The question of how different HPMC grades can improve your applications is pivotal in many industrial sectors, particularly in construction, pharmaceuticals, and food. Hydroxypropyl Methylcellulose (HPMC) serves vital functions across these industries, often acting as a thickening agent, emulsifier, or binder. Understanding these various grades and their specific applications allows businesses to optimize their products significantly. This article will explore how HPMC grades, particularly E5 and E15, impact formulation choices and efficiencies, enabling B2B decision-makers to make informed choices essential for successful project outcomes.
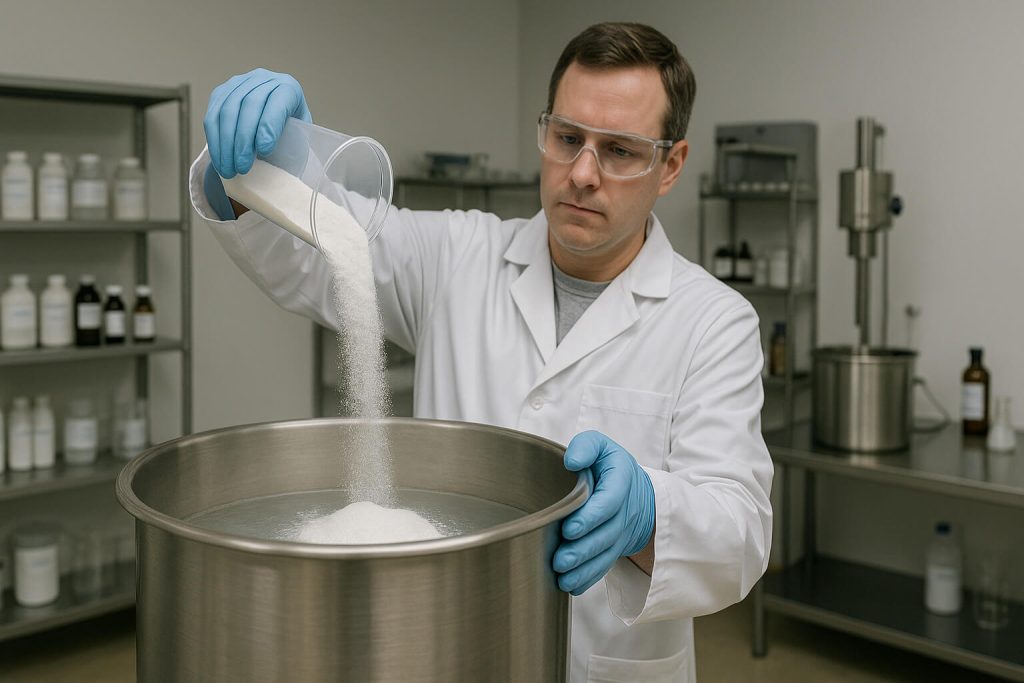
WHAT ARE HPMC GRADES AND WHY DO THEY MATTER?
HPMC grades are classified based on their viscosity and solubility characteristics, which can greatly affect their functionality across different applications. But here’s the kicker: not all HPMC grades are created equal, and understanding these differences is crucial for anyone looking to optimize their product formulations. HPMC’s versatility makes it a popular choice in numerous applications, ranging from construction materials to pharmaceuticals.
Understanding HPMC grades helps in several ways. For instance, HPMC grades can enhance the flow properties, adhesion, and overall stability of various formulations. Choosing the right grade can lead to increased efficiency during production, ultimately improving product quality. E5, known for its lower viscosity, allows for quick hydration and is often utilized in quick-drying products, whereas E15, with its higher viscosity, supports formulations demanding stability and controlled release.
Data shows that the proper use of HPMC not only leads to improved product performance but also optimizes resource consumption during production. This can lead to significant cost savings over time. Therefore, knowing how to select the right HPMC grade is essential to avoid costly mistakes that can arise from a lack of understanding.
HPMC-Qualität | Viskosität | Häufige Anwendungen | Primary Benefits |
---|---|---|---|
E5 | Niedrig | Gypsum plasters, adhesives | Quick hydration, cost-effective |
E15 | Hoch | Pharmazeutika, Lebensmittel | Improved stability and controlled release |
WHAT ARE THE KEY HPMC GRADES IN USE TODAY?
In today’s market, two primary HPMC grades dominate the landscape: E5 and E15. What’s the real story? Each grade serves distinct functions based on varying viscosity levels and solubility properties. E5, with its lower viscosity, thrives in applications requiring rapid hydration and easy dispersion. It is a go-to choice for contractors seeking efficient mixability in settings like tile adhesives and gypsum-based plasters.
On the other hand, E15 excels in scenarios where greater viscosity is essential. It boasts enhanced gel strength, making it highly suitable for pharmaceuticals where controlled release is necessary. Its superior water retention capabilities allow it to stabilize emulsions more effectively during production, ensuring longevity and reliability in end products.
In addition, while E5 and E15 are the most common, other grades exist—each with unique performance characteristics—such as E10, which balances between the two. This variety enables businesses to select an HPMC grade that best fits their specific operational needs. Industry experts caution against underestimating these differences, as selecting the wrong grade can lead to formulation issues and inefficiencies.
HPMC-Qualität | Eigenschaften | Suitable Industries | Beste Verwendung |
---|---|---|---|
E5 | Niedrige Viskosität | Bau, Lebensmittel | Adhesives, mortars |
E10 | Mäßige Viskosität | Pharmazeutika, Kosmetik | Creams, lotions |
E15 | Hohe Viskosität | Lebensmittel, Pharmazeutika | Systeme mit kontrollierter Freisetzung |
HOW DO YOU CHOOSE THE RIGHT HPMC GRADE FOR YOUR NEEDS?
Choosing the right HPMC grade isn’t merely about picking a product off a shelf; careful consideration is essential. Ready for the good part? By evaluating specific application requirements, businesses can streamline operations and enhance product functions. The first step is to conduct a thorough analysis of the intended use—whether in pharmaceuticals, construction, or food production. Here, understanding viscosity needs and hydration speeds becomes paramount.
It’s also vital to consider the environmental conditions under which the product will be used. For instance, if the final product must withstand high moisture, E15 may be better suited due to its robust properties. Case studies reveal that manufacturers have achieved significant performance improvements merely by switching from E5 to E15 for moisture-sensitive applications.
Additionally, businesses often benefit from pilot testing different HPMC grades in small batches. This allows companies to observe performance characteristics firsthand before committing to large-scale production. There’s no one-size-fits-all solution. Therefore, organizations should tailor their choice of HPMC to their unique needs, weighing performance against cost to find the best balance.
Decision Criteria | Überlegungen | Steps to Take |
---|---|---|
Application type | Wall systems, coatings, pharmaceuticals | Identify specific project needs |
Performance requirements | Adhesion, gel strength | Test HPMC grades in small batches |
Environmental conditions | Temperature, humidity issues | Evaluate suitability and stability |
WHAT ARE THE UNIQUE PROPERTIES OF E5 HPMC?
Diving into E5, it’s essential to understand its key characteristics. E5 is primarily known for its low viscosity, which promotes rapid hydration. But here’s where it gets interesting: this feature helps manufacturers produce products that set quickly and maintain a workable consistency. This trait has made E5 a favorite for construction applications like tile adhesives and gypsum-based materials.
However, while E5 has numerous advantages, it also has limitations. Its lower gel strength means that in applications requiring extended stability and durability, E5 may not perform as efficiently. For example, in pharmaceutical applications where controlled release is essential, E5 might not retain the active ingredients effectively. Its viscosity can hinder its ability to maintain the structural integrity of a final product, leading to formulation problems over time.
The versatility of E5 extends to its applicability in personal care items as well. Many companies are finding innovative ways to incorporate E5 into their lotions and creams because it aids in creating a smooth application without leaving a greasy residue. However, businesses should conduct specific studies to ensure that the inclusion of E5 aligns with their overall product development goals.
E5 Properties | Vorteile | Einschränkungen |
---|---|---|
Niedrige Viskosität | Quick hydration for efficient mixing | Lower gel strength for long-term use |
Wide application range | Cost-effective in many formulations | May not suit all stability needs |
Easy to blend | Creates smooth textures in personal care | Compatibility issues in some mixtures |
WHAT ARE THE UNIQUE PROPERTIES OF E15 HPMC?
Now, let’s transition to examining E15 HPMC. What are its standout features? E15 is characterized by higher viscosity, making it exceedingly beneficial in applications where gel strength and stability are crucial. This higher viscosity can significantly enhance the mechanical properties of final products, making it the preferred choice in pharmaceutical formulations where controlled release and extended efficacy are paramount.
The exceptional ability of E15 to retain moisture and form stable emulsions means it performs exceptionally well in food production. Products designed for prolonged shelf life often incorporate E15 to ensure they maintain their quality and consistency over time. This property extends to adhesives and sealants used in construction, where strength and durability over time are critical.
However, like E5, E15 is not without its challenges. Its higher viscosity might lead to more cumbersome mixing processes, which can slow down production speeds. Additionally, due to its cost, companies must weigh the benefits against their budgets, particularly for large-scale manufacturing applications. Making the right choice means understanding how these properties align with production goals and efficiency.
E15 Properties | Anwendungen | Stärken |
---|---|---|
Hohe Viskosität | Pharmaceuticals, adhesives, food | Excellent gel strength and stability |
Feuchtigkeitsspeicherung | Construction and personal care | Long-lasting performance |
Kompatibilität | Works well with various formulations | Reduces separation in mixtures |
HOW DO ENVIRONMENTAL CONDITIONS AFFECT HPMC PERFORMANCE?
Understanding the role of environmental conditions on HPMC performance is crucial for manufacturers. So, what’s the bottom line? HPMC grades react differently to varying temperatures and humidity levels, impacting their effectiveness in applications. For example, E5’s rapid hydration properties can become a disadvantage in extremely dry conditions, leading to product inconsistencies. This can result in poor adhesion in construction materials or instability in pharmaceutical formulations.
Conversely, E15 performs remarkably well in challenging environments. Its structure allows it to maintain gel strength and stability even when exposed to moisture or varying temperatures. This attribute is vital for items used outdoors, such as construction materials that must withstand harsh weather conditions. The ability of E15 to ensure consistent performance across different environments makes it an attractive choice for businesses focused on producing high-quality, resilient products.
To optimize HPMC performance, manufacturers should consider storage recommendations. Keeping products in cool, dry places and maintaining appropriate packaging can mitigate many of the environmental issues associated with HPMC. Furthermore, consistent testing under simulated conditions can help businesses understand how their formulations will behave in real-world scenarios, which is critical for long-term success.
Umweltfaktor | Impact on E5 | Impact on E15 |
---|---|---|
Temperatur | Quick hydration can be hindered | Maintains gel strength even under stress |
Luftfeuchtigkeit | Less effective in high humidity | Excellent retention of properties |
Storage | Needs careful monitoring | Requires no special adjustments |
WHAT INNOVATIONS ARE EMERGING IN HPMC TECHNOLOGY?
As various industries evolve, so too does the field of HPMC production. What’s the buzz? Current innovations focus on enhancing both the functionality and sustainability of HPMC grades. Companies are investing in advanced production technologies that enhance purity levels, which could lead to materials that perform better and are more environmentally friendly.
One notable area of innovation is the development of bio-based HPMC. Researchers are exploring the use of renewable resources to produce HPMC, decreasing dependence on synthetic materials and reducing the overall environmental footprint. These developments not only bolster product performance but also align with increasing regulatory demands for sustainability.
Moreover, formulation techniques are benefiting from advancements as well. Improved blending methods and the introduction of additives that can synergize with HPMC are redefining how products are created across industries. Companies can now formulate with more confidence that their HPMC choices will deliver desired results, especially for products requiring extended shelf. This commitment to innovation presents opportunities for companies to stay ahead of competitors by adopting cutting-edge practices.
Innovation Aspect | Current Trends | Future Implications |
---|---|---|
Production | Enhanced purity processes in HPMC manufacturing | Improved performance and sustainability |
Formulation technology | Development of bio-based HPMC using renewable resources | Reduced reliance on synthetic materials |
New applications | Use of HPMC in novel products and sectors | Greater versatility for future formulations |
HOW CAN HPMC GRADES CONTRIBUTE TO PRODUCT SUSTAINABILITY?
In today’s conscientious market, sustainability is no longer a bonus; it’s a necessity. So how can HPMC grades play a role? As an intrinsic part of many formulations, HPMC can help reduce environmental impact. Both E5 and E15 present unique opportunities for companies focused on sustainability missions. E5 allows manufacturers to achieve high performance while minimizing costs, enabling companies to invest in more sustainable practices across their operations.
A notable sustainability benefit of HPMC is its biodegradability. Many industrial sectors are seeking alternatives that align with eco-friendly practices, and HPMC serves as an excellent choice in this regard. Products made with E5 or E15 can contribute to a reduced carbon footprint during the lifecycle of the product, satisfying growing consumer demand for sustainable options.
Moreover, careful sourcing and production methods can further enhance the sustainability of HPMC applications. By using renewable resources and refining manufacturing processes, companies can demonstrate their commitment to reducing waste. This alignment between sustainable practices and HPMC usage is becoming increasingly central to company messaging, especially in consumer-facing industries.
Sustainability Aspect | HPMC Benefits | Company Implications |
---|---|---|
Biologische Abbaubarkeit | Less environmental impact | Appeals to eco-conscious consumers |
Resource efficiency | Optimization of material usage | Improved operational practices |
Supply chain transparency | Cleaner production methods | Builds brand trust |
WHAT DO INDUSTRY EXPERTS SAY ABOUT HPMC GRADE SELECTION?
Industry experts stress the importance of an informed approach when selecting HPMC grades. What’s the insight? Understanding the distinctive properties of E5 and E15 is crucial for making educated decisions that perfectly align with project needs. Manufacturers must assess technical specifications, desired product characteristics, and the end-use environment to choose the most appropriate grade.
Feedback from industry leaders indicates that companies where R&D teams are actively involved in decision-making tend to achieve better outcomes. This collaborative approach fosters innovation and enables informed choices that can prevent costly oversights during production.
Case studies reveal that companies that prioritize understanding HPMC grades often experience fewer issues during formulation. Additionally, maintaining communication with suppliers can provide invaluable insights into new developments and trends in HPMC technology, enhancing decision-making. Adopting a forward-thinking yet grounded approach to HPMC grade selection can lead businesses to sustainable growth and product mastery.
Expert Insight | Key Recommendations | Potential Risks |
---|---|---|
Understand grade properties | Deep dive into viscosity and solubility | Risk of misalignment in formulations |
Involve R&D in decision-making | Foster a culture of innovation | Missed opportunities for improvement |
Seek supplier collaboration | Regular dialogue for updated knowledge | Disconnect from industry trends |
HOW CAN YOU ENSURE QUALITY CONTROL WHEN USING HPMC?
Ensuring quality control when utilizing HPMC is non-negotiable for success. So, how can businesses guarantee consistent quality? Establishing rigorous quality assurance protocols is essential. Conclusively, industries must implement testing procedures for every lot of HPMC to ensure it meets specifications and continues to provide the performance expected.
Moreover, regular analysis of product performance can reveal how different HPMC grades react under various conditions. Companies should conduct stability tests under multiple environmental influences to gauge potential vulnerabilities effectively. In doing so, businesses can optimize formulations and eliminate issues before they arise.
Training staff in quality control processes adds another layer of assurance. Having team members knowledgeable about HPMC properties will enhance monitoring and enable quick corrective actions when needed. Quality should never be compromised, and incorporating these procedures will ultimately lead to more robust products and more satisfied customers.
Quality Control Aspect | Bewährte Methoden | Ergebnis |
---|---|---|
Consistent testing process | Test each lot for HPMC specifications | Assures reliability in performance |
Comprehensive staff training | Educate on HPMC properties and usage | Improved detection of quality issues |
Routine audits | Regular reviews of production processes | Enhanced product consistency |
CONCLUSION
In conclusion, understanding how different HPMC grades can improve your applications is essential for decision-makers in various industries. The attributes of E5 and E15 provide unique advantages that, when properly recognized and applied, lead to enhanced efficiency, performance, and sustainability. From the careful selection of grades that suit specific applications to the importance of quality control and sustainability, businesses can make strategic choices that yield significant benefits. Embracing innovations and expert insights can further facilitate growth and success in an increasingly competitive landscape.
Häufig gestellte Fragen
Frage 1: Was ist HPMC?
HPMC, or Hydroxypropyl Methylcellulose, is a cellulose-based polymer primarily used as a thickening agent, binder, and emulsifier across various industries.
Frage 2: How does HPMC improve product formulations?
HPMC enhances product formulations by improving viscosity, stability, and performance characteristics, contributing to overall effectiveness in end products.
Frage 3: What are the differences between E5 and E15 HPMC?
E5 has lower viscosity, suitable for quick-setting applications, while E15 offers higher viscosity, making it ideal for products needing greater stability and controlled release.
Frage 4: How should HPMC be stored to maintain its properties?
HPMC should be stored in a cool, dry place away from direct sunlight and humidity to prevent degradation and to ensure optimal performance in applications.
F5: What are current trends in HPMC production?
Current trends focus on developing more sustainable manufacturing processes and innovations that enhance performance characteristics, ensuring HPMC fits into a greener economy.