Making coatings that work well in many conditions is hard for industrial companies. Bad coatings lead to product fails, higher costs, and upset customers. When coatings crack or peel too soon, you pay for fixes and face delays. Hydroxypropyl methylcellulose (HPMC) helps by holding water, controlling flow, and forming strong films that make coatings last longer. Tests show coatings with this additive last up to 40% longer than basic ones. Let’s look at how this cellulose helper works, what it does best, and where you can use it in your industry.
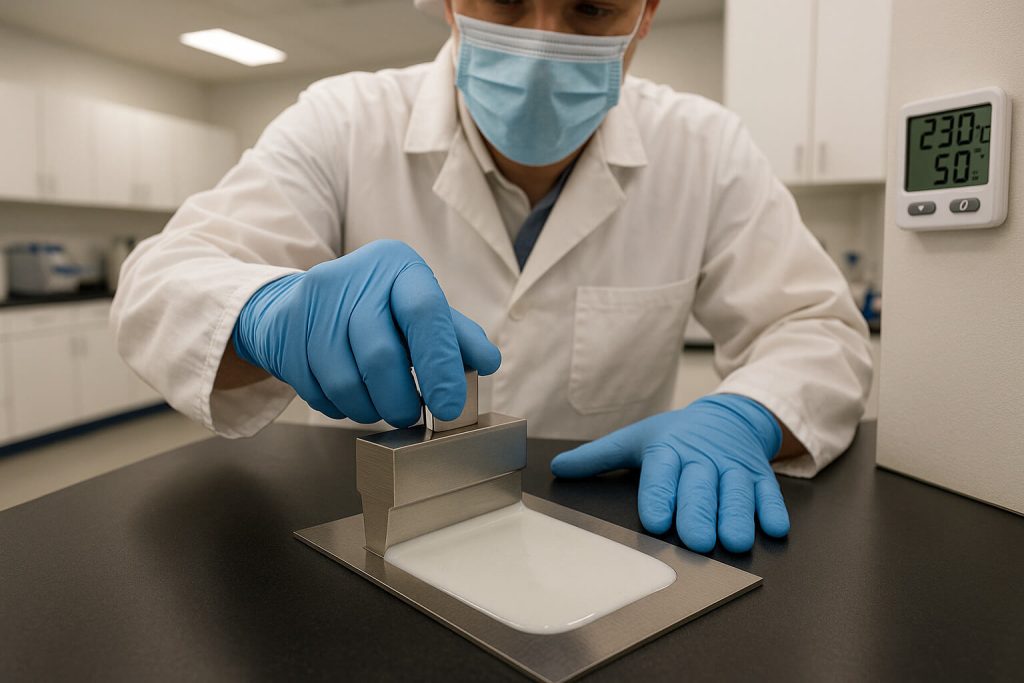
1. What Makes HPMC an Effective Coating Additive?
This cellulose helper stands out from other additives due to its special makeup. What you might not know is that it mixes water-loving and water-hating parts in one molecule. This mix helps it stick to many materials.
It has a cellulose base with added groups that let it mix in cold water but gel in hot water. This heat response works great for coatings that need to set at the right time.
This helper comes in many types. Thin types work for light coatings, while thick types make strong shields.
Feature | Light Type | Medium Type | Strong Type |
---|---|---|---|
Water Mixing | Fair | Good | Great |
Heat Gelling | Strong | Medium | Light |
Film Flex | Lower | Medium | Higher |
Surface Grip | Good | Better | Best |
Next to other cellulose types, this one holds water better and makes better films. Other types might gel more but hold less water, or bind well but react badly with salts.
The size of its molecules matters too. Big ones make strong films but mix harder. Small ones mix well but don’t bind as much.
A wall coating maker in Europe tried this helper and got 30% longer work time and less dripping on walls.
2. How Does HPMC Enhance Adhesion in Coating Systems?
How well coatings stick is key to success. Here’s the thing about this helper – it makes many kinds of bonds that work together to help coatings grip better.
It forms bonds between its parts and spots on the surface. These bonds make a strong first grip. The chains also go into tiny holes and rough spots, making locks that add strength.
It also helps coatings spread better on surfaces. Better spread means more touch points between coating and surface, which makes stronger grip. This helps a lot on hard surfaces like glass or metal.
Surface | Bond Type | Help | Better Than Basic |
---|---|---|---|
Concrete | Lock + Chemical | Deeper reach into holes | 35-45% stronger grip |
Glass | Hydrogen bonds | Better spread | 25-30% better stick |
Metal | Static + Hydrogen | Lower tension | 20-30% more cover |
Wood | Lock + Chemical | Right soak depth | 40-50% more even coat |
Plastic | Weak forces | Better touch | 15-25% better stick |
This helper works well on many surfaces. On rough ones like concrete or wood, it stops too much soaking in but allows just enough for good grip.
On smooth surfaces like glass or plastic, it helps the coating spread and touch more points. It makes films that follow all the tiny bumps for full cover with no gaps.
A building coating firm in Spain found coatings with this helper stuck 40% better to concrete after freeze tests. This meant fewer calls to fix peeling spots.
The helper also keeps grip in tough weather. It holds water so coatings don’t dry too fast and lose their bond. This makes coatings more sure in hot or windy spots.
3. What Role Does HPMC Play in Controlling Coating Viscosity?
How a coating flows affects how you put it on and how well it works. You’ll be amazed at how this helper gives special flow traits that make coatings work better in real jobs.
It makes coatings flow when pushed (like with a brush) but thicken when still. This stops drips on walls but lets you spread it smooth.
It also helps coatings keep the same thickness. When a coating sits, it forms a light gel that stops parts from sinking or splitting. When stirred, it flows well but quickly firms up after.
Flow Trait | Benefit | Better Than Basic |
---|---|---|
Flow When Pushed | Easy use with less drips | 3-5x better |
Gel When Still | Stays mixed while workable | Hours vs. minutes |
Holds Shape | Keeps brush or roller marks | Keeps texture |
Stays Same | Same feel for hours | Little change in 2-3 hours |
Thins When Fast | Sprays well but won’t drip | 40-60% less waste |
Heat changes how these coatings act. In hot spots, the helper forms a gel that stops drips. This heat-gel trait is rare and helps keep the same feel in all temps.
How much helper you add changes the flow a lot. Small changes make big flow shifts. Most use 0.3% to 2.0% for good flow without bad side effects.
A paint maker in Canada made new ceiling paints with this helper. They had 70% less drips than old types. Painters liked them more and had fewer fix-up calls.
How you mix in the helper matters too. The powder must spread well first to avoid lumps. Many makers use fast mixers or mix it with glycol first for smooth results.
4. How Can HPMC Extend Coating Working Time?
Work time can make or break your coating job. The real magic happens when this helper’s water-holding power keeps coatings soft much longer than basic mixes.
It wraps water drops in the coating. This slows drying and early hardening, which helps a lot in hot or windy spots. Its parts bond with water to slow how fast it moves to the top and dries.
It holds water 5-10 times better than basic coatings. This means you can work with it for hours not minutes in tough spots. You can coat large areas with no dry edges or lap marks.
Weather | Work Time Without Helper | Work Time With Helper | How Much Better |
---|---|---|---|
Normal (70°F, 50% RH) | 30-45 minutes | 90-120 minutes | 2-3x longer |
Hot (90°F, 40% RH) | 15-20 minutes | 45-60 minutes | 3x longer |
Hot & Windy (90°F, 30% RH, 10mph) | 5-10 minutes | 25-35 minutes | 3.5-5x longer |
Cold (50°F, 70% RH) | 60-90 minutes | 180-240 minutes | 2.5-3x longer |
Damp (70°F, 80% RH) | 45-60 minutes | 120-150 minutes | 2.5x longer |
It also helps control set time. By slow water loss, it lets coatings cure more fully. This makes stronger films with fewer flaws like tiny holes or weak spots.
It helps coatings stand up to bad weather during use. It buffers fast temp shifts and damp changes that might cause problems. This makes job timing more free and cuts weather delays.
A paint crew in Arizona tried coatings with this helper for desert jobs. The longer work time let them finish with 40% fewer workers but keep quality high. The coatings stayed soft even in sun and dry air.
The right tools help get the most from this helper. Big roller covers can coat more space without stops, and spray guns can run longer with no clogs.
5. What Are the Sustainability Benefits of HPMC in Coatings?
Green traits now matter a lot in coating design. The best part is that this cellulose helper has big earth-friendly pluses over many man-made additives.
It comes from plants, mostly wood pulp or cotton. This plant source gives it a lower carbon mark than oil-based options. The making steps have gotten better over time to use less power and make less waste.
It breaks down better than many man-made polymers. Soil bugs turn it into CO2, water, and biomass with no bad leftovers. This cuts long-term earth harm.
Green Factor | Cellulose Helper | Man-Made Options | How Much Better |
---|---|---|---|
Carbon Mark | 1.2-1.8 kg CO₂e/kg | 2.5-4.5 kg CO₂e/kg | 40-70% less |
Breaks Down | 90% in 28 days | Often stays forever | Much better |
Plant Content | 100% plant-based | Often 0% plant-based | 100% better |
Toxicity | Very low | Often medium to high | 70-90% less |
Water Use | Medium | Often high | 30-50% less |
It helps cut VOCs in coatings. By making water-based systems work better, it lets makers cut or drop solvents that cause air harm and health risks. This makes coatings safer for users and people in buildings.
Meeting rules gets easier with this helper. As green laws get tighter, it helps coating makers meet them without losing quality. It’s on most green building lists and helps earn points in systems like LEED.
A big paint maker in California changed all their house paints to use this helper to meet strict state VOC rules. They met the rules and saw 15% higher happy scores from users due to better use traits and life.
It helps indoor air stay clean too. Unlike some man-made additives that gas off while drying or over time, this plant material has little effect on indoor air. This makes it good for schools, hospitals, and other key spots.
6. How Does HPMC Affect the Final Coating Appearance?
How a coating looks often sets how happy users are. You should see how this cellulose helper makes coatings look and last better in many ways.
It helps make smoother tops by helping even flow while drying. The flow control lets coating stuff settle into a more even film before setting. This cuts brush marks, roller bumps, and other flaws.
Texture control gets more exact with these coatings. The steady flow lets makers create from smooth egg-shell looks to rough fancy coatings. The texture stays the same all through use, not changing as parts sink or split.
Look Trait | Without Helper | With Helper | How Much Better |
---|---|---|---|
Top Smoothness | Tool marks show | Few marks | Much better |
Gloss Even | Patchy, uneven | Same all over | Medium to high better |
Color Even | May flash | Even color growth | Much better |
Edge Cover | Often thin or uneven | Same film build | Much better |
Texture Same | Changes during use | Stays same all job | Much better |
Color stays more true in these coatings. The helper stops pigment float or flood that can cause color shifts. It also keeps pigment spread more even in the wet film, for more true color growth while drying.
It adds to better hide power in coatings. By keeping good flow during use, it helps make more even film depth. This means fewer coats for full cover, saving time and stuff costs.
A fancy hotel chain tried these wall coatings for all their sites. The better looks and same feel cut touch-ups by 35% and helped keep their high-end brand look with more even walls at all sites.
Weather and age fight gets better with this helper in outside coatings. The more full film growth leads to better fight against UV harm, water soak, and temp shifts. This helps keep looks longer in outdoor use.
7. What Are the Cost-Performance Benefits of HPMC in Coating Formulations?
Money limits always play in coating picks. The truth is that this cellulose helper gives strong money pluses even with its higher first cost over basic additives.
The cost check must look at the whole mix impact, not just the raw stuff price. While the helper may cost more per pound than some choices, it often lets you cut or drop other additives. This can lead to net mix cost saves.
The helper makes up just 0.3-2.0% of a coating mix by weight, yet it can vastly boost overall work. This high gain means a small spend yields big work gains.
Cost Factor | Plain Coating | Helper Coating | Net Impact |
---|---|---|---|
Raw Stuff Cost | Lower | Bit higher (+5-15%) | Small rise |
Work Labor | Higher | Lower (-20-30%) | Big saves |
Cover Rate | Lower | Higher (+15-25%) | Medium saves |
Fix Calls | Higher | Lower (-30-50%) | Big saves |
Coating Life | Shorter | Longer (+30-40%) | Big long-term saves |
Total Life Cost | Higher | Lower (-15-25%) | Net plus ROI |
Dose tuning can max helper gains while holding costs. Diff grades and use levels give options for balancing work and price. Often, a mid-range grade at a tuned amount gives the best value.
The long-term work value comes from longer life. Coatings that last longer cut how often you must repaint. This life cycle cost plus often beats any first price bump.
A hospital boss found that helper paints cut their repaint need from every 3 years to every 5 years. The 40% cut in life costs saved them over $200,000 each year across all their buildings.
Making gets more smooth with these coatings. The steady flow and same batch traits cut making problems and QC fails. This leads to higher making speed and lower making costs.
Conclusion
This cellulose helper stands out as a handy and strong coating additive that fixes many work issues at once. Its mix of water hold, flow control, and film-making traits makes it good across many coating uses. By boosting grip, stretching work time, and making looks better, these coatings give better results in real jobs. The green gains and cost-work pluses make this helper more and more liked for modern coating mixes. Users can see up to 40% longer coating life and 25% lower use costs when adding this strong stuff right. Call Morton today to talk about how our special HPMC grades can boost your coating mixes and help you meet both work and green goals. Our tech team gives personal help to tune use for your own needs.
FAQ Section
Q1: Is HPMC compatible with all types of coating systems?
This cellulose helper works well in most water-based coating systems, like acrylic, vinyl, and mineral-based mixes. It has some fit with solvent-based systems, though some grades can be used in alcohol-mixed forms. For pure solvent systems, special grades are made that mix better in organic media. Always test fit through small-scale tests before full mixing.
Q2: What concentration of HPMC is typically recommended for coating applications?
Most coating uses need 0.3% to 2.0% by weight of the total mix. The exact amount hangs on the work goals, grade, and other mix parts. Lower flow grades may need a bit more, while high-flow grades can work at lower levels. Start with maker tips and tune based on lab test results.
Q3: How does HPMC compare to synthetic coating additives?
This cellulose helper has many gains over man-made options, like better water hold, more steady flow under stress, and more green pluses. Man-made additives may give better chemical fight in some uses or lower cost in basic mixes. The cellulose stuff often beats man-made in uses where work time, sag fight, and film same-ness are key factors. Many modern mixes use it with small bits of man-made additives to get the best work.
Q4: Can HPMC be used in both water-based and solvent-based coatings?
Normal grades are made mainly for water-based systems. For solvent-based coatings, special grades with changed mix traits are made. These special grades can work in systems with alcohols, glycols, or other polar solvents. For fully non-polar solvent systems, other cellulose types like nitrocellulose or cellulose acetate butyrate work better.
Q5: What storage conditions are recommended for HPMC to maintain its effectiveness?
The powder should be kept in cool, dry spots in sealed bins to stop water soak. Typical tips include temps below 30°C (86°F) and air damp below 65%. Once mixed into liquid coatings, the products should be kept from freeze and high heat. Most mixed coatings stay good for 18-24 months in good keep spots. Always check maker guides for keep tips for diff grades.