Los fabricantes de recubrimientos se enfrentan a graves problemas con la estabilidad del producto y la calidad de la película. Cuando los recubrimientos fallan, se desperdicia dinero en reparaciones. Además, se generan clientes insatisfechos. Los recubrimientos deficientes causan retrasos, mayores costos y perjudican la imagen de marca. La HPMC ofrece una solución mejorando el rendimiento de los recubrimientos. Ayuda a la retención de agua y la formación de película. Las pruebas demuestran que una buena HPMC puede prolongar la vida útil del recubrimiento 40%. También reduce los defectos. Este artículo analiza cómo la HPMC mejora el rendimiento de los recubrimientos en diversas superficies.
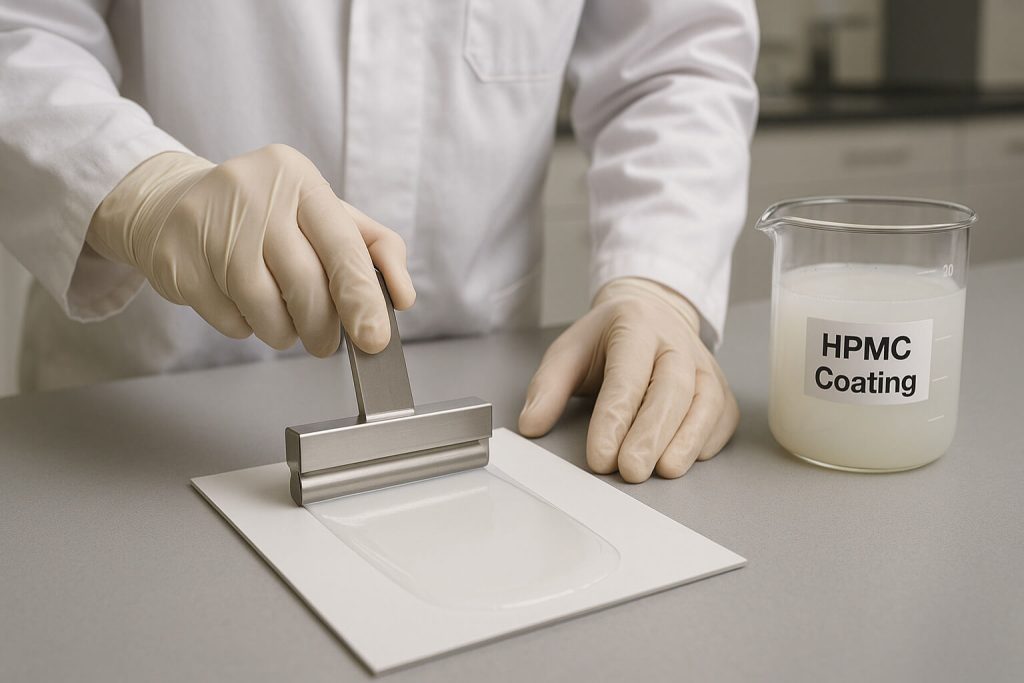
1. ¿Cuáles son las propiedades básicas de la hidroxipropilmetilcelulosa en los recubrimientos?
El HPMC es una fibra vegetal modificada que proviene de árboles. Contiene grupos especiales añadidos a una base de fibra. Esta composición única le confiere sus excelentes propiedades para recubrimientos.
¿Pero qué lo hace tan efectivo? El HPMC se puede mezclar con agua y formar películas. Al añadirse a recubrimientos, el HPMC se descompone en agua a temperatura ambiente. Esto produce una mezcla transparente y sin grumos.
El tamaño del HPMC afecta su rendimiento en recubrimientos. Los tipos más grandes producen mezclas más espesas. Los tipos más pequeños fluyen mejor, pero retienen menos agua.
El HPMC se presenta en diversas formas. El componente metílico suele ser 19-30%. El componente hidroxipropílico es 7-12%. Estas proporciones modifican su comportamiento con el agua y otros componentes del recubrimiento.
Una gran ventaja del HPMC es su capacidad de gelificación por calor. A diferencia de muchos productos que se diluyen al calentarse, las mezclas de HPMC forman geles cortos a mayor temperatura. Esto evita el goteo durante el uso y el secado.
Rasgo | HPMC de bajo espesor | HPMC de espesor medio | HPMC de alto espesor |
---|---|---|---|
Espesor | 5-100 mPa·s | 100-5.000 mPa·s | 5.000-100.000 mPa·s |
Retención de agua | Bajo | Medio | Alto |
Profundidad de la película | Delgado | Medio | Grueso |
Lucha contra el goteo | Bajo | Medio | Alto |
Rasgos suaves | Excelente | Bien | Justo |
El trabajo superficial del HPMC también contribuye al éxito del recubrimiento. Si bien no es un jabón puro, el HPMC reduce ligeramente la tracción superficial. Esto facilita que los recubrimientos se humedezcan mejor las superficies.
Al combinar HPMC con otros tipos de fibra, se observan algunas deficiencias. El HPMC retiene mejor el agua que el MC. Combate mejor los gérmenes que el HEC. También produce películas más flexibles que el CMC.
El tamaño de la partícula del polvo de HPMC afecta su velocidad de descomposición. Los tipos de polvo fino se descomponen más rápido, pero pueden generar más polvo. Los tipos gruesos generan menos polvo, pero requieren más mezcla para descomponerse.
2. ¿Cómo afecta el HPMC a la viscosidad y aplicación del recubrimiento?
La relación entre la cantidad de HPMC y el espesor del recubrimiento sigue un camino claro. A medida que se añade más, el espesor aumenta rápidamente. Esto permite a los fabricantes realizar grandes cambios de espesor con pequeñas variaciones de HPMC.
Aquí está la parte interesante: La HPMC hace que los recubrimientos fluyan de una manera especial. Su espesor disminuye al agitar más rápido. Al aplicar el recubrimiento con una brocha, la agitación lo diluye para facilitar su uso. Una vez aplicado, el recubrimiento se espesa de nuevo para evitar goteos.
El tamaño del tipo HPMC influye directamente en esta característica delgada. Los tipos más grandes muestran mayor intensidad de este efecto. Los tipos más pequeños fluyen con mayor fluidez.
El calor tiene un gran efecto en los recubrimientos HPMC durante su uso. Por debajo del punto de gelificación por calor (a menudo entre 50 y 70 °C), el espesor disminuye a medida que aumenta la temperatura. Por encima de este punto, se forma un gel corto, lo que puede perjudicar el uso del aerosol si las herramientas se calientan demasiado.
Método de uso | El mejor tipo de HPMC | Cantidad típica | Ganancia principal |
---|---|---|---|
Uso en aerosol | Bajo y grueso | 0.1-0.5% | Detiene las obstrucciones y ayuda a rociar. |
Uso del rodillo | De grosor medio | 0.3-0.8% | Reduce el desorden y ayuda a moverse |
Uso del pincel | Grosor medio-alto | 0.5-1.0% | Detiene los goteos y ayuda a recoger |
Recubrimiento por inmersión | De grosor bajo a medio | 0.2-0.6% | Establece la profundidad del pelaje y corta las pasadas. |
Recubrimiento de cortina | De grosor medio | 0.3-0.7% | Mantiene la cortina y ayuda a que el pelaje quede parejo. |
El pH de la mezcla de recubrimiento afecta el funcionamiento del HPMC como espesante. El HPMC mantiene un espesor constante en un rango de pH de 3 a 11. Esto lo hace ideal tanto para recubrimientos ácidos como básicos.
Algunos trucos prácticos para controlar el espesor con HPMC incluyen la premezcla en agua caliente antes de enfriar. Añadir HPMC al agua antes de añadir los colores evita las manchas secas en el recubrimiento final.
Un caso real de un importante fabricante de pinturas demostró que el uso de HPMC redujo los costos en 15%. La mezcla siguió funcionando bien. El recubrimiento de HPMC tuvo mejor rendimiento de arrastre con brocha y generó menos suciedad al usar el rodillo.
La vida útil de los recubrimientos de HPMC depende de un buen control de plagas. Si bien el HPMC por sí mismo combate las plagas, las mezclas de agua con HPMC requieren insecticidas para evitar la pérdida de espesor durante el almacenamiento.
3. ¿Qué papel desempeña el HPMC en la retención de agua de los recubrimientos?
La retención de agua es la característica más útil que el HPMC aporta a las mezclas de recubrimiento. Las partes de la base de fibra forman una red hidrófuga que retiene las partículas de agua. Esta red ralentiza la pérdida de agua durante el secado.
Te sorprendería saber que La retención de agua afecta directamente la calidad del recubrimiento. Cuando un recubrimiento pierde agua demasiado rápido en una superficie porosa como la de un panel de yeso, surgen muchos problemas: mala adherencia, aspecto irregular y corta duración.
La HPMC retiene el agua mediante enlaces entre los fragmentos de agua y los grupos de la fibra. Estos enlaces retienen el agua en la película de recubrimiento. A medida que el recubrimiento se seca, estos enlaces se rompen lentamente, permitiendo la salida del agua de forma constante.
El nivel de cambio del HPMC afecta su capacidad de retención de agua. Un mayor cambio suele significar una mayor retención de agua. El componente metílico afecta la temperatura a la que la fibra empieza a perder su capacidad de retención de agua.
Tipo de base | Ganancia de retención de agua | El mejor tipo de HPMC | Dosis típica |
---|---|---|---|
Muy poroso (hormigón) | Detiene el secado prematuro | Alto y grueso | 0.8-1.2% |
Porosidad media (paneles de yeso) | Establece el flujo de agua | De grosor medio | 0.5-0.9% |
No poroso (metal) | Ayuda a suavizar el tiempo | De grosor bajo a medio | 0.3-0.6% |
Poroso mixto | Hace que la tasa de secado sea uniforme | De grosor medio | 0.5-0.8% |
Estados cálidos y secos | Detiene la formación de piel. | Alto y grueso | 0.7-1.1% |
Entre las formas de evaluar la capacidad de retención de agua se incluye la prueba DIN, que verifica la pérdida de agua al vacío. La prueba ASTM verifica la pérdida de agua a una base sedienta. Ambas pruebas ayudan a los fabricantes a elegir el mejor tipo de HPMC.
Una prueba de campo con revestimientos de paredes demostró que una mayor cantidad de HPMC prolongó el tiempo de trabajo del 40% en condiciones de calor y sequedad. Esto permitió a los usuarios mantener un borde húmedo y evitar marcas durante trabajos grandes.
El efecto de retención de agua del HPMC también ayuda a mantener las partículas de color dispersas durante el secado. Al ralentizar el flujo de agua, el HPMC evita la flotación del color, que puede causar cambios de color.
El tamaño del HPMC está relacionado con su capacidad de retención de agua. Los tipos más grandes forman más redes de unión. Esto retiene más agua en la película de recubrimiento durante el uso y las primeras etapas del secado.
4. ¿Cómo influye el HPMC en la adhesión del recubrimiento a diferentes sustratos?
La adherencia es una característica clave de cualquier recubrimiento, y el HPMC influye significativamente en su adhesión a las bases. La principal vía de adhesión funciona a través de los grupos del HPMC, formando enlaces con las caras de la base. Estos enlaces proporcionan una primera adherencia fuerte durante el uso.
¿Quieres saber algo interesante? El HPMC facilita la adhesión de diferentes maneras según los poros de la base. En bases porosas, el HPMC facilita que el recubrimiento penetre en las imperfecciones de la superficie antes de fraguar. En bases lisas, ralentiza el tiempo de secado, lo que permite una mejor humectación y adherencia.
La diminuta estructura del HPMC presenta componentes hidrófilos y hidrófilos. Esta doble naturaleza le permite actuar como puente entre la resina de recubrimiento y las bases resistentes. Los grupos metilo forman enlaces hidrófilos, mientras que los grupos hidroxilo forman enlaces hidrófilos.
En superficies de concreto y paredes, los recubrimientos HPMC 30-50% muestran una mejor adherencia que los recubrimientos simples. Esta mejora se debe al flujo constante de agua que evita que el recubrimiento se seque demasiado rápido.
Base | Prueba del palo | Cómo ayuda HPMC | Ganancia probada |
---|---|---|---|
Concreto | Muy básico, poroso | Establece el flujo de agua y combate los efectos del pH. | 40-50% mayor resistencia al arranque |
Madera | Poros mixtos, aceites vegetales. | Fija la absorción y bloquea el flujo de aceite vegetal. | 25-35% mejor varilla de trama cruzada |
Metal | Suave, no poroso | Aumenta el tiempo de humedad para una mejor humectación. | 15-25% mejor lucha de impacto directo |
Vaso | Muy suave, amante del agua. | Enlaces polares de UPS | 20-30% mejor resistencia al remojo en agua |
Plástico | Tirón de cara baja | Ayuda a humedecerse mediante el trabajo del jabón. | 30-40% puntuaciones de adherencia de cinta más altas |
Las pruebas para medir la adherencia incluyen pruebas de trama cruzada, pruebas de adherencia por arranque y pruebas de adherencia con cinta. Estos métodos proporcionan información clara sobre cómo el HPMC afecta la resistencia de adhesión del recubrimiento.
El nivel de hidroxipropilo afecta más la adherencia que el componente metílico. Un mayor nivel de hidroxipropilo favorece la adherencia a superficies resistentes al agua, como el vidrio y el metal. Un mayor componente metílico favorece la adherencia a superficies resistentes al agua, como algunos plásticos.
Un estudio de caso con recubrimientos para el mantenimiento en taller demostró que la adición de HPMC a una capa base mejoró la adherencia al acero en 27% tras la prueba de niebla salina. La capa base de HPMC mantuvo mejor la forma bajo la película durante la oxidación.
La flexibilidad de la película de HPMC también aumenta la adherencia a largo plazo. Las películas más flexibles pueden moverse con la base sin agrietarse. Esto es muy útil para recubrimientos exteriores que se someten a ciclos de calor y cambios de temperatura.
5. ¿Cuáles son los beneficios de la formación de películas del HPMC en recubrimientos?
La formación de película es la forma en que un recubrimiento húmedo se transforma en una película sólida. El HPMC desempeña muchas funciones en esta fase clave. Ayuda a regular la tasa de pérdida de agua, lo que permite un secado más uniforme en toda la superficie recubierta.
El punto clave aquí es que El HPMC crea una red de fibras más ordenada durante la formación de la película. A medida que el agua se seca, los fragmentos de HPMC se alinean y forman enlaces entre sí y con el aglutinante principal. Esta forma ordenada reduce los puntos de tensión que podrían provocar grietas.
La eliminación de defectos comunes en la película es una gran ventaja del uso de HPMC. La formación de cráteres, un defecto causado por las grietas en la cara, disminuye con la presencia de HPMC. Las propiedades jabonosas suaves de la fibra ayudan a mantener una cara uniforme durante el secado.
La resistencia a las grietas mejora con el HPMC gracias a su efecto de suavidad. Las piezas flexibles de HPMC se mantienen entre las piezas aglutinantes al unirse, reduciendo la tensión interna. Este efecto de suavidad es temporal en usos exteriores, ya que el HPMC se degrada con el sol con el tiempo.
Rasgo cinematográfico | Sin HPMC | Con el mejor HPMC | Factor de ganancia |
---|---|---|---|
Película Even | Profundidad mixta | Misma profundidad | 2-3 veces más uniforme |
Lucha contra el crack | Medio | Alto | 3-4 veces menos grietas |
Lucha contra Sag | Medio-bajo | Alto | 2× profundidad de tecla |
Pelea de bloqueo temprano | Pobre | Bien | Crecimiento 3 veces más rápido |
Pelea de frotamiento | Medio | Bueno-Genial | Ganancia 30-40% |
El impacto en la dureza del recubrimiento depende del tipo y la cantidad de HPMC. En niveles bajos, el HPMC tiene un efecto mínimo en la dureza final. En niveles altos, puede reducir ligeramente la dureza, mejorando al mismo tiempo la flexibilidad. Esta compensación suele ser beneficiosa para obtener mejores características de uso.
El HPMC afecta el calor de desplazamiento vítreo de la película de recubrimiento final. A menudo lo reduce ligeramente. Esto puede ayudar a combatir las grietas en zonas frías, pero puede reducir la resistencia al bloqueo en zonas calientes. Los fabricantes deben equilibrar estos efectos según el uso previsto del recubrimiento.
La mayor durabilidad de los recubrimientos HPMC se debe a una mejor formación de la película y adherencia de la base. Un estudio de pinturas para exteriores demostró que la adición de HPMC mejoró la resistencia a la intemperie en 25% en pruebas rápidas. La mejor formación de la película reduce las vías de agua que provocan fallas en el recubrimiento.
El aspecto de la película final también se beneficia del HPMC. Al facilitar una distribución más uniforme del color durante el secado, el HPMC mejora el poder cubriente y la uniformidad del color. Este efecto es muy útil en recubrimientos para el hogar, donde la estética es fundamental.
6. ¿Cómo afectan los diferentes grados de HPMC la estabilidad y la vida útil del recubrimiento?
La vida útil es una gran preocupación para los fabricantes de recubrimientos. El HPMC prolonga su vida útil de muchas maneras. En primer lugar, su efecto espeso mantiene los colores y rellenos adheridos. Esto evita el hundimiento duro que puede inutilizar los productos después del almacenamiento.
Lo que mucha gente no sabe es que El HPMC forma un gel débil en reposo. Esta forma proporciona el valor de fluencia, la fuerza necesaria para que el recubrimiento comience a fluir. Un valor de fluencia más alto impide que la broca se mueva durante el almacenamiento sin afectar su rendimiento una vez aplicada la cizalladura.
La eliminación de la separación por agua es otra ventaja. La capacidad de unión por agua de HPMC elimina el agua libre que podría separarse durante el almacenamiento. Esto mantiene el recubrimiento bien mezclado y listo para usar sin necesidad de mezclarlo durante mucho tiempo.
Los diferentes tipos de HPMC ofrecen diversas características de vida. Los de mayor grosor ofrecen mejor suspensión, pero pueden atrapar aire. Los de menor grosor permiten una mejor salida del aire, pero pueden requerir más ayudantes para una mayor durabilidad.
Control de vida | HPMC de bajo espesor | HPMC de espesor medio | HPMC de alto espesor |
---|---|---|---|
Control del fregadero | Justo | Bien | Excelente |
Parada de división de agua | Justo | Bien | Excelente |
Vida congelada y descongelada | Bien | Muy bien | Excelente |
Vida útil del calor (50 °C) | Excelente | Bien | Justo |
Salida de aire | Excelente | Bien | Justo |
El impacto en la vida útil de los recubrimientos a base de agua durante el ciclo de congelación es muy útil. El HPMC reduce la formación de hielo durante la congelación al retener los trozos de agua. Esto previene el daño a la mezcla que se produce cuando se forman grandes trozos de hielo.
Un estudio de vida útil de pinturas de látex demostró que la adición de HPMC aumentó la resistencia al ciclo de congelación-descongelación de 3 a 5 ciclos. La pintura HPMC mantuvo un buen espesor y propiedades de uso después de numerosos ciclos de calor.
La vida útil del HPMC en pH ayuda a mantener características estables durante el almacenamiento. A diferencia de algunos espesantes artificiales que pierden su eficacia con la variación del pH, el HPMC mantiene su eficacia en un rango de pH de 3 a 11. Esto lo hace ideal para recubrimientos tanto ácidos como básicos.
La conservación a largo plazo de las propiedades de los productos de recubrimiento almacenados depende de la correcta selección de HPMC. Para maximizar su vida útil, los fabricantes deben elegir tipos de HPMC con buena resistencia a los insectos. Algunos tipos reciben un cuidado especial para combatir la rotura por insectos que podría causar pérdidas de espesor.
Conclusión
La HPMC ofrece numerosas ventajas que mejoran el rendimiento y las características de uso del recubrimiento. Desde un mejor control del espesor y la retención de agua hasta una mayor adherencia y formación de película, la HPMC resuelve problemas clave que enfrentan fabricantes y usuarios de recubrimientos. Al elegir el tipo y la cantidad de HPMC adecuados, puede reducir los defectos hasta en un 40%. También puede prolongar el tiempo de trabajo en condiciones difíciles. Contacte con Morton hoy mismo para solicitar una punta de HPMC personalizada para su recubrimiento. Nuestro equipo técnico puede ayudarle a elegir el mejor tipo para alcanzar sus objetivos de trabajo y mejorar sus resultados.
P1: ¿Qué concentración de HPMC se utiliza normalmente en las formulaciones de recubrimiento?
La mayoría de las mezclas de recubrimiento utilizan cantidades de HPMC entre 0,11 TP³T y 1,21 TP³T por peso. Esto varía según el método de uso y las características deseadas. Para aplicaciones con pistola, se necesitan de 0,1 a 0,51 TP³T, para aplicaciones con rodillo, de 0,3 a 0,81 TP³T y para aplicaciones con brocha, de 0,5 a 1,01 TP³T. La cantidad exacta depende del espesor del HPMC, el tipo de recubrimiento y la base. Cantidades mayores ofrecen mayor retención de agua y resistencia al descolgamiento, pero pueden afectar el aspecto liso y el acabado final.
P2: ¿Se puede combinar HPMC con otros aditivos en formulaciones de recubrimiento?
Sí, el HPMC funciona bien con la mayoría de los aditivos de recubrimiento comunes. Muestra una buena mezcla con aglutinantes acrílicos, vinílicos y de estireno-acrílicos. El HPMC puede funcionar con espesantes sintéticos como HEUR y HASE para un mejor control del flujo. También funciona bien con aditivos de flujo, detención de espuma y aditivos de humedad cuando se añade en el orden correcto. El punto principal es añadir el HPMC a la parte acuosa antes de añadir colores y otros sólidos para evitar grumos y una descomposición deficiente.
P3: ¿Cómo se compara el HPMC con otros espesantes en aplicaciones de recubrimiento?
El HPMC ofrece una combinación única de propiedades en comparación con otros espesantes. A diferencia de los espesantes sintéticos, el HPMC ofrece una excelente retención de agua y es menos sensible a los cambios de mezcla. En comparación con otros tipos de plantas, el HPMC ofrece mejor rendimiento superficial que el CMC y mejor control de plagas que el HEC. El HPMC ofrece una mayor fluidez que los poliacrilatos, lo que proporciona una mejor resistencia al descolgamiento después del uso. Si bien los espesantes sintéticos pueden funcionar mejor a baja cizalladura, el HPMC ofrece un rendimiento general superior en muchas propiedades de recubrimiento.
P4: ¿El HPMC afecta el tiempo de secado de los recubrimientos a base de agua?
Sí, el HPMC suele prolongar el tiempo de secado de los recubrimientos a base de agua, pero el efecto varía según la base y el estado. En bases porosas, el efecto de retención de agua puede acelerar el tiempo de secado real. Impide una absorción de agua demasiado rápida que dejaría el aglutinante en la superficie. En bases no porosas, el HPMC prolonga el tiempo de apertura (15-40%) según el tipo y la cantidad. Este mayor tiempo de apertura suele ayudar a obtener un aspecto más liso y a evitar marcas de solape, sobre todo en climas cálidos o ventosos.
P5: ¿Existen limitaciones al utilizar HPMC en aplicaciones de recubrimiento?
Si bien el HPMC ofrece muchas ventajas, tiene algunas limitaciones. Una cantidad elevada puede reducir el brillo en algunas mezclas debido a la mancha de la fibra en la cara. El HPMC puede reducir ligeramente la resistencia al agua en los primeros pasos después del uso, aunque este efecto disminuye al secarse completamente el recubrimiento. En exteriores, el HPMC se degrada lentamente con la luz solar, por lo que sus efectos sobre la flexibilidad son a corto plazo. Algunos tipos pueden formar espuma, lo que requiere ajustes en los niveles de espuma. Estos límites se pueden solucionar mediante ajustes adecuados de la mezcla de tipos.