard-Umgebungsbedingungen
- Wasserimmersion
- Wärmealterung
- Frost-Tau-Wechsel
- Auswertung der offenen Zeit
Die nordamerikanische Norm ANSI A118.4 bietet ähnliche Leistungsnachweise, allerdings mit methodischen Unterschieden. Unser technisches Team unterstützt Hersteller bei der Bewältigung dieser regionalen Testunterschiede, um den globalen Marktzugang zu gewährleisten. HPMC-Beiträge erweisen sich als besonders wertvoll, um die Anforderungen dieser Norm an die verlängerte Offenzeit und Standfestigkeit zu erfüllen.
ISO 13007 ist eng an EN 12004 angelehnt und bietet eine weltweit anerkannte Klassifizierung. Für internationale Hersteller bietet diese Norm den am weitesten verbreiteten Rahmen für die Leistungsüberprüfung.
Über die klebstoffspezifischen Standards hinaus wird HPMC selbst während unseres Herstellungsprozesses strengen Qualitätsprüfungen unterzogen. Wir überprüfen kritische Parameter, darunter:
- Viskosität (Brookfield-Methode)
- Substitutionsgrad (Gaschromatographie)
- Feuchtigkeitsgehalt
- Aschegehalt
- Partikelgrößenverteilung
- pH-Wert der Lösung
Diese Rohstoffkontrollen gewährleisten eine gleichbleibende Leistung der fertigen Klebstoffformulierungen. Unser Qualitätsmanagementsystem hält für jeden Parameter strenge Spezifikationsbereiche ein und bietet Herstellern Charge für Charge zuverlässige Leistung.
Umweltprüfungen werden für Baumaterialien immer wichtiger. HPMC-modifizierte Klebstoffe schneiden bei VOC-Emissionstests typischerweise hervorragend ab und tragen kaum zur Luftverschmutzung in Innenräumen bei. Diese Eigenschaft unterstützt Zertifizierungsprogramme für umweltfreundliches Bauen wie LEED und BREEAM, die wesentliche Umweltauswirkungen bewerten.
Für spezielle Anwendungen können zusätzliche Tests spezifische Leistungsmerkmale bestätigen. Außeninstallationen erfordern oft Frost-Tau-Beständigkeitstests, die über die Standardanforderungen hinausgehen. Anwendungen in Nassbereichen werden üblicherweise zusätzlich auf Wasserbeständigkeit geprüft. Umgebungen mit hohen Temperaturen können spezielle thermische Stabilitätstests erfordern. Unser Labor unterstützt Hersteller bei der Entwicklung dieser maßgeschneiderten Testprotokolle, wenn Standardzertifizierungen die spezifischen Anwendungsanforderungen nicht abdecken.
FAQs
Was ist HPMC für Fliesen?
HPMC für Fliesen ist ein Polymer auf Zellulosebasis und ein wichtiger Leistungszusatz in zementbasierten Fliesenklebern. Es verlängert die offene Zeit, indem es Wasser in der Kleberschicht hält, wodurch sich die Verarbeitungszeit typischerweise von 10 Minuten auf über 30 Minuten erhöht. HPMC verbessert zudem die Kleberkonsistenz, verbessert die Standfestigkeit und fördert eine bessere Benetzung von Fliesen und Untergründen. In professionellen Klebern liegt die HPMC-Dosierung typischerweise zwischen 0,2% und 0,5%, abhängig von den gewünschten Leistungsmerkmalen und den Anwendungsbedingungen.
Was ist ein zementbasierter Fliesenkleber?
Ein zementbasierter Fliesenkleber ist eine trockene Pulvermischung, die hauptsächlich Portlandzement, abgestufte Zuschlagstoffe und Hochleistungsadditive enthält und mit Wasser vermischt eine starke, dauerhafte Verbindung bildet. Die Zementkomponente (typischerweise 25-35%) sorgt durch ihre hydraulischen Abbindeeigenschaften für die grundlegende Bindefestigkeit. Zuschlagstoffe (50-70%) sorgen für die Struktur, während Additive wie HPMC und Polymere die Verarbeitbarkeit, Haftung und Flexibilität verbessern. Diese Kleber härten durch einen chemischen Hydratationsprozess statt durch einfaches Trocknen aus und entwickeln dadurch eine außergewöhnliche Festigkeit und Feuchtigkeitsbeständigkeit, die für die dauerhafte Fliesenverlegung unerlässlich ist.
Was ist HPMC für Trockenmörtel?
HPMC für Trockenmörtel dient als multifunktionaler Zusatzstoff, der die Wasserrückhaltung, Verarbeitbarkeit und Haftungseigenschaften von vorgemischten Zementmischungen verbessert. In Mörtelanwendungen liegt der HPMC-Gehalt typischerweise zwischen 0,11 TP3T und 0,41 TP3T der Trockenformulierung, wobei die spezifischen Qualitäten je nach erforderlicher Offenzeit und Konsistenz ausgewählt werden. Es erzeugt eine ausgewogene Rheologie, die die Verarbeitbarkeit ohne übermäßiges Fließen aufrechterhält und gleichzeitig die Nutzungsdauer der Mischung auf der Platte deutlich verlängert. HPMC verbessert zudem die Mörtelkohäsion während der Anwendung und verbessert die Haftung auf verschiedenen Untergründen, was es sowohl für Mauerwerks- als auch für Putzanwendungen unverzichtbar macht.
Kann man Kleber und Zement mischen?
Das Mischen von vorgefertigtem Klebstoff mit zusätzlichem Zement wird generell nicht empfohlen, da dies die sorgfältig abgestimmte Chemie der ursprünglichen Formulierung stört. Die Zugabe von Zement verändert typischerweise das Wasser-Zement-Verhältnis, was möglicherweise zu einer verringerten Verarbeitbarkeit, einer verkürzten offenen Zeit und einer verringerten Haftfestigkeit führt. Für spezielle Anwendungen, die modifizierte Eigenschaften erfordern, empfehlen wir die Wahl eines speziell formulierten Produkts anstelle einer Modifikation vor Ort. Wenn Anpassungen unbedingt erforderlich sind, wenden Sie sich an den Klebstoffhersteller. Einige Systeme vertragen eine geringe Zementzugabe (maximal 5-10%), wenn zusätzliche Festigkeit erforderlich ist. Dies sollte jedoch mit Vorsicht angegangen werden.
Abschluss
HPMC weist eine hervorragende Kompatibilität mit zementbasierten Fliesenklebersystemen auf, da es sich nicht auf chemische Einflüsse, sondern auf ergänzende physikalische Wechselwirkungen stützt. Diese Kompatibilität führt zu erheblichen Leistungsvorteilen während des gesamten Klebstofflebenszyklus – vom Mischen und Auftragen bis hin zur endgültigen Aushärtung und Langzeitbeständigkeit.
Unsere langjährige Fertigungserfahrung bestätigt, dass ausgewählte HPMC-Typen herkömmliche Zementmischungen in Hochleistungsklebstoffe mit verlängerter Offenzeit, verbesserter Verarbeitbarkeit und erhöhter Haftfestigkeit verwandeln. Die Wasserrückhaltefähigkeit löst häufige Installationsprobleme und fördert gleichzeitig die vollständige Zementhydratation für eine optimale Strukturentwicklung.
Für Klebstoffhersteller, die ihre Produktleistung und Installationserfolgsraten verbessern möchten, ist die Kontaktaufnahme mit Morton für spezielles HPMC in Bauqualität der direkteste Weg zur Rezepturoptimierung. Unser technisches Team empfiehlt Ihnen gerne spezifische Qualitäten, die genau auf Ihre Anwendungsanforderungen und regionalen Installationsbedingungen abgestimmt sind.