Hydroxypropyl Methylcellulose (HPMC) plays a significant practical role in film coating that impacts a variety of industrial applications such as pharmaceuticals, food, and construction. This article will explore the technical and functional aspects of HPMC in film coating, covering everything from its chemical nature to how it enhances product stability and quality. You’ll gain a thorough understanding of why HPMC is a preferred polymer in coatings and the specific requirements it meets across industries. The goal here is to equip decision-makers and purchasing professionals with detailed insights to make informed choices about incorporating HPMC in their production processes.
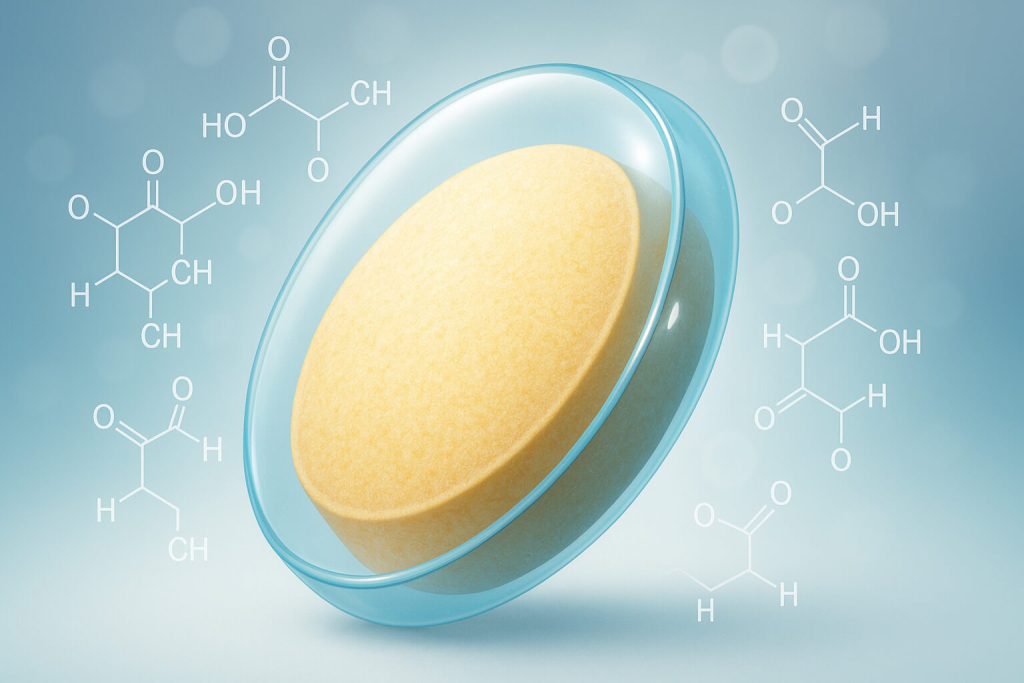
1. What is Hydroxypropyl Methylcellulose and why is it used in film coating?
Hydroxypropyl Methylcellulose, often abbreviated as HPMC, is a semi-synthetic polymer derived from cellulose. Chemically, it is a non-ionic cellulose ether featuring both methyl and hydroxypropyl functional groups, which collectively provide solubility in water and film-forming abilities. In the context of film coating, HPMC is highly valued for creating smooth, consistent coatings that protect, bind, or modify the surface characteristics of tablets, food products, or construction materials.
But here’s the kicker: HPMC’s versatility comes from its ability to form transparent, durable films that are tasteless, odorless, and safe to consume, making it especially popular in the pharmaceutical sector for tablet coatings that control drug release or mask unpleasant tastes. In food manufacturing, it serves as an edible film to extend shelf life and improve texture. In construction, HPMC is incorporated into cementitious and gypsum-based products to enhance workability and surface finish via its film-forming properties.
HPMC’s success dates back several decades, with steady improvements in production methods increasing its purity and controlling molecular weight—factors critical to performance in coatings. Its water solubility and biocompatibility set it apart from many other polymers. Additionally, HPMC participates in both aqueous and organic solvent-based formulations, providing flexibility for manufacturers.
This adaptability means that industries from pharma to construction rely on it not just for protective layers but for improving handling, processing, and final product appearance. What’s the real story? It’s that HPMC’s chemical makeup and user-friendly traits position it as a go-to ingredient for delivering a variety of functional benefits in film coatings.
Propiedad | Descripción | Industrial Impact |
---|---|---|
Chemical Type | Non-ionic cellulose ether | Provides solubility and film-forming capability |
Solubilidad | Water soluble | Facilitates use in aqueous coating systems |
Grupos funcionales | Methyl and hydroxypropyl groups | Enhance flexibility and durability |
Perfil de seguridad | Non-toxic, generally recognized as safe (GRAS) | Enables edible and pharmaceutical applications |
Historical Use | Used since mid-20th century | Proven performance across multiple industries |
2. How does Hydroxypropyl Methylcellulose affect the film coating’s physical properties?
The physical properties of film coatings are central to their utility, and here’s where Hydroxypropyl Methylcellulose proves its worth in numerous ways. Ready for the good part? HPMC influences film flexibility, mechanical strength, adhesion, and resistance to moisture—factors that determine how well the coating protects and maintains the quality of the underlying product.
First, the flexibility of the HPMC film ensures it withstands mechanical stress without cracking or peeling. For instance, pharmaceutical tablets coated with HPMC remain intact during tablet handling, packaging, and transport. In food packaging films, the flexibility prevents the film from breaking during processing or consumer use, maintaining barrier integrity. Studies show that HPMC formulations with higher molecular weight offer films with superior elongation and tensile strength.
Adhesion is another critical property. HPMC films exhibit excellent adhesion to diverse substrates such as pill surfaces, food items, or building panels. In pharmaceutical coatings, strong adhesion is essential for sustained release or controlled dissolution of drugs. This adhesion also reduces manufacturing defects like blistering or detachment during drying.
But this is where it gets interesting: HPMC’s moisture barrier properties help shield products from humidity and oxygen. Its hydrophilic nature forms films that are permeable enough to allow controlled release of active ingredients but resist excessive moisture ingress that can cause degradation. In construction materials, this property keeps coatings effective under varying environmental conditions.
Propiedad física | Efecto HPMC | Industrial Example |
---|---|---|
Flexibilidad | Prevents cracking and peeling | Tablets maintain coating integrity |
Adhesión | Fuerte adhesión a los sustratos | Food products achieve uniform coating |
Resistencia a la humedad | Controls moisture penetration | Construction surfaces resist weather damage |
Resistencia mecánica | Enhances durability under stress | Extended shelf life for coated materials |
Transparencia | Produces clear films | Visually appealing coatings in pharma & food |
3. Why is Hydroxypropyl Methylcellulose preferred over other polymers in film coating?
What sets Hydroxypropyl Methylcellulose apart from other polymers used in film coating? When evaluating alternatives such as cellulose acetate phthalate, ethyl cellulose, or vinyl polymers, HPMC offers a balanced combination of properties that often makes it the preferred choice.
First, its ease of dissolution in water simplifies processing, requiring less solvent and lowering chemical hazards associated with organic solvents. This factor appeals to industries focused on sustainability and regulatory compliance.
Secondly, HPMC is versatile in molecular weight and substitution patterns, allowing customization to specific industry needs. For example, low-viscosity grades produce thin, fast-drying films suitable for pharmaceutical tablets, while high-viscosity grades yield thicker, more durable coatings ideal for construction applications.
Cost is another influential factor. Compared to specialty polymers, HPMC is widely available and competitively priced, providing reliable performance without escalating production expenses. Its status as an established excipient also means regulatory hurdles tend to be lower, especially in controlled environments like pharmaceuticals and food.
Here’s the real story: industries appreciate HPMC’s unmatched balance of safety, performance, and economics. Unlike some synthetic polymers, HPMC does not require plasticizers to improve flexibility, reducing formulation complexity and potential compatibility issues.
Polymer Type | Solubilidad | Flexibilidad | Costo | Uso típico |
---|---|---|---|---|
Hidroxipropilmetilcelulosa | Agua | Alto | Moderado | Pharma, food, construction |
Cellulose Acetate Phthalate | disolventes orgánicos | Moderado | Más alto | Enteric coatings in pharma |
Etilcelulosa | disolventes orgánicos | Bajo | Moderado | Controlled release coatings |
Vinyl Polymers | Various | Variable | Alto | Industrial coatings |
4. How does Hydroxypropyl Methylcellulose contribute to product stability during storage?
You might wonder: how does HPMC affect the stability of coated products over time? The short answer is that it plays a vital role in extending shelf life by providing moisture and oxidation barriers, maintaining mechanical integrity, and protecting active ingredients or substrates.
HPMC films act as semi-permeable barriers that limit exposure to air and moisture without completely sealing the product, which can create unwanted condensation. This property is crucial for pharmaceuticals, where drug potency must be preserved, and for food, where freshness and texture are key selling points.
Take pharmaceutical tablets coated with HPMC. Research shows these coatings reduce moisture uptake by up to 30%, helping maintain drug stability under fluctuating humidity. Similarly, in food packaging, HPMC films slow down spoilage by controlling oxygen ingress and maintaining product moisture balance.
Moreover, HPMC’s compatibility with various active ingredients prevents adverse reactions that may occur with other polymers. This characteristic is important for both pharma and food sectors where chemical stability is paramount.
But here’s the kicker: studies on cement-based coatings demonstrate that HPMC can improve surface durability during long-term storage, preventing cracking caused by drying shrinkage or environmental exposure. This indicates its value beyond just barrier function.
Stability Factor | HPMC Contribution | Industry Implication |
---|---|---|
Control de humedad | Reduces moisture uptake | Prolongs shelf life of pharmaceuticals |
Oxidation Barrier | Limits oxygen penetration | Preserves freshness in food |
Chemical Compatibility | Prevents ingredient interaction | Ensures active ingredient stability |
Mechanical Integrity | Prevents cracking or brittleness | Sustains coating performance over time |
Environmental Resistance | Protects against weather effects | Enhances durability in construction |
5. What are the technical considerations when using Hydroxypropyl Methylcellulose in coating formulations?
This is where it gets interesting for formulators and engineers. Using Hydroxypropyl Methylcellulose effectively requires careful selection of parameters such as molecular weight, concentration, temperature controls, and solvent systems.
The molecular weight of HPMC affects viscosity and film thickness. For example, high molecular weight grades create more viscous solutions and thicker coatings, ideal for robust protection but requiring adjustments in processing equipment. Lower molecular weight variants are preferred for thin, rapid-dry layers.
Concentration of HPMC in formulation impacts coating uniformity and drying time. Too low a concentration can produce fragile films prone to defects; too high can increase viscosity excessively, complicating application and drying.
Processing temperature also matters. HPMC films form best within a specific temperature range, often between 40°C and 70°C, depending on grade and solvent system. Temperatures too high can cause film cracking; too low can yield incomplete adhesion.
Additionally, the solvent choice affects dissolution and film clarity. Water-based systems are most common, but organic solvents might be used when water-sensitive ingredients require it.
Ready for the good part? Attention to these technical details ensures consistent quality, reduces waste, and optimizes product performance.
Technical Parameter | Effect on Coating | Practical Notes |
---|---|---|
Peso molecular | Controls viscosity & thickness | Choose depending on desired film robustness |
Concentración | Influences film uniformity | Optimize to avoid defects or processing issues |
Temperatura | Affects adhesion and drying | Mantener un rango de temperatura óptimo |
Sistema de disolventes | Impacts solubility & film clarity | Favor water-based systems where possible |
Velocidad de mezcla | Ensures homogeneity | Prevents lumps and uneven coatings |
6. How is Hydroxypropyl Methylcellulose optimized for different industry requirements?
Adapting Hydroxypropyl Methylcellulose to specific industry needs illustrates its flexibility as a polymer. Whether used in pharma, food, or construction, manufacturers modify its grades and formulations to meet stringent performance criteria.
In pharmaceuticals, HPMC is often tailored for modified-release coatings. Low-viscosity, high-purity grades with controlled substitution levels help achieve targeted drug dissolution profiles. For example, enteric coatings that resist stomach acid but dissolve in the intestines depend on specialized HPMC blends combined with other polymers for precise timing.
In food industries, HPMC’s molecular weight and formulation are adjusted to create edible films that improve texture, act as moisture barriers, or carry flavors and preservatives. For instance, snack food coatings use lower viscosity HPMC to create thin, transparent films that don’t alter taste or appearance.
Construction materials benefit from HPMC’s thickening and water-retention properties, with high-viscosity grades preferred for enhancing workability and surface smoothness. Additives are sometimes blended with HPMC to improve bonding or reduce shrinkage in mortar and plaster applications.
But here’s the kicker: this ability to customize HPMC ensures it fits a wide range of applications with minimal compromise, maintaining functional performance while meeting regulatory and operational demands.
Industria | HPMC Grade Characteristic | Typical Application | Customization Example |
---|---|---|---|
Farmacéutico | Low viscosity, high purity | Modified tablet coatings | Liberación controlada de fármacos |
Alimento | Medium to low viscosity | Edible films and packaging | Flavor carrier coatings |
Construcción | Alta viscosidad | Cementitious and gypsum products | Improved workability and surface finish |
7. What challenges can arise when using Hydroxypropyl Methylcellulose in film coatings?
No solution is free of challenges, and understanding potential issues with HPMC is critical for successful application. Among the primary difficulties are ensuring uniform film formation, preventing processing problems, and navigating regulatory requirements.
Achieving consistent film thickness across batches can be tough. Variations in HPMC grade or mixing can lead to defects such as pinholes, cracks, or uneven surfaces that compromise protection. This is particularly sensitive in pharmaceutical applications where uniform coating impacts drug delivery.
Handling and mixing HPMC powders require expertise. Improper dispersion can cause clumping or lump formation, affecting viscosity and film integrity. Industrial mixers with adequate shear and time control are often necessary.
Regulatory considerations vary by industry. While HPMC is generally recognized as safe, variations in molecular substitution or impurities can cause compliance issues, especially in food-related sectors with strict hypersensitivity guidelines.
But here’s the kicker: manufacturers who understand and control these challenges often gain a competitive edge by producing reliable, high-performing films consistently.
Desafío | Impacto | Mitigation Strategy |
---|---|---|
Film uniformity | Defects affecting protection | Strict process control and QC |
Mixing difficulties | Clumping and uneven viscosity | Use proper mixers and dispersion aids |
Cumplimiento normativo | Delays or rejection approval | Source certified grades and documentation |
Drying control | Film cracking or blisters | Optimize drying temperature and humidity |
Formulation compatibility | Adverse interactions with additives | Conduct compatibility testing |
8. How can manufacturers ensure consistent quality when using Hydroxypropyl Methylcellulose?
Ensuring consistent quality when working with Hydroxypropyl Methylcellulose requires a combination of rigorous quality control, supplier management, and performance testing. Monitoring raw materials, formulation processes, and final product attributes is crucial.
Quality control starts with verifying raw material purity, viscosity, and substitution levels according to supplier certificates of analysis. Discrepancies here can translate into product failures down the line. Working with reputable suppliers that provide full traceability and adherence to regulatory standards reduces risk.
During production, real-time monitoring of coating viscosity, drying conditions, and film thickness helps catch deviations early. Technologies such as inline viscometers and coating weight sensors can improve accuracy.
Performance testing includes mechanical strength, adhesion tests, moisture permeability measurements, and visual inspection. Samples from each production batch need to meet predefined specifications to ensure reliability.
Ready for the good part? These quality assurance practices not only ensure product consistency but also help manufacturers optimize formula adjustments and troubleshoot faster, saving time and costs.
Paso de control de calidad | Objetivo | Method/Tool |
---|---|---|
Prueba de materia prima | Verify purity and viscosity | Suppliers’ certificates, lab analysis |
Process Monitoring | Ensure uniform mixing and coating | Inline sensors, viscosity meters |
Film Testing | Confirm mechanical and barrier properties | Tensile tests, moisture permeability |
Supplier Management | Secure consistent input quality | Approved vendor lists, audits |
Documentation & Traceability | Comply with regulation | Batch records, quality manuals |
Conclusión
This article has covered the practical role Hydroxypropyl Methylcellulose plays in film coating. We examined its chemical nature, how it influences physical properties like flexibility and moisture resistance, and why it’s preferred over other polymers. We explored its contribution to product stability, technical formulation considerations, industry-specific customization, potential challenges, and quality control best practices. The information presented is aimed at industrial decision-makers looking to optimize coating performance through informed HPMC usage. In summary, HPMC stands out as a versatile, reliable polymer that meets the demanding requirements of pharmaceutical, food, and construction sectors, offering real-world benefits that support product quality and longevity.
Preguntas frecuentes
Q1: What is Hydroxypropyl Methylcellulose?
Hydroxypropyl Methylcellulose (HPMC) is a cellulose-derived polymer widely used as a film former in different industries due to its excellent binding, coating, and moisture retention properties.
Q2: How does Hydroxypropyl Methylcellulose work in film coating?
HPMC forms a uniform, flexible film on surfaces, improving adhesion and protecting the underlying material from environmental stressors such as moisture and oxidation.
Q3: Can Hydroxypropyl Methylcellulose be used in food and pharmaceutical products?
Yes, HPMC is commonly used in pharmaceutical tablet coatings and as an edible film in food packaging because of its safety profile and functional characteristics.
Q4: What factors influence the performance of HPMC in coatings?
Properties such as molecular weight, concentration, solvent system, and processing conditions directly affect film formation, durability, and application efficiency.
Q5: Are there limitations to using Hydroxypropyl Methylcellulose in industrial coatings?
Some challenges include achieving uniform coating thickness, controlling drying times, and complying with industry-specific regulations depending on the application.