Are you struggling to achieve consistent, high-quality film coatings for your pharmaceutical tablets? Selecting the right polymer is critical, and Hydroxypropyl Methylcellulose (HPMC) E3 grade stands out as a versatile and reliable option. Many formulators face challenges with film integrity, moisture protection, and dissolution control. This article directly addresses these concerns by exploring the specific role and advantages of HPMC E3 in film coating. We will delve into its properties, application techniques, and how it overcomes common manufacturing hurdles. By understanding how HPMC E3 functions, you can optimize your coating processes, improve product stability, and ensure reliable drug delivery for better patient outcomes. Trust in proven solutions to elevate your pharmaceutical manufacturing.
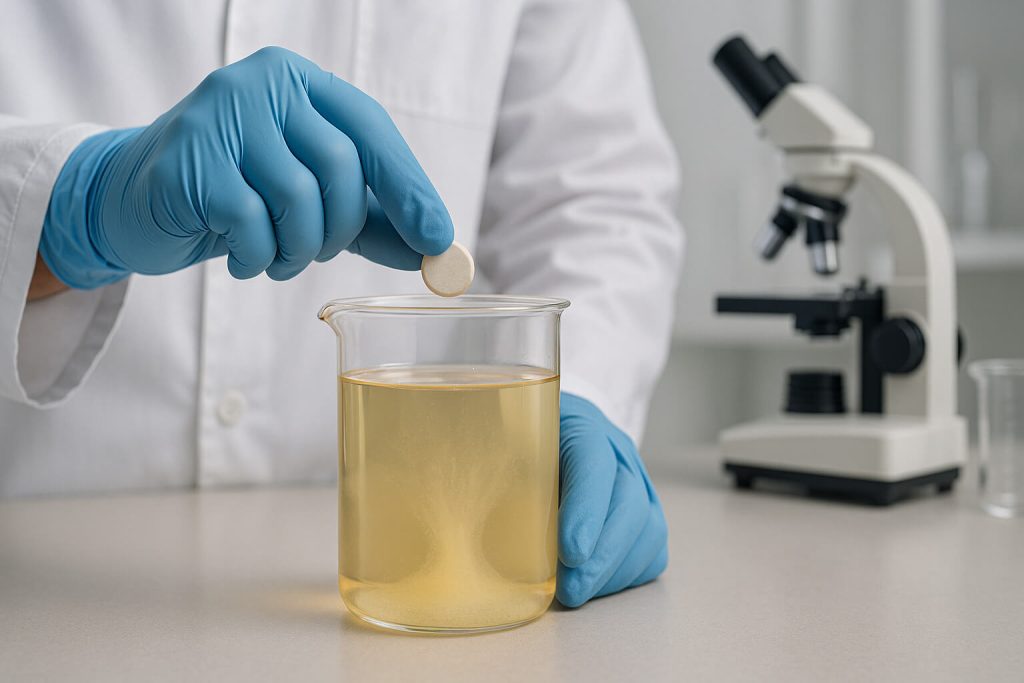
1. What Is HPMC E3 and Why Is It Important for Pharmaceutical Coatings?
Hydroxypropyl Methylcellulose (HPMC) E3 is a specific grade of cellulose ether polymer widely used in pharmaceutical coating. Derived from natural cellulose, it undergoes chemical modification to introduce hydroxypropyl and methoxy groups onto the cellulose backbone. This modification creates unique properties crucial for film coating. Here’s the key takeaway: its low viscosity (typically around 3 mPa·s for a 2% aqueous solution) allows for higher polymer concentrations in coating solutions without becoming too thick to spray effectively, leading to faster coating times and reduced processing costs.
Compared to other HPMC grades (E5, E6, E15, K grades), HPMC E3 offers excellent film formation with good adhesion and flexibility at lower viscosity, making it easier to handle and apply. Its solubility in cold water and various organic solvents adds versatility. HPMC E3 became popular for immediate-release tablet coatings because of its rapid dissolution and compatibility with many active pharmaceutical ingredients (APIs). From a regulatory standpoint, HPMC is generally recognized as safe (GRAS) and is listed in major pharmacopeias, simplifying global product registration.
Property | Typical Value for HPMC E3 | Significance in Coating |
---|---|---|
Viscosity (2% aq.) | ~3 mPa·s | Allows higher solids content, faster spray |
Methoxy Substitution | Varies by manufacturer | Influences solubility, film properties |
Hydroxypropyl Subst. | Varies by manufacturer | Affects flexibility, water interaction |
Solubility | Cold water, some solvents | Versatile solvent systems possible |
Regulatory Status | GRAS, Pharmacopeial | Widely accepted for pharmaceutical use |
2. How Does HPMC E3 Function in the Film Coating Process?
The primary function of HPMC E3 in film coating is to form a thin, uniform, and continuous layer around the tablet core. When dissolved in an appropriate solvent (usually water), the polymer chains hydrate and disperse. During coating, this solution is sprayed onto the tumbling tablet bed. Now, consider this: as the warm drying air flows through the pan, the solvent evaporates, and the HPMC E3 polymer chains coalesce and entangle, forming a solid film that adheres to the tablet surface. The low viscosity facilitates the formation of a smooth, even film by allowing droplets to spread effectively before drying.
HPMC E3 exhibits inverse thermal gelation – becoming less soluble as temperature increases. This requires careful control during solution preparation; typically, HPMC is dispersed in hot water first (where it disperses easily but doesn’t dissolve well) and then cooled to achieve full dissolution. Solution concentration usually ranges from 5% to 15% w/w, depending on desired film thickness and processing equipment.
Key process parameters include spray rate, atomization pressure, inlet air temperature, and pan speed. HPMC E3 solutions can often be sprayed at higher rates compared to higher viscosity polymers, potentially shortening process times. However, spray rate must balance with drying capacity to avoid overwetting. HPMC E3 often interacts synergistically with other coating excipients like plasticizers (e.g., polyethylene glycol), pigments (e.g., titanium dioxide), and anti-tacking agents (e.g., talc).
Parameter | Typical Range/Consideration | Impact on HPMC E3 Coating |
---|---|---|
Polymer Concentration | 5-15% w/w | Affects viscosity, spray rate, film thickness |
Solution Temperature | Controlled (often cool) | Prevents gelation, ensures stability |
Spray Rate | Balanced with drying capacity | Affects efficiency, prevents overwetting |
Atomization Pressure | Optimized for droplet size | Influences film uniformity, surface finish |
Inlet Air Temperature | Moderate (e.g., 50-70°C) | Ensures drying, avoids degradation/gelation |
3. What Technical Advantages Does HPMC E3 Offer for Tablet Coating?
HPMC E3 provides several significant technical advantages for immediate-release pharmaceutical film coating applications. Crucially, when formulated with appropriate plasticizers (typically 10-25% based on polymer weight), HPMC E3 films exhibit good flexibility and strength. This prevents common coating defects like cracking, peeling, or edge splitting, especially important for tablets with complex shapes or debossed logos.
Another key advantage is its performance as a moisture barrier. While HPMC itself is hydrophilic, the continuous film provides protection against ambient moisture, beneficial for moisture-sensitive APIs. The effectiveness can be enhanced by increasing film thickness or incorporating hydrophobic excipients.
Regarding dissolution, HPMC E3 is ideal for immediate-release formulations. Being readily soluble across the physiological pH range, coatings dissolve quickly upon contact with gastrointestinal fluids, allowing prompt drug release. This predictable and rapid dissolution ensures bioavailability and therapeutic efficacy.
Furthermore, HPMC E3 enhances overall tablet stability. The coating provides a physical barrier against light and atmospheric gases, improves mechanical strength, reduces friability, and masks unpleasant tastes or odors. The smooth surface finish facilitates easier swallowing and provides an elegant appearance.
Advantage | Description | Benefit for Formulation |
---|---|---|
Film Strength & Flexibility | Robust yet pliable film (with plasticizer) | Prevents cracking, peeling; ensures integrity |
Moisture Barrier | Provides moderate protection against humidity | Enhances stability of sensitive APIs |
Rapid Dissolution | Readily soluble in GI fluids | Ensures immediate drug release |
Stability Enhancement | Protects against light, gases; improves mechanical strength; masks taste | Improves shelf life, handling, compliance |
4. How Do Manufacturing Parameters Affect HPMC E3 Coating Quality?
Achieving high-quality, uniform film coats using HPMC E3 depends heavily on precise control of manufacturing parameters. Think about it: even the best formulation can fail if the process isn’t optimized. Spray rate and atomization pressure are critical interdependent parameters. Too high a spray rate leads to overwetting, causing tablets to stick together or to the pan. Too low extends process time unnecessarily and can cause spray drying of droplets before reaching the tablet surface. Atomization pressure controls droplet size – higher pressure generally produces smaller droplets for smoother films, but excessive pressure increases spray drying.
Temperature and humidity control are equally vital. The inlet air temperature must be high enough for efficient drying but low enough to prevent damage to the API or HPMC E3 polymer. Maintaining a consistent tablet bed temperature (typically 35-45°C for aqueous HPMC E3 coatings) is key. If too low, drying is inefficient; if too high, it can cause premature drying or film defects.
Tablet bed movement, controlled by coating pan speed and baffle design, ensures uniform exposure to spray and drying air. If pan speed is too slow, coating distribution becomes uneven; if too fast, it can damage tablets and the forming film. Scale-up from laboratory to production presents significant challenges in maintaining equivalent thermodynamic conditions and mixing efficiency. Careful process development and validation are essential.
Parameter | Critical Aspect | Potential Issues if Not Optimized |
---|---|---|
Spray Rate | Balance with drying capacity | Overwetting (sticking, erosion) or spray drying |
Atomization Pressure | Droplet size control | Roughness, uneven coverage, spray drying |
Inlet/Bed Temperature | Efficient drying without damage | Overwetting, sticking, film stress (cracking) |
Pan Speed / Mixing | Uniform exposure to spray/drying | Non-uniform coating thickness, tablet attrition |
5. What Are the Common Formulation Challenges with HPMC E3 and Their Solutions?
While HPMC E3 is versatile, formulators encounter several challenges. Managing viscosity, especially when aiming for higher solids content, can be difficult. Here’s a potential solution: careful selection of the specific HPMC E3 sub-grade, precise temperature control, and appropriate mixing techniques can help manage viscosity effectively.
Common film defects include peeling (poor adhesion), cracking (insufficient plasticization or excessive drying temperatures), bridging (coating solution filling debossed logos), and twinning (tablets sticking due to overwetting). Solutions include adjusting plasticizer levels, optimizing atomization pressure, improving mixing, and balancing spray rate with drying efficiency.
Compatibility with the active pharmaceutical ingredient (API) requires consideration. Some APIs might be sensitive to moisture during aqueous coating or interact chemically with excipients. Thorough pre-formulation studies are essential to identify and address compatibility issues.
Coating uniformity issues often point to process parameters rather than formulation. The bottom line is this: ensuring proper mixing, optimizing spray patterns, and maintaining consistent spray rate and drying conditions are key. Process analytical technology (PAT) can help monitor and control coating uniformity in real-time.
Challenge | Common Cause(s) | Potential Solution(s) |
---|---|---|
High Solution Viscosity | High polymer/solids concentration, temperature | Optimize concentration, control temperature, select sub-grade |
Film Peeling/Cracking | Poor adhesion, insufficient plasticizer, high stress | Adjust plasticizer, optimize drying, add adhesion promoters |
Logo Bridging | Large droplets, poor mixing | Optimize atomization, improve mixing |
Tablet Sticking/Twinning | Overwetting | Reduce spray rate, increase drying efficiency |
6. How Does HPMC E3 Compare to Alternative Coating Polymers?
When selecting a polymer for immediate-release film coating, HPMC E3 must be compared with alternatives. So, what’s the verdict? For standard immediate-release coatings requiring good processability and rapid dissolution, HPMC E3 often presents an optimal profile among cellulose ethers.
Compared to other cellulose derivatives like Hydroxypropyl Cellulose (HPC) or Ethylcellulose (EC), HPMC E3 offers a good balance of properties. HPC provides flexible films and good adhesion but might be more humidity-sensitive. Ethylcellulose, being water-insoluble, is unsuitable for immediate-release applications where HPMC E3 excels.
Synthetic polymers like polyvinyl alcohol (PVA) systems offer excellent moisture barrier properties and superior adhesion but at higher cost. Acrylic polymers like Eudragit® E provide specialized functionality like taste-masking or pH-dependent dissolution but are more expensive and may require organic solvents.
From an environmental perspective, HPMC E3, derived from renewable plant sources, has advantages over petroleum-based synthetic polymers. It’s biodegradable and aqueous HPMC E3 coating processes eliminate organic solvents, reducing environmental hazards and workplace safety concerns.
Polymer Type | Advantages vs. HPMC E3 | Disadvantages vs. HPMC E3 | Best Applications |
---|---|---|---|
Higher HPMC Grades | Stronger films, better barrier | Higher viscosity, slower processing | When film strength is critical |
PVA-based Systems | Better barrier, faster processing | Higher cost, less history of use | Moisture-sensitive products |
Acrylic Polymers | Functional properties (pH-dependent, etc.) | Much higher cost, may need organic solvents | Specialized release profiles |
Ethylcellulose | Excellent moisture barrier | Water-insoluble, not for immediate release | Extended-release applications |
7. What Are the Future Trends for HPMC E3 in Pharmaceutical Coating Technology?
Despite being well-established, HPMC E3 continues to find new applications and improvements. What’s particularly interesting is the emergence of hybrid coatings where HPMC E3 serves as the base film former with functional polymers added to achieve targeted release profiles. This approach leverages HPMC E3’s excellent film-forming properties while incorporating functional benefits of other polymers.
Beyond traditional additives, formulators are incorporating specialized components like antioxidants, UV blockers, antimicrobial preservatives, and taste-masking agents. Nanoparticles and cyclodextrins are being explored to enhance barrier properties, add functionality, or improve solubility of poorly water-soluble drugs.
Advancements in coating equipment technology enable more efficient and precise application of HPMC E3 coatings. Modern systems feature improved spray nozzle designs, continuous coating processes, and Process Analytical Technology (PAT) tools for real-time monitoring and adaptive process control.
The regulatory landscape continues to evolve, with increased emphasis on excipient characterization and control. As personalized medicine gains traction, specialized HPMC formulations optimized for small-batch production or 3D-printed dosage forms may emerge.
Future Trend | Description | Potential Impact |
---|---|---|
Hybrid Release Systems | HPMC E3 combined with functional polymers | Better processability with specialized functionality |
Functional Additives | Incorporation of nanoparticles, cyclodextrins, etc. | Enhanced barrier, stability, or release properties |
Advanced Equipment | Continuous coating, improved nozzles, PAT integration | More uniform coatings, reduced variability |
Personalized Medicine | Specialized formulations for novel manufacturing | Adaptability to emerging production methods |
In conclusion, HPMC E3 remains an essential and versatile excipient for pharmaceutical film coating applications. Its unique balance of properties – low viscosity for efficient processing, good film formation, and compatibility with a wide range of active ingredients – makes it a preferred choice for many immediate-release tablet coatings. By understanding its chemical nature, optimizing formulation parameters, and carefully controlling the manufacturing process, pharmaceutical companies can leverage HPMC E3 to create high-quality, elegant, and functional coatings that enhance both product performance and patient experience. Morton’s specialized grades of HPMC E3 offer consistent quality and performance, backed by technical expertise to help you overcome formulation challenges. Contact Morton today to discuss how our pharmaceutical-grade excipients can improve your coating processes and product quality.
FAQ Section
Q1: Is HPMC E3 suitable for all types of pharmaceutical tablets?
HPMC E3 is highly versatile but not universally optimal for all tablet types. It excels for immediate-release formulations where rapid dissolution is desired. However, for extended-release products, higher viscosity grades or different polymers are typically more appropriate. For tablets containing highly moisture-sensitive APIs, additional moisture barrier properties might be needed beyond what basic HPMC E3 provides. HPMC E3 is generally suitable for most conventional tablet shapes and sizes when properly formulated with appropriate plasticizers and processing conditions.
Q2: What is the typical concentration range for HPMC E3 in coating formulations?
The typical concentration range for HPMC E3 in aqueous coating formulations is 5-15% w/w. The specific concentration depends on several factors including desired coating thickness, processing equipment capabilities, and the presence of other solids like pigments or plasticizers. Lower concentrations (5-8%) are easier to spray but require more coating time to achieve target weight gain. Higher concentrations (10-15%) enable faster processing but may require careful viscosity management.
Q3: How does HPMC E3 affect the shelf life of coated pharmaceutical products?
HPMC E3 coatings can positively impact product shelf life by protecting the tablet core from environmental moisture, light, and oxygen, which can degrade sensitive APIs or affect tablet physical stability. The coating improves mechanical strength, reducing friability and damage risk during handling. However, HPMC itself is hygroscopic, so in extremely humid conditions, moisture can still be absorbed by the coating. For products requiring exceptional moisture protection, additional measures like appropriate packaging or modified coating formulations may be necessary.
Q4: Can HPMC E3 be used in combination with other polymers for specialized coatings?
Yes, HPMC E3 is frequently used in combination with other polymers to achieve specialized coating properties. Common combinations include: HPMC E3 with hydrophobic polymers to enhance moisture barrier properties; HPMC E3 with enteric polymers for delayed release; HPMC E3 with PVA for improved mechanical properties; and HPMC E3 with solubility-enhancing polymers for poorly soluble drugs. These polymer blends must be carefully formulated to ensure compatibility and stability in the coating solution.
Q5: What quality control tests are essential when using HPMC E3 in film coating?
Essential quality control tests include: viscosity testing of raw material; monitoring of coating solution viscosity, pH, and solids content; continuous monitoring of process parameters (spray rate, atomization pressure, temperatures, pan speed); visual inspection of coated tablets for appearance; measurement of weight gain; disintegration and dissolution testing to verify drug release; friability testing to confirm mechanical strength improvement; and stability studies to assess the coating’s protective function over time. Advanced analytical methods like NIR or Raman spectroscopy might be used to assess coating uniformity and thickness distribution.