Aspettare che l'adesivo per piastrelle faccia presa correttamente può decretare il successo o il fallimento del progetto di installazione. I problemi di tempistica sono fonte di frustrazione anche per i professionisti più esperti.
L'idrossipropilmetilcellulosa (HPMC) agisce come un agente essenziale per la ritenzione idrica, prolungando notevolmente il tempo di presa degli adesivi per piastrelle, consentendo di regolare correttamente il posizionamento delle piastrelle e mantenendo al contempo una consistenza ottimale per installazioni di livello professionale.
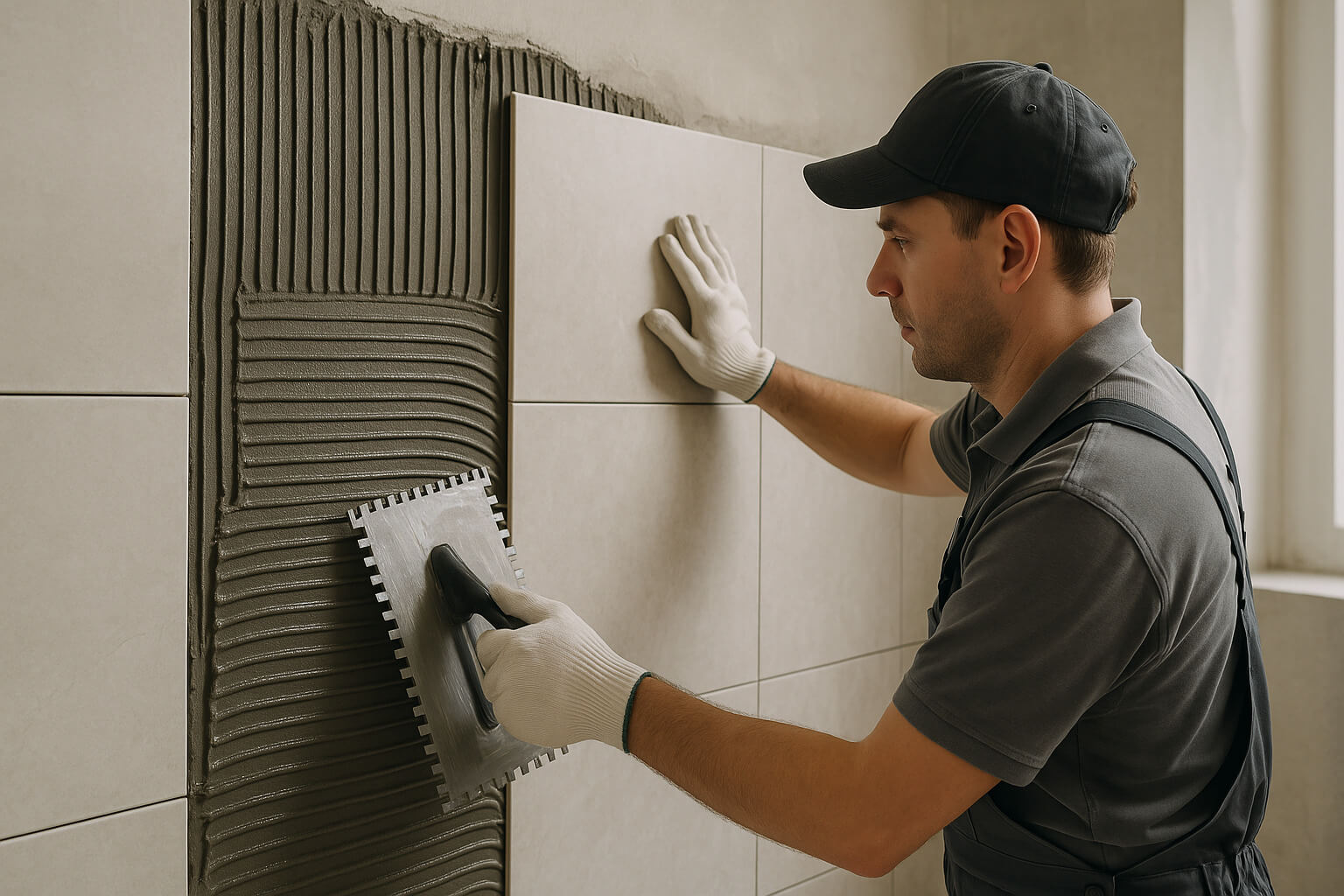
Un installatore professionista sistema piastrelle in ceramica su uno strato adesivo fresco contenente HPMC, evidenziando i vantaggi di un tempo di lavorazione prolungato per un allineamento preciso.
Many installers focus on adhesive strength but overlook setting time control. Let’s examine how HPMC creates the perfect working window for successful tile projects.
Qual è la correlazione tra l'HPMC e il comportamento di presa dell'adesivo per piastrelle?
Hai mai applicato l'adesivo solo per vederlo asciugare prima di terminare la posa delle piastrelle? Questo problema comune rovina l'installazione e spreca materiali costosi.
L'HPMC forma una matrice di gel protettivo all'interno dell'adesivo per piastrelle che regola il movimento dell'acqua, prevenendo l'essiccazione prematura, mantenendo al contempo la corretta viscosità e stabilendo un meccanismo di presa controllato essenziale per le installazioni professionali.
We’ve manufactured HPMC for tile adhesive applications for over a decade, giving us unique insight into its setting control mechanisms. The relationship between HPMC and adhesive setting behavior stems from its fundamental physical properties. When mixed into adhesive formulations, HPMC molecules interact with water through hydrogen bonding, creating a three-dimensional network throughout the mixture.
Questa rete svolge molteplici funzioni cruciali. In primo luogo, riduce significativamente il tasso di evaporazione dell'acqua legando fisicamente le molecole d'acqua all'interno della massa adesiva. In secondo luogo, forma una barriera temporanea che rallenta le reazioni di idratazione del cemento. In terzo luogo, mantiene proprietà reologiche costanti in diverse condizioni ambientali.
I nostri test di laboratorio dimostrano costantemente che la viscosità dell'HPMC è direttamente correlata al tempo di presa. I gradi di HPMC a viscosità più elevata possono prolungare il tempo di lavorazione di 30-45 minuti rispetto alle formulazioni non modificate, consentendo comunque una corretta polimerizzazione in tempi accettabili. Questo equilibrio tra lavorabilità e sviluppo della resistenza finale rende l'HPMC un componente essenziale nei moderni adesivi per piastrelle, secondo le associazioni di settore che monitorano i materiali da costruzione.
The physics behind this process involves controlled water management rather than simply "slowing" the entire reaction. We observe that properly formulated HPMC-modified adhesives maintain their original properties even after repeated troweling and adjustments – a key performance indicator for professional-grade materials.
In che modo l'HPMC ritarda il tempo di presa degli adesivi per piastrelle?
Hai visto un ottimo lotto di adesivo indurirsi nel secchio mentre stavi ancora preparando l'area di installazione? Le reazioni chimiche non aspettano nessuno, a meno che non siano adeguatamente controllate.
L'HPMC ritarda l'indurimento attraverso tre meccanismi principali: crea una rete colloidale protettiva attorno alle particelle di cemento inibendo l'idratazione rapida, mantiene una distribuzione ottimale dell'acqua in tutto lo strato adesivo e forma una pellicola protettiva temporanea che riduce la perdita di umidità nei substrati porosi.
The science behind HPMC’s setting time modification capabilities comes from its unique molecular structure. Our production processes can carefully control substitution levels and molecular weight distributions to achieve specific setting profiles. When integrated into cement-based adhesives, HPMC molecules strategically position themselves between cement particles and water.
I seguenti meccanismi dimostrano come l'HPMC ritarda efficacemente il tempo di presa:
- Hydration control – HPMC temporarily coats cement particles, controlling water access
- Water retention – Hydroxyl groups in the HPMC structure bond with water molecules
- Rheology modification – Changes in flow properties reduce water migration
- Film formation – Creates microscopic barriers against rapid evaporation
- Substrate interaction – Reduces excessive water absorption into porous surfaces
La nostra esperienza produttiva dimostra che diversi gradi di HPMC producono variazioni prevedibili dei tempi di presa. Ad esempio, il nostro HPMC a media viscosità (60.000 mPa·s) in genere prolunga il tempo di lavorabilità di 35-45 minuti nelle formulazioni di cemento standard. Varianti con peso molecolare più elevato possono prolungare ulteriormente questo tempo quando le condizioni ambientali lo richiedono.
Studi di microscopia elettronica condotti nei nostri laboratori rivelano che l'HPMC crea una microstruttura distinta all'interno della matrice adesiva. Questa struttura non solo ritarda la presa iniziale, ma favorisce anche un'idratazione più completa nel tempo, migliorando in definitiva forza di legame a lungo termine come hanno confermato i ricercatori delle riviste specializzate in scienze dei materiali.
Quali vantaggi offre ai piastrellisti un tempo di posa prolungato?
La fretta nell'installazione delle piastrelle porta a disallineamenti, scarsa adesione e, infine, a rotture. La pressione di dover lavorare velocemente compromette la qualità e la reputazione professionale.
Un tempo di presa prolungato offre quattro vantaggi essenziali: tempo di regolazione adeguato per un allineamento preciso delle piastrelle, riduzione degli sprechi dovuti all'essiccazione prematura, migliore copertura grazie al mantenimento di una consistenza ottimale e migliore forza di adesione grazie a un'idratazione più completa del cemento.
From our extensive work with professional tiling contractors across Europe and North America, we’ve documented numerous tangible benefits of properly controlled setting times. Their feedback has directly influenced our HPMC formulation development, helping us create products tailored to real-world installation challenges.
Il tempo di presa prolungato trasforma il processo di installazione offrendo un'ampia finestra di lavoro. Questo periodo di adattamento si rivela particolarmente utile per layout complessi, piastrelle di grande formato e applicazioni verticali in cui la gravità aggrava le difficoltà di allineamento. Gli installatori professionisti che utilizzano i nostri adesivi modificati con HPMC segnalano una riduzione del 30-40% dei problemi di allineamento rispetto alle alternative a presa rapida.
Le implicazioni finanziarie vanno oltre la qualità immediata dell'installazione. La riduzione degli sprechi di materiale rappresenta un significativo vantaggio in termini di costi. I nostri studi sul campo dimostrano che gli appaltatori che utilizzano adesivi HPMC correttamente formulati riscontrano circa 22% in meno di sprechi dovuti a prodotti essiccati prematuramente. Per i grandi progetti commerciali, questo si traduce in risparmi sostanziali nel tempo.
I vantaggi tecnici persistono a lungo dopo l'installazione. Quando il cemento ha un tempo di idratazione sufficiente in condizioni di umidità controllata, le strutture cristalline microscopiche si sviluppano in modo più completo. In pratica, ciò si traduce in una migliore penetrazione dell'adesivo sia nel substrato che nel supporto delle piastrelle, creando legami meccanici più forti. I test dimostrano che tempi di presa ottimizzati si correlano a un miglioramento fino a 15% nelle misurazioni della resistenza finale dell'adesione.
Anche la pianificazione dei progetti beneficia notevolmente della prevedibilità dei tempi di lavoro. I team di installazione possono coordinare meglio le loro attività, soprattutto con squadre numerose che lavorano su aree estese. Il fattore affidabilità riduce lo stress e promuove una lavorazione metodica e di alta qualità, un aspetto ripetutamente sottolineato dai nostri clienti professionisti.
In che modo il dosaggio di HPMC influenza le prestazioni dell'adesivo?
Aggiungere troppo poco o troppo HPMC crea risultati imprevedibili. Trovare il giusto equilibrio è una sfida per molti produttori e porta a un comportamento incoerente del prodotto.
Il rapporto di dosaggio segue uno schema non lineare in cui le concentrazioni comprese tra 0,2-0,5% prolungano significativamente il tempo di presa migliorando al contempo la resistenza alla colatura, ma livelli superiori a 0,7% possono ritardare eccessivamente la polimerizzazione e potenzialmente compromettere la resistenza adesiva finale.
Dosaggio HPMC | Impostazione dell'impatto temporale | Resistenza al cedimento | Prestazioni adesive complessive | Applicazioni consigliate |
---|---|---|---|---|
0.1-0.2% | Estensione minima (10-15 min) | Basso miglioramento | Adatto per applicazioni di base | Piastrelle di piccolo formato, aree non critiche |
0.3-0.5% | Estensione moderata (30-45 min) | Ottimo miglioramento | Equilibrio ottimale per la maggior parte degli usi | Piastrelle di grande formato, pareti, motivi complessi |
0.6-0.7% | Estensione significativa (60+ min) | Molto alto | Solo applicazioni speciali | Climi estremi, piastrelle molto grandi |
>0,8% | Ritardo eccessivo (90+ min) | Potrebbe diventare troppo rigido | Riduzione potenziale della forza | Non generalmente consigliato |
La nostra esperienza nella produzione ci ha permesso di acquisire una conoscenza approfondita dell'ottimizzazione del dosaggio in diverse formulazioni di adesivi. La relazione tra la concentrazione di HPMC e il comportamento di presa segue schemi prevedibili, consentendo ai formulatori di raggiungere specifiche caratteristiche prestazionali. Controlliamo attentamente i parametri di produzione per garantire profili di viscosità costanti, il che influisce direttamente sulla precisione con cui i produttori possono prevedere i tempi di presa.
I meccanismi molecolari alla base degli effetti del dosaggio sono correlati alle interazioni fisiche e chimiche all'interno della matrice adesiva. A concentrazioni inferiori (0,1-0,2%), l'HPMC agisce principalmente come agente di ritenzione idrica con un impatto minimo sulla cinetica di idratazione del cemento. All'aumentare del dosaggio fino all'intervallo ottimale (0,3-0,5%), la rete molecolare diventa sufficientemente densa da modificare sostanzialmente la reologia, creando al contempo efficaci barriere al movimento dell'acqua.
Quando i produttori superano i dosaggi raccomandati, in particolare superiori a 0,7%, emergono diversi potenziali problemi. Un'eccessiva ritenzione idrica può ritardare troppo a lungo le necessarie reazioni di idratazione, compromettendo potenzialmente lo sviluppo della resistenza finale. Inoltre, elevate concentrazioni di HPMC influenzano la lavorabilità in modo diverso, creando a volte adesivi che rimangono inizialmente lavorabili ma che improvvisamente si induriscono, un fenomeno ampiamente documentato dal nostro laboratorio.
We’ve found that temperature sensitivity also correlates with HPMC dosage. Higher concentrations amplify the effects of environmental conditions, making adhesive behavior less predictable across varying jobsite environments. This relationship sottolinea l'importanza di una corretta calibrazione del dosaggio secondo i ricercatori di scienza dei materiali che studiano la chimica delle costruzioni.
Quali fattori esterni influenzano il comportamento dell'HPMC negli adesivi per piastrelle?
Le variabili ambientali nei cantieri variano notevolmente. Sbalzi di temperatura, fluttuazioni di umidità e condizioni del substrato creano sfide imprevedibili per gli installatori.
Temperatura, umidità, porosità del substrato e qualità dell'acqua influiscono notevolmente sulle prestazioni dell'HPMC: temperature più elevate accelerano la presa nonostante la presenza di HPMC, mentre una maggiore umidità e substrati non porosi prolungano i tempi di lavorazione oltre le aspettative standard.
Through our production operations in variable climate regions and extensive field testing programs, we’ve documented precisely how external factors interact with HPMC-modified adhesives. These insights allow us to provide application-specific recommendations based on anticipated installation conditions.
La temperatura rappresenta l'influenza esterna più significativa sul comportamento di presa. I nostri dati tecnici mostrano che per ogni aumento di 10 °C della temperatura ambiente, il tempo di presa diminuisce tipicamente di 15-20 µm³/s, anche con un contenuto ottimale di HPMC. Questa relazione diventa particolarmente critica nelle installazioni in climi caldi, dove un'asciugatura accelerata può compromettere il corretto posizionamento delle piastrelle.
Substrate porosity creates another critical variable affecting HPMC performance. Highly absorbent surfaces like unprimed gypsum board or dry concrete can withdraw moisture from the adhesive layer, counteracting HPMC’s water retention capabilities. Our field measurements indicate that extremely porous substrates can reduce effective working time by up to 40% compared to standard conditions, regardless of HPMC content.
Conversely, non-absorbent substrates like existing tile or certain waterproofing membranes prevent moisture migration entirely. In these scenarios, HPMC’s effect becomes more pronounced, sometimes extending working time beyond what’s desirable for project timelines. Professional installers must adjust their application approach accordingly.
L'umidità relativa influenza l'equilibrio idrico tra l'adesivo e l'aria circostante. Condizioni di elevata umidità (superiore a 70°C di umidità relativa) prolungano in genere il tempo di lavorazione riducendo la velocità di evaporazione. I nostri test mostrano finestre di regolazione di circa 25°C in più in ambienti ad elevata umidità rispetto a condizioni standard (40-60°C di umidità relativa).
Water quality variations, particularly mineral content and pH values, can interact with HPMC’s hydroxyl groups and affect gel formation. Hard water with high calcium content sometimes reduces HPMC effectiveness slightly, though modern HPMC formulations have become increasingly tolerant of these variations through manufacturing improvements our technical team has implemented.
Quali strategie di formulazione chiave migliorano il controllo della presa negli adesivi per piastrelle?
Gli approcci generici alla formulazione degli adesivi producono risultati deludenti. Senza una selezione strategica degli ingredienti e un dosaggio preciso, il tempo di presa rimane imprevedibile.
Strategie di formulazione efficaci includono l'utilizzo di gradi HPMC specializzati con modelli di sostituzione mirati, il bilanciamento di additivi complementari come eteri di amido o polimeri sintetici, l'ottimizzazione dei tipi di cemento e delle dimensioni delle particelle e l'incorporazione di acceleratori di presa per controbilanciare il tempo di apertura prolungato.
Nel nostro stabilimento produttivo, produciamo diverse qualità di HPMC specificamente progettate per applicazioni edilizie. Il fattore di formulazione più critico riguarda la selezione del peso molecolare e del modello di sostituzione appropriati. I nostri adesivi per piastrelle ad alte prestazioni presentano rapporti idrossipropilici/metossilici accuratamente bilanciati che ottimizzano la ritenzione idrica senza eccessiva appiccicosità o ritardo nella polimerizzazione finale.
Le formulazioni di successo raramente si basano solo sull'HPMC. La relazione sinergica tra HPMC e altri additivi garantisce prestazioni più stabili in condizioni variabili. Il nostro team tecnico consiglia questi approcci comprovati:
- Combinare HPMC con polveri polimeriche ridisperdibili (RPP) per migliorare la flessibilità mantenendo il controllo della presa
- Balance cement/aggregate ratios to complement HPMC’s water retention properties
- Selezionare i tipi di cemento appropriati: il tipo Portland I offre una presa più prevedibile con HPMC rispetto alle varietà a indurimento rapido
- Incorporare piccole quantità di acceleratori di impostazione per compensare ritardi eccessivi quando necessario
- Considerare l'aggiunta di tensioattivi per migliorare la dissoluzione e la distribuzione dell'HPMC in tutta la miscela
The cement component itself significantly influences how HPMC functions within the formulation. Finer cement particles with higher surface areas interact more extensively with HPMC molecules, sometimes requiring dosage adjustments. Through our R&D program, we’ve determined that medium-ground cements typically provide the most predictable performance with standard HPMC grades.
Gli approcci di formulazione avanzati a volte includono miglioratori della stabilità termica che riducono la sensibilità alla temperatura della rete HPMC, secondo una ricerca condotta da associazioni di chimica edile. Questi additivi specializzati contribuiscono a mantenere profili di presa costanti in intervalli di temperatura più ampi, un vantaggio significativo per i prodotti venduti in regioni con climi variabili.
L'ultima considerazione riguarda il bilanciamento dei tempi di lavorazione prolungati con requisiti di presa finale ragionevoli. Mentre i periodi di adattamento prolungati favoriscono gli installatori, ritardi eccessivi prima della movimentazione o della stuccatura creano problemi nelle tempistiche del progetto. Le formulazioni moderne raggiungono questo equilibrio attraverso meccanismi di presa attentamente sequenziati: l'HPMC controlla la presa iniziale, mentre gli additivi complementari garantiscono una presa finale tempestiva.
Domande frequenti
Qual è il ruolo dell'HPMC negli adesivi per piastrelle?
L'HPMC è un additivo multifunzionale fondamentale negli adesivi per piastrelle, in quanto trattiene principalmente l'acqua per prolungare i tempi di lavorabilità e, al contempo, migliora la consistenza dell'adesivo e la resistenza alla colatura. I suoi gruppi ossidrilici formano legami a idrogeno con le molecole d'acqua, creando una rete di gel protettivo che rallenta l'evaporazione e controlla la velocità di idratazione del cemento. L'HPMC migliora inoltre la spalmabilità dell'adesivo, rendendo l'applicazione più efficiente e garantendo il tempo aperto necessario per un posizionamento e una regolazione precisi delle piastrelle.
Perché la colla per piastrelle non ha fatto presa?
Diversi fattori possono impedire una corretta presa: un'eccessiva concentrazione di HPMC (superiore a 0,7%), temperature estremamente basse (inferiori a 10°C/50°F), ambienti ad alta umidità o substrati non assorbenti che impediscono la migrazione dell'umidità. Verificare che l'adesivo contenga un contenuto di cemento adeguato, poiché alcune formulazioni economiche potrebbero non contenere sufficienti materiali reattivi. Più comunemente, diluire eccessivamente l'adesivo con troppa acqua compromette l'equilibrio chimico necessario per una corretta presa. In condizioni di umidità elevata, provare ad applicare uno strato più sottile o a utilizzare un deumidificatore.
Come posso accelerare il tempo di asciugatura dell'adesivo per piastrelle?
To accelerate setting time while maintaining adhesive quality, increase ventilation in the work area, maintain moderate warmth (21-25°C/70-77°F), and use fans to circulate air without directly blowing on the adhesive surface. Select a lower-viscosity HPMC-modified adhesive specifically formulated for faster setting. Avoid excessive water during mixing, as this significantly extends drying time. For critical timeline projects, consider specialized rapid-set formulations containing setting accelerators like calcium formate that balance HPMC’s water retention while promoting faster strength development.
In che modo la temperatura influisce sull'HPMC?
Temperature significantly influences HPMC behavior in tile adhesives through multiple mechanisms. At higher temperatures (above 30°C/86°F), HPMC’s water retention capacity decreases as thermal energy weakens hydrogen bonding, resulting in faster setting despite HPMC presence. Conversely, colder conditions (below 15°C/59°F) strengthen hydrogen bonds while slowing cement hydration reactions, extending setting time substantially. Temperature also affects HPMC dissolution during mixing—cold water slows gel formation while warm water accelerates it. Modern HPMC grades maintain better thermal stability, but temperature remains the most influential external factor affecting their performance in adhesive applications.
Conclusione
HPMC trasforma i comuni adesivi per piastrelle in materiali di qualità professionale, garantendo il controllo essenziale del tempo di presa che garantisce installazioni di successo. Grazie ai suoi esclusivi meccanismi di ritenzione idrica, HPMC crea la finestra di lavoro fondamentale necessaria per il corretto posizionamento, allineamento e regolazione delle piastrelle.
We’ve seen firsthand how proper HPMC selection dramatically improves adhesive performance across diverse installation challenges. The right viscosity grade and dosage deliver predictable setting behavior while enhancing adhesive properties from application through final curing. This balance of extended working time without excessive delays makes HPMC indispensable in quality tile adhesive formulations.
For tile adhesive manufacturers seeking consistent setting performance and exceptional water retention, contact our technical team at Morton for specialized HPMC grades engineered specifically for construction applications. Our production expertise ensures you’ll receive precisely the performance characteristics your formulations require.