Drug makers face big challenges when creating new medicines. Poor ingredient choices can cause batch failures and costly delays. Tablets may fail tests or break apart during shipping. Without good binding agents, pills might not release drugs properly. This wastes time and money. Methocel HPMC K4M solves these problems. It binds tablets well and controls drug release. This guide shows you how to use HPMC K4M in your formulations. You’ll learn about its properties, benefits, and best practices for different drug forms.
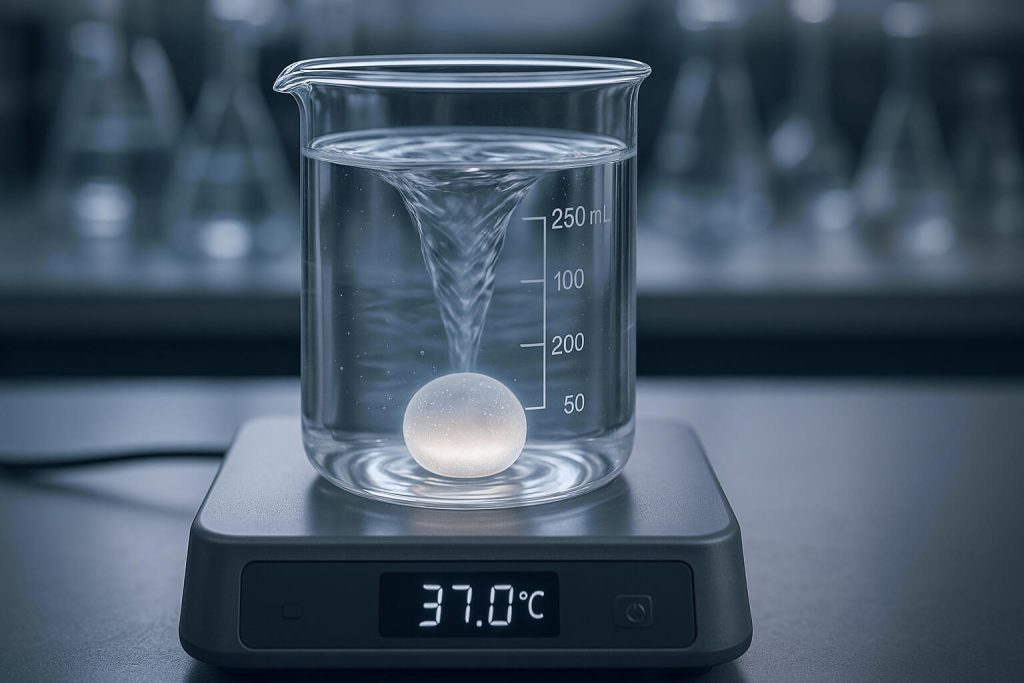
1. What Are the Key Properties of Methocel HPMC K4M?
Methocel HPMC K4M is a special type of cellulose. Here’s what makes it work so well: it has methyl and hydroxypropyl groups attached to cellulose chains. This creates a polymer that dissolves in water and forms gels.
The chemical makeup includes 19-24% methoxyl content. It also has 7-12% hydroxypropoxyl content. These numbers matter because they control how the polymer behaves. The viscosity measures 4000 centipoises in a 2% water solution at 20°C.
Viscosity tells you how thick the solution gets. HPMC K4M sits between thinner grades like K100 and thicker ones like K15M. This middle range works well for many drug uses. It’s thick enough to control release but not too thick to process.
The molecular weight ranges from 10,000 to 1,500,000 daltons. This wide range gives the polymer its unique properties. Higher molecular weights create stronger gels. Lower weights flow better during processing.
Property | Value | Why It Matters |
---|---|---|
Viscosity | 4000 cP | Controls gel strength |
Methoxyl content | 19-24% | Affects how it dissolves |
Hydroxypropoxyl content | 7-12% | Changes film properties |
Molecular weight | 10,000-1,500,000 Da | Determines gel strength |
The polymer dissolves easily in cold water. It makes clear or slightly cloudy solutions. But here’s something cool: it doesn’t dissolve in hot water above 50-55°C. When you cool it down, it dissolves again. This helps during manufacturing.
This behavior is called thermoreversible gelation. It means you can heat solutions to remove air bubbles. Then cool them down to get clear solutions again. Many other polymers can’t do this.
HPMC K4M stays stable up to 200°C. This means normal drug making processes won’t damage it. Store it below 30°C in dry conditions. It lasts five years when stored properly.
The material comes as a white powder. It has no smell or taste. This makes it good for medicines. It won’t change how your drug tastes or looks. The powder flows well through equipment.
Particle size affects how well the polymer works. Smaller particles dissolve faster. Larger particles may leave lumps in solutions. Most suppliers provide particle size data to help you choose the right grade.
2. How Does HPMC K4M Function in Drug Applications?
HPMC K4M works by forming gels when it touches water. The magic happens when tablets with this polymer get wet. The outside forms a gel layer. This layer controls how fast the drug comes out.
The gel forms quickly when water hits the tablet. First, the polymer swells up. Then it makes a thick gel around the tablet. Drugs must pass through this gel to get out. Thicker gels slow down drug release.
Water penetrates the tablet surface within seconds. The polymer chains start to hydrate and expand. This creates a thick gel layer that grows over time. The gel layer acts like a barrier that drugs must cross.
You can control release speed by changing how much HPMC K4M you use. More polymer makes thicker gels. Thicker gels release drugs slower. This lets you make 8-hour or 24-hour release tablets.
The polymer also binds tablet ingredients together. During mixing, it forms bridges between particles. These bridges hold the tablet together. This binding strength helps tablets stay intact during shipping and handling.
When you use 20% or more HPMC K4M, it creates a matrix. This matrix spreads throughout the whole tablet. It controls both drug release and tablet swelling. This works great for long-acting medicines.
Use | Amount Needed | What It Does | Release Pattern |
---|---|---|---|
Tablet binder | 2-5% | Holds tablet together | Fast release |
Controlled release | 15-40% | Controls drug release speed | 8-24 hours |
Film coating | 5-15% | Protects from moisture | Depends on core |
Suspension aid | 0.1-0.5% | Prevents settling | Not applicable |
Film coating uses HPMC K4M’s ability to form smooth films. These films protect tablets from moisture. They also make tablets look better. The films are clear and flexible.
For liquid medicines, small amounts of HPMC K4M thicken the liquid. This stops particles from settling. The liquid stays mixed longer. This thickening effect makes liquid medicines easier to measure and pour.
The polymer shows special flow behavior. It gets thinner when you shake or stir it. But it thickens again when you stop. This makes liquids easy to pour but stable when sitting.
3. What Are the Main Benefits for Drug Manufacturers?
HPMC K4M costs less than many other polymers. The savings add up quickly when you make large batches. It costs 20-30% less than special controlled-release polymers. Yet it works just as well for most uses.
Cost comparisons show clear benefits. Special polymers like Eudragit cost much more per kilogram. HPMC K4M delivers similar performance at lower cost. This improves profit margins on finished products.
You can use regular equipment to process HPMC K4M. No special machines needed. This saves money on equipment costs. Your staff doesn’t need extra training either. The polymer works with standard mixing and tablet-making machines.
Equipment works well with HPMC K4M across all common drug processes. Fluid bed granulators work well with it. High-shear mixers handle it easily. Tablet presses don’t need special tooling.
Regulators around the world accept HPMC K4M. It’s in the USP, EP, and JP books. The FDA says it’s safe to use. This acceptance means faster approval for your new drugs. Less paperwork and fewer questions from regulators.
The regulatory history spans decades of safe use. Thousands of approved products contain HPMC K4M. This track record reduces regulatory risk. New uses face fewer questions.
Benefit | How Much You Save | Why It Matters |
---|---|---|
Lower cost | 20-30% vs other polymers | More profit per batch |
Standard equipment | No new machines needed | Lower startup costs |
Fast approval | Weeks or months saved | Get to market faster |
Less testing | Fewer studies needed | Lower development costs |
The polymer flows well during processing. It doesn’t create much dust. This makes it safer to handle. It mixes evenly with other ingredients. This even mixing means consistent tablets every time.
Quality stays the same from batch to batch. Good suppliers provide consistent material. This means your tablets will perform the same way every time. Less testing needed. Fewer rejected batches.
The polymer handles small changes in processing well. If temperature or humidity changes a bit, it still works. This makes manufacturing more reliable. This reliability reduces the chance of batch failures.
You can use HPMC K4M for multiple jobs in one formulation. It can bind, control release, and coat tablets. This reduces the number of ingredients you need. Simpler formulations are easier to make and test.
4. Which Dosage Forms Work Best with HPMC K4M?
Fast-release tablets work well with 2-5% HPMC K4M. The right amount gives strong tablets that still break apart quickly. Too much polymer slows down tablet breakdown. Too little makes weak tablets.
Tablet hardness improves with HPMC K4M. Tablets get 20-40% harder when you add 3-4% polymer. Harder tablets handle shipping better. They don’t chip or break as easily.
The tablets still break apart fast enough for quick drug release. Keep polymer levels below 5% for fast release. Higher amounts may make tablets too slow to break apart.
Slow-release tablets need 15-40% HPMC K4M. This creates a strong matrix that controls drug release. The amount you use determines how long the tablet releases drug. More polymer means longer release.
Extended release works through gel formation and erosion. The polymer creates a barrier that drugs must cross. As the gel erodes, new surface area becomes available for release.
Tablet Type | HPMC K4M Amount | Release Time | Key Points |
---|---|---|---|
Fast release | 2-5% | Under 30 minutes | Balance strength and speed |
Slow release | 15-40% | 8-24 hours | More polymer = longer release |
Coated tablets | 5-15% coating | Depends on core | Protects tablet inside |
Chewable tablets | 1-3% | Immediate | Improves texture |
Release patterns follow clear rules. Lower amounts (15-20%) give steady release rates. Higher amounts (30-40%) give more constant release. This helps you design the release you want.
Capsules work well with HPMC K4M too. You can make granules with the polymer inside capsules. Or make small tablets to put in capsules. The capsule shell doesn’t change how the polymer works.
Hard capsules with HPMC K4M granules stay uniform. The drug spreads evenly throughout. The polymer keeps everything stable. No interactions with the capsule shell.
Liquid medicines use small amounts of HPMC K4M. Just 0.1-0.5% thickens the liquid enough. This stops particles from settling. The liquid pours easily despite being thicker.
Liquid suspensions with HPMC K4M stay mixed longer. The polymer resists bacteria better than other thickeners. This means longer shelf life. This stability reduces the need for preservatives.
5. How Do You Optimize HPMC K4M Concentrations?
Start by defining what you want your tablet to do. The first step involves setting targets for release time, tablet strength, and manufacturing needs. These goals guide how much polymer to use.
For fast-release tablets, start with 2-3% HPMC K4M. Test tablet hardness and break-apart time. Add more polymer if tablets are too weak. Watch break-apart time to keep it fast enough.
Slow-release tablets need a different approach. Start with 20% HPMC K4M for 12-hour release. Test how fast the drug comes out. The relationship between amount and release speed follows clear patterns.
Target Release | Starting Amount | How to Adjust | Testing Points |
---|---|---|---|
8-hour release | 15-18% | Add 2-3% if too fast | 1, 2, 4, 8 hours |
12-hour release | 20-25% | Fine-tune in 1-2% steps | 1, 2, 4, 8, 12 hours |
24-hour release | 30-35% | May need tablet shape changes | 1, 4, 8, 12, 24 hours |
Once weekly | 40-50% | Consider other polymers too | Daily for 7 days |
Check how HPMC K4M works with other ingredients. It mixes well with most tablet ingredients. But some combinations need testing. Watch out for ingredients that absorb lots of water.
Disintegrants work well with HPMC K4M in fast-release tablets. Super-disintegrants like croscarmellose sodium help tablets break apart faster. Regular disintegrants may need amount adjustments.
Processing conditions affect how well HPMC K4M works. The polymer performs well across many different conditions. But best results need attention to specific settings.
Wet granulation with HPMC K4M needs 10-15% less water than other binders. The polymer binds particles very well. This saves time in drying steps.
Tablet pressing may need slightly higher forces with HPMC K4M. The polymer is elastic and springs back. Higher forces ensure tablets reach target hardness.
Common problems have clear solutions. Slow drug release usually means not enough polymer or poor gel formation. Fast release suggests too little polymer or processing issues.
Tablet defects like capping often relate to moisture or pressing force. Adjust these before changing polymer amounts. Most problems come from processing, not the polymer itself.
6. What Quality Standards Apply to HPMC K4M?
The USP sets strict rules for drug-grade HPMC K4M. These rules ensure every batch meets the same high standards. The rules cover identity tests, purity, and performance.
Identity tests confirm the material is really HPMC K4M. Infrared light tests check the molecular structure. Chemical tests measure methoxyl and hydroxypropoxyl content. These tests prove you have the right grade.
Purity tests look for harmful substances. Heavy metals must stay below 20 ppm. Leftover solvents follow ICH safety limits. Bacteria counts must meet drug standards.
Test | USP Limit | Typical Results | Test Method |
---|---|---|---|
Viscosity | 3000-5600 cP | 4000 ± 400 cP | Brookfield viscometer |
Methoxyl content | 19.0-24.0% | 21-23% | Gas chromatography |
Hydroxypropoxyl content | 7.0-12.0% | 8-10% | Gas chromatography |
Water content | ≤5.0% | 2-4% | Karl Fischer titration |
Heavy metals | ≤20 ppm | <5 ppm | Atomic absorption |
European rules match USP requirements closely. The EP adds some extra tests for specific impurities. This gives you options for testing methods.
Testing needs special equipment and trained people. Viscosity tests require exact temperature control. The accuracy of these tests affects whether batches pass or fail.
Certificates should include all required tests plus extra supplier tests. Look for particle size, bulk density, and flow properties. These affect how well the polymer works in your formulation.
Good suppliers meet more than just basic requirements. Check for quality certifications and inspection records. A good supplier gives consistent quality and helpful technical support.
Regular supplier visits ensure continued quality. Check manufacturing processes and quality control. Look at change control systems. This prevents quality problems before they happen.
Stability data shows how long the material stays good. Long-term studies prove stability under different storage conditions. This supports shelf-life claims and storage rules.
Conclusion
Methocel HPMC K4M gives drug makers a reliable solution for better formulations. It binds tablets well and controls drug release effectively. The polymer costs less than alternatives while meeting strict quality standards. Its proven safety record speeds regulatory approval. Manufacturing becomes more reliable with consistent polymer performance. For companies ready to improve their products, Morton provides expert support and high-quality HPMC K4M backed by years of experience. Contact Morton’s team today to discuss your needs and see how HPMC K4M can help your next product succeed.
FAQ
Q1: What is the difference between HPMC K4M and other HPMC grades?
HPMC K4M has a viscosity of 4000 cP, making it perfect for controlled release. Other grades like K100M or K15M have different thicknesses for different uses. K4M offers the best balance of gel strength and processability.
Q2: Can HPMC K4M be used in immediate release formulations?
Yes, HPMC K4M works great in fast-release tablets as a binder. Use 2-5% to bind tablets without slowing drug release. It makes tablets stronger while keeping fast breakdown times.
Q3: What is the typical shelf life of HPMC K4M?
HPMC K4M lasts 5 years when stored properly. Keep it in original packaging below 30°C and 65% humidity. Proper storage maintains all performance properties throughout the shelf life.
Q4: Is HPMC K4M compatible with all active pharmaceutical ingredients?
HPMC K4M works with most drugs. But test each combination, especially with moisture-sensitive compounds. Compatibility studies should include accelerated stability testing.
Q5: What are the regulatory considerations for using HPMC K4M?
HPMC K4M is listed in major drug books (USP, EP, JP) and is FDA-approved as safe. It meets all requirements for drug products. The extensive regulatory history speeds approval processes.