Die Auswahl der richtigen Hydroxypropylmethylcellulose (HPMC)-Sorte stellt für viele Unternehmen eine Herausforderung dar. Diese Wahl wirkt sich direkt auf die Produktleistung, die Fertigungseffizienz und letztendlich den Markterfolg aus. Fehler können zu kostspieligen Neuformulierungen, Produktionsverzögerungen und einer beeinträchtigten Produktqualität führen und so zu erheblicher Frustration führen. Dieser Artikel bietet klare Hinweise zu HPMC-Sorten und hilft Ihnen, fundierte Entscheidungen zu treffen, um Ihre Produktentwicklung zu optimieren und hervorragende Ergebnisse zu erzielen. Der Leitfaden behandelt HPMC-Grundlagen, Klassifizierungsmethoden, gängige Sorten und Auswahlkriterien für verschiedene Anwendungen.
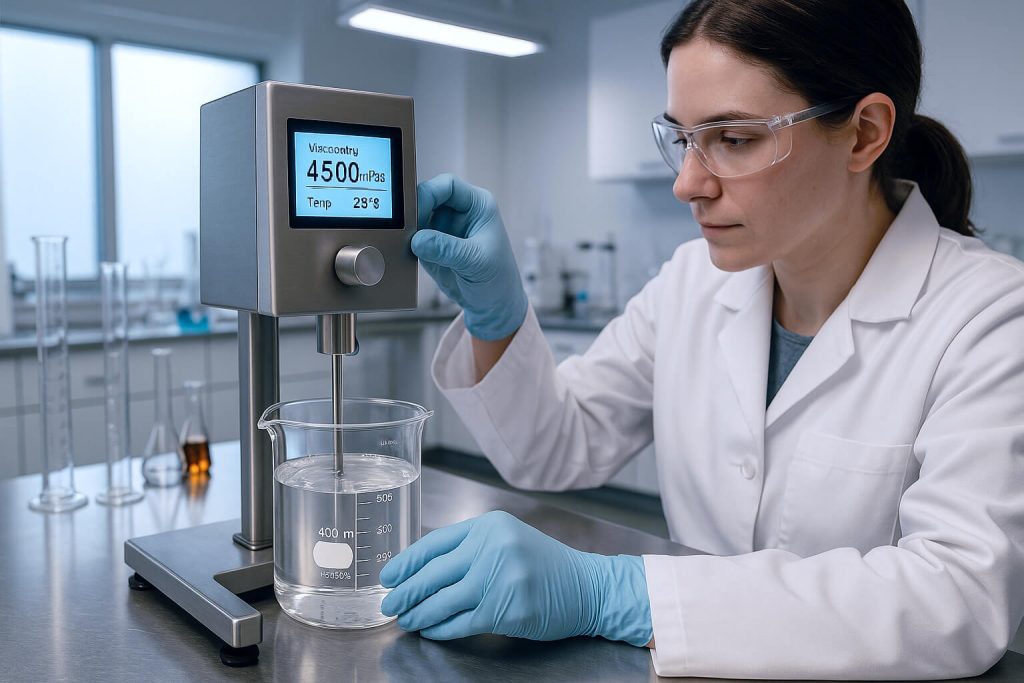
1. Was ist HPMC und warum ist es wichtig?
HPMC ist ein vielseitiges Polymer, das aus Zellulose, einer natürlichen Pflanzenfaser, gewonnen wird. Es wird chemisch modifiziert, um seine Eigenschaften zu verbessern und es für eine Vielzahl industrieller Anwendungen geeignet zu machen. Diese halbsynthetische Verbindung ist geruchs- und geschmacksneutral und erscheint als weißes bis cremefarbenes Pulver. Dank seiner einzigartigen Molekularstruktur löst es sich in kaltem Wasser auf und bildet eine klare Lösung, die beim Erhitzen eindickt. Diese thermische Gelierungseigenschaft ist für viele Anwendungen besonders wertvoll. Deshalb ist es wichtig … HPMC dient in verschiedenen Bereichen als Verdickungsmittel, Bindemittel, Filmbildner und Wasserrückhaltemittel.
Seine Bedeutung liegt in seiner Fähigkeit, Produktstabilität, Textur und Leistung zu verbessern. Im Bauwesen verbessert HPMC beispielsweise die Verarbeitbarkeit und Haftung von Mörtel. In der Pharmaindustrie steuert es die Wirkstofffreisetzung. In Lebensmitteln wirkt es als Stabilisator und Emulgator. Diese vielfältigen Funktionen machen HPMC zu einem unverzichtbaren Bestandteil moderner Herstellungsprozesse. Das Verständnis seiner grundlegenden Zusammensetzung hilft, seinen breiten Nutzen zu erkennen.
Eigentum | Beschreibung |
---|---|
Chemischer Ursprung | Cellulosederivat |
Aussehen | Weißes bis cremefarbenes Pulver |
Löslichkeit | Löslich in kaltem Wasser |
Thermisches Verhalten | Bildet beim Erhitzen ein Gel |
Schlüsselfunktionen | Verdickungsmittel, Bindemittel, Filmbildner, Wasserrückhaltemittel |
2. Wie werden HPMC-Typen klassifiziert?
HPMC-Typen werden hauptsächlich nach Viskosität, Substitutionstypen und Partikelgröße klassifiziert. Die Viskosität ist oft das erste betrachtete Merkmal, da sie die Verdickungskraft des Materials in Lösung bestimmt. Hersteller messen die Viskosität bei bestimmten Konzentrationen und Temperaturen, typischerweise mit einer 2%-Lösung bei 20 °C. Höhere Viskositätswerte weisen auf eine dickere Lösung hin. Dieser Messwert gibt einen direkten Hinweis auf die Leistung des HPMC in einer bestimmten Anwendung. Unterschiedliche Anwendungen erfordern unterschiedliche Verdickungsgrade. Beispielsweise benötigt eine Beschichtung eine geringere Viskosität als eine Retardtablette.
Substitutionstypen bezeichnen den Grad und das Muster der an das Celluloserückgrat gebundenen Methoxy- und Hydroxypropoxygruppen. Diese Gruppen beeinflussen Eigenschaften wie Gelierungstemperatur, Löslichkeit und Filmflexibilität. Auch die Partikelgröße spielt eine wichtige Rolle und beeinflusst die Auflösungsgeschwindigkeit und Dispersion. Feinere Partikel lösen sich schneller auf, lassen sich aber unter Umständen schwerer dispergieren, ohne zu verklumpen. Gröbere Partikel dispergieren leichter, benötigen aber länger für die vollständige Hydratisierung. Jeder Klassifizierungsfaktor trägt dazu bei, die spezifischen Leistungsmerkmale einer HPMC-Sorte zu definieren und deren Auswahl für bestimmte Anwendungen zu bestimmen.
Klassifizierungsfaktor | Auswirkungen auf die Leistung |
---|---|
Viskosität | Verdickungskraft, Fließeigenschaften |
Substitutionstyp | Gelierungstemperatur, Löslichkeit, Filmeigenschaften |
Partikelgröße | Lösungsgeschwindigkeit, Dispersionsverhalten |
3. Was sind die gängigen HPMC-Typen und ihre Eigenschaften?
Gängige HPMC-Typen sind auf bestimmte Branchen zugeschnitten und weisen jeweils unterschiedliche Eigenschaften auf. Pharmazeutische Typen, oft mit Buchstaben wie K, E, F und P gekennzeichnet, unterscheiden sich in ihrem Methoxyl- und Hydroxypropoxyl-Gehalt, der sich auf ihre Gelierungstemperatur und Löslichkeit auswirkt. HPMC vom Typ K beispielsweise hat eine niedrigere Gelierungstemperatur und wird aufgrund seiner starken Gelierungseigenschaften häufig für Anwendungen mit verzögerter Freisetzung eingesetzt. HPMC vom Typ E hat eine höhere Gelierungstemperatur und wird häufig in Filmbeschichtungen und Bindemitteln verwendet. Diese Unterschiede ermöglichen eine präzise Kontrolle der Wirkstofffreisetzung und der Tablettenintegrität. Aber hier ist die Sache … Die Auswahl der richtigen pharmazeutischen Qualität gewährleistet eine optimale Arzneimittelverabreichung und Patientensicherheit.
Lebensmittelqualitäten wie E464 erfüllen strenge gesetzliche Vorschriften für den Verzehr. Sie dienen als Verdickungsmittel, Stabilisatoren und Emulgatoren in verschiedenen Lebensmitteln. Bauqualitäten sind auf hohe Wasserrückhaltefähigkeit und verbesserte Verarbeitbarkeit in zementbasierten Materialien ausgelegt. Sie weisen oft eine höhere Viskosität und spezielle Modifikationen zur Verbesserung der Haftung und der Offenzeit auf. Andere Industriequalitäten dienen unterschiedlichen Zwecken, von Körperpflegeprodukten bis hin zu Farben und Beschichtungen. Jede Qualität ist so konzipiert, dass sie in ihrem vorgesehenen Anwendungsbereich spezifische Leistungsvorteile bietet.
HPMC-Sortentyp | Typische Merkmale | Primäre Anwendungen |
---|---|---|
Pharmazeutisch (K-Typ) | Niedrigere Gelierungstemperatur, starke Gelierung | Retardtabletten |
Pharmazeutisch (E-Typ) | Höhere Gelierungstemperatur, gute Filmbildung | Filmbeschichtungen, Bindemittel |
Lebensmittel (E464) | Hohe Reinheit, verdickend, stabilisierend | Backwaren, Milchprodukte, Dressings |
Konstruktion | Hohe Wasserspeicherfähigkeit, verbesserte Verarbeitbarkeit | Fliesenkleber, Putze |
4. Wie wirkt sich die Viskosität auf die HPMC-Leistung aus?
Die Viskosität ist ein entscheidender Parameter für die Leistung von HPMC in verschiedenen Anwendungen. HPMC-Typen mit niedriger Viskosität ergeben dünne Lösungen und eignen sich daher ideal für Filmüberzüge auf Tabletten oder als ophthalmische Lösungen. Sie bilden eine glatte, gleichmäßige Schicht ohne übermäßige Verdickung. Typen mit mittlerer Viskosität dienen als effektive Bindemittel in Tablettenformulierungen oder als allgemeine Verdickungsmittel in flüssigen Produkten. Sie bieten ein ausgewogenes Verhältnis zwischen Fließfähigkeit und struktureller Integrität. HPMC-Typen mit hoher Viskosität bilden dicke, viskose Lösungen, die für Retard-Arzneimittelformulierungen unerlässlich sind, da sie die Auflösungs- und Absorptionsgeschwindigkeit eines Arzneimittels steuern. Sie werden auch in Zementmörteln eingesetzt, um die Wasserspeicherung zu verbessern und vorzeitiges Austrocknen zu verhindern. Jetzt fragen Sie sich vielleicht … wie wird diese Viskosität gemessen?
Die Viskosität wird üblicherweise mit einem Brookfield-Viskosimeter bei einer bestimmten Konzentration und Temperatur gemessen, häufig mit einer 2%-Lösung bei 20 °C. Dieser standardisierte Test gewährleistet konsistente Ergebnisse und ermöglicht einen genauen Vergleich verschiedener HPMC-Typen. Die Wahl der Viskosität wirkt sich direkt auf Textur, Stabilität und funktionelle Eigenschaften des Endprodukts aus. Beispielsweise verhindert hochviskoses HPMC in einer Farbformulierung das Ablaufen und verbessert die Streichfähigkeit, während niedrigviskoses HPMC in einem Flüssigwaschmittel für leichtes Ausgießen sorgt.
Viskositätsbereich | Typische Anwendungen | Auswirkungen auf die Leistung |
---|---|---|
Niedrig | Filmüberzüge, ophthalmische Lösungen | Dünne, gleichmäßige Schichten, schnelle Auflösung |
Medium | Tablettenbinder, allgemeine Verdickungsmittel | Ausgeglichener Fluss und strukturelle Integrität |
Hoch | Zementmörtel mit verzögerter Freisetzung | Kontrollierte Freisetzung, Wasserspeicherung, Anti-Sag |
5. Welche Rolle spielen Substitutionstypen bei der HPMC-Auswahl?
Substitutionsarten, insbesondere der Methoxyl- und Hydroxypropoxylgehalt, beeinflussen die Eigenschaften und die Auswahl von HPMC maßgeblich. Der Methoxylgehalt bestimmt maßgeblich die Gelierungstemperatur von HPMC-Lösungen. Ein höherer Methoxylgehalt führt in der Regel zu niedrigeren Gelierungstemperaturen. Dies ist wichtig für Anwendungen, bei denen eine thermische Gelierung bei bestimmten Temperaturen erwünscht ist, wie beispielsweise bei bestimmten Lebensmitteln oder Systemen mit kontrollierter Freisetzung. Der Hydroxypropoxylgehalt hingegen bestimmt maßgeblich die Wasserlöslichkeit und Oberflächenaktivität von HPMC. Ein höherer Hydroxypropoxylgehalt erhöht die Wasserlöslichkeit und kann die Filmbildung und die Haftungseigenschaften verbessern. Lassen Sie mich erklären … Diese subtilen chemischen Unterschiede führen zu erheblichen funktionellen Abweichungen.
Das Gleichgewicht zwischen diesen beiden Substitutionsgruppen ermöglicht es Herstellern, HPMC-Typen für spezifische Anwendungen zu optimieren. Beispielsweise könnte ein HPMC mit einem bestimmten Methoxy-Hydroxypropoxyl-Verhältnis aufgrund seiner Fähigkeit, einen starken, flexiblen Film in einer pharmazeutischen Beschichtung zu bilden, gewählt werden, während ein anderes Verhältnis aufgrund seiner besseren Wasserspeicherung in einem Baumaterial bevorzugt wird. Das Verständnis dieser Substitutionsmuster hilft, das Verhalten eines HPMC-Typs unter verschiedenen Bedingungen und in verschiedenen Formulierungen vorherzusagen. Diese chemische Anpassung gewährleistet optimale Leistung für unterschiedliche industrielle Anforderungen.
Substitutionstyp | Primärer Einfluss | Anwendungsrelevanz |
---|---|---|
Methoxylgehalt | Gelierungstemperatur | Thermische Gelierung, kontrollierte Freisetzung |
Hydroxypropoxyl-Gehalt | Wasserlöslichkeit, Oberflächenaktivität | Filmbildung, Haftung, Verdickung |
6. Wie beeinflusst die Partikelgröße die HPMC-Funktionalität?
Die Partikelgröße beeinflusst die HPMC-Funktionalität maßgeblich, insbesondere die Auflösungsgeschwindigkeit und das Dispersionsverhalten. Feine HPMC-Pulver lösen sich schneller auf, was bei Anwendungen, die eine schnelle Hydratisierung erfordern, wie z. B. Instant-Getränkemischungen oder schnell abbindenden Baumaterialien, von Vorteil ist. Feinere Partikel neigen jedoch auch eher zum Verklumpen oder zur Klumpenbildung, wenn sie nicht richtig dispergiert werden. Dies kann zu einer ungleichmäßigen Hydratisierung und inkonsistenter Produktleistung führen. Gröbere HPMC-Partikel hingegen dispergieren sich leichter, ohne zu verklumpen, benötigen aber länger für die vollständige Hydratisierung. Sie werden häufig bei Anwendungen bevorzugt, bei denen eine langsamere, kontrollierte Auflösung akzeptabel oder sogar erwünscht ist, wie z. B. bei bestimmten Formulierungen mit verzögerter Freisetzung oder Trockenmörteln. Dies ist wichtig, weil… Die richtige Partikelgröße gewährleistet eine effiziente Verarbeitung und gleichbleibende Produktqualität.
Die Wahl der Partikelgröße beeinflusst auch die endgültige Textur und das Aussehen eines Produkts. Beispielsweise kann bei pharmazeutischen Suspensionen eine feinere Partikelgröße gewählt werden, um eine glatte, gleichmäßige Konsistenz zu gewährleisten und Sedimentation zu verhindern. Im Gegensatz dazu kann bei Trockenbauprodukten eine gröbere Partikelgröße verwendet werden, um deren Fließfähigkeit zu verbessern und Staubbildung bei der Handhabung zu reduzieren. Hersteller bieten HPMC häufig in verschiedenen Partikelgrößen an, darunter Standard-, Fein- und sogar Ultrafeinkorn, um unterschiedlichen Verarbeitungs- und Anwendungsanforderungen gerecht zu werden. Die Wahl der richtigen Partikelgröße ist ein entscheidender Schritt zur Optimierung der HPMC-Leistung.
Partikelgröße | Auflösungsrate | Dispersionsverhalten | Typischer Anwendungsfall |
---|---|---|---|
Bußgeld | Schnell | Neigt zur Verklumpung | Sofortmischungen, schnelle Hydratisierung |
Grob | Langsam | Einfache Dispersion | Trockenmörtel mit verzögerter Freisetzung |
7. Was sind die spezifischen Anwendungen für verschiedene HPMC-Typen?
Aufgrund ihrer maßgeschneiderten Eigenschaften finden verschiedene HPMC-Typen spezifische Anwendungen in unterschiedlichen Branchen. In der Pharmaindustrie ist HPMC ein Allroundtalent. Es dient als Bindemittel in Tabletten und gewährleistet deren strukturelle Integrität. Zudem fungiert es als Filmbildner für Tablettenüberzüge, schützt die Wirkstoffe und erleichtert das Schlucken. Ein entscheidender Vorteil von HPMC ist die Verwendung als Matrixbildner in Retardformulierungen, um die Geschwindigkeit zu steuern, mit der ein Medikament in den Körper freigesetzt wird. Beispielsweise kann hochviskoses HPMC zur Herstellung von Retardtabletten für chronische Erkrankungen verwendet werden. In der Lebensmittelindustrie dient HPMC als Verdickungsmittel in Soßen und Dressings, als Stabilisator in Milchprodukten und als Geliermittel in Backwaren. Es verbessert die Textur und verlängert die Haltbarkeit. Willst du das Geheimnis erfahren? HPMC trägt dazu bei, die Konsistenz und Attraktivität des Produkts aufrechtzuerhalten.
In der Bauindustrie ist HPMC entscheidend für die Verbesserung der Leistungsfähigkeit zementbasierter Materialien. Es verbessert die Wasserspeicherung in Fliesenklebern, verhindert vorzeitiges Austrocknen und verbessert die Haftfestigkeit. In Putzen und Gips verbessert es die Verarbeitbarkeit und die Standfestigkeit. Bei selbstnivellierenden Spachtelmassen sorgt HPMC für eine glatte, ebene Oberfläche. Auch Körperpflegeprodukte profitieren von HPMC, wo es als Verdickungsmittel in Shampoos und Lotionen sowie als Filmbildner in Kosmetika fungiert. Jede Anwendung nutzt spezifische HPMC-Eigenschaften – von der Viskosität bis zur thermischen Gelierung –, um die gewünschten Produkteigenschaften und -leistungen zu erzielen.
Industrie | HPMC-Anwendung | Spezifische Funktion |
---|---|---|
Pharmazeutische | Tabletten, Überzüge, Retardtabletten | Bindemittel, Filmbildner, Matrixbildner |
Essen | Saucen, Milchprodukte, Backwaren | Verdickungsmittel, Stabilisator, Geliermittel |
Konstruktion | Fliesenkleber, Putze, Verlaufsmassen | Wasserrückhaltevermögen, Verarbeitbarkeit, Standfestigkeit |
Körperpflege | Shampoos, Lotionen, Kosmetik | Verdickungsmittel, Filmbildner |
8. Wie wählen Sie die richtige HPMC-Sorte für ein Projekt aus?
Die Auswahl der richtigen HPMC-Sorte erfordert einen systematischen Ansatz, bei dem die HPMC-Eigenschaften an die spezifischen Anwendungsanforderungen angepasst werden. Definieren Sie zunächst die gewünschten funktionellen Eigenschaften Ihres Endprodukts. Benötigen Sie Verdickungs-, Binde-, Filmbildungs- oder Wasserrückhalteeigenschaften? Berücksichtigen Sie den erforderlichen Viskositätsbereich, die Auflösungsrate und die thermischen Gelierungseigenschaften. Beispielsweise benötigt eine Arzneimitteltablette mit verzögerter Freisetzung ein hochviskoses HPMC mit spezifischen Gelierungseigenschaften. Eine Farbformulierung, die Standfestigkeit erfordert, benötigt ebenfalls eine hochviskose Sorte. Das Endergebnis? Ein klares Verständnis der Anforderungen Ihres Produkts ist die Grundlage für die anfängliche Auswahl.
Berücksichtigen Sie als Nächstes die Einhaltung gesetzlicher Vorschriften und Industriestandards. HPMC, das in Arzneimitteln oder Lebensmitteln verwendet wird, muss strenge Reinheits- und Sicherheitsvorschriften erfüllen. Stellen Sie stets sicher, dass die gewählte Qualität den relevanten Arzneibüchern (z. B. USP, EP) oder Vorschriften für Lebensmittelzusatzstoffe (z. B. E464) entspricht. Führen Sie abschließend eine Kosten-Nutzen-Analyse durch. Obwohl einige spezielle HPMC-Typen eine überlegene Leistung bieten, sind ihre höheren Kosten möglicherweise nicht für alle Anwendungen gerechtfertigt. Pilotversuche und Tests im kleinen Maßstab sind entscheidend, um die Leistung des ausgewählten Typs in Ihrem spezifischen Formulierungs- und Herstellungsprozess zu validieren. Dieser iterative Prozess stellt sowohl die technische Eignung als auch die wirtschaftliche Rentabilität sicher.
Auswahlschritt | Wichtige Überlegungen |
---|---|
Produktanforderungen definieren | Gewünschte Funktion (Verdickung, Bindung), Viskosität, Auflösung, Gelierung |
Einhaltung gesetzlicher Vorschriften | Arzneibücher (USP, EP), Lebensmittelzusatzstoffverordnungen (E464) |
Kosten-Nutzen-Analyse | Leistung vs. Kosten, Wirtschaftlichkeit |
Pilotversuche | Validieren Sie die Leistung in einer bestimmten Formulierung |
9. Welche Aspekte der Qualitätskontrolle sind bei HPMC-Typen zu beachten?
Die Qualitätskontrolle von HPMC-Sorten ist unerlässlich, um eine gleichbleibende Produktleistung und -sicherheit zu gewährleisten. Reinheits- und Verunreinigungsprofile sind insbesondere für pharmazeutische und Lebensmittelanwendungen von größter Bedeutung. Hersteller müssen sicherstellen, dass HPMC-Chargen frei von Verunreinigungen sind und strenge Reinheitsstandards erfüllen. Dies beinhaltet häufig Tests auf Schwermetalle, Lösungsmittelrückstände und mikrobielle Grenzwerte. Stabilität und Haltbarkeit sind ebenfalls wichtige Aspekte. HPMC sollte seine physikalischen und chemischen Eigenschaften über die vorgesehene Lagerdauer hinweg beibehalten. Geeignete Lagerbedingungen, wie Temperatur- und Feuchtigkeitskontrolle, sind notwendig, um die Qualität zu erhalten. Was bedeutet das für Sie? Eine gleichbleibende Qualität wirkt sich direkt auf die Zuverlässigkeit Ihres Produkts aus.
Die Chargenkonsistenz ist ein weiterer wichtiger Aspekt der Qualitätskontrolle. Abweichungen zwischen Chargen können zu Inkonsistenzen im Endprodukt führen und so Leistung und Verbraucherakzeptanz beeinträchtigen. Hersteller setzen strenge Testmethoden ein, darunter Viskositätsmessungen, Substitutionsanalysen und Partikelgrößenverteilungsanalysen, um sicherzustellen, dass jede Charge die Spezifikationen erfüllt. Analysezertifikate (CoA) liefern detaillierte Informationen über die Eigenschaften einer Charge und bestätigen deren Einhaltung der Qualitätsstandards. Regelmäßige Audits der HPMC-Lieferanten und interne Testprotokolle sind unerlässlich, um eine hohe Qualität zu gewährleisten. Diese Maßnahmen stellen sicher, dass das von Ihnen gelieferte HPMC stets die erwartete Leistung erbringt.
Aspekt der Qualitätskontrolle | Bedeutung | Testmethoden |
---|---|---|
Reinheit | Produktsicherheit, Einhaltung gesetzlicher Vorschriften | Schwermetalle, Restlösemittel, mikrobielle Grenzwerte |
Stabilität | Haltbarkeit, gleichbleibende Leistung | Beschleunigte Alterungstests, Lagerbedingungen |
Chargenkonsistenz | Produktzuverlässigkeit, gleichmäßige Leistung | Viskosität, Substitutionsanalyse, Partikelgröße |
10. Was sind die zukünftigen Trends und Innovationen in der HPMC-Technologie?
Die Zukunft der HPMC-Technologie konzentriert sich auf nachhaltige Produktionsmethoden, neue Modifizierungstechniken und neue Anwendungen. Die Entwicklung umweltfreundlicherer Herstellungsverfahren für HPMC, die Reduzierung von Energieverbrauch und Abfall, rückt zunehmend in den Fokus. Dazu gehört die Erforschung alternativer Rohstoffe und effizienterer Synthesewege. Innovationen in den Modifizierungstechniken zielen darauf ab, HPMC-Derivate mit verbesserten oder neuartigen Eigenschaften zu entwickeln. Forscher entwickeln beispielsweise HPMC mit verbesserter thermischer Stabilität, verbesserter Filmbildungsfähigkeit oder spezifischen Funktionalitäten für fortschrittliche Arzneimittelverabreichungssysteme. Diese Fortschritte versprechen, den Nutzen von HPMC noch weiter zu erweitern. So sieht der Deal aus … Diese Innovationen werden die Entwicklung neuer Produkte vorantreiben.
Auch neue Anwendungen prägen die Zukunft von HPMC. Im biomedizinischen Bereich wird HPMC aufgrund seiner Biokompatibilität für Tissue Engineering Scaffolds und Wundauflagen erforscht. Im Bereich nachhaltiger Verpackungen wird es als biologisch abbaubares Folienmaterial untersucht. Die Nachfrage nach pflanzlichen und nachhaltigen Inhaltsstoffen wächst stetig und positioniert HPMC als Schlüsselkomponente verschiedener Umweltinitiativen. Da die Industrie nach effizienteren, nachhaltigeren und leistungsstärkeren Materialien sucht, wird sich die HPMC-Technologie weiterentwickeln und neue Lösungen für komplexe Herausforderungen bieten. Diese Trends unterstreichen die Anpassungsfähigkeit von HPMC und seine anhaltende Relevanz in einer sich schnell verändernden Industrielandschaft.
Zukunftstrend | Beschreibung | Mögliche Auswirkungen |
---|---|---|
Nachhaltige Produktion | Umweltfreundliche Herstellung, alternative Rohstoffe | Reduzierter ökologischer Fußabdruck, Kosteneinsparungen |
Neue Modifikationen | Verbesserte thermische Stabilität, spezifische Funktionalitäten | Fortschrittliche Arzneimittelverabreichung, neuartige Materialeigenschaften |
Neue Anwendungen | Biomedizinische, nachhaltige Verpackungen | Neue Märkte, erweiterter Nutzen |
Abschluss
Das Verständnis der HPMC-Typen ist entscheidend für die Optimierung der Produktleistung und den Produktionserfolg. Wir haben die HPMC-Grundlagen, die detaillierte Klassifizierung nach Viskosität, Substitution und Partikelgröße behandelt und spezifische Anwendungen in den Bereichen Pharma, Lebensmittel und Bauwesen untersucht. Dieses Wissen ermöglicht Ihnen die Auswahl des passenden HPMC-Typs für Ihr Projekt und gewährleistet optimale Funktionalität und Konformität. Die richtige HPMC-Wahl führt zu verbesserter Produktqualität und optimierten Produktionsprozessen. Um sich einen Wettbewerbsvorteil zu sichern und sicherzustellen, dass Ihre Produkte höchsten Standards entsprechen, sollten Sie eine Partnerschaft mit Morton in Betracht ziehen. Wir bieten Ihnen kompetente Beratung und ein umfassendes Angebot an HPMC-Lösungen, die auf Ihre individuellen Bedürfnisse zugeschnitten sind. Kontaktieren Sie Morton noch heute, um Ihre spezifischen HPMC-Anforderungen zu besprechen und Ihre Produktentwicklung voranzutreiben.
Häufig gestellte Fragen
F1: Wofür wird HPMC in Arzneimitteln verwendet?
HPMC wird in der Pharmaindustrie häufig als Bindemittel, Filmbildner, Sprengmittel und Retardmittel in Tabletten und Kapseln eingesetzt. Darüber hinaus dient es als Verdickungsmittel und Stabilisator in flüssigen Formulierungen.
F2: Kann HPMC in Lebensmitteln verwendet werden?
Ja, HPMC ist als Lebensmittelzusatzstoff (E464) zugelassen und wird als Verdickungsmittel, Emulgator, Stabilisator und Geliermittel in verschiedenen Lebensmittelprodukten verwendet, darunter Backwaren, Milchprodukte und Dressings.
F3: Welchen Einfluss hat HPMC auf zementbasierte Materialien?
HPMC verbessert die Verarbeitbarkeit, Wasserrückhaltung und Haftung von zementbasierten Materialien wie Fliesenklebern, Putzen und selbstnivellierenden Spachtelmassen. Es verbessert außerdem deren Offenzeit und Standfestigkeit.
F4: Was ist der Unterschied zwischen HPMC mit niedriger und hoher Viskosität?
HPMC mit niedriger Viskosität eignet sich für Anwendungen, die dünne Filme oder eine schnelle Auflösung erfordern, wie z. B. Filmbeschichtungen. HPMC mit hoher Viskosität wird zur verzögerten Freisetzung, Verdickung und Wasserretention in Anwendungen wie Tabletten mit kontrollierter Freisetzung oder Zementmörtel eingesetzt.
F5: Ist HPMC ein natürliches oder synthetisches Polymer?
HPMC ist ein halbsynthetisches Polymer, das aus Zellulose gewonnen wird, einem natürlichen Polymer, das in pflanzlichen Zellwänden vorkommt. Es wird chemisch modifiziert, um seine Eigenschaften für verschiedene industrielle Anwendungen zu verbessern.