Hydroxypropyl Methylcellulose (HPMC) is a versatile ingredient used across various industries, including pharmaceuticals, food, and construction. Different grades of HPMC, such as K4M and K100M, offer unique characteristics suited for specific applications. Understanding these grades and their properties can help you choose the best fit for your needs. This article provides an in-depth breakdown of HPMC grades, highlighting their differences and the most suitable applications for each.
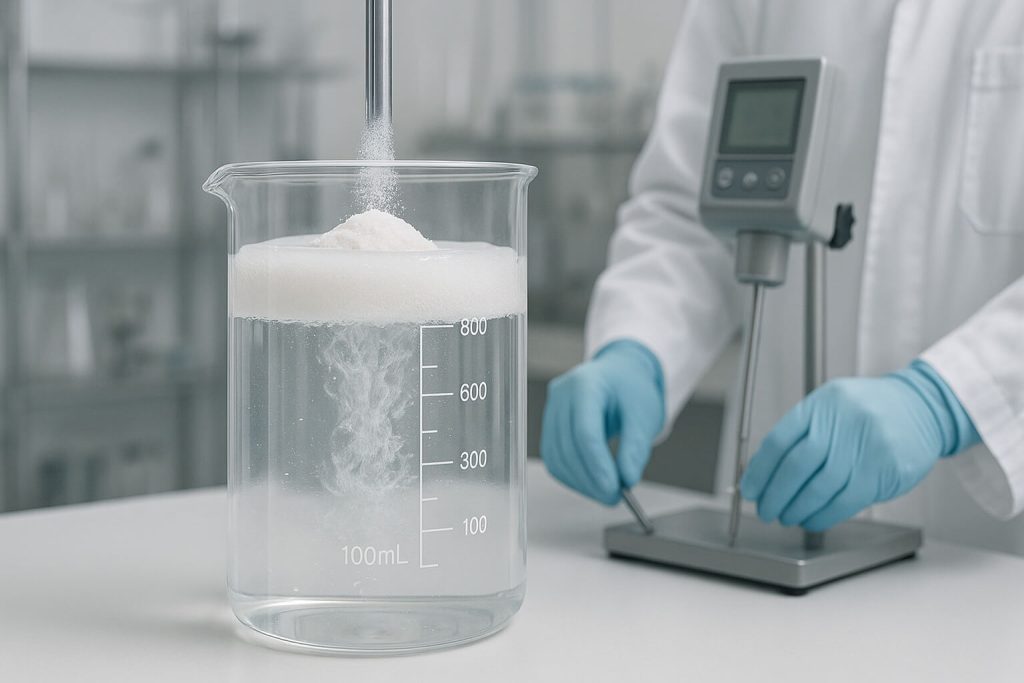
1. What is HPMC and Why Is It Important for Industrial Applications?
HPMC (Hydroxypropyl Methylcellulose) is a cellulose derivative modified with hydroxypropyl and methyl groups, making it water-soluble and highly functional across different industries. But here’s the kicker… its ability to control viscosity, enhance texture, and stabilize formulations makes it a go-to material in many applications. Whether you’re in pharmaceuticals, food, or construction, understanding how HPMC works and its benefits is crucial.
In pharmaceuticals, HPMC serves multiple roles such as a binder, emulsifier, and stabilizer in tablet formulations. It is particularly valuable in controlled-release drug formulations, where it helps regulate the rate at which drugs are released into the body. In food, HPMC is used as a thickening agent, emulsifier, and stabilizer, improving texture and consistency in products like sauces, dairy alternatives, and dressings. For construction, HPMC helps enhance the workability and adhesion of cement-based materials like mortars and adhesives.
HPMC’s importance in these industries cannot be overstated. It provides excellent water retention, film-forming capabilities, and stability, which is why it is found in so many consumer products.
Application | Role of HPMC | Benefit |
---|---|---|
Pharmaceuticals | Binder, emulsifier, stabilizer | Controls drug release, improves stability |
Food | Thickener, emulsifier, stabilizer | Enhances texture, prevents separation |
Construction | Water retention, workability | Improves adhesion, enhances consistency |
2. What Are the Different Grades of HPMC and How Do They Differ?
HPMC comes in various grades, each tailored for specific applications based on its molecular weight, viscosity, and solubility. Ready for the good part? The grades of HPMC can be broadly divided into low, medium, and high viscosity categories, with each category having distinct applications.
Low-viscosity grades, such as HPMC K4M, are ideal for fast-release formulations, emulsions, and suspensions. They are often used in the food and pharmaceutical industries for products that require quick dissolution or dispersion. Medium-viscosity grades, like K15M, offer a balance between rapid release and sustained performance, making them suitable for controlled-release tablets and capsules.
High-viscosity grades, such as HPMC K100M, are used in formulations that require slower release or sustained therapeutic effects. They are especially useful in controlled-release systems, where a high viscosity gel matrix is necessary to regulate the release of the active ingredient over time.
Understanding these grades and their properties is key to choosing the right one for your specific formulation needs. Whether you need a quick-release or sustained-release formulation, HPMC offers a variety of grades to meet your requirements.
Grade | Viscosity Level | Common Applications | Ideal Use |
---|---|---|---|
HPMC K4M | Low viscosity | Fast-release formulations, emulsions | Quick dissolution, rapid drug release |
HPMC K15M | Medium viscosity | Controlled-release tablets, capsules | Balanced performance, moderate release |
HPMC K100M | High viscosity | Sustained-release formulations, coatings | Slow drug release, extended therapeutic effect |
3. How Does Viscosity Influence the Choice of HPMC Grade?
Viscosity plays a crucial role in determining the behavior of HPMC in pharmaceutical, food, and construction applications. What’s the real story? The viscosity of HPMC directly influences the release rate of active ingredients in pharmaceutical formulations, the texture of food products, and the workability of construction materials.
Low viscosity grades like HPMC K4M are ideal for fast-release formulations. In pharmaceutical tablets, they help the active ingredients dissolve quickly, providing a rapid therapeutic effect. Similarly, in food formulations, low-viscosity HPMC is used to ensure smooth textures in products like sauces and dressings, where fast dissolution and consistent texture are essential.
High-viscosity grades like HPMC K100M, on the other hand, are used in controlled-release drug formulations, where the slow release of the active ingredient over time is needed. These grades form a thicker gel matrix that dissolves more slowly, allowing for sustained drug release, which is beneficial for long-acting medications.
In construction, high-viscosity HPMC grades are used to improve the workability of mortars and adhesives, ensuring that the materials remain workable for longer periods and providing better adhesion.
Application | Role of Viscosity | Benefit |
---|---|---|
Pharmaceuticals | Fast-release or controlled-release | Quick or sustained drug release |
Food | Smooth texture, stability | Prevents separation, improves consistency |
Construction | Workability and adhesion | Easier application, better bonding |
4. Why Should You Choose Low Viscosity HPMC for Your Formulations?
Low viscosity HPMC grades like K4M are essential for formulations that require quick dissolution and rapid therapeutic effects. Ready for the good part? Low viscosity allows HPMC to dissolve quickly in water, making it ideal for fast-release pharmaceuticals and liquid suspensions. It also helps create smooth, uniform textures in food and cosmetic products.
In the pharmaceutical industry, low viscosity HPMC is often used in formulations like effervescent tablets, where quick dissolution is necessary. It is also used in oral suspensions, ensuring the active ingredient is evenly distributed in the solution. In food, low-viscosity HPMC is used in sauces, dressings, and plant-based products, where it helps to maintain smooth texture and prevent separation.
Additionally, low viscosity HPMC is often preferred in emulsions and cosmetic formulations. It improves the consistency and feel of products like lotions and creams without making them overly thick or greasy. The ability to provide smooth textures without adding unnecessary thickness makes it a popular choice for many formulations.
Application | Benefits of Low Viscosity HPMC | Ideal Formulations |
---|---|---|
Pharmaceuticals | Fast dissolution, smooth texture | Effervescent tablets, suspensions |
Food | Prevents separation, smooth texture | Sauces, dressings, plant-based foods |
Cosmetics | Improves consistency, prevents greasiness | Lotions, creams, emulsions |
5. Why Opt for High Viscosity HPMC for Controlled-Release Products?
High viscosity HPMC grades like K100M are often the go-to choice for controlled-release formulations. This is where it gets interesting… the thick gel matrix formed by high-viscosity HPMC slows the dissolution rate of the active ingredient, allowing for sustained drug release. This property is particularly valuable in sustained-release pharmaceuticals, where a steady release of the active ingredient over time is necessary to maintain therapeutic levels in the body.
In pharmaceutical formulations, high-viscosity HPMC helps ensure that the drug is released gradually, minimizing peaks and troughs in drug levels, which can improve efficacy and reduce side effects. These formulations are especially useful for medications that need to be taken less frequently or for chronic conditions where long-term drug delivery is required.
High viscosity HPMC is also used in coatings for tablets and capsules, where it helps improve the mechanical strength and stability of the formulation. The gel-like consistency helps prevent breakage during handling and provides a controlled release of the drug, enhancing patient compliance.
Application | Benefits of High Viscosity HPMC | Ideal Formulations |
---|---|---|
Pharmaceuticals | Slow, sustained drug release | Controlled-release tablets, capsules |
Coatings | Increased tablet strength | Tablets requiring prolonged release |
Long-acting drugs | Improved bioavailability | Chronic condition medications |
6. How Does HPMC in Pharmaceutical Formulations Enhance Drug Release?
In pharmaceutical formulations, HPMC is primarily used to control the release rate of active ingredients. But here’s the kicker… HPMC’s ability to form a gel matrix around the active pharmaceutical ingredient (API) allows for controlled drug release, improving both the bioavailability and therapeutic efficacy of the drug.
HPMC works by swelling in water and forming a gel, which encapsulates the drug and releases it slowly over time. This process is particularly useful for drugs that require prolonged action or those that need to be delivered at specific intervals throughout the day. By adjusting the grade of HPMC, manufacturers can control how quickly or slowly the drug is released, providing a tailored approach to drug delivery.
In controlled-release tablets, for example, HPMC K100M forms a thick gel that dissolves slowly, ensuring that the drug is released over several hours. In contrast, lower-viscosity grades like K4M are used in fast-release formulations, where a rapid onset of action is required.
Application | Role of HPMC | Benefit |
---|---|---|
Controlled-release tablets | Forms gel matrix for sustained release | Prolonged drug action, improved bioavailability |
Fast-release tablets | Quick dissolution, no gel formation | Immediate drug release, quick therapeutic effect |
7. What Are the Applications of HPMC in the Food Industry?
HPMC’s versatility extends to the food industry, where it is used as a stabilizer, emulsifier, and thickening agent. Ready for the good part? Its ability to modify the texture and stability of food products makes it ideal for use in a wide range of applications, from dairy to plant-based foods.
In the dairy industry, HPMC is commonly used to stabilize emulsions in milk, yogurt, and cheese. It helps prevent separation, improving the texture and consistency of the product. For plant-based foods, HPMC mimics the mouthfeel of dairy products, making it a key ingredient in plant-based alternatives such as non-dairy milk and ice cream.
In sauces, dressings, and soups, HPMC is used to provide smooth, stable textures without affecting flavor or color. Its ability to thicken liquids and prevent separation helps maintain product quality during storage and transport.
Application | Role of HPMC | Benefit |
---|---|---|
Dairy products | Stabilizer, emulsifier | Prevents separation, improves texture |
Plant-based foods | Texture enhancer | Mimics dairy texture, improves mouthfeel |
Sauces and dressings | Thickening agent, emulsifier | Enhances texture, prevents separation |
8. How Does HPMC Benefit the Construction Industry?
In the construction industry, HPMC is commonly used in mortars, adhesives, and plasters. What’s the real story? The addition of HPMC improves the workability, water retention, and adhesion of these materials, making them easier to apply and more durable.
HPMC helps keep the mortar or plaster moist for longer periods, preventing premature drying and ensuring proper curing. This is especially important in hot or dry conditions, where materials can dry out too quickly. HPMC also enhances the consistency and smoothness of the mixture, making it easier to apply and finish surfaces.
In adhesives, HPMC helps improve bond strength, ensuring that the materials adhere securely over time. Its role in construction applications highlights its versatility and effectiveness in a variety of industrial settings.
Application | Role of HPMC | Benefit |
---|---|---|
Mortars and plasters | Water retention, workability | Better consistency, prevents premature drying |
Tile adhesives | Improves adhesion and spreadability | Stronger bond, better workability |
Cement-based products | Enhances smoothness and texture | Easier application, improved finish |
9. How to Choose the Right HPMC Grade for Your Specific Needs?
Choosing the right HPMC grade depends on several factors, including viscosity, solubility, and the specific application requirements. Ready for the good part? Understanding these factors is key to selecting the grade that will deliver the best performance for your formulation.
For fast-release formulations, low-viscosity grades like HPMC K4M are typically preferred. These grades dissolve quickly in water, ensuring a rapid onset of action. For sustained-release products, high-viscosity grades like HPMC K100M are the best choice, as they form a gel matrix that dissolves slowly and controls drug release over an extended period.
When selecting an HPMC grade, it’s important to consider the product’s intended use, the required viscosity, and the desired release profile. Testing small batches with different grades can help identify the most effective option for your formulation.
Consideration | Low Viscosity HPMC | High Viscosity HPMC |
---|---|---|
Ideal Applications | Fast-release, emulsions | Controlled-release, sustained-action |
Key Benefit | Quick dissolution, smooth texture | Slow drug release, improved bioavailability |
10. What Are the Future Trends for HPMC Usage and Innovation?
As industries continue to evolve, so does the use of HPMC. But here’s the kicker… innovations in HPMC technology are making it even more adaptable and sustainable. In the pharmaceutical industry, for example, researchers are exploring new methods to modify HPMC for improved drug release profiles and enhanced patient compliance.
The demand for eco-friendly and biodegradable products is also growing, and HPMC, being derived from renewable resources, is positioned to meet this need. Advances in HPMC-based formulations are expected to make products more efficient, cost-effective, and environmentally friendly.
Trend | Potential Impact | Future Applications |
---|---|---|
Customization | Tailored formulations for specific needs | Pharmaceuticals, food, cosmetics |
Sustainability | Biodegradable products | Eco-friendly formulations, green technologies |
FAQ Section
Q1: What is HPMC and why is it important in industrial applications?
HPMC (Hydroxypropyl Methylcellulose) is a cellulose derivative used as a binder, emulsifier, stabilizer, and thickening agent in pharmaceuticals, food, and construction.
Q2: How does viscosity influence the choice of HPMC grade?
Viscosity affects the dissolution rate and release profile. High-viscosity grades are used for controlled-release formulations, while low-viscosity grades are used for fast-release applications.
Q3: Why should you choose low viscosity HPMC for your formulations?
Low viscosity HPMC is ideal for quick dissolution and smooth textures, making it suitable for fast-release pharmaceutical tablets and emulsions.
Q4: What are the benefits of high viscosity HPMC in controlled-release products?
High viscosity HPMC provides slower dissolution, making it ideal for sustained-release formulations that require a prolonged therapeutic effect.
Q5: How do I choose the right HPMC grade for my specific needs?
Choose the right grade based on factors like viscosity, solubility, and application type. Low-viscosity grades are ideal for fast-release formulations, while high-viscosity grades work best for controlled-release products.