Introduction
What is HPMC? A Quick Overview
Hydroxypropyl Methylcellulose (HPMC) is a versatile and non-ionic cellulose ether derived from natural materials such as wood pulp or cotton. Renowned for its exceptional properties—such as thickening, binding, and film-forming—HPMC serves as a cornerstone in various industries. Beyond being a chemical compound, it acts as a transformative agent that enhances efficiency and quality across applications ranging from pharmaceuticals to construction materials.
Why HPMC is Essential Across Industries
HPMC is not limited to one field—it’s a critical component driving innovation across multiple sectors. In construction, it improves the strength and workability of mortars and cement. In the pharmaceutical industry, it ensures precise drug delivery and reliable tablet formation. The food and cosmetics industries also rely on its ability to stabilize and enhance texture. Understanding the science and applications of HPMC unlocks its potential to revolutionize products, streamline processes, and meet the evolving demands of both industries and consumers.
This article explores the unique chemistry of HPMC, its broad applications, and the transformative impact it delivers across a variety of industries.
What Does HPMC Mean?
Breaking Down Hydroxypropyl Methylcellulose
Hydroxypropyl Methylcellulose (HPMC) is a modified cellulose derivative designed to combine functionality and adaptability. Derived from natural cellulose, it undergoes a chemical transformation to acquire hydroxypropyl and methyl groups, giving it unique water-solubility, thermal gelation, and binding properties. This dual modification allows HPMC to excel in applications where standard cellulose falls short, acting as a thickener, stabilizer, and film-forming agent in products ranging from construction materials to pharmaceuticals.
But how do these modifications translate to real-world performance? Let’s dive deeper.
HPMC vs. Methylcellulose: Key Differences
While both HPMC and Methylcellulose share a cellulose-based origin, their differences define their utility. HPMC boasts hydroxypropyl substitutions, enhancing its thermal stability and solubility across a wider range of temperatures. Methylcellulose, on the other hand, lacks these modifications, limiting its adaptability in complex formulations. HPMC’s enhanced properties make it the preferred choice in industries requiring precision and versatility, such as controlled drug release or cement formulations that demand robust performance.
Now, let’s examine the industries where HPMC truly shines.
How is HPMC Made?
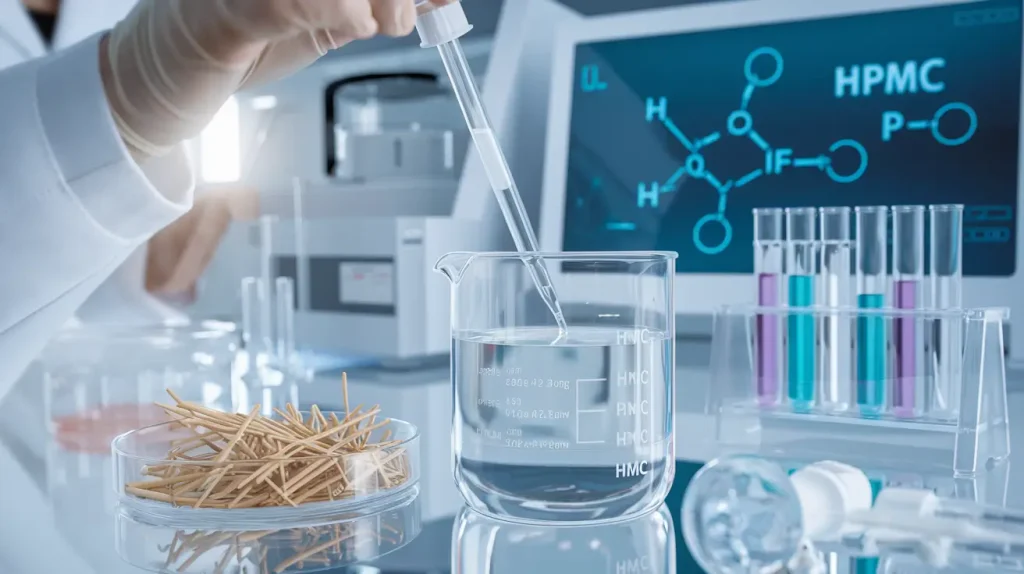
The HPMC Production Process: A Simplified Guide
Hydroxypropyl Methylcellulose (HPMC) is crafted through a meticulous process that transforms raw cellulose into a versatile, multifunctional polymer. It begins with the extraction of natural cellulose from sources like wood pulp or cotton. This cellulose is then treated with a combination of methyl chloride and propylene oxide in a controlled environment. These reactions introduce methyl and hydroxypropyl groups, resulting in the modified molecular structure that gives HPMC its unique solubility, binding, and thermal gelation properties.
Curious about how these modifications impact its practical applications? Keep reading.
Role of Cellulose Ethers in Creating HPMC
At its core, HPMC is part of the cellulose ethers family, a group of polymers known for their exceptional performance in a variety of applications. Cellulose ethers like HPMC are engineered to optimize the properties of natural cellulose, adding versatility to its natural strength. The chemical modifications enhance its functionality, enabling it to dissolve in cold water, form stable gels at specific temperatures, and provide consistent performance in demanding conditions.
So, how does this versatility translate into real-world usage? Let’s explore its applications.
Core Properties of HPMC
Thermal Gelation: Why Temperature Matters
One of the standout features of Hydroxypropyl Methylcellulose (HPMC) is its thermal gelation property. When exposed to heat, HPMC solutions transform into gels, creating stability in high-temperature environments. This unique characteristic is critical in applications like drug formulations, where controlled release relies on this thermal responsiveness, and in construction, where it ensures the consistency of cement and mortar under variable conditions.
But what makes HPMC so adaptable across different formulations? Let’s find out.
Viscosity Modifier: How It Enhances Formulations
HPMC serves as an exceptional viscosity modifier, adapting to specific needs across diverse formulations. Its ability to thicken solutions without compromising performance makes it a valuable tool in industries like food production, cosmetics, and pharmaceuticals. By tailoring the viscosity, HPMC ensures smooth application, uniform texture, and improved product efficacy.
How does HPMC maintain hydration and stability in challenging environments? The next property holds the answer.
Water Retention Agent: Protecting Against Dehydration
In applications where water loss can compromise quality—such as cement, mortars, or skincare products—HPMC acts as a powerful water retention agent. It locks in moisture, ensuring proper curing in construction materials or hydration in personal care products. This property not only improves durability but also enhances the efficiency of resource use.
And there’s one more feature that makes HPMC truly indispensable. Let’s look at its role in surface protection.
Film-Forming Abilities: Applications in Coatings
HPMC’s film-forming capability elevates its versatility. It creates uniform, durable films that protect surfaces in paints, coatings, and even pharmaceutical tablets. This property provides a balance of flexibility and strength, ensuring long-lasting protection and a polished finish in every application.
Clearly, these properties illustrate why HPMC is a preferred choice across numerous industries. But how does it perform in real-world applications? Let’s explore.
HPMC in Construction and Building Materials
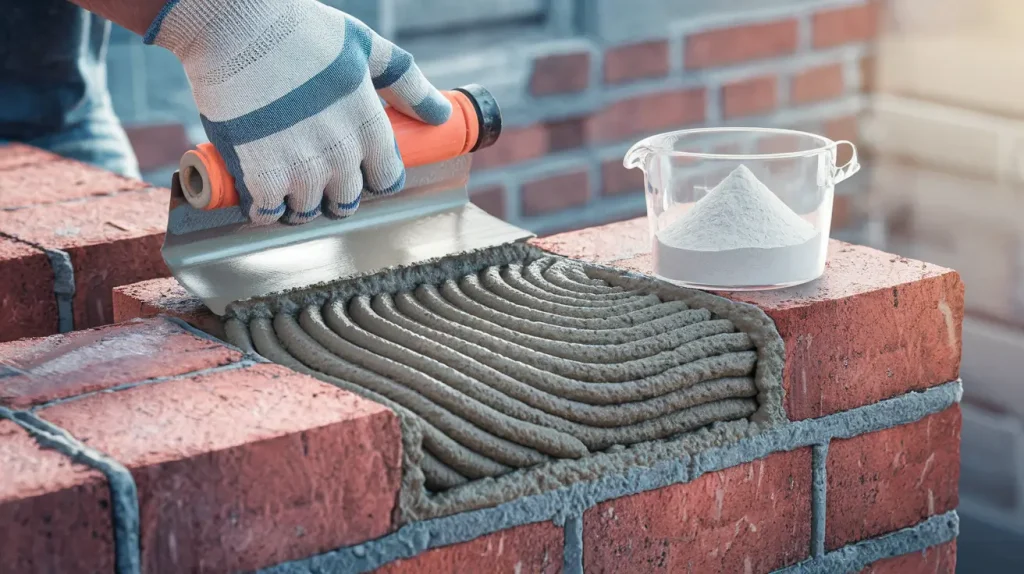
HPMC in Cement and Mortars: Strengthening Structures
In the realm of construction, Hydroxypropyl Methylcellulose (HPMC) is a cornerstone of innovation. By enhancing the performance of cement and mortars, HPMC provides superior bonding strength, water retention, and workability. It ensures that mixtures cure evenly, reducing cracks and improving durability. Whether for load-bearing structures or intricate masonry, HPMC ensures long-lasting and reliable results in construction projects.
But how does HPMC optimize specific formulations like dry-mix mortars? Let’s take a closer look.
Dry-Mix Mortars: The Role of HPMC in Consistency and Workability
Dry-mix mortars rely on HPMC to achieve consistent quality and performance. Acting as a stabilizer and lubricant, HPMC ensures uniform dispersion of components and prevents segregation. This results in smoother application, better adhesion, and reduced material waste. From tile adhesives to wall plasters, HPMC elevates the efficiency and reliability of dry-mix mortars, making it an essential ingredient in modern building practices.
Clearly, HPMC transforms construction materials. But how does it contribute to other industries? Let’s explore its broader impact.
HPMC in Pharmaceuticals
HPMC as a Pharmaceutical Excipient: Tablet Binding Agent
Hydroxypropyl Methylcellulose (HPMC) is a vital component in pharmaceutical formulations, acting as a highly effective excipient. Its binding properties ensure that tablets hold their structure during manufacturing, storage, and administration. HPMC not only provides mechanical strength but also enhances the stability and uniformity of active ingredients, ensuring reliable dosage delivery.
But what sets HPMC apart in revolutionizing drug delivery systems? The next section reveals the answer.
Controlled Drug Release with HPMC: A Revolutionary Approach
One of HPMC’s most groundbreaking applications in medicine is its ability to enable controlled drug release. By forming hydrophilic matrices, HPMC regulates the release rate of active ingredients, allowing for extended therapeutic effects and reduced dosing frequency. This property revolutionizes drug delivery systems, improving patient compliance and treatment outcomes in chronic and acute conditions.
How does HPMC’s customization impact its effectiveness in various formulations? Let’s delve deeper.
Dissolution Properties and Substitution Degree in Medicine
HPMC’s role in pharmaceuticals extends to its customizable dissolution properties, determined by its substitution degree. Adjusting the levels of hydroxypropyl and methyl groups enables precise control over how the polymer interacts with water and releases active ingredients. This flexibility ensures that HPMC meets the diverse demands of drug formulations, from immediate-release tablets to slow-release capsules.
These capabilities make HPMC an essential asset in the pharmaceutical industry. But where else can this remarkable polymer make a difference? Let’s explore its broader applications.
HPMC in Food and Beverage Applications
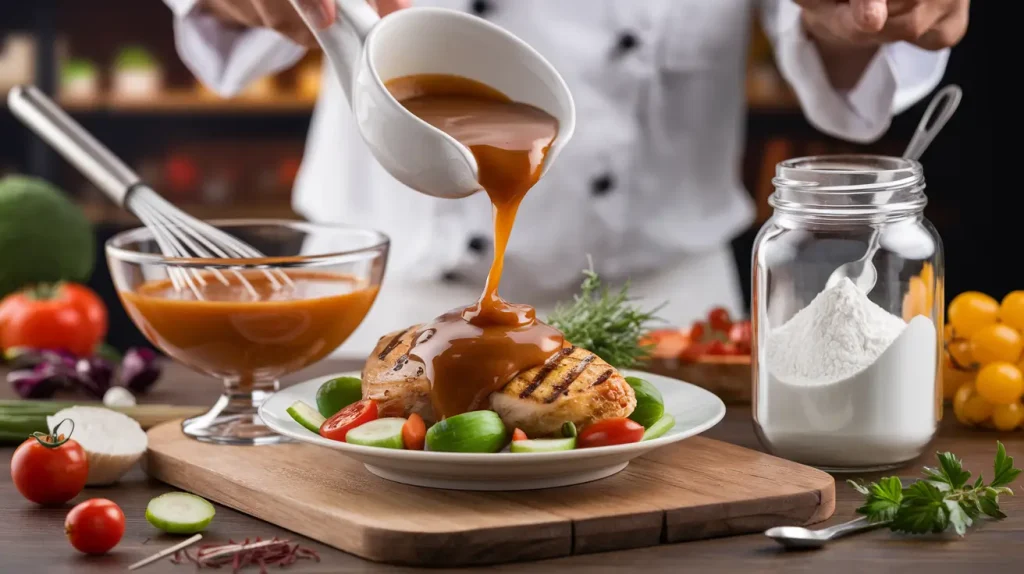
HPMC as a Food Additive: Vegan and Gluten-Free Alternatives
Hydroxypropyl Methylcellulose (HPMC) has become a staple ingredient in the food and beverage industry, particularly for vegan and gluten-free products. As a plant-derived alternative to animal-based ingredients like gelatin, HPMC provides the binding and thickening properties needed for meat substitutes, dairy-free cheeses, and gluten-free baked goods. Its neutral flavor and exceptional functionality make it a key component in meeting the growing demand for ethical and allergen-friendly food options.
But how else does HPMC elevate food products to meet modern expectations? Let’s explore further.
Improving Texture and Shelf Life with HPMC
Beyond its role as an additive, HPMC significantly enhances the texture and stability of food products. It improves mouthfeel in soups and sauces, stabilizes emulsions in dressings, and ensures consistent dough performance in baked goods. Additionally, HPMC acts as a moisture barrier, extending shelf life by preventing staling and spoilage. This multifunctionality not only improves product quality but also optimizes production efficiency.
With such versatility, it’s clear why HPMC is a game-changer in food innovation. But how does its use compare to other sectors? Let’s take a broader view.
HPMC in Cosmetics and Personal Care
Film Formers in Skincare and Haircare Products
Hydroxypropyl Methylcellulose (HPMC) is a cornerstone ingredient in cosmetics and personal care formulations, thanks to its film-forming abilities. In skincare, it creates a breathable, protective layer that locks in moisture, enhancing hydration and skin softness. In haircare products like shampoos and styling gels, HPMC forms lightweight films that improve hair manageability, add shine, and reduce frizz. Its natural origin and gentle properties make it suitable for all skin and hair types, including sensitive ones.
But how does HPMC ensure long-term stability in these formulations? Let’s break it down.
Enhancing Product Stability and Viscosity
HPMC also plays a critical role in ensuring the stability and consistency of personal care products. It acts as a thickening agent, providing the desired viscosity in lotions, creams, and serums. This not only improves the sensory experience during application but also ensures that ingredients remain evenly distributed, preventing separation or settling. By enhancing both performance and aesthetics, HPMC enables manufacturers to meet high consumer expectations for quality and reliability.
Clearly, HPMC is indispensable in cosmetics. But how does it perform in sustainable and eco-friendly formulations? Let’s find out.
HPMC in Paints and Coatings
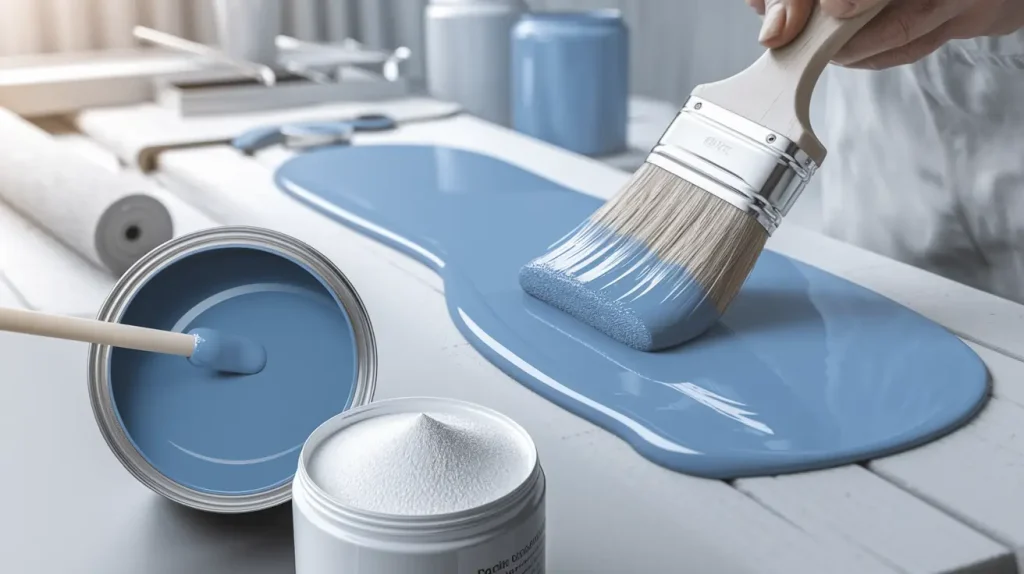
The Importance of Rheological Properties in Paint Formulations
Hydroxypropyl Methylcellulose (HPMC) is an indispensable ingredient in the paints and coatings industry, primarily due to its rheological properties. By enhancing viscosity and flow control, HPMC ensures that paints and coatings maintain consistent texture and stability throughout application. It prevents dripping and sagging, enabling precise and efficient coverage on walls, furniture, or industrial surfaces. This ensures that every brushstroke or spray yields professional-quality results.
But how does HPMC contribute to the visual and structural integrity of coatings? Let’s explore further.
Achieving Smooth Finishes with HPMC
HPMC also excels in delivering smooth, uniform finishes, a critical attribute in high-performance coatings. Its ability to regulate the dispersion of pigments ensures even color distribution without streaking or clumping. Additionally, HPMC promotes the formation of durable films, providing resistance to cracking and wear. Whether used in decorative paints or protective industrial coatings, HPMC guarantees a flawless finish that stands the test of time.
With these advantages, it’s no surprise that HPMC is a go-to solution for paint and coating professionals. But what innovations might lie ahead for this versatile material? Let’s consider the possibilities.
Sustainability and Environmental Impact of HPMC
Biodegradable Polymers: An Eco-Friendly Choice
Hydroxypropyl Methylcellulose (HPMC) stands out as a sustainable alternative in a world increasingly focused on eco-friendly solutions. Derived from renewable natural cellulose, HPMC is biodegradable, breaking down into harmless substances without harming the environment. This property makes it a sought-after material in industries looking to reduce their ecological footprint. From green building initiatives to clean-label products, HPMC offers an effective and sustainable choice that aligns with environmental goals.
But how does HPMC compare to other similar polymers in environmental performance? Let’s take a closer look.
Comparing HPMC to Carboxymethyl Cellulose (CMC)
When compared to other cellulose derivatives like Carboxymethyl Cellulose (CMC), HPMC demonstrates distinct environmental advantages. While both are biodegradable and plant-based, HPMC's thermal gelation and enhanced water retention capabilities make it more versatile, requiring less material in certain applications. Its ability to deliver high performance with minimal resource use further cements its status as an eco-conscious option across various industries.
Clearly, HPMC provides a pathway to innovation with sustainability in mind. But how can industries fully harness its potential while meeting future environmental challenges? Let’s explore the next steps.
Market Trends and Innovations in HPMC
Current Demand Across Industries
The global demand for Hydroxypropyl Methylcellulose (HPMC) is surging, fueled by its versatility and proven performance. Industries ranging from construction to pharmaceuticals are driving growth as they increasingly rely on HPMC to enhance their products. In construction, it ensures the stability of mortars; in food, it acts as a vegan-friendly additive; and in personal care, it supports the development of high-performance formulations. This widespread utility positions HPMC as a cornerstone ingredient in modern manufacturing.
But what’s next for HPMC as technology continues to advance? The answer lies in emerging applications.
Emerging Applications of HPMC in New Technologies
Beyond traditional applications, HPMC is carving a niche in emerging technologies. From its use in advanced 3D printing materials to its role in next-generation drug delivery systems, HPMC is at the forefront of innovation. Researchers are exploring its potential in sustainable packaging and bio-based polymers, showcasing how HPMC can meet the demands of a rapidly evolving technological landscape.
With such a wide range of possibilities, how will HPMC’s role continue to expand? Let’s look at the future outlook for this game-changing material.
Choosing the Right HPMC for Your Needs
Substitution Degrees: Methoxyl and Hydroxypropyl Content Explained
Selecting the ideal Hydroxypropyl Methylcellulose (HPMC) begins with understanding substitution degrees. The levels of methoxyl and hydroxypropyl groups determine the polymer’s key properties, including solubility, gelation temperature, and viscosity. Higher methoxyl content enhances water retention and thermal gelation, while increased hydroxypropyl substitution improves flexibility and solubility. Tailoring these ratios allows manufacturers to meet specific performance requirements across industries like pharmaceuticals, construction, and food production.
But how can these properties be fine-tuned for specific industrial challenges? Let’s delve into customization.
Customizing HPMC for Industrial Applications
Not all HPMC grades are created equal. Customizing HPMC for industrial use involves optimizing its viscosity, particle size, and substitution degrees to align with the unique demands of each application. For instance, high-viscosity HPMC is preferred for tile adhesives, ensuring superior bonding, while pharmaceutical-grade HPMC prioritizes purity and controlled release capabilities. This customization ensures that every industry achieves maximum efficiency and product performance.
Wondering how to make the best choice for your application? Let’s explore the decision-making process.
Challenges in Using HPMC
Compatibility with Organic Solvents: Tips for Success
While Hydroxypropyl Methylcellulose (HPMC) offers incredible versatility, its compatibility with organic solvents can present challenges in certain formulations. Not all solvents interact uniformly with HPMC, which may lead to incomplete dissolution or reduced effectiveness. Overcoming these challenges requires selecting the appropriate solvent system and fine-tuning concentrations to maintain stability and functionality. By understanding these nuances, manufacturers can optimize HPMC performance without compromising product quality.
But how can industries navigate the complexities introduced by temperature sensitivity? Let’s examine further.
Temperature Sensitivity: Avoiding Common Pitfalls
HPMC’s thermal gelation property, while highly beneficial, also introduces sensitivity to temperature fluctuations. This sensitivity can lead to unexpected changes in viscosity or gel strength, particularly in environments with varying temperatures. To avoid these pitfalls, it’s essential to control processing conditions and understand the specific thermal behavior of the selected HPMC grade. Proper formulation and testing can mitigate temperature-related issues, ensuring consistent results.
Successfully addressing these challenges ensures HPMC remains a reliable solution. What best practices can help achieve this? Let’s explore practical strategies for overcoming obstacles.
Conclusion
The Versatility of HPMC: A Game-Changer Across Industries
Hydroxypropyl Methylcellulose (HPMC) has proven itself as a transformative ingredient, bridging the gap between diverse industries with its unmatched versatility. From enhancing construction materials and pharmaceutical formulations to redefining food, cosmetics, and paints, HPMC is more than just a compound—it’s an enabler of innovation and efficiency. Its unique properties, including thermal gelation, water retention, and film formation, make it a cornerstone material in modern manufacturing and beyond.
But how can you unlock its full potential for your specific application? Let’s consider the next steps.
Your Next Steps: Finding the Right HPMC Solution
The journey to leveraging HPMC’s potential begins with selecting the right grade tailored to your industry’s needs. Whether optimizing for viscosity in construction or purity in pharmaceuticals, understanding HPMC’s capabilities is key to maximizing its benefits. Partnering with trusted suppliers and staying informed about market trends can help you make confident, strategic choices.
Are you ready to explore how HPMC can elevate your products and processes? Now is the time to act.
FAQ Section (Rewritten)
Q1: What is HPMC and what does it stand for?
A1: HPMC stands for Hydroxypropyl Methylcellulose, a versatile cellulose derivative. It is widely used as a thickener, stabilizer, and film-forming agent in industries such as construction, pharmaceuticals, food, and cosmetics.
Q2: How does HPMC differ from other cellulose derivatives like CMC?
A2: HPMC has unique properties, such as thermal gelation and superior water retention, which distinguish it from Carboxymethyl Cellulose (CMC). These properties make it ideal for applications like controlled drug release and enhancing construction materials.
Q3: Is HPMC safe for food and pharmaceutical use?
A3: Yes, HPMC is recognized as safe for consumption and is commonly used as a vegan alternative to gelatin in food products. In pharmaceuticals, it serves as an excipient in tablets and capsules.
Q4: How does HPMC enhance construction material performance?
A4: In construction, HPMC improves water retention, workability, and bonding strength in materials like mortars and adhesives. This ensures consistent application and enhances material durability.
Q5: Can HPMC be customized for specific applications?
A5: Absolutely. HPMC can be tailored by adjusting its viscosity, particle size, and the degree of substitution (methoxyl and hydroxypropyl content) to meet various industrial needs.
Q6: Which industries benefit most from HPMC?
A6: HPMC serves a variety of industries, including construction, pharmaceuticals, food and beverages, cosmetics, and paints, due to its multifunctional and adaptable properties.
Q7: Is HPMC environmentally friendly?
A7: Yes, HPMC is biodegradable and derived from renewable cellulose sources, making it a sustainable and eco-friendly option.
Q8: What challenges might arise when working with HPMC?
A8: Challenges include compatibility with certain organic solvents and sensitivity to temperature changes. However, these issues can be mitigated through proper formulation techniques.
Q9: How does HPMC contribute to product shelf life?
A9: HPMC acts as a moisture barrier, which helps prevent staling in baked goods, spoilage in food products, and maintains the stability of formulations in cosmetics and pharmaceuticals.
Q10: Where can I source high-quality HPMC?
A10: High-quality HPMC can be sourced from reputable suppliers specializing in cellulose derivatives. Always verify their certifications and product specifications to ensure quality and suitability for your application.