Hydroxypropyl Methyl Cellulose (HPMC) is a cellulose derivative that has become an essential raw material across various industries, including pharmaceuticals, food, cosmetics, and construction. This versatile polymer is primarily known for its water solubility, gel-forming properties, and ability to adjust viscosity in a wide range of applications. In this article, we will dive into the key raw materials that go into the production of HPMC, how it is made, and why it’s so crucial in today’s industrial landscape.
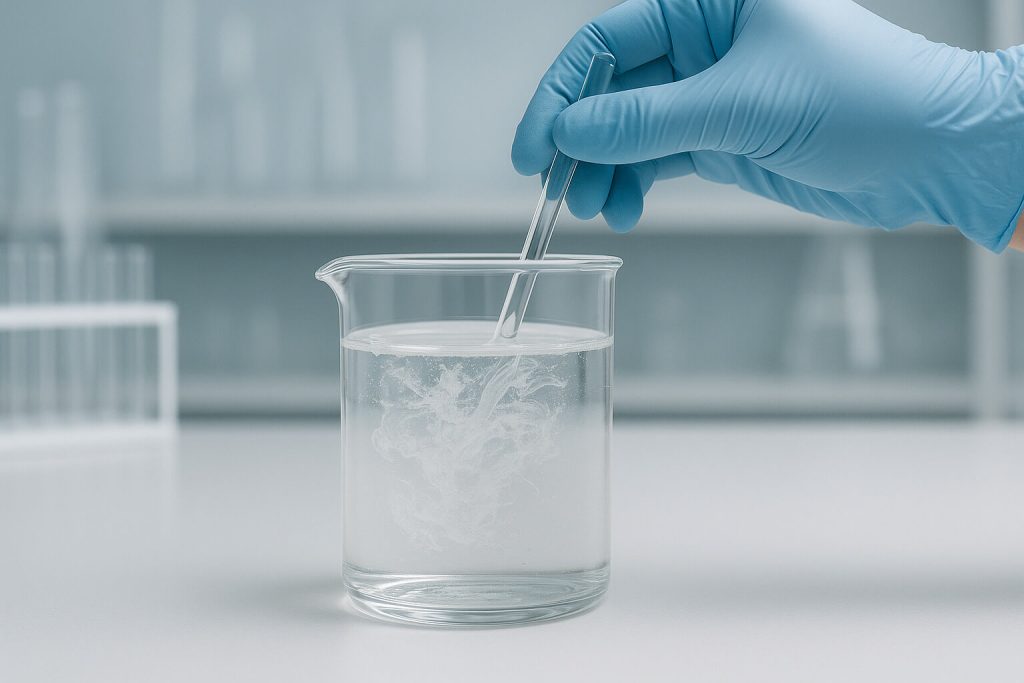
1. What is Hydroxypropyl Methyl Cellulose (HPMC)?
Hydroxypropyl Methyl Cellulose (HPMC) is a chemically modified form of cellulose, a natural polymer derived from plant fibers. The modification involves introducing hydroxypropyl and methyl groups into the cellulose structure. This alteration significantly enhances the solubility of the polymer in water and allows it to function as a versatile ingredient in various applications, ranging from thickening agents in food to binders in pharmaceuticals.
Why is this important? Well, the modification of cellulose into HPMC gives it unique properties, such as improved solubility in both hot and cold water, increased viscosity, and a gel-forming ability. These properties make it ideal for use in diverse sectors. For instance, in the pharmaceutical industry, HPMC is used in tablet formulations to control the release of active ingredients. In construction, it enhances the workability and consistency of cement-based products like mortars and adhesives.
The use of HPMC as a raw material is a game-changer for industries that rely on stability, solubility, and controlled release in their products. Understanding the key components involved in its production is crucial for making informed decisions about its use in specific applications.
Proprietà | Function in Industry | Examples of Use |
---|---|---|
Solubilità | Enhances water solubility | Pharmaceuticals, Food |
Gel-forming Ability | Forms stable gels | Food, Pharmaceuticals |
Viscosità | Adjusts consistency and texture | Cosmetics, Construction |
2. How is Hydroxypropyl Methyl Cellulose (HPMC) Made?
The production of HPMC involves several stages of chemical modification, starting with cellulose as the base material. Cellulose, typically derived from wood or cotton fibers, undergoes a chemical process to introduce hydroxypropyl and methyl groups. These groups are added through a reaction with propylene oxide and methyl chloride, respectively.
Why does this matter? The introduction of these groups into the cellulose structure alters the polymer’s characteristics significantly. The hydroxypropyl group increases solubility in water, while the methyl group helps improve the polymer’s ability to thicken liquids and form gels. The modification process allows for precise control over the polymer’s properties, including viscosity and solubility, making it customizable for specific applications.
The production process typically involves dissolving cellulose in a solvent, followed by adding the modifying chemicals in controlled conditions. After the reaction, the resulting HPMC is purified, dried, and then processed into various grades, each suited for different applications based on the desired viscosity and solubility.
Understanding how HPMC is made helps manufacturers and researchers make informed decisions about the right grades for specific applications. By controlling the degree of substitution and modification, they can optimize the material’s properties for maximum efficiency.
Stage in Production | Process Description | Outcome |
---|---|---|
Cellulose Isolation | Extraction from natural fibers | Provides the base for modification |
Chemical Modification | Reaction with propylene oxide and methyl chloride | Changes chemical structure, improves solubility |
Purification & Drying | Removal of impurities, drying | High-quality HPMC, ready for use |
3. What Are the Key Raw Materials for HPMC Production?
The primary raw materials used to produce HPMC are cellulose, hydroxypropyl groups, and methyl groups. Let’s break down each component.
- Cellulose: This is the backbone of HPMC. It’s typically derived from wood pulp, cotton linters, or other plant-based sources. Cellulose is a naturally occurring polymer that is insoluble in water, making it an ideal candidate for modification to produce water-soluble derivatives like HPMC.
- Gruppi idrossipropilici: These are introduced through a chemical reaction with propylene oxide. Hydroxypropyl groups increase the water solubility of cellulose and are responsible for HPMC’s ability to dissolve in both cold and hot water. This makes HPMC more versatile than other cellulose derivatives.
- Gruppi metilici: Methyl groups are added through a reaction with methyl chloride. This modification helps HPMC perform well as a thickener and stabilizer. The methyl groups also enhance the material’s gel-forming ability, making it valuable in food and pharmaceutical formulations that require controlled release.
These raw materials are carefully selected and processed to ensure that HPMC meets the specific requirements of different industries, from pharmaceuticals to construction materials.
Materia prima | Function in HPMC Production | Fonte |
---|---|---|
Cellulose | Base polymer, provides structure | Wood pulp, cotton linters |
Hydroxypropyl Group | Enhances water solubility | Ossido di propilene |
Methyl Group | Improves gel-forming and thickening ability | Cloruro di metile |
4. What Role Does Cellulose Play in HPMC Production?
Cellulose plays a crucial role in the production of HPMC, acting as the foundational material upon which all modifications are based. Pure cellulose, although a polymer, is insoluble in water and lacks the gel-forming properties needed for many industrial applications. By introducing chemical modifications, cellulose is transformed into a material that is not only soluble in water but also able to thicken and form gels.
Cellulose used in HPMC production typically comes from plant sources such as wood pulp or cotton. It undergoes a series of chemical treatments to make it more reactive. The first step is to isolate and purify cellulose, removing any unwanted components such as lignin or hemicellulose. After purification, cellulose is subjected to chemical reactions that introduce hydroxypropyl and methyl groups, enhancing its functionality.
What makes cellulose such an important raw material? Its natural abundance, sustainability, and ability to be chemically modified make it an ideal starting point for creating versatile derivatives like HPMC. The modification process enhances its properties, enabling it to perform a wide range of functions across various industries.
Palcoscenico | Process Description | Importance in Production |
---|---|---|
Cellulose Isolation | Extraction from plant fibers | Provides the base polymer |
Purificazione | Removal of impurities | Ensures high-quality HPMC |
Chemical Treatment | Modification with propylene oxide and methyl chloride | Enhances solubility, viscosity, and gel formation |
5. How Are Hydroxypropyl and Methyl Groups Introduced to Cellulose?
The introduction of hydroxypropyl and methyl groups into cellulose is a key step in creating HPMC, and it requires precise chemical reactions. These modifications are what transform cellulose from an insoluble substance into a water-soluble polymer with improved functionality.
The process begins with cellulose being dissolved in a solvent, typically sodium hydroxide or an alkali solution, which helps to break down the crystalline structure of cellulose. Once the cellulose is in a dissolved state, propylene oxide is added to introduce the hydroxypropyl group. This group significantly enhances the solubility of cellulose in both cold and hot water, making it more versatile for various applications.
Next, methyl chloride is introduced to attach the methyl group to the cellulose structure. This modification not only helps with water solubility but also increases the gel-forming ability of the polymer. By controlling the amounts of hydroxypropyl and methyl groups added, manufacturers can tailor the properties of HPMC for specific uses, such as in pharmaceuticals, food, or construction products.
These chemical modifications are essential because they enable cellulose to perform a wide range of functions that it cannot achieve in its natural state, like improving the texture, consistency, and performance of products in diverse industries.
Chemical Group | Process | Effect on HPMC |
---|---|---|
Hydroxypropyl Group | Reaction with propylene oxide | Increases water solubility, viscosity |
Methyl Group | Reaction with methyl chloride | Enhances gel formation, thickening ability |
6. What Are the Properties of HPMC That Make It So Useful?
HPMC offers a unique set of properties that make it extremely useful across many industries. Its ability to dissolve in water and form stable gels is key to its widespread use. These properties are particularly valuable in applications requiring thickening, emulsification, and controlled release.
- Solubilità in acqua: HPMC is soluble in both cold and hot water, which allows it to be used in a wide range of formulations, from pharmaceutical tablets to food products and cosmetic creams.
- Viscosità: HPMC is often used to adjust the viscosity of a product, making it thicker or more stable. Its ability to form a gel when mixed with water is an essential property, especially in the pharmaceutical industry where it is used for controlled-release drug formulations.
- Gel-forming Ability: HPMC’s ability to form stable gels is particularly important in the food and cosmetics industries, where it is used to improve texture and stability.
These properties make HPMC an essential material in a wide variety of applications, helping to ensure the quality and consistency of the final product. Whether in pharmaceuticals or construction, the versatility of HPMC helps meet the specific needs of each industry.
Proprietà | Functionality | Application Areas |
---|---|---|
Solubilità in acqua | Enhances solubility in cold and hot water | Pharmaceuticals, Food, Cosmetics |
Viscosità | Adjusts product thickness and consistency | Construction, Food, Pharmaceuticals |
Gel-forming Ability | Forms stable gels for texture and stability | Food, Cosmetics, Pharmaceuticals |
7. What Industries Use HPMC Raw Material and Why?
HPMC is used in a broad range of industries due to its versatile properties. Let’s take a closer look at the key sectors that rely on HPMC
.
- Prodotti farmaceutici: HPMC is essential in the pharmaceutical industry for its ability to control the release of drugs in tablet formulations. Its solubility and gel-forming ability make it an excellent choice for controlled-release systems.
- Costruzione: In construction, HPMC is used in mortars, cement, and tile adhesives. Its ability to improve water retention and workability makes it invaluable for these products, ensuring better consistency and performance.
- Cibo: HPMC is used in food processing as a stabilizer and thickener. It helps maintain texture and prevents separation in products like sauces, dressings, and ice cream.
- Cosmetici: In cosmetics, HPMC is used to thicken lotions, creams, and gels, providing the necessary consistency for a smooth, luxurious feel.
The diverse applications of HPMC across these industries highlight its importance as a raw material that enhances product quality and performance.
Industria | Use of HPMC | Benefici |
---|---|---|
Prodotti farmaceutici | Formulazioni a rilascio controllato | Ensures consistent drug release |
Costruzione | Malte, adesivi | Improves consistency and workability |
Cibo | Stabilizer, thickener | Maintains texture and stability |
Cosmetici | Thickener, emulsifier | Enhances product texture and consistency |
8. What Are the Environmental Considerations of Using HPMC?
One of the key advantages of using HPMC is its environmental sustainability. HPMC is derived from cellulose, which is a renewable resource. The production of cellulose itself has a lower environmental impact compared to synthetic polymers. Moreover, HPMC is biodegradable, making it a more eco-friendly option compared to many other chemical additives.
However, the production process for HPMC does involve chemical modifications that require careful management to minimize any potential environmental impact. Many manufacturers are now adopting more sustainable practices, such as using non-toxic solvents and reducing energy consumption during production.
As sustainability becomes a more significant focus for industries, the use of HPMC aligns with the growing trend toward green chemistry and environmentally responsible manufacturing.
Impatto ambientale | HPMC | Cellulose |
---|---|---|
Sustainability | Biodegradabile, rinnovabile | Naturally derived from plants |
Manufacturing Impact | Chemical modification required | Requires minimal processing |
9. How is HPMC Processed and Manufactured?
The manufacturing process of HPMC involves several stages to ensure the polymer’s solubility, viscosity, and gel-forming ability meet industry specifications. The process begins with cellulose extraction from plant sources. Once purified, the cellulose undergoes chemical modification, where propylene oxide and methyl chloride are added to introduce the hydroxypropyl and methyl groups.
After the modification, the material is purified to remove any byproducts and solvents. The resulting HPMC is then dried, ground, and packaged in various grades depending on the intended application. Different grades of HPMC have varying degrees of substitution, which affect their viscosity and solubility.
Manufacturers closely monitor the production process to ensure consistency and quality control. This is critical for ensuring that HPMC performs as expected in each specific application.
Fase di produzione | Process Description | Key Objective |
---|---|---|
Cellulose Extraction | Purification of cellulose | Provides base material |
Chemical Modification | Reaction with propylene oxide and methyl chloride | Alters solubility and viscosity |
Purification & Drying | Removal of solvents, drying | Ensures high-quality product |
10. What Are the Benefits of Using HPMC in Various Applications?
The use of HPMC in various applications brings numerous benefits. Its ability to adjust viscosity, form stable gels, and improve product consistency makes it invaluable in industries ranging from pharmaceuticals to food and construction.
For pharmaceuticals, HPMC provides excellent control over drug release, ensuring that active ingredients are delivered at the desired rate. In construction, its ability to improve water retention and workability enhances the performance of products like adhesives and mortars. In food, HPMC is used to stabilize emulsions and maintain texture, while in cosmetics, it helps provide the right consistency for lotions and creams.
Overall, the flexibility of HPMC ensures that it can be used to enhance the performance and quality of products across a broad range of industries.
Industria | Vantaggio dell'HPMC | Application Example |
---|---|---|
Prodotti farmaceutici | Controlled-release, stability | Tablet formulations, suspensions |
Costruzione | Workability, adhesion | Mortars, tile adhesives |
Cibo | Texture, stabilization | Sauces, dressings, ice cream |
Cosmetici | Consistency, texture | Creams, lotions, shampoos |
Sezione FAQ
Q1: What is Hydroxypropyl Methyl Cellulose (HPMC)?
Answer: Hydroxypropyl Methyl Cellulose (HPMC) is a water-soluble cellulose derivative used in various industries for its thickening, gel-forming, and stabilizing properties.
Q2: How is HPMC made?
Answer: HPMC is made by chemically modifying cellulose with hydroxypropyl and methyl groups, which enhances its water solubility and gel-forming capabilities.
Q3: What are the raw materials for HPMC production?
Answer: The primary raw materials for HPMC production are cellulose, hydroxypropyl groups (from propylene oxide), and methyl groups (from methyl chloride).
Q4: What role does cellulose play in HPMC production?
Answer: Cellulose serves as the base material for HPMC. It undergoes chemical modification to increase its solubility and improve its ability to form gels.
Q5: Why is HPMC used in the pharmaceutical industry?
Answer: HPMC is used in pharmaceuticals for controlled-release drug formulations, where it ensures that active ingredients are released slowly over time for extended therapeutic effects.