When considering the quality of Hydroxypropyl Methylcellulose (HPMC) for your business, evaluating the right attributes is crucial. HPMC is a versatile compound used in a wide range of industries, from construction and pharmaceuticals to food production. The quality of HPMC directly impacts the effectiveness, performance, and consistency of the products it’s used in. This article will provide you with a comprehensive guide on how to evaluate the quality of HPMC, ensuring you make informed purchasing decisions for your business.
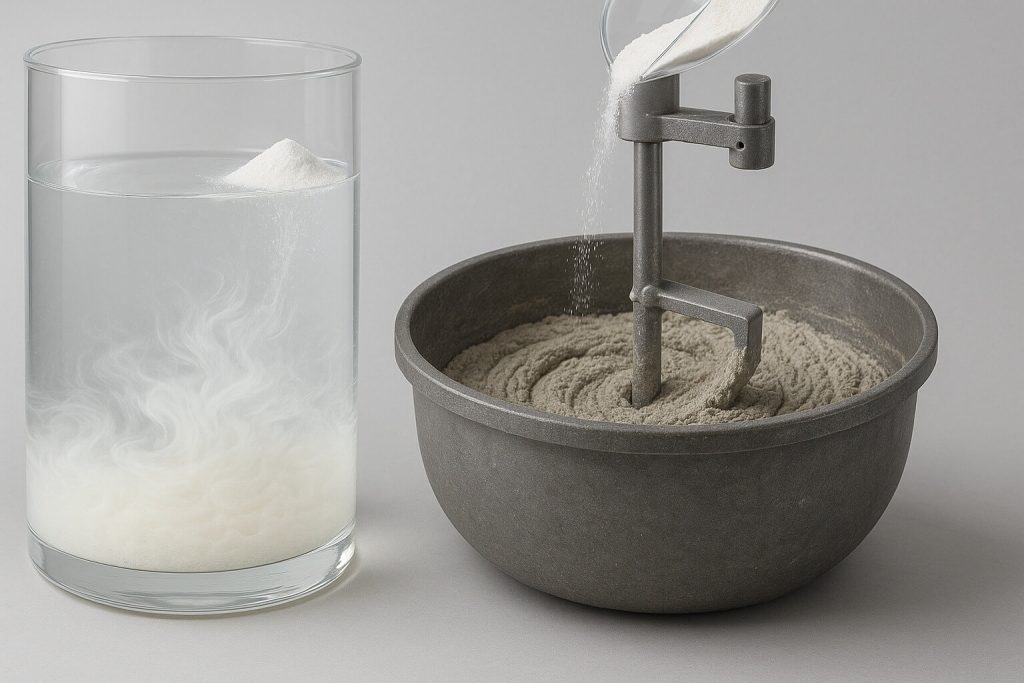
1. What is HPMC and Why is It Important for Industrial Applications?
HPMC, or Hydroxypropyl Methylcellulose, is a cellulose derivative that has widespread use in various industrial applications. So what’s the real story here? HPMC is a non-ionic, water-soluble polymer that functions as a thickener, binder, emulsifier, and stabilizer. Its unique properties make it an essential ingredient in products across many industries, from construction materials to pharmaceuticals and food production.
In construction, HPMC is widely used in mortar, tile adhesives, and plaster, where it helps improve workability and extend open time. This allows builders to work with the material for longer periods before it begins to set. In the pharmaceutical industry, HPMC is used as a binder in tablet formulations, ensuring that the active ingredients are evenly distributed. For the food industry, it is used to stabilize emulsions, improve texture, and extend shelf life.
What’s the real value of HPMC for your business? In construction, it ensures that materials maintain their consistency and workability, making it easier for construction companies to apply adhesives and mortars. In pharmaceuticals, it guarantees that products are uniform and reliable. And in food production, it ensures that products have the desired texture and stability. Evaluating the quality of HPMC is vital because it impacts the final product’s effectiveness in these industries.
Industry | Application | Benefits of HPMC |
---|---|---|
Construction | Mortar, adhesives | Improved workability, extended open time |
Pharmaceuticals | Tablets, capsules | Uniformity, consistency |
Food | Sauces, dressings, ice cream | Texture, stability, shelf life |
2. What Factors Determine the Quality of HPMC?
When evaluating HPMC, several key factors must be considered to ensure its quality. But here’s where it gets interesting – the quality of HPMC is determined not only by its chemical composition but also by its manufacturing process, molecular weight, and purity. These factors directly influence the properties of the HPMC, such as its viscosity, solubility, and stability.
The first factor to consider is the purity of the HPMC. High-quality HPMC should have minimal impurities to ensure that it doesn’t affect the final product’s performance. Impurities can cause inconsistent behavior, affecting the effectiveness of HPMC in the applications it’s used in. The manufacturing process is another critical element. HPMC should be produced using a reliable and standardized process to ensure consistency across batches.
Then there’s molecular weight – the higher the molecular weight of the HPMC, the thicker and more stable the solution will be. This is especially important for applications like controlled-release pharmaceuticals, where a higher molecular weight ensures a steady release of active ingredients over time. Finally, viscosity and solubility are critical parameters that determine how HPMC will perform in different formulations. A good-quality HPMC should dissolve quickly in water and provide the desired viscosity for the application.
Factor | Impact on HPMC Quality | Importance |
---|---|---|
Purity | Minimal impurities | Ensures consistent performance |
Manufacturing Process | Standardized production | Consistency between batches |
Molecular Weight | Determines viscosity and stability | Affects product effectiveness |
3. How Can You Assess the Viscosity of HPMC?
Viscosity is one of the most important factors in determining the quality of HPMC. But here’s the kicker – viscosity directly influences the functionality of HPMC in its final application. For example, in construction materials, high viscosity ensures that the material can be applied smoothly and won’t run off the surface. In pharmaceutical formulations, the viscosity affects how the drug is released in the body, influencing its therapeutic effectiveness.
There are several methods to assess the viscosity of HPMC. The most common method is using a Brookfield viscometer, which measures the flow resistance of a solution. This tool is widely used in the pharmaceutical and food industries to ensure the viscosity of HPMC meets the desired specifications. Another method involves using a rotational viscometer, which provides a more detailed measurement of the shear rate, making it ideal for applications where the viscosity needs to be finely tuned.
What’s the real value of viscosity testing? It ensures that the HPMC you’re using in your formulations has the right thickness for the intended application. Whether you’re producing a mortar or a tablet, ensuring the right viscosity guarantees that your product will perform as expected, with the right consistency and stability.
Viscosity Test | Measurement Method | Applications |
---|---|---|
Brookfield Viscometer | Measures flow resistance | Pharmaceuticals, food |
Rotational Viscometer | Measures shear rate | Cosmetics, construction materials |
Rheometer | Measures viscosity under various conditions | R&D, specialized formulations |
4. What Role Does Solubility Play in Evaluating HPMC Quality?
Solubility is another critical factor in evaluating the quality of HPMC. Ready for the good part? The solubility of HPMC affects how it behaves in formulations. In industries like pharmaceuticals and food production, it’s essential that HPMC dissolves quickly and completely in water to provide the desired texture and stability in the final product.
Testing solubility is crucial for ensuring the performance of HPMC in different applications. In pharmaceuticals, HPMC’s solubility determines how quickly the active ingredients in tablets or capsules are released. In construction, the solubility of HPMC can impact how easily the product can be mixed with water to form a smooth, workable paste. For food products, solubility influences texture and mouthfeel, which are important factors in consumer satisfaction.
What’s the takeaway here? If HPMC does not dissolve properly, it can lead to issues such as inconsistent texture, poor adhesion, or uneven release of active ingredients. To evaluate HPMC’s solubility, manufacturers typically conduct tests where the solubility rate is measured under specific conditions, ensuring it meets the standards for the intended application.
Solubility Test | Testing Method | Impact on Application |
---|---|---|
Solubility in Water | Measure time for complete dissolution | Pharmaceuticals, food, cosmetics |
pH Solubility Test | Test solubility under different pH levels | Construction, adhesives |
Temperature Test | Measure solubility at various temperatures | R&D, specialized formulations |
5. How Can Impurities Impact the Quality of HPMC?
Impurities in HPMC can have a significant impact on its quality and performance. But here’s the kicker – even small amounts of impurities can lead to issues in product consistency and stability. Impurities can alter the viscosity, solubility, and even the overall functionality of HPMC in different applications, which is why ensuring high purity is critical when evaluating its quality.
Common impurities in HPMC include residual solvents, salts, and other byproducts from the manufacturing process. These impurities can negatively affect the product’s performance, leading to inconsistencies in texture, stability, and efficacy. In pharmaceutical applications, impurities can compromise the safety and effectiveness of medications. In food, they can lead to changes in taste, texture, or shelf life. To assess the purity of HPMC, manufacturers use several techniques, including high-performance liquid chromatography (HPLC) and other analytical methods that help identify and quantify impurities.
What’s the real value of impurity testing? By ensuring that HPMC is free from harmful impurities, you’re not only safeguarding product quality but also protecting your brand’s reputation. High-quality HPMC with minimal impurities guarantees that your products will perform reliably and consistently.
Impurity Type | Potential Impact | Testing Method |
---|---|---|
Residual Solvents | Can affect solubility and viscosity | HPLC, chromatography |
Salts | Can alter consistency | ICP-MS, spectroscopy |
Byproducts | Can compromise performance | HPLC, NMR |
6. How Does the Particle Size of HPMC Affect Its Quality?
The particle size of HPMC plays a crucial role in determining its performance in various applications. What’s the real story here? Smaller particles generally result in faster dissolution rates, which is beneficial for certain applications like pharmaceuticals, where quick release of active ingredients is required. On the other hand, larger particles can provide better control over the texture and stability of products, making them ideal for applications like construction, where longer open time and better workability are important.
To evaluate the particle size of HPMC, manufacturers use techniques like laser diffraction and microscopy to measure the size and distribution of particles in the HPMC powder. Particle size analysis helps ensure that HPMC meets the specific needs of the application, whether it’s providing a smooth, fast-dissolving solution or a thicker, more stable product.
The key takeaway? The particle size directly influences how HPMC will perform in its intended application. Ensuring the correct particle size is essential for achieving the desired texture, consistency, and release properties.
Particle Size Range | Effect on Performance | Applications |
---|---|---|
< 50 microns | Fast dissolution, smooth texture | Pharmaceuticals, food |
50 – 200 microns | Improved stability, longer open time | Construction, adhesives |
> 200 microns | Enhanced texture, slow release | Food, specialized formulations |
7. What is the Role of HPMC’s Molecular Weight in Quality Evaluation?
The molecular weight of HPMC is another critical factor in evaluating its quality. But here’s the kicker – molecular weight plays a significant role in determining the viscosity, solubility, and performance of HPMC in various applications. A higher molecular weight results in a thicker solution, making it ideal for products that require stability and controlled release, such as pharmaceutical tablets.
The molecular weight of HPMC also impacts its ability to form films, which is crucial in applications like controlled-release coatings for tablets. Low molecular weight HPMC, on the other hand, is preferred in applications that require faster dissolution or a more fluid consistency, such as in certain food products or adhesives.
Molecular weight analysis is typically done using gel permeation chromatography (GPC), a technique that allows manufacturers to determine the exact molecular weight distribution of HPMC. By understanding the molecular weight, manufacturers can ensure that the HPMC meets the specifications required for specific applications.
Molecular Weight | Impact on Application | Ideal Uses |
---|---|---|
Low Molecular Weight | Faster dissolution, fluid consistency | Food, adhesives |
High Molecular Weight | Thicker solutions, controlled release | Pharmaceuticals, controlled coatings |
8. How Do HPMC Suppliers Ensure Consistent Quality?
To ensure consistent quality, HPMC suppliers employ strict quality control measures throughout the manufacturing process. Ready for the good part? Quality assurance starts from raw material sourcing and continues through every stage of production. Reputable suppliers adhere to international standards and certifications, such as ISO 9001 and Good Manufacturing Practice (GMP), to ensure the highest quality product.
In addition to certifications, suppliers perform rigorous testing at each stage of production, including checks for purity, viscosity, solubility, and molecular weight. Regular audits and inspections are conducted to ensure that the final product meets the necessary specifications. This consistency is critical for industries that rely on the stable performance of HPMC in their products.
The key takeaway here is that working with a reliable, certified supplier is essential for ensuring that the HPMC you receive will meet your quality standards and perform consistently across applications.
Quality Control Process | Purpose | Key Parameters Tested |
---|---|---|
Raw Material Sourcing | Ensure purity and consistency | Impurities, moisture content |
Manufacturing Process | Maintain consistency between batches | Viscosity, molecular weight |
Final Product Testing | Verify compliance with standards | Purity, solubility, particle size |
9. How Can You Perform a Practical Quality Test for HPMC?
Performing practical quality tests for HPMC ensures that it meets the necessary standards for its intended application. So what’s the real story here? It’s about using the right tools and techniques to evaluate key attributes like viscosity, solubility, and molecular weight.
A simple test involves preparing a solution of HPMC in water and measuring its viscosity using a Brookfield viscometer. This test provides an indication of how the HPMC will behave in its final application, whether it’s used in a mortar, tablet, or food product. Solubility tests can also be performed by dissolving HPMC in different solvents and observing the time it takes for it to fully dissolve. This gives an idea of how it will perform in real-world applications. Finally, particle size and molecular weight can be determined using laser diffraction and gel permeation chromatography, respectively.
Why is this important? Quality testing ensures that the HPMC will perform as expected, meeting both functional and safety standards for the end product. By conducting these tests, you can ensure that the HPMC you use will contribute to the success of your product.
Test Type | Method | Purpose |
---|---|---|
Viscosity Test | Brookfield Viscometer | Measure thickness and consistency |
Solubility Test | Dissolution in various solvents | Test for dissolution speed |
Particle Size Test | Laser Diffraction | Measure particle distribution |
10. What Are the Common Mistakes When Evaluating HPMC Quality?
When evaluating HPMC quality, several common mistakes can lead to poor decision-making. But here’s the kicker – overlooking key quality parameters can result in choosing an unsuitable product that doesn’t meet the needs of your application. One common mistake is failing to check for impurities in the HPMC, which can affect performance. Another mistake is misjudging the required viscosity for specific applications, leading to inconsistent products.
It’s also essential to evaluate solubility and molecular weight, as these parameters directly influence the application’s success. For example, using low molecular weight HPMC in a controlled-release pharmaceutical formulation may result in the active ingredients being released too quickly. Failing to test particle size can also lead to issues with consistency and product texture.
The real value of quality evaluation? By avoiding these mistakes, you ensure that you select the right HPMC for your needs, contributing to the overall success of your product.
Mistake | Impact | How to Avoid |
---|---|---|
Overlooking Impurities | Affects performance and safety | Regular impurity testing |
Misjudging Viscosity | Inconsistent application | Conduct viscosity tests |
Ignoring Molecular Weight | Inconsistent product performance | Measure molecular weight for specific uses |
Conclusion
In conclusion, evaluating the quality of HPMC is critical for ensuring that your products perform consistently and effectively. By focusing on factors like purity, viscosity, solubility, molecular weight, and particle size, you can make more informed decisions when selecting HPMC for your industrial applications. Regular testing and working with reliable suppliers who adhere to strict quality standards are essential steps in ensuring that the HPMC you use meets the required specifications. By understanding these key quality indicators and avoiding common mistakes, you’ll be able to optimize the performance of your products and ensure their long-term success.
FAQ Section
Q1: What is HPMC?
A1: HPMC, or Hydroxypropyl Methylcellulose, is a cellulose derivative used in various industries like construction, pharmaceuticals, and food. It functions as a binder, thickener, and stabilizer in formulations.
Q2: How do you measure the viscosity of HPMC?
A2: Viscosity of HPMC is commonly measured using viscometers like Brookfield or rotational viscometers. These tools help determine the flow resistance of HPMC solutions, ensuring they meet application standards.
Q3: Why is solubility important in HPMC quality evaluation?
A3: Solubility affects how easily HPMC dissolves in water or other solvents. This property is critical for its performance in applications such as pharmaceuticals and food, where consistent dissolution is necessary.
Q4: How can impurities affect HPMC quality?
A4: Impurities in HPMC can alter its performance, leading to inconsistencies or contamination. High-quality HPMC should have minimal impurities to ensure product safety and effectiveness, especially in pharmaceuticals and food products.
Q5: What tests can be used to evaluate the quality of HPMC?
A5: Common tests include viscosity measurement, solubility testing, particle size analysis, and molecular weight determination. These tests help assess the suitability of HPMC for specific applications in different industries.