Die Wahl der richtigen HPMC-Dicke ist entscheidend. Viele Firmen wählen Sorten aus Gewohnheit und nicht nach tatsächlichem Bedarf. Das führt zu Problemen, schlechter Qualität und Abfall. Falsche HPMC-Dicken können zu einer schlechten Wasseraufnahme in Baumischungen, einer ungleichmäßigen Wirkstofffreisetzung in Tabletten oder instabilen Lebensmitteln führen. Gute Nachrichten! Wenn Sie wissen, wie die Dicke funktioniert und was Sie benötigen, können Sie bessere Produkte zu geringeren Kosten herstellen. Firmen, die die richtige HPMC-Sorte wählen, können Kosten um bis zu 15 % senken und bessere Produkte herstellen. Dieser Leitfaden hilft Ihnen, die HPMC-Grundlagen zu erlernen, die Sorten kennenzulernen und die beste Wahl zu treffen.
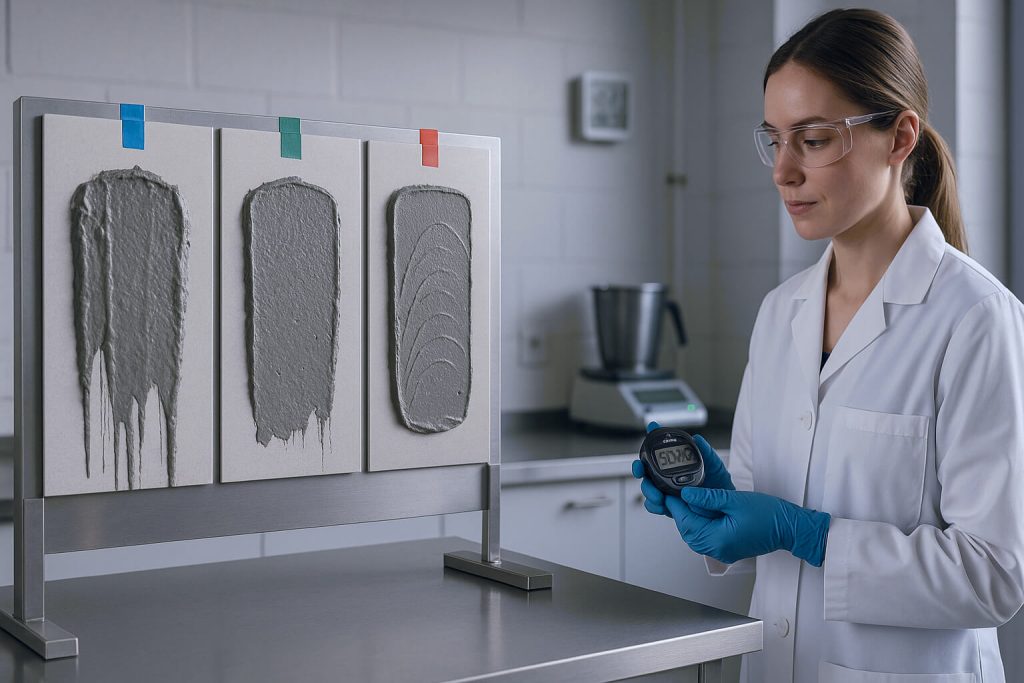
1. Was ist HPMC und warum ist seine Viskosität wichtig?
HPMC ist ein pflanzlicher Stoff, der in vielen Produkten verwendet wird. Es eignet sich zum Bau von Mischungen, Pillen und Lebensmitteln.
Das macht es besonders: Die Dichte von HPMC beeinflusst die Wirkung Ihrer Produkte. Beim Mischen mit Wasser bildet HPMC ein Gel. Dieses Gel steuert die Wasseraufnahme, -bindung und -abgabe.
Die HPMC-Dicke hängt ab von:
- Größe der Bits
- Chemische Zusammensetzung
- Verwendete Menge
- Hitze
- Mischkraft
Faktor | Einfluss auf die Dicke | Auswirkungen auf die Nutzung |
---|---|---|
Bitgröße | Größer = Dicker | Beeinflusst Kosten und benötigte Menge |
Chemische Zusammensetzung | Ändert die Wassermischung | Beeinflusst die Wirkung bei unterschiedlichen Temperaturen |
Verwendete Menge | Mehr = Viel dicker | Legt fest, wie viel Sie benötigen |
Hitze | Komplexe Effekte | Beeinflusst das Mischen und die Stabilität |
In Baumischungen steuert die HPMC-Dicke die Wasseraufnahme in Mörtel und Kleber. Dies beeinflusst die Verarbeitungszeit und die Haftfestigkeit. Ein Fliesenkleber mit zu geringer Dicke kann zu schnell trocknen. Dadurch bleibt den Arbeitern weniger Zeit zum Verlegen der Fliesen.
Bei Tabletten bestimmt die HPMC-Dicke, wie schnell Wirkstoffe freigesetzt werden. Eine höhere Dichte sorgt für dickere Gelschichten um die Tabletten. Dies verlangsamt die Wirkstofffreisetzung bei Tabletten mit verzögerter Wirkstofffreisetzung.
Lebensmittelhersteller verwenden HPMC, um stabile Mischungen und eine bessere Textur zu erzielen. Die falsche Dicke kann dazu führen, dass Lebensmittel gespalten werden oder sich nicht gut anfühlen.
Das Endergebnis? Die falsche Wahl verschwendet Geld und mindert die Qualität. Ein Baustoffhersteller wechselte von einer dickeren zu einer dünneren HPMC-Sorte. Dadurch konnte er 12% Material einsparen und gleichzeitig die Wasseraufnahmefähigkeit beibehalten. Dies zeigt, wie die richtige Wahl Geld spart und die Qualität erhält.
2. Welche unterschiedlichen Viskositätsklassen von HPMC sind erhältlich?
HPMC ist in vielen Dickengraden für unterschiedliche Anwendungen erhältlich. Die Hersteller gruppieren diese Grade nach der Dicke einer 2%-Wassermischung bei 20 °C.
Die HPMC-Dicke wird in mPa·s oder cP gemessen, wobei 1 mPa·s 1 cP entspricht. Die meisten Verkäufer verwenden Namen, die sowohl den chemischen Typ als auch die Dicke angeben.
Gruppe „Dicke“ | Bereich (mPa·s) | Häufige Verwendung |
---|---|---|
Sehr niedrig | 3-10 | Tablettenüberzüge, Sprays |
Niedrig | 10-100 | Zementzusätze, Farbverdicker |
Medium | 100-4,000 | Fliesenkleber, Pillenbinder |
Hoch | 4,000-15,000 | Tabletten mit verzögerter Wirkstofffreisetzung, Wandbeschichtungen |
Sehr hoch | 15,000-100,000+ | Spezielle Baumischungen, Tabletten mit verlängerter Wirkstofffreisetzung |
HPMC mit geringer Dichte (10–100 mPa·s) lässt sich gut mit Wasser mischen. Es eignet sich für Anwendungen, bei denen nur eine leichte Verdickung erforderlich ist. Diese Typen schmelzen schnell und fließen gut. Sie werden verwendet in:
- Zementmischungen zur Wasserspeicherung
- Pillenbindung, wenn nur eine geringe Gelstärke erforderlich ist
- Farbe als Helfer
- Papier- und Stoffherstellung
Das sollten Sie wissen Dünnere Sorten kosten oft weniger pro Pfund als dickere Sorten. Um den gleichen Effekt zu erzielen, müssen Sie jedoch möglicherweise mehr verwenden. Dies kann den Preisvorteil ausgleichen.
HPMC mittlerer Dicke (100–4.000 mPa·s) bietet ein ausgewogenes Verhältnis von Verdickungskraft und Klarheit. Diese praktischen Qualitäten eignen sich für:
- Fliesenkleber und selbstnivellierende Böden
- Pillenherstellung
- Lebensmittelverdickungsmittel
- Shampoos und Lotionen
HPMC mit hoher Dichte (4.000–15.000 mPa·s) bildet starke Gele und hält Wasser gut. Sie eignen sich hervorragend für:
- Außenwandsysteme
- Pillen mit langsamer Freisetzung
- Produkte, die eine starke Bindung erfordern
- Hoher Wasserspeicherbedarf
Sehr hohe Dicken (15.000–100.000+ mPa·s) ermöglichen maximale Verdickung mit geringen Mengen. Diese Top-Qualitäten eignen sich für:
- Spezielle Baumischungen mit extremer Wasserhaltefähigkeit
- Sehr langsam wirkende Pillen
- Anwendungen, bei denen Sie sehr wenig verwenden müssen
Notenbeispiel | Dicke (mPa·s) | Typische Verwendungen |
---|---|---|
HPMC E5 | 5 | Pillenbeschichtung, Zementwechsel |
HPMC E15 | 15 | Baumischungen, Bindemittel |
HPMC K100M | 100,000 | Retardtabletten, Spezialmörser |
HPMC F4M | 4,000 | Kontrollierte Freisetzung, Wandbeschichtungen |
HPMC E4M | 4,000 | Basisches Verdickungsmittel |
Beachten Sie bei der Auswahl der Sorten, dass Sorten mit höherer Dicke:
- Benötigen Sie weniger für die gleiche Wasserspeicherung
- Machen Sie stärkere Gele
- Langsamer schmelzen
- Kostet mehr
- Kann die Verarbeitbarkeit verändern
3. Welchen Einfluss hat die HPMC-Viskosität auf Bauanwendungen?
Bei Baumischungen beeinflusst die HPMC-Dicke die Wasserhaltefähigkeit, die Verarbeitbarkeit, die Standfestigkeit und die offene Zeit. Diese Eigenschaften bestimmen, wie einfach die Mischungen verarbeitet werden können und wie gut sie nach dem Aushärten funktionieren.
Die Wasserbindung ist vielleicht die wichtigste Aufgabe von HPMC in Baumischungen. Wenn sich Zement mit Wasser vermischt, beginnen sofort chemische Veränderungen. Ohne gute Wasserbindung können diese Veränderungen zu schnell erfolgen. Dies ist bei heißem oder windigem Wetter noch schlimmer.
Was Sie wissen müssen ist HPMC-Typen mit höherer Dicke halten Wasser oft besser. Dieser Zusammenhang ist jedoch nicht immer eindeutig. Ein Test vieler HPMC-Typen in Zementmörteln ergab, dass ein Typ mit 15.000 mPa·s bei 0,31 TP3T eine ähnliche Wasserhaltefähigkeit wie ein Typ mit 100.000 mPa·s bei 0,21 TP3T aufweist.
HPMC-Dickenklasse | Typische Menge in Mörtel | Wasserhaltung | Offene Zeit | Auswirkungen auf die Verarbeitbarkeit |
---|---|---|---|---|
5-15 mPa·s | 0.5-0.8% | Niedrig | Kurz | Wenig Verdickung |
100-400 mPa·s | 0.3-0.5% | Medium | Medium | Gleichmäßige Merkmale |
4.000–15.000 mPa·s | 0.2-0.4% | Hoch | Lang | Große Verdickung |
30.000–100.000 mPa·s | 0.1-0.3% | Sehr hoch | Extra lang | Kann den Blutfluss unterbrechen |
Verarbeitbarkeit und Offenzeit hängen mit der Wasseraufnahme zusammen. Die Offenzeit gibt an, wie lange die Mischung nach Gebrauch verarbeitbar bleibt. Bei Fliesenklebern gibt eine längere Offenzeit den Handwerkern mehr Zeit, Fliesenstellen zu reparieren.
Ein Hersteller von Fliesenkleber testete verschiedene HPMC-Dickengrade und fand:
- Geringe Dicke (50 mPa·s): 10 Minuten offene Zeit, schlechte Standfestigkeit
- Mittlere Dicke (4.000 mPa·s): 20 Minuten offene Zeit, gute Standfestigkeit
- Hohe Schichtdicke (15.000 mPa·s): 30 Minuten offene Zeit, hervorragende Standfestigkeit
Die Verhinderung von Absacken ist besonders wichtig bei Wandanwendungen wie Fliesenverlegung oder Beschichtungen. HPMC-Typen mit höherer Dicke helfen dabei, Absacken zu verhindern. Sie bilden stärkere Gele, die Mischungen trotz der Schwerkraft an Ort und Stelle halten.
Verwenden | Beste HPMC-Dicke | Wichtige Bedürfnisse |
---|---|---|
Fliesenkleber | 4.000–15.000 mPa·s | Lange offene Zeit, Standfestigkeit |
Selbstnivellierende Böden | 100–4.000 mPa·s | Fließeigenschaften, mittlere Wasseraufnahme |
Wandbeschichtungen | 15.000–50.000 mPa·s | Hoher Wasserstand, starke Senkungsbekämpfung |
Jointmischungen | 15.000–30.000 mPa·s | Verarbeitbarkeit, Rissbekämpfung |
Zementbasierte Farben | 400–4.000 mPa·s | Spritzerbekämpfung, Anhaften |
Häufige Fehler bei der Dickenbestimmung für Baumischungen sind:
- Zu hohe Schichtdicke für selbstnivellierende Böden, wodurch der Fluss unterbrochen wird
- Die Wahl einer zu geringen Dicke für Wandanwendungen führt zu einem Durchhängen
- Beim Mischen nicht an das lokale Wetter denken
- Fehlt, wie HPMC mit anderen Adds funktioniert
4. Welche Rolle spielt die HPMC-Viskosität in pharmazeutischen Formulierungen?
Bei Tabletten beeinflusst die HPMC-Dicke die Freisetzungsrate, die Herstellungsschritte und die Stabilität der Tablettenarten. Die richtige Dicke kann den Unterschied zwischen einer wirksamen und einer wirkungslosen Tablette ausmachen.
Die Freisetzungsrate von Medikamenten hängt stark von der Dicke des in Tabletten verwendeten HPMC ab. Wenn eine Tablette mit HPMC mit Magenflüssigkeiten in Berührung kommt, bildet sich eine Gelschicht. Dieses Gel kontrolliert den Medikamentenfluss.
Was diesen Schlüssel ausmacht, ist Höhere Schichtdicken ergeben dickere Gelschichten. Diese verlangsamen die Wirkstofffreisetzung. Niedrigere Schichtdicken ermöglichen eine schnellere Freisetzung. Dieser Zusammenhang macht die Wahl der HPMC-Schichtdicke zu einem wichtigen Werkzeug für die Herstellung von Tabletten mit verzögerter Wirkstofffreisetzung.
HPMC-Dickenklasse | Gelschichtherstellung | Arzneimittelfreisetzungsrate | Typische Veröffentlichungszeit |
---|---|---|---|
5-50 mPa·s | Dünn, schnell formbar | Schnell | 1-4 Stunden |
100–4.000 mPa·s | Mittlere Dicke | Medium | 4-8 Stunden |
4.000–15.000 mPa·s | Dick, stark | Langsam | 8-12 Stunden |
15.000–100.000+ mPa·s | Sehr dick, sehr stark | Sehr langsam | 12-24+ Stunden |
Für schnell freisetzende Tabletten wählen Hersteller oft dünnere Stärken (3–15 mPa·s). Diese wirken hauptsächlich als Bindemittel und nicht als Verlangsamer. Sie helfen, die Tablette zusammenzuhalten. Sie verlangsamen das Schmelzen des Wirkstoffs kaum.
Retardtabletten verwenden mittlere bis sehr hohe Dickengrade. Eine gängige Methode ist die Mischung verschiedener Dickengrade. Dadurch werden feste Freisetzungsraten erreicht:
- Erste Berstfreigabe: Teil mit geringer Dicke (50–100 mPa·s)
- Mittlere Freisetzungsphase: Teil mittlerer Dicke (4.000 mPa·s)
- Lange Freisetzungsphase: Hohe Schichtdicke (15.000–100.000 mPa·s)
Die Herstellungsschritte werden auch durch die HPMC-Dicke beeinflusst. Während der Pillenherstellung:
- Dünnere Sorten fließen besser in Trichtern und Matrizenlöchern
- Bei dicken Sorten kann eine höhere Presskraft erforderlich sein.
- Für sehr dicke Qualitäten sind möglicherweise spezielle Fertigungswerkzeuge erforderlich
Pillentyp | Beste HPMC-Dicke | Gedanken machen |
---|---|---|
Schnell freisetzende Pillen | 3-15 mPa·s | Guter Verlauf, geringe Presskraft |
Pillen mit verzögerter Freisetzung | 4.000–100.000 mPa·s | Möglicherweise ist eine höhere Presskraft erforderlich |
Kapselmischungen | 3-100 mPa·s | Muss in Kapselhüllen fließen |
Pillenbeschichtung | 3-15 mPa·s | Sprühbarkeit, Filmbildung |
Augentropfen | 4.000–15.000 mPa·s | Saubere Filterung erforderlich |
5. Wie sollten Sie die HPMC-Viskosität für Ihre Anwendung testen und messen?
Eine gründliche Dickenprüfung ist der Schlüssel zur Auswahl der richtigen HPMC-Sorte. Sie trägt auch dazu bei, sicherzustellen, dass Ihr Produkt jedes Mal gleich gut funktioniert. Es gibt viele Testmethoden. Jede hat ihre eigenen Vorteile und Grenzen.
Die gängigste Prüfmethode verwendet ein Drehwerkzeug, um die Dicke einer 2% HPMC-Mischung bei 20 °C zu messen. Mit dieser einfachen Methode können Sie verschiedene Sorten und Hersteller vergleichen.
Das sollten Sie wissen Hitze beeinflusst HPMC-Dickentests erheblich. Ein Temperaturanstieg von 5 °C kann die gemessene Dicke um 10-15% reduzieren. Dieser Wärmeeffekt macht festgelegte Testzustände für gute Ergebnisse entscheidend.
Testweg | Werkzeug | Gute Punkte | Grenzen | Am besten für |
---|---|---|---|---|
Drehtest | Brookfield-Werkzeug | Branchenüblich, kann erneuert werden | Einzelschergeschwindigkeitstest | Qualitätsprüfungen, Notenabgleich |
Röhrchentest | Ubbelohde-Werkzeug | Leicht zu verarbeiten, gut für geringe Dicke | Nur für geringe Dickenbereiche | Studie, geringe Dickengrade |
Durchflusstest | Rheometer | Tests über Schergeschwindigkeiten hinweg, ergibt Fließkurven | Schwer zu betreiben, teuer | F&E, eingehende Studien |
Fallender Ball | Fallendes Ballwerkzeug | Einfach, kann sich bewegen | Begrenzte Wahrheit | Feldtests |
Cup Ways | Ford/Zahn-Pokal | Schnell, handlich | Nur für geringe Dickenbereiche | Bodenkontrollen durchführen |
Gehen Sie beim Testen der HPMC-Dicke folgendermaßen vor:
- Stellen Sie eine 2%-Mischung her, indem Sie HPMC in heißes Wasser (80–90 °C) geben.
- Die Mischung unter leichtem Rühren auf 20 °C abkühlen lassen
- Lassen Sie die Mischung 12 Stunden stehen, damit sie das Wasser vollständig aufnehmen kann.
- Behalten Sie die eingestellte Wärmeregelung während des Tests bei
- Verwenden Sie den richtigen Spinner und die richtige Drehgeschwindigkeit für Ihr Werkzeug
- Nehmen Sie Messungen vor, nachdem der Test abgeschlossen ist (oft 30–60 Sekunden).
6. Welche Faktoren sollten Ihren HPMC-Viskositätsauswahlprozess leiten?
Die Auswahl der besten HPMC-Dickenklasse erfolgt schrittweise. Achten Sie dabei nicht nur auf die Dicke. Bei der Auswahl sollten Sie Nutzungsanforderungen, Fertigungsfähigkeiten, finanzielle Überlegungen und Standortfaktoren berücksichtigen.
Beginnen Sie mit einer umfassenden Analyse der spezifischen Anforderungen Ihres Anwenders. Unterschiedliche Anwendungen erfordern unterschiedliche HPMC-Eigenschaften:
Der entscheidende Punkt hierbei ist Die Wahl der Dicke sollte sich nach den Bedürfnissen der Anwender richten, nicht nach Gewohnheit. Viele Hersteller verwenden jahrelang dieselbe Qualität. Sie prüfen nicht, ob sie wirklich die beste für ihre aktuellen Mischungen ist.
Nutzungsart | Hauptarbeitsbedürfnisse | Andere Gedanken | Leitfaden zum Dickenbereich |
---|---|---|---|
Zementbasierte Mörtel | Wasserhaltevermögen, Verarbeitbarkeit | Offene Zeit, Durchhangbekämpfung | 15.000–50.000 mPa·s |
Fliesenkleber | Offene Zeit, Durchhangbekämpfung | Fixieren, Benetzen | 4.000–15.000 mPa·s |
Selbstnivellierende Mischungen | Fließeigenschaften, gute Wasserhaltung | Abbindezeit, Oberflächenfinish | 100–4.000 mPa·s |
Pillen mit verzögerter Freisetzung | Legen Sie die Wirkstofffreisetzungsrate fest | Leichtigkeit schaffen | 4.000–100.000 mPa·s |
Schnell freisetzende Pillen | Bindekraft, Aufbrechen | Fließeigenschaften, Pressen | 3-15 mPa·s |
Lebensmittelverdickungsmittel | Gefühl, Stabilität | Mundgefühl, Klarheit | 4.000–15.000 mPa·s |
Die Passgenauigkeit des Werkzeugs ist ein weiterer wichtiger Faktor. Ihre Fertigungseinrichtung kann die Auswahl der Dicke einschränken:
- Hochschermischer können höhere Dicken verarbeiten
- Bei Sprühanwendungen ist eine geringere Schichtdicke für ein gutes Sprühergebnis erforderlich
- Werkzeuge zum Pressen von Pillen können bei sehr hohen Dickengraden Probleme verursachen
- Pumpsysteme haben maximale Dickengrenzen
Finanzielle Überlegungen sollten die Rohstoffkosten mit den Betriebsgewinnen abwägen. Höhere Dickengrade:
- Kosten höher pro Kilo
- Benötigen Sie geringere Beträge für die gleiche Arbeit
- Kann den Bedarf an anderen Adds verringern
- Kann die Funktionsfähigkeit und den Wert des Endprodukts verbessern
Abschluss
Die Wahl der richtigen HPMC-Dicke erfordert eine Abwägung zwischen technischen Anforderungen, Fertigungskompetenz und Kostenfaktoren. In diesem Leitfaden haben wir gezeigt, wie sich die Dicke auf die Wasseraufnahme in Baumischungen, die Wirkstofffreisetzung in Tabletten und die Stabilität in vielen Anwendungen auswirkt. Wenn Sie diese Zusammenhänge kennen, können Sie intelligente Entscheidungen treffen, die sowohl die Leistung als auch die Kosten verbessern. Unternehmen, die die richtige HPMC-Dicke wählen, senken die Mischkosten oft um 10-20%. Sie verbessern außerdem die Produktqualität. Für fachkundige Unterstützung bei der Auswahl der perfekten HPMC-Sorte für Ihren Anwendungszweck wenden Sie sich noch heute an das technische Team von Morton. Unsere Experten analysieren Ihre Anforderungen und finden die beste Dicke. So sparen Sie Tausende an Mischkosten und verbessern gleichzeitig die Leistung Ihres Produkts.
Häufig gestellte Fragen
F1: Können HPMC unterschiedlicher Viskositätsklassen gemischt werden, um Zwischeneigenschaften zu erzielen?
Ja, Sie können verschiedene HPMC-Dicken mischen, um individuelle Eigenschaften zu erzielen. Dies eignet sich gut zur Optimierung der Wirkstofffreisetzung in Tabletten oder zur Änderung der Wasserbindung in Baumischungen. Für optimale Ergebnisse mischen Sie Sorten mit ähnlichen chemischen Mustern, aber unterschiedlichen Dicken. Die endgültige Dicke ist kein einfacher Mittelwert, sondern folgt einem logarithmischen Zusammenhang. Testen Sie das gemischte System stets gründlich. Manchmal können sich Sorten auf unerwartete Weise vermischen.
F2: Wie wirkt sich die Temperatur auf das Viskositätsverhalten von HPMC-Lösungen aus?
HPMC-Mischungen weisen wärmebedingte Besonderheiten auf. Bei niedrigeren Temperaturen nimmt die Dicke mit steigender Temperatur leicht ab. Dies entspricht dem normalen Polymerverhalten. Erreicht die Mischung jedoch ihren Gelpunkt (oft 65–80 °C, je nach Sorte), steigt die Dicke sprunghaft an. Dies geschieht, da das Polymer ein Gelnetz bildet. Diese Eigenschaft macht HPMC für Anwendungen geeignet, die eine Verdickung durch Wärmebehandlung erfordern. Halten Sie die Temperatur während der Herstellung unter dem Gelpunkt. Dies gewährleistet die Verarbeitbarkeit.
F3: Was sind die Hauptunterschiede zwischen HPMC und anderen Celluloseethern hinsichtlich der Viskositätsleistung?
HPMC unterscheidet sich in vielerlei Hinsicht von anderen Celluloseethern wie MC, CMC und HEC. Neben MC schmilzt HPMC besser in kalten Wasser-Öl-Mischungen. Im Gegensatz zu CMC ist HPMC nichtionisch. Dadurch wird es durch Salz- und pH-Wert-Veränderungen weniger stark verändert. HEC besitzt nicht die Eigenschaften von HPMC zur Wärmegelierung. HPMC bietet bei gleicher Dichte oft eine bessere Wasseraufnahme als HEC. CMC führt bei gleicher Dichte oft zu zäheren Mischungen als HPMC.
F4: Wie wirken sich die Lagerbedingungen auf die Viskositätsstabilität von HPMC-Produkten aus?
Die Lagerbedingungen beeinflussen die Stabilität von HPMC stark. Hohe Feuchtigkeit (> 70 % relative Luftfeuchtigkeit) kann zu einer Wasseraufnahme des Teils führen. Dies führt zu Klumpenbildung und verlangsamtem Schmelzen. Temperaturen über 40 °C können das Polymer langsam zersetzen. Dies verringert mit der Zeit die Dicke. UV-Licht kann das Zelluloserückgrat zerstören. Dies verringert ebenfalls die Dicke. Für optimale Stabilität lagern Sie HPMC in verschlossenen Behältern an einem kühlen, trockenen Ort ohne direkte Sonneneinstrahlung. Gut gelagertes HPMC behält seine angegebene Dicke 3–5 Jahre lang.
F5: Was sind die häufigsten Probleme bei der Fehlerbehebung im Zusammenhang mit der falschen Auswahl der HPMC-Viskosität?
Häufige Probleme bei falsch gewählter Schichtdicke sind: (1) Schlechte Wasseraufnahme im Mörtel, was zu schnellem Trocknen und schwachen Bindungen führt – oft durch zu geringe Schichtdicke; (2) Zu starke Verdickung erschwert das Mischen oder die Anwendung der Produkte – oft durch zu hohe Schichtdicke; (3) Ungleichmäßige Wirkstofffreisetzung in Tabletten – oft durch chargenweise Änderung der Schichtdicke; (4) Absetzen oder Spalten in flüssigen Mischungen – oft durch zu geringe Schichtdicke; und (5) Lange Schmelzzeiten während der Herstellung – oft durch zu hohe Schichtdicke ohne Änderung der Herstellungsschritte. Die meisten Probleme lassen sich durch Änderung der Schichtdicke oder Menge beheben.