Las empresas farmacéuticas se enfrentan a graves problemas con la estabilidad de los fármacos, el tiempo de liberación y el uso en pacientes. Cuando los recubrimientos fallan, los fármacos pueden degradarse rápidamente, liberarse en momentos inoportunos o tener mal sabor. Esto provoca el desperdicio de lotes, el rechazo de productos y pérdidas económicas. La HPMC (hidroxipropilmetilcelulosa) ofrece una buena solución. Produce recubrimientos estables con patrones de liberación precisos. Las pruebas demuestran que los medicamentos recubiertos con HPMC se conservan en buen estado hasta 36 meses más. Este artículo analiza cómo funciona la HPMC en el recubrimiento de películas, sus propiedades de barrera, los métodos de liberación, los factores de la fórmula, los pasos del proceso y cómo se compara con otras opciones.
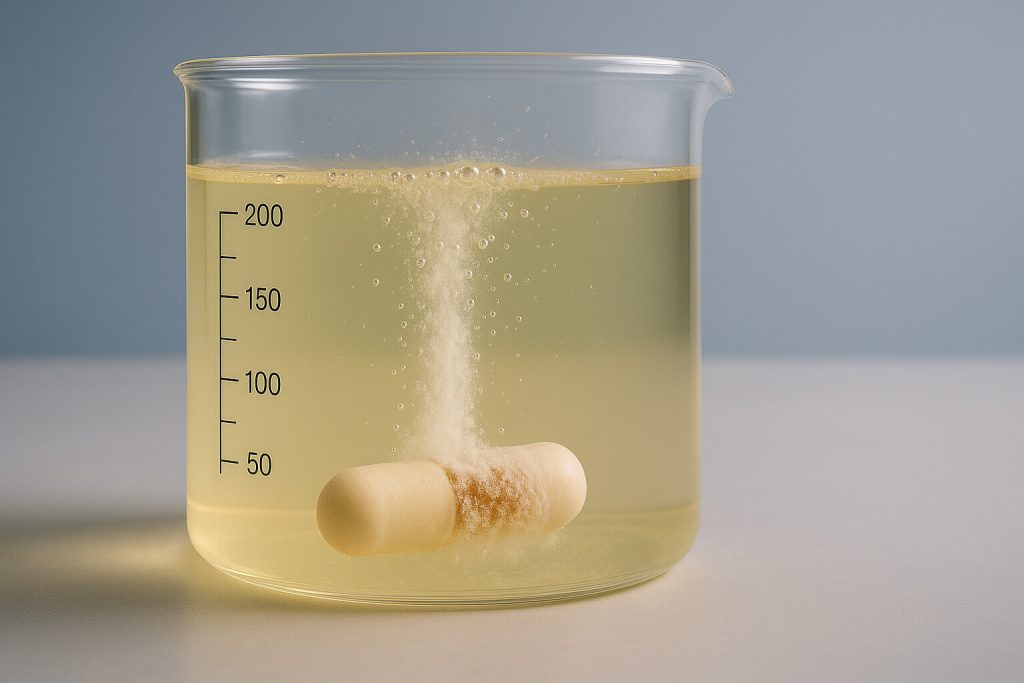
1. ¿Cuáles son las propiedades básicas del HPMC para el recubrimiento de películas?
El HPMC es un éter de celulosa con propiedades especiales para el recubrimiento de fármacos. Su base es de celulosa con grupos metoxi e hidroxipropilo. Sabías ¿Que estos grupos permitan que el HPMC forme películas fuertes mientras se mezcla bien con el agua?
Las características físicas del HPMC lo hacen ideal para recubrimientos. Forma películas transparentes y resistentes que no se agrietan y se adhieren bien a los comprimidos. Bloquea el oxígeno y deja pasar la humedad. Esto ayuda a evitar la descomposición de los fármacos.
El HPMC se presenta en diversos grados con espesores que van desde 3 hasta 100 000 mPa·s. Los grados de bajo espesor (3-15 mPa·s) son adecuados para recubrimientos de liberación rápida. Los grados de alto espesor (4000-100 000 mPa·s) son adecuados para aplicaciones de liberación lenta. Los grupos químicos también varían, y las diferentes proporciones afectan su disolución y reacción al calor.
Grado HPMC | Espesor (mPa·s) | Uso principal | Rasgos cinematográficos |
---|---|---|---|
E3 | 3 | Liberación rápida | Delgado, de rápida disolución. |
E5 | 5 | Liberación rápida | De espesor medio, de rápida disolución. |
E15 | 15 | Liberación rápida | Más espeso, de disolución media rápida. |
K4M | 4,000 | Liberación lenta | Grueso, de lento desgaste. |
K15M | 15,000 | Liberación lenta | Muy grueso, se desgasta muy lentamente. |
K100M | 100,000 | Liberación extra larga | Extremadamente grueso, de muy larga duración. |
En comparación con otros polímeros de recubrimiento, el HPMC presenta numerosas ventajas. A diferencia de la etilcelulosa, se mezcla bien con el agua, lo que lo hace más ecológico. En comparación con el alcohol polivinílico, el HPMC se mantiene más estable ante los cambios de humedad. Además, es más económico que muchas opciones sintéticas y funciona igual de bien.
El peso de las moléculas de HPMC afecta la formación de películas. Los grados de mayor peso forman películas más resistentes y elásticas, pero requieren más agua. Este equilibrio entre la resistencia de la película y la facilidad de uso requiere una cuidadosa consideración durante el diseño de la fórmula.
2. ¿Cuáles son las propiedades de barrera básicas de los recubrimientos de HPMC?
Las características de barrera de los recubrimientos de HPMC ayudan a proteger los medicamentos de daños externos. Aquí está la cosa Sobre la protección contra la humedad: El HPMC forma una capa semiabierta que ralentiza el vapor de agua sin bloquearlo por completo. Esto ayuda a prevenir los daños por humedad y a evitar la formación de películas quebradizas.
Las películas de HPMC ofrecen una protección media contra el oxígeno, lo que favorece a los fármacos que reaccionan con este. Las cadenas de polímero se compactan lo suficiente como para limitar el paso del oxígeno. Añadir agentes antioxígeno a la HPMC puede ser aún más eficaz. En el caso de fármacos muy sensibles al oxígeno, los fabricantes suelen mezclar la HPMC con otros polímeros para crear una barrera más resistente.
La protección contra la luz es otra función clave de los recubrimientos de HPMC. Si bien las películas de HPMC puras son transparentes, los fabricantes añaden pigmentos para bloquear la luz UV y visible. El dióxido de titanio es el bloqueador de luz más común, lo que proporciona una gran protección contra los daños causados por la luz.
Tipo de barrera | Nivel de HPMC | Formas de mejorar | Límites |
---|---|---|---|
Humedad | Medio | Añadir piezas que eviten el agua | No es bueno para medicamentos muy sensibles a la humedad. |
Oxígeno | Bajo a medio | Mezclar con agentes antioxígeno | No es suficiente para medicamentos muy sensibles al oxígeno |
Luz | Bajo (claro) | Añadir TiO₂ u óxidos de hierro | Necesita aditivos para una buena protección. |
Sabor/Olor | De media a alta | Hacer la película más gruesa | Puede retardar la disolución si es demasiado espesa. |
El espesor de la película afecta la función de barrera. Duplicar el espesor del recubrimiento reduce el paso de 40-60%. Esta relación no es directa debido a los diminutos canales presentes en las películas más gruesas. La mayoría de los fármacos utilizan un espesor de recubrimiento de HPMC de entre 20 y 80 μm. Esto equilibra las propiedades de barrera con las necesidades de disolución.
La forma en que el HPMC absorbe el agua también contribuye a su función de barrera. Al mojarse, la capa exterior forma un gel que retarda la penetración del agua en el núcleo. Este sistema de autofijación ayuda a mantener los productos estables incluso cuando varían los niveles de humedad.
3. ¿Qué hace que la HPMC sea ideal para la liberación controlada de fármacos?
La HPMC funciona bien para la liberación controlada gracias a su absorción de agua y a su capacidad de gelificación. Cuando una tableta recubierta de HPMC entra en contacto con los fluidos estomacales, forma una capa de gel alrededor del núcleo. Te podrías sorprender saber que esta capa de gel actúa como una pared, controlando la velocidad con la que se libera el medicamento en el cuerpo.
La forma en que los fármacos se mueven a través de la HPMC sigue la ley de Fick. La velocidad depende de la cantidad de fármaco y la longitud del recorrido. A medida que el agua se desplaza más profundamente, la capa de gel se engrosa, alargando el recorrido. Esto crea un sistema de autofijación donde la liberación del fármaco disminuye lentamente con el tiempo, lo que a menudo resulta en velocidades de liberación constantes.
Método de liberación | Cómo funciona | Patrón de liberación típico | Mejor grado de HPMC |
---|---|---|---|
Difusión | El fármaco se mueve a través de la capa de gel. | Raíz cuadrada del tiempo | K4M, K15M |
Erosión | La capa de gel se desgasta lentamente | Estable (lineal) | K100M |
Hinchazón | La matriz se expande, creando poros. | Tasa de caída | E4M, E15M |
Conjunto | Múltiples métodos a la vez | Bifásico o en forma de S | Mezcla K15M + E5 |
El comportamiento ligado al pH del HPMC añade una ventaja adicional a la liberación controlada. A diferencia de algunos polímeros que se disuelven solo a ciertos niveles de pH, el HPMC se mantiene estable en todo el rango de pH corporal (1,2-7,4). Esta propiedad de pH libre garantiza que la liberación del fármaco se mantenga constante en todo el intestino, independientemente de las diferencias en la acidez estomacal del paciente.
Los estudios de caso demuestran que la HPMC funciona bien en la liberación controlada. Una fórmula de metformina con HPMC K100M proporcionó una liberación lenta de 24 horas. Esto ayudó a los pacientes al reducir la dosis de tres veces al día a una vez al día. En otro caso con diltiazem, se utilizó HPMC K15M para mantener los niveles sanguíneos estables durante 12 horas. Esto redujo considerablemente el riesgo de dolor torácico en comparación con las formulaciones de liberación rápida.
El patrón de grupos químicos en el HPMC afecta su absorción de agua y la resistencia del gel. Un mayor número de grupos hidroxipropilo acelera la absorción de agua. Un mayor número de grupos metoxilo fortalece la capa de gel. Al seleccionar ciertos grados de HPMC, los fabricantes pueden ajustar los patrones de liberación para satisfacer las necesidades del tratamiento.
4. ¿Cómo afectan los factores de fórmula a los resultados del recubrimiento HPMC?
El peso molecular y el patrón del grupo químico del HPMC afectan en gran medida los resultados del recubrimiento. La realidad es Los grados de mayor peso forman películas más resistentes, pero requieren más agua, lo que ralentiza el proceso de recubrimiento. La proporción metoxi:hidroxipropilo determina la atracción del agua. Una mayor concentración de hidroxipropilo crea películas más resistentes al agua que la absorben y se disuelven más rápidamente.
Los suavizantes desempeñan un papel fundamental en las propiedades de las películas de HPMC. Estos aditivos facilitan el movimiento de las cadenas de polímeros, aumentando la flexibilidad de las películas. Entre los suavizantes comunes para HPMC se incluyen los polietilenglicoles, el propilenglicol y la triacetina. La cantidad óptima de suavizante oscila entre 10 y 301 TP3T del peso del polímero. Una concentración más alta aumenta la flexibilidad de las películas, pero puede reducir sus propiedades de barrera.
Suavizante | Cantidad típica (% p/p) | Efecto sobre los rasgos cinematográficos | Compatible con HPMC |
---|---|---|---|
PEG 400 | 10-20% | Más flexible, atrae el agua. | Excelente |
Propilenglicol | 5-15% | Medianamente flexible, atrae menos agua. | Muy bien |
Triacetina | 10-25% | Buena flexibilidad, evita el agua. | Bien |
Glicerina | 5-15% | Altamente flexible, muy absorbente del agua. | Excelente |
sebacato de dibutilo | 15-30% | Alta flexibilidad, evita el agua. | Medio |
Los sistemas de solventes afectan considerablemente la calidad del recubrimiento. Las soluciones de HPMC a base de agua ofrecen ventajas ecológicas y de seguridad, pero se secan más lentamente que los sistemas orgánicos. La mezcla de solventes afecta la forma de la cadena de polímeros durante la formación de la película. Esto modifica las características físicas del recubrimiento final. Las soluciones típicas de HPMC a base de agua contienen polímero 5-10%. Las soluciones orgánicas pueden contener hasta 15-20% debido a su menor espesor.
Los aditivos en las fórmulas de HPMC cumplen diversas funciones. Los agentes humectantes, como el polisorbato 80, ayudan a que el recubrimiento se adhiera al núcleo del comprimido. Los agentes antiadherentes, como el talco, evitan que los comprimidos se adhieran entre sí durante el recubrimiento. Los pigmentos no solo añaden color, sino que también bloquean la luz y facilitan la identificación del producto.
La proporción entre HPMC y aditivos requiere un equilibrio preciso. Un exceso de aditivos puede romper las cadenas de polímeros, debilitando la película. Una fórmula típica podría contener 60-80% de HPMC, 10-20% de suavizante, 5-10% de pigmentos y 1-5% de agentes humectantes u otros aditivos activos.
La sensibilidad al calor es otro factor de fórmula. El HPMC presenta una propiedad única de gelificación por calor. Forma un gel al calentarse por encima de su punto de enturbiamiento (normalmente entre 70 y 90 °C). El recubrimiento debe mantenerse por debajo de esta temperatura para evitar una gelificación prematura. Esto bloquearía las boquillas de pulverización y provocaría defectos en el recubrimiento.
5. ¿Cuáles son los métodos de procesamiento para el recubrimiento de película de HPMC?
Los fabricantes de medicamentos pueden aplicar recubrimientos de HPMC utilizando agua o métodos con solventes orgánicos. Déjame explicarte Por qué el recubrimiento con agua se ha convertido en el estándar de la industria. Elimina los riesgos de incendio, reduce el impacto ecológico y evita los problemas de solventes residuales. Sin embargo, los sistemas de agua requieren tiempos de secado más largos. Pueden causar problemas de estabilidad con medicamentos sensibles a la humedad.
Los ajustes de pulverización afectan críticamente la calidad del recubrimiento. La velocidad de pulverización debe equilibrar una aplicación rápida con un secado adecuado para evitar imperfecciones. La presión de pulverización determina el tamaño de la gota. Una presión más alta produce gotas más finas que se secan más rápido, pero puede causar mayores pérdidas por secado. La distancia entre la pistola y la base afecta la superposición del patrón de pulverización y el éxito del recubrimiento.
Ajuste de pulverización | Rango típico | Efecto si es demasiado bajo | Efecto si es demasiado alto |
---|---|---|---|
Tasa de pulverización | 5-15 g/min/kg | Proceso lento | Demasiado húmedo, defectos. |
Presión de pulverización | 1,5-3,0 bares | Gotas grandes, recubrimiento irregular | Niebla fina, secado por aspersión |
Presión del aire de patrón | 1,0-2,0 bares | Patrón de pulverización estrecho | Patrón amplio, pérdidas de pared |
Distancia del arma a la cama | 8-12 pulgadas | Demasiado mojado | Secado por aspersión, poco éxito |
Número de pistolas pulverizadoras | 2-12 (según el tamaño) | Tiempo de proceso más largo | Posible sobrehumectación |
Las condiciones de secado afectan considerablemente la calidad de la película. La temperatura del aire de entrada suele oscilar entre 50 y 70 °C. Esto equilibra la velocidad de secado con el riesgo de gelificación por calor. El caudal de aire afecta tanto la potencia de secado como el movimiento de las tabletas dentro de la bandeja de recubrimiento. Un secado insuficiente produce tabletas pegajosas y defectos en el recubrimiento. Un secado excesivo puede provocar la formación prematura de la película y su agrietamiento.
El proceso de recubrimiento consta de varias fases. Una fase inicial de calentamiento lleva las tabletas a la temperatura deseada. La fase de pulverización aplica la solución de recubrimiento a una velocidad determinada. Una fase de curado posterior a la pulverización permite que la película se una completamente y se fortalezca. Este paso de curado, que suele durar entre 15 y 30 minutos a la temperatura de recubrimiento, mejora considerablemente la función y la estabilidad de la película.
La ampliación del laboratorio a la producción presenta varios desafíos. Los cambios en el tamaño del equipo no se reflejan directamente en la configuración del proceso. La relación entre la velocidad de pulverización y la potencia de secado debe mantenerse constante en todas las escalas. La temperatura del lecho de la tableta es un parámetro clave sin incrustaciones. Debe mantenerse constante independientemente del tamaño del lote.
Las herramientas de seguimiento de procesos ayudan a mantener la calidad del recubrimiento. Los sistemas automatizados rastrean factores como la temperatura del lecho de la tableta, la humedad del aire de escape y la presión del recipiente. Las pruebas de infrarrojo cercano pueden proporcionar mediciones del espesor del recubrimiento en tiempo real. Esto permite determinar con precisión el punto final y mantener una calidad constante entre lotes.
6. ¿Cómo se compara el HPMC con otros polímeros de recubrimiento?
Al comparar HPMC con otros tipos de celulosa, aparecen varias diferencias funcionales. La verdad es que La metilcelulosa se disuelve más rápido que la HPMC, pero forma películas más débiles. La etilcelulosa ofrece mayor protección contra la humedad, pero requiere disolventes orgánicos o mezclas especiales de agua. La hidroxipropilcelulosa se adhiere mejor a los núcleos de los comprimidos, pero es más costosa que la HPMC.
El HPMC presenta varias ventajas sobre los polímeros sintéticos. A diferencia de los polimetacrilatos (Eudragit®), el HPMC no requiere pasos de fijación del pH. En comparación con el alcohol polivinílico, el HPMC presenta menores cambios en las propiedades de disolución entre lotes. Además, se procesa con mayor facilidad que el ftalato de acetato de polivinilo, que tiende a obstruir las boquillas de pulverización.
Tipo de polímero | Solubilidad en agua | Resistencia de la película | Complejidad del proceso | Nivel de costo |
---|---|---|---|---|
HPMC | Alto | Medio | Bajo | Bajo |
etilcelulosa | No soluble | Alto | Alto | Medio |
Polimetacrilatos | basado en pH | Alto | De media a alta | Alto |
PVA | Alto | De media a alta | Bajo | Medio |
PVAP | basado en pH | Medio | Medio | De media a alta |
El análisis de costos muestra que el HPMC es una de las opciones de recubrimiento más económicas. El costo de la materia prima es entre 30 y 501 TP3T menor que el de muchas opciones sintéticas. Su sencillo procesamiento reduce los costos de mano de obra y energía. La estabilidad del HPMC permite una mayor vida útil de las soluciones de recubrimiento, lo que reduce el desperdicio. Estos factores hacen del HPMC la opción más económica para muchos usos básicos de recubrimiento.
El estado de aprobación de la HPMC ofrece otra ventaja. Cuenta con la certificación GRAS (Generalmente Reconocido como Seguro) ante la FDA. Aparece en la lista de ingredientes inactivos de muchos medicamentos aprobados. Las normas farmacéuticas europeas, japonesas y de otros países también aceptan la HPMC. Esto facilita la aprobación global de productos.
Las tendencias del mercado muestran un crecimiento continuo en el uso de HPMC. La transición hacia sistemas de recubrimiento con agua favorece al HPMC frente a otras opciones. La flexibilidad del polímero le permite cumplir diversas funciones. Desde el simple enmascaramiento del sabor hasta la liberación modificada compleja, reduce las necesidades de inventario. Los avances recientes incluyen grados especiales con especificaciones de espesor más estrictas para un procesamiento más predecible.
Resumen
El HPMC funciona como un polímero flexible y resistente para el recubrimiento de películas de fármacos, con propiedades comprobadas en múltiples usos. Desde la protección básica contra la humedad hasta sistemas avanzados de liberación controlada, el HPMC ofrece resultados confiables gracias a su estructura química y características físicas únicas. Los fabricantes obtienen beneficios tangibles, como menores costos de materia prima (30-50%) y una vida útil del producto hasta 36 meses más larga. Morton ofrece HPMC de grado farmacéutico, diseñado específicamente para recubrimientos, con soporte técnico para perfeccionar su fórmula y la configuración de su proceso. Contacte hoy mismo con el equipo de polímeros farmacéuticos de Morton para solicitar muestras y documentos técnicos para sus necesidades específicas de recubrimiento.
P1: ¿Se puede utilizar HPMC para aplicaciones de recubrimiento entérico?
La HPMC por sí sola no puede proporcionar una verdadera protección entérica, ya que se disuelve en el líquido estomacal ácido. Sin embargo, se puede modificar la HPMC con grupos ftalato o acetato succinato para crear formas entéricas (HPMCP o HPMCAS). También se puede mezclar la HPMC con polímeros basados en pH, como los polimetacrilatos, en un sistema de subcapa/capa superior. Este método utiliza la HPMC como capa amortiguadora entre el núcleo y el polímero entérico, impidiendo la mezcla directa que podría dañar cualquiera de las partes.
P2: ¿Cuál es el perfil de estabilidad de los recubrimientos de HPMC durante el almacenamiento a largo plazo?
Los recubrimientos de HPMC mantienen su estabilidad física de 3 a 5 años en condiciones normales de almacenamiento (25 °C/60 °F/HR). El polímero presenta una degradación química mínima con el tiempo; estudios muestran una variación de peso molecular inferior a 21 °F/HR después de 36 meses. La sensibilidad a la humedad sigue siendo la principal preocupación, ya que una humedad alta (>75 °F/HR) puede ablandar las películas y reducir su capacidad protectora. Los ciclos de temperatura entre frío y calor pueden causar pequeñas grietas en las películas con una cantidad insuficiente de suavizante. El envasado adecuado en recipientes resistentes a la humedad con agentes secantes prolonga la vida útil del producto recubierto.
P3: ¿Cómo afectan los diferentes grados de espesor de HPMC a las tasas de liberación del fármaco?
Los grados de HPMC de mayor espesor crean capas de gel más gruesas al humedecerse, lo que prolonga los tiempos de liberación del fármaco. Un grado K100M suele ofrecer patrones de liberación de 20 a 24 horas, mientras que los grados K4M suelen ofrecer patrones de 8 a 12 horas para el mismo fármaco. La relación entre el espesor y la velocidad de liberación sigue un patrón logarítmico en lugar de lineal. Duplicar el espesor no duplica el tiempo de liberación. Las tabletas matriciales con K15M pueden liberar 80% de fármaco en 8 horas, mientras que K100M libera solo 50% en el mismo tiempo. Los grados de bajo espesor (E3-E5) se humedecen demasiado rápido para una liberación prolongada, pero son eficaces para una liberación rápida retardada, donde se requiere un tiempo de retardo corto.
P4: ¿Existen consideraciones especiales al recubrir medicamentos sensibles a la humedad con HPMC?
Los medicamentos sensibles a la humedad requieren métodos de recubrimiento con HPMC modificados. Se recomienda presecar los núcleos de los comprimidos hasta alcanzar un contenido de humedad inferior a 1,51 TP3T antes del recubrimiento. El uso de temperaturas de entrada más altas (65-70 °C) y velocidades de pulverización más bajas reduce el tiempo de exposición a la humedad. La adición de componentes que evitan la humedad, como el estearato de magnesio (1-31 TP3T), al recubrimiento reduce el paso del vapor de agua. Algunos fabricantes aplican una capa de un polímero que evita la humedad antes de la capa de HPMC. La solución de recubrimiento debe tener el menor contenido de agua posible, posiblemente utilizando mezclas de alcohol y agua cuando la normativa lo permita. Tras el recubrimiento, el secado rápido y el envasado con agentes secantes protegen aún más los productos sensibles a la humedad.
P5: ¿Cuáles son los enfoques comunes para la solución de problemas de defectos en el recubrimiento de HPMC?
Para el agrietamiento de la película, agregue 5-10% más suavizante o reduzca la temperatura de curado. Corrija los problemas de desprendimiento agregando un agente humectante (0,1-0,5%) para facilitar la adhesión o rugosidad de los núcleos de las tabletas antes del recubrimiento. Corrija la formación de puentes en los logotipos o líneas de rotura de las tabletas reduciendo el espesor de la solución de recubrimiento o aumentando la presión de pulverización para obtener gotas más finas. Corrija el recubrimiento irregular modificando la velocidad del recipiente y los deflectores para facilitar el movimiento del lecho de la tableta. Corrija la textura de cáscara de naranja aumentando la temperatura de la solución para reducir el espesor o reduciendo la velocidad de pulverización. Combata el relleno de logotipos utilizando soluciones más diluidas y una pulverización más fina. En todos los defectos, modificar un factor a la vez ayuda a encontrar la causa raíz sin generar nuevos problemas.