Trouver le bon additif pour vos formulations de revêtement peut faire toute la différence en termes de qualité. De nombreux fabricants de revêtements sont confrontés à une mauvaise adhérence et à une application irrégulière. Sans additifs appropriés, les revêtements peuvent se détériorer prématurément, ce qui entraîne des réclamations clients et des réparations coûteuses.
L'HPMC offre une solution à ces problèmes de revêtement. Il améliore l'écoulement, la formation du film et le pouvoir collant. Des tests montrent qu'un HPMC approprié peut prolonger la durée de vie du revêtement jusqu'à 40% dans des conditions difficiles.
Examinons le fonctionnement de ce polymère dans les revêtements. Nous aborderons ses effets sur l'écoulement, la formation de film, le pouvoir adhésif et le blocage de l'eau. Nous vous aiderons également à choisir le grade le mieux adapté à vos besoins.
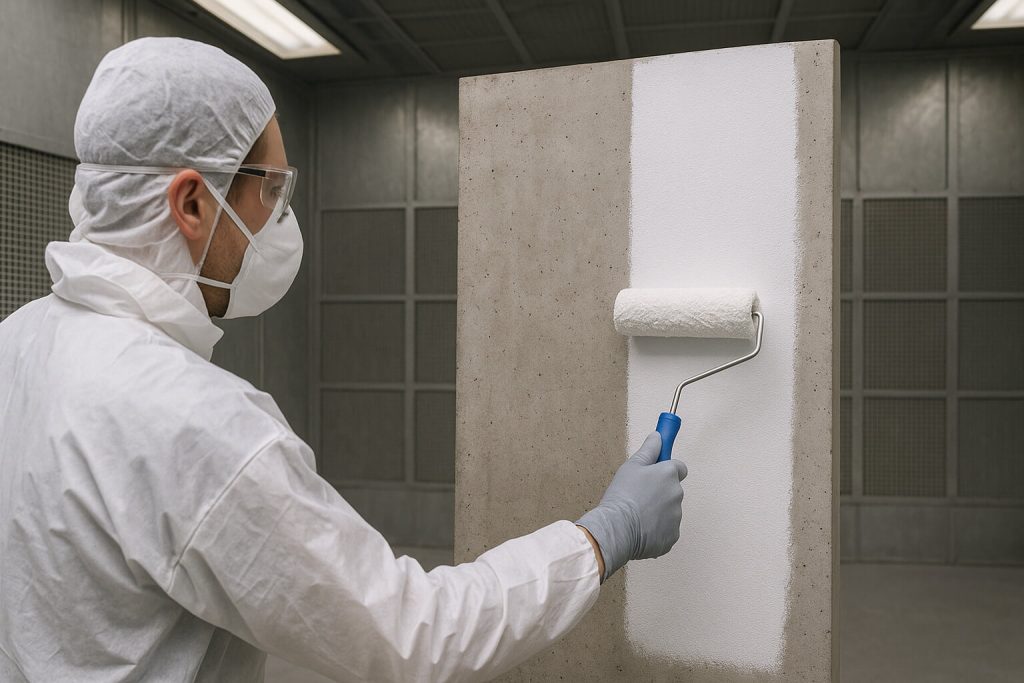
1. Qu’est-ce que l’HPMC et pourquoi est-il utilisé dans les revêtements ?
HPMC signifie Hydroxypropylméthylcellulose. Il est obtenu à partir de cellulose naturelle par transformation chimique. Le matériau de base est traité avec deux produits chimiques pour créer un composé utile. Vous voulez savoir ce qui le rend spécial ? Cette structure unique confère au polymère un bon mélange avec l'eau tout en formant des films.
Les fabricants ajoutent ce type de cellulose aux revêtements principalement comme épaississant et liant. Il permet de contrôler l'écoulement des revêtements à base d'eau, ce qui facilite leur application et les rend plus stables au stockage. Les chaînes polymères forment un réseau qui maintient les pigments et autres composants en place.
Cet additif est efficace dans les peintures murales, les revêtements pour béton et les colles à carrelage. Non toxique, il est donc sans danger pour les revêtements destinés au contact alimentaire, là où la sécurité est primordiale.
Comparé aux autres types de cellulose, ce polymère présente plusieurs avantages. Il se mélange plus facilement à l'eau froide que la méthylcellulose. Contrairement à la CMC, il est efficace sur une plage de pH plus large.
Propriété | HPMC | CMC | Méthylcellulose |
---|---|---|---|
Mélange d'eau | Excellent (eau froide) | Bon (à mélanger) | Bon (nécessite de l'eau chaude) |
Stabilité du pH | 2-12 | 4-9 | 3-11 |
Film Flex | Haut | Moyen | Moyen |
Tolérance au sel | Bien | Pauvre | Moyen |
Valeur du coût | Moyen | Haut | Haut |
Le poids de cette cellulose varie de 10 000 à 1 500 000 unités. Cela permet aux fabricants de choisir des qualités présentant des profils d'écoulement spécifiques. Les qualités plus légères offrent un bon mouillage, tandis que les qualités plus lourdes produisent des films plus résistants.
2. Comment l'HPMC affecte-t-il la viscosité et les propriétés d'écoulement du revêtement ?
Cette cellulose modifie l'écoulement du revêtement grâce à un processus simple : ajoutées à l'eau, ses molécules s'imprègnent d'eau et gonflent. Vous pourriez être surpris d'apprendre Cet épaississement se produit sans modification chimique, ce qui permet à l'additif de bien se mélanger aux autres composants du revêtement.
À faible dose (0,1-0,5%), le polymère épaissit légèrement. À mesure que l'on ajoute de la 1-2%, l'épaisseur augmente considérablement. Cela crée un mélange gélatineux qui empêche les coulures sur les parois. Cela permet aux fabricants d'affiner les caractéristiques du revêtement.
La chaleur joue un rôle essentiel dans le fonctionnement de cet additif. La plupart des grades s'épaississent à mesure que la chaleur augmente jusqu'à se gélifier. Cela permet aux revêtements de rester épais même par temps chaud.
Montant | Effet d'épaisseur | Utiliser l'avantage |
---|---|---|
0.1-0.5% | Épaississement léger | Meilleure tenue des pigments |
0.5-1.0% | Épaississement moyen | Meilleur flux et soirée |
1.0-2.0% | Épaississement élevé | Pas de gouttes sur les murs |
2.0-3.0% | Mélange gélatineux | Création de textures |
>3.0% | Très forte épaisseur | Utilisations spéciales épaisses |
La cellulose prévient les problèmes courants comme les coulures. Le polymère maintient le revêtement en place jusqu'à l'application de la force. Cela permet au revêtement de bien s'étaler lors de l'application au pinceau ou au rouleau, tout en restant en place après.
Les propriétés d'écoulement de ces revêtements les rendent parfaits pour une application par pulvérisation. Sous l'effet d'une force élevée dans les outils de pulvérisation, l'épaisseur diminue, facilitant ainsi la pulvérisation. Une fois appliqué sur le mur, le revêtement se raffermit rapidement pour éviter les coulures.
Pour un résultat optimal, mélangez bien l'additif avant d'ajouter les autres ingrédients. Ajoutez de l'eau froide avant de chauffer pour éviter les grumeaux. Certains fabricants proposent des qualités spéciales qui facilitent le mélange.
3. Qu’est-ce qui fait du HPMC un agent filmogène efficace dans les revêtements ?
Cette cellulose permet de former des films par séchage plutôt que par fixation chimique. Lorsque l'eau s'échappe du revêtement, les molécules se rapprochent et se lient, formant ainsi un film solide. La partie fascinante est Ces films se forment sans liant supplémentaire, ce qui simplifie les mélanges de revêtement.
La résistance des films varie en fonction de la taille des molécules. Les films de poids supérieur sont plus résistants et plus extensibles. La plupart des films offrent une bonne flexibilité sans ajout supplémentaire, bien que certains fabricants en ajoutent de petites quantités pour améliorer cette propriété.
La rétention d'eau pendant le séchage est l'une des caractéristiques les plus utiles. Le polymère ralentit la perte d'eau, ce qui laisse plus de temps pour l'uniformisation et la formation d'un film correct. Cela évite les imperfections dues à un séchage trop rapide par temps chaud ou venteux.
Trait du film | Grades de faible poids | Grades de poids moyen | Grades de poids élevé |
---|---|---|---|
Force | Faible | Moyen | Haut |
Fléchir | Haut | Moyen | Moyen-faible |
Rétention d'eau | Faible | Moyen | Haut |
Remixage | Haut | Moyen | Faible |
Clarté du film | Haut | Moyen | Moyen-faible |
De nombreux facteurs influencent la qualité de ces films. L'humidité de l'air pendant l'utilisation modifie considérablement le temps de séchage. La porosité de la surface est également importante : des parois très poreuses peuvent absorber l'eau trop rapidement. Il faut donc ajouter davantage d'additifs pour assurer une bonne formation du film.
L'homogénéité du film dépend du choix du polymère approprié. Une quantité insuffisante peut entraîner une couverture irrégulière. Une quantité excessive peut provoquer des fissures lors du séchage. La plupart des mélanges de revêtement utilisent 0,3 à 1,51 TP3T en poids pour obtenir les meilleures propriétés du film.
Les films offrent une bonne rétention des huiles tout en restant relativement ouverts à l'eau grâce à leur nature. Cette propriété hydrofuge est particulièrement utile pour les applications nécessitant une décomposition ou un nettoyage à l'eau.
4. Comment le HPMC améliore-t-il l’adhérence du revêtement à différents substrats ?
La cellulose favorise l'adhérence du revêtement de plusieurs manières à la fois. Le polymère forme des liaisons avec les parois superficielles, créant ainsi des points d'ancrage pour le revêtement. Ce que vous devez savoir, c'est ces liaisons fonctionnent très bien sur les matériaux contenant des groupes hydroxyles, comme le bois et le béton.
Sur les murs poreux comme le béton, l'additif permet de contrôler l'enfoncement du revêtement. Il empêche un affaissement excessif tout en laissant suffisamment de place pour créer une adhérence solide. Cet enfoncement équilibré permet une meilleure couverture et une adhérence plus forte.
Le polymère agit différemment sur différents types de murs. Sur le métal, il offre une adhérence moyenne, principalement par formation de film. Sur le bois, il excelle en se liant aux fibres et en contrôlant le flux d'humidité.
Type de mur | Méthode du bâton | À quel point cela fonctionne bien | Meilleure note |
---|---|---|---|
Béton/Pierre | Contrôle du trempage, collage | Très élevé | Épaisseur moyenne-élevée |
Bois | Liaison des fibres, contrôle de l'humidité | Haut | Épaisseur moyenne |
Métal | Formation de film, Adhésion physique | Moyen | Épaisseur faible-moyenne |
Verre | Mouillage de surface, résistance du film | Moyen | Faible épaisseur |
Plastique | Mouillage de surface, Film flexible | Faible-Moyen | Faible épaisseur avec extras |
Dans les mélanges d'apprêt, cette cellulose est un excellent agent d'adhérence. Elle contribue à créer une couche souple entre le mur et la couche de finition. Cette flexibilité est très utile en extérieur, où les variations de température provoquent la dilatation et le rétrécissement des murs.
Les tests d'adhérence de ces revêtements comprennent des tests de ruban adhésif et des tests d'arrachement. La plupart des revêtements contenant de la cellulose 20-30% présentent de meilleurs résultats d'adhérence que les mélanges sans cellulose.
Pour les parois dures comme les plastiques ou les métaux, mélanger le polymère avec des agents d'adhérence spéciaux donne de meilleurs résultats. Certains agents sont compatibles avec les systèmes de revêtement métallique. D'autres renforcent la cellulose pour les parois en plastique.
5. Quel rôle joue le HPMC dans la résistance à l’eau et la durabilité ?
La cellulose contribue à bloquer l'eau du revêtement grâce à ses caractéristiques de film, bien que son effet soit mitigé. Voici le point clé : tandis que l'additif se mélange à l'eau, lorsqu'il est correctement mélangé avec d'autres liants, il forme des films qui bloquent bien l'eau après séchage complet.
Les propriétés barrières contre l'humidité dépendent de la composition chimique. Une teneur élevée en méthoxyle permet d'obtenir des films plus hydrofuges. La plupart des mélanges de revêtements utilisent des grades dont la teneur en méthoxyle se situe entre 19 et 30% afin d'équilibrer les propriétés hydrofuges avec d'autres propriétés.
La résistance à long terme de ces revêtements dépend d'un mélange approprié. Associé à des liants acryliques ou vinyliques, le polymère permet d'obtenir des revêtements d'une durée de vie de 5 à 7 ans en conditions extérieures normales. La flexibilité de l'additif réduit la fissuration au fil du temps.
Type de météo | Effet sur le revêtement | Impact sur la durabilité | Méthode de correction |
---|---|---|---|
Humidité élevée | Séchage plus lent, peut ramollir | Chute moyenne | Utiliser des qualités de méthoxyle supérieures |
Lumière UV | Faible effet direct sur le polymère | Faible impact | Mélanger avec des liants bloquant les UV |
Gel/Dégel | Stress possible du film | Chute moyenne | Ajouter des assistants flexibles |
Sel | Faible effet sur le polymère lui-même | Faible impact | Utilisez des produits antirouille pour la sécurité des murs |
Pluie acide | Rupture possible du polymère | Chute moyenne | Tampon avec charges basiques |
Les propriétés de résistance aux intempéries de ces revêtements donnent de bons résultats sous des climats doux. Le polymère permet aux revêtements de résister aux fissures lors des variations de température en restant flexibles. Cependant, dans des conditions difficiles, des renforts supplémentaires peuvent être nécessaires.
L'équilibre entre le mélange et le blocage de l'eau est un défi majeur. Lors de l'utilisation, le mélange à l'eau confère une excellente maniabilité. Après séchage, le polymère s'intègre à un système de film complet. D'autres liants assurent le blocage de l'eau, tandis que la cellulose renforce la résistance du film.
Pour les applications nécessitant une imperméabilisation optimale, les fabricants utilisent souvent la cellulose avec des liants ou des agents d'étanchéité hydrophobes. Cela permet de conserver une bonne fluidité et une bonne filmification tout en obtenant l'imperméabilisation souhaitée.
6. Comment les fabricants peuvent-ils optimiser les qualités HPMC pour des applications de revêtement spécifiques ?
Pour choisir la bonne qualité, il faut connaître les spécifications de débit et les besoins d'utilisation. La vérité est cette qualité d'écoulement, mesurée en unités au mélange 2%, sert de principal facteur de sélection pour la plupart des utilisations de revêtement.
Les grades à faible fluidité (3 à 15 unités) sont particulièrement adaptés aux applications par pulvérisation et aux revêtements fins. Les grades à fluidité moyenne (15 à 50 unités) offrent de bons résultats polyvalents au pinceau et au rouleau. Les grades à fluidité élevée (50 à 100 unités et plus) sont excellents pour stopper les coulures sur les murs.
La composition chimique a un impact considérable sur les résultats du revêtement. La teneur en méthoxyle affecte le mélange avec l'eau et les caractéristiques du film. La teneur en hydroxypropyle affecte l'action de surface et le mélange avec d'autres composants. La plupart des applications de revêtement nécessitent une cellulose avec une teneur en méthoxyle de 19 à 241 TP3T et une teneur en hydroxypropyle de 7 à 121 TP3T.
Type d'utilisation | Meilleur flux | Meilleur mélange chimique | Trait clé |
---|---|---|---|
Peinture murale intérieure | 15 à 40 unités | Méthoxyle moyen, hydroxypropyle moyen | Bonne maniabilité, faible projection |
Revêtement extérieur en pierre | 30 à 80 unités | Teneur élevée en méthoxyle et moyennement en hydroxypropyle | Blocage des intempéries, bâton |
Mortier de fixation pour béton | 50 à 100+ unités | Méthoxyle moyen, hydroxypropyle élevé | Rétention d'eau, blocage des gouttes |
Colle à carrelage | 40 à 80 unités | Méthoxyle moyen, hydroxypropyle élevé | Temps ouvert, blocage par glissement |
Texture de pulvérisation | 15 à 30 unités | Teneur élevée en méthoxyle et faible en hydroxypropyle | Maintien des modèles, pompabilité |
Le mélange avec d'autres composants du revêtement doit être pris en compte lors du choix de la cellulose. Ce polymère est compatible avec la plupart des liants aqueux, comme les acryliques et les vinyles. Cependant, les mélanges fortement chargés peuvent provoquer un agglomérat avec certains types de matériaux.
Les conseils de fabrication incluent des méthodes de mélange appropriées. Pour un résultat optimal, ajoutez l'additif à l'eau avant d'ajouter les pigments. Certains fabricants proposent des mélanges à l'eau froide qui mouillent plus lentement, facilitant ainsi l'ajout aux mélanges de revêtement.
La stabilité thermique pendant le stockage influence la récolte. Les qualités standard assurent un écoulement stable entre 5 et 40 °C. Cependant, des qualités spéciales existent pour les températures extrêmes. La plupart des mélanges d'enrobage bénéficient de qualités offrant des résultats stables malgré les variations de température saisonnières.
Le rapport coût-efficacité joue également un rôle dans le choix des qualités. Les qualités à haut débit coûtent souvent plus cher au kilo, mais peuvent être utilisées en quantités moindres. Une analyse complète du coût d'utilisation montre souvent que les qualités à débit moyen offrent le meilleur compromis entre résultats et économies.
Conclusion
L'HPMC améliore les résultats des revêtements grâce à ses nombreuses propriétés : épaississant, filmogène et agent d'adhérence. En contrôlant l'écoulement, cette cellulose permet de créer des revêtements lisses et uniformes, résistants aux coulures et offrant une excellente couverture. Ses propriétés filmogènes prolongent la durée de vie des revêtements, tandis que ses propriétés d'adhérence garantissent une adhérence solide sur de nombreuses parois. Des tests montrent que ces additifs peuvent prolonger la durée de vie des revêtements de 25 à 401 TP3T dans des conditions difficiles. Morton propose des grades spéciaux spécialement conçus pour les revêtements, avec une assistance technique pour vous aider à choisir le grade le mieux adapté à vos besoins. Contactez les experts en revêtement de Morton dès aujourd'hui pour demander des échantillons et obtenir de l'aide pour le mélange de vos revêtements.
Rubrique FAQ
Q1 : Quelle concentration de HPMC est généralement utilisée dans les formulations de revêtement ?
La plupart des mélanges de revêtements utilisent cette cellulose à des concentrations comprises entre 0,31 TP3T et 2,01 TP3T en poids, selon l'usage et les caractéristiques recherchées. Les peintures d'intérieur utilisent souvent 0,3 à 0,71 TP3T, tandis que les revêtements texturés peuvent en utiliser jusqu'à 1,5 à 2,01 TP3T pour une meilleure épaisseur et une meilleure rétention d'eau.
Q2 : Le HPMC peut-il être utilisé dans les systèmes de revêtement à base d'eau et à base de solvant ?
Ce polymère est principalement utilisé dans les systèmes de revêtement à base d'eau grâce à sa capacité de mélange avec l'eau. Il se mélange très peu aux solvants organiques, ce qui le rend inadapté à la plupart des mélanges à base de solvants. Pour les systèmes à base de solvants, d'autres types de cellulose, comme la nitrocellulose, sont plus adaptés.
Q3 : Comment le HPMC se compare-t-il aux autres éthers de cellulose comme le CMC dans les applications de revêtement ?
Le HPMC offre plusieurs avantages par rapport au CMC pour les revêtements, notamment une meilleure stabilité du pH, une meilleure gestion des sels et un blocage enzymatique. Il offre également une meilleure flexibilité du film et une meilleure action de surface. Cependant, le CMC peut offrir un épaississement plus fort à moindre coût dans les applications où ces autres caractéristiques sont moins importantes.
Q4 : Le HPMC affecte-t-il le temps de séchage des revêtements ?
Oui, cette cellulose prolonge souvent le temps de séchage des revêtements grâce à ses propriétés de rétention d'eau. Cela peut contribuer à améliorer l'uniformité et à prévenir les imperfections dues à un séchage trop rapide, notamment par temps chaud ou sec. L'effet sur le temps de séchage varie selon le grade et la quantité, les grades d'écoulement les plus élevés entraînant un allongement du temps de séchage.
Q5 : Existe-t-il des exigences de stockage particulières pour les revêtements contenant du HPMC ?
Les revêtements contenant cet additif doivent être conservés entre 5 °C et 40 °C pour rester stables. La congélation doit être évitée, car elle peut entraîner des modifications durables de la structure du polymère et nuire aux résultats du revêtement. Les récipients doivent être maintenus fermés pour éviter la formation d'une peau due à la perte d'eau. La plupart des mélanges contenant de la cellulose bien conservée ont une durée de conservation de 12 à 24 mois selon ces règles.