Die Wahl der richtigen Hydroxypropylmethylcellulose (HPMC) ist für Hersteller verschiedenster Branchen eine wichtige Entscheidung. Eine falsche Wahl kann zu erheblichen Produktionsineffizienzen, beeinträchtigter Produktqualität und letztlich zu finanziellen Verlusten führen. Herausforderungen wie inkonsistente Viskosität, schlechte Wasseraufnahme oder unzureichende Bindeeigenschaften wirken sich direkt auf die Leistung und Marktakzeptanz Ihres Endprodukts aus. Aus diesem Grund ist es so wichtig, die HPMC-Qualitäten zu verstehen. Dieser Artikel führt Sie durch die Komplexität von HPMC und beschreibt detailliert seine Eigenschaften, verschiedene Qualitäten und optimale Anwendungen in der Pharmaindustrie, im Bauwesen und in der Körperpflege. Sie erfahren außerdem, wie Sie häufige Probleme beheben und fundierte Entscheidungen für Ihre spezifischen Projektanforderungen treffen.
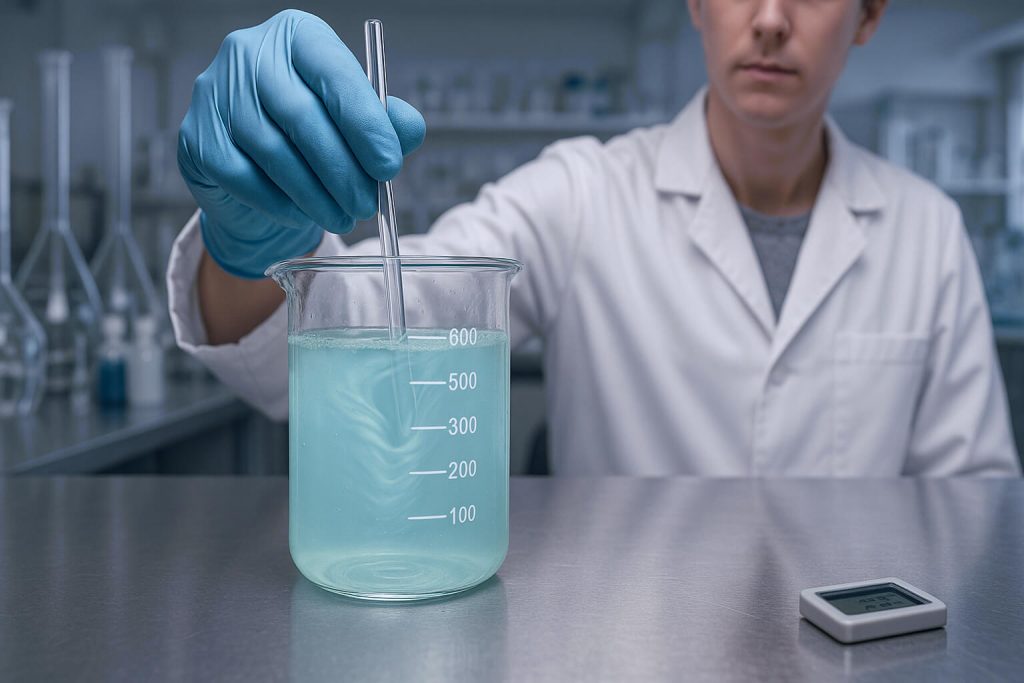
1. Was ist HPMC und warum ist es für Ihre Projekte wichtig?
HPMC (Hydroxypropylmethylcellulose) ist ein vielseitiges Polymer, das aus Cellulose gewonnen wird. Es handelt sich um einen nichtionischen, wasserlöslichen Celluloseether. Diese Verbindung findet in vielen Branchen Anwendung. Ihre einzigartige chemische Struktur ermöglicht es ihr, mehrere wichtige Funktionen zu erfüllen. Zu diesen Funktionen gehören Verdickung, Bindung, Filmbildung und Wasserretention. Das Verständnis dieser Eigenschaften ist der Schlüssel zur erfolgreichen Anwendung.
Eigentum | Beschreibung | Typische Anwendung |
---|---|---|
Verdickung | Erhöht die Viskosität von Lösungen. | Farben, Reinigungsmittel, Lebensmittel |
Bindung | Hält Komponenten zusammen. | Tabletten, Baumaterialien |
Filmbildend | Bildet einen Schutz- oder Funktionsfilm. | Beschichtungen, Körperpflegeprodukte |
Wassereinlagerungen | Verhindert Wasserverlust aus Formulierungen. | Mörser, Backwaren |
Thermische Gelierung | Bildet beim Erhitzen ein Gel und wird beim Abkühlen wieder flüssig. | Arzneimittel mit kontrollierter Freisetzung, Nahrungsmittelgele |
Seine breite Anwendung in der Pharma-, Bau-, Lebensmittel- und Körperpflegebranche unterstreicht seine Bedeutung. In der Pharmaindustrie dient HPMC als Bindemittel in Tabletten und als Freisetzungsmodifikator. Im Bauwesen verbessert es die Verarbeitbarkeit und Haftung von Mörtel. Lebensmittelprodukte erhalten Textur und Stabilität. Körperpflegeprodukte profitieren von seinen filmbildenden und verdickenden Eigenschaften. HPMC bietet viele Vorteile. Es verbessert die Produktleistung und -stabilität und verlängert die Haltbarkeit. Das macht es zu einem wertvollen Bestandteil vieler Formulierungen.
2. Welchen Einfluss haben unterschiedliche HPMC-Typen auf die Leistung?
HPMC ist in verschiedenen Qualitäten erhältlich, die jeweils für spezifische Leistungsmerkmale entwickelt wurden. Diese Unterschiede ergeben sich aus Variationen im Molekulargewicht, Substitutionsgrad und der Partikelgröße. Das Verständnis dieser Unterschiede hilft Ihnen bei der Auswahl der richtigen Qualität. Diese Auswahl wirkt sich direkt auf die endgültige Leistung Ihres Produkts aus.
Die Viskosität ist ein Hauptunterscheidungsmerkmal zwischen HPMC-Typen. Sie bestimmt die Verdickungskraft des HPMC. Hochviskose Typen ergeben dicke Lösungen. Niedrigviskose Typen ergeben dünnere Lösungen. Diese Eigenschaft ist entscheidend für Fließfähigkeit und Anwendung. Beispielsweise eignet sich hochviskoses HPMC für Farben. Niedrigviskose Typen funktionieren gut in Augentropfen. Auch die Substitutionsarten, insbesondere der Methoxy- und Hydroxypropoxylgehalt, spielen eine Rolle. Diese beeinflussen die Löslichkeit und die thermische Gelierung. Ein höherer Methoxylgehalt bedeutet oft eine niedrigere Gelierungstemperatur. Ein höherer Hydroxypropoxylgehalt verbessert die Wasserlöslichkeit. Die Partikelgröße beeinflusst die Lösungsgeschwindigkeit. Feinere Partikel lösen sich schneller auf. Gröbere Partikel verteilen sich besser. Dies wirkt sich auf Mischen und Verarbeiten aus. Die Gelierungstemperatur ist ein weiterer wichtiger Faktor. Sie ist die Temperatur, bei der eine HPMC-Lösung ein Gel bildet. Diese Eigenschaft ist entscheidend für Anwendungen, die Hitzestabilität erfordern. Reinheit und die Einhaltung gesetzlicher Vorschriften sind ebenfalls entscheidend. Diese stellen sicher, dass das HPMC den Industriestandards entspricht. Sie bestätigen auch, dass es für den vorgesehenen Gebrauch sicher ist. Dies gilt insbesondere für pharmazeutische und Lebensmittelanwendungen.
HPMC-Eigenschaft | Auswirkungen auf die Leistung | Überlegungen |
---|---|---|
Viskositätsbereich | Steuert die Verdickungskraft und den Fluss. | Auftragsverfahren, gewünschte Konsistenz |
Substitutionstyp | Beeinflusst Löslichkeit, thermische Gelierung und Filmeigenschaften. | Wasserlöslichkeit, Hitzestabilität |
Partikelgröße | Beeinflusst die Auflösungsrate und Dispersion. | Mischzeit, Klumpenbildung |
Gelierungstemperatur | Bestimmt die Hitzestabilität und das Gelierverhalten. | Verarbeitungstemperatur, Produktstabilität |
Reinheit/Konformität | Gewährleistet Sicherheit und erfüllt Industriestandards. | Regulatorische Anforderungen, Endproduktsicherheit |
Verschiedene HPMC-Typen bieten unterschiedliche Vorteile. Beispielsweise könnte sich hochviskoses HPMC mit spezifischen Substitutionsgraden ideal für eine pharmazeutische Tablette mit kontrollierter Freisetzung eignen. Umgekehrt könnte niedrigviskoses HPMC mit unterschiedlichen Substitutionsgraden perfekt für ein klares Körperpflegegel geeignet sein. Die Wahl hängt von Ihren spezifischen Anforderungen und dem gewünschten Ergebnis ab. Berücksichtigen Sie all diese Faktoren. Dies gewährleistet eine optimale Produktleistung und trägt dazu bei, regulatorische Anforderungen zu erfüllen.
3. Welche HPMC-Sorte eignet sich für pharmazeutische Anwendungen?
In der Pharmaindustrie ist HPMC ein weit verbreiteter Hilfsstoff. Seine Vielseitigkeit macht es für verschiedene Wirkstoffabgabesysteme geeignet. Die Wahl des HPMC-Typs hängt von der jeweiligen Anwendung ab. Diese Wahl wirkt sich auf die Freisetzung und Stabilität des Arzneimittels aus.
Bei festen Darreichungsformen wie Tabletten und Kapseln fungiert HPMC als Bindemittel. Es verleiht mechanische Festigkeit. Außerdem hilft es beim Zerfall. Verschiedene HPMC-Typen bieten unterschiedliche Bindungsstärken. Dies wirkt sich auf die Härte der Tablette aus. Es beeinflusst auch die Zerbrechlichkeit. HPMC ist auch für Formulierungen mit kontrollierter Freisetzung von entscheidender Bedeutung. Es bildet eine Gelschicht um die Tablette. Diese Schicht steuert die Freisetzungsrate des Arzneimittels. HPMC mit hoher Viskosität wird häufig für eine verlängerte Freisetzung bevorzugt. HPMC mit niedriger Viskosität kann für eine sofortige Freisetzung verwendet werden. In flüssigen Arzneimitteln und Suspensionen fungiert HPMC als Suspensionsmittel. Es verhindert das Absetzen von Partikeln. Außerdem verbessert es die Konsistenz. Dies gewährleistet eine gleichmäßige Dosierung. Es gibt strenge gesetzliche Standards und Arzneibuchanforderungen. In Arzneimitteln verwendetes HPMC muss diese erfüllen. Dazu gehören Standards wie USP, EP und JP. Diese Standards gewährleisten Reinheit und Qualität. Fallstudien zeigen die Rolle von HPMC bei der Arzneimittelverabreichung. Es wird beispielsweise in Matrixtabletten verwendet. Es ist auch in Filmbeschichtungen enthalten. Diese Anwendungen unterstreichen seine Bedeutung. Sie zeigen auch seine Anpassungsfähigkeit.
Pharmazeutische Anwendung | Empfohlene HPMC-Eigenschaften | Beispiel für Güteklassenmerkmale |
---|---|---|
Tablet-Bindung | Gute Kompressibilität, moderate Viskosität | Niedrige bis mittlere Viskosität, hohe Reinheit |
Kontrollierte Freisetzung | Hohe Viskosität, gleichmäßige Gelierung, geringe Substitution | Hohes Molekulargewicht, spezifisches Methoxyl/Hydroxypropoxyl-Verhältnis |
Fahrwerksstabilisierung | Mittlere bis hohe Viskosität, gutes Suspensionsvermögen | Mittlere Viskosität, gute Wasserlöslichkeit |
Filmbeschichtung | Niedrigviskose, gut filmbildende, klare Lösungen | Niedrige Viskosität, hervorragende Filmeigenschaften |
Ophthalmische Lösungen | Niedrige Viskosität, nicht reizend, gute Klarheit | Niedrige Viskosität, hohe Reinheit, steril |
Die Auswahl der richtigen HPMC-Qualität für pharmazeutische Anwendungen erfordert sorgfältige Überlegungen. Sie müssen die gewünschten Wirkstofffreisetzungsprofile mit den Verarbeitungsanforderungen abwägen. Die Einhaltung gesetzlicher Vorschriften ist ebenfalls von größter Bedeutung. Die Zusammenarbeit mit einem kompetenten Lieferanten hilft Ihnen, die beste Qualität zu wählen. Dies garantiert Produktwirksamkeit und -sicherheit.
4. Welche HPMC-Typen eignen sich optimal für Baumaterialien?
In der Bauindustrie ist HPMC ein wichtiger Zusatzstoff. Es verbessert die Leistung verschiedener Baumaterialien. Seine Eigenschaften verbessern die Verarbeitbarkeit, Haftung und Haltbarkeit. Die Wahl der richtigen HPMC-Sorte ist für den Erfolg eines Bauprojekts von entscheidender Bedeutung.
HPMC wird häufig in zementbasierten Produkten verwendet. Dazu gehören Mörtel, Putze und Fliesenkleber. Es hat einen erheblichen Einfluss auf die Verarbeitbarkeit. Die Mischung lässt sich dadurch leichter verteilen. Außerdem verlängert es die offene Zeit. Dadurch bleibt mehr Zeit für die Anwendung. HPMC verbessert die Haftfestigkeit. Es schafft eine stärkere Verbindung zwischen Materialien. Auch die Wasserrückhalteeigenschaften sind entscheidend. HPMC verhindert einen schnellen Wasserverlust aus der Mischung. Dies gewährleistet eine ausreichende Hydratisierung des Zements. Außerdem reduziert es die Rissbildung. Das Ergebnis ist eine haltbarere Oberfläche. HPMC beeinflusst die Standfestigkeit. Es verhindert das Absacken vertikaler Flächen. Dies ist wichtig für dicke Anwendungen. Außerdem hilft es bei der Rissvermeidung. Dies ist auf die verbesserte Hydratisierung und das verringerte Schrumpfen zurückzuführen. Für unterschiedliche Bauanforderungen sind spezielle HPMC-Typen erhältlich. Einige Typen sind beispielsweise für selbstverlaufende Massen konzipiert. Andere sind für Wärmedämmverbundsysteme (WDVS) optimiert. Diese speziellen Typen gewährleisten optimale Leistung. Sie erfüllen auch spezifische Anwendungsanforderungen.
Bauantrag | Wichtige HPMC-Funktionalität | Gewünschte HPMC-Qualitätseigenschaften |
---|---|---|
Fliesenkleber | Verbesserte Verarbeitbarkeit, verlängerte offene Zeit, Standfestigkeit | Hohes Wasserrückhaltevermögen, mittlere bis hohe Viskosität |
Putze | Verbesserte Haftung, Rissvermeidung, glatte Oberfläche | Gute Verarbeitbarkeit, mäßige Wasserspeicherung |
Mörser | Bessere Konsistenz, geringere Entmischung, höhere Festigkeit | Mittlere Viskosität, gute Wasserrückhaltung, Luftporenbildung |
Selbstverlaufsmassen | Durchflusskontrolle, reduziertes Ausbluten, verbesserte Oberflächenbeschaffenheit | Niedrige Viskosität, gute Fließeigenschaften, schnelle Auflösung |
WDVS | Haftung auf der Isolierung, Flexibilität, Witterungsbeständigkeit | Hohes Wasserrückhaltevermögen, gute Filmbildung, hohe Viskosität |
Bei der Auswahl der optimalen HPMC-Sorte für Baumaterialien müssen verschiedene Faktoren berücksichtigt werden. Sie müssen Materialart, Anwendungsmethode und gewünschte Leistung berücksichtigen. Die richtige HPMC-Sorte kann zu deutlichen Verbesserungen führen. Sie verbessert die Materialqualität und steigert die Baueffizienz. Das Ergebnis sind bessere und langlebigere Strukturen.
5. Welche Leistung bringt HPMC in Körperpflege- und Kosmetikprodukten?
In der Körperpflege- und Kosmetikindustrie ist HPMC ein wertvoller Inhaltsstoff. Es trägt zur Produktstabilität, Textur und sensorischen Attraktivität bei. Seine vielfältigen Eigenschaften machen es für eine breite Palette von Formulierungen geeignet. Dies macht HPMC zu einer vielseitigen Wahl für viele kosmetische Anwendungen.
HPMC dient als Verdickungsmittel und Stabilisator in Cremes und Lotionen. Es sorgt für die gewünschte Konsistenz und verhindert die Trennung von Inhaltsstoffen. Dies gewährleistet ein glattes, gleichmäßiges Produkt. Seine filmbildenden Eigenschaften sind in Haarpflege- und Stylingprodukten von Vorteil. HPMC bildet einen leichten, flexiblen Film auf dem Haar. Dieser bietet Halt und Schutz. Zudem reduziert es Frizz. In Wasch- und Reinigungsmitteln wirkt HPMC als Rheologiemodifikator. Es reguliert den Fluss und verhindert das Absetzen von Wirkstoffen. Dies gewährleistet die Produktwirksamkeit. Die Verträglichkeit mit anderen Inhaltsstoffen ist bei Körperpflegeformulierungen entscheidend. HPMC ist grundsätzlich mit einer Vielzahl gängiger kosmetischer Inhaltsstoffe kompatibel. Dazu gehören Tenside, Emollientien und Konservierungsmittel. Auch sensorische Eigenschaften sind wichtig. HPMC kann das Tragegefühl eines Produkts auf Haut und Haar verbessern. Es kann ein glattes, nicht klebriges Gefühl vermitteln. Dies steigert das allgemeine Benutzererlebnis. Die Verbraucherwahrnehmung wird von diesen Eigenschaften beeinflusst. Eine angenehme Textur und Haptik tragen zur Produktakzeptanz bei. Deshalb ist HPMC für viele Formulierer die bevorzugte Wahl.
Körperpflegeprodukt | HPMC-Funktion | Vorteile |
---|---|---|
Cremes und Lotionen | Verdickungsmittel, Stabilisator | Glatte Textur, verbesserte Streichfähigkeit, erhöhte Stabilität |
Shampoos und Spülungen | Verdickungsmittel, Schaumverstärker | Reichhaltiger Schaum, verbesserte Viskosität, besseres Haargefühl |
Haargele und -schaum | Filmbildner, Rheologiemodifikator | Starker Halt, kein Abblättern, natürliches Gefühl |
Flüssigseifen | Verdickungsmittel, Stellmittel | Konstante Viskosität, verhindert das Absetzen der Inhaltsstoffe |
Sonnenschutzmittel | Verdickungsmittel, Emulsionsstabilisator | Gleichmäßiger Auftrag, verbesserte Wasserbeständigkeit |
Bei der Auswahl der richtigen HPMC-Qualität für Körperpflegeprodukte müssen die gewünschte Textur, Stabilität und das sensorische Profil berücksichtigt werden. Auch die Kompatibilität mit anderen Inhaltsstoffen muss berücksichtigt werden. Die richtige HPMC-Qualität kann die Produktleistung deutlich verbessern und die Kundenzufriedenheit steigern. Dies trägt zur Herstellung hochwertiger und ansprechender Körperpflegeprodukte bei.
6. Welche Faktoren beeinflussen die Auswahl der HPMC-Sorte?
Die Auswahl der richtigen HPMC-Sorte ist ein systematischer Prozess. Dabei werden mehrere Schlüsselfaktoren berücksichtigt. Diese Faktoren stellen sicher, dass die ausgewählte Sorte Ihren spezifischen Anwendungsanforderungen entspricht. Durch sorgfältige Berücksichtigung dieser Elemente können kostspielige Fehler vermieden werden.
Berücksichtigen Sie zunächst Ihre projektspezifischen Anforderungen. Welche Rheologie benötigen Sie? Welche Abbindezeit ist ideal? Welche Stabilität ist notwendig? Beispielsweise benötigt ein schnell abbindender Mörtel ein anderes HPMC als eine pharmazeutische Tablette mit langsamer Wirkstofffreisetzung. Auch die Kompatibilität mit anderen Rohstoffen ist entscheidend. HPMC muss synergetisch mit allen Komponenten Ihrer Formulierung zusammenarbeiten. Inkompatibilität kann zu unerwünschten Reaktionen führen. Sie kann auch Produktversagen verursachen. Auch Verarbeitungsbedingungen und -geräte spielen eine Rolle. Einige HPMC-Typen dispergieren besser in kaltem Wasser. Andere benötigen heißes Wasser. Ihre Mischgeräte können die Wahl ebenfalls beeinflussen. Ein Hochschermischer kann andere HPMC-Typen verarbeiten als ein Niedrigschermischer. Eine Kosten-Nutzen-Analyse der verschiedenen Typen ist ebenfalls wichtig. Während ein Premiumtyp eine überlegene Leistung bieten kann, reicht möglicherweise eine günstigere Option aus. Sie müssen Leistung und Kosten in Einklang bringen. Lieferantensupport und technische Unterstützung sind von unschätzbarem Wert. Ein guter Lieferant bietet technische Daten. Er stellt auch Anwendungshinweise zur Verfügung. Er kann bei der Fehlerbehebung helfen. Diese Unterstützung gewährleistet, dass Sie eine fundierte Entscheidung treffen. Sie hilft auch, Ihre Formulierung zu optimieren.
Faktor | Beschreibung | Beispielüberlegung |
---|---|---|
Projektanforderungen | Gewünschte Rheologie, Abbindezeit, Stabilität, Eigenschaften des Endprodukts | Viskosität, Gelierungstemperatur, Wasserretention |
Kompatibilität | Wechselwirkung mit anderen Rohstoffen in der Formulierung | pH-Empfindlichkeit, Ionenstärke, Vorhandensein anderer Polymere |
Verarbeitungsbedingungen | Temperatur, Mischgerät, Zugabereihenfolge | Lösungsgeschwindigkeit, Dispersionseigenschaften |
Kosten-Nutzen-Analyse | Balance zwischen Leistung und Wirtschaftlichkeit | Preis pro kg, erforderliche Dosierung, Gesamtkosten der Formulierung |
Lieferantensupport | Technische Daten, Anwendungshinweise, Fehlerbehebung | Technische Datenblätter, Formulierungsunterstützung, Musterverfügbarkeit |
Durch die systematische Bewertung dieser Faktoren können Sie sicher die optimale HPMC-Qualität auswählen. Dieser Ansatz minimiert Risiken und maximiert die Leistung Ihres Produkts. Er stellt sicher, dass Ihr Projekt seine technischen und wirtschaftlichen Ziele erreicht.
7. Wie können Sie häufige Probleme bei HPMC-Anwendungen beheben?
Selbst bei sorgfältiger Auswahl kann die HPMC-Anwendung manchmal eine Herausforderung darstellen. Kenntnisse zur Behebung häufiger Probleme sparen Zeit und Ressourcen. Durch effektive Problemlösung wird eine gleichbleibende Produktqualität gewährleistet.
Ein häufiges Problem ist schlechte Auflösung oder Klumpenbildung. Dies passiert oft, wenn HPMC zu schnell zu Wasser gegeben wird. Es kann auch auftreten, wenn das Wasser zu kalt ist. Versuchen Sie, HPMC in einem Nichtlösungsmittel vorzudispergieren. Dies könnte Glycerin oder Propylenglykol sein. Geben Sie diese Aufschlämmung dann zu Wasser. Alternativ können Sie heißes Wasser für die anfängliche Dispersion verwenden. Kühlen Sie es anschließend ab, um eine vollständige Auflösung zu ermöglichen. Auch die Viskositätskontrolle ist häufig problematisch. Ist die Viskosität zu niedrig, benötigen Sie möglicherweise eine höhere HPMC-Konzentration. Oder Sie benötigen eine höhere Viskositätsklasse. Ist sie zu hoch, reduzieren Sie die Konzentration. Oder wechseln Sie zu einer niedrigeren Viskositätsklasse. Achten Sie auf eine ausreichende Mischzeit. So kann HPMC vollständig hydratisieren. Probleme mit der Filmintegrität oder Haftung können auftreten. Dies kommt häufig bei Beschichtungen vor. Es kann an einer unzureichenden HPMC-Konzentration liegen. Es können auch ungeeignete Trocknungsbedingungen vorliegen. Passen Sie die HPMC-Konzentration an. Optimieren Sie Trocknungstemperaturen und -zeiten. Tipps zur Optimierung der HPMC-Dispersion umfassen die Verwendung eines Hochschermischers. Geben Sie HPMC außerdem langsam und unter ständigem Rühren hinzu. Dies verhindert ein Verklumpen. Wenn alle Versuche scheitern, sollten Sie Expertenrat einholen. Anbieter verfügen oft über technische Supportteams. Diese können wertvolle Einblicke liefern und auf Grundlage ihrer Erfahrung Lösungen anbieten. Dies hilft Ihnen, komplexe Probleme zu bewältigen.
Ausgabe | Häufige Ursachen | Schritte zur Fehlerbehebung |
---|---|---|
Schlechte Auflösung/Klumpen | Schnelle Zugabe, unzureichendes Rühren, kaltes Wasser | In Nicht-Lösungsmittel vordispergieren, langsam hinzufügen, heißes Wasser verwenden, dann abkühlen lassen |
Inkonsistente Viskosität | Falsche HPMC-Konzentration, unvollständige Hydratisierung, Temperaturschwankungen | Konzentration anpassen, vollständige Flüssigkeitszufuhr sicherstellen, Temperatur kontrollieren |
Schlechte Filmintegrität/Haftung | Unzureichendes HPMC, unsachgemäße Trocknung, inkompatible Inhaltsstoffe | HPMC erhöhen, Trocknung optimieren, Zutatenverträglichkeit prüfen |
Schäumen | Hohe Agitation, bestimmte HPMC-Sorten | Reduzieren Sie die Bewegung, verwenden Sie Antischaummittel und wählen Sie schaumarmes HPMC |
Gelierungsprobleme | Falsche Temperatur, falsche HPMC-Qualität | Überprüfen Sie die Temperatur und wählen Sie HPMC mit der entsprechenden Gelierungstemperatur |
Wenn Sie diese häufigen Probleme und deren Lösungen verstehen, können Sie Ihre Produktion effizient aufrechterhalten und hochwertige Produkte sicherstellen. Proaktive Fehlerbehebung minimiert Ausfallzeiten und reduziert Materialverschwendung. Dies führt zu einer höheren Gesamtbetriebseffizienz.
Abschluss
Die Wahl der richtigen HPMC-Sorte ist eine strategische Entscheidung. Sie wirkt sich direkt auf Produktleistung und Fertigungseffizienz aus. Wir haben die grundlegenden Eigenschaften von HPMC untersucht und seine vielfältigen Anwendungen in den Bereichen Pharma, Bauwesen und Körperpflege untersucht. Das Verständnis der Nuancen von Viskosität, Substitution und Partikelgröße hilft Ihnen, fundierte Entscheidungen zu treffen. Durch die sorgfältige Abstimmung der HPMC-Sorten auf Ihre spezifischen Projektanforderungen erzielen Sie eine überragende Produktqualität. Zudem können Sie Produktionsprozesse optimieren. Dies führt zu weniger Abfall und verbesserter Kosteneffizienz. Morton bietet fachkundige Beratung und ein umfassendes Sortiment an HPMC-Lösungen. Arbeiten Sie mit Morton zusammen, um Ihre Formulierungen zu verfeinern. Nutzen Sie unseren technischen Support und erfahren Sie, wie unsere HPMC-Typen Ihre Produktstandards verbessern. Wir unterstützen Sie dabei, Ihre Produktionsziele zu erreichen.
Häufig gestellte Fragen
F1: Was ist die Hauptfunktion von HPMC in den meisten Anwendungen?
HPMC fungiert in erster Linie als Verdickungsmittel, Bindemittel und Filmbildner und verbessert die Konsistenz, Haftung und Stabilität verschiedener Produkte.
F2: Kann HPMC sowohl in wasserbasierten als auch in lösungsmittelbasierten Systemen verwendet werden?
HPMC ist hauptsächlich wasserlöslich und eignet sich daher ideal für wasserbasierte Systeme. Modifizierte HPMC-Typen können eine verbesserte Kompatibilität mit bestimmten organischen Lösungsmitteln bieten.
F3: Welcher Zusammenhang besteht zwischen der Viskosität von HPMC und seiner Anwendung?
HPMC-Typen mit höherer Viskosität bieten eine stärkere Verdickung und Wasserspeicherung, während Typen mit niedrigerer Viskosität für Anwendungen geeignet sind, die eine geringere Verdickung oder schnellere Auflösung erfordern.
F4: Ist HPMC für die Verwendung in Lebensmitteln und pharmazeutischen Produkten sicher?
Ja, bestimmte HPMC-Sorten sind für die Verwendung in Lebensmitteln und pharmazeutischen Produkten zugelassen und erfüllen strenge gesetzliche Reinheits- und Sicherheitsstandards.
F5: Welche Bedeutung hat die Gelierungstemperatur bei der HPMC-Auswahl?
Die Gelierungstemperatur gibt an, wann eine HPMC-Lösung beim Erhitzen geliert. Diese Eigenschaft ist entscheidend für Anwendungen, bei denen thermische Stabilität oder kontrollierte Freisetzung erwünscht sind.