When working with Hydroxypropyl Methyl Cellulose (HPMC), ensuring it dissolves correctly is key to obtaining the desired consistency and functionality for various industrial applications. Whether you’re in construction, pharmaceuticals, or food industries, understanding the best practices for dissolving HPMC is crucial. This article dives into the technicalities of HPMC dissolution, addressing common challenges, methods, and best practices to achieve optimal results. We’ll cover the science behind it, offer practical solutions, and guide you through the process for consistent, high-quality outcomes.
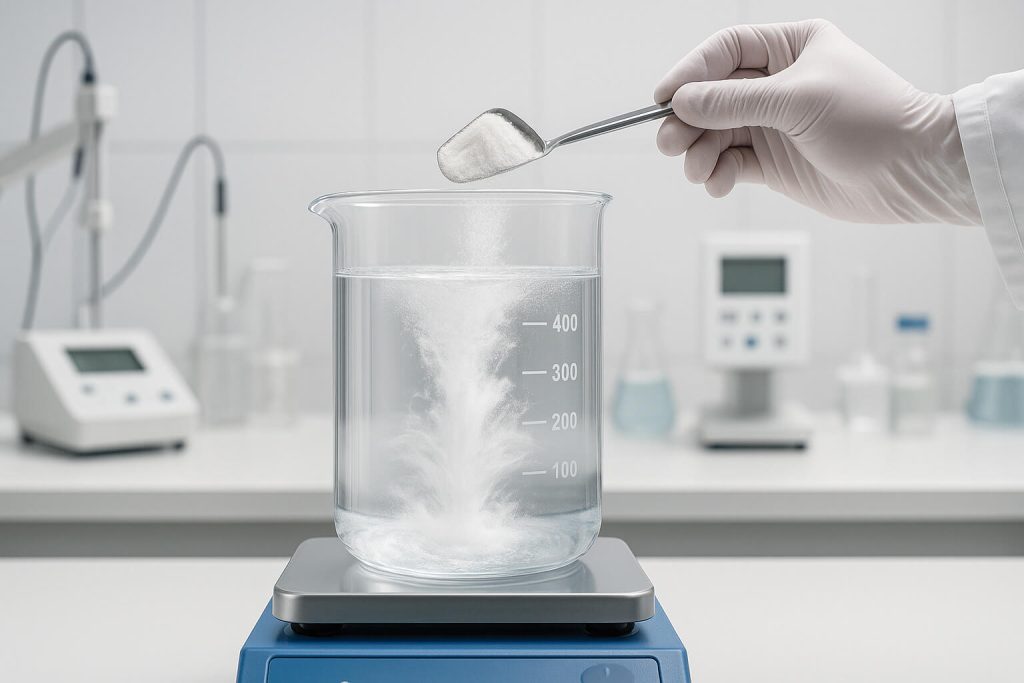
1. What is HPMC (Hydroxypropyl Methyl Cellulose)?
Hydroxypropyl Methyl Cellulose, commonly referred to as HPMC, is a water-soluble, plant-derived polymer. It is widely used in the construction, pharmaceutical, and food industries for its excellent binding, thickening, and stabilizing properties. In construction, it enhances the workability of mortars and adhesives. In pharmaceuticals, it is used as a binder in tablets and capsules. In the food industry, it acts as an emulsifier and stabilizer in various products like ice cream and sauces.
To understand why it’s so important, consider how these industries depend on precise formulations. A construction material like tile adhesive requires a specific viscosity to ensure easy application. In pharmaceuticals, HPMC must dissolve properly to ensure the consistent release of active ingredients. Without a precise dissolution process, these applications could fail to meet performance standards, resulting in poor product quality or customer dissatisfaction.
What makes HPMC particularly versatile is its solubility in both hot and cold water, making it easy to manipulate according to the required consistency. For example, HPMC’s thickening properties can be controlled by adjusting the concentration or molecular weight. This flexibility makes it a staple ingredient across multiple industries.
Промышленность | Распространенное использование |
---|---|
Строительство | Tile adhesives, plaster, and other cement-based materials |
Фармацевтика | Tablet binders, controlled release agents |
Еда | Emulsifiers, stabilizers for sauces, ice cream |
2. Why Is Dissolving HPMC Correctly So Important?
The correct dissolution of HPMC is vital for achieving the intended product properties. Inconsistent dissolution can lead to lumps, uneven viscosity, and a poor final product. For example, in pharmaceutical formulations, undissolved HPMC could cause uneven tablet hardness, affecting drug release rates. In construction, improper dissolution could result in inconsistent mortar or adhesive, leading to poor bonding and workability issues.
But why exactly is this such a challenge? The answer lies in the inherent characteristics of HPMC. Its high viscosity and gel-forming ability mean that it can clump together if not dissolved under the right conditions. Temperature, stirring speed, and water quality all play a role in ensuring that HPMC dissolves uniformly.
Proper dissolution is also essential for maintaining quality control. If the dissolution process isn’t controlled, the final product might not meet regulatory standards. Whether it’s ensuring a precise viscosity for mortar or ensuring controlled release for drugs, proper dissolution directly impacts performance.
Проблема | Effect |
---|---|
Poor Dissolution | Inconsistent product performance |
Uneven Viscosity | Poor texture and functionality |
Слипание | Non-uniform product consistency |
3. What Are the Basic Methods to Dissolve HPMC?
Dissolving HPMC is not a one-size-fits-all process. There are several approaches, each suited for different applications and desired outcomes. The most common methods for dissolving HPMC include hot water dissolution, cold water dissolution, and continuous stirring techniques.
Hot water dissolution is the most common and effective method for quickly dissolving HPMC. In this process, HPMC is added to hot water (typically between 60°C and 80°C) and stirred thoroughly. The high temperature helps break down the polymer chains, enabling faster dissolution. This method is often used in pharmaceutical and food applications where high viscosity is required.
Cold water dissolution, on the other hand, is used when a gentler approach is needed. In this method, HPMC is dispersed into cold water and allowed to hydrate slowly. It’s crucial to ensure that the water is stirred constantly to avoid clumping, as the cold temperature doesn’t help dissolve the polymer as quickly.
Постоянное перемешивание is often used in larger-scale industrial settings where consistent results are required. This method involves adding HPMC to water and continuously stirring until the polymer fully dissolves. Industrial mixers or blenders are often used to ensure that the solution remains homogeneous.
Метод | Температура | Приложение |
---|---|---|
Hot Water Dissolution | 60°C to 80°C | Pharmaceuticals, high viscosity food products |
Cold Water Dissolution | Room Temperature | Sensitive formulations, slow hydration |
Continuous Stirring | Варьируется | Large-scale industrial use, consistency |
4. What Are the Common Challenges When Dissolving HPMC?
While dissolving HPMC is relatively straightforward, certain challenges can arise. One of the most common issues is the formation of lumps. HPMC has a high affinity for water, and if added too quickly or without sufficient agitation, it can form clumps that are difficult to break up.
Another challenge is controlling viscosity. When dissolving HPMC, the solution’s viscosity increases as the polymer dissolves, which can result in a paste-like consistency if not properly managed. The viscosity of the solution must be carefully controlled to meet specific application needs. For instance, in construction materials, the viscosity determines the ease of spreading and adhesion, while in pharmaceuticals, it affects tablet binding and release rates.
Finally, water quality can have a significant impact on the dissolution process. Impurities or excessive minerals in the water can affect how well HPMC dissolves, leading to inconsistencies. It is essential to use purified or distilled water when possible to achieve the best results.
Испытание | Причина | Решение |
---|---|---|
Lump Formation | Rapid addition without agitation | Gradually add HPMC, stir continuously |
Контроль вязкости | Incorrect water-to-HPMC ratio | Adjust water temperature, use correct mixing speeds |
Качество воды | Impurities in water | Use purified or distilled water |
5. How Can You Control the Viscosity of Dissolved HPMC?
Viscosity control is a critical factor when dissolving HPMC, particularly in industries like construction and pharmaceuticals. The viscosity of a dissolved HPMC solution can be influenced by several factors, including the temperature of the water, the concentration of HPMC, and the mixing speed.
Water temperature plays a crucial role in viscosity control. Higher temperatures tend to reduce the viscosity, allowing HPMC to dissolve more easily. However, temperatures that are too high can degrade the polymer, resulting in reduced effectiveness. The ideal temperature range for dissolving HPMC is typically between 60°C and 80°C.
HPMC concentration also directly affects viscosity. Higher concentrations of HPMC result in thicker solutions, while lower concentrations produce more fluid solutions. Adjusting the amount of HPMC added allows you to fine-tune the viscosity for specific applications, such as controlling the thickness of a mortar mix or the gel consistency of a pharmaceutical formulation.
Stirring speed is another key factor. Faster stirring helps break down the HPMC more quickly, but it can also introduce air bubbles into the solution. On the other hand, slow stirring can prevent air entrapment but may not dissolve the polymer as efficiently. A balance of speed is necessary for achieving the desired viscosity without compromising product quality.
Фактор | Effect | Recommended Approach |
---|---|---|
Температура воды | Controls viscosity and dissolution rate | 60°C to 80°C for optimal results |
Концентрация ГПМЦ | Более высокая концентрация увеличивает вязкость | Adjust based on application needs |
Stirring Speed | Faster speeds dissolve quickly but may introduce air | Moderate speed to prevent air entrapment |
6. What Are the Best Practices for Dissolving HPMC in Different Industries?
Each industry has its own set of requirements when it comes to dissolving HPMC. For the pharmaceutical industry, precision is key. The dissolution process must be controlled to ensure consistent tablet binding and drug release. In this sector, high-quality mixing equipment и precise temperature control are essential.
For construction, HPMC is often used in mortar and adhesives, where viscosity directly impacts application and performance. In these cases, hot water dissolution methods are typically preferred to achieve the required thick consistency. It’s important to ensure thorough mixing to avoid clumps or uneven viscosity.
In the food industry, HPMC serves as a stabilizer and emulsifier in products like sauces and dressings. Here, cold water dissolution is often used to prevent the product from becoming too thick. Gentle stirring is also required to avoid overworking the solution, which could alter the texture of the food product.
Промышленность | Dissolution Method | Ключевые соображения |
---|---|---|
Фармацевтическая | Hot water dissolution | Precision and temperature control |
Строительство | Hot water dissolution | Viscosity and workability |
Еда | Cold water dissolution | Texture and consistency |
7. How Does Temperature Affect HPMC Dissolution?
Temperature has a significant impact on how HPMC dissolves. Higher temperatures reduce the time required for the polymer to dissolve. They also lower the viscosity of the solution, which is beneficial for applications where a thinner solution is needed. However, temperatures above 80°C can cause HPMC to degrade, reducing its effectiveness.
On the other hand, cold water dissolution is often slower but beneficial for more delicate formulations, such as those used in food or pharmaceuticals. For industries that need a more gradual dissolution process, cold water can allow for better control over the final product’s consistency.
In short, temperature affects both the speed and consistency of the dissolution process. Maintaining a controlled temperature range ensures that HPMC dissolves efficiently without compromising its properties.
Диапазон температур | Влияние на растворение | Рекомендуемые приложения |
---|---|---|
60°C to 80°C | Faster dissolution, reduced viscosity | Фармацевтика, строительство |
Below 60°C | Slower dissolution, higher viscosity | Food, sensitive formulations |
8. How Can You Avoid Common Mistakes During the HPMC Dissolution Process?
Mistakes during the dissolution process can lead to poor product quality, inconsistencies, and waste. One of the most common errors is adding HPMC too quickly to water, which can cause clumping. To avoid this, always add the polymer gradually, ensuring it is thoroughly mixed before adding more.
Another common mistake is not controlling the temperature. If the water is too hot or too cold, the HPMC may not dissolve properly. Always monitor the temperature closely, especially when using hot water dissolution methods.
Finally, stirring speed should not be too high, as this can lead to the incorporation of air into the solution. This can affect the final viscosity and texture of the product. Avoid using excessive mixing speeds, and aim for a balance between speed and consistency.
Ошибка | Причина | Решение |
---|---|---|
Adding HPMC Too Quickly | HPMC clumps together | Gradually add HPMC to water |
Incorrect Temperature | Dissolution is incomplete | Monitor temperature closely |
High Stirring Speed | Air bubbles interfere with viscosity | Используйте умеренную скорость перемешивания. |
9. How Do You Ensure Consistency in Dissolved HPMC Across Batches?
Consistency is key to maintaining quality across different batches of dissolved HPMC. The first step in ensuring consistency is standardizing the dissolution process. This means using the same water quality, temperature range, and stirring speed for every batch.
Another essential practice is calibrating equipment regularly. In industrial settings, equipment like mixers and blenders must be calibrated to ensure uniform results. Consistent calibration helps avoid variations in viscosity and ensures that the dissolved HPMC meets the required specifications.
И наконец, quality control is crucial. Implementing regular testing and quality checks throughout the dissolution process helps identify potential issues early on, preventing batch-to-batch inconsistencies.
Practice | Effect | Example |
---|---|---|
Standardization | Ensures consistency across batches | Use the same temperature, stirring speed |
Калибровка оборудования | Avoids variations in results | Regular calibration of mixing equipment |
Контроль качества | Early detection of issues | Routine testing of dissolved HPMC |
10. What Are the Alternatives to HPMC for Similar Applications?
While HPMC is widely used, several alternatives can serve similar purposes, depending on the application. Methyl Cellulose (MC) is often used in place of HPMC in construction materials due to its similar properties, such as water retention and thickening.
Карбоксиметилцеллюлоза (КМЦ) is another alternative used in food and pharmaceuticals. It has a slightly different chemical structure but offers similar functionality in binding, thickening, and stabilizing.
Ethyl Cellulose can be used in specific pharmaceutical and food formulations, though it does not offer the same level of water solubility as HPMC. Each alternative has its strengths and weaknesses, and the choice of which to use depends on the specific requirements of the product being developed.
Альтернатива | Основные характеристики | Приложения |
---|---|---|
Methyl Cellulose | Water retention, thickening | Construction, adhesives |
Carboxymethyl Cellulose | Binding, thickening | Продукты питания, фармацевтика |
Ethyl Cellulose | Low solubility | Pharmaceuticals, coatings |
Заключение
Dissolving HPMC correctly is essential for achieving high-quality results in a variety of industrial applications. By understanding the best methods for dissolution, controlling key factors like temperature and viscosity, and avoiding common mistakes, you can ensure a consistent and reliable product every time. Whether you’re in the construction, pharmaceutical, or food industry, following these best practices will help you maximize the effectiveness of HPMC and improve the quality of your end product.
Часто задаваемые вопросы
Q1: What is HPMC (Hydroxypropyl Methyl Cellulose)?
HPMC is a plant-based polymer used for binding, thickening, and stabilizing in various industries like construction, pharmaceuticals, and food.
Q2: How does the temperature affect the dissolution of HPMC?
Temperature significantly impacts dissolution speed and viscosity. Higher temperatures speed up dissolution but excessive heat can degrade HPMC.
Q3: Why is viscosity control critical in HPMC dissolution?
Viscosity control is essential for achieving the desired texture and consistency, whether in construction materials or pharmaceutical formulations.
4-й квартал: What common mistakes should be avoided during HPMC dissolution?
Common mistakes include adding HPMC too quickly, incorrect temperature control, and using high stirring speeds that can introduce air.
Q5: Can HPMC be dissolved in any liquid?
HPMC dissolves best in water, and the quality of water—whether hot or cold—can affect how well it dissolves.