Do you find it hard to control HPMC viscosity in your products? Many makers in drug and building work face this same issue. When viscosity is wrong, batches fail tests. This causes delays and costs money. Most often, the cause is not knowing how factors change HPMC behavior. By learning what controls HPMC viscosity, you can make products that work the same way each time. You’ll waste less and get better results. Tests show that a step-by-step plan for HPMC viscosity can make batches 40% more alike. In this guide, we’ll look at six key factors that affect HPMC viscosity and how to control them.
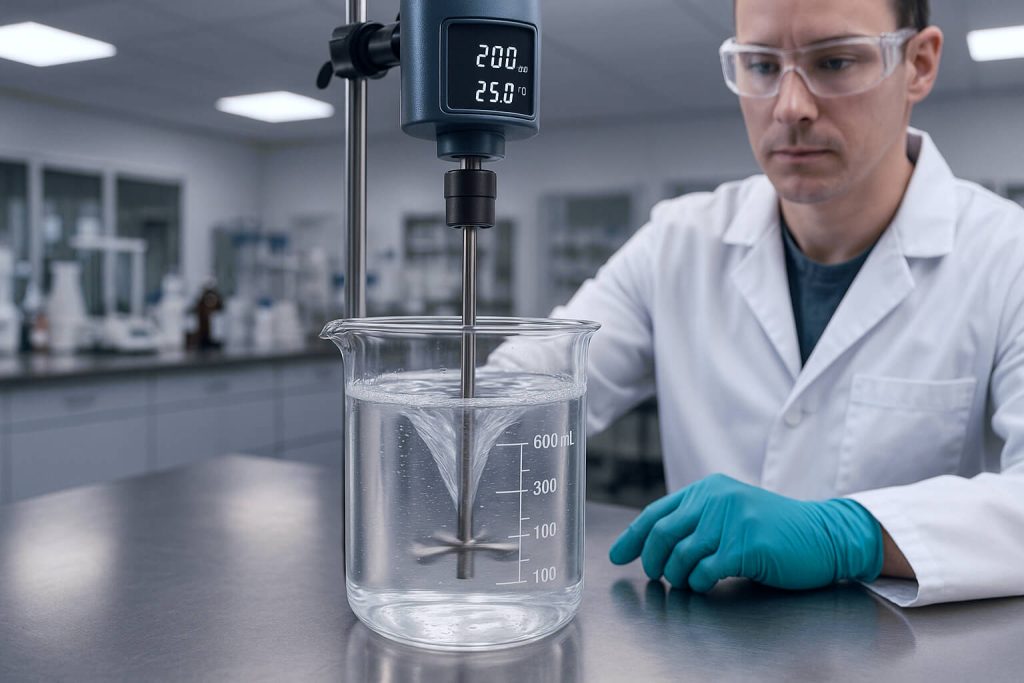
1. What Is HPMC and Why Is Its Viscosity Important?
HPMC stands for hydroxypropyl methylcellulose. It’s a changed form of plant fiber made with chemicals. The process uses methyl chloride and propylene oxide to change natural cellulose.
The basic form has a cellulose chain with methoxyl and hydroxypropyl groups added. These groups replace the hydroxyl parts of cellulose, which changes how it works.
But here’s the thing: How these groups sit on the chain affects how HPMC acts in water, mainly its thickness or viscosity.
Drug makers use HPMC to control how fast drugs release in the body. The viscosity sets the drug release rate.
In building mixes, HPMC helps keep water in cement. The right viscosity makes the mix easy to use and stops water from leaving too fast.
Food makers use HPMC to keep mixes from splitting and to make food feel better in your mouth. Without the right viscosity, foods may split or feel odd.
Industry | What HPMC Viscosity Does | Problems If Viscosity Is Wrong |
---|---|---|
Drugs | Controls drug release speed | Random drug delivery |
Building | Keeps water in the mix | Hard to use, sets too fast |
Food | Keeps mixes stable | Products split, feels wrong |
Personal Care | Makes products flow right | Products apply unevenly |
Coatings | Controls film thickness | Uneven coating, looks bad |
HPMC can range from thin like water to thick like gel. This range makes HPMC very useful but means you need to control it well.
When makers don’t watch viscosity factors, products may fail tests. This leads to wasted batches, wasted stuff, and delays.
Testing HPMC viscosity uses tools that measure how much the liquid fights flow. These tests must follow set rules to get good results.
2. How Does Molecular Weight Affect HPMC Viscosity?
Molecular weight is the main thing that sets HPMC viscosity. Higher weight HPMC makes thicker mixes than lower weight types at the same amount.
This follows a power law: viscosity goes up much faster than weight. A small weight change can cause a big change in thickness.
You might be surprised to learn that if you double the weight, the viscosity can go up 8-10 times in some cases. This makes picking the right weight very key.
Makers label HPMC types by viscosity rather than by weight. For example, HPMC K4M means it forms a 4,000 mPa·s mix at 2%.
The spread of weights also matters. Two HPMC samples with the same average weight but different spreads can flow differently.
Narrow weight spreads tend to give more steady results. Wider spreads may show complex flow patterns that change with stir speed.
HPMC Type | Weight Range (Daltons) | Viscosity Range (2% mix, mPa·s) | Common Uses |
---|---|---|---|
Low Weight | 10,000 – 65,000 | 3 – 100 | Pill coatings, Thin films |
Medium Weight | 65,000 – 120,000 | 100 – 4,000 | Timed pills, Cement adds |
High Weight | 120,000 – 250,000 | 4,000 – 15,000 | Slow drugs, Thickeners |
Ultra High Weight | 250,000+ | 15,000+ | Very thick gels, Special uses |
Ways to measure weight include gel tests and light tests. These give good data but need special tools.
For daily work, many makers just measure viscosity instead of weight. This works well when using HPMC from the same maker.
When changing HPMC brands, know that types with the same listed viscosity may have different weight profiles. Always test before switching.
HPMC chains can break down during use or storage, which lowers weight and viscosity. Avoid too much heat, strong oxidizers, and very high or low pH to keep chains whole.
3. What Role Does Temperature Play in HPMC Viscosity?
Temperature changes HPMC viscosity in a unique way. Unlike most polymers that just get thinner when hot, HPMC shows a more complex pattern.
At lower temps, HPMC acts as you’d think—it gets thinner as it warms up. This happens because heat makes bits move more and tangle less.
Here’s what makes HPMC special: Above a certain point (the gel point), HPMC suddenly gets thicker and may form a gel. This happens because the polymer parts start to stick.
The gel point is usually between 65-90°C, based on the HPMC type. This makes HPMC useful for products that need to thicken when heated.
Temperature Range | How HPMC Viscosity Acts | What This Means for Use |
---|---|---|
Below 20°C | Thicker, slower to mix | Needs more mixing time |
20-50°C | Best working range, stable | Good for most processes |
50-65°C | Gets thinner | May need stabilizers |
Above 65-90°C | Gets much thicker, may gel | Good for heat-triggered uses |
Cooling after heating | Usually returns to normal | Can be used for cycle-based products |
The methoxyl content affects the gel point. More methoxyl usually lowers the gel point, while more hydroxypropyl raises it.
For drug makers, this temp effect changes how fast drugs release. Pills with HPMC may dissolve differently at body temp versus room temp.
In building products, outdoor temp changes can greatly affect workability. Mortars with HPMC may need different water amounts in summer versus winter.
Heating and cooling cycles can sometimes cause lasting changes in HPMC viscosity. Repeated cycles may change the polymer structure, mainly at extreme temps.
When making HPMC solutions, first mix the powder in cold water to prevent early gelling. Once fully wet, the mix can be warmed if needed.
4. How Do Concentration and Dissolution Methods Impact HPMC Viscosity?
Concentration has a strong, direct effect on HPMC viscosity. The link follows a power curve, with viscosity rising much faster than concentration.
A 1% HPMC mix might flow like water, a 2% mix could be like syrup, and a 4% mix might form a soft gel. This makes exact concentration control very key.
What many people don’t realize is that how you mix HPMC greatly affects the final viscosity, even at the same concentration. Poor mixing leads to uneven results.
The right mixing method starts with spreading HPMC powder in cold water (below 25°C). This lets the bits get fully wet before they start to swell, which stops clumps.
Once spread out, the temp can be raised to speed up mixing. But staying below the gel point is key to avoid early gelling.
Concentration (w/v) | Typical Viscosity Range (mPa·s)* | How It Looks | Common Uses |
---|---|---|---|
0.5% | 5 – 50 | Slightly thick liquid | Eye drops, Sprays |
1.0% | 50 – 400 | Light syrup | Liquid meds, Light glues |
2.0% | 400 – 4,000 | Thick syrup to soft gel | Pills, Cement adds |
3.0% | 4,000 – 15,000 | Soft gel | Slow-release drugs |
5.0%+ | 15,000+ | Firm gel | Special uses, Modeling |
*For medium viscosity HPMC; actual values vary by type |
Stir speed affects mixing quality. Too little stirring leads to slow mixing and clumps, while too much can trap air bubbles that change the apparent thickness.
Water quality matters too. Minerals in hard water can mix with HPMC and affect how it swells. Pure water often gives more steady results.
Common mixing mistakes include adding HPMC to hot water (causing instant surface gelling and “fish eyes”) and not mixing long enough (leading to partial swelling).
For big batches, special mixing tools like high-speed mixers can improve results. These help get even swelling across batches.
After mixing, HPMC solutions should rest for hours to reach their final viscosity. Fresh mixes may not show their true viscosity until fully swelled.
5. What Effect Do pH and Ionic Strength Have on HPMC Viscosity?
HPMC stays stable across a wide pH range compared to many other polymers. It has no charges, so pH changes don’t affect it directly.
But extreme pH can still impact HPMC viscosity in indirect ways. Very high or low pH can break the polymer chain, reducing weight and viscosity.
The surprising fact is that while HPMC itself is pH-stable, many mixes with HPMC show pH-based viscosity changes due to how it works with other items.
The best pH range for HPMC stability is between 3-11. In this range, viscosity stays mostly the same if other factors are controlled.
Ionic strength—the amount of ions in solution—affects HPMC viscosity through a “salting-out” effect. As salt levels rise, water becomes less able to wet the polymer.
pH Range | Effect on HPMC Viscosity | Stability Tips |
---|---|---|
1-3 | Possible acid breakdown, slow viscosity drop | Avoid long exposure, use acid-proof types |
3-7 | Best stability, steady viscosity | Best range for most uses |
7-11 | Good stability, steady viscosity | Good for basic mixes |
11-14 | Possible base breakdown, viscosity drop | Limit exposure time, watch viscosity |
Different salts affect HPMC differently. Two-charge ions like calcium (Ca²⁺) and magnesium (Mg²⁺) usually have stronger effects than one-charge ions like sodium (Na⁺) and potassium (K⁺).
At low levels, some salts may actually raise HPMC viscosity slightly by helping polymer parts stick together. But higher salt levels almost always lower viscosity.
Buffer mixes can help keep stable pH and ion levels in HPMC products. Common buffers include citrate, phosphate, and acetate systems, picked based on the target pH range.
For drug uses, body-like buffers that match body fluids are often used to predict how HPMC will act after being taken. These usually contain salt mixes at levels like body fluids.
When making products with HPMC, think about the whole ion mix, including active drugs, preservatives, and other items. Each part may add to the total ion strength.
6. How Do Substitution Type and Degree Influence HPMC Viscosity?
The pattern of groups on HPMC—the ratio and spread of methoxyl and hydroxypropyl groups—sets how it acts in solution, including viscosity.
HPMC types are often labeled using a code that shows substitution levels. For example, in the USP system, “2910” means 29% methoxyl and 10% hydroxypropyl substitution.
What’s fascinating is that even small changes in substitution patterns can greatly change how HPMC mixes with water and other molecules, affecting everything from viscosity to gel temp.
Higher methoxyl content generally makes it more water-shy and lowers the gel temp. This changes how viscosity shifts with temp and can be used to fine-tune temp-based behaviors.
Higher hydroxypropyl content usually makes it mix better in cold water and organic solvents. It also tends to raise the gel temp and change the viscosity profile.
Substitution Type | Methoxyl Content (%) | Hydroxypropyl Content (%) | Viscosity Features | Common Uses |
---|---|---|---|---|
Low Substitution | 16-24 | 4-12 | Higher viscosity at low temps, stronger gel effect | Food thickeners, Building |
Medium Substitution | 28-30 | 7-12 | Balanced traits, good stability | Drug matrices, General use |
High Substitution | 28-30 | 19-24 | Better organic mixing, higher gel temp | Film-forming, Slow release |
Specialized | Custom ratios | Custom ratios | Use-specific traits | Special products |
The spread of groups along the cellulose chain also matters. More even spread usually gives more steady viscosity behavior.
Making processes can control substitution patterns to create HPMC types with specific traits. This allows for custom products made for certain uses.
When picking an HPMC type, look at both the viscosity spec and the substitution type. Two products with the same listed viscosity but different substitution patterns may act differently in your product.
For drug uses, substitution type affects drug release methods. Some patterns favor erosion-based release while others promote diffusion-based release.
In building products, substitution patterns affect water holding power and work time. The right pattern depends on what the specific use needs.
Conclusion
Managing the factors that affect HPMC viscosity means watching weight, temperature, concentration, mixing methods, pH, and substitution patterns. By knowing these variables, you can get steady results in your products. Good control of these factors can cut batch fails by up to 35% and make products work much better. Contact Morton’s tech team today for help with making HPMC viscosity work best for your uses. Our experts can help you pick the right type and process settings to meet your needs, saving you time and money through our proven formula plan.
FAQ
Q1: Can HPMC viscosity be adjusted after initial preparation?
Yes, you can change HPMC viscosity after mixing. You can add water to make it thinner or add thickeners to make it thicker. Changing the temp gives short-term viscosity changes. For lasting changes, you can adjust pH within safe ranges or add salts to change how the polymer wets. Always test small amounts before changing big batches.
Q2: What testing methods are most accurate for measuring HPMC viscosity?
Spinning viscometers give the most reliable measures for HPMC solutions. The Brookfield viscometer is widely used, with the spinner type and speed picked based on the expected viscosity range. For more detailed tests, rheometers that measure viscosity at different stir rates give better insights into flow behavior. Always test at set temps (usually 20°C or 25°C) and let solutions fully wet before testing.
Q3: How do storage conditions affect HPMC viscosity stability?
Storage greatly impacts HPMC viscosity stability. Dry HPMC powder should be kept in sealed boxes in cool, dry places to prevent moisture uptake, which can cause early wetting and clumping. For HPMC solutions, cooling (2-8°C) slows microbe growth but may briefly increase viscosity. Avoid freezing, as ice crystals can break the polymer network. Solutions usually stay stable for 1-4 weeks based on how they’re kept.
Q4: Are there differences between HPMC viscosity behavior in water versus organic solvents?
HPMC shows different viscosity behaviors in water versus organic solvents. In water, HPMC forms hydrogen bonds that create a thick solution, with viscosity based on amount and temp. In organic solvents, behavior varies based on the solvent’s polarity. HPMC mixes in some polar organic solvents like ethanol-water blends but at different viscosity levels than in pure water. In non-polar solvents, HPMC usually doesn’t mix well, limiting viscosity growth.
Q5: What are the common troubleshooting steps for unexpected HPMC viscosity issues?
When facing odd HPMC viscosity problems, first check your test method and tool setup. Check mixing methods, making sure to spread in cold water before heating. Confirm the HPMC type and batch match with maker certs. Check storage of both powder and solutions. Test water quality, as mineral content affects wetting. Measure pH and check for other items that might mix in. For ongoing issues, make fresh solutions under set rules to create a baseline for testing.