Encontrar el aditivo adecuado para las formulaciones de sus recubrimientos puede marcar una gran diferencia en la calidad del producto. Muchos fabricantes de recubrimientos tienen problemas de mala adhesión y aplicación irregular. Sin los aditivos adecuados, los recubrimientos pueden fallar prematuramente. Esto genera quejas de los clientes y costosas reparaciones.
La HPMC ofrece una solución a estos problemas de recubrimiento. Mejora el flujo, la formación de película y la adherencia. Las pruebas demuestran que una HPMC adecuada puede aumentar la vida útil del recubrimiento hasta en 40% en entornos exigentes.
Veamos cómo funciona este polímero en recubrimientos. Analizaremos sus efectos sobre la fluidez, la formación de película, la adherencia y el bloqueo del agua. También le ayudaremos a elegir el grado adecuado para sus necesidades.
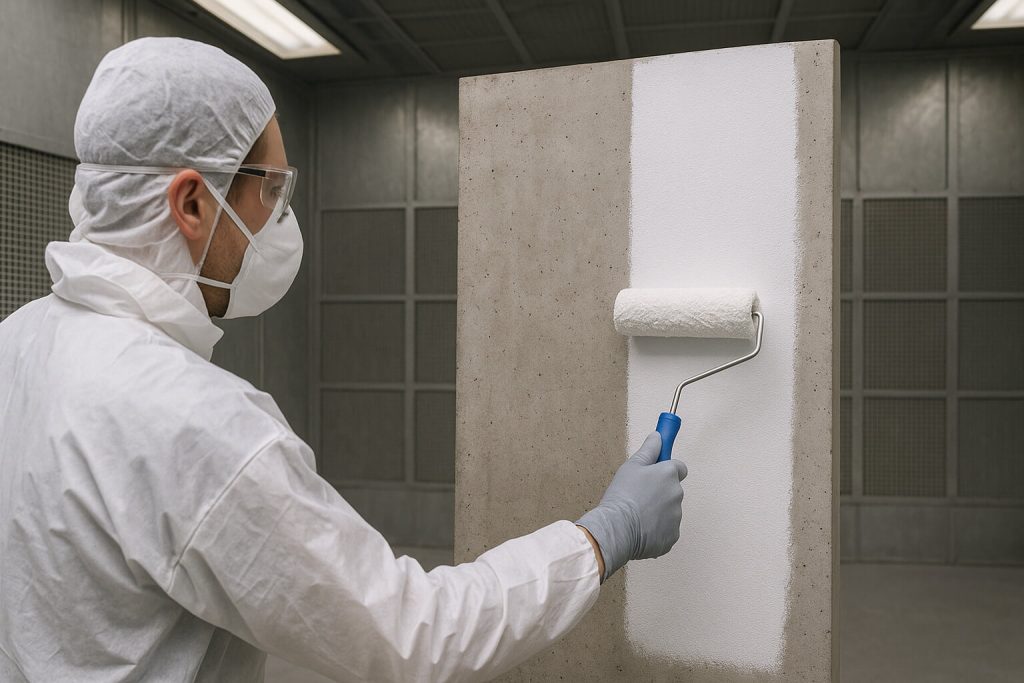
1. ¿Qué es HPMC y por qué se utiliza en recubrimientos?
HPMC significa hidroxipropilmetilcelulosa. Se obtiene a partir de celulosa natural mediante cambios químicos. El material base se trata con dos productos químicos para crear un compuesto útil. ¿Quieres saber qué lo hace especial? Esta estructura única le otorga al polímero una buena capacidad de mezcla con agua y al mismo tiempo forma películas.
Los fabricantes añaden este tipo de celulosa a los recubrimientos principalmente como espesante y aglutinante. Ayuda a controlar la fluidez de los recubrimientos a base de agua, lo que facilita su aplicación y los hace más estables durante el almacenamiento. Las cadenas de polímero forman una red que fija los pigmentos y otros componentes.
Este aditivo funciona bien en pinturas para paredes, revestimientos de hormigón y pegamentos para azulejos. No es tóxico, por lo que es seguro para revestimientos en contacto con alimentos, donde la seguridad es fundamental.
En comparación con otros tipos de celulosa, este polímero ofrece varias ventajas. Se mezcla más fácilmente en agua fría que la metilcelulosa. A diferencia de la CMC, funciona en un rango de pH más amplio.
Propiedad | HPMC | CMC | Metilcelulosa |
---|---|---|---|
Mezcla de agua | Excelente (agua fría) | Bueno (necesita mezclarse) | Bueno (necesita agua caliente) |
Estabilidad del pH | 2-12 | 4-9 | 3-11 |
Película flexible | Alto | Medio | Medio |
Tolerancia a la sal | Bien | Pobre | Medio |
Valor del costo | Medio | Alto | Alto |
El peso de esta celulosa varía entre 10 000 y 1 500 000 unidades. Esto permite a los fabricantes elegir grados con perfiles de flujo específicos. Los grados de menor peso ofrecen una buena humectación. Los grados de mayor peso crean películas más resistentes.
2. ¿Cómo afecta el HPMC a la viscosidad del recubrimiento y a las propiedades de flujo?
Esta celulosa modifica el flujo del recubrimiento mediante un proceso sencillo. Al añadirse al agua, sus moléculas la absorben y se hinchan. Te sorprenderá saber que Este espesamiento se produce sin cambios químicos, lo que facilita la correcta mezcla del aditivo con otros componentes del recubrimiento.
En cantidades bajas (0,1-0,51 TP3T), el polímero proporciona un espesamiento suave. Al añadir más 1-21 TP3T, el espesamiento aumenta considerablemente. Esto crea una mezcla gelatinosa que impide el goteo en las paredes. Esto permite a los fabricantes ajustar con precisión las características del recubrimiento.
El calor juega un papel clave en el funcionamiento de este aditivo. La mayoría de los grados se espesan con el calor hasta que se gelifican. Esto ayuda a que los recubrimientos mantengan su espesor durante el uso en climas cálidos.
Cantidad | Efecto de espesor | Utilice el beneficio |
---|---|---|
0.1-0.5% | Engrosamiento leve | Mejor retención de pigmento |
0.5-1.0% | Espesamiento medio | Mejor flujo y noche. |
1.0-2.0% | Alto espesamiento | Sin goteos en las paredes |
2.0-3.0% | Mezcla gelatinosa | Creación de texturas |
>3.0% | Espesor muy alto | Usos especiales de espesor |
La celulosa previene problemas comunes como el goteo. El polímero mantiene el recubrimiento en su lugar hasta que se aplica fuerza. Esto permite que el recubrimiento fluya bien al usar la brocha o el rodillo, pero que permanezca en su lugar después.
Las características de flujo de estos recubrimientos los hacen ideales para su uso con pistolas. Al aplicar mucha fuerza con las herramientas de pulverización, el espesor disminuye, facilitando la pulverización. Una vez aplicado en la pared, el recubrimiento se endurece rápidamente, evitando que se corra.
Para obtener mejores resultados, mezcle bien el aditivo antes de añadir otros componentes. Mezcle con agua fría antes de calentar para evitar grumos. Algunos fabricantes ofrecen grados especiales que se mezclan más fácilmente.
3. ¿Qué hace que el HPMC sea un agente formador de película eficaz en recubrimientos?
Esta celulosa forma películas mediante secado en lugar de fraguado químico. A medida que el agua sale del recubrimiento, las moléculas se acercan y se unen, creando una película sólida. La parte fascinante es Estas películas se forman sin agentes adhesivos adicionales, lo que simplifica la preparación de mezclas de recubrimiento.
La resistencia de las películas varía según el tamaño de la molécula. Los grados de mayor gramaje producen películas más resistentes y elásticas. La mayoría de las películas se flexionan bien sin aditivos, aunque algunos fabricantes añaden pequeñas cantidades para mejorar esta característica.
La retención de agua durante el secado es una de las características más útiles. El polímero ralentiza la pérdida de agua, lo que permite más tiempo para la uniformidad y la correcta formación de la película. Esto previene imperfecciones causadas por un secado demasiado rápido en climas cálidos o ventosos.
Rasgo cinematográfico | Grados de bajo peso | Grados de peso medio | Calificaciones de alto peso |
---|---|---|---|
Fortaleza | Bajo | Medio | Alto |
Doblar | Alto | Medio | Medio-bajo |
Retención de agua | Bajo | Medio | Alto |
Remezclando | Alto | Medio | Bajo |
Claridad de la película | Alto | Medio | Medio-bajo |
Muchos factores afectan la calidad de estas películas. La humedad del aire durante el uso modifica considerablemente el tiempo de secado. La porosidad de la superficie también es importante: las paredes muy porosas pueden absorber agua con demasiada rapidez. Esto requiere más aditivo para mantener una formación adecuada de la película.
La uniformidad de la película depende de la elección del polímero adecuado. Una cantidad insuficiente puede causar una cobertura desigual. Una cantidad excesiva puede provocar grietas durante el secado. La mayoría de las mezclas de recubrimiento utilizan entre 0,3 y 1,51 TP3T en peso para obtener las mejores características de la película.
Las películas presentan un buen bloqueo de los aceites, a la vez que se mantienen relativamente permeables al agua debido a su naturaleza. Esta propiedad hidrófuga puede ser beneficiosa en aplicaciones donde se requiere la descomposición o la purificación del agua.
4. ¿Cómo mejora el HPMC la adhesión del recubrimiento a diferentes sustratos?
La celulosa facilita la adhesión del recubrimiento de varias maneras a la vez. El polímero se adhiere a las paredes superficiales, creando puntos de anclaje para el recubrimiento. Lo que necesitas saber es Estos enlaces funcionan muy bien en materiales con grupos hidroxilo, como la madera y el hormigón.
En paredes porosas como el hormigón, el aditivo ayuda a controlar la penetración del revestimiento. Impide una penetración excesiva y permite una adhesión firme. Este hundimiento equilibrado permite una mejor cobertura y una adherencia más firme.
El polímero funciona de forma diferente en distintos tipos de pared. En metal, ofrece una adherencia media, principalmente mediante la formación de película. En madera, destaca por su adhesión a las fibras de madera y el control del flujo de humedad.
Tipo de pared | Método del palo | Qué tan bien funciona | Mejor calificación |
---|---|---|---|
Hormigón/Piedra | Control de remojo, unión | Muy alto | Espesor medio-alto |
Madera | Unión de fibras, control de humedad | Alto | Espesor medio |
Metal | Formación de película, barra física | Medio | Espesor bajo-medio |
Vaso | Humectación de la superficie, resistencia de la película | Medio | Bajo espesor |
Plástico | Humectación de superficies, flexión de película | Bajo-Medio | Bajo espesor con extras |
En las mezclas de imprimación, esta celulosa es un excelente auxiliar de adherencia. Ayuda a crear una capa flexible entre la pared y la capa superior. Esta flexibilidad es muy útil en exteriores, donde los cambios de calor provocan el crecimiento y la contracción de la pared.
Las pruebas de adherencia para estos recubrimientos incluyen pruebas de cinta adhesiva y de desprendimiento. La mayoría de los recubrimientos con celulosa adecuada muestran mejores resultados en la prueba de adherencia (20-30%) que las mezclas sin ella.
Para paredes duras como plásticos o metales, mezclar el polímero con adhesivos especiales da mejores resultados. Algunos agentes funcionan bien con él en sistemas de recubrimiento de metales. Otros tipos complementan la celulosa para paredes de plástico.
5. ¿Qué papel juega el HPMC en la resistencia al agua y la durabilidad?
La celulosa contribuye al bloqueo del agua del recubrimiento a través de sus propiedades de película, aunque su efecto es mixto. Aquí está el punto clave: Mientras que el aditivo se mezcla con agua, cuando se mezcla adecuadamente con otros aglutinantes, forma películas que bloquean bien el agua después del secado completo.
Las propiedades de barrera contra la humedad dependen de la composición química. Un mayor contenido de metoxilo produce películas más resistentes al agua. La mayoría de las mezclas de recubrimiento utilizan grados con un contenido de metoxilo entre 19 y 30% para equilibrar el bloqueo del agua con otras propiedades.
La resistencia a largo plazo de estos recubrimientos depende de una mezcla adecuada. Al combinarse con aglutinantes acrílicos o vinílicos, el polímero ayuda a crear recubrimientos que duran de 5 a 7 años en condiciones normales de exterior. La flexibilidad del aditivo reduce el agrietamiento con el tiempo.
Tipo de clima | Efecto sobre el recubrimiento | Impacto en la durabilidad | Método de reparación |
---|---|---|---|
Alta humedad | Secado más lento, puede ablandarse. | Caída media | Utilice grados de metoxilo más altos |
Luz ultravioleta | Pequeño efecto directo sobre el polímero | Bajo impacto | Mezclar con aglutinantes bloqueadores de rayos UV |
Congelación/descongelación | Posible estrés de la película | Caída media | Agregar ayudantes flexibles |
Sal | Pequeño efecto sobre el propio polímero | Bajo impacto | Utilice bloqueadores de óxido para la seguridad de las paredes. |
Lluvia ácida | Posible rotura del polímero | Caída media | Buffer con rellenos básicos |
La resistencia a la intemperie de estos recubrimientos muestra buenos resultados en climas templados. El polímero ayuda a los recubrimientos a resistir el agrietamiento durante los cambios de temperatura al mantener su flexibilidad. Sin embargo, en entornos hostiles, podrían necesitarse más ayudantes.
Equilibrar la mezcla y el bloqueo del agua es un reto clave. Durante el uso, la mezcla con agua proporciona una gran trabajabilidad. Tras el secado, el polímero se integra en un sistema de película completo. Otros aglutinantes proporcionan un bloqueo principal del agua, mientras que la celulosa aumenta la resistencia de la película.
Para usos que requieren impermeabilización superficial, los fabricantes suelen usar la celulosa con aglutinantes o selladores resistentes al agua. Esto mantiene una buena fluidez y formación de película, a la vez que consigue la impermeabilización deseada.
6. ¿Cómo pueden los fabricantes optimizar los grados de HPMC para aplicaciones de recubrimiento específicas?
Para elegir el grado correcto es necesario conocer las especificaciones de flujo y las necesidades de uso. La verdad es que Ese grado de flujo, medido en unidades de mezcla 2%, sirve como el principal factor de selección para la mayoría de los usos de recubrimiento.
Los grados de flujo bajo (3-15 unidades) son ideales para aplicaciones con pistola y recubrimientos finos. Los grados de flujo medio (15-50 unidades) ofrecen buenos resultados en general con brocha y rodillo. Los grados de flujo alto (50-100+ unidades) son excelentes para detener el goteo en las paredes.
La composición química influye considerablemente en los resultados del recubrimiento. El contenido de metoxilo afecta la mezcla con agua y las características de la película. El contenido de hidroxipropilo afecta la acción superficial y la mezcla con otras piezas. La mayoría de los recubrimientos requieren celulosa con un contenido de metoxilo de 19-24% y un contenido de hidroxipropilo de 7-12%.
Tipo de uso | Mejor flujo | La mejor mezcla química | Rasgo clave |
---|---|---|---|
Pintura para paredes interiores | 15-40 unidades | Metoxilo medio, hidroxipropilo medio | Buena trabajabilidad, bajas salpicaduras. |
Revestimiento de piedra exterior | 30-80 unidades | Alto metoxilo, hidroxipropilo medio | Bloqueo del clima, palo |
Mortero para fijar hormigón | 50-100+ unidades | Metoxilo medio, hidroxipropilo alto | Retención de agua, bloqueo de goteo |
Pegamento para azulejos | 40-80 unidades | Metoxilo medio, hidroxipropilo alto | Tiempo abierto, bloqueo de deslizamiento |
Textura en aerosol | 15-30 unidades | Alto metoxilo, bajo hidroxipropilo | Mantenimiento del patrón, bombeabilidad |
Al elegir la celulosa, es importante considerar la mezcla con otros componentes del recubrimiento. El polímero funciona bien con la mayoría de los aglutinantes a base de agua, como los acrílicos y los vinílicos. Sin embargo, las mezclas con mucha carga pueden causar aglomeración en algunos grados.
Los consejos de fabricación incluyen métodos de mezcla adecuados. Para obtener mejores resultados, añada el aditivo a la parte acuosa antes de añadir los pigmentos. Algunos fabricantes ofrecen grados de "mezcla en agua fría" que se humedecen más lentamente. Esto facilita la adición a las mezclas de recubrimiento.
La estabilidad térmica durante el almacenamiento afecta la recolección. Los grados estándar mantienen un flujo estable entre 5 y 40 °C. Sin embargo, existen grados especiales para temperaturas extremas. La mayoría de las mezclas de recubrimiento se benefician de los grados con resultados constantes a lo largo de los cambios de temperatura estacionales.
El valor del costo también influye en la selección del grado. Los grados de mayor flujo suelen costar más por kilo, pero pueden usarse en cantidades menores. Una verificación completa del costo en uso suele mostrar que los grados de flujo medio ofrecen la mejor combinación de resultados y ahorro.
Conclusión
El HPMC mejora los resultados del recubrimiento gracias a sus múltiples propiedades como espesante, formador de película y mejorador de adherencia. Al controlar el flujo, esta celulosa ayuda a crear recubrimientos lisos y uniformes que resisten el goteo y ofrecen una excelente cobertura. Su capacidad para formar película prolonga la vida útil, mientras que su adherencia garantiza una adhesión firme a diversas paredes. Las pruebas demuestran que estos aditivos pueden prolongar la vida útil del recubrimiento en un 25-40% en entornos difíciles. Morton ofrece grados especiales diseñados específicamente para recubrimientos, con asistencia técnica para ayudarle a elegir el grado que mejor se adapte a sus necesidades. Contacte hoy mismo con los expertos en recubrimientos de Morton para solicitar muestras y ayuda con la mezcla para su próximo proyecto de recubrimiento.
Sección de preguntas frecuentes
P1: ¿Qué concentración de HPMC se utiliza normalmente en las formulaciones de recubrimiento?
La mayoría de las mezclas de recubrimientos utilizan esta celulosa en cantidades de entre 0,31 TP₃T y 2,01 TP₃T por peso, según el uso y las características deseadas. Las pinturas para interiores suelen usar entre 0,3 y 0,71 TP₃T, mientras que los recubrimientos texturizados pueden usar hasta entre 1,5 y 2,01 TP₃T para mayor espesor y retención de agua.
P2: ¿Se puede utilizar HPMC tanto en sistemas de recubrimiento a base de agua como a base de solventes?
Este polímero funciona principalmente en sistemas de recubrimiento a base de agua debido a su mezcla con agua. Su mezcla con disolventes orgánicos es muy baja, por lo que no es apto para la mayoría de las mezclas a base de disolventes. Para sistemas con disolventes, otros tipos de celulosa, como la nitrocelulosa, son más recomendables.
P3: ¿Cómo se compara el HPMC con otros éteres de celulosa como el CMC en aplicaciones de recubrimiento?
La HPMC ofrece varias ventajas sobre la CMC en recubrimientos, como una mejor estabilidad del pH, mejor manejo de sales y bloqueo enzimático. Además, proporciona una mejor flexibilidad de la película y una mejor acción superficial. Sin embargo, la CMC puede proporcionar un espesamiento más fuerte a un menor costo en aplicaciones donde estas otras características son menos importantes.
P4: ¿El HPMC afecta el tiempo de secado de los recubrimientos?
Sí, esta celulosa suele prolongar el tiempo de secado de los recubrimientos gracias a su capacidad de retención de agua. Esto puede ayudar a mejorar la uniformidad y evitar imperfecciones causadas por un secado demasiado rápido, especialmente en climas cálidos o secos. El efecto en el tiempo de secado varía según el grado y la cantidad, y los grados de mayor fluidez causan un mayor estiramiento del tiempo de secado.
P5: ¿Existen requisitos especiales de almacenamiento para los recubrimientos que contienen HPMC?
Los recubrimientos con este aditivo deben conservarse entre 5 °C y 40 °C para mantener su estabilidad. Debe evitarse la congelación, ya que puede causar cambios permanentes en la estructura del polímero, lo que podría perjudicar el resultado del recubrimiento. Los envases deben mantenerse cerrados para evitar la formación de costras por pérdida de agua. La mayoría de las mezclas con celulosa bien conservada tienen una vida útil de 12 a 24 meses según estas normas.