La hidroxipropilmetilcelulosa, o HPMC, es un polímero versátil con una amplia gama de usos en numerosas industrias. Quizás se pregunte qué hace que este compuesto sea tan especial. Este artículo busca ofrecer una visión general clara de la HPMC, abarcando su producción, propiedades, principales aplicaciones y consideraciones para su uso. Analizaremos su papel en sectores que van desde la construcción hasta el farmacéutico, ofreciendo información a los profesionales B2B que buscan comprender o incorporar la HPMC en sus productos. El objetivo aquí es para brindarle una comprensión básica de este importante material.
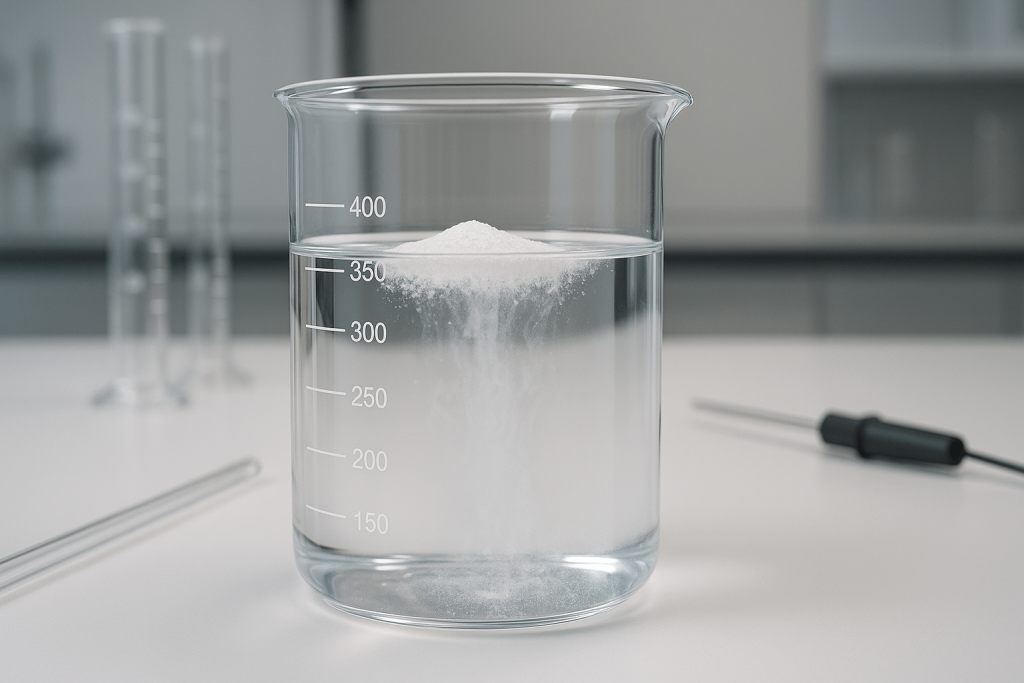
1. ¿Qué es la hidroxipropilmetilcelulosa (HPMC)?
La hidroxipropilmetilcelulosa, comúnmente conocida como HPMC, es un polímero viscoelástico inerte y semisintético. Pero ¿qué significa esto realmente para su uso práctico? Es un tipo de éter de celulosa derivado de la celulosa natural, el polímero orgánico más abundante en la Tierra. La materia prima principal del HPMC suele ser línter de algodón altamente purificado o pulpa de madera. Mediante una serie de modificaciones químicas, esta celulosa natural se transforma en HPMC, un polímero soluble en agua con una combinación única de propiedades.
Su estructura química consiste en una cadena principal de celulosa con grupos metoxi (-OCH₃) e hidroxipropil (-OCH₂CH(OH)CH₃) unidos mediante enlaces éter. Estas sustituciones son clave para sus características. El HPMC generalmente se presenta como un polvo fibroso o granular, inodoro e insípido, de color blanco a ligeramente blanquecino. Su naturaleza no iónica lo hace estable en un amplio rango de pH y compatible con muchos otros ingredientes.
2. ¿Cómo se produce comercialmente el HPMC?
La producción comercial de HPMC es un proceso químico de varios pasos. Todo comienza con Celulosa natural de alta pureza. Esta celulosa se trata primero con una solución alcalina, generalmente hidróxido de sodio, para producir celulosa alcalina. Este paso es crucial, ya que activa la celulosa, haciéndola más reactiva para el posterior proceso de eterificación.
Tras el tratamiento alcalino, la celulosa activada se hace reaccionar con cloruro de metilo (para introducir grupos metoxi) y óxido de propileno (para introducir grupos hidroxipropilo) en un reactor químico. Esta reacción de eterificación es fundamental en la síntesis de HPMC. El grado y la proporción de estas sustituciones pueden controlarse cuidadosamente para producir diferentes grados de HPMC con propiedades variables, como la viscosidad y la temperatura de gelificación térmica. Tras la reacción, el HPMC crudo se purifica para eliminar los subproductos, se seca y se muele hasta obtener el tamaño de partícula deseado. El resultado es Un polímero altamente funcional listo para diversas aplicaciones.
3. ¿Cuáles son las características y propiedades definitorias del HPMC?
El HPMC exhibe una gama de propiedades valiosas que lo convierten en un aditivo muy solicitado. Aquí está el trato: Su solubilidad es una característica clave. El HPMC es soluble en agua fría, pero generalmente insoluble en agua caliente, lo que le confiere una propiedad única de gelificación térmica. Esto significa que, al calentar una solución acuosa de HPMC, forma un gel reversible a una temperatura específica, que se licua al enfriarse. Esta propiedad es crucial para muchas aplicaciones.
Otras características importantes incluyen:
- Viscosidad y comportamiento reológico: Las soluciones de HPMC pueden ofrecer un amplio rango de viscosidades, desde muy bajas hasta extremadamente altas, según el grado y la concentración. Suelen presentar un comportamiento pseudoplástico (seudoplástico).
- Capacidades de formación de películas: HPMC puede formar películas transparentes y flexibles cuando se seca a partir de una solución acuosa, lo que es útil para recubrimientos.
- Retención de Agua: Tiene excelentes capacidades de retención de agua, evitando la pérdida de agua en formulaciones como morteros de cemento o yesos.
- Actividad superficial: HPMC muestra una actividad superficial leve, actuando como emulsionante o estabilizador en algunos sistemas.
- Estabilidad del pH: Es estable en un amplio rango de pH, normalmente de pH 3 a 11.
Propiedad | Descripción |
---|---|
Solubilidad | Soluble en agua fría, forma geles térmicos reversibles. |
Rango de viscosidad | Amplio, de bajo a muy alto, dependiendo del grado |
Formación de películas | Forma películas transparentes y flexibles. |
Retención de agua | Excelente, crucial para la construcción y otras aplicaciones. |
Estabilidad del pH | Estable en un amplio rango de pH (normalmente 3-11) |
4. ¿En qué industrias se utiliza predominantemente HPMC?
La versatilidad de HPMC significa que encuentra aplicación en un conjunto sorprendentemente diverso de industrias. Quizá te sorprenda su alcance. Uno de los mayores consumidores es la industria de la construcción, donde el HPMC se utiliza como espesante, agente de retención de agua y potenciador de la trabajabilidad en morteros a base de cemento, adhesivos para baldosas, lechadas y sistemas de aislamiento y acabado exterior (EIFS).
Más allá de la construcción, el HPMC se utiliza ampliamente en:
- Productos farmacéuticos: como aglutinante, desintegrante y agente de recubrimiento de película para comprimidos; para crear sistemas de administración de fármacos de liberación modificada; y como modificador de la viscosidad en soluciones oftálmicas y geles tópicos.
- Productos alimenticios: Aprobado como aditivo alimentario (E464), funciona como espesante, estabilizador, emulsionante y agente gelificante en productos como salsas, aderezos, productos horneados y tripas vegetarianas.
- Pinturas y recubrimientos: Se utiliza como espesante y modificador de reología en pinturas y recubrimientos a base de agua, mejorando las propiedades de aplicación y la estabilidad del almacenamiento.
- Cuidado personal y cosméticos: Se encuentra en champús, lociones, cremas y pastas de dientes como espesante, emulsionante y estabilizador.
- Otras aplicaciones incluyen adhesivos, cerámicas y textiles. ¡La lista continúa!
5. ¿Cómo mejora el HPMC el rendimiento de los materiales de construcción?
En el ámbito de los materiales de construcción, el HPMC supone una innovación. ¿Cuál es la verdadera historia detrás de su efectividad? Su función principal es mejorar la trabajabilidad y el rendimiento de los productos cementosos y a base de yeso. Por ejemplo, en los adhesivos para baldosas, el HPMC proporciona una excelente retención de agua, lo que prolonga el tiempo de instalación y ofrece a los colocadores mayor flexibilidad durante la instalación. También mejora la adhesión y la resistencia al descuelgue, garantizando la fijación de las baldosas, especialmente en superficies verticales.
Las mejoras clave incluyen:
- Trabajabilidad y consistencia mejoradas: HPMC imparte una consistencia suave y fácil de aplicar a morteros y yesos, reduciendo el esfuerzo de mano de obra.
- Retención de agua mejorada: esto es crucial en los morteros de mezcla seca, ya que evita el secado prematuro y garantiza la hidratación completa del cemento para un desarrollo óptimo de la resistencia.
- Mejor Adherencia y Resistencia de Unión: Mejora la unión entre el mortero y el sustrato o baldosa.
- Reducción del hundimiento y el agrietamiento: al controlar la reología, HPMC ayuda a prevenir el hundimiento en aplicaciones gruesas y reduce el agrietamiento por contracción durante el secado.
Beneficio de HPMC en la construcción | Impacto |
---|---|
Retención de agua | Tiempo abierto prolongado, hidratación mejorada, reducción del agrietamiento. |
Control de espesamiento y reología | Mayor trabajabilidad, anti-flacidez, mejor consistencia. |
Mejora de la adhesión | Mayor adhesión a sustratos y baldosas. |
Arrastre de aire (leve) | Mayor resistencia a la congelación y descongelación, mejor trabajabilidad. |
6. ¿Qué funciones desempeña el HPMC en las formulaciones farmacéuticas?
HPMC es un excipiente ampliamente aceptado en la industria farmacéutica debido a su seguridad, versatilidad y aceptación regulatoria. Su impacto aquí es bastante significativo. Una de sus principales funciones es la de aglutinante de comprimidos, ayudando a mantener unidos los ingredientes y garantizando su resistencia mecánica. También puede actuar como desintegrante, facilitando la descomposición del comprimido en el tracto digestivo para la liberación del fármaco.
Además, la HPMC se utiliza ampliamente para:
- Recubrimientos peliculares: Forma películas transparentes, resistentes y flexibles, ideales para recubrir comprimidos y cápsulas. Estos recubrimientos pueden mejorar la apariencia, enmascarar el sabor, proteger el medicamento y facilitar su deglución.
- Sistemas de liberación modificada de fármacos: Se utilizan diferentes grados de viscosidad de HPMC para crear matrices hidrofílicas que controlan la velocidad de liberación de los fármacos durante un período prolongado. Esto permite una dosificación menos frecuente y concentraciones plasmáticas más estables del fármaco.
- Soluciones y Suspensiones Oftálmicas: Sus propiedades mejoradoras de viscosidad lo hacen adecuado para colirios, aumentando el tiempo de contacto sobre la superficie ocular.
- Preparaciones tópicas: Se utiliza como espesante y estabilizador en geles, cremas y ungüentos. Las aplicaciones son realmente diversas.
7. ¿Hay varios tipos y grados de HPMC disponibles?
Sí, HPMC no es un material que se adapte a todos. Aquí es donde se pone interesante. Los fabricantes ofrecen una amplia variedad de grados de HPMC adaptados a las necesidades específicas de cada aplicación. Estos grados se diferencian principalmente en su viscosidad, grado de sustitución (DS) de los grupos metoxilo y sustitución molar (MS) de los grupos hidroxipropilo.
Los diferenciadores clave incluyen:
- Niveles de viscosidad: Esta es quizás la forma más común de clasificar la HPMC. La viscosidad se mide típicamente en una solución acuosa de 2% a 20 °C y puede variar desde muy baja (p. ej., 3 mPa·s) hasta muy alta (p. ej., más de 100 000 mPa·s).
- Tipos de sustitución: La proporción de sustitución de metoxilo a hidroxipropilo influye en propiedades como la temperatura de gelificación térmica, la solubilidad y la actividad superficial. Por ejemplo, un mayor contenido de hidroxipropilo generalmente conlleva temperaturas de gelificación más altas.
- Tamaño de partícula: Hay diferentes tamaños de partículas disponibles para distintas tasas de disolución y características de manipulación.
- Grados especiales: algunos grados se modifican para necesidades específicas, como una mejor resistencia a las enzimas, una mejor dispersabilidad en agua o resistencias de gel específicas.
Comprender los códigos y las especificaciones de los productos de los proveedores es fundamental para seleccionar el grado de HPMC adecuado. Lo importante es adecuar el grado a la necesidad.
Parámetro de grado de HPMC | Variación típica |
---|---|
Viscosidad | 3 mPa·s a >100.000 mPa·s (en solución 2%) |
Contenido de metoxilo | Normalmente 19-30% |
Contenido de hidroxipropilo | Normalmente 4-12% |
Tamaño de partícula | Polvos finos a formas granulares |
8. ¿Qué factores deben tenerse en cuenta al elegir el HPMC adecuado?
Seleccionar el grado correcto de HPMC es fundamental para lograr el rendimiento deseado en un producto final. Entonces, ¿qué deberías buscar? La consideración principal siempre es la aplicación específica y el papel funcional que se espera que desempeñe la HPMC. Por ejemplo, una HPMC de alta viscosidad podría ser ideal para espesar una pintura, mientras que una de baja viscosidad podría ser preferible para el recubrimiento de comprimidos farmacéuticos.
Otros factores a tener en cuenta incluyen:
- Viscosidad deseada y resistencia del gel: el efecto espesante requerido o las características del gel determinarán el grado de viscosidad.
- Tiempo de fraguado y resistencia (para construcción): En sistemas cementosos, el HPMC puede influir en el tiempo de fraguado y el desarrollo de la resistencia final.
- Compatibilidad: asegúrese de que el grado de HPMC elegido sea compatible con otros ingredientes de la formulación, como sales, surfactantes o ingredientes farmacéuticos activos.
- Cumplimiento normativo: Para aplicaciones alimentarias y farmacéuticas, el HPMC debe cumplir con normas regulatorias específicas (p. ej., USP, EP, E464). Verifique siempre las certificaciones.
- Velocidad de disolución: La velocidad a la que se disuelve el HPMC puede ser importante, especialmente en productos de mezcla seca que se mezclan con agua en el sitio. Tomar la decisión correcta es de suma importancia.
9. ¿Cuáles son las mejores prácticas para manipular y almacenar HPMC?
La manipulación y el almacenamiento adecuados de HPMC son esenciales para mantener su calidad y garantizar la seguridad. Esto es lo que necesitas saber. El HPMC es generalmente un material estable, pero es higroscópico, lo que significa que puede absorber la humedad del aire. Por lo tanto, debe almacenarse en su envase original, bien cerrado, en un lugar seco y fresco, alejado de la luz solar directa y de fuentes de calor.
Las precauciones de seguridad durante la manipulación incluyen:
- Control de polvo: Al igual que muchos polvos orgánicos finos, el polvo de HPMC puede formar mezclas explosivas con el aire si está presente en altas concentraciones. Asegúrese de que haya una buena ventilación y evite la acumulación de polvo. Utilice el equipo de protección personal (EPP) adecuado, como mascarillas antipolvo y gafas de seguridad.
- Hoja de datos de seguridad del material (MSDS): consulte siempre la MSDS del proveedor para obtener información de seguridad detallada, procedimientos de manipulación y medidas de emergencia.
- Vida útil: Si bien la HPMC tiene una buena vida útil (a menudo varios años si se almacena correctamente), es recomendable utilizar primero el material más antiguo. Un almacenamiento prolongado o inadecuado puede provocar la absorción de humedad, lo que podría afectar su rendimiento, en particular sus características de disolución. El almacenamiento adecuado es clave para la longevidad.
Consideración de almacenamiento | Recomendación |
---|---|
Embalaje | Mantener en bolsas o recipientes originales bien cerrados. |
Ambiente | Lugar fresco y seco, alejado del calor y la luz solar directa. |
Humedad | Proteger de la humedad debido a su naturaleza higroscópica. |
Seguridad | Minimizar el polvo, utilizar EPP, consultar la MSDS |
10. ¿Qué depara el futuro a las aplicaciones y el desarrollo de HPMC?
El futuro del HPMC parece prometedor, impulsado por la investigación en curso y la demanda de materiales sostenibles y de alto rendimiento. ¿Listo para lo que sigue? Es probable que sigamos experimentando una expansión hacia aplicaciones nuevas e innovadoras. Por ejemplo, su biocompatibilidad y sus singulares propiedades gelificantes lo convierten en un candidato ideal para aplicaciones biomédicas avanzadas, como la ingeniería de tejidos y los sistemas de administración de fármacos.
Las tendencias a tener en cuenta incluyen:
- Abastecimiento y producción sostenibles: cada vez se hace más hincapié en el uso de celulosa de origen sostenible y en el desarrollo de procesos de fabricación más respetuosos con el medio ambiente para HPMC.
- Nuevas funcionalidades: La investigación se centra en modificar HPMC para impartir nuevas funcionalidades, como una mayor resistencia enzimática para aplicaciones alimentarias o interacciones específicas para la administración dirigida de fármacos.
- Grados mejorados: desarrollo de grados de HPMC con características de rendimiento aún mejores, como disolución más rápida, mayor claridad en la solución o perfiles reológicos personalizados.
- Combinación con otros polímeros: exploración de efectos sinérgicos al combinar HPMC con otros polímeros naturales o sintéticos para crear materiales con propiedades combinadas únicas. El potencial del HPMC continúa creciendo.
Tendencia futura para HPMC | Impacto esperado |
---|---|
Abastecimiento sostenible | Huella ambiental reducida, mayor atractivo para el consumidor |
Usos biomédicos avanzados | Aplicaciones en ingeniería de tejidos, administración avanzada de fármacos |
Calificaciones de rendimiento mejorado | Mayor eficiencia, nuevas posibilidades de aplicación |
Sistemas de polímeros híbridos | Nuevos materiales con propiedades sinérgicas |
En resumen, el HPMC es un derivado de celulosa extraordinariamente versátil con un amplio espectro de aplicaciones. Sus propiedades únicas, como la solubilidad en agua, la gelificación térmica y la capacidad de formar películas, lo convierten en un ingrediente indispensable en las industrias de la construcción, farmacéutica, alimentaria y muchas otras. Comprender los diferentes grados y sus características específicas es clave para aprovechar al máximo el potencial del HPMC. A medida que avanza la investigación, podemos anticipar usos aún más innovadores para este valioso polímero.
Sección de preguntas frecuentes
Q1:¿Qué es HPMC?
- La HPMC, o hidroxipropilmetilcelulosa, es un polímero semisintético derivado de la celulosa natural. Se utiliza ampliamente como espesante, aglutinante, formador de película y agente de retención de agua en diversas industrias gracias a sus propiedades únicas, como la solubilidad en agua fría y la gelificación térmica.
Q2¿Cómo mejora HPMC el rendimiento del producto?
- El HPMC mejora el rendimiento del producto al proporcionar una viscosidad controlada, mejorar la trabajabilidad (por ejemplo, en morteros), extender el tiempo abierto, garantizar una suspensión uniforme de partículas, formar películas protectoras (por ejemplo, en tabletas) y estabilizar emulsiones. Sus beneficios son multifacéticos.
T3¿Es seguro el uso de HPMC en alimentos y productos farmacéuticos?
- Sí, el HPMC está generalmente reconocido como seguro (GRAS) para aplicaciones alimentarias (E464) y es un excipiente ampliamente aceptado en formulaciones farmacéuticas, conforme con farmacopeas como la USP y la EP. Es atóxico e hipoalergénico para la mayoría de los usos.
T4:¿Cuáles son las principales diferencias entre HPMC y otros éteres de celulosa como HEC o CMC?
- Si bien todos son derivados de la celulosa, difieren en sus grupos sustituyentes y, por lo tanto, en sus propiedades. Por ejemplo, la HPMC (y la metilcelulosa) presentan gelificación térmica, algo que no es habitual en la hidroxietilcelulosa (HEC) ni en la carboximetilcelulosa (CMC). La CMC es aniónica, mientras que la HPMC y la HEC son no iónicas, lo que afecta a su compatibilidad y estabilidad del pH. Cada uno tiene su nicho.
Q5¿Dónde puedo obtener HPMC de alta calidad para mi negocio?
- Se puede obtener HPMC de alta calidad de fabricantes y distribuidores químicos de renombre especializados en éteres de celulosa. Se recomienda buscar proveedores con buenas prácticas de fabricación (GMP), certificaciones pertinentes (p. ej., ISO) y que puedan proporcionar soporte técnico y muestras de producto para su evaluación, garantizando así que satisfaga las necesidades específicas de su aplicación B2B.