Hydroxypropyl Methylcellulose (HPMC) is a key ingredient in various industries, including pharmaceuticals, food production, construction, and cosmetics. Understanding the properties and production of HPMC is critical for manufacturers who seek to optimize its use in their products. This guide will provide a detailed overview of HPMC, explaining its chemical composition, manufacturing process, applications, and benefits across different industries. By the end, you will have a comprehensive understanding of HPMC and how it can be utilized effectively in your business.
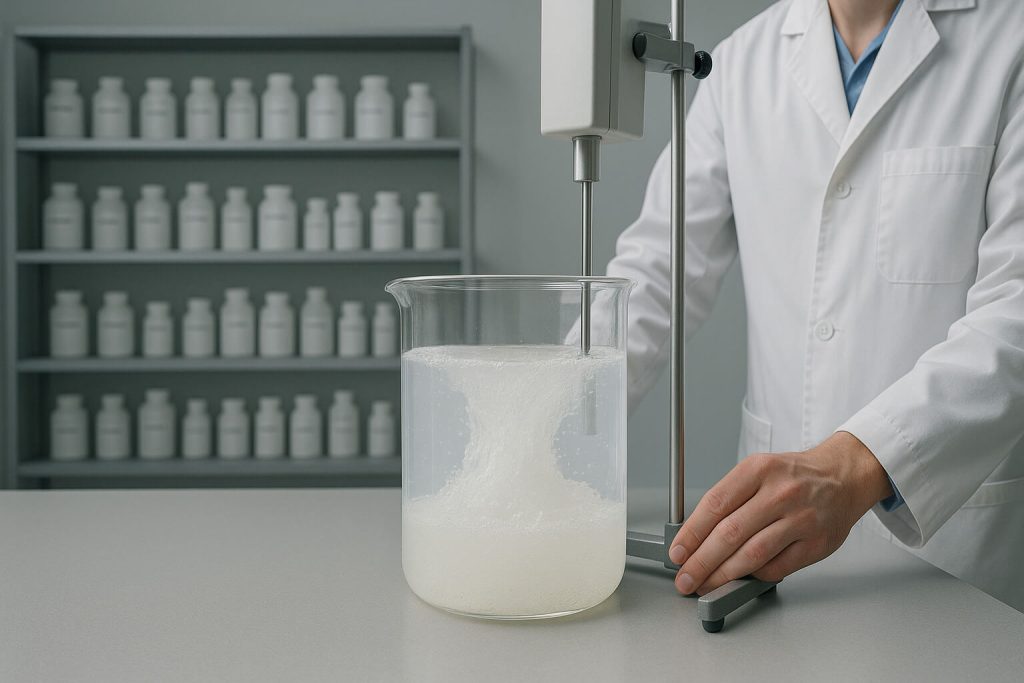
1. Qu'est-ce que l'hydroxypropylméthylcellulose (HPMC) ?
HPMC, or Hydroxypropyl Methylcellulose, is a non-ionic cellulose ether that is soluble in water. It is widely used as a thickener, binder, emulsifier, and stabilizer across various industries. Derived from cellulose, a natural polymer found in plant cell walls, HPMC’s chemical modification with hydroxypropyl and methyl groups enhances its properties and makes it versatile for a wide range of applications.
So, why should you care about HPMC? Its unique properties make it a go-to ingredient in numerous products. In the pharmaceutical industry, HPMC plays a key role in controlled-release drug formulations and tablet coatings. In food production, it improves texture, consistency, and shelf life, especially in gluten-free products. In construction, it enhances the workability of dry mixes, such as mortars and adhesives. Additionally, it is used in cosmetics to stabilize emulsions and improve product texture.
Understanding the chemical composition of HPMC and its functional groups—hydroxypropyl and methyl groups—is essential to understanding its diverse applications. These groups enhance solubility, water retention, and viscosity, which are critical in many formulations.
Tableau : Propriétés de l'HPMC
Propriété | Description |
---|---|
Composition chimique | Cellulose modifiée avec des groupes hydroxypropyle et méthyle |
Solubilité | Soluble dans l'eau, forme un gel dans l'eau |
Viscosité | Peut être ajusté en fonction de l'application |
Applications courantes | Produits pharmaceutiques, agroalimentaire, construction, cosmétiques |
2. How is HPMC Produced?
The production of HPMC involves chemically modifying cellulose, a natural polymer, with propylene oxide and methyl chloride. The process begins by dissolving cellulose in sodium hydroxide, a strong base, to break down the cellulose into a more manageable form. After this, the cellulose is reacted with propylene oxide and methyl chloride, which introduce the hydroxypropyl and methyl groups into the cellulose structure.
What’s the process in more detail? Once the cellulose is treated with sodium hydroxide, it undergoes a reaction with propylene oxide. The hydroxypropyl group is introduced, making the polymer more hydrophilic and soluble in water. The methyl chloride reacts with the cellulose to introduce the methyl group, which provides hydrophobic properties. These two modifications work together to give HPMC its ability to dissolve in water and form gels, making it useful in a variety of industries.
After the chemical reactions, the mixture is neutralized and washed to remove any remaining chemicals. The final product is then dried and ground into a fine powder, which can be used in a wide range of applications.
Pourquoi est-ce important ? Understanding how HPMC is produced allows businesses to optimize its production process for specific uses. The degree of substitution—the number of hydroxypropyl and methyl groups added to the cellulose—can be adjusted to control properties like solubility, viscosity, and water retention.
Table: Chemical Production Process of HPMC
Étape | Description |
---|---|
Préparation de cellulose | La cellulose est dissoute dans l'hydroxyde de sodium |
Réaction avec des produits chimiques | L'oxyde de propylène et le chlorure de méthyle réagissent avec la cellulose |
Degré de substitution | Ajusté en faisant varier la quantité de produits chimiques utilisés |
Produit final | HPMC avec des propriétés personnalisées pour différentes applications |
3. What Are the Common Uses of HPMC?
HPMC’s versatility makes it suitable for a wide variety of applications across several industries. Here are some of the most common uses:
In pharmaceuticals: HPMC is used extensively in tablet formulations as a binder and stabilizer. Its ability to form gels allows for controlled drug release, making it essential in the production of sustained-release tablets and capsules. It is also used as a coating agent to enhance tablet stability and provide a smooth, easily digestible coating.
In food production: HPMC is used as a food additive to improve the texture and consistency of various products. It is especially valuable in gluten-free foods, where it helps to replicate the texture and structure of traditional wheat-based products. Additionally, HPMC is used in sauces, dressings, and ice cream to stabilize emulsions and prevent ice crystallization.
In construction: HPMC is added to dry mortar mixes and adhesives to improve water retention, workability, and bonding strength. Its thickening properties also help improve the flow and consistency of these materials.
In cosmetics: HPMC is used in creams, lotions, shampoos, and other personal care products as a thickening agent and stabilizer. It enhances the texture of products and improves the feel on the skin.
Pourquoi devriez-vous vous en soucier ? Understanding HPMC’s wide range of applications allows businesses to tap into its potential across various industries, providing a competitive edge in product formulation.
Tableau : Applications courantes de l'HPMC
Industrie | Application |
---|---|
Médicaments | Tablet coatings, controlled drug release |
Nourriture | Texture, emulsification, and stabilization |
Construction | Water retention, workability in mortars and adhesives |
Produits de beauté | Thickening agent, emulsifier, stabilizer |
4. How Does HPMC Affect the Pharmaceutical Industry?
HPMC plays a pivotal role in the pharmaceutical industry, particularly in the development of controlled-release drug formulations. The ability to form gels and regulate the release of active ingredients is crucial for ensuring consistent drug delivery.
What’s the role of HPMC in pharmaceuticals? One of its primary uses is as a binder in tablet formulations. It helps hold the tablet together, preventing it from disintegrating prematurely. In addition, HPMC is used in controlled-release formulations, where it forms a gel in the digestive system and releases the drug slowly over time. This ensures a consistent therapeutic effect.
HPMC is also used in capsule formulations, where it improves the stability and performance of the capsule shell. It provides a smooth texture that is easy to swallow and helps maintain the stability of the drug inside the capsule.
Pourquoi est-ce important ? HPMC’s ability to control drug release makes it a key ingredient in modern pharmaceutical formulations. It allows for more precise dosing, fewer side effects, and better patient compliance.
Tableau : HPMC dans les applications pharmaceutiques
Application | Rôle du HPMC |
---|---|
Comprimés à libération contrôlée | Libération progressive du médicament |
Capsule Formulations | Improves stability and performance |
Enrobages de comprimés | Enhances tablet stability and ease of swallowing |
5. How Does HPMC Improve Food Products?
HPMC’s ability to improve the texture and consistency of food products is one of its key benefits. In the food industry, it is used as an emulsifier, stabilizer, and thickening agent.
So, how does it work in food? In gluten-free products, HPMC helps create a structure that mimics the texture of traditional wheat-based products. For example, it is used in gluten-free bread and baked goods to improve their texture and volume. It also plays a role in sauces and dressings, where it helps to stabilize emulsions and improve mouthfeel.
In ice cream, HPMC is used to prevent the formation of large ice crystals, ensuring a smooth and creamy texture. It helps maintain consistency and enhances the overall sensory experience of the product.
Why is this valuable? HPMC’s ability to enhance the texture and stability of food products makes it an indispensable ingredient in modern food manufacturing, particularly in gluten-free and dairy-free products.
Table: HPMC in Food Applications
Type de produit | Rôle du HPMC |
---|---|
Produits sans gluten | Improves texture and structure |
Sauces et vinaigrettes | Stabilizes emulsions and thickens |
Glace | Prevents ice crystallization, improves texture |
6. What Are the Benefits of Using HPMC in Cosmetics?
In the cosmetics industry, HPMC serves as a thickening agent, emulsifier, and stabilizer. Its ability to improve the texture and consistency of personal care products makes it a go-to ingredient for formulators.
What makes HPMC so effective in cosmetics? HPMC is commonly used in creams, lotions, and shampoos, where it improves the texture and enhances product performance. It helps achieve the desired consistency, whether thick or thin, and ensures that the product is stable throughout its shelf life.
In addition to its thickening properties, HPMC also serves as an emulsifier, helping to combine water and oil-based ingredients in products like moisturizers and facial cleansers. This ensures that the product remains smooth and uniform.
Why is this important for your business? HPMC’s role in enhancing the texture and stability of cosmetic products ensures that they meet consumer expectations for quality and consistency.
Table: HPMC in Cosmetics
Type de produit | Rôle du HPMC |
---|---|
Crèmes et lotions | Thickening agent, stabilizer |
Shampoings | Improves texture, enhances performance |
Nettoyants pour le visage | Emulsifier, improves consistency |
7. How Does HPMC Benefit the Construction Industry?
HPMC is a valuable ingredient in the construction industry, particularly in dry mixes, adhesives, and coatings. It enhances the workability, water retention, and bonding strength of construction materials.
How does HPMC work in construction? When added to dry mortars, HPMC improves the flow and workability of the mixture, making it easier to apply. It also helps retain water, which is crucial for ensuring that the mortar remains workable during the application process.
In adhesives and coatings, HPMC improves the adhesion of materials and ensures that the products dry evenly and uniformly. It also enhances the spreadability and consistency of the mixture, making it easier to apply in various construction applications.
Pourquoi est-ce important ? HPMC’s ability to improve the performance of construction materials makes it an essential additive for manufacturers in the building materials industry.
Table: HPMC in Construction
Application | Rôle du HPMC |
---|---|
Dry Mortars | Improves workability and water retention |
Adhésifs | Enhances adhesion and spreadability |
Revêtements | Ensures smooth, uniform drying |
8. How Does the Degree of Substitution Impact HPMC?
The degree of substitution (DS) is a key factor that determines the properties of HPMC. It refers to the number of hydroxypropyl and methyl groups that are attached to each cellulose unit during the production process.
So, what does this mean for you? A higher DS results in higher solubility, viscosity, and water retention, making the product more suitable for applications like pharmaceuticals and food products. Conversely, a lower DS is preferred for applications that require a thinner consistency, such as in some cosmetics.
The DS also affects the gel formation of HPMC. Higher DS HPMC forms more stable gels, making it ideal for controlled-release drug formulations, while lower DS HPMC is better suited for applications requiring a more fluid or free-flowing product.
Pourquoi est-ce important ? Understanding the DS of HPMC allows businesses to tailor its properties to meet the specific needs of their applications.
Table: Effect of Degree of Substitution on HPMC
Degré de substitution | Viscosité | Solubilité | Application |
---|---|---|---|
Faible | Faible | Modéré | Cosmétiques, formules douces |
Moyen | Moyen | Haut | Produits alimentaires, applications industrielles |
Haut | Haut | Très élevé | Produits pharmaceutiques, formulations à libération contrôlée |
9. What Are the Different Types and Grades of HPMC?
There are various types and grades of HPMC, each designed to meet the specific needs of different industries. These grades vary based on factors like viscosity, solubility, and the degree of substitution.
Qu'est-ce que cela signifie pour votre entreprise ? Higher viscosity grades are typically used in pharmaceutical and construction applications, where thickening and water retention are essential. Medium viscosity grades are commonly used in food products and some cosmetic formulations, while low viscosity grades are used in products that require a thinner consistency.
Pourquoi devriez-vous vous en soucier ? Understanding the different grades of HPMC helps businesses choose the right product for their specific needs, ensuring optimal performance in the final formulation.
Table: Types and Grades of HPMC
Grade | Viscosité | Application |
---|---|---|
Faible viscosité | Faible | Produits alimentaires, cosmétiques |
Viscosité moyenne | Moyen | Pharmaceuticals, industrial formulations |
Haute viscosité | Haut | Construction materials, controlled-release formulations |
10. What Are the Environmental and Sustainability Considerations of HPMC Production?
Sustainability is a key concern in the manufacturing of many materials, including HPMC. The raw material, cellulose, is a renewable resource, but the chemicals used in HPMC production, such as propylene oxide and methyl chloride, can have environmental impacts.
What’s the solution? Companies are increasingly focusing on making HPMC production more sustainable by reducing the use of harmful chemicals and improving energy efficiency. The goal is to minimize the environmental footprint while maintaining high-quality products.
Pourquoi est-ce important ? As sustainability becomes a larger concern for consumers and regulators, businesses must consider the environmental impact of their production processes. Opting for eco-friendly production methods can help companies meet sustainability goals and appeal to environmentally conscious consumers.
Table: Environmental Considerations in HPMC Production
Facteur | Impact |
---|---|
Raw Material (Cellulose) | Renewable and biodegradable |
Chemicals Used | Potential environmental concerns with propylene oxide and methyl chloride |
Pratiques durables | Efforts to reduce chemical waste and improve energy efficiency |
Conclusion
In conclusion, HPMC is a highly versatile material with a wide range of applications across multiple industries. From its use in pharmaceuticals to its role in food, construction, and cosmetics, HPMC’s unique properties make it indispensable. By understanding its production process, various grades, and environmental considerations, businesses can better leverage HPMC to meet their needs and create high-quality products.
Rubrique FAQ
Q1 : Qu'est-ce que l'HPMC ?
HPMC (Hydroxypropyl Methylcellulose) is a cellulose derivative used in various industries, including pharmaceuticals, food, construction, and cosmetics, for its thickening, stabilizing, and emulsifying properties.
Q2 : Comment l'HPMC est-il produit ?
HPMC is produced by chemically modifying cellulose with propylene oxide and methyl chloride, introducing hydroxypropyl and methyl groups to alter the polymer’s solubility and viscosity.
Q3 : What are the benefits of using HPMC in food products?
HPMC is used in food products to improve texture, enhance emulsification, and increase shelf life. It is especially valuable in gluten-free products to mimic the texture of traditional baked goods.
Q4 : How does HPMC benefit the pharmaceutical industry?
HPMC is widely used in pharmaceuticals for controlled drug release, tablet coatings, and improving stability. Its ability to form gels and enhance controlled drug delivery makes it essential in drug formulations.
Q5 : What are the environmental considerations in HPMC production?
HPMC is made from cellulose, a renewable resource, but the chemicals used in its production process can have environmental impacts. Sustainable production methods are being developed to minimize the ecological footprint of HPMC manufacturing.