Les propriétés thermiques de l'hydroxypropylméthylcellulose (HPMC) sont un facteur crucial pour les fabricants des secteurs pharmaceutique, agroalimentaire et de la construction. Lors de la formulation de produits à base d'HPMC, la compréhension de son comportement de fusion exact a un impact direct sur les décisions de traitement, la stabilité du produit final et les performances des applications. Cet article examine les plages de points de fusion spécifiques de l'HPMC, explore les facteurs affectant son comportement thermique et fournit des conseils pratiques pour optimiser les températures de traitement. Maîtriser les propriétés thermiques de l'HPMC permet d'éviter les problèmes de fabrication, de prolonger la durée de conservation des produits et de garantir des performances constantes dans toutes les applications.
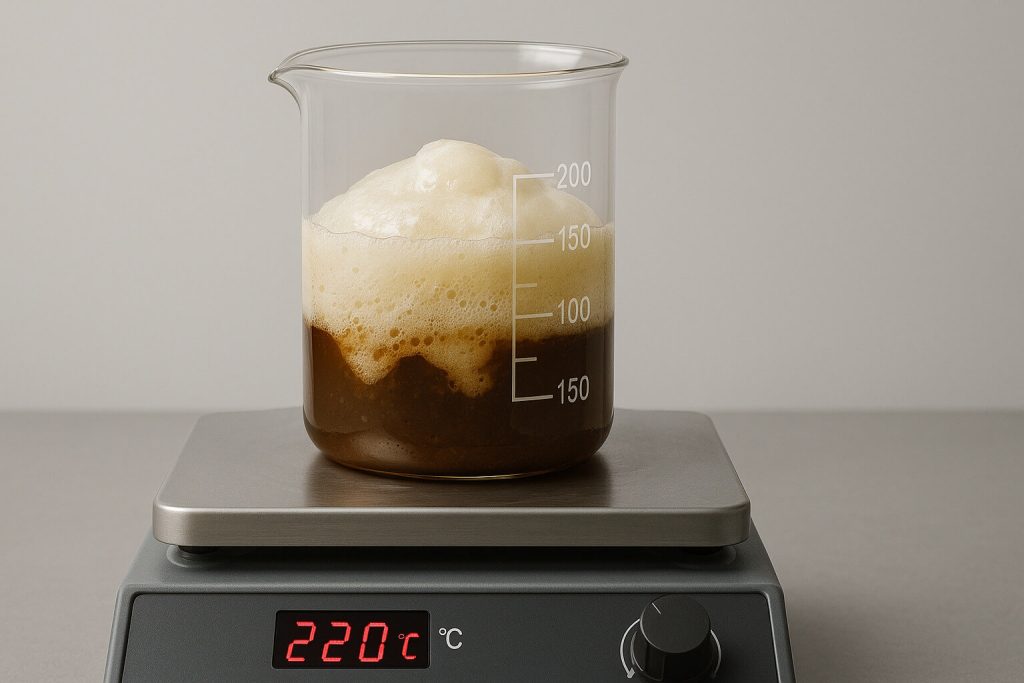
1. Qu'est-ce que l'HPMC et pourquoi son point de fusion est-il important ?
L'hydroxypropylméthylcellulose (HPMC) est un polymère inerte semi-synthétique dérivé de la cellulose par modification chimique. La structure de base de la cellulose est substituée par des groupes hydroxypropyle et méthyle, créant un composé polyvalent aux propriétés thermiques uniques. L'HPMC se présente sous la forme d'une poudre blanche à blanc cassé qui se dissout dans l'eau pour former des solutions limpides de viscosité variable selon le grade.
Mais voici le point critique : La compréhension du comportement de fusion de l'HPMC a un impact direct sur les procédés de fabrication et les performances du produit final. Contrairement aux matériaux cristallins à point de fusion précis, l'HPMC présente un comportement thermique complexe en raison de sa nature amorphe et de sa structure polymère.
Les caractéristiques de fusion du HPMC déterminent les paramètres de traitement dans de nombreuses industries :
Industrie | Application | Pourquoi le point de fusion est important |
---|---|---|
Pharmaceutique | Matrices à libération contrôlée | Détermine les limites de température de traitement lors de la fabrication des comprimés |
Construction | Additifs pour ciment | Affecte la stabilité lors du mélange avec des composés de ciment chaud |
Nourriture | Agents épaississants | Assure la stabilité pendant les processus de cuisson et de pâtisserie |
Soins personnels | Formules de gel | Impacte la stabilité du produit pendant la fabrication et le stockage |
Revêtements | Les cinéastes | Détermine les exigences de température de séchage et de durcissement |
La stabilité thermique du HPMC influence directement la durée de conservation des produits, la cinétique de libération dans les applications pharmaceutiques et l'intégrité structurelle des matériaux de construction. Le polymère commence à subir des modifications bien avant d'atteindre sa température de décomposition, ce qui rend la compréhension de son profil thermique complet essentielle à une manipulation appropriée.
Les fabricants doivent prendre en compte non seulement le point de fusion final, mais aussi l'ensemble de la plage de transition thermique lors de la conception des protocoles de traitement. Cette connaissance permet d'éviter les défaillances des produits, de garantir la cohérence d'un lot à l'autre et d'optimiser l'efficacité de la fabrication.
2. Quelle est la plage de points de fusion réelle du HPMC ?
Contrairement aux substances cristallines, l'HPMC ne présente pas de point de fusion précis et clairement défini. Il présente plutôt une plage de transition thermique où le ramollissement se produit avant la fusion complète. La plage de points de fusion conventionnelle de l'HPMC de qualité pharmaceutique se situe généralement entre 225 et 230 °C, mais peut varier selon les grades et les méthodes de fabrication.
Tu devrais savoir que L'HPMC subit plusieurs transitions thermiques avant d'atteindre son point de fusion, notamment la perte d'eau, la transition vitreuse et, enfin, la fusion suivie d'une dégradation.
Le tableau suivant décrit les principaux points de transition thermique pour le HPMC standard :
Transition thermique | Plage de température (°C) | Changements physiques |
---|---|---|
Perte d'eau | 50-100 | Évaporation de l'eau liée |
Transition vitreuse | 170-195 | Adoucissement, mobilité moléculaire accrue |
Plage de fusion | 225-230 | Perte complète de structure |
Début de la dégradation | 270-290 | Dégradation chimique, décoloration |
Dégradation complète | >300 | Carbonisation |
En comparant le HPMC à d’autres dérivés de la cellulose, ses caractéristiques de fusion deviennent plus apparentes :
Dérivé de cellulose | Plage de points de fusion (°C) | Stabilité thermique relative |
---|---|---|
HPMC | 225-230 | Haut |
Méthylcellulose (MC) | 290-305 | Très élevé |
Hydroxyéthylcellulose (HEC) | 200-220 | Modéré |
Carboxyméthylcellulose (CMC) | 227-252 | Haut |
Éthylcellulose (EC) | 160-210 | Modéré |
La détermination des points de fusion de l'HPMC fait généralement appel à la calorimétrie différentielle à balayage (DSC), qui mesure le flux thermique lors d'augmentations contrôlées de température. Cette technique révèle les pics endothermiques associés aux transitions de fusion.
Les facteurs affectant la précision des mesures du point de fusion comprennent :
- Méthode de préparation des échantillons
- Taux de chauffage pendant l'analyse
- Historique thermique antérieur de l'échantillon
- Présence d'additifs ou d'impuretés
- Teneur en humidité avant le test
Pour les applications pratiques, les fabricants considèrent souvent le début du ramollissement (autour de 190-200°C) comme la limite supérieure pratique pour le traitement plutôt que le point de fusion réel, offrant ainsi une marge de sécurité contre la dégradation.
3. Comment le grade de viscosité du HPMC affecte-t-il son comportement à la fusion ?
Les grades de viscosité des HPMC sont directement corrélés à leur masse moléculaire, ce qui influence significativement les propriétés thermiques, notamment le comportement à la fusion. Les grades HPMC de masse moléculaire élevée (viscosité plus élevée) présentent généralement des points de fusion légèrement plus élevés et des plages de fusion plus larges que les variétés de masse moléculaire plus faible.
L’idée clé ici est Le choix du grade de viscosité a un impact non seulement sur les propriétés de la solution, mais aussi sur les paramètres de traitement thermique. Cette relation résulte de l'enchevêtrement accru des chaînes et des forces intermoléculaires présentes dans les HPMC de masse moléculaire plus élevée.
Le tableau ci-dessous illustre comment les différents grades de viscosité affectent les propriétés thermiques :
Grade de viscosité HPMC | Poids moléculaire approximatif | Transition vitreuse (°C) | Plage de fusion (°C) | Stabilité thermique |
---|---|---|---|---|
Faible (3-15 mPa·s) | 10,000-30,000 | 170-180 | 220-225 | Bien |
Moyen (100-150 mPa·s) | 40,000-60,000 | 175-185 | 225-230 | Mieux |
Élevé (4 000 à 6 000 mPa·s) | 80,000-120,000 | 180-190 | 230-235 | Meilleur |
Ultra-élevé (> 10 000 mPa·s) | >150 000 | 185-195 | 235-240 | Excellent |
Lors du chauffage, les grades de viscosité plus élevés démontrent :
- Plus grande résistance à l'écoulement à des températures élevées
- Élasticité plus prononcée avant la fusion
- Taux de dégradation thermique plus lents
- Besoins énergétiques plus élevés pour une fusion complète
Ces différences deviennent particulièrement importantes dans des applications comme l'extrusion à chaud, où les plages de température de traitement doivent être soigneusement contrôlées. Les grades de viscosité plus faibles facilitent le traitement à basse température, mais peuvent offrir une stabilité thermique moins robuste dans l'application finale.
Lors du choix de grades HPMC pour des applications thermiquement exigeantes, les fabricants doivent trouver un équilibre entre la facilité de mise en œuvre et les exigences de performances thermiques. Les applications nécessitant une exposition prolongée à des températures élevées bénéficient généralement de grades à viscosité plus élevée, tandis que celles privilégiant la facilité de mise en œuvre peuvent opter pour des alternatives à viscosité plus faible.
4. Qu'arrive-t-il au HPMC pendant le chauffage ?
Lorsque l'HPMC est chauffé, il subit une série de modifications physiques et chimiques distinctes, plutôt qu'une simple transition solide-liquide. Comprendre ce comportement thermique complexe est essentiel pour une manipulation et un traitement corrects des matériaux.
Ce que vous trouverez fascinant, c'est Le comportement unique de gélification thermique distingue l'HPMC de nombreux autres polymères. Ce phénomène crée à la fois des défis et des opportunités dans diverses applications.
La séquence de transformation thermique du HPMC se déroule comme suit :
Plage de température (°C) | État physique | Changements observables | événements moléculaires |
---|---|---|---|
25-50 | Poudre solide | Aucun changement visible | Mouvement moléculaire limité |
50-100 | Solide avec perte d'humidité | Perte de poids | Évaporation de l'eau, renforcement des liaisons hydrogène |
100-170 | Solide sec | Une légère décoloration commence | Relaxation initiale de la chaîne |
170-195 | Transition vitreuse | Adoucissement, adhérence accrue | Augmentation significative de la mobilité de la chaîne |
195-225 | État caoutchouteux | Déformation sous pression | Le démêlage de la chaîne commence |
225-230 | Fusion | Écoulement sous pression, la transparence change | Perte complète de la structure physique |
>230 | Fondu/en dégradation | Brunissement, réduction de la viscosité | Scission de chaîne, oxydation |
Lors du chauffage, l'HPMC présente un mécanisme unique de gélification thermique en solution aqueuse. À basse température, l'HPMC se dissout pour former des solutions limpides. À mesure que la température augmente (généralement autour de 65-80 °C selon le grade), la solution forme un gel grâce aux interactions hydrophobes entre les groupes méthoxy. Un chauffage supplémentaire entraîne finalement une précipitation.
Ce comportement de gélification thermique crée un système sensible à la température utile dans :
- Systèmes d'administration de médicaments à libération contrôlée
- Épaississants alimentaires sensibles à la température
- Des matériaux intelligents qui répondent aux changements environnementaux
Pour les considérations de traitement, les fabricants doivent tenir compte de plusieurs facteurs critiques :
- La température de transition vitreuse (Tg) représente le point où l'HPMC passe d'un état vitreux rigide à un état caoutchouteux plus flexible.
- La fenêtre de traitement se situe généralement entre Tg et 20-30°C en dessous du début de la dégradation
- Une exposition prolongée, même en dessous des températures de fusion, peut entraîner une dégradation progressive
- L'histoire thermique affecte le comportement thermique ultérieur
La compréhension de ces transitions permet aux processeurs d’optimiser les profils de température pendant la fabrication, évitant à la fois un chauffage insuffisant (conduisant à un traitement incomplet) et un chauffage excessif (provoquant une dégradation).
5. Comment les niveaux de substitution impactent-ils les propriétés de fusion du HPMC ?
Le schéma de substitution des groupes hydroxypropyle et méthoxy sur le squelette cellulosique détermine fondamentalement les propriétés thermiques de l'HPMC, notamment son comportement à la fusion. Ces substitutions perturbent les liaisons hydrogène dans la structure cellulosique native, modifiant ainsi les transitions thermiques et les caractéristiques de solubilité.
Le détail crucial à comprendre est Le rapport et la distribution de ces substituants peuvent être conçus avec précision pour obtenir des profils thermiques spécifiques à différentes applications. Cette capacité de personnalisation fait du HPMC un polymère exceptionnellement polyvalent.
Les types d'HPMC sont classés à l'aide d'un système de désignation USP/NF ou EP à quatre chiffres qui indique les niveaux de substitution :
Type HPMC | Teneur en méthoxyle (%) | Teneur en hydroxypropyle (%) | Plage de fusion typique (°C) | Caractéristiques thermiques |
---|---|---|---|---|
1828 | 16.5-20.0 | 23.0-32.0 | 215-225 | Point de fusion plus bas, plus hydrophile |
2208 | 19.0-24.0 | 4.0-12.0 | 220-230 | Propriétés thermiques équilibrées |
2906 | 27.0-30.0 | 4.0-7.5 | 225-235 | Point de fusion plus élevé, moins hydrophile |
2910 | 28.0-30.0 | 7.0-12.0 | 230-240 | Point de fusion le plus élevé |
La substitution méthoxyle influence principalement :
- Résistance thermique (une teneur plus élevée en méthoxyle augmente généralement le point de fusion)
- Solubilité des solvants organiques
- Activité de surface et propriétés interfaciales
Pendant ce temps, la substitution hydroxypropylique affecte :
- Solubilité dans l'eau (une teneur plus élevée en hydroxypropyle augmente la solubilité dans l'eau)
- Gélification à basse température de solution
- Flexibilité de la chaîne polymère
Le schéma de distribution de ces substituants le long de la chaîne cellulosique (en blocs ou aléatoire) influence également le comportement thermique. Des schémas de substitution plus hétérogènes entraînent généralement des plages de fusion plus larges qu'une substitution homogène.
Pour les applications nécessitant un contrôle thermique précis, les fabricants peuvent sélectionner des grades HPMC spécifiques ou même demander des modèles de substitution personnalisés à leurs fournisseurs. Cela permet d'affiner :
- Fenêtres de température de traitement
- Températures de gélification thermique
- Stabilité thermique pendant le stockage
- Caractéristiques de la viscosité à l'état fondu
La compréhension de ces relations structure-propriété permet aux formulateurs de sélectionner la qualité HPMC optimale pour les exigences spécifiques de traitement thermique, en équilibrant les besoins de performance et les contraintes de traitement.
6. Quelles sont les meilleures températures de traitement pour le HPMC ?
Déterminer les températures de traitement optimales pour l'HPMC nécessite de trouver un équilibre entre la transformation efficace du matériau et les risques de dégradation thermique. La plage de températures idéale varie considérablement en fonction du procédé de fabrication, de la qualité de l'HPMC et des caractéristiques souhaitées du produit final.
Voici ce qui compte le plus : Le respect de la fenêtre de sécurité de traitement permet d'éviter les problèmes de qualité et d'équipement tout en maximisant l'efficacité de la production. Cette fenêtre varie selon la méthode d'application.
Le tableau suivant décrit les plages de températures recommandées pour les méthodes de traitement HPMC courantes :
Méthode de traitement | Plage de température recommandée (°C) | Considérations critiques | Indicateurs de qualité |
---|---|---|---|
Extrusion à chaud | 140-180 | Temps de séjour, taux de cisaillement | Clarté, dégradation des couleurs |
Séchage par atomisation | Entrée : 170-210, Sortie : 70-100 | Paramètres d'atomisation | Morphologie des particules, teneur en humidité |
Casting de films | 60-90 | Taux de séchage, débit d'air | Uniformité du film, solvant résiduel |
Compression de comprimés | 20-30 | Force de compression | Dureté, temps de désintégration |
Granulation humide | 50-70 | Concentration du liant | Distribution granulométrique |
Applications de revêtement | 40-60 | Concentration de la solution | Uniformité du revêtement, adhérence |
Pour l'extrusion à chaud, un procédé thermique particulièrement exigeant, plusieurs facteurs influencent le profil de température optimal :
- Conception et configuration des vis
- Temps de séjour dans l'extrudeuse
- Présence de plastifiants ou d'autres additifs
- Type de substitution HPMC et grade de viscosité
- Caractéristiques de libération souhaitées du produit final
Pour éviter la dégradation thermique pendant le traitement, les fabricants doivent mettre en œuvre ces meilleures pratiques :
- Minimiser le temps de séjour à des températures élevées
- Utilisez des profils de température avec des augmentations progressives plutôt que des sauts soudains
- Incorporer des antioxydants lorsque cela est approprié
- Surveillez le couple et la pression pour détecter tout signe de dégradation
- Mettre en œuvre un refroidissement rapide après un traitement à haute température
- Valider chaque lot avec des techniques d'analyse thermique
La validation du processus doit inclure des tests pour :
- Changements de couleur (le jaunissement indique une dégradation)
- Réduction de la viscosité (scission de chaîne)
- Profils de dissolution modifiés
- Modifications des propriétés mécaniques
- Caractéristiques de sortie inattendues
En contrôlant soigneusement les températures de traitement dans les plages recommandées, les fabricants peuvent maintenir la fonctionnalité HPMC tout en obtenant les caractéristiques de produit et l'efficacité de traitement souhaitées.
7. Comment pouvez-vous tester et vérifier les propriétés de fusion du HPMC ?
Des tests et une vérification précis des propriétés thermiques de l'HPMC garantissent la cohérence des processus de fabrication et la performance du produit final. Plusieurs techniques d'analyse fournissent des informations complémentaires sur le comportement à la fusion, les transitions thermiques et la stabilité.
Ce que vous devez reconnaître, c'est Une caractérisation thermique complète nécessite plusieurs méthodes d'essai, car aucune technique ne permet à elle seule de saisir toutes les propriétés thermiques pertinentes. Cette approche multi-méthodes fournit un profil thermique complet pour le contrôle qualité et le dépannage.
Le tableau ci-dessous résume les principales méthodes d’analyse pour la caractérisation thermique de l’HPMC :
Méthode analytique | Informations fournies | Taille de l'échantillon | Plage de température (°C) | Principaux avantages |
---|---|---|---|---|
Calorimétrie différentielle à balayage (DSC) | Transition vitreuse, transitions de fusion, capacité thermique | 2 à 10 mg | -90 à 550 | Haute sensibilité aux transitions thermiques |
Analyse thermogravimétrique (ATG) | Perte de poids, température de décomposition, teneur en humidité | 5 à 20 mg | 25 à 1000 | Quantifie la dégradation et l'humidité |
Analyse mécanique dynamique (DMA) | Propriétés viscoélastiques, le module change avec la température | 10 à 500 mg | -150 à 500 | Mesure les changements de propriétés mécaniques |
Microscopie à platine chauffante | Changements visuels pendant le chauffage | <1 mg | 25 à 350 | Observation directe des changements physiques |
Rhéométrie | Viscosité à l'état fondu, température de gélification | 1 à 2 g | -20 à 300 | Mesure les propriétés d'écoulement pendant le chauffage |
Pour le contrôle qualité de routine, la DSC et l'ATG sont les plus couramment utilisées. Un protocole DSC standard pour l'HPMC comprend généralement :
- Équilibrage de l'échantillon à 25°C
- Premier balayage de chauffage à 250°C à 10°C/min
- Refroidissement à 25°C à 20°C/min
- Deuxième balayage de chauffage à 250°C à 10°C/min (révèle les effets de l'historique thermique)
Lors de l'interprétation des résultats d'analyse thermique, les paramètres clés à évaluer comprennent :
- Température de transition vitreuse (Tg) : Généralement 170-195 °C pour le HPMC
- Début de fusion : Généralement 10 à 15 °C en dessous de la température de fusion maximale
- Température de fusion maximale : généralement 225-230 °C pour les nuances standard
- Enthalpie de fusion : indique le degré d'organisation dans la structure du polymère
- Début de dégradation : Doit être > 270 °C pour un matériau de haute qualité
Les scénarios de dépannage courants pour un comportement de fusion incohérent incluent :
- Températures de fusion décalées : indique souvent des variations de teneur en humidité ou des modèles de substitution différents
- Pics de fusion élargis : peuvent suggérer des changements dans la distribution du poids moléculaire ou une dégradation partielle
- Enthalpie de fusion réduite : pourrait indiquer un historique thermique antérieur ou des dommages liés au traitement
- Début précoce de la dégradation : problèmes potentiels de contamination ou d'oxydation
L'établissement de limites de spécification pour les propriétés thermiques garantit la cohérence d'un lot à l'autre et aide à identifier les problèmes de fabrication potentiels avant qu'ils n'affectent les performances du produit final.
Conclusion
Comprendre le comportement précis de fusion de l'HPMC, généralement compris entre 225 et 230 °C, avec des transitions thermiques plus précoces commençant autour de 170 °C, permet aux fabricants d'acquérir les connaissances nécessaires à un traitement optimal et au développement d'applications. En identifiant l'impact des grades de viscosité, des schémas de substitution et des conditions de traitement sur les propriétés thermiques, vous pouvez éviter les défaillances de fabrication coûteuses et les problèmes de stabilité des produits. Les méthodes complètes de tests thermiques décrites ici permettent un contrôle qualité et un dépannage précis. Pour des conseils d'experts sur le choix et le traitement du grade d'HPMC adapté à vos exigences thermiques spécifiques, contactez l'équipe technique de Morton dès aujourd'hui. Nos scientifiques spécialisés en polymères peuvent vous aider à développer des formulations HPMC personnalisées avec des profils thermiques précisément conçus pour répondre aux besoins de vos applications les plus exigeantes.
Rubrique FAQ
Q1 : Le HPMC peut-il résister aux températures de stérilisation en autoclave ?
Les grades HPMC standard ne supportent généralement pas les conditions d'autoclave (121 °C, vapeur sous pression) sans se dégrader. Bien que le polymère ne fonde pas complètement à la température de l'autoclave, une exposition prolongée peut entraîner une dégradation partielle, une baisse de viscosité et une altération des performances. Pour les applications nécessitant une stérilisation, envisagez d'utiliser des grades à teneur en méthoxyle plus élevée (2906 ou 2910) ou d'autres méthodes de stérilisation comme l'irradiation gamma ou le traitement à l'oxyde d'éthylène.
Q2 : Le point de fusion du HPMC change-t-il lorsqu'il est mélangé à d'autres polymères ?
Oui, le mélange de l'HPMC avec d'autres polymères modifie généralement son comportement à la fusion. Les polymères compatibles peuvent créer des mélanges miscibles avec des points de fusion intermédiaires entre les deux composants. Les plastifiants comme le polyéthylène glycol ou la glycérine abaissent la transition vitreuse et les températures de fusion apparente en augmentant la mobilité des chaînes. Les polymères incompatibles forment des systèmes à phases séparées avec des transitions thermiques distinctes pour chaque composant. Ces interactions doivent être évaluées au cas par cas par une analyse thermique de la composition du mélange spécifique.
Q3 : Comment la teneur en humidité affecte-t-elle le comportement de fusion du HPMC ?
L'humidité a un impact significatif sur le comportement thermique de l'HPMC en agissant comme plastifiant. Une teneur en humidité plus élevée abaisse la température de transition vitreuse et peut réduire le point de fusion apparent de 10 à 20 °C. Les molécules d'eau perturbent les liaisons hydrogène entre les chaînes polymères, augmentant ainsi la mobilité moléculaire à basse température. Pour un traitement thermique homogène, la teneur en humidité doit être normalisée, généralement inférieure à 5%. Un séchage adéquat avant l'analyse thermique ou le traitement garantit des résultats reproductibles et prévient les problèmes de traitement tels que la formation de mousse ou une fusion irrégulière.
Q4 : Que se passe-t-il si l'HPMC est traité au-dessus de son point de fusion ?
Le traitement de l'HPMC au-dessus de son point de fusion (> 230 °C) entraîne une dégradation thermique rapide par scission de chaîne, oxydation et décoloration. Cette dégradation entraîne une diminution du poids moléculaire, une diminution de la viscosité de la solution, une altération des profils de dissolution et la formation de produits de dégradation potentiellement nocifs. Le matériau passe du blanc au jaune-brun et perd ses propriétés fonctionnelles. La récupération est impossible une fois la dégradation effectuée. Maintenez toujours les températures de traitement au moins 30 à 50 °C en dessous du point de fusion, avec un temps de séjour minimal à des températures élevées afin de préserver la fonctionnalité de l'HPMC.
Q5 : Existe-t-il des différences significatives de point de fusion entre les fournisseurs de HPMC ?
Oui, les HPMC de différents fournisseurs peuvent présenter des variations de point de fusion de 5 à 15 °C malgré des désignations de grade identiques. Ces différences proviennent de variations dans les procédés de fabrication, l'uniformité des schémas de substitution, la distribution des masses moléculaires et les niveaux de pureté. Lors d'un changement de fournisseur, effectuez systématiquement une analyse thermique comparative afin d'identifier les ajustements de traitement nécessaires. Les fournisseurs pharmaceutiques ou alimentaires établis appliquent généralement des spécifications et une cohérence d'un lot à l'autre plus strictes que les fournisseurs industriels généraux, ce qui les rend préférables pour les applications thermosensibles.