Drug makers face big problems with drug stability, release timing, and patient use. When coatings fail, drugs can break down fast, release at wrong times, or taste bad. This leads to wasted batches, rejected products, and lost money. HPMC (hydroxypropyl methylcellulose) offers a good answer. It makes stable coatings with exact release patterns. Tests show HPMC-coated drugs stay good up to 36 months longer. This article looks at how HPMC works in film coating, its barrier traits, release methods, formula factors, process steps, and how it compares to other options.
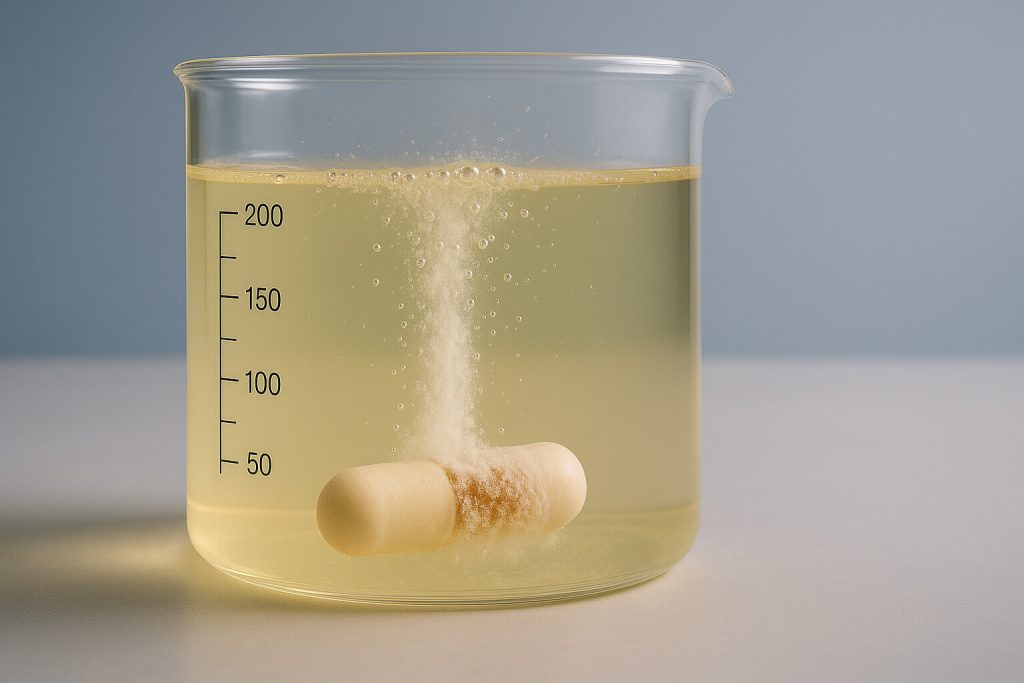
1. What Are the Basic Properties of HPMC for Film Coating?
HPMC is a cellulose ether with special traits for drug coating. It has a cellulose base with methoxy and hydroxypropyl groups. Did you know that these groups let HPMC form strong films while still mixing well with water?
The physical traits of HPMC make it great for coating. It forms clear, tough films that don’t crack and stick well to tablets. It blocks oxygen while letting some moisture pass. This helps keep drugs from breaking down.
HPMC comes in many grades with thickness from 3 to 100,000 mPa·s. Low thickness grades (3-15 mPa·s) work for fast-release coatings. High thickness grades (4,000-100,000 mPa·s) fit slow-release uses. The chemical groups also change, with different ratios affecting how it dissolves and reacts to heat.
HPMC Grade | Thickness (mPa·s) | Main Use | Film Traits |
---|---|---|---|
E3 | 3 | Fast release | Thin, fast dissolving |
E5 | 5 | Fast release | Medium thick, quick dissolving |
E15 | 15 | Fast release | Thicker, medium quick dissolving |
K4M | 4,000 | Slow release | Thick, slow wearing away |
K15M | 15,000 | Slow release | Very thick, very slow wearing away |
K100M | 100,000 | Extra-long release | Extremely thick, very long wearing away |
When compared to other coating polymers, HPMC has many good points. Unlike ethylcellulose, it mixes well with water, making it more eco-friendly. Compared to polyvinyl alcohol, HPMC stays more stable when humidity changes. It also costs less than many man-made options while working just as well.
The weight of HPMC molecules affects how it forms films. Higher weight grades form stronger, more stretchy films but need more water. This trade-off between film strength and ease of use needs careful thought during formula design.
2. What Are the Basic Barrier Properties of HPMC Coatings?
The barrier traits of HPMC coatings help protect drugs from outside harm. Here’s the thing about moisture protection: HPMC forms a semi-open layer that slows water vapor without fully blocking it. This helps prevent moisture damage while avoiding brittle films.
HPMC films give medium oxygen protection, which helps drugs that react with oxygen. The polymer chains pack tight enough to limit oxygen passing through. Adding anti-oxygen agents to HPMC can help more. For drugs very sensitive to oxygen, makers often mix HPMC with other polymers to create a stronger barrier.
Light protection is another key job of HPMC coatings. While pure HPMC films are clear, makers add pigments to block UV and visible light. Titanium dioxide works as the most common light-blocker, giving great protection against light damage.
Barrier Type | HPMC Level | Ways to Improve | Limits |
---|---|---|---|
Moisture | Medium | Add water-avoiding parts | Not good for very moisture-sensitive drugs |
Oxygen | Low to medium | Mix with anti-oxygen agents | Not enough for very oxygen-sensitive drugs |
Light | Low (clear) | Add TiO₂ or iron oxides | Needs additives for good protection |
Taste/Odor | Medium to high | Make film thicker | May slow dissolving if too thick |
Film thickness affects barrier function. Doubling the coating thickness cuts passing by 40-60%. This link is not straight due to tiny channels in thicker films. Most drug uses have HPMC coating thickness between 20-80 μm. This balances barrier traits with dissolving needs.
The way HPMC takes up water also helps its barrier job. When wet, the outer layer forms a gel that slows water getting to the core. This self-fixing system helps keep products stable even when humidity levels change.
3. What Makes HPMC Ideal for Controlled Drug Release?
HPMC works well for controlled-release due to its water uptake and gel forming. When an HPMC-coated tablet touches stomach fluids, it forms a gel layer around the core. You might be surprised to know this gel layer acts as a wall, controlling how fast the drug releases into the body.
The way drugs move through HPMC follows Fick’s law. The rate depends on the drug amount and path length. As water moves deeper, the gel layer grows thicker, making the path longer. This creates a self-fixing system where drug release slowly drops over time, often giving steady release rates.
Release Method | How It Works | Typical Release Pattern | Best HPMC Grade |
---|---|---|---|
Diffusion | Drug moves through gel layer | Square root of time | K4M, K15M |
Erosion | Gel layer slowly wears away | Steady (linear) | K100M |
Swelling | Matrix expands, creating pores | Dropping rate | E4M, E15M |
Combined | Multiple methods at once | Two-phase or S-shaped | K15M + E5 blend |
The pH-linked behavior of HPMC adds another plus to controlled release. Unlike some polymers that dissolve only at certain pH levels, HPMC stays the same across body pH range (1.2-7.4). This pH-free trait makes sure drug release stays steady throughout the gut, no matter patient differences in stomach acid.
Case studies show HPMC works well in controlled release. A metformin formula using HPMC K100M gave 24-hour slow release. This helped patients by cutting dosing from three times daily to once daily. Another case with diltiazem used HPMC K15M to keep blood levels steady for 12 hours. This greatly cut the risk of chest pain compared to fast-release forms.
The pattern of chemical groups on HPMC affects its water uptake and gel strength. More hydroxypropyl groups speed up water uptake. More methoxyl groups make the gel layer stronger. By picking certain HPMC grades, makers can fine-tune release patterns to match treatment needs.
4. How Do Formula Factors Affect HPMC Coating Results?
The molecular weight and chemical group pattern of HPMC greatly impact coating results. The reality is that higher weight grades form stronger films but need more water, slowing the coating process. The methoxyl:hydroxypropyl ratio sets water attraction. More hydroxypropyl creates more water-loving films that soak up water and dissolve faster.
Softeners play a key role in HPMC film traits. These additives help polymer chains move, making films more flexible. Common softeners for HPMC include polyethylene glycols, propylene glycol, and triacetin. The best softener amount ranges from 10-30% of polymer weight. Higher levels make films more flexible but may cut barrier traits.
Softener | Typical Amount (% w/w) | Effect on Film Traits | Fit with HPMC |
---|---|---|---|
PEG 400 | 10-20% | More flexible, water-attracting | Excellent |
Propylene glycol | 5-15% | Medium flexible, less water-attracting | Very good |
Triacetin | 10-25% | Good flexible, water-avoiding | Good |
Glycerin | 5-15% | High flexible, very water-attracting | Excellent |
Dibutyl sebacate | 15-30% | High flexible, water-avoiding | Medium |
Solvent systems greatly affect coating quality. Water-based HPMC solutions offer eco and safety plus points but dry more slowly than organic systems. The solvent mix affects polymer chain shape during film forming. This changes physical traits of the final coating. Typical water-based HPMC solutions contain 5-10% polymer. Organic solutions may hold up to 15-20% due to lower thickness.
Additives in HPMC formulas serve many jobs. Wetting agents like polysorbate 80 help coating stick to the tablet core. Anti-sticking agents such as talc keep tablets from sticking together during coating. Pigments not only add color but also block light and help product ID.
The ratio between HPMC and additives needs careful balance. Too many additives can break polymer chain bonds, weakening the film. A typical formula might contain 60-80% HPMC, 10-20% softener, 5-10% pigments, and 1-5% wetting agents or other working additives.
Heat sensitivity is another formula factor. HPMC shows a unique heat gelling trait. It forms a gel when heated above its cloud point (typically 70-90°C). Coating must stay below this temperature to prevent early gelling. This would block spray tips and create coating flaws.
5. What Are the Processing Methods for HPMC Film Coating?
Drug makers can apply HPMC coatings using either water or organic solvent methods. Let me explain why water coating has become the industry standard. It removes fire risks, cuts eco impact, and avoids leftover solvent issues. However, water systems need longer drying times. They may cause stability issues with moisture-sensitive drugs.
Spray settings critically affect coating quality. The spray rate must balance fast application with enough drying to prevent flaws. Spray pressure sets droplet size. Higher pressures make finer droplets that dry faster but may cause more spray-drying losses. The gun-to-bed distance affects spray pattern overlap and coating success.
Spray Setting | Typical Range | Effect if Too Low | Effect if Too High |
---|---|---|---|
Spray rate | 5-15 g/min/kg | Slow process | Too wet, flaws |
Spray pressure | 1.5-3.0 bar | Large drops, uneven coating | Fine mist, spray drying |
Pattern air pressure | 1.0-2.0 bar | Narrow spray pattern | Wide pattern, wall losses |
Gun-to-bed distance | 8-12 inches | Too wet | Spray drying, poor success |
Number of spray guns | 2-12 (size based) | Longer process time | Possible over-wetting |
Drying conditions greatly impact film quality. Inlet air temperature typically ranges from 50-70°C. This balances drying speed with the risk of heat gelling. Airflow rate affects both drying power and tablet movement within the coating pan. Not enough drying leads to sticky tablets and coating flaws. Too much drying can cause early film forming and cracking.
The coating process has several phases. A starting warming phase brings tablets to the target temperature. The actual spraying phase applies the coating solution at a set rate. A curing phase after spraying lets the film fully join and strengthen. This curing step, typically 15-30 minutes at coating temperature, greatly improves film function and stability.
Scaling up from lab to production presents several challenges. Equipment size changes don’t directly translate to process settings. The ratio of spray rate to drying power must stay the same across scales. Tablet bed temperature serves as a key scale-free parameter. It should stay the same no matter the batch size.
Process tracking tools help maintain coating quality. Automated systems track factors like tablet bed temperature, exhaust air humidity, and pan pressure. Near-infrared testing can provide real-time coating thickness measurements. This allows exact endpoint finding and steady batch-to-batch quality.
6. How Does HPMC Compare to Other Coating Polymers?
When comparing HPMC to other cellulose types, several function differences show up. The truth is that methylcellulose dissolves faster than HPMC but forms weaker films. Ethylcellulose provides better moisture protection but needs organic solvents or special water mixes. Hydroxypropyl cellulose sticks better to tablet cores but costs more than HPMC.
HPMC holds several good points over man-made polymers. Unlike polymethacrylates (Eudragit®), HPMC doesn’t need pH fixing steps. Compared to polyvinyl alcohol, HPMC shows less batch-to-batch change in dissolving traits. It also processes more easily than polyvinyl acetate phthalate, which tends to cause spray tip clogging.
Polymer Type | Water Solubility | Film Strength | Process Complexity | Cost Level |
---|---|---|---|---|
HPMC | High | Medium | Low | Low |
Ethylcellulose | Not soluble | High | High | Medium |
Polymethacrylates | pH-based | High | Medium to high | High |
PVA | High | Medium to high | Low | Medium |
PVAP | pH-based | Medium | Medium | Medium to high |
Cost analysis shows HPMC as one of the most money-saving coating options. Raw material costs run 30-50% lower than many man-made options. The simple processing needs cut labor and energy costs. HPMC’s stability allows longer shelf-life for coating solutions, cutting waste. These factors make HPMC the most cost-saving option for many basic coating uses.
The approval status of HPMC provides another plus. It has GRAS (Generally Recognized As Safe) status with the FDA. It appears in the inactive ingredient list for many approved drug products. The European, Japanese, and other global drug rules also accept HPMC. This makes global product approval easier.
Market trends show continued growth in HPMC use. The shift toward water coating systems favors HPMC over some options. The polymer’s flexibility lets it serve many jobs. From simple taste-masking to complex modified release, it cuts inventory needs. Recent advances include special grades with tighter thickness specs for more predictable processing.
Summary
HPMC works as a flexible, strong polymer for drug film coating with proven skills across many uses. From basic moisture protection to advanced controlled-release systems, HPMC gives reliable results through its unique chemical structure and physical traits. Makers gain real benefits including 30-50% lower raw material costs and up to 36 months longer product shelf life. Morton offers drug-grade HPMC made just for coating uses, with tech support to perfect your formula and process settings. Contact Morton’s drug polymers team today to ask for samples and tech papers for your specific coating challenges.
Q1: Can HPMC be used for enteric coating applications?
HPMC alone cannot provide true enteric protection as it dissolves in acidic stomach fluid. However, you can change HPMC with phthalate or acetate succinate groups to create enteric forms (HPMCP or HPMCAS). Or you can mix HPMC with pH-based polymers like polymethacrylates in a sub-coat/top-coat system. This approach uses HPMC as a buffer layer between the core and the enteric polymer, stopping direct mixing that might harm either part.
Q2: What is the stability profile of HPMC coatings during long-term storage?
HPMC coatings keep physical stability for 3-5 years under normal storage conditions (25°C/60% RH). The polymer shows very little chemical breakdown over time, with studies showing less than 2% change in molecular weight after 36 months. Moisture sensitivity remains the main worry, as high humidity (>75% RH) can soften films and cut their protective power. Temperature cycling between cold and warm may cause tiny cracks in films with too little softener. Proper packing in moisture-proof containers with drying agents extends coated product shelf life.
Q3: How do different thickness grades of HPMC affect drug release rates?
Higher thickness HPMC grades create thicker gel layers when wet, extending drug release times. A K100M grade typically gives 20-24 hour release patterns, while K4M grades often yield 8-12 hour patterns for the same drug. The link between thickness and release rate follows a log rather than straight pattern. Doubling thickness does not double release time. Matrix tablets using K15M might release 80% of drug in 8 hours, while K100M releases only 50% in the same time. Low-thickness grades (E3-E5) wet too quickly for extended-release but work well for delayed fast-release where a short lag time is wanted.
Q4: Are there special considerations when coating moisture-sensitive drugs with HPMC?
Moisture-sensitive drugs need changed HPMC coating methods. You should pre-dry the tablet cores to moisture content below 1.5% before coating. Using higher inlet temps (65-70°C) and lower spray rates cuts exposure time to moisture. Adding water-avoiding parts like magnesium stearate (1-3%) to the coating cuts water vapor passing. Some makers apply a coat of a water-avoiding polymer before the HPMC layer. The coating solution should have the least practical water content, possibly using alcohol-water mixes where rules allow. After coating, quick drying and packing with drying agents further protects moisture-sensitive products.
Q5: What are the common troubleshooting approaches for HPMC coating defects?
For film cracking, add 5-10% more softener or lower curing temperature. Fix peeling issues by adding a wetting agent (0.1-0.5%) to help sticking or roughening tablet cores before coating. Fix bridging in tablet logos or break-lines by cutting coating solution thickness or raising spray pressure for finer drops. Fix uneven coating by changing pan speed and baffles to help tablet bed movement. Solve orange-peel texture by raising solution temperature to cut thickness or lowering the spray rate. Combat logo filling by using more dilute solutions and finer spraying. For all flaws, changing one factor at a time helps find the root cause without making new problems.