La hidroxipropilmetilcelulosa (HPMC) es un polímero versátil con aplicaciones en las industrias de la construcción, farmacéutica, alimentaria y del cuidado personal. Para los gerentes de compras y los responsables de la toma de decisiones técnicas, comprender los parámetros óptimos para la implementación de HPMC puede tener un impacto significativo en la calidad y la rentabilidad del producto. Este artículo proporciona directrices técnicas completas para el uso de HPMC en diversas aplicaciones, abordando desafíos comunes y ofreciendo soluciones prácticas. Siguiendo estas recomendaciones basadas en la evidencia, adquirirá los conocimientos necesarios para seleccionar los grados adecuados, optimizar las condiciones de procesamiento y solucionar problemas comunes, mejorando así el rendimiento y la eficiencia operativa de su producto.
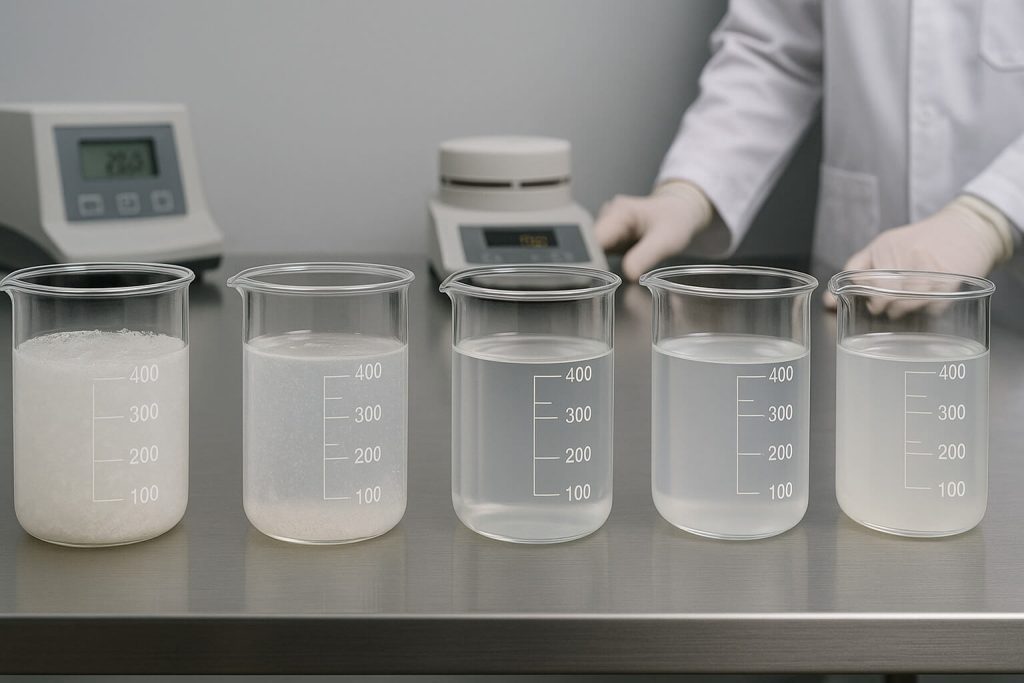
1. ¿Cuáles son las propiedades clave de la hidroxipropilmetilcelulosa (HPMC)?
El HPMC es un éter de celulosa semisintético y no iónico derivado de la celulosa mediante modificación química. Su estructura única consiste en una cadena principal de celulosa con sustituyentes hidroxipropilo y metilo, que determinan sus características funcionales. El grado de sustitución (DS) y la sustitución molar (MS) son parámetros críticos que influyen en su rendimiento en diversas aplicaciones.
Esto es lo que hace que HPMC sea realmente valioso: El polímero exhibe una notable versatilidad gracias a su capacidad para formar soluciones viscosas en agua fría, a la vez que presenta gelificación térmica a temperaturas elevadas. Esta respuesta térmica lo hace especialmente útil en formulaciones de liberación controlada y materiales de construcción.
El HPMC está disponible en varios grados de viscosidad, que suelen oscilar entre 3 y 100 000 mPa·s (medido como una solución de 2% a 20 °C). La viscosidad se correlaciona directamente con el peso molecular, y los grados de mayor peso molecular producen soluciones más viscosas. Esta propiedad permite a los formuladores seleccionar grados específicos según los requisitos de la aplicación.
El perfil de solubilidad del HPMC presenta otra característica clave. Se disuelve fácilmente en agua fría, formando soluciones transparentes, pero presenta una solubilidad limitada en agua caliente. Esta solubilidad, dependiente de la temperatura, se debe a la interacción hidrofóbica entre los grupos metoxi a temperaturas elevadas, lo que provoca la precipitación o gelificación.
Propiedad | Rango | Impacto de la aplicación |
---|---|---|
Viscosidad | 3-100.000 mPa·s | Controla las propiedades del flujo, la estabilidad y el espesor de la película. |
Contenido de metoxilo | 19-30% | Afecta la solubilidad en agua y la temperatura de gelificación térmica. |
Contenido de hidroxipropilo | 4-12% | Influye en la actividad superficial y la solubilidad orgánica. |
Tamaño de partícula | 20-150 micras | Determina la tasa de disolución y la calidad de la dispersión. |
Temperatura del gel | 50-90°C | Crítico para aplicaciones con respuesta térmica |
Las características físicas de manejo del HPMC incluyen su apariencia de polvo blanco a blanquecino con buenas propiedades de flujo. El material es higroscópico, por lo que requiere condiciones de almacenamiento adecuadas para evitar la absorción de humedad, lo cual puede provocar grumos y reducir su funcionalidad.
2. ¿Cómo funciona el HPMC en aplicaciones de construcción?
Los materiales de construcción representan uno de los sectores de aplicación más importantes del HPMC. En sistemas a base de cemento, el HPMC actúa principalmente como agente de retención de agua, impidiendo su rápida pérdida a sustratos porosos o por evaporación. Esta función es crucial para la correcta hidratación del cemento y el desarrollo de su resistencia.
Pero eso no es todo lo que necesitas saber. El mecanismo de retención de agua implica la formación de una red polimérica que atrapa físicamente las moléculas de agua y las libera gradualmente durante el proceso de curado. Esta liberación controlada de agua garantiza la hidratación completa del cemento, lo que reduce el riesgo de grietas por retracción y mejora la durabilidad general.
En morteros y revoques, el HPMC mejora significativamente la trabajabilidad al lubricar las partículas de áridos. Esta mayor trabajabilidad se traduce en una aplicación más sencilla, menores costes de mano de obra y un mejor acabado superficial. El mayor tiempo abierto que proporciona el HPMC permite realizar ajustes durante la aplicación, lo cual es especialmente valioso en adhesivos para baldosas, donde la flexibilidad de posicionamiento es esencial.
Función HPMC | Beneficio en la construcción | Dosis recomendada |
---|---|---|
Retención de agua | Previene el secado prematuro, asegura una hidratación completa. | 0,1-0,5% por peso |
Mejora de la trabajabilidad | Mejora la facilidad de aplicación y el acabado de la superficie. | 0,05-0,3% por peso |
Promoción de la adhesión | Aumenta la fuerza de adhesión a los sustratos. | 0,2-0,6% por peso |
Resistencia al hundimiento | Evita el deslizamiento de los materiales recién aplicados. | 0,1-0,4% por peso |
Arrastre de aire | Mejora la resistencia a la congelación y descongelación. | 0,05-0,2% por peso |
El mecanismo de mejora de la adhesión del HPMC implica la formación de enlaces de hidrógeno entre el polímero, el sustrato y los materiales cementicios. Esta interacción aumenta la resistencia de la unión, lo cual es especialmente importante en adhesivos para baldosas y revocos. El HPMC también influye en el tiempo de fraguado al formar una película protectora alrededor de las partículas de cemento, lo que retarda ligeramente las reacciones de hidratación y garantiza un desarrollo de la resistencia más uniforme.
Al formular con HPMC, se debe considerar la compatibilidad con otros aditivos de construcción. Generalmente, funciona sinérgicamente con agentes inclusores de aire, polvos poliméricos redispersables y cargas minerales. Sin embargo, las interacciones con algunos superplastificantes y aceleradores pueden requerir optimización para lograr el rendimiento deseado.
3. ¿Qué parámetros técnicos se deben controlar al utilizar HPMC en productos farmacéuticos?
Las aplicaciones farmacéuticas exigen un control preciso de los parámetros de HPMC para garantizar una administración uniforme del fármaco. El grado de sustitución influye significativamente en los perfiles de liberación del fármaco, ya que un mayor contenido de metoxilo suele resultar en velocidades de liberación más lentas debido a una mayor hidrofobicidad y resistencia del gel.
¿Quieres saber el secreto de una formulación exitosa? La selección de la viscosidad representa quizás la decisión más crítica en aplicaciones farmacéuticas. Los grados de baja viscosidad (3-100 mPa·s) son los preferidos para formulaciones de liberación inmediata y recubrimientos peliculares, mientras que los grados de viscosidad media a alta (4000-100 000 mPa·s) son esenciales para sistemas matriciales de liberación controlada.
El mecanismo de control de la velocidad de disolución de la HPMC implica la formación de una capa de gel alrededor de la forma farmacéutica al entrar en contacto con un medio acuoso. Esta capa de gel actúa como barrera de difusión, controlando la liberación del fármaco mediante una combinación de procesos de difusión y erosión. El equilibrio entre estos mecanismos puede ajustarse mediante la selección de los grados y concentraciones de HPMC adecuados.
Parámetro | Publicación inmediata | Liberación controlada | Versión extendida |
---|---|---|---|
Viscosidad de HPMC | 3-100 mPa·s | 100-4.000 mPa·s | 4.000-100.000 mPa·s |
Contenido de metoxilo | 19-24% | 22-30% | 28-30% |
Contenido de hidroxipropilo | 7-12% | 4-12% | 4-7% |
Concentración típica | 2-5% | 10-30% | 20-40% |
Impacto del medio de disolución | Mínimo | Moderado | Significativo |
Al desarrollar formulaciones farmacéuticas basadas en HPMC, es necesario evaluar la estabilidad en diversos entornos de pH. Si bien el HPMC es estable en un amplio rango de pH (3-11), su interacción con los fármacos puede variar según las condiciones de pH. Esto puede afectar la cinética de liberación, especialmente en el caso de fármacos ionizables, cuya solubilidad varía con el pH.
El cumplimiento normativo es otro aspecto crucial del uso de HPMC en la industria farmacéutica. El material debe cumplir con las especificaciones de la farmacopea, incluyendo las monografías de la USP, la Ph.Eur. y la JP. Estas especificaciones abarcan parámetros como el grado de sustitución, la viscosidad, el contenido de metales pesados y los límites microbianos. Los fabricantes deben mantener la documentación y los protocolos de prueba adecuados para garantizar el cumplimiento.
4. ¿Cómo se puede optimizar el rendimiento de HPMC en productos alimenticios?
Las aplicaciones alimentarias aprovechan las propiedades únicas del HPMC para la modificación de textura, la estabilización y el recubrimiento. Su capacidad de formación de película lo hace especialmente valioso en aplicaciones de recubrimiento, donde proporciona barreras contra la humedad y el oxígeno, y una mejor apariencia.
La verdadera ventaja viene de entender esto: Los mecanismos de estabilización del HPMC en emulsiones y suspensiones implican tanto la mejora de la viscosidad como la actividad interfacial. El polímero se adsorbe en las interfaces aceite-agua, reduciendo la tensión interfacial y proporcionando un impedimento estérico contra la coalescencia de gotas. Esta doble funcionalidad lo hace más eficaz que muchos otros hidrocoloides en la estabilización de sistemas alimentarios complejos.
El comportamiento dependiente de la temperatura en los sistemas alimentarios presenta tanto desafíos como oportunidades. La propiedad de gelificación térmica puede aprovecharse para generar cambios de textura durante la cocción, especialmente útil en productos horneados y fritos, donde la HPMC forma una barrera que reduce la absorción de aceite y la pérdida de humedad.
Solicitud | Función HPMC | Grado recomendado | Nivel de uso |
---|---|---|---|
Productos horneados | Retención de humedad, volumen mejorado. | Viscosidad media, alto metoxilo | 0.5-2.0% |
Alimentos fritos | Barrera de aceite, retención de humedad. | Alta viscosidad, alto metoxilo | 1.0-3.0% |
Salsas y aderezos | Estabilización, textura | Viscosidad media-baja | 0.3-1.0% |
Proteínas de origen vegetal | Encuadernación, mejora de la textura | Viscosidad media | 0.5-2.0% |
Productos sin gluten | Edificio de estructura | Alta viscosidad | 1.0-3.0% |
Los efectos sinérgicos con otros hidrocoloides pueden mejorar la funcionalidad general. El HPMC funciona especialmente bien con la goma xantana, mejorando la estabilidad y la textura de la suspensión. Las combinaciones con pectina o carragenina pueden crear perfiles de textura únicos que no se pueden lograr con hidrocoloides individuales. Estas combinaciones sinérgicas suelen permitir un uso reducido del hidrocoloide, lo que potencialmente reduce los costos de formulación.
Las consideraciones de etiquetado limpio han cobrado cada vez mayor importancia en las aplicaciones alimentarias. Si bien la HPMC no se considera "natural" según la mayoría de los estándares, su origen vegetal y su amplio historial de uso seguro la hacen más aceptable que muchos aditivos sintéticos. Los fabricantes deben considerar la percepción del consumidor y los requisitos regulatorios al comercializar productos que contienen HPMC.
5. ¿Cuáles son las mejores técnicas de procesamiento para la integración de HPMC?
Una dispersión adecuada es fundamental para una integración exitosa de HPMC. El material tiende a formar grumos al añadirse directamente al agua debido a la rápida hidratación superficial, que crea una barrera de gel que impide su disolución completa. Para superar este desafío, se pueden emplear diversas técnicas de dispersión.
Aquí es donde muchos fabricantes se equivocan: Añadir HPMC directamente al agua fría sin una dispersión adecuada suele provocar la formación de ojos de pescado y una hidratación incompleta. En cambio, la técnica "caliente/fría" resulta más eficaz para muchas aplicaciones. Esta consiste en dispersar el HPMC en agua caliente (por encima de 80 °C), donde permanece insoluble, y luego enfriarlo para permitir su completa disolución.
El control de la temperatura durante la incorporación influye significativamente en la calidad de la solución final. En el método de calor/frío, la temperatura inicial del agua debe superar el punto de gel (normalmente 80-90 °C) para evitar una hidratación prematura. La velocidad de enfriamiento debe controlarse para asegurar una hidratación uniforme, manteniendo una agitación moderada durante todo el proceso.
Método de dispersión | Ventajas | Limitaciones | Mejor para |
---|---|---|---|
Técnica de calor/frío | Hidratación completa, mínima formación de grumos. | Requiere mucho tiempo y energía | Aplicaciones farmacéuticas y alimentarias |
Mezcla en seco | Proceso sencillo, sin equipo especial. | Es posible que no se active completamente el HPMC | Construcción, soluciones de baja viscosidad |
Mezcla de alto cizallamiento | Dispersión rápida, eficiente | Costo del equipo, posible incorporación de aire | Procesos industriales, grandes volúmenes |
Método de suspensión | Buena dispersión en sistemas no acuosos. | Requiere manipulación de disolventes orgánicos. | Recubrimientos, sistemas orgánicos |
Ajuste del pH | Tasa de disolución mejorada | Limitado a aplicaciones tolerantes al pH | Aplicaciones especializadas |
Los parámetros de mezcla para una hidratación óptima incluyen la velocidad de cizallamiento y la duración. La dispersión inicial se beneficia de un alto cizallamiento para desintegrar los aglomerados, mientras que la fase de hidratación requiere una agitación moderada para evitar la incorporación de aire y asegurar una distribución uniforme. Los tiempos de hidratación típicos varían de 30 minutos para materiales de baja viscosidad a varias horas para materiales de alta viscosidad.
Las consideraciones de escalado, desde el laboratorio hasta la producción, requieren una atención cuidadosa a la geometría de la mezcla, la distribución del esfuerzo cortante y el control de la temperatura. Se recomienda encarecidamente realizar pruebas piloto antes de la implementación completa de la producción. Los parámetros clave que deben monitorearse durante el escalado incluyen el tiempo de disolución, la claridad de la solución, el desarrollo de la viscosidad y la homogeneidad de la solución final.
La solución de problemas comunes de procesamiento suele centrarse en la hidratación incompleta, que se manifiesta como partículas de gel transparentes u "ojos de pescado" en la solución final. Esto se puede solucionar mejorando la dispersión inicial, aumentando el tiempo de hidratación o ajustando la técnica de dispersión. Otros problemas comunes incluyen las variaciones de viscosidad, que pueden deberse a propiedades inconsistentes de la materia prima o a las condiciones de procesamiento.
6. ¿Cómo afectan los factores ambientales la funcionalidad de HPMC?
Las condiciones ambientales pueden afectar significativamente el rendimiento del HPMC en diversas aplicaciones. La humedad es una preocupación fundamental tanto para la materia prima como para el producto terminado. Al ser un material higroscópico, el HPMC absorbe la humedad del ambiente, lo que puede provocar la formación de grumos durante el almacenamiento y la manipulación.
Quizás te sorprenda saber que Una humedad relativa superior a 651 TP3T puede causar cambios significativos en las propiedades del polvo de HPMC, lo que afecta las características de flujo y el comportamiento de dispersión. En productos terminados, los entornos con alta humedad pueden acelerar la absorción de humedad en las películas de HPMC, lo que podría comprometer las propiedades de barrera o las funciones de liberación controlada.
Los efectos de la temperatura sobre las propiedades de la solución siguen un patrón distintivo. Las soluciones de HPMC presentan una disminución de la viscosidad al aumentar la temperatura hasta el punto de gelificación, tras el cual se produce la gelificación térmica. Este comportamiento debe tenerse en cuenta durante el procesamiento, el almacenamiento y la aplicación, especialmente en productos sensibles a la temperatura.
Factor ambiental | Impacto en HPMC | Estrategia de mitigación |
---|---|---|
Alta humedad (>65% RH) | Absorción de humedad, formación de grumos | Contenedores sellados, desecantes, control de clima. |
Baja humedad (<30% RH) | Acumulación de carga estática, problemas de manipulación | Medidas antiestáticas, control de humedad. |
Alta temperatura (>80 °C) | Gelificación térmica, pérdida de viscosidad | Monitoreo de temperatura, sistemas de refrigeración |
Baja temperatura (<5°C) | Hidratación más lenta, mayor viscosidad. | Tiempo de mezcla extendido, ajuste de temperatura. |
Exposición a la luz ultravioleta | Efecto directo mínimo, oxidación potencial. | Envases opacos, antioxidantes. |
La sensibilidad al pH y las interacciones del sistema tampón deben considerarse en las formulaciones. Si bien la HPMC mantiene la estabilidad en un amplio rango de pH (3-11), las condiciones extremas de pH pueden afectar la velocidad de hidratación y las propiedades de la solución. En aplicaciones farmacéuticas, los componentes del tampón pueden interactuar con la HPMC, lo que podría alterar la cinética de liberación del fármaco o la estabilidad de la solución.
Las consideraciones sobre la exposición a la luz y al oxígeno se relacionan principalmente con la posible degradación oxidativa durante períodos prolongados. Si bien la HPMC presenta una buena estabilidad, la oxidación puede provocar la escisión de la cadena y una reducción del peso molecular, lo que se manifiesta en una disminución de la viscosidad de la solución. Este efecto se acentúa en presencia de ciertos iones metálicos o agentes oxidantes.
Las recomendaciones de almacenamiento para mantener la calidad incluyen conservar el HPMC en recipientes sellados en un lugar fresco y seco (idealmente a menos de 30 °C y con una humedad relativa de 60%). El material debe protegerse de la luz solar directa y almacenarse lejos de agentes oxidantes fuertes. En condiciones adecuadas de almacenamiento, el HPMC suele mantener su funcionalidad durante al menos dos años a partir de su fecha de fabricación.
Conclusión
Dominar los parámetros técnicos de la hidroxipropilmetilcelulosa ofrece beneficios sustanciales en diversas industrias. Al seleccionar los grados adecuados, optimizar las condiciones de procesamiento y comprender las influencias ambientales, puede lograr una mejora de hasta 30% en el rendimiento del producto, a la vez que reduce potencialmente los costos de formulación entre 15 y 20%. El equipo de soporte técnico de Morton ofrece servicios de consultoría especializados para ayudarle a implementar estas directrices eficazmente en sus aplicaciones específicas. Colabore con nuestros expertos para desarrollar soluciones HPMC personalizadas que aborden sus desafíos específicos e impulsen la innovación en sus iniciativas de desarrollo de productos.
Sección de preguntas frecuentes
P1: ¿Cuál es la diferencia entre HPMC y otros derivados de celulosa?
La HPMC se diferencia de otros derivados de celulosa principalmente en su patrón de sustitución y las propiedades resultantes. A diferencia de la metilcelulosa (MC), la HPMC contiene grupos hidroxipropilo que aumentan la solubilidad orgánica y reducen la temperatura de gelificación térmica. En comparación con la carboximetilcelulosa (CMC), la HPMC es no iónica y menos sensible a los electrolitos. La hidroxietilcelulosa (HEC) carece de la sustitución de metilo de la HPMC, lo que resulta en diferentes perfiles de solubilidad y ausencia de gelificación térmica. Estas características hacen que la HPMC sea especialmente valiosa en aplicaciones que requieren un comportamiento termosensible y estabilidad en diversas condiciones de pH.
P2: ¿Cómo se determina el grado de HPMC óptimo para aplicaciones específicas?
Seleccionar el grado óptimo de HPMC requiere evaluar varios parámetros según los requisitos de la aplicación. Primero, determine la viscosidad necesaria según las propiedades de flujo, la estabilidad o el perfil de liberación deseados. A continuación, considere el contenido de metoxilo e hidroxipropilo según las características de solubilidad requeridas y la temperatura de gelificación térmica. Para aplicaciones farmacéuticas, el cumplimiento normativo con monografías de farmacopeas específicas puede limitar las opciones disponibles. Finalmente, realice pruebas de aplicación con múltiples grados para evaluar el rendimiento en condiciones reales de uso, ya que las predicciones teóricas pueden no reflejar todos los efectos de interacción en formulaciones complejas.
P3: ¿Se puede utilizar HPMC en combinación con otros polímeros?
El HPMC funciona eficazmente en combinación con numerosos polímeros, produciendo a menudo efectos sinérgicos. En aplicaciones farmacéuticas, las combinaciones con polivinilpirrolidona (PVP) u óxido de polietileno (PEO) pueden optimizar los perfiles de liberación de fármacos. En materiales de construcción, el HPMC se combina bien con polvos poliméricos redispersables para mejorar la flexibilidad y la adhesión. En sistemas alimentarios, las combinaciones con goma xantana o carragenina crean perfiles de textura únicos. Al formular combinaciones de polímeros, comience con pruebas de compatibilidad a pequeña escala para identificar posibles interacciones y, a continuación, optimice las proporciones mediante la evaluación sistemática de los parámetros clave de rendimiento.
P4: ¿Qué pruebas de control de calidad son esenciales para la evaluación de HPMC?
Las pruebas esenciales de control de calidad para HPMC incluyen la medición de la viscosidad (mediante viscosímetros rotacionales a concentraciones y temperaturas definidas), la determinación del grado de sustitución (normalmente mediante cromatografía de gases tras la derivatización), la distribución del tamaño de partícula (mediante difracción láser o análisis granulométrico), el contenido de humedad (mediante pérdida por secado) y la medición de la temperatura del gel (mediante punto de enturbiamiento o métodos reológicos). Para los grados farmacéuticos, se realizan pruebas adicionales que incluyen el contenido de metales pesados, los disolventes residuales y los límites microbianos, según los requisitos de la farmacopea. El establecimiento de rangos de especificación para estos parámetros garantiza la consistencia entre lotes y el rendimiento de la aplicación.
P5: ¿Cómo afecta el proceso de fabricación al rendimiento de HPMC?
El proceso de fabricación influye significativamente en el rendimiento de la HPMC a través de diversos mecanismos. Las condiciones de alcalinización durante la producción afectan la distribución de los sustituyentes a lo largo de la cadena de celulosa, lo que influye en las propiedades de la solución y el comportamiento térmico. El grado de polimerización de la celulosa de partida determina el rango de peso molecular del producto final, lo que afecta directamente la viscosidad de la solución. Las etapas de purificación influyen en el contenido de reactivos residuales y subproductos, lo que puede afectar la estabilidad y la compatibilidad. Los fabricantes pueden adaptar estos parámetros del proceso para producir grados con características de rendimiento específicas, lo que hace que la comprensión del proceso sea crucial tanto para los productores como para los usuarios finales de HPMC.