When working with Hydroxypropyl Methyl Cellulose (HPMC), achieving the correct dissolution is essential for ensuring the desired properties in various applications such as construction, pharmaceuticals, and food. Proper solubility directly impacts the quality and functionality of the final product, whether you’re creating adhesives, pharmaceutical tablets, or emulsifiers for food products. This article will delve into the factors influencing HPMC solubility, best practices for dissolving it, and how to avoid common mistakes. By understanding these key aspects, you can ensure that your HPMC is dissolved effectively to achieve the highest performance in your applications.
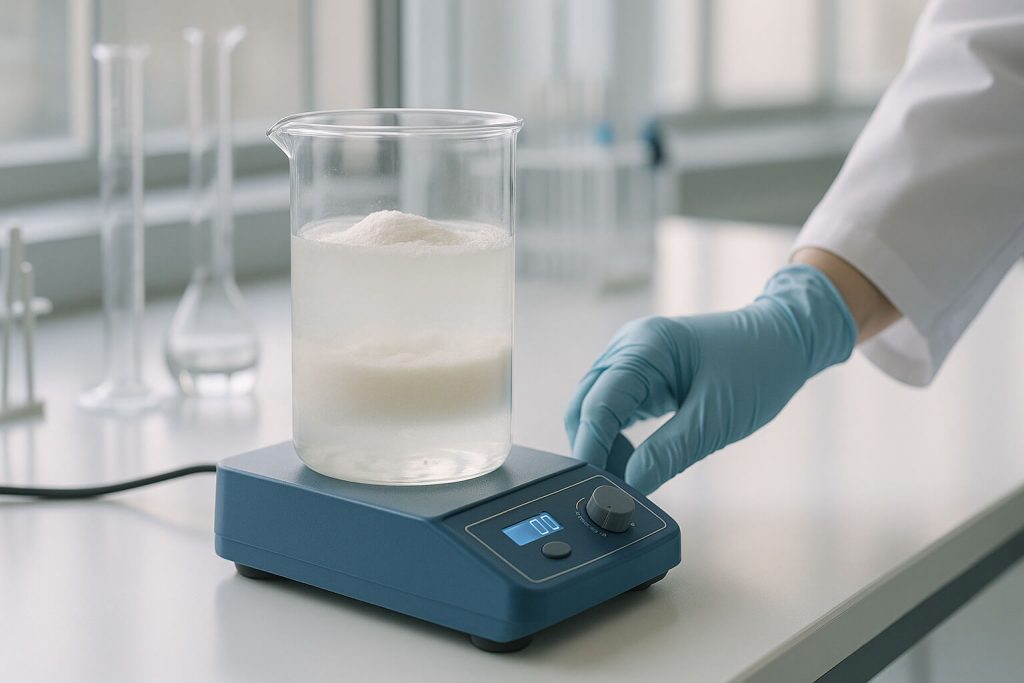
1. What is HPMC and Why is Its Solubility Important?
Hydroxypropyl Methyl Cellulose (HPMC) is a water-soluble polymer widely used in industrial applications such as construction, pharmaceuticals, and food. It’s primarily valued for its ability to function as a binder, thickener, and stabilizer. In construction, it enhances the workability of dry-mix mortars, while in pharmaceuticals, it helps control the release rate of drugs in tablet formulations. In the food industry, HPMC acts as a stabilizing agent in emulsions and provides a smooth texture in products like sauces and dressings.
But why exactly is HPMC solubility so important? Simply put, solubility determines how effectively HPMC performs in its intended application. If HPMC is not properly dissolved, it can result in poor consistency, ineffective binding, or an uneven product texture. For example, in pharmaceutical tablet production, improper dissolution of HPMC could lead to variations in tablet hardness, which may affect the drug release rate. In construction, improper dissolution can result in clumping or uneven viscosity in the mortar, compromising the adhesion and spreadability of the product.
Effective dissolution of HPMC ensures a uniform solution, which is crucial for producing consistent results across batches. Whether you’re developing an adhesive or a food product, achieving proper solubility is key to maintaining product quality and performance.
Solicitud | Papel de HPMC | Importance of Solubility |
---|---|---|
Construcción | Binder and thickener | Ensures smooth and consistent application of mortars |
Productos farmacéuticos | Tablet binder, controlled release | Affects drug release rates and tablet integrity |
Alimento | Stabilizer and emulsifier | Maintains texture, prevents separation |
2. How Does HPMC Solubility Affect Product Quality?
HPMC solubility directly influences the final quality of the product in which it is used. The performance of the end product heavily relies on the consistency and uniformity of the HPMC solution. Inconsistent dissolution can lead to various issues such as clumping, viscosity inconsistencies, and even product failure. Let’s look at how solubility affects product quality in different sectors.
In construction, HPMC is used to improve the workability and adhesion of dry mortars. If the HPMC is not dissolved correctly, it may cause the mixture to clump, affecting the uniformity of the paste. This can lead to an uneven spread, making it harder to apply and reducing the bond strength of the adhesive or mortar. In pharmaceutical manufacturing, poorly dissolved HPMC can result in tablets with inconsistent hardness, which may cause problems in tablet disintegration and drug release. This inconsistency can lead to unreliable dosing, which is critical in pharmaceutical applications.
In the food industry, HPMC is used to stabilize emulsions, preventing ingredients from separating. Poor solubility could result in lumps or uneven texture in sauces or dressings, which would degrade the quality and consumer experience of the product. Achieving the proper solubility ensures that the product maintains its intended consistency and functionality.
The key takeaway here is that solubility is a direct indicator of the product’s overall quality. Ensuring that HPMC is fully dissolved guarantees the desired performance, whether it’s for a pharmaceutical tablet, a construction adhesive, or a food product.
Industria | Effect of Poor Solubility | Solución |
---|---|---|
Construcción | Clumping, uneven viscosity | Ensure proper dissolution to maintain consistency |
Productos farmacéuticos | Inconsistent tablet hardness | Use correct temperature and mixing speeds |
Alimento | Lumps, poor texture | Gradual dissolution and correct water-to-HPMC ratio |
3. What Factors Influence HPMC Solubility?
Several factors influence the solubility of HPMC. The main ones are temperature, water-to-HPMC ratio, and mixing speed. Temperature plays a significant role in how quickly and efficiently HPMC dissolves. Higher temperatures tend to increase the solubility rate of HPMC, but if the temperature is too high, it can degrade the polymer and reduce its effectiveness. Therefore, it’s crucial to maintain the right temperature range during the dissolution process.
El water-to-HPMC ratio is another key factor. Too little water can cause HPMC to form clumps, making it difficult to dissolve evenly. On the other hand, too much water can dilute the solution, affecting the viscosity and overall effectiveness. The ideal ratio depends on the specific application, but generally, a moderate amount of water ensures that HPMC dissolves efficiently without compromising its functional properties.
Finally, mixing speed is a critical factor that can make or break the dissolution process. If the HPMC is added too quickly or the solution is stirred too rapidly, clumping may occur. Slow and steady mixing allows for the polymer to hydrate and dissolve more evenly. Using a consistent and moderate stirring speed ensures that the solution remains homogeneous and free from lumps.
Factor | Impacto en la solubilidad | Mejores prácticas |
---|---|---|
Temperatura | Affects dissolution speed | Keep between 60°C and 80°C for optimal results |
Water-to-HPMC Ratio | Influences viscosity and dissolution | Maintain a balanced ratio for even dissolution |
Velocidad de mezcla | Affects clumping and consistency | Stir gently and consistently for best results |
4. How Can You Achieve Consistent HPMC Dissolution?
Achieving consistent HPMC dissolution is essential for maintaining the quality and performance of the final product. One of the best methods to ensure consistency is by standardizing the dissolution process. This includes controlling the water temperature, maintaining a consistent water-to-HPMC ratio, and using the correct mixing equipment.
Water temperature plays a significant role in achieving uniform dissolution. Keeping the temperature between 60°C and 80°C helps to ensure that the HPMC dissolves efficiently without degradation. Using water that is too hot can degrade the polymer, reducing its effectiveness, while water that is too cold will slow down the dissolution process.
Stirring speed is another crucial factor. Moderate and consistent stirring ensures that the HPMC dissolves evenly and prevents clumping. When using industrial mixers, it’s important to adjust the stirring speed to ensure that the solution remains homogeneous. Too high a speed can introduce air, which can affect the viscosity and consistency of the final solution.
Además, using purified water is essential for achieving the best results. Impurities in the water can affect the dissolution process and lead to inconsistent results. High-quality, purified water ensures that the HPMC dissolves evenly and without issues related to water quality.
Mejores prácticas | Descripción |
---|---|
Standardization | Consistent process ensures reliable results |
Temperature Control | Maintain temperature between 60°C and 80°C |
Purified Water | Use high-quality water for best dissolution |
5. What Are the Common Mistakes When Dissolving HPMC?
Despite being a relatively straightforward process, dissolving HPMC can be tricky if certain mistakes are made. One common mistake is adding HPMC too quickly to the water. When HPMC is added too quickly, it can clump together, forming lumps that are difficult to break up. To avoid this, always add HPMC gradually and stir continuously.
Another common mistake is using incorrect water temperature. If the water is too hot or too cold, it can negatively impact the dissolution process. Water that is too hot can degrade the polymer, while water that is too cold may slow down the dissolution rate, leading to incomplete dissolution.
Stirring speed is another critical factor. If the stirring is too fast, air bubbles can get trapped in the solution, affecting the viscosity and texture. If it’s too slow, the polymer may not dissolve evenly, leading to an inconsistent solution. The ideal stirring speed is moderate, ensuring the solution remains smooth and free from air bubbles.
Error | Consequence | Solución |
---|---|---|
Adding HPMC Too Quickly | Lumps, inconsistent dissolution | Gradually add HPMC and stir continuously |
Incorrect Temperature | Polymer degradation or slow dissolution | Maintain water temperature between 60°C and 80°C |
High Stirring Speed | Air bubbles, uneven viscosity | Stir at moderate speeds to avoid air entrapment |
6. How Do Different Industries Handle HPMC Solubility?
HPMC’s solubility is approached differently depending on the industry and its specific needs. In the pharmaceutical industry, solubility is critical for ensuring the controlled release of drugs. Tablets must disintegrate uniformly, and the HPMC must dissolve at a controlled rate to ensure consistent drug delivery. For this, precision mixing and controlled temperature are essential to achieving the desired dissolution properties.
In the industria de la construcción, HPMC is used primarily in mortar and adhesives. Here, control de viscosidad is more important than rapid dissolution. Hot water dissolution is often preferred to achieve the desired thick consistency for mortars and tile adhesives. Ensuring that the solution is well-mixed prevents clumping and ensures a smooth and workable mixture.
El industria alimentaria uses HPMC to stabilize emulsions, ensuring products like sauces and dressings maintain their texture. In this case, cold water dissolution is often preferred, as it prevents the solution from becoming too viscous. Gradual dissolution allows for better control over texture and consistency.
Industria | Solicitud | Solubility Handling |
---|---|---|
Productos farmacéuticos | Drug release, tablet binding | Precise mixing, controlled temperature |
Construcción | Morteros, adhesivos | Hot water dissolution for thick viscosity |
Alimento | Emulsifiers, stabilizers | Cold water dissolution for smooth texture |
7. What Are the Best Methods for Dissolving HPMC?
The method you choose for dissolving HPMC largely depends on your application. Hot water dissolution is the most common method and is particularly useful when you need to dissolve HPMC quickly. This method uses water temperatures between 60°C and 80°C, which facilitates faster dissolution without compromising the polymer’s integrity. It’s particularly effective in industries like pharmaceuticals and construction, where speed and viscosity control are important.
For more delicate formulations, cold water dissolution is preferred. Cold water dissolution involves slowly adding HPMC to water and stirring gradually, allowing the polymer to hydrate and dissolve more gently. This method is commonly used in the food industry, where a smooth, consistent texture is critical.
In large-scale industrial applications, continuous stirring is often used to ensure that HPMC dissolves evenly. Using specialized mixing equipment ensures that the solution remains homogeneous and free from clumps. This method is particularly important in industries with high-volume production.
Método | Temperatura | Aplicaciones comunes |
---|---|---|
Hot Water Dissolution | 60°C to 80°C | Pharmaceuticals, construction |
Cold Water Dissolution | Room temperature | Food, delicate formulations |
Continuous Stirring | Varía | Large-scale industrial production |
8. How Can You Control Viscosity During the Dissolution Process?
Controlling viscosity is crucial when dissolving HPMC, particularly in applications where the consistency of the final product is vital. One of the most important factors affecting viscosity is the water-to-HPMC ratio. A higher concentration of HPMC results in a thicker solution, while a lower concentration creates a more fluid mixture. Adjusting this ratio allows you to achieve the desired viscosity for your application.
Temperature also plays a significant role in viscosity control. Higher temperatures generally result in a thinner solution, while lower temperatures increase viscosity. It’s essential to keep the temperature within the optimal range to ensure that the HPMC dissolves properly without becoming too thick or too thin.
El stirring speed is another important consideration. Stirring too fast can create bubbles that affect viscosity, while stirring too slowly can result in inconsistent dissolution. Moderate stirring speeds ensure that the solution remains smooth and free of air bubbles.
Factor | Impact on Viscosity | Solución |
---|---|---|
Water-to-HPMC Ratio | Una mayor concentración aumenta la viscosidad. | Adjust ratio based on desired viscosity |
Temperatura | Affects viscosity and dissolution rate | Maintain temperature between 60°C and 80°C |
Stirring Speed | Affects air bubbles and consistency | Stir at moderate speeds to avoid air entrapment |
9. How Do You Troubleshoot Issues with HPMC Solubility?
Even when following the best practices, problems with HPMC solubility can arise. One common issue is the formation of lumps. If HPMC is added too quickly or not mixed thoroughly, clumping can occur. Gradual addition of HPMC and continuous stirring can help prevent this issue. If lumps still form, they can be broken up by increasing the stirring speed or slightly raising the temperature of the solution.
Another problem could be poor dissolution due to improper water quality. If the water used has high mineral content, it can interfere with the dissolution process. Using purified or distilled water is always recommended to achieve the best results.
Finally, if the solution is too thick or too thin, adjusting the water-to-HPMC ratio or the mixing speed can resolve the issue. By making small adjustments, you can ensure that the HPMC dissolves perfectly every time.
Asunto | Causa | Solución |
---|---|---|
Lump Formation | Rapid addition, insufficient stirring | Gradual addition, continuous stirring |
Poor Dissolution | Water impurities | Use purified or distilled water |
Incorrect Viscosity | Incorrect ratio or stirring speed | Adjust water-to-HPMC ratio, moderate stirring |
10. Are There Alternatives to HPMC for Similar Applications?
While HPMC is highly versatile, several alternatives can serve similar purposes in different industries. Methyl Cellulose (MC) is one such alternative. It is used in construction and pharmaceuticals for its similar binding and thickening properties. Carboximetilcelulosa (CMC) is another alternative, often used in food and pharmaceutical applications. Both alternatives offer similar functionality but may differ in terms of solubility and viscosity control.
Ethyl Cellulose is another option for pharmaceutical applications. While it does not dissolve as easily as HPMC, it provides certain benefits, such as stronger film-forming properties. However, it is less commonly used due to its lower solubility.
Each of these alternatives has strengths and weaknesses depending on the application. HPMC remains a popular choice due to its excellent solubility, versatility, y consistent performance.
Alternativa | Características principales | Aplicaciones |
---|---|---|
Methyl Cellulose | Similar binding, thickening | Construcción, productos farmacéuticos |
Carboxymethyl Cellulose | Binding, thickening | Alimentos, productos farmacéuticos |
Ethyl Cellulose | Strong film-forming properties | Pharmaceuticals, coatings |
Conclusión
In conclusion, achieving proper HPMC solubility is essential for ensuring the high quality and effectiveness of products across multiple industries. By controlling key factors such as temperature, water-to-HPMC ratio, and stirring speed, you can ensure that HPMC dissolves correctly every time. Whether you’re working in construction, pharmaceuticals, or food production, maintaining solubility will lead to improved product performance and consistency. By following the best practices outlined in this article and troubleshooting common issues, you can ensure that your products meet the highest standards.
Preguntas frecuentes
Q1: What is HPMC (Hydroxypropyl Methyl Cellulose)?
HPMC is a plant-based polymer used for binding, thickening, and stabilizing in various industries like construction, pharmaceuticals, and food.
Q2: How does temperature affect the solubility of HPMC?
Temperature significantly impacts HPMC’s dissolution rate. Higher temperatures speed up the process, but excessive heat may degrade the polymer.
Q3: Why is controlling viscosity important when dissolving HPMC?
Viscosity affects the texture and functionality of the end product, ensuring it performs as intended, whether in pharmaceuticals, construction materials, or food applications.
Q4: What are the most common mistakes to avoid when dissolving HPMC?
Common mistakes include using incorrect water temperatures, stirring too slowly or too quickly, and using low-quality water.
Q5: Can HPMC be used in both hot and cold water?
Yes, HPMC is versatile and can be dissolved in both hot and cold water. However, the dissolution process may vary depending on the water temperature used.