Hydroxypropyl Methylcellulose (HPMC) grades E3, E5, E6, E15, E50, and E4M represent a versatile family of cellulose ethers with distinct performance characteristics. These grades differ primarily in viscosity and substitution levels, directly impacting their suitability for specific applications. For purchasing managers and technical decision-makers, selecting the appropriate HPMC grade can significantly affect product performance, processing efficiency, and cost-effectiveness. This article examines the key differences between these grades, their technical specifications, and application-specific performance to help you make informed procurement decisions for your manufacturing needs.
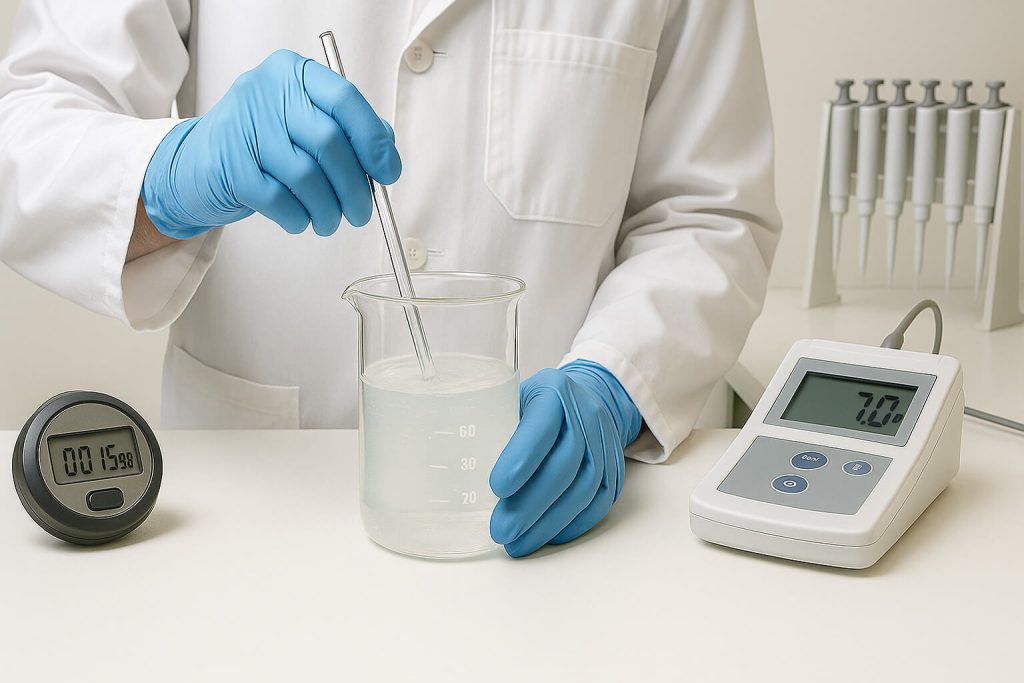
1. What Is Hydroxypropyl Methylcellulose (HPMC) And Why Is It Important?
Hydroxypropyl Methylcellulose (HPMC) is a semi-synthetic, non-ionic cellulose ether derived from cellulose through chemical modification. The base material undergoes a two-step process involving alkalization with sodium hydroxide followed by etherification with methyl chloride and propylene oxide. This creates a polymer with both methoxyl and hydroxypropyl substituent groups attached to the cellulose backbone.
But what makes this material so valuable across industries? HPMC possesses a unique combination of properties including water solubility, surface activity, film-forming capability, and thickening power. These characteristics make it an exceptionally versatile material with applications spanning multiple sectors.
The manufacturing process begins with purified cellulose, typically derived from wood pulp or cotton linters. After alkalization and etherification, the resulting product undergoes washing, neutralization, and drying before being milled to specific particle sizes.
Industry | Primary HPMC Functions | Common Grades Used |
---|---|---|
Construction | Water retention, workability improvement | E3, E5, E15 |
Pharmaceutical | Controlled release, film coating, binding | E5, E6, E15, E4M |
Food | Thickening, stabilization, emulsification | E3, E5, E15 |
Personal Care | Viscosity control, film formation | E5, E6, E15 |
Paints & Coatings | Thickening, anti-settling | E3, E5, E15 |
HPMC serves as a critical ingredient in numerous industries. In construction, it functions as a water-retention agent and rheology modifier in cement-based products. The pharmaceutical sector utilizes it as a controlled-release matrix, tablet binder, and film-coating agent. Food manufacturers incorporate it as a thickener, stabilizer, and emulsifier.
2. How Do The Different HPMC Grades (E3, E5, E6, E15, E50, E4M) Differ?
The HPMC grade designation system primarily indicates viscosity levels, with each grade offering distinct performance characteristics. The letter “E” denotes the product type, while the numerical values or alphanumeric combinations indicate the approximate viscosity of a 2% aqueous solution measured in millipascal-seconds (mPa·s) at 20°C.
Here’s what you need to understand about these differences: Lower-numbered grades like E3 and E5 provide lower viscosities, while higher-numbered grades such as E15, E50, and E4M deliver progressively higher viscosities. The E4M grade represents a significantly higher viscosity level, with the “M” indicating “thousand” (approximately 4,000 mPa·s).
The molecular weight directly correlates with viscosity—higher molecular weight polymers produce more viscous solutions. E3 has the lowest molecular weight in this series (approximately 10,000-30,000 Daltons), while E4M has the highest (approximately 300,000-400,000 Daltons).
HPMC Grade | Approximate Viscosity (2% solution, mPa·s) | Typical Molecular Weight Range (Daltons) | Common Applications |
---|---|---|---|
E3 | 2.4-3.6 | 10,000-30,000 | Cement additives, paints, food thickeners |
E5 | 4.0-6.0 | 20,000-50,000 | Pharmaceutical coatings, construction products |
E6 | 5.0-7.0 | 25,000-60,000 | Tablet binding, controlled release matrices |
E15 | 12.0-18.0 | 60,000-100,000 | Premium construction products, sustained release formulations |
E50 | 40.0-60.0 | 150,000-200,000 | Extended-release pharmaceuticals, specialty adhesives |
E4M | 3,500-5,600 | 300,000-400,000 | Long-acting drug delivery systems, specialty applications |
Performance characteristics vary significantly across the grade spectrum. Lower viscosity grades (E3, E5, E6) dissolve more rapidly in water and provide moderate film strength. Mid-range grades (E15, E50) offer balanced properties with good film formation and moderate dissolution rates. The highest viscosity grade (E4M) provides exceptional water retention, strong gel formation, and extended release properties.
3. What Are The Primary Applications For Each HPMC Grade?
Each HPMC grade serves specific functions across various industries, with viscosity being the primary determinant of application suitability. Understanding these application-specific uses helps procurement specialists select the most appropriate grade for their manufacturing requirements.
The key to maximizing value lies in matching the grade to your exact application needs. In the construction industry, E3 and E5 grades function as water-retention agents and workability enhancers in tile adhesives, renders, and self-leveling compounds. E15 finds use in premium construction products where extended open time and superior water retention are required.
The pharmaceutical sector utilizes multiple grades based on specific formulation requirements. E5 and E6 serve as binders in direct compression tablet formulations and as film-coating agents. E15 and E50 function effectively in extended-release matrix systems. E4M, with its high viscosity, is the preferred choice for long-acting controlled-release formulations.
Application Category | Recommended HPMC Grades | Key Performance Benefits |
---|---|---|
Tile Adhesives | E3, E5 | Water retention, sag resistance, extended open time |
Renders & Plasters | E5, E15 | Workability, adhesion improvement, reduced cracking |
Self-Leveling Compounds | E3, E5, E15 | Flow control, bleeding prevention, setting time regulation |
Immediate-Release Tablets | E5, E6 | Binding strength, disintegration control |
Controlled-Release Matrices | E15, E50, E4M | Customizable release rates, erosion control |
Film Coating | E5, E6, E15 | Film strength, dissolution profile, appearance |
In the food industry, E3 and E5 serve as thickeners and stabilizers in sauces, dressings, and dairy products. E15 finds application in premium food products requiring higher stability and texture control, such as ice creams and bakery fillings.
Personal care and cosmetic applications typically utilize E5 and E6 grades in lotions, creams, and hair care products. E15 appears in premium formulations where enhanced stability and texture are required.
4. How Does HPMC Viscosity Affect Performance In Different Systems?
Viscosity represents the most critical parameter affecting HPMC performance across applications. This property influences everything from processing characteristics to end-product functionality.
You’ll find that viscosity impacts every aspect of HPMC functionality in practical applications. In aqueous systems, viscosity directly correlates with water retention capability—higher viscosity grades like E50 and E4M retain water more effectively than lower viscosity grades like E3 and E5. This property proves particularly important in construction applications where preventing premature water loss ensures proper cement hydration.
Temperature significantly affects HPMC viscosity behavior. Most HPMC grades exhibit inverse thermal gelation, where viscosity decreases with initial temperature increase (up to approximately 50-60°C) but then increases dramatically as temperature rises further, eventually forming a thermal gel.
HPMC Grade | Approximate Gel Temperature Range (°C) | Viscosity Change with Temperature | Recommended Processing Temperature |
---|---|---|---|
E3 | 65-75 | Moderate decrease until gel point | Below 60°C |
E5 | 63-73 | Moderate decrease until gel point | Below 58°C |
E6 | 62-72 | Moderate decrease until gel point | Below 57°C |
E15 | 60-70 | Significant decrease until gel point | Below 55°C |
E50 | 58-68 | Significant decrease until gel point | Below 53°C |
E4M | 55-65 | Pronounced decrease until gel point | Below 50°C |
Dissolution rates vary significantly across the grade spectrum. Lower viscosity grades (E3, E5, E6) dissolve more rapidly in water, typically achieving complete dissolution within 15-30 minutes under proper dispersion conditions. Mid-range grades (E15, E50) require 30-60 minutes, while the highest viscosity grade (E4M) may need 60-120 minutes for complete dissolution.
The relationship between viscosity and functionality extends to film-forming properties as well. Lower viscosity grades produce thinner, more flexible films with faster drying times but lower mechanical strength. Higher viscosity grades create thicker films with greater mechanical strength but longer drying times.
5. What Technical Parameters Should You Consider When Selecting HPMC Grades?
Beyond viscosity, several technical parameters require careful consideration when selecting the appropriate HPMC grade for specific applications. These parameters directly influence performance characteristics and processing requirements.
The truth is that substitution levels play a crucial role in determining HPMC functionality. Methoxyl content (percentage of methoxy groups) affects organic solubility, with higher methoxyl content increasing solubility in organic solvents and improving film-forming properties. Hydroxypropyl content influences thermal gelation temperature and surface activity.
Particle size distribution significantly impacts dissolution behavior and dispersion characteristics. Finer particle sizes dissolve more rapidly but may be more prone to lumping during dispersion. Coarser particles disperse more easily but dissolve more slowly.
Parameter | Typical Range | Impact on Performance | Testing Method |
---|---|---|---|
Methoxyl Content | 19-30% | Organic solubility, film properties | HPLC or titration |
Hydroxypropyl Content | 4-12% | Gelation temperature, surface activity | HPLC or titration |
Particle Size | 95% < 100 μm | Dissolution rate, dispersion behavior | Laser diffraction |
Moisture Content | 3-5% | Storage stability, flowability | Loss on drying |
Gel Temperature | 55-75°C | Processing window, application behavior | Visual observation |
Moisture content specifications typically range from 3-5% across all grades. Higher moisture content can reduce flowability and potentially affect storage stability, while excessively low moisture content may generate static electricity issues during handling.
Additional technical parameters to consider include ash content (typically <1.5%), pH of aqueous solution (typically 5.5-8.0), and specific gravity (approximately 1.3). These parameters may have application-specific importance, particularly in pharmaceutical or food applications.
6. How Do You Properly Handle And Process Different HPMC Grades?
Proper handling and processing techniques for HPMC vary by grade and significantly impact final product performance. Following best practices for storage, dispersion, and processing helps maximize efficiency and ensure consistent results.
You should know that storage conditions directly affect HPMC stability and performance. All grades should be stored in cool, dry conditions with temperatures below 30°C and relative humidity below 65%. Higher viscosity grades (E15, E50, E4M) may be more sensitive to moisture absorption than lower viscosity grades, potentially requiring more stringent storage controls.
Dispersion and dissolution techniques vary based on grade viscosity. For lower viscosity grades (E3, E5, E6), direct addition to water under high shear mixing often proves sufficient. For higher viscosity grades (E15, E50, E4M), the “hot/cold” technique typically yields better results—dispersing the powder in hot water (above the gel temperature) to prevent lumping, then adding cold water to complete dissolution.
HPMC Grade | Recommended Dispersion Method | Mixing Equipment | Approximate Dissolution Time |
---|---|---|---|
E3, E5 | Direct addition with high shear | High-speed mixers | 15-30 minutes |
E6, E15 | Hot/cold technique preferred | Medium-speed mixers with heating | 25-45 minutes |
E50, E4M | Hot/cold technique essential | Low-speed mixers with heating | 45-120 minutes |
Processing equipment considerations include mixer type, shear requirements, and temperature control capabilities. Lower viscosity grades can be processed with standard mixing equipment, while higher viscosity grades may require more specialized equipment with greater torque capacity and temperature control.
Quality control and testing methods should be tailored to the specific grade and application. Common tests include viscosity measurement (typically using Brookfield or rotational viscometers), gel temperature determination, dissolution rate assessment, and application-specific performance tests.
7. What Are The Cost-Benefit Considerations For Different HPMC Grades?
Cost-effectiveness represents a critical factor in HPMC grade selection, particularly for large-volume applications. Understanding the price-performance relationship helps procurement specialists optimize material selection for both technical performance and economic efficiency.
The reality is that price points vary significantly across the grade spectrum. Lower viscosity grades (E3, E5, E6) typically cost 15-30% less than mid-range grades (E15, E50), which in turn cost 20-40% less than the highest viscosity grade (E4M). This pricing structure generally reflects manufacturing complexity, raw material requirements, and processing challenges associated with higher molecular weight polymers.
Performance-to-cost ratio analysis should consider both direct material costs and indirect costs related to processing efficiency, end-product performance, and potential formulation simplification. Lower viscosity grades may offer cost advantages in direct material terms but could require higher usage levels to achieve equivalent functionality.
HPMC Grade | Relative Price Index | Typical Usage Level | Cost-Performance Consideration |
---|---|---|---|
E3 | 70-80 | Higher | Good for cost-sensitive applications with moderate performance requirements |
E5 | 80-90 | Moderate-High | Balanced cost-performance for many applications |
E6 | 85-95 | Moderate-High | Similar to E5 with slightly higher viscosity |
E15 | 100 (reference) | Moderate | Standard grade for many applications |
E50 | 110-120 | Low-Moderate | Premium performance with moderate cost premium |
E4M | 130-150 | Very Low | Highest performance, justified for specialized applications |
Supply chain and availability factors also influence grade selection decisions. Lower and mid-range viscosity grades (E3, E5, E6, E15) typically enjoy broader availability from multiple suppliers, while higher viscosity grades may have more limited supply sources.
Conclusion
Selecting the appropriate HPMC grade requires balancing technical requirements, processing capabilities, and economic considerations. The grade spectrum from E3 to E4M offers solutions for virtually any application, with viscosity serving as the primary differentiator affecting performance. By understanding the specific characteristics and applications of each grade, procurement specialists can make informed decisions that optimize both product performance and cost-effectiveness.
For comprehensive technical support and consistent, high-quality HPMC across all grades, Morton offers industry-leading expertise and a complete product portfolio. Contact Morton today to discuss your specific application requirements and receive personalized recommendations from our technical team. Our specialists can help you select the optimal HPMC grade for your needs, potentially improving your product performance while optimizing costs through our global supply network and application knowledge.
FAQ
Q1: Can different grades of HPMC be mixed to achieve specific properties?
Yes, different HPMC grades can be blended to achieve intermediate viscosities or customize performance characteristics. This approach allows for fine-tuning of properties such as viscosity, dissolution rate, and gel strength. However, blending should be conducted under controlled conditions with thorough testing to ensure consistent performance. For optimal results, pre-blending in dry form followed by proper dispersion techniques yields the most consistent outcomes.
Q2: How does temperature affect the viscosity of different HPMC grades?
Temperature has a significant impact on HPMC viscosity across all grades. At lower temperatures (5-30°C), viscosity remains relatively stable. As temperature increases (30-50°C), viscosity gradually decreases. When temperature approaches the gel point (typically 55-75°C, varying by grade), viscosity increases dramatically as thermal gelation occurs. Higher viscosity grades (E50, E4M) generally show more pronounced temperature sensitivity and lower gel temperatures than lower viscosity grades (E3, E5).
Q3: What are the regulatory considerations for HPMC grades in pharmaceutical applications?
Pharmaceutical applications require HPMC grades that comply with relevant pharmacopeia standards, including USP, EP, and JP. These grades must meet strict specifications for purity, heavy metals content, residual solvents, and microbiological quality. Different substitution types are designated in pharmacopeias (e.g., HPMC 2208, HPMC 2910), indicating specific methoxyl and hydroxypropyl content ranges. Manufacturers must maintain Drug Master Files (DMFs) and provide necessary documentation for regulatory submissions.
Q4: How do you determine the optimal HPMC grade for a specific construction application?
Determining the optimal HPMC grade for construction applications involves evaluating several key parameters: required water retention level, open time needs, mechanical strength contribution, and processing conditions. For basic tile adhesives and standard mortars, E3 or E5 grades typically provide sufficient performance. Premium products requiring extended open time and superior water retention may benefit from E15. Laboratory testing should assess water retention, sag resistance, adhesion strength, and workability.
Q5: What are the sustainability aspects of HPMC compared to other cellulose derivatives?
HPMC offers several sustainability advantages compared to many synthetic polymers and some other cellulose derivatives. As a wood-derived product, it comes from renewable resources when sourced from properly managed forestry operations. The manufacturing process has been optimized over decades to reduce solvent use and energy consumption. HPMC is biodegradable under appropriate conditions, though degradation rates vary with molecular weight and substitution pattern. In construction applications, it reduces water requirements and improves material efficiency.