Les fabricants de revêtements sont confrontés à de graves problèmes de stabilité des produits et de qualité des films. Lorsque les revêtements sont défectueux, vous gaspillez de l'argent en réparations. Vous vous exposez également à des clients mécontents. Des revêtements de mauvaise qualité entraînent des retards, des coûts plus élevés et nuisent à votre marque. L'HPMC offre une solution en améliorant l'efficacité des revêtements. Il favorise la rétention d'eau et la formation de film. Des tests montrent qu'un bon HPMC peut prolonger la durée de vie du revêtement 40% et réduire les défauts. Cet article explique comment l'HPMC améliore l'efficacité des revêtements sur de nombreuses surfaces.
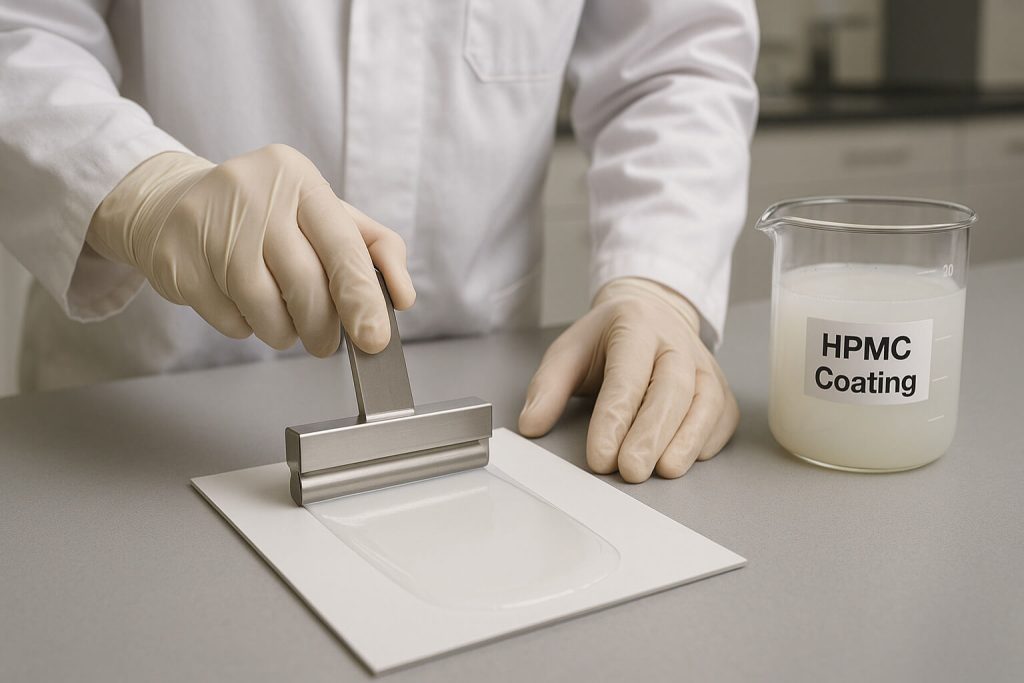
1. Quelles sont les propriétés de base de l’hydroxypropylméthylcellulose dans les revêtements ?
L'HPMC est une fibre végétale modifiée issue des arbres. Des groupes spécifiques ont été ajoutés à sa base fibreuse. Cette composition unique lui confère ses excellentes propriétés pour les revêtements.
Mais qu’est-ce qui le rend si efficace ? L'HPMC peut se mélanger à l'eau et former des films. Ajouté aux revêtements, l'HPMC se décompose dans l'eau à température ambiante. Le mélange est alors limpide et sans grumeaux.
La taille de l'HPMC influence son efficacité dans les revêtements. Les plus gros formats produisent des mélanges plus épais. Les plus petits formats s'écoulent mieux, mais retiennent moins d'eau.
L'HPMC se présente sous de nombreuses formes. La partie méthyle est souvent 19-30%. La partie hydroxypropyle est 7-12%. Ces ratios modifient son interaction avec l'eau et les autres composants du revêtement.
L'un des principaux avantages du HPMC est sa capacité à geler à chaud. Contrairement à de nombreux produits qui se fluidifient à chaud, les mélanges HPMC forment des gels courts à haute température. Cela évite les coulures pendant l'utilisation et le séchage.
Trait | HPMC à faible épaisseur | HPMC d'épaisseur moyenne | HPMC à haute épaisseur |
---|---|---|---|
Épaisseur | 5 à 100 mPa·s | 100 à 5 000 mPa·s | 5 000 à 100 000 mPa·s |
Rétention d'eau | Faible | Moyen | Haut |
Profondeur du film | Mince | Moyen | Épais |
Lutte contre les gouttelettes | Faible | Moyen | Haut |
Traits lisses | Super | Bien | Équitable |
Le travail de surface du HPMC contribue également à la réussite du revêtement. Bien qu'il ne s'agisse pas d'un véritable savon, le HPMC réduit légèrement l'arrachement de surface. Cela permet aux revêtements de mieux mouiller les surfaces.
Lorsque l'on associe le HPMC à d'autres types de fibres, des écarts apparaissent. Le HPMC retient mieux l'eau que le MC. Il combat mieux les bactéries que le HEC. Il permet également de produire des films plus flexibles que le CMC.
La granulométrie de la poudre HPMC influence sa vitesse de décomposition. Les poudres finement broyées se décomposent plus rapidement, mais peuvent produire davantage de poussière. Les poudres grossières produisent moins de poussière, mais nécessitent un mélange plus important pour se décomposer.
2. Comment le HPMC affecte-t-il la viscosité et l’application du revêtement ?
Le lien entre la quantité de HPMC et l'épaisseur du revêtement est clair. Plus on en ajoute, plus l'épaisseur augmente rapidement. Cela permet aux fabricants d'effectuer d'importantes variations d'épaisseur avec de faibles variations de HPMC.
Voici la partie intéressante : L'HPMC confère aux revêtements une fluidité particulière. Leur épaisseur diminue à mesure que l'on agite plus vite. L'application au pinceau fluidifie le revêtement pour une application plus facile. Une fois appliqué, le revêtement redevient épais et évite les coulures.
La taille du type HPMC a un impact direct sur cette finesse. Les types plus grands présentent davantage cet effet. Les types plus petits s'écoulent davantage comme de l'eau.
La chaleur a un impact important sur les revêtements HPMC lors de leur utilisation. En dessous du point de gélification (souvent entre 50 et 70 °C), l'épaisseur diminue à mesure que la température augmente. Au-delà, un gel court se forme, ce qui peut nuire à la pulvérisation si les outils chauffent trop.
Méthode d'utilisation | Meilleur type de HPMC | Montant typique | Gain principal |
---|---|---|---|
Utilisation par pulvérisation | Faible épaisseur | 0.1-0.5% | Arrête les obstructions, aide à pulvériser |
Utilisation du rouleau | Épaisseur moyenne | 0.3-0.8% | Réduit le désordre, aide à se déplacer |
Utilisation du pinceau | Épais moyen-élevé | 0.5-1.0% | Arrête les gouttes, aide à ramasser |
Revêtement par immersion | Faible-moyennement épais | 0.2-0.6% | Définit la profondeur de la couche, coupe les passages |
Revêtement de rideau | Épaisseur moyenne | 0.3-0.7% | Maintient le rideau, aide à uniformiser le pelage |
Le pH du mélange de revêtement influence l'action épaississante de l'HPMC. L'HPMC maintient une épaisseur constante entre 3 et 11 pH. Il est donc adapté aux revêtements acides et basiques.
Pour contrôler l'épaisseur de l'HPMC, il est conseillé de le prémélanger à l'eau chaude avant refroidissement. L'ajout d'HPMC à l'eau avant l'ajout des couleurs permet d'éviter les taches sèches dans le revêtement final.
Un cas réel, réalisé par un grand fabricant de peinture, a démontré que l'utilisation du HPMC a permis de réduire les coûts de 15%. Le mélange a néanmoins bien fonctionné. Le revêtement HPMC présentait une meilleure résistance à la brosse et moins de salissures lors de l'utilisation au rouleau.
La durée de conservation des revêtements HPMC dépend d'une bonne gestion des insectes. Si le HPMC lui-même combat les insectes, les mélanges d'eau et de HPMC nécessitent des insecticides pour empêcher la perte d'épaisseur pendant le stockage.
3. Quel rôle joue l’HPMC dans la rétention d’eau des revêtements ?
La rétention d'eau est la caractéristique la plus utile de l'HPMC pour les mélanges de revêtement. Les composants de la base fibreuse forment un réseau hydrophile qui retient les particules d'eau. Ce réseau ralentit la perte d'eau lors du séchage.
Vous pourriez être choqué d'apprendre La rétention d'eau a un effet direct sur la qualité du revêtement. Lorsqu'un revêtement perd trop rapidement son eau sur une surface poreuse comme les cloisons sèches, de nombreux problèmes apparaissent : faible adhérence, aspect irrégulier et durée de vie réduite.
Le HPMC retient l'eau grâce aux liaisons entre les particules d'eau et les groupes présents sur la fibre. Ces liaisons emprisonnent l'eau dans le film de revêtement. À mesure que le revêtement sèche, ces liaisons se rompent progressivement, libérant ainsi l'eau de manière régulière.
Le degré de modification de l'HPMC affecte sa capacité de rétention d'eau. Plus la modification est importante, plus la capacité de rétention d'eau est importante. La partie méthyle affecte la température à laquelle la fibre commence à perdre sa capacité de rétention d'eau.
Type de base | Gain de rétention d'eau | Meilleur type de HPMC | Dose typique |
---|---|---|---|
Très poreux (béton) | Arrête le séchage prématuré | Haute épaisseur | 0.8-1.2% |
Mi-poreux (cloisons sèches) | Règle le débit d'eau | Épaisseur moyenne | 0.5-0.9% |
Non poreux (métal) | Aide à lisser le temps | Faible-moyennement épais | 0.3-0.6% |
Mixte Poreux | Rend le taux de séchage uniforme | Épaisseur moyenne | 0.5-0.8% |
États chauds/secs | Empêche la formation de peau | Haute épaisseur | 0.7-1.1% |
Parmi les méthodes permettant de tester les caractéristiques de rétention d'eau, on peut citer le test DIN, qui vérifie la perte d'eau sous vide, et le test ASTM, qui vérifie la perte d'eau sur une base assoiffée. Ces deux tests aident les fabricants à choisir le type d'HPMC le plus adapté.
Un essai pratique sur des revêtements muraux a montré qu'une plus grande quantité de HPMC allongeait le temps de travail du 40% à chaud et à sec. Cela permettait aux utilisateurs de conserver un bord humide et d'éviter les marques lors de travaux importants.
L'effet de rétention d'eau du HPMC contribue également à répartir les particules de couleur pendant le séchage. En ralentissant le débit d'eau, le HPMC empêche le flottement de la couleur, source de variations de couleur.
La taille de l'HPMC est liée à sa capacité de rétention d'eau. Les plus gros types forment davantage de réseaux de liaison, ce qui permet de piéger davantage de particules d'eau dans le film de revêtement pendant l'utilisation et les premières étapes de séchage.
4. Comment le HPMC influence-t-il l’adhérence du revêtement à différents substrats ?
L'adhérence est une caractéristique essentielle de tout revêtement, et l'HPMC a un impact majeur sur la liaison des revêtements aux bases. Cette adhérence se manifeste principalement par la formation de liaisons entre les groupes de l'HPMC et les surfaces de la base. Ces liaisons assurent une forte adhérence initiale lors de l'utilisation.
Vous voulez savoir quelque chose de cool ? L'HPMC favorise l'adhérence de différentes manières en fonction des pores du support. Sur les supports poreux, l'HPMC permet au revêtement de pénétrer dans les aspérités du support avant la prise. Sur les supports lisses, il ralentit le temps de séchage, ce qui permet un meilleur mouillage et une meilleure adhérence.
La structure compacte du HPMC possède des éléments hydrophiles et hydrophiles. Cette double nature lui permet de servir de pont entre la résine de revêtement et les bases résistantes. Les groupes méthyles forment des liaisons hydrophiles, tandis que les groupes hydroxyles forment des liaisons hydrophiles.
Sur les surfaces en béton et les murs, les revêtements HPMC 30-50% affichent une meilleure adhérence que les revêtements ordinaires. Cette amélioration est due à un débit d'eau constant qui empêche le revêtement de sécher trop vite.
Base | Test du bâton | Comment HPMC aide | Gain testé |
---|---|---|---|
Béton | Très basique, poreux | Régule le débit de l'eau, combat les effets du pH | 40-50% résistance à l'arrachement supérieure |
Bois | Pores mixtes, huiles végétales | Fixe la pénétration, bloque le flux d'huile végétale | 25-35% meilleur bâton de hachures croisées |
Métal | Lisse, non poreux | Allonge le temps de mouillage pour un meilleur mouillage | 15-25% meilleur combat direct |
Verre | Très doux, aime l'eau | Liens polaires Ups | 20-30% meilleure résistance à l'eau |
Plastique | Traction du visage bas | Aide à mouiller le savon | 30-40% scores de bâton de ruban adhésif plus élevés |
Les méthodes de test pour l'adhérence comprennent les tests de hachures croisées, les tests d'adhérence par arrachement et les tests d'adhérence au ruban adhésif. Ces méthodes fournissent des données claires sur l'influence de l'HPMC sur la résistance d'adhérence des revêtements.
Le taux de transformation de l'hydroxypropyle affecte davantage les propriétés d'adhérence que la proportion de méthyle. Une transformation plus importante de l'hydroxypropyle favorise l'adhérence sur les surfaces hydrophiles comme le verre et le métal. Une proportion plus importante de méthyle favorise l'adhérence sur les surfaces hydrophobes comme certains plastiques.
Une étude de cas portant sur des revêtements d'entretien d'atelier a montré que l'ajout d'HPMC à une couche de base augmentait l'adhérence sur l'acier de 27% après un essai au brouillard salin. La couche de base HPMC conservait une meilleure forme sous le film lors des phases de rouille.
La flexibilité du film HPMC contribue également à une adhérence durable. Les films plus souples peuvent suivre le support sans se fissurer. Ceci est particulièrement utile pour les revêtements extérieurs soumis aux cycles thermiques et aux conditions humides.
5. Quels sont les avantages de la formation de film du HPMC dans les revêtements ?
La formation de film est la transformation d'un revêtement humide en film solide. L'HPMC joue de nombreux rôles dans cette phase clé. Il contribue à réguler la perte d'eau, ce qui permet un séchage plus uniforme sur toute la surface revêtue.
Le point clé ici est que L'HPMC forme un réseau de fibres plus net lors de la formation du film. À mesure que l'eau s'assèche, les particules d'HPMC s'alignent et forment des liaisons entre elles et avec le liant principal. Cette forme nette élimine les points de tension susceptibles de provoquer des fissures.
L'élimination des défauts courants du film est un atout majeur de l'HPMC. La formation de cratères, un défaut dû aux espaces entre les couches, diminue en présence d'HPMC. Les propriétés savonneuses douces de la fibre permettent de maintenir une couche uniforme pendant le séchage.
La résistance aux fissures est améliorée grâce à l'HPMC grâce à son effet souple. Les particules flexibles de HPMC restent entre les particules de liant lors de leur assemblage, réduisant ainsi les contraintes internes. Cet effet souple est de courte durée en extérieur, car l'HPMC se dégrade progressivement au soleil.
Trait du film | Sans HPMC | Avec le meilleur HPMC | Facteur de gain |
---|---|---|---|
Film Even | Profondeur mixte | Même profondeur | 2-3× plus uniforme |
Combattre le crack | Milieu | Haut | 3 à 4 fois moins de fissures |
Combattre l'affaissement | Bas-moyen | Haut | profondeur de clé 2× |
Combat de bloc précoce | Pauvre | Bien | Croissance 3 fois plus rapide |
Combat de frottements | Milieu | Bon-Excellent | Gain 30-40% |
L'impact sur la dureté du revêtement dépend du type et de la quantité d'HPMC. À faible concentration, l'HPMC a un faible effet sur la dureté finale. À concentration plus élevée, il peut légèrement réduire la dureté tout en améliorant la flexibilité. Ce compromis est souvent avantageux pour de meilleures caractéristiques d'utilisation.
Le HPMC affecte la chaleur de décalage vitreux du film de revêtement final. Il la diminue souvent légèrement. Cela peut favoriser la lutte contre les fissures dans les zones froides, mais peut réduire la résistance au blocage dans les zones chaudes. Les fabricants doivent équilibrer ces effets en fonction de l'utilisation prévue du revêtement.
Les gains de durée de vie des revêtements HPMC proviennent d'une meilleure forme du film et d'une meilleure adhérence de la base. Une étude sur les peintures extérieures a montré que l'ajout de HPMC augmentait la résistance aux intempéries de 25% lors de tests rapides. Cette meilleure formation du film réduit les passages d'eau responsables de la défaillance du revêtement.
L'HPMC améliore également l'aspect du film final. En favorisant une répartition plus uniforme de la couleur pendant le séchage, il améliore le pouvoir couvrant et l'homogénéité de la couleur. Cet effet est particulièrement utile pour les revêtements de maison où l'esthétique est primordiale.
6. Comment les différentes qualités de HPMC affectent-elles la stabilité et la durée de conservation du revêtement ?
La durée de conservation est une préoccupation majeure pour les fabricants de revêtements. L'HPMC améliore la durée de conservation de multiples façons. Tout d'abord, son effet épaississant empêche les couleurs et les charges de s'accumuler, empêchant ainsi la formation de dépôts durs, qui peuvent rendre les produits inutilisables après stockage.
Ce que beaucoup de gens ne savent pas, c'est que Le HPMC forme un gel fragile au repos. Cette forme détermine la limite d'élasticité, c'est-à-dire la force nécessaire pour amorcer l'écoulement du revêtement. Une limite d'élasticité plus élevée empêche le déplacement du foret pendant le stockage sans altérer les caractéristiques d'utilisation une fois le cisaillement appliqué.
L'arrêt de la séparation de l'eau est un autre avantage. La capacité de liaison de l'HPMC à l'eau élimine l'eau libre susceptible de se séparer pendant le stockage. Le revêtement reste ainsi bien mélangé et prêt à l'emploi, sans avoir à le mélanger longtemps.
Les différents types de HPMC offrent des caractéristiques de durée de vie variées. Les types les plus épais offrent une meilleure adhérence, mais peuvent emprisonner de l'air. Les types les moins épais laissent mieux s'échapper l'air, mais peuvent nécessiter davantage d'agents d'adhérence pour une durée de vie prolongée.
Bilan de vie | HPMC à faible épaisseur | HPMC d'épaisseur moyenne | HPMC à haute épaisseur |
---|---|---|---|
Contrôle de l'évier | Équitable | Bien | Super |
Arrêt de séparation d'eau | Équitable | Bien | Super |
La vie au gel et au dégel | Bien | Très bien | Super |
Durée de vie thermique (50 °C) | Super | Bien | Équitable |
Aérer | Super | Bien | Équitable |
L'effet sur la résistance au gel-dégel est très utile pour les revêtements à base d'eau. L'HPMC limite la formation de particules de glace pendant le gel en captant les particules d'eau. Cela prévient les dommages corporels causés par la formation de gros particules de glace.
Une étude de la durée de vie des peintures au latex a montré que l'ajout d'HPMC augmentait la résistance aux cycles de gel-dégel de 3 à 5 cycles. La peinture HPMC conservait une bonne épaisseur et de bonnes propriétés d'utilisation après de nombreux cycles de chauffage.
La stabilité du pH de l'HPMC permet de conserver des propriétés stables pendant le stockage. Contrairement à certains épaississants synthétiques dont l'efficacité diminue avec la dérive du pH, l'HPMC conserve ses propriétés entre 3 et 11 pH. Il est donc adapté aux revêtements acides et basiques.
La conservation à long terme des caractéristiques des produits de revêtement stockés dépend du choix judicieux de l'HPMC. Pour une durée de conservation maximale, les fabricants doivent choisir des types d'HPMC résistants aux insectes. Certains types bénéficient d'un traitement spécial pour lutter contre les insectes susceptibles d'entraîner des pertes d'épaisseur.
Conclusion
L'HPMC offre de nombreux avantages qui optimisent le travail et les caractéristiques d'utilisation des revêtements. D'un meilleur contrôle de l'épaisseur et de la tenue à l'eau, en passant par une meilleure adhérence et une meilleure filmification, l'HPMC résout les problèmes clés rencontrés par les fabricants et les utilisateurs de revêtements. En choisissant le type et la quantité d'HPMC adaptés, vous pouvez réduire les défauts jusqu'à 40%. Vous pouvez également allonger le temps de travail dans les conditions difficiles. Contactez Morton dès aujourd'hui pour demander une buse HPMC personnalisée pour votre revêtement. Notre équipe technique peut vous aider à choisir le type le plus adapté à vos objectifs et à vos résultats.
Q1 : Quelle concentration de HPMC est généralement utilisée dans les formulations de revêtement ?
La plupart des mélanges de revêtements utilisent des quantités d'HPMC comprises entre 0,11 TP3T et 1,21 TP3T en poids. Ces quantités varient selon la méthode d'utilisation et les caractéristiques recherchées. Au pistolet, il faut compter entre 0,1 et 0,51 TP3T, au rouleau entre 0,3 et 0,81 TP3T et au pinceau entre 0,5 et 1,01 TP3T. La quantité exacte dépend de l'épaisseur du type d'HPMC, du type de revêtement et de la base. Des quantités plus élevées offrent une meilleure tenue à l'eau et une meilleure résistance à l'affaissement, mais peuvent nuire à l'aspect lisse et à la finition.
Q2 : Le HPMC peut-il être combiné avec d’autres additifs dans les formulations de revêtement ?
Oui, l'HPMC est compatible avec la plupart des additifs de revêtement courants. Il se mélange bien avec les liants acryliques, vinyliques et styrène-acryliques. L'HPMC peut être utilisé avec des épaississants synthétiques comme l'HEUR et l'HASE pour un meilleur contrôle de l'écoulement. Il est également efficace comme agent d'écoulement, anti-mousse et agent mouillant lorsqu'il est ajouté dans le bon ordre. L'important est d'ajouter l'HPMC à l'eau avant les colorants et autres solides afin d'éviter la formation de grumeaux et une mauvaise décomposition.
Q3 : Comment le HPMC se compare-t-il aux autres épaississants dans les applications de revêtement ?
L'HPMC offre un mélange unique de caractéristiques par rapport aux autres épaississants. Contrairement aux épaississants synthétiques, l'HPMC offre une excellente rétention d'eau et est moins sensible aux variations de mélange. Comparé aux autres types de plantes, l'HPMC présente un meilleur habillage que le CMC et une meilleure résistance aux insectes que le HEC. L'HPMC offre un écoulement plus spécifique que les polyacrylates, ce qui permet une meilleure résistance à l'affaissement après utilisation. Si les épaississants synthétiques peuvent être plus efficaces à faible cisaillement, l'HPMC offre une meilleure performance globale pour de nombreuses caractéristiques de revêtement.
Q4 : Le HPMC affecte-t-il le temps de séchage des revêtements à base d’eau ?
Oui, l'HPMC allonge souvent le temps de séchage des revêtements à base d'eau, mais cet effet varie selon la base et l'état. Sur les supports poreux, l'effet de rétention d'eau peut accélérer le temps de séchage réel. Il empêche une imprégnation trop rapide qui laisserait du liant sur la surface. Sur les supports non poreux, l'HPMC allonge le temps ouvert du 15-40% en fonction du type et de la quantité. Ce temps ouvert plus long permet souvent d'obtenir un aspect plus lisse et d'éviter les marques de chevauchement, surtout par temps chaud ou venteux.
Q5 : Existe-t-il des limitations lors de l’utilisation du HPMC dans les applications de revêtement ?
Bien que le HPMC offre de nombreux avantages, il présente certaines limites. Des quantités élevées peuvent réduire la brillance de certains mélanges en raison de la présence de fibres sur la face. Le HPMC peut légèrement réduire la résistance à l'eau dans les premières étapes suivant l'utilisation, mais cet effet diminue lorsque le revêtement sèche complètement. En extérieur, le HPMC se dégrade lentement au soleil, ses effets sur la flexibilité sont donc de courte durée. Certains types peuvent former de la mousse, nécessitant des ajustements des niveaux d'arrêt de mousse. Ces limites peuvent être corrigées par des ajustements de type et de mélange appropriés.