Hydroxypropyl Methylcellulose, commonly known as HPMC, is a critical excipient used extensively in pharmaceutical drug film coating. What’s the real story? This article will delve into the role of HPMC in drug film coating, highlighting its essential functions, technical properties, and practical applications within pharmaceutical production. We will explore why this polymer is chosen by manufacturers, how it affects drug stability, release, and patient compliance, and what challenges companies may face when incorporating HPMC into coating formulations. For decision-makers in pharmaceutical procurement, manufacturing, and quality assurance, understanding HPMC’s role is key to optimizing both product performance and regulatory compliance.
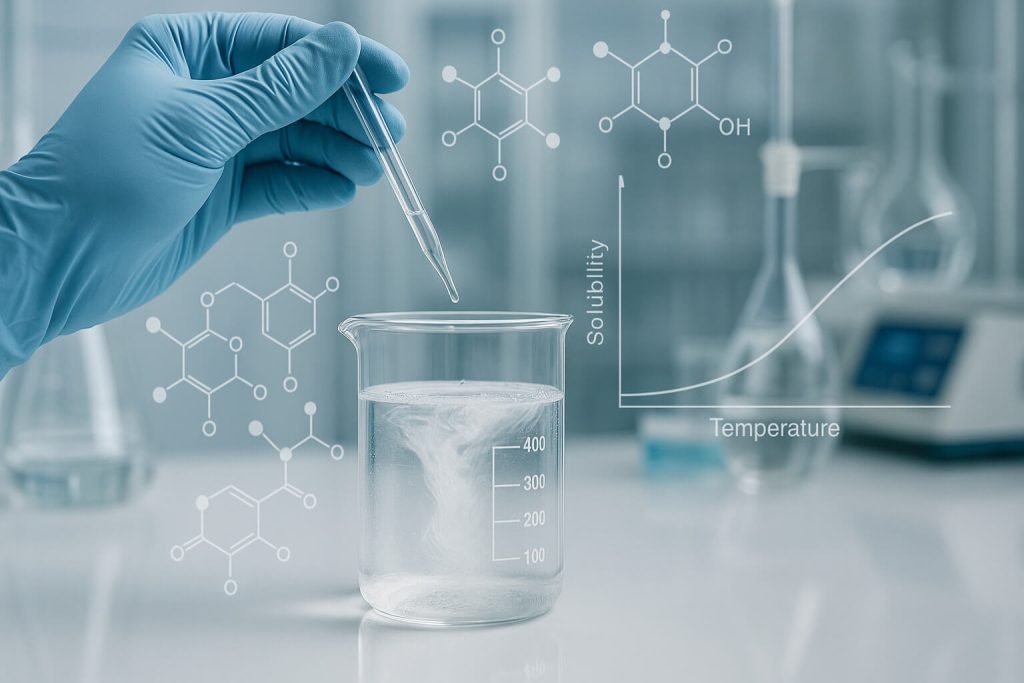
1 What is HPMC and why is it used in drug film coating?
To understand why HPMC is widely used in drug film coating, we must first look at what it is chemically and physically. HPMC is a semi-synthetic cellulose ether derived by substituting the hydroxyl groups of cellulose with hydroxypropyl and methyl groups. But here’s the kicker—this modification makes HPMC water-soluble and capable of forming transparent, flexible films, which are indispensable in pharmaceutical coatings.
The importance of HPMC in pharma lies in its non-toxic, inert nature and its acceptance by regulatory agencies worldwide such as the FDA and EMA. It is well-known for its safety profile, biocompatibility, and stability, which makes it suitable for oral solid dosage forms including tablets and capsules.
Ready for the good part? HPMC coatings provide a protective barrier against environmental factors like moisture, oxygen, and light, which otherwise could degrade the active pharmaceutical ingredients (APIs). Additionally, the polymer’s ability to form uniform films aids in masking unpleasant tastes and odors, improving patient compliance.
In practical terms, companies use HPMC to deliver functional coatings that ensure the tablet’s integrity during storage and handling while controlling drug release profiles.
For example, an international pharmaceutical company reported improved product shelf life by incorporating HPMC coatings in their cardiovascular tablet line, resulting in better moisture resistance and reduced breakage during packaging.
This is where it gets interesting: the variability in HPMC grades, differentiated by molecular weight and degree of substitution, allows formulators to customize coating thickness, dissolution characteristics, and mechanical strength to suit various formulations.
Characteristic | Description | Pharmaceutical Benefit |
---|---|---|
Chemical Nature | Cellulose derivative with methyl and hydroxypropyl substitution | Water soluble, film forming |
Safety Profile | Non-toxic, non-irritant, GRAS status | Safe for human use |
Film Properties | Transparent, flexible films | Protects formulation, taste masking |
Customizability | Different molecular weights and viscosities | Tailored drug release |
Regulatory Approval | Widely accepted in pharmacopeias | Facilitates global product registration |
2 How does HPMC improve tablet protection and stability?
But here’s the kicker: one of the primary advantages of using HPMC in drug film coatings is its ability to shield tablets from environmental stressors. Film coatings act as physical barriers that protect tablets from moisture, oxygen, and light—factors that contribute to chemical and physical degradation.
This protective effect directly impacts the shelf life and stability of pharmaceuticals. For example, moisture-sensitive APIs like aspirin and vitamin C greatly benefit from HPMC coatings, which prevent moisture ingress that could trigger hydrolysis or oxidation.
What’s the real story? HPMC’s hydrophilic nature forms films that do not trap moisture but rather regulate water vapor permeation, maintaining the right moisture balance to protect the drug while preventing excessive swelling or stickiness.
In addition, HPMC coatings contribute to mechanical robustness. Tablets coated with HPMC exhibit improved resistance to abrasion and chipping during packaging and transportation. For instance, in a study involving coated ibuprofen tablets, HPMC coatings effectively reduced friability by over 40%, decreasing product loss and packaging defects.
Pharmaceutical companies also use HPMC coatings to enhance tablet aesthetics, such as gloss and color uniformity, which influences patient perception and brand reputation.
Ready for the good part? HPMC coatings improve handling efficiency within automated packaging lines by reducing dust and powder contamination, contributing to cleaner manufacturing environments.
Protection Factor | HPMC Contribution | Resulting Benefit |
---|---|---|
Moisture Barrier | Regulates vapor transmission | Protects moisture-sensitive APIs |
Oxygen Protection | Provides physical shielding | Prevents oxidation of drug |
Light Protection | Transparent but can be combined with pigments | Guards against photodegradation |
Mechanical Strength | Enhances tablet surface robustness | Reduces breakage and chipping |
Aesthetic Improvement | Produces uniform glossy films | Improves patient acceptance |
3 What are the technical attributes of HPMC that make it suitable for film coating?
When it comes to coating polymers, HPMC offers several technical advantages. This is where it gets interesting. HPMC’s ability to form strong, flexible films is crucial in creating coatings that can withstand mechanical stresses without cracking or peeling.
The polymer’s solubility in water allows manufacturers to use environmentally friendly aqueous coating systems, avoiding hazardous organic solvents. This contributes to safer workplace conditions and regulatory compliance related to environmental standards.
Viscosity is a key parameter: HPMC grades range widely in viscosity, and selection depends on the desired film thickness and coating process. Lower viscosity grades are preferred for thin coatings; higher viscosities help form thicker, more protective films.
Compatibility is another strength. HPMC mixes well with common pharmaceutical excipients and can incorporate plasticizers, colorants, and opacity enhancers without losing film integrity. For instance, combining HPMC with polyethylene glycol plasticizers can improve film flexibility, reducing brittleness.
The polymer also offers good thermal stability, with typical processing temperatures below 90°C to avoid degradation. This makes it compatible with standard pan and fluidized bed coating equipment.
What’s the real story? Choosing the right HPMC grade and formulation components ensures the coating performs consistently across batches, improving product quality and reducing manufacturing downtime.
For example, in a multisite pharma production setup, standardizing coating parameters using specific HPMC grades reduced batch variability and improved coating uniformity by 25%.
Technical Attribute | Description | Impact on Coating Process |
---|---|---|
Film Formation | Strong, flexible films | Durability and resistance |
Solubility | Water soluble | Environmentally friendly coatings |
Viscosity Range | Wide viscosity grades | Adjustable film thickness |
Compatibility | Mixes well with excipients | Versatile formulation options |
Thermal Stability | Stable up to ~90°C | Broad processing compatibility |
4 How does HPMC control drug release in coated formulations?
Ready for the good part? Beyond physical protection, HPMC film coatings are often engineered to control the release of drugs. This can provide immediate, delayed, or sustained release profiles depending on the polymer properties and coating thickness.
HPMC is a hydrophilic polymer that swells upon contact with gastrointestinal fluids, forming a gel layer. This gel acts as a diffusion barrier that regulates the rate at which the API dissolves and becomes available for absorption.
For example, cardiovascular drugs benefit from HPMC coatings that slow release, allowing once-daily dosing instead of multiple tablets per day. Studies have shown formulations with higher HPMC content exhibiting more controlled dissolution kinetics.
Delayed-release tablets use HPMC coatings with adjusted thickness to protect the API from stomach acid, releasing active ingredients only when reaching the intestine, improving efficacy and reducing side effects.
A case study on anti-diabetic drugs demonstrated how layered HPMC coatings helped maintain plasma drug concentrations within therapeutic windows longer.
What’s the real story? Fine-tuning molecular weight and substitution in HPMC grades allows formulators to precisely design film permeability and erosion characteristics.
This improves patient compliance by reducing dosing frequency, stabilizes blood levels, and minimizes adverse effects.
Release Mechanism | HPMC Influence | Pharmaceutical Outcome |
---|---|---|
Immediate Release | Thin coatings dissolve quickly | Fast therapeutic onset |
Sustained Release | Gel layer regulates diffusion | Prolonged therapeutic effect |
Delayed Release | Barrier resists gastric fluids | Targeted drug delivery in intestines |
Molecular Weight | Higher weight slows release | Extended duration |
Film Thickness | Thicker films slow dissolution | Customizable dosing profiles |
5 What coating methods utilize HPMC and how does it perform in these processes?
What’s the real story? HPMC is compatible with several coating processes, with spray coating and fluidized bed coating being the most prevalent in pharmaceutical manufacturing.
Spray coating involves atomizing an aqueous HPMC solution onto tablets in a rotating pan or drum. HPMC’s solubility and viscosity enable the formation of uniform films that dry rapidly under controlled temperatures.
Fluidized bed coating suspends tablets in an upward stream of warm air while spraying HPMC solution, yielding more consistent coverage on complex shapes and higher throughput.
For instance, a large-scale production of coated vitamin tablets employed aqueous HPMC coatings via fluidized bed, achieving a 30% faster production cycle compared to solvent-based methods.
HPMC’s rheological properties facilitate atomization and reduce nozzle clogging, enhancing process reliability.
But here’s the kicker: controlling drying rates is crucial since overly rapid evaporation can cause film defects like cracking or peeling. Optimizing parameters such as inlet air temperature, spray rate, and atomizing pressure prevents these issues.
Coating defects can cause batch rejection and financial loss, so understanding HPMC’s performance in each coating method is vital for quality assurance.
Coating Method | HPMC Performance | Manufacturing Advantage |
---|---|---|
Spray Coating | Forms uniform films, easy atomization | Safer, solvent-free processes |
Fluidized Bed Coating | Consistent coverage on complex shapes | Faster, efficient coating |
Drying Control | Sensitive to drying parameters | Avoids film cracking |
Rheology | Optimal viscosity for spraying | Reduces nozzle clogging |
Scale-Up | Good batch-to-batch consistency | Reliable large-scale manufacturing |
6 How does HPMC contribute to improving patient compliance through film coatings?
Patient compliance is a cornerstone of effective therapy. Ready for the good part? HPMC film coatings play a significant role in increasing adherence to medication regimens.
First, HPMC films effectively mask the bitter or unpleasant taste of many APIs, improving palatability. For example, children’s chewable tablets or capsules often incorporate HPMC coatings to hide flavors without chemical additives.
Second, coatings improve swallowing ease by providing a smooth, glossy surface reducing tablet friction in the mouth and throat. This is especially important for elderly patients or those with dysphagia.
Third, the visual appeal of HPMC-coated tablets supports stronger brand recognition and trust, influencing patient willingness to continue medication.
Moreover, HPMC coatings contribute to dose accuracy by protecting tablets from chipping or crumbling during handling and packaging.
Pharmaceutical marketers report that formulations with HPMC coatings experience reduced prescription abandonment, supporting healthier outcomes.
What’s the real story? Patient adherence isn’t just about convenience—it directly affects therapeutic success, and HPMC coatings are a simple, effective means to achieve this.
Compliance Factor | HPMC Contribution | Patient Benefit |
---|---|---|
Taste Masking | Tasteless film coatings | Increases acceptability |
Swallowing Ease | Smooth, glossy surface | Improves ease of ingestion |
Visual Appeal | Uniform, glossy finish | Enhances patient confidence |
Tablet Integrity | Reduces chipping and breakage | Ensures accurate dosing |
Adherence Impact | Increased palatability and ease | Better therapeutic outcomes |
7 What challenges and limitations exist when using HPMC in drug film coating?
But here’s the kicker: despite its many advantages, using HPMC in drug film coating comes with challenges that formulators must manage carefully.
One common issue is film brittleness, especially if the HPMC grade or plasticizer choice does not provide adequate flexibility. Brittle coatings may crack during handling, reducing protection.
Environmental factors such as high humidity can influence the drying process and long-term stability of HPMC coatings. Excess moisture during storage may lead to tackiness or swelling.
Also, HPMC’s hydrophilic nature may not be suitable for moisture-sensitive drugs requiring water-impermeable coatings, necessitating combination with other polymers.
Interactions with other excipients or APIs may alter dissolution profiles unpredictably, making compatibility testing vital.
An example involves a formulation in which improper drying and low plasticizer content caused peeling films, prompting costly reformulations and production delays.
Ready for the good part? These challenges can be mitigated by thorough pre-formulation studies, judicious plasticizer use, and controlled environmental conditions during coating and storage.
Challenge | Potential Impact | Mitigation Strategy |
---|---|---|
Film Brittleness | Cracking or peeling of coats | Use plasticizers, optimize grade |
Humidity Sensitivity | Tackiness or swelling | Control environmental storage |
Moisture Permeability | Unsuitable for extremely moisture-sensitive drugs | Combine with hydrophobic polymers |
Excipient Interaction | Altered drug release | Conduct compatibility studies |
Process Variability | Inconsistent coating quality | Standardize parameters |
8 How do pharma companies ensure the quality and consistency of HPMC film coatings?
This is where it gets interesting. Quality control is paramount when using HPMC film coatings to guarantee product performance and regulatory compliance.
Raw material testing for HPMC includes measuring viscosity, particle size, moisture content, and substitution degree. These parameters directly influence coating properties and batch consistency.
In-process controls monitor coating solution viscosity, spray rate, drying conditions, and coating weight gain. Real-time adjustments ensure uniformity and avoid defects.
Finished products undergo visual inspection, adhesion tests, dissolution testing, and hardness measurements to confirm coating integrity and therapeutic efficacy.
Pharma companies also maintain detailed documentation and traceability for HPMC batches and coating runs to meet stringent regulatory standards such as GMP and ICH guidelines.
A leading global drug manufacturer reported a 20% reduction in coating-related batch rejections after implementing advanced PAT tools to monitor HPMC coating consistency.
Ready for the good part? Supplier qualification is another essential step, involving audits and certification to ensure raw HPMC quality.
Quality Control Aspect | Testing Parameters | Industry Impact |
---|---|---|
Raw Material Testing | Viscosity, moisture, purity | Ensures consistent inputs |
In-Process Monitoring | Viscosity, spray rate, drying | Prevents defects during coating |
Finished Product QC | Hardness, dissolution, adhesion | Confirms performance and safety |
Documentation | Batch records and traceability | Compliance with regulations |
Supplier Qualification | Audits and certificates | Mitigates supply chain risks |
Conclusion
In conclusion, the role of HPMC in drug film coating is multifaceted and crucial for pharmaceutical product success. Its unique physicochemical properties enable it to provide protection, control drug release, improve patient compliance, and aid manufacturing efficiency. Despite certain formulation challenges like brittleness or moisture sensitivity, these can be managed with best practices in pre-formulation and process control. Pharmaceutical companies that invest in quality assurance and supplier management maximize the benefits of HPMC coatings, resulting in better product stability, compliance, and patient outcomes. Understanding the role of HPMC empowers decision-makers to optimize pharmaceutical formulations with confidence.
Q1: What is HPMC in drug film coating?
Hydroxypropyl Methylcellulose (HPMC) is a polymer used to form protective, flexible films on tablets and capsules, aiding in drug stability, release control, and patient compliance.
Q2: How does HPMC work in film coating?
HPMC dissolves in water to create films that protect drugs from moisture and oxygen, mask taste, and modulate drug release rates through swelling and gel formation.
Q3: What are the benefits of using HPMC for taste masking?
HPMC coatings effectively cover unpleasant tastes and odors of active ingredients, making medications easier to swallow and improving patient adherence.
Q4: What manufacturing methods are commonly used with HPMC coatings?
Spray coating and fluidized bed coating are standard techniques for applying HPMC films, benefiting from its water solubility and adjustable viscosity.
Q5: What quality controls are important for HPMC film coatings?
Critical quality controls include raw material viscosity and purity testing, in-process monitoring of coating parameters, finished product dissolution and hardness tests, and comprehensive documentation for regulatory compliance.