Introduction
In the world of advanced polymers, Hydroxypropyl Methylcellulose K4M (HPMC K4M) represents a paradigm of innovation and reliability. It transcends its roles as a binder or thickener, serving as a versatile excipient that propels advancements in industries such as pharmaceuticals, construction, and more. The distinctive qualities of HPMC K4M—precise viscosity control, robust gelation properties, and seamless integration of synthetic and natural polymer characteristics—make it an indispensable solution.
For formulators and industry leaders, the importance of selecting the right polymer cannot be overstated. It influences not only product performance but also cost efficiency and regulatory adherence. A comprehensive understanding of HPMC K4M’s unique properties is essential, positioning this polymer as a gold standard for stability, consistency, and adaptability in a range of applications.
What exactly makes HPMC K4M a standout in practical applications? Let’s explore further.
What is HPMC K4M?
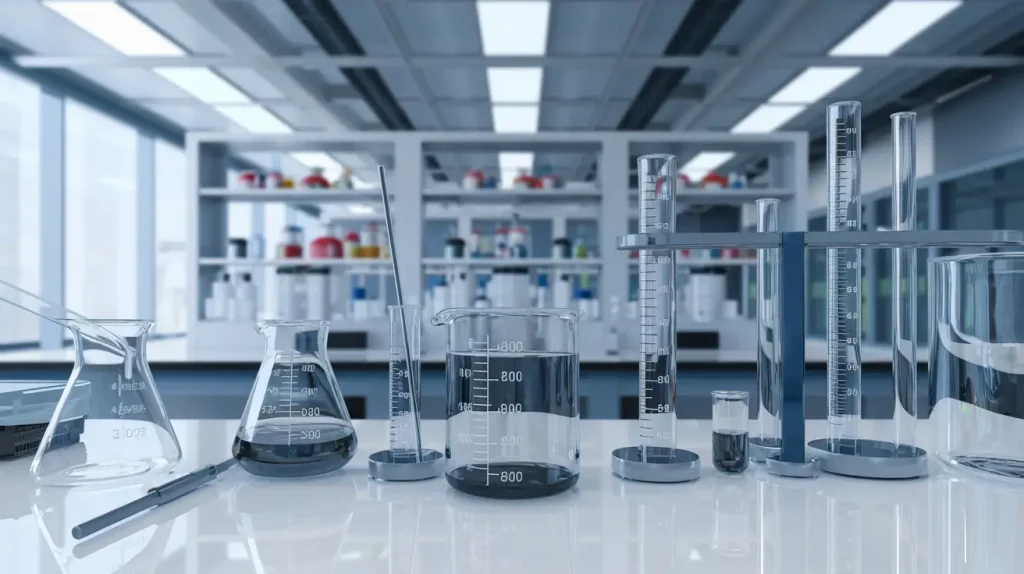
Key Features and Composition
Hydroxypropyl Methylcellulose K4M is a highly engineered polymer designed for versatility and functionality. Its foundation lies in cellulose, chemically modified with methoxyl and hydroxypropyl groups to achieve an optimal balance of hydrophilic and hydrophobic properties. This unique composition gives HPMC K4M its non-ionic character, enabling it to maintain stability across a broad pH range. Additionally, its remarkable thermal stability facilitates precise gelation at defined temperatures, a critical attribute for controlled-release technologies and temperature-sensitive applications.
Why are these features so significant? They unlock the potential for HPMC K4M to excel in demanding, real-world applications.
Common Applications
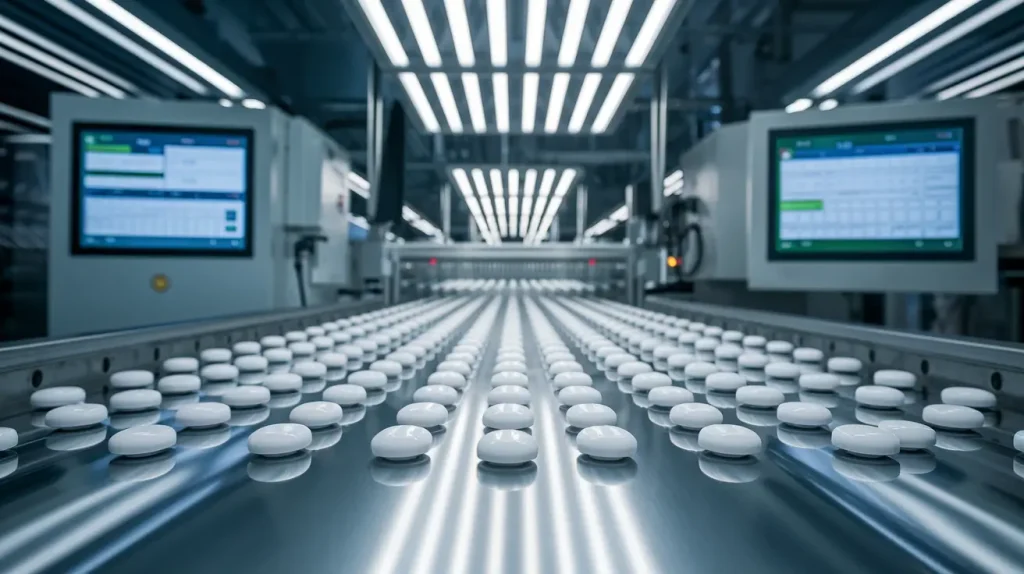
HPMC K4M is more than just a polymer—it is a tailored solution to modern industrial challenges. In pharmaceuticals, it plays a pivotal role in controlled-release tablets, ensuring precise and sustained delivery of active ingredients. Its superior film-forming capabilities make it essential for tablet coatings, enhancing durability, stability, and bioavailability. Beyond pharmaceuticals, HPMC K4M is a key thickening and stabilizing agent in the food industry, improving the texture and consistency of products like sauces and dressings. In construction, it serves as a water retention agent in cement and mortar, promoting smoother application and stronger adhesion.
Across diverse industries, HPMC K4M demonstrates its indispensability by consistently bridging innovation with functionality. What drives this exceptional performance? Let’s explore its mechanisms in detail.
HPMC K4M Properties in Detail
Viscosity and Gel Formation
HPMC K4M stands out for its precise and consistent viscosity, a critical attribute that underpins its versatility across numerous applications. Available in a wide range of viscosity grades, it accommodates diverse needs—from creating smooth, uniform tablet coatings to forming highly stable gel matrices. Its capacity to absorb water and develop robust gel networks enhances water retention and ensures uniform dispersion, a cornerstone for high-performance formulations in both pharmaceuticals and construction.
How does this flexibility translate into practical efficiency? Let’s explore further.
Substitution Levels and Customization
A defining feature of HPMC K4M is its customizable substitution levels. By varying the content of methoxyl and hydroxypropyl groups, manufacturers can fine-tune the polymer’s performance to meet specific application requirements. For example, higher methoxyl content improves film-forming properties, while increased hydroxypropyl levels enhance water solubility. This ability to adapt its composition allows K4M to excel in diverse scenarios, delivering tailored viscosity, thermal behavior, and dissolution rates. Such customization ensures that HPMC K4M remains a preferred solution for industries demanding precision and flexibility.
But how does it maintain consistent performance across such variations? Let’s find out.
Thermal Gelation and Stability
HPMC K4M is a leader in thermal gelation, forming stable gels at elevated temperatures—a feature crucial for controlled-release drug formulations and heat-sensitive processes. Unlike similar polymers, K4M maintains enhanced stability across a wider temperature spectrum, providing reliable performance even under challenging conditions. Whether in pharmaceuticals or industrial applications, this thermal stability ensures that K4M meets the highest standards of reliability and efficiency.
Now, let’s examine how these properties enable groundbreaking advancements across industries.
Benefits of HPMC K4M in Pharmaceutical Applications
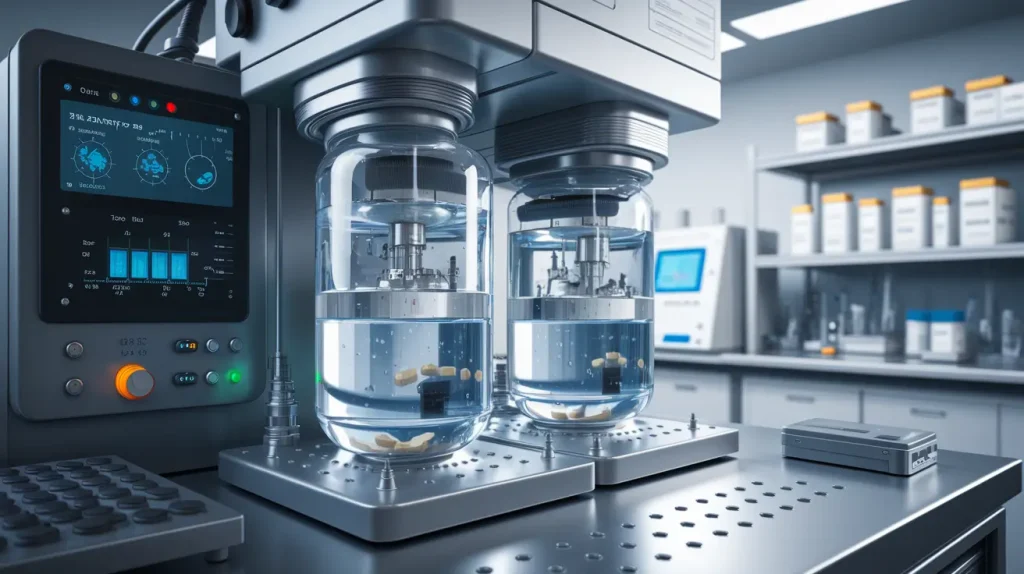
Controlled Drug Release
HPMC K4M plays a pivotal role in sustained-release formulations, offering an innovative solution for precise drug delivery. Its gel-forming mechanism creates a stable matrix that regulates the release of active pharmaceutical ingredients (APIs) over time. This controlled release enhances therapeutic outcomes and reduces the need for frequent dosing, benefiting both patients and manufacturers. From chronic condition therapies to formulations designed to improve bioavailability, K4M stands out as an essential tool for optimizing drug release profiles and ensuring consistent performance.
What gives K4M an edge over alternative excipients? Let’s investigate its other key roles.
Binder and Thickener Capabilities
In addition to enabling controlled drug release, HPMC K4M serves as a reliable binder and thickener. It strengthens tablets by ensuring structural integrity and uniformity, even under challenging conditions. Unlike carbomer, which may exhibit pH sensitivity, or guar gum, which often lacks consistency, K4M provides unmatched reliability across a variety of formulations. Its dual functionality simplifies manufacturing processes while delivering exceptional performance, making it a trusted choice for pharmaceutical applications demanding both efficiency and durability.
However, K4M’s advantages don’t stop there. Let’s delve into its superior film-forming capabilities.
Film-Forming Properties
The film-forming properties of HPMC K4M offer significant benefits for pharmaceutical coatings. It forms a smooth, protective layer that shields tablets from moisture, oxygen, and physical damage, while effectively masking unpleasant tastes. Unlike synthetic alternatives, K4M is non-toxic and biodegradable, making it a safe and eco-friendly option. Whether used for enteric coatings or visually appealing finishes, K4M delivers precision and durability, all while enhancing patient compliance and sustainability.
How does K4M consistently achieve this balance of versatility and dependability? Its applications across industries reveal the answer. Stay tuned to learn more.
Alternatives to HPMC K4M
Synthetic Polymers
Synthetic polymers, such as carbomers, are often considered alternatives to HPMC K4M due to their strong gelling and thickening properties. However, carbomers come with inherent drawbacks, including sensitivity to pH changes and the requirement for neutralization to achieve optimal functionality. While these polymers may offer cost advantages for specific uses, their limited versatility and potential for reduced stability over time make them less suitable for demanding pharmaceutical applications. In contrast, HPMC K4M provides unmatched reliability and adaptability, ensuring consistent performance across a broad range of formulations.
But how do natural alternatives measure up? Let’s find out.
Natural Polymers
Xanthan gum is one of the more prominent natural alternatives, prized for its exceptional thickening capabilities in suspensions and semi-solid formulations. However, its susceptibility to enzymatic degradation and reduced gel stability under extreme conditions limit its utility in precision-driven pharmaceutical applications. Similarly, guar gum, while effective in certain binding and dietary supplement applications, often struggles with consistency and lacks the advanced film-forming properties required for pharmaceutical coatings. These limitations position HPMC K4M as a superior choice when consistency and performance are critical.
How do other cellulose-based polymers compare? Let’s examine.
Other Cellulose Ethers
Other cellulose ethers, such as HPMC K100M, share similarities with K4M but differ in their application scope. K100M’s higher viscosity makes it ideal for specific, highly specialized uses, yet K4M’s balanced properties and broader versatility make it the preferred option for a wide range of formulations. Methylcellulose, another alternative, offers dependable performance but lacks the thermal gelation properties and customization potential that define HPMC K4M’s edge in the market.
With these comparisons in mind, what solidifies HPMC K4M’s position as the leading polymer? The next section will delve into its defining advantages.
HPMC K4M vs. Natural and Synthetic Polymers
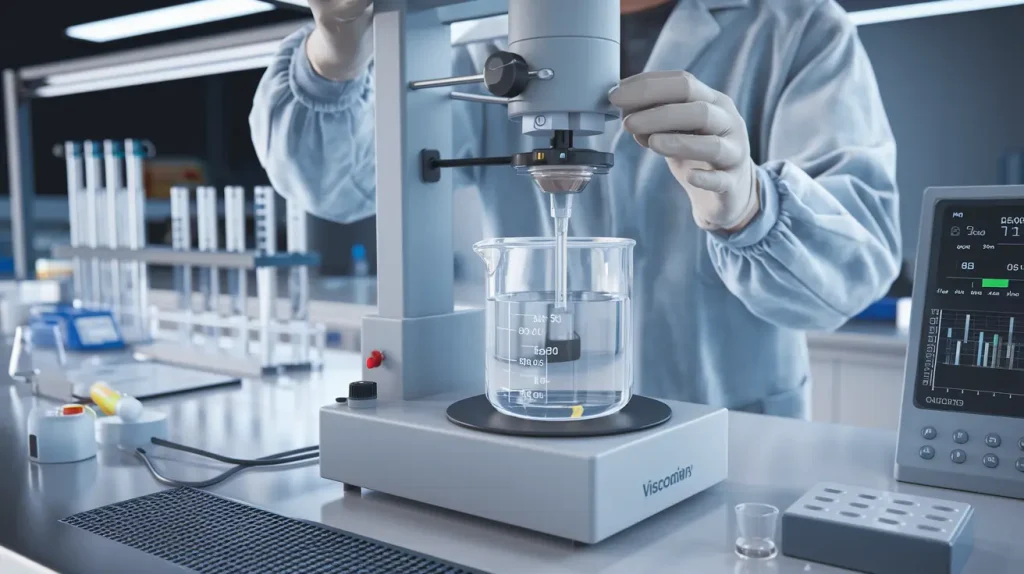
Gel Strength and Rheological Properties
HPMC K4M excels in gel strength and consistent rheological behavior, outperforming both natural and synthetic polymer alternatives. Its ability to maintain stability under diverse conditions ensures uniformity and effectiveness across various applications, from pharmaceutical controlled-release systems to industrial formulations. Unlike many alternatives, which may exhibit variability under stress, K4M provides dependable and predictable performance, making it an essential component in precision-driven formulations.
How does this translate to real-world application in complex systems? Let’s dive into its compatibility.
Compatibility and Blending
A major advantage of HPMC K4M is its exceptional compatibility with excipients and active pharmaceutical ingredients (APIs). Its non-ionic nature minimizes the risk of chemical interactions, allowing it to blend seamlessly into sophisticated formulations without compromising stability or efficacy. This ensures that even delicate APIs retain their therapeutic activity, enhancing overall formulation reliability and performance.
But beyond technical superiority, K4M aligns with a growing focus on sustainability and safety. Let’s explore.
Environmental and Safety Considerations
HPMC K4M stands out for its environmentally friendly and safe profile. As a biodegradable, non-toxic polymer, it provides a sustainable alternative to synthetic polymers, which often face scrutiny for their ecological impact and long-term safety concerns. By meeting both high-performance and environmental standards, K4M supports industries striving for greener solutions while maintaining uncompromised functionality and safety.
With these advantages in mind, it’s clear why HPMC K4M is the polymer of choice for innovation across industries. Let’s summarize its defining qualities.
Applications Beyond Pharmaceuticals
Food Industry
In the food sector, HPMC K4M serves as a reliable thickener and stabilizer, enhancing product quality and consistency. Its ability to form stable gels and maintain viscosity under various conditions makes it ideal for applications such as sauces, dressings, and baked goods. Unlike hydrocolloids like xanthan gum, HPMC K4M offers superior heat stability and uniform dispersion, ensuring consistent texture and functionality across diverse food formulations. This dependable performance helps food manufacturers meet stringent quality and regulatory requirements while delivering exceptional consumer experiences.
How does HPMC K4M adapt to industrial demands? Let’s examine its role in construction.
Construction and Adhesives
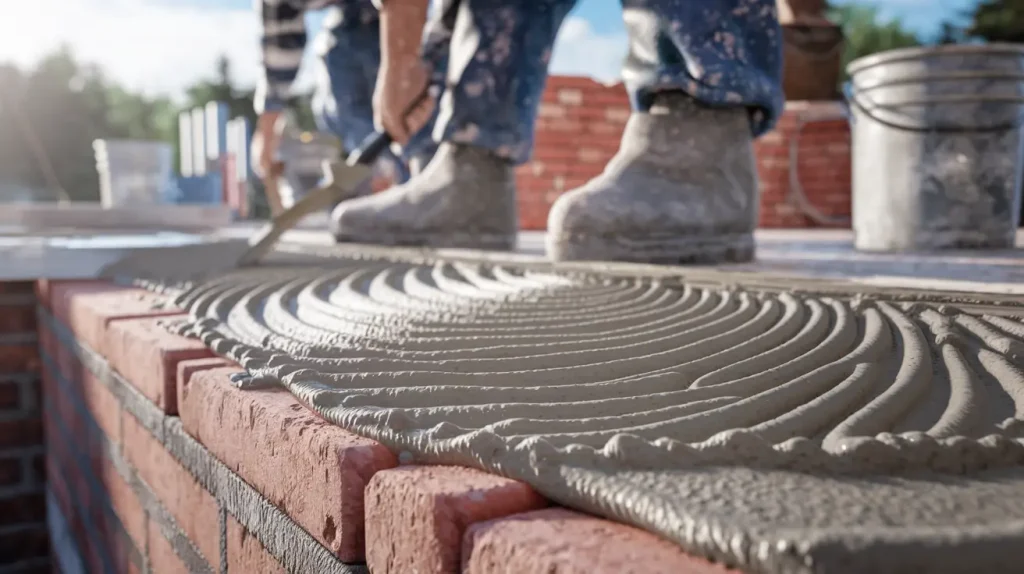
HPMC K4M proves indispensable in the construction industry, particularly as a water retention agent in cement and mortar formulations. Its unique properties promote even hydration, improve workability, and enhance adhesive strength, leading to smoother application and durable results. Compared to alternatives like guar gum, HPMC K4M demonstrates greater stability and resilience to environmental variations, ensuring reliable performance under demanding conditions. Whether optimizing the consistency of cement or strengthening adhesive formulations, HPMC K4M redefines efficiency and reliability in construction applications.
What unites its diverse applications? Let’s explore the universal attributes that make HPMC K4M a standout solution.
How to Choose the Right Polymer for Your Needs
Key Factors to Consider
Choosing the right polymer is essential for ensuring optimal performance, cost efficiency, and compliance in your applications. Start by evaluating the specific demands of your project: Does it require precise viscosity control, exceptional solubility, or stability under varying thermal conditions? Budget considerations also play a role, as some polymers offer cost-effective solutions while others prioritize high-end performance. Regulatory compliance is particularly crucial in industries like pharmaceuticals and food, where adherence to stringent standards is non-negotiable.
How can you navigate these factors effectively? Let’s explore some practical decision-making strategies.
Decision-Making Tips
Identifying the ideal polymer, such as HPMC K4M, requires a clear understanding of its advantages relative to alternatives. Projects involving controlled drug release, robust film-forming capabilities, or applications where biodegradability is important often benefit from K4M’s unique properties. Assess critical attributes such as substitution levels, viscosity grades, and thermal gelation characteristics to ensure alignment with your needs. Additionally, prioritize suppliers with recognized certifications to guarantee consistent quality and regulatory compliance.
Still uncertain? Let’s delve into how K4M consistently meets real-world requirements across diverse industries.
Innovations and Future Trends in Polymer Excipients
Recent Developments in HPMC Grades
Polymer excipients are undergoing significant advancements, with HPMC grades leading the charge. Enhanced formulations now deliver greater precision and functionality, supporting complex applications like precision medicine, where controlled drug release and targeted delivery are critical. These innovations highlight a shift toward excipient customization, allowing manufacturers to tailor properties such as viscosity, solubility, and thermal stability to meet the demands of cutting-edge pharmaceutical and industrial solutions.
How does this evolution intersect with developments beyond HPMC? Let’s examine the role of emerging alternatives.
Emerging Alternatives
The polymer excipient landscape is expanding with the introduction of advanced hydrocolloids and synthetic polymers designed to meet modern challenges. These emerging options emphasize features like superior biodegradability, increased functionality, and sustainability. While some alternatives aim to compete directly with HPMC in performance, others target specific niches, particularly in environmentally conscious industries. As research progresses, the balance between high-performance materials and eco-friendly solutions will continue to drive innovation, opening doors to more sustainable practices across sectors.
What lies ahead for polymer excipients? Let’s explore how these advancements will shape future industry practices.
Conclusion
HPMC K4M is a standout polymer, renowned for its unmatched versatility, stability, and adaptability across diverse industries. From revolutionizing pharmaceutical formulations with controlled drug release to enhancing the functionality of food and construction materials, HPMC K4M has consistently set the benchmark for performance. Its ability to combine technical excellence with environmental sustainability positions it as a critical solution in an ever-evolving marketplace.
Why is HPMC K4M the polymer of choice for the future? The answer lies in its unique qualities.
Selecting the right polymer—whether it’s HPMC K4M or an alternative—requires a clear understanding of application-specific needs and compliance requirements. With features like thermal gelation, customizable substitution levels, and superior compatibility, HPMC K4M delivers exceptional reliability and flexibility. These attributes make it a trusted choice for projects demanding precision, consistency, and innovation.
As industries increasingly prioritize sustainable and high-performing solutions, HPMC K4M’s relevance will only continue to grow. Its proven track record and adaptability make it more than just a polymer for today—it’s a foundation for future breakthroughs. Whether optimizing existing formulations or exploring new applications, HPMC K4M provides a dependable pathway to achieving your goals.
The next step is yours—unlock the full potential of HPMC K4M and lead the way in innovation.
FAQ: HPMC K4M and Its Alternatives
1. What is HPMC K4M commonly used for?
HPMC K4M is widely utilized in pharmaceuticals for controlled drug release, as a binder in tablets, and as a coating agent for moisture protection. It also serves as a thickener and stabilizer in food products and acts as a water retention agent in construction materials like cement and mortar.
2. How does HPMC K4M compare to natural polymers like xanthan gum?
HPMC K4M offers superior thermal stability, consistent viscosity, and enhanced film-forming properties compared to xanthan gum. These qualities make it a better fit for applications requiring precision, such as pharmaceuticals and construction.
3. Is HPMC K4M biodegradable and environmentally friendly?
Yes, HPMC K4M is biodegradable and non-toxic, providing an environmentally friendly alternative to many synthetic polymers.
4. Can HPMC K4M be customized for specific applications?
Absolutely. HPMC K4M’s methoxyl and hydroxypropyl substitution levels can be tailored to adjust its viscosity, solubility, and gelation properties, meeting the unique demands of various applications.
5. What are the key advantages of HPMC K4M in controlled drug release?
HPMC K4M forms a stable gel matrix that ensures consistent and sustained drug release, enhancing therapeutic efficacy and reducing the need for frequent dosing.
6. How does HPMC K4M perform in high-temperature applications?
HPMC K4M exhibits excellent thermal gelation properties, maintaining its stability and performance even in high-temperature environments.
7. Are there cost-effective alternatives to HPMC K4M?
While alternatives like carbomers and guar gum can be more cost-effective for certain uses, they often lack the versatility, stability, and customization options that HPMC K4M provides.
8. Is HPMC K4M safe for use in food products?
Yes, HPMC K4M is approved for food-grade applications and is commonly used as a thickener and stabilizer in food products, meeting strict regulatory standards.
9. How does HPMC K4M compare to synthetic polymers like carbomer?
HPMC K4M offers better compatibility with active pharmaceutical ingredients (APIs), broader pH stability, and a more natural, biodegradable profile compared to carbomers, making it ideal for sensitive and eco-conscious applications.
10. How do I decide if HPMC K4M is the right choice for my application?
Assess your specific requirements, such as viscosity, solubility, thermal stability, and compliance needs. HPMC K4M is an excellent choice for applications requiring versatility, reliability, and environmental sustainability.