Hydroxypropyl Methylcellulose (HPMC) is a widely used cellulose derivative that plays a critical role in industries ranging from pharmaceuticals to construction. Understanding the manufacturing process of HPMC is essential for professionals seeking to optimize its use in their products. This article will explore how HPMC is produced, from its raw materials to the chemical modifications that make it so versatile. By the end of this article, you’ll have a comprehensive understanding of the production process and its importance across various industries.
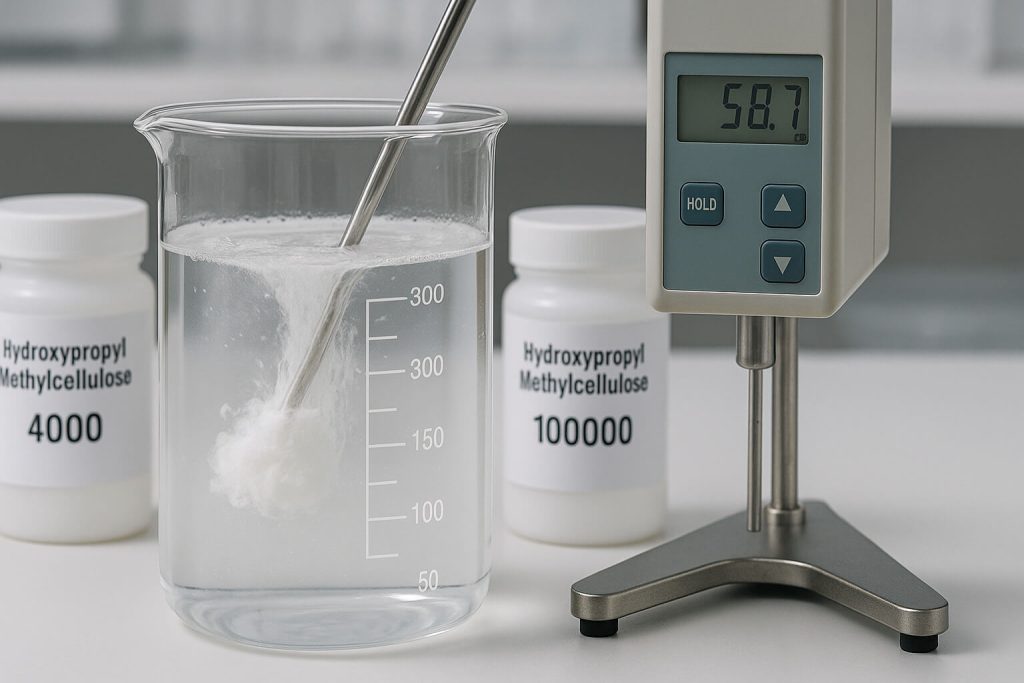
1. What is Hydroxypropyl Methylcellulose (HPMC)?
Hydroxypropyl Methylcellulose (HPMC) is a non-ionic cellulose ether that is water-soluble and forms a gel-like consistency when dissolved in water. It is primarily used as a binder, thickener, emulsifier, and stabilizer in various industries such as pharmaceuticals, food, construction, and cosmetics.
Why should this matter to you? The unique properties of HPMC, such as its ability to modify viscosity, retain water, and create smooth, uniform formulations, make it an essential ingredient in many products. In pharmaceuticals, for example, HPMC is used in tablet coatings and controlled-release drug formulations. In construction, it enhances the workability of dry mortars and adhesives.
HPMC is derived from cellulose, a natural polymer found in plant cell walls, making it an eco-friendly option. The modification of cellulose with hydroxypropyl and methyl groups allows for the customization of HPMC’s properties, which is key to its wide array of applications.
Таблица: Свойства HPMC
Свойство | Описание |
---|---|
Chemical Composition | Modified cellulose with hydroxypropyl and methyl groups |
Растворимость | Water-soluble, forms gel in water |
Вязкость | Can be adjusted based on application |
Распространенные приложения | Фармацевтика, продукты питания, строительство, косметика |
2. How is HPMC Chemically Produced?
The production of Hydroxypropyl Methylcellulose (HPMC) begins with cellulose, a natural polymer that is extracted from wood, cotton, or other plant materials. The cellulose is then subjected to a series of chemical reactions that introduce hydroxypropyl and methyl groups.
Here’s how it works: The first step in the HPMC production process involves the dissolution of cellulose in a strong base like sodium hydroxide. This step helps to break down the cellulose fibers into a more manageable form. After the cellulose is dissolved, it reacts with propylene oxide to introduce the hydroxypropyl group and methyl chloride to introduce the methyl group. These modifications make the cellulose soluble in water and impart other useful properties such as thickening and emulsification.
Once these reactions have taken place, the cellulose derivative is neutralized and washed to remove any remaining chemicals. The resulting product, HPMC, can then be dried and ground into a fine powder, ready for use in various applications.
Why is this important? The chemical process used in HPMC production directly impacts its properties, such as solubility, viscosity, and water retention. Understanding these chemical modifications helps manufacturers optimize the material for different applications.
Table: Chemical Production Process of HPMC
Шаг | Описание |
---|---|
Cellulose Preparation | Cellulose is dissolved in sodium hydroxide |
Reaction with Chemicals | Propylene oxide and methyl chloride react with cellulose |
Степень замещения | Adjusted by varying the amount of chemicals used |
Final Product | HPMC with customized properties for different applications |
3. What Are the Raw Materials Used in HPMC Production?
The raw materials used in the production of HPMC play a crucial role in determining its final properties. The primary ingredient is cellulose, but other chemicals are necessary to modify the cellulose structure and give HPMC its unique characteristics.
Let’s break it down: The source of cellulose can vary, but it is most commonly derived from plant-based materials such as wood pulp, cotton, or other agricultural by-products. The cellulose must be of high quality to ensure that the final HPMC product is consistent and performs well in its applications.
To modify the cellulose, chemicals like propylene oxide and methyl chloride are used. These reagents introduce the hydroxypropyl and methyl groups, which enhance the solubility, viscosity, and water retention properties of the cellulose. The quality and purity of these chemicals are critical because any impurities can affect the final properties of HPMC.
So why is this relevant? The quality and source of raw materials directly influence the final properties of HPMC, which in turn affects its performance in various applications. Manufacturers need to carefully select and control the quality of these materials to ensure consistent product performance.
Table: Raw Materials Used in HPMC Production
Material | Role in Production |
---|---|
Cellulose | Primary raw material, sourced from plants |
Propylene Oxide | Introduces the hydroxypropyl group |
Methyl Chloride | Introduces the methyl group |
4. What is the Role of Hydroxypropyl and Methyl Groups in HPMC Production?
The hydroxypropyl and methyl groups are the key to HPMC’s unique properties. These functional groups are introduced into the cellulose molecule during the chemical modification process and drastically alter the physical properties of the polymer.
Here’s why this matters: The hydroxypropyl group, which is hydrophilic, makes HPMC more soluble in water. This increases the polymer’s ability to form gels and improves its water retention properties. The methyl group, on the other hand, is hydrophobic and helps to stabilize the HPMC structure, making it less soluble in organic solvents and ensuring that it remains stable in a variety of applications.
These modifications allow HPMC to be used in a wide range of industries. For instance, in pharmaceuticals, HPMC’s gel-forming ability is key for controlled drug release. In food production, the water retention properties help improve texture and consistency in products like sauces and dressings.
Why should you care? The introduction of these groups is what makes HPMC so versatile. The balance between hydrophilic and hydrophobic properties enables it to perform well in diverse applications.
Table: Role of Hydroxypropyl and Methyl Groups in HPMC
Group | Effect on HPMC Properties |
---|---|
Hydroxypropyl Group | Increases solubility, water retention |
Methyl Group | Stabilizes the structure, reduces solubility in organic solvents |
5. How Does the Degree of Substitution Affect HPMC Production?
The degree of substitution (DS) is a crucial factor in the production of HPMC. It refers to the number of hydroxypropyl and methyl groups attached to each cellulose unit. This parameter directly affects the solubility, viscosity, and overall performance of HPMC.
Here’s the deal: A higher degree of substitution means more hydroxypropyl and methyl groups are attached to the cellulose molecule, which typically results in higher solubility and viscosity. For applications where thicker solutions are required, such as in pharmaceuticals and food, a higher DS is preferred. Conversely, a lower degree of substitution may be suitable for applications where a lower viscosity is needed, such as in some cosmetic formulations.
The DS is carefully controlled during the production process by adjusting the amounts of propylene oxide and methyl chloride used. Manufacturers can thus produce different grades of HPMC with varying properties based on the required application.
Why is this important? The ability to control the degree of substitution allows manufacturers to tailor HPMC’s properties for specific uses, ensuring optimal performance in each application.
Table: Effect of Degree of Substitution on HPMC Properties
Степень замещения | Вязкость | Растворимость | Приложение |
---|---|---|---|
Низкий | Низкий | Умеренный | Cosmetics, mild formulations |
Середина | Середина | Высокий | Food products, industrial applications |
Высокий | Высокий | Очень высокий | Pharmaceuticals, controlled-release formulations |
6. What Are the Key Steps in the HPMC Manufacturing Process?
The production of HPMC involves several key steps, each of which plays a crucial role in determining the final properties of the material. These steps are carefully controlled to ensure that the HPMC meets the specifications required for different applications.
Here’s a breakdown of the process: First, cellulose is prepared by dissolving it in a strong base. Once the cellulose is dissolved, it reacts with propylene oxide and methyl chloride in a controlled environment to introduce the hydroxypropyl and methyl groups. After the reaction, the mixture is neutralized, washed, and dried to remove any impurities.
The final step involves grinding the dried product into a fine powder, which is then tested for its solubility, viscosity, and other key properties. The product is then packaged and ready for use in various industries.
Why is this process important? The steps involved in HPMC production are carefully designed to ensure that the final product has the desired characteristics for specific applications. By understanding these steps, manufacturers can optimize the production process to achieve the best results.
Table: HPMC Manufacturing Process Overview
Шаг | Описание |
---|---|
Cellulose Preparation | Cellulose is dissolved in sodium hydroxide |
Reaction with Chemicals | Propylene oxide and methyl chloride react with cellulose |
Neutralization and Washing | Непрореагировавшие химикаты удаляются. |
Drying and Grinding | The product is dried and ground into a fine powder |
7. How Are HPMC Properties Controlled During Production?
The properties of HPMC are controlled through several factors during the manufacturing process. Key variables like the degree of substitution, the ratio of propylene oxide to methyl chloride, and the reaction conditions all play a role in determining the final product’s characteristics.
So, how is this achieved? The viscosity and solubility of HPMC can be fine-tuned by adjusting the degree of substitution. Additionally, the reaction conditions, such as temperature and pressure, are closely monitored to ensure the desired chemical modifications are achieved. By controlling these factors, manufacturers can produce HPMC with specific properties tailored to meet the needs of different industries.
Why should this matter? Understanding how HPMC’s properties are controlled allows businesses to select the right grade for their applications, ensuring that the material performs optimally.
Table: Factors Affecting HPMC Properties
Фактор | Impact on Properties |
---|---|
Степень замещения | Affects viscosity and solubility |
Reaction Conditions | Temperature and pressure affect chemical structure |
Chemical Ratio | The ratio of propylene oxide to methyl chloride influences final product |
8. What Are the Different Types of HPMC Produced?
HPMC can be customized to meet the needs of different industries. Depending on the degree of substitution and solubility, HPMC comes in various grades suited for specific applications.
What does this mean for you? In pharmaceuticals, high-viscosity HPMC is used for controlled-release formulations. In the food industry, lower-viscosity grades are used to improve the texture of sauces and dressings. Similarly, in construction, HPMC with the right viscosity helps improve the workability of dry mixes and adhesives.
Why is this important? Customizing the properties of HPMC allows manufacturers to achieve optimal performance in a variety of applications, ensuring that the material meets industry-specific requirements.
Table: Types of HPMC and Their Applications
Оценка | Вязкость | Приложение |
---|---|---|
Низкая вязкость | Низкий | Food products, cosmetics |
Средняя вязкость | Середина | Pharmaceuticals, industrial formulations |
Высокая вязкость | Высокий | Construction materials, controlled-release formulations |
9. What Are the Applications of HPMC in Various Industries?
HPMC is widely used across a range of industries, each with its specific requirements. In pharmaceuticals, it is used as a binder in tablet formulations and as a controlled-release agent. In the food industry, HPMC enhances the texture and consistency of products like sauces, dressings, and baked goods.
Let’s explore further: In cosmetics, HPMC serves as a stabilizer in creams and lotions, while in construction, it improves the workability of dry mortars and adhesives. Its versatility makes it a go-to material in many different industries.
Why does this matter for you? Understanding the applications of HPMC in these industries helps businesses make informed decisions about how to incorporate it into their products and optimize performance.
Table: HPMC Applications by Industry
Промышленность | Приложение |
---|---|
Фармацевтика | Tablet coatings, controlled drug release |
Еда | Texture and emulsification in food products |
Косметика | Stabilizer in creams and lotions |
Строительство | Water retention in dry mixes and adhesives |
10. What Are the Environmental Considerations in HPMC Production?
Sustainability is becoming increasingly important in manufacturing, and the production of HPMC is no exception. The raw material, cellulose, is a renewable resource, making HPMC an eco-friendly option. However, the chemicals used in the production process, such as propylene oxide and methyl chloride, can have environmental impacts if not handled properly.
What’s the bottom line? Efforts are being made to reduce the environmental footprint of HPMC production by exploring greener production methods, such as using more sustainable chemicals and improving production efficiency.
Why should this matter? Understanding the environmental impact of HPMC production can help businesses make more sustainable choices and meet growing consumer demand for eco-friendly products.
Table: Environmental Impact of HPMC Production
Фактор | Impact |
---|---|
Raw Material (Cellulose) | Renewable and biodegradable |
Chemicals Used | Potential environmental concerns with propylene oxide and methyl chloride |
Sustainable Practices | Efforts to reduce chemical waste and improve energy efficiency |
Заключение
In conclusion, the production of Hydroxypropyl Methylcellulose (HPMC) is a complex process that involves the chemical modification of cellulose to achieve specific properties. By understanding the production process and its impact on HPMC’s performance, businesses can better optimize its use across a range of industries, from pharmaceuticals to construction. With continued advancements in sustainable production practices, HPMC will remain a valuable material for years to come.
Раздел часто задаваемых вопросов
В1: Что такое ГПМЦ?
HPMC (Hydroxypropyl Methylcellulose) is a cellulose derivative used in pharmaceuticals, food, construction, and cosmetics due to its thickening, stabilizing, and emulsifying properties.
В2: How is HPMC produced?
HPMC is produced by chemically modifying cellulose with propylene oxide and methyl chloride to introduce hydroxypropyl and methyl groups, which alter the polymer’s solubility and viscosity.
В3: What are the raw materials used in HPMC production?
The main raw material for HPMC production is cellulose, derived from plant sources like wood and cotton. Other chemicals like propylene oxide and methyl chloride are also used to modify the cellulose structure.
В4: How does the degree of substitution affect HPMC?
The degree of substitution refers to the number of hydroxypropyl and methyl groups attached to the cellulose. A higher degree of substitution leads to higher solubility and viscosity, making the product more suitable for specific applications.
В5: What are the main applications of HPMC?
HPMC is used in a wide range of industries, including pharmaceuticals for controlled drug release, in food to improve texture and consistency, and in construction for improving the workability of dry mixes and adhesives.