Understanding the function of HPMC in cement is crucial for professionals in the construction and industrial sectors. Hydroxypropyl Methylcellulose (HPMC) serves as a key additive that improves many aspects of cement performance. So läuft's: cement alone can face issues like poor workability, fast water evaporation, and inadequate adhesion. That’s where HPMC steps in. This article explores how HPMC enhances cement’s properties, from water retention to durability, and why it is a preferred choice in formulations used by purchasing managers, engineers, and product developers. We will cover what HPMC is, how it works in cement, its impact on performance, and practical considerations for choosing the right grade. By the end, you’ll have a detailed understanding tailored for B2B decision-making.
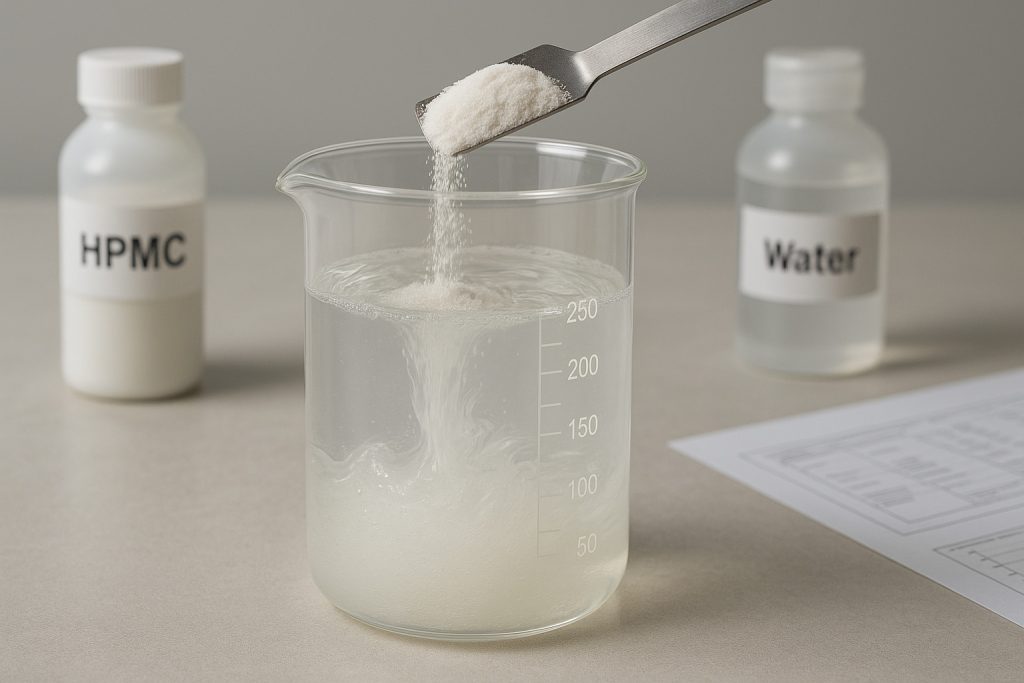
1 What is HPMC and how is it related to cement?
Hydroxypropyl Methylcellulose (HPMC) is a cellulose derivative widely used as an additive in cement-based products. Sie fragen sich vielleicht why a cellulose derivative matters in cement. The answer lies in its unique chemical structure that allows it to retain water, stabilize mixtures, and improve workability without compromising strength. HPMC is synthesized by modifying cellulose fibers to introduce hydroxypropyl and methyl groups, making it water-soluble and able to form viscous solutions. Cement, primarily a mixture of clinker, gypsum, and other compounds, requires additives to solve challenges like rapid drying and weak adhesion. HPMC addresses these by improving the physical and chemical environment during the cement curing process.
Several case studies demonstrate HPMC’s effectiveness. For example, in dry mortar production, adding HPMC improves mix homogeneity and prevents water loss during application, reducing cracking. In tile adhesives, HPMC maintains consistency for easier spreading and longer open time. Another instance is thermal insulation mortars where HPMC controls setting speed and enhances adhesion on various substrates. The chemical compatibility between HPMC and cement ingredients enables these benefits.
The industry relies heavily on precise formulations, and understanding HPMC’s properties helps optimize cement products for specific use cases. Cement without HPMC may dry unevenly or become brittle, while formulations with HPMC show improved flexibility and durability. Let me tell you, this makes a big difference in product quality and customer satisfaction.
Eigentum | Beschreibung | Effect on Cement |
---|---|---|
Wasserlöslichkeit | Forms viscous solution when mixed with water | Verbessert die Wasserretention |
Viskositätskontrolle | Adjustable by substitution degree | Verbessert die Verarbeitbarkeit |
Chemical stability | Resistant to alkali in cement | Maintains performance during curing |
Adhesion support | Forms film on surfaces | Increases bonding strength |
2 Why is HPMC used in cement formulations?
HPMC finds wide application in cement formulations because it solves multiple performance issues that affect construction quality and efficiency. Here’s something you need to know: the primary reasons for using HPMC include improved workability, water retention, and surface adhesion. Cement-based materials such as dry mortars, tile adhesives, and plasters must be easy to apply and remain workable for a reasonable time. HPMC modifies the rheological properties of the mix, making it smoother and less prone to segregation.
In practice, manufacturers report that adding HPMC reduces water evaporation during mixing and application, which is critical in hot or dry environments. This water retention maintains hydration reactions longer, resulting in better curing and strength development. In addition, HPMC enhances the thixotropic behavior, meaning the material remains thick enough to prevent sagging on vertical surfaces but can be easily spread when applied.
Industries such as construction, pharmaceuticals, and food also use HPMC, but cement and dry mortar producers are among the heaviest users due to these benefits. For example, a leading dry mortar producer in Europe increased product durability by over 20% after optimizing HPMC content. Another case from Asia showed that tile adhesive manufacturers reduced customer complaints on workability by standardizing HPMC grades.
The use of HPMC also supports compliance with industry standards like ASTM and EN, ensuring products meet regulatory and performance benchmarks. This alignment builds trust with buyers, especially procurement managers who demand consistent quality and predictable supply.
Anwendungsfall | Nutzen | Industry Example |
---|---|---|
Dry mortar | Improved water retention | European dry mortar manufacturer |
Tile adhesive | Better spreadability | Asian tile adhesive producer |
Thermal insulation mortar | Controlled setting and adhesion | Insulation supplier in North America |
3 How does HPMC improve workability and water retention in cement?
Workability and water retention are critical to cement performance on job sites. Let me break it down: workability refers to how easy it is to mix, spread, and shape cement products. Without proper workability, materials become difficult to handle, causing delays and defects. Water retention means the ability of the cement mix to hold moisture long enough for hydration—the chemical reaction essential for strength.
HPMC works by creating a viscous network that traps water molecules and slows evaporation. This network also suspends fine particles in the mix evenly, preventing segregation or bleeding. For example, in plastering applications, a cement mix with HPMC remains pliable longer, allowing applicators to work efficiently without the mix drying out too fast.
Case studies from construction projects show that using HPMC reduced surface cracks caused by rapid drying by nearly 30%. This is significant for maintaining structural integrity and reducing repair costs. Another example from tile adhesive production revealed that HPMC extended the open time from 30 minutes to over 90 minutes, allowing more flexibility in application and reducing waste.
Moreover, HPMC’s ability to improve workability without increasing water content prevents weakening of the cement matrix. Unlike simply adding more water, which dilutes strength, HPMC allows for consistent strength development with better handling.
Parameter | Ohne HPMC | Mit HPMC |
---|---|---|
Workability time | 15-30 minutes | 60-90 minutes |
Wassereinlagerungen | Niedrig | Hoch |
Surface cracking | Frequent | Reduced |
Strength retention | Lower due to added water | Maintained |
4 What impact does HPMC have on the setting time and strength of cement?
The effect of HPMC on setting time and strength is often a key concern for purchasing managers and product formulators. Here’s the catch: HPMC can adjust the hydration process, which influences how fast the cement sets and ultimately how strong it becomes. Depending on the grade and dosage, HPMC can retard or moderately delay the setting time. This delay is usually beneficial because it allows better handling and finishing without compromising final strength.
Research shows that HPMC interacts with cement hydration by forming a thin polymer film around cement particles, slowing water penetration. This controlled hydration prevents premature setting and reduces internal stresses that cause cracking. For example, in a construction project in Germany, adjusting HPMC content extended the setting time by 45 minutes, allowing workers more flexibility during application.
Regarding strength, extensive testing confirms that appropriate HPMC levels maintain or even improve compressive and flexural strength. This is because the additive supports a uniform hydration process and reduces micro-cracking during curing. In contrast, excessive dosage can lower early strength, so precise formulation is essential.
Manufacturers often balance HPMC grades with other admixtures such as accelerators to meet specific project timelines. For example, a tile adhesive product used in the U.S. optimized HPMC with setting accelerators to achieve fast initial set without sacrificing long-term durability.
Setting Time Effect | Beschreibung | Impact on Strength |
---|---|---|
Moderate delay | Polymer film slows hydration | Maintains or improves final strength |
Excessive dosage | Prolonged retardation | Possible early strength reduction |
Balanced dosage | Optimized set time and strength | Meets project requirements |
5 How does HPMC enhance the durability and adhesion of cement products?
Durability and adhesion are vital properties for cement products exposed to harsh environments or demanding applications. Here’s what you should know: HPMC contributes significantly to both. Its water retention ability minimizes shrinkage cracks, a common durability issue. The polymer film also improves bonding between the cement matrix and substrates like bricks, tiles, or insulation boards.
A well-documented case from a European building project showed that dry mortar with HPMC exhibited 25% better resistance to freeze-thaw cycles compared to standard mortar. This increased lifespan means lower maintenance costs and improved structural safety.
In tile adhesive production, HPMC enhances adhesion to different substrates such as concrete, ceramic, and natural stone. This reduces tile detachment failures, which are costly and time-consuming to fix. In one Asian construction project, switching to HPMC-modified adhesives lowered tile failure rates by 15% within the first year.
Another benefit is crack resistance. HPMC forms a flexible polymer network within the cement, allowing the material to absorb minor movements without cracking. This property is essential for thin plaster layers and finishing coats.
Eigentum | Ohne HPMC | Mit HPMC |
---|---|---|
Freeze-thaw resistance | Standard resistance | 25% improvement |
Haftfestigkeit | Lower bonding | Strong bonding |
Crack resistance | Higher chance of cracking | Reduced cracking |
6 What types of cement products commonly incorporate HPMC?
HPMC is versatile and used in a range of cement-based products tailored to various industrial needs. Here’s the scoop: dry mortar is one of the largest consumers of HPMC. These include tile adhesives, repair mortars, and general-purpose dry mixes. In these applications, HPMC ensures consistent mixing, easy application, and durable final performance.
Tile adhesives particularly benefit from HPMC because of the extended open time and improved adhesion it provides. Many premium-grade adhesives incorporate HPMC to meet stringent quality standards. For instance, a North American tile manufacturer reported a 20% reduction in installation errors after switching to HPMC-enhanced adhesives.
Plasters and finishing coats also use HPMC to prevent shrinkage cracks and improve surface smoothness. Its water retention keeps plasters workable and prevents premature drying.
Thermal insulation mortars employ HPMC to balance workability with thermal properties. In colder climates, insulation mortars with HPMC maintain integrity despite temperature fluctuations.
Cement Product | Main Benefit of HPMC | Industry Example |
---|---|---|
Dry mortar | Workability and water retention | European dry mortar producer |
Tile adhesive | Extended open time and adhesion | North American tile manufacturer |
Plasters and finishing | Crack resistance and smoothness | Construction finishing companies |
Thermal insulation | Stability in temperature variations | Insulation manufacturers |
7 How to select the right HPMC grade for specific cement applications?
Choosing the correct HPMC grade is essential for achieving desired cement performance. Here’s the thing: HPMC grades vary mainly in viscosity and substitution degree, both of which affect water retention and mix consistency. High-viscosity grades provide stronger water retention but may reduce flowability. Lower-viscosity grades improve spreadability but retain less water.
Substitution degree refers to how much hydroxypropyl and methyl groups are attached to the cellulose backbone. This impacts solubility and interaction with cement particles. Selecting a grade depends on the specific product, application method, and environmental conditions.
For example, dry mortar formulations in hot climates may require high-viscosity HPMC to prevent rapid drying. Tile adhesives used in colder regions might favor medium viscosity to balance open time and strength.
Supplier evaluation also matters. Consistent quality, compliance with standards like USP or EP, and technical support are critical factors. Some producers offer customized HPMC with adjusted viscosity or dissolution speed tailored for unique formulations.
Grade Parameter | Effect on Cement | Anwendungsbeispiel |
---|---|---|
Hohe Viskosität | Strong water retention | Dry mortars in hot environments |
Mittlere Viskosität | Balanced retention and flow | Tile adhesives in temperate zones |
Niedrige Viskosität | High flowability | Finishing plasters |
High substitution degree | Better solubility and stability | Specialized industrial uses |
8 What are the challenges and precautions when using HPMC in cement?
While HPMC offers many benefits, it also presents challenges that must be managed carefully. You need to be aware that improper dosing can cause issues like excessive retardation of setting or poor mechanical properties. Overdosing HPMC may lead to too much viscosity, making mixing difficult and potentially reducing strength.
Storage and handling are other considerations. HPMC powders can absorb moisture and clump if not stored in dry conditions. This affects dissolution rates and performance. Mixing procedures must ensure full dispersion to avoid lumps or uneven consistency.
Another challenge is compatibility with other admixtures such as accelerators, retarders, or plasticizers. Some combinations may interact negatively, requiring thorough testing before large-scale use.
Manufacturers and purchasing managers should run small-scale trials to optimize dosage for their specific cement mix and environmental conditions. Proper training for on-site workers also helps ensure correct application and maximize benefits.
Herausforderung | Ursache | Empfohlene Aktion |
---|---|---|
Excessive retardation | Overdosing HPMC | Optimize dosage through trials |
Clumping in storage | Feuchtigkeitsaufnahme | Store in dry, airtight containers |
Poor mixing | Incomplete dispersion | Use proper mixing equipment |
Admixture incompatibility | Chemical interactions | Conduct compatibility tests |
FAQ-Bereich
Frage 1: Was ist HPMC?
Hydroxypropyl Methylcellulose (HPMC) is a cellulose-based additive used in cement to improve water retention, workability, and adhesion properties, enhancing product performance.
Frage 2: How does HPMC improve cement properties?
HPMC forms a viscous network that holds water in the cement mix, controls setting time, and strengthens adhesion to substrates, resulting in better durability and ease of application.
Frage 3: Can HPMC affect the strength of cement?
Yes, when used correctly, HPMC supports consistent hydration and prevents micro-cracking, maintaining or improving the final mechanical strength of cement products.
Frage 4: What cement products typically use HPMC?
Common products include dry mortars, tile adhesives, plasters, and thermal insulation mortars, where HPMC enhances workability and durability.
F5: How do I choose the right HPMC grade for cement?
Select based on viscosity and substitution degree suited to your application, climate, and mix requirements. Supplier quality and technical support are also important considerations.