HPMC E50, or Hydroxypropyl Methylcellulose E50, plays a key role in many manufacturing processes but often causes confusion for purchasing managers and technical teams. You might struggle with understanding its exact properties, applications, or how to select the right grade for your specific needs. This article breaks down what HPMC E50 is, how it functions across different industries, and what makes it valuable for your production processes. With over 30 years of supplying premium cellulose derivatives to global manufacturers, we’ve compiled the most practical information to help you make informed decisions about this versatile polymer.
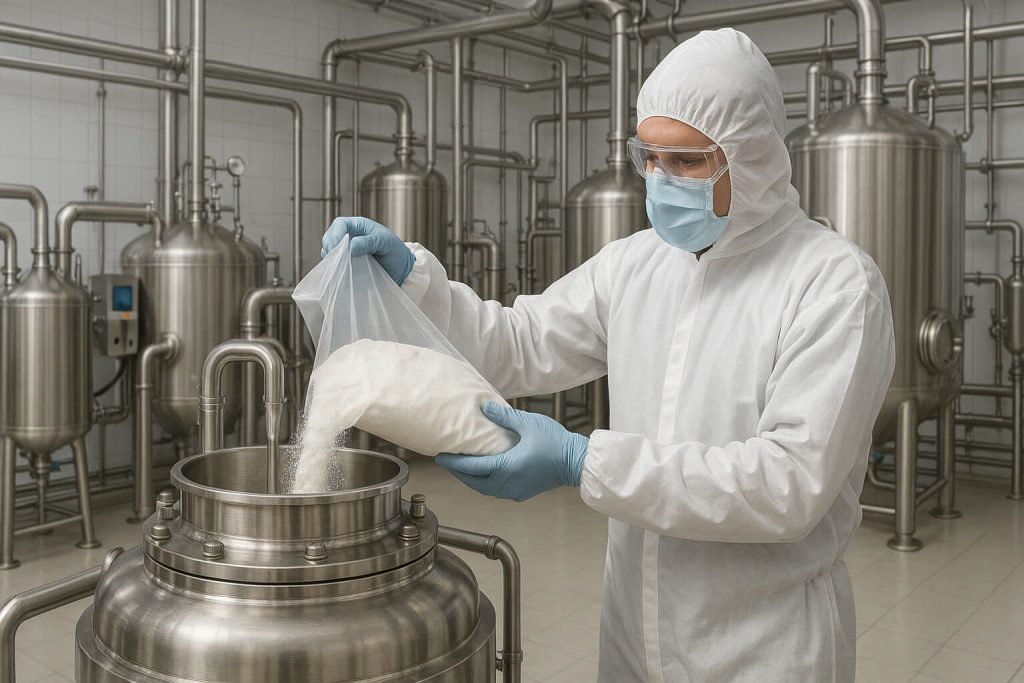
1. What Is HPMC E50 and How Is It Different From Other Cellulose Derivatives?
HPMC E50 is a semi-synthetic polymer made from cellulose. The name stands for Hydroxypropyl Methylcellulose with an E50 viscosity grade. Want to know what makes it special? It has a unique chemical structure that gives it both hydrophilic and hydrophobic properties.
The “E50” in the name refers to the viscosity grade, which means it creates a solution with 40-60 mPa·s viscosity when dissolved at 2% concentration in water at 20°C. This medium viscosity grade makes it perfect for many industrial uses where moderate thickening is needed.
HPMC E50 is made by treating cellulose with sodium hydroxide, then reacting it with methyl chloride and propylene oxide. This process adds methyl and hydroxypropyl groups to the cellulose backbone. The ratio of these groups affects how the polymer behaves in water and other solvents.
When you compare HPMC E50 to other grades like E3, E5, or E15, the main difference is viscosity. E3 has much lower viscosity (2-3 mPa·s), while E15 falls in the middle range (15-20 mPa·s).
HPMC Grade | Viscosity Range (mPa·s) | Typical Applications |
---|---|---|
E3 | 2-3 | Tablet coating, eye drops |
E5 | 4-6 | Liquid medications, food thickener |
E15 | 15-20 | Paints, construction products |
E50 | 40-60 | Tile adhesives, pharmaceuticals |
E4M | 4,000-6,000 | Sustained release tablets, cement mortars |
Physically, HPMC E50 appears as a white to off-white powder. It has no taste or odor, making it ideal for food and pharmaceutical uses. The powder flows freely and dissolves completely in cold water to form a clear solution.
2. What Industries Use HPMC E50 and Why?
The construction industry is the largest user of HPMC E50. Here’s the thing about construction applications: HPMC E50 adds water retention to cement-based products like tile adhesives, mortars, and renders. This prevents water from being absorbed too quickly by porous substrates, giving cement enough time to cure properly.
In a typical tile adhesive formulation, adding just 0.3% HPMC E50 can increase the open time by 15-20 minutes. This gives workers more time to place tiles correctly. It also improves adhesion strength by up to 25% compared to formulations without HPMC.
The pharmaceutical industry values HPMC E50 for tablet coating and controlled release formulations. When used as a coating agent, it creates a smooth, uniform film that protects the active ingredients and masks bitter tastes.
Industry | Application | Benefits of HPMC E50 |
---|---|---|
Construction | Tile adhesives | Extends open time, improves water retention |
Construction | Renders and plasters | Improves workability, reduces sagging |
Pharmaceutical | Tablet coating | Creates uniform film, masks taste |
Pharmaceutical | Controlled release | Forms gel matrix for timed drug release |
Food | Bakery products | Improves texture, extends shelf life |
Food manufacturers use HPMC E50 as a thickener and stabilizer. In ice cream, it prevents ice crystal formation, creating a smoother texture. In baked goods, it helps retain moisture and extends shelf life. HPMC E50 is also vegetarian/vegan-friendly, making it a popular choice for plant-based food products.
The personal care industry incorporates HPMC E50 into shampoos, lotions, and creams. It adds thickness and a silky feel to products without the greasiness of some other thickeners. It also helps suspend particles in formulations like exfoliating scrubs.
Paint manufacturers add HPMC E50 to water-based paints to improve flow and leveling. It helps prevent pigment settling during storage and gives the paint better spatter resistance during application. Typical addition rates range from 0.2-0.5% of the total formulation.
3. How Does HPMC E50 Affect Product Performance?
The water retention capability of HPMC E50 is perhaps its most valued property in many applications. You might be surprised to learn that adding just 0.3% HPMC E50 to a cement mortar can increase water retention from 75% to over 95%. This means the water stays in the mixture rather than being absorbed by porous substrates.
This water retention leads to better cement hydration, which results in stronger final products. Tests show that mortars with proper HPMC E50 dosage can achieve up to 30% higher compressive strength compared to those without it.
As a thickening agent, HPMC E50 creates predictable viscosity increases in water-based systems. The viscosity remains stable across a wide pH range (3-11), making it versatile for many formulations.
Property | Effect on Product | Measurement Method |
---|---|---|
Water Retention | Prevents premature drying | ASTM C1506 test method |
Viscosity | Controls flow and application properties | Brookfield viscometer at 20°C |
Binding Strength | Improves cohesion between particles | Tensile adhesion testing |
Film Formation | Creates continuous, flexible coating | Film thickness and uniformity tests |
Thermal Gelation | Forms gel at elevated temperatures | Gel point determination |
The binding ability of HPMC E50 helps hold formulations together. In tablets, it acts as a binder during wet granulation, creating stronger tablets that still disintegrate properly. In construction products, it improves adhesion to difficult substrates like glass and porcelain.
HPMC E50 forms excellent films when dried. These films are clear, flexible, and have good oxygen barrier properties. In pharmaceutical coatings, this translates to better protection for sensitive ingredients. In food applications, it can create edible films that extend shelf life.
One unique property of HPMC E50 is its thermal gelation behavior. While it dissolves easily in cold water, it forms a gel when heated above 65-80°C (depending on the exact grade). This property is useful for controlled release applications, as the gel forms a barrier that slows down drug release.
Products containing HPMC E50 typically show improved stability and shelf life. The polymer prevents particle settling in suspensions and emulsion separation in creams and lotions.
4. What Are the Technical Specifications You Need to Know About HPMC E50?
The viscosity specification is the defining characteristic of HPMC E50. But here’s what matters most: the viscosity must fall within the range of 40-60 mPa·s when measured as a 2% solution in water at 20°C using a Brookfield viscometer. This specification ensures consistent performance across batches.
Manufacturers measure viscosity using standardized methods like USP <911> or European Pharmacopoeia methods. These tests use specific equipment and conditions to ensure results are comparable between different suppliers.
The substitution degree refers to the percentage of hydroxyl groups replaced by methoxyl and hydroxypropyl groups. For HPMC E50, the methoxyl content typically ranges from 28-30%, while the hydroxypropyl content is usually 7-12%.
Technical Parameter | Typical Specification | Impact on Performance |
---|---|---|
Viscosity (2% solution) | 40-60 mPa·s | Determines thickening power |
Methoxyl Content | 28-30% | Affects solubility and gel strength |
Hydroxypropyl Content | 7-12% | Influences water retention and surface activity |
Particle Size | 95% < 100 mesh | Controls dissolution rate |
Moisture Content | ≤ 5% | Affects stability and flow properties |
Particle size distribution plays a key role in how quickly HPMC E50 dissolves. Most commercial grades specify that 95% of particles pass through a 100-mesh screen (approximately 149 microns). Finer grades dissolve faster but may be more prone to lumping during mixing.
The moisture content specification is typically ≤ 5%. Higher moisture can cause clumping during storage and may affect the stability of the final product. Most manufacturers test moisture content using loss on drying methods at 105°C.
HPMC E50 shows different solubility in different media. It dissolves well in cold water, forming clear solutions. In hot water above its gel point, it forms a gel instead. It’s also soluble in some mixed solvent systems like water/alcohol mixtures, but insoluble in pure organic solvents.
The pH of a 2% solution typically falls between 5.5-8.0. This near-neutral pH makes HPMC E50 compatible with a wide range of other ingredients without causing pH shifts that might affect stability.
5. How Do You Properly Handle and Store HPMC E50?
Proper storage conditions are critical for maintaining HPMC E50 quality. The truth is that improper storage can lead to significant property changes. Store HPMC E50 in a cool, dry place with temperatures below 30°C and relative humidity below 65%.
The original packaging should remain sealed until use to prevent moisture absorption. Once opened, any unused material should be resealed tightly. Under proper storage conditions, HPMC E50 has a shelf life of at least two years from the production date.
When handling HPMC E50, wear appropriate personal protective equipment including dust masks and gloves. While the material has low toxicity, the fine powder can cause respiratory irritation if inhaled in large amounts.
Storage Condition | Recommendation | Consequence if Not Followed |
---|---|---|
Temperature | Below 30°C | May affect viscosity stability |
Humidity | Below 65% RH | Can cause clumping and hydration |
Packaging | Sealed, moisture-proof | Prevents premature hydration |
Stacking | Maximum 3 pallets high | Prevents compaction of powder |
Rotation | First in, first out | Ensures oldest stock used first |
The dissolution technique greatly affects how well HPMC E50 performs. The “hot/cold” method works best: disperse the powder in about one-third of the required hot water (80-90°C) while stirring vigorously, then add the remaining water as cold water or ice to lower the temperature below the gel point. This prevents lumping and ensures complete hydration.
Common handling mistakes include adding the powder too quickly to water, which causes lumping, or trying to dissolve it directly in hot water, which causes immediate gelation on the surface of the particles. Another mistake is insufficient mixing time – HPMC E50 needs adequate time (usually 30-60 minutes) for complete hydration.
Before using HPMC E50 in production, perform basic quality control checks. Visual inspection should confirm a white, free-flowing powder without discoloration or clumps. A simple viscosity check of a 2% solution can verify that the material still meets specifications after storage.
6. What Are the Cost Considerations When Using HPMC E50?
The price of HPMC E50 varies based on several factors. You should know that raw material costs, especially cellulose pulp prices, directly impact HPMC pricing. Market demand, especially from the construction sector, also causes price fluctuations.
Current market prices for industrial grade HPMC E50 typically range from $3.50-$5.00 per kilogram, depending on quantity and quality. Pharmaceutical and food grades command premium prices, often 30-50% higher due to stricter quality controls and documentation requirements.
Optimizing dosage can significantly reduce costs. Many users initially add more HPMC E50 than needed due to concerns about performance. Laboratory testing to determine the minimum effective dosage often reveals opportunities for savings of 10-20% without affecting product quality.
Cost Factor | Impact Level | Optimization Strategy |
---|---|---|
Purchase Price | High | Bulk purchasing, long-term contracts |
Dosage Rate | Medium-High | Lab testing to find minimum effective dose |
Mixing Time | Medium | Proper dispersion techniques to reduce time |
Waste | Medium | Proper inventory management, careful measuring |
Quality Issues | High | Consistent supplier with good quality control |
When comparing HPMC E50 with alternative materials, consider total formulation cost rather than just the raw material price. For example, while some starches might cost less per kilogram than HPMC E50, they often require higher dosages to achieve similar effects, negating the apparent price advantage.
The long-term value of HPMC E50 comes from its multifunctional nature. In many formulations, it can replace two or more single-function additives, simplifying the formula and potentially reducing overall costs. For example, in a tile adhesive, HPMC E50 provides water retention, workability improvement, and sag resistance – functions that might otherwise require multiple additives.
When selecting suppliers, look beyond price alone. Consistency between batches is crucial for production efficiency. A slightly higher-priced supplier with excellent batch-to-batch consistency may actually save money by reducing quality issues and production problems.
7. How Can You Troubleshoot Common HPMC E50 Issues?
Dissolution problems are among the most common issues with HPMC E50. The key thing to remember is that the powder must be properly dispersed before hydration. If lumps form during mixing, try the “hot/cold” method described earlier, or pre-blend the HPMC E50 with other dry ingredients before adding water.
For persistent lumping issues, consider using a high-shear mixer or dispersing the powder in a non-solvent (like glycerin or oil) before adding to water. Some manufacturers also offer “surface-treated” grades of HPMC E50 that disperse more easily.
Inconsistent viscosity can result from several factors. Variation in water temperature during mixing is a common cause – even a 5°C difference can affect hydration rates. Ensure water temperature is consistent between batches.
Problem | Possible Causes | Solutions |
---|---|---|
Lumping during dissolution | Too rapid addition to water, improper dispersion | Use hot/cold method, increase agitation, pre-blend with dry ingredients |
Inconsistent viscosity | Variable water temperature, insufficient mixing time | Standardize water temperature, extend mixing time |
Compatibility issues | Ionic interactions, pH extremes | Adjust formula pH, add protective colloids |
Film defects | Uneven application, contamination | Filter solutions, improve application technique |
Premature gelation | Water temperature too high | Monitor and control water temperature |
Compatibility problems with other ingredients sometimes occur. High salt concentrations can reduce HPMC E50 viscosity. If your formula contains >2% salt, you may need to increase the HPMC dosage slightly. Strongly acidic or alkaline conditions can also affect performance, so try to maintain pH between 3-11 for optimal results.
Film defects like pinholes or uneven coverage often result from contamination or improper application. Filter HPMC solutions before use in coating applications to remove any undissolved particles. Ensure coating equipment applies an even layer, and control drying conditions to prevent too-rapid moisture loss.
For construction applications, sag resistance issues might occur. If renders or adhesives slide down vertical surfaces, the HPMC E50 dosage may be too low, or you might need a higher viscosity grade. Adding 0.05-0.1% more HPMC E50 often solves this problem.
When HPMC E50 is used in controlled release pharmaceuticals, inconsistent drug release rates can be problematic. This often relates to variations in tablet compression force or HPMC distribution within the tablet. Standardizing manufacturing parameters and ensuring thorough powder blending helps address these issues.
HPMC E50 is a versatile and valuable additive across many industries. Understanding its properties, proper handling, and troubleshooting techniques helps you get the most value from this material in your manufacturing processes.
The right approach to using HPMC E50 can significantly improve your products while controlling costs. Contact Morton’s technical team today for personalized assistance with your specific HPMC E50 application. Our experts can help you optimize formulations, solve technical challenges, and improve your manufacturing efficiency with our premium grade cellulose derivatives.
Q1: Is HPMC E50 safe for food and pharmaceutical applications?
HPMC E50 is approved for use in food and pharmaceutical products when sourced from manufacturers who comply with appropriate regulations. It meets FDA requirements in the US and E464 standards in Europe. Always verify that your supplier provides food or pharmaceutical grade HPMC E50 with proper certification for these sensitive applications.
Q2: How does temperature affect HPMC E50 performance?
HPMC E50 exhibits unique thermal gelation properties. It dissolves well in cold water but forms a gel when heated to its gel point (typically 65-80°C depending on the exact formulation). This property makes it useful for controlled release applications. At room temperature, it maintains stable viscosity, but you should adjust your processing methods when working at different temperatures.
Q3: What is the difference between HPMC E50 and HPMC K100M?
The main difference lies in their viscosity and substitution type. HPMC E50 has a viscosity of approximately 40-60 mPa·s (2% solution at 20°C) and belongs to the E-type with a higher methoxyl content. HPMC K100M has a much higher viscosity (80,000-120,000 mPa·s) and belongs to the K-type with different substitution ratios. E50 is typically used where moderate viscosity is needed, while K100M is used for high-viscosity applications.
Q4: Can HPMC E50 be used as a direct replacement for other cellulose ethers?
HPMC E50 cannot always directly replace other cellulose ethers without formulation adjustments. While it may substitute for some grades of methylcellulose in certain applications, differences in solubility, thermal gelation, and surface activity mean you should test thoroughly before making a switch. Dosage adjustments are typically needed when replacing CMC, HEC, or other non-HPMC cellulose derivatives.
Q5: How much HPMC E50 should I add to my formulation?
The optimal dosage of HPMC E50 varies by application. For construction products like tile adhesives, typical addition rates range from 0.2-0.5% of the dry mix. In pharmaceutical tablets, it might range from 2-5% for coating applications. Food applications typically use 0.1-1% depending on the desired thickening effect. Always start with the lower recommended dosage for your specific application and adjust based on performance testing.