Selecting the right grade of Hydroxypropyl Methylcellulose can make or break your product. Many makers struggle to pick which grade works best for their needs. Using the wrong grade leads to failed products, wasted materials, and lost money. Poor choices result in weak binding, low water holding, or uneven thickness. This guide breaks down HPMC grades and uses, helping you make smart choices for better products. Studies show proper grade choice cuts failures by 40% and saves weeks of work time. Let’s look at the different grades and how to pick the right one for your needs.
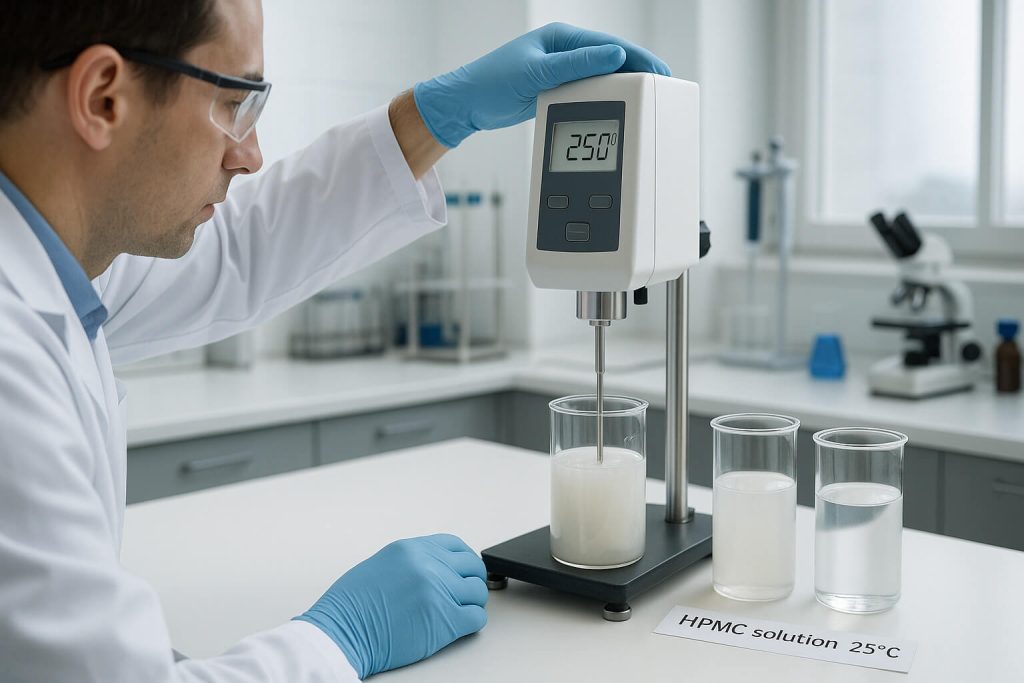
1. What Is HPMC And Why Is It Important In Manufacturing?
HPMC stands for Hydroxypropyl Methylcellulose, a changed cellulose polymer used in many fields. This useful material comes from wood pulp or cotton. It then gets changed by adding methoxyl and hydroxypropyl groups to its structure.
But why should you care about this material? It has great traits that make it useful in many ways. It forms clear films, binds things, holds water, and changes thickness as needed in today’s making.
The world market grows steady at 6-8% each year, now worth over $1.2 billion. This growth comes from more use in building items, drug making, and food goods. The building field alone uses about 40% of all HPMC made.
This polymer offers key gains that drive its wide use. It makes stable mixes across pH levels from 2-12, holds water well, and sticks well to surfaces. The stuff is also safe, breaks down in nature, and works well with many other items.
Industry | Main Uses | Market Share (%) |
---|---|---|
Building | Mortars, Tile Glues, Wall Coats | 40% |
Drug Making | Tablet Binding, Pill Coating, Slow Release | 30% |
Food | Thickener, Mixer, Blender | 15% |
Body Care | Gels, Creams, Hair Wash | 10% |
Other | Paints, Cloth, Clay Work | 5% |
Its range comes from its changing makeup. Makers can adjust how it’s made to create grades with exact traits for each job.
2. How Are Different Grades Of HPMC Classified?
These grades follow several sorting systems that help makers find the right product. Knowing these systems helps you find your way through the world of HPMC types.
The thickness-based sorting stands as the most common way to tell grades apart. Makers check thickness in units called mPa·s using a 2% mix at 20°C. Grades range from very thin (5-10 mPa·s) to very thick (100,000+ mPa·s).
Methoxyl amount gives another key sorting point. This shows how many hydroxyl groups on the chain have been swapped with methoxyl groups. The stuff often has 19-30% methoxyl, with higher amounts making it more water-shy.
Hydroxypropyl amount also changes between grades, often ranging from 7-12%. This swap affects how it mixes with water, acts on surfaces, and forms gels with heat. More hydroxypropyl helps it mix better in cold water.
Sorting Factor | Range | Effect on Traits |
---|---|---|
Thickness | 5 – 100,000+ mPa·s | Controls flow, bulk, water holding |
Methoxyl Amount | 19 – 30% | Affects water-shyness, gel power |
Hydroxypropyl Amount | 7 – 12% | Changes water mixing, heat gel forming |
Bit Size | 20 – 150 mesh | Sets how fast it mixes |
Weight Size | 10,000 – 1,500,000 Da | Impacts thickness, film power |
Field-set rules add more sorting layers. Drug grades must meet strict pure rules (USP, EP, JP). Building grades focus on water holding and work ease. Food grades must meet food safety rules (FDA, EFSA).
The naming for grades often joins these sorting parts. For example, a grade called “K15M” shows a set thickness (15,000 mPa·s) and methoxyl/hydroxypropyl swap type.
3. What Are The Key Properties That Vary Between HPMC Grades?
Different grades show changing traits that affect how they work in set uses. Seeing these changes helps you match the right grade to what you need.
Thickness ranges show the most clear change between grades. Low-thickness grades (5-100 mPa·s) give small thickening and work well in spray uses. Mid-thickness grades (100-15,000 mPa·s) offer mixed traits for wide use. High-thickness grades (15,000-100,000+ mPa·s) give top water holding and binding power.
How does this affect your product? The thickness grade you pick changes how you mix, apply, and get final results. For example, high-thickness grades need strong mixing tools but hold more water in cement uses.
Mixing changes between grades stem from their swap patterns. Some grades mix fast in cold water, while others need hot water to fully mix. Some special grades can mix in other fluids like pure alcohol or nail polish remover for set uses.
Trait | Low-Grade | Mid-Grade | High-Grade |
---|---|---|---|
Thickness (2% mix) | 5-100 mPa·s | 100-15,000 mPa·s | 15,000-100,000+ mPa·s |
Gel Heat | 40-50°C | 50-70°C | 70-90°C |
Water Holding | Low | Mid | High |
Film Power | Low | Mid | High |
Mix Speed | Fast | Mid | Slow |
Gel heat changes between grades affect heat acts. The stuff shows reverse heat gelling, making gels when heated above its set gel heat. This heat range is 40-90°C based on grade, with more methoxyl often making higher gel heats.
Bit size spread impacts mix speed and how to apply. Fine bits (20-50 mesh) mix fast but may clump. Mid bits (50-80 mesh) give good mix balance. Coarse bits (80-150 mesh) give slow, even mixing best for slow-release uses.
4. Which HPMC Grades Work Best For Construction Applications?
Building uses need set grades that give the right mix of water holding, work ease, and stick power. Picking the right grade can greatly boost your building product work.
Cement-based goods often use mid to high-thickness grades (15,000-100,000 mPa·s) with high water holding skills. These grades stop water from being soaked up too fast by dry bases, letting cement wet well. Building-grade stuff often has 28-30% methoxyl and 7-12% hydroxypropyl.
Want to know a work secret? The best building grades join high water holding with good work ease. This mix lets you apply it more easily while keeping work time and stopping sags on walls.
Tile glue mixes need grades that give great slip stop and long work time. Grades with thickness between 20,000-60,000 mPa·s work best for these uses. The amount in tile glues is often 0.2-0.5% of the total mix weight.
Building Use | Best Grade | Usual Amount | Key Gains |
---|---|---|---|
Cement Mixes | 30,000-70,000 mPa·s | 0.1-0.3% | Water holding, work ease |
Tile Glues | 20,000-60,000 mPa·s | 0.2-0.5% | Work time, slip stop |
Wall Coats | 15,000-40,000 mPa·s | 0.1-0.4% | Work ease, sag stop |
Self-Level Mixes | 5,000-15,000 mPa·s | 0.05-0.2% | Flow check, foam cut |
Joint Fills | 40,000-100,000 mPa·s | 0.3-0.6% | Crack stop, stick power |
Wall coat uses gain from grades with thickness between 15,000-40,000 mPa·s. These grades make work easier, keep work time, and boost stick to many bases. The water holding traits stop fast drying, cutting crack risk and making it last longer.
Water holding traits change much between building grades. Top grades can hold over 95% of mix water for long times, while basic grades hold 70-85%. This trait changes work time, which can range from 15 minutes to over an hour based on the grade used.
5. What HPMC Grades Are Used In Pharmaceutical Products?
Drug uses need special grades that meet strict rules. These grades must work the same way each time while staying pure and safe for people to take.
USP/EP/JP grade needs set the base for drug use. These grades must meet book rules for swap type, metal bits, bug limits, and left-over mix fluids. The most common book types are 2208 (22% methoxyl, 8% hydroxypropyl) and 2910 (29% methoxyl, 10% hydroxypropyl).
Slow-release forms often use high-thickness grades (15,000-100,000+ mPa·s). These grades form a gel layer around the pill when in gut fluids, slowing drug release over time. The release rate can be fine-tuned by picking set thickness grades or mixing many grades.
Did you know this matters for drug work? The right grade can stretch drug release from 4-24 hours, helping people take pills as told and get better. Studies show that well-made slow-release pills can help people take them right by up to 30%.
Drug Use | Best Type | Thickness Range | Job |
---|---|---|---|
Fast Release Pills | 2910 | 3-15 mPa·s | Binder, Break-up Aid |
Slow Release Pills | 2208 | 4,000-100,000 mPa·s | Release Check |
Film Coating | 2910 | 3-15 mPa·s | Film Maker |
Pill Shells | 2910 | 3-15 mPa·s | Gel Stand-in |
Eye Drops | 2906/2910 | 80-30,000 mPa·s | Thickness Boost |
Film coating uses need low-thickness grades (3-15 mPa·s) that can be sprayed as fine drops. These grades form thin, even films around pills, giving wet guard, taste mask, or changed look. Type 2910 is best for most coating uses due to its great film-making traits.
Pill binding grade choice hangs on the press way and wanted break-up shape. Direct press forms often use low to mid thickness grades (5-100 mPa·s), while wet grain ways can use higher thickness grades (100-4,000 mPa·s) as binders.
6. How Do You Select The Right HPMC Grade For Your Application?
Picking the best grade needs a step-by-step way that thinks about your set use needs. Using a clear path helps avoid costly mix fails.
The pick path starts with naming your main work needs. Ask: What is the most key job in your use? Is it water holding, thickness change, binding, film making, or slow release? This first check cuts down the likely grade groups.
Next, think about your mix states. Different grades work in their own ways under many mix ways, heats, and pH states. Low-thickness grades mix more easily but hold less water. High-thickness grades give better work but may need more strong mix tools.
Here’s a handy tip: Always test many grades in your real mix. Lab tests may not fully show real-world work. Small tests with 2-3 grades often show the best pick for your set states.
Pick Factor | Ask These | Impact on Grade Pick |
---|---|---|
Main Job | Water holding? Binding? Film making? | Sets thickness range |
Mix Way | Dry mix? Wet mix? Spray use? | Affects bit size needs |
Use Place | Heat? pH? Base soak? | Guides swap type |
Rule Needs | Food? Drug? Building? | Sets rule marks |
Cost Limits | Cash limits? Work wants? | Guides grade/work balance |
Test ways for grade check should have use-set tests. For building uses, check water holding, work time, and stick power. For drug uses, check how it breaks down, film look, or bind power. Food uses should check thickness stay, mouth feel, and how it works with other parts.
Common swap choices exist between like grades. If your best grade isn’t there, you can often swap a grade with like thickness and swap type. In some cases, mixing two grades can get mid traits that match your needs.
7. What Quality Control Measures Apply To Different HPMC Grades?
Quality checks change much between grades and uses. Knowing these changes helps you keep the same product quality and follow rules.
Set test ways change by field. Building grades get tests for water holding, mix state, and air pull by rules like EN 934-2. Drug grades follow book ways for swap level, thickness, and pure state. Food grades need tests by food add specs like FAO/WHO JECFA.
Proof of Check lists give key quality facts. A usual list has thickness, wet amount, pH, swap level, and ash amount. Drug grades add tests for metal bits, left-over mix fluids, and bug limits. Food grades add more tests for bad stuff.
Why does this matter for your work? Same quality checks stop making problems and product fails. One making place saw 75% less batch throws after using full test ways.
Quality Point | Set Test Way | Usual Spec | Key For |
---|---|---|---|
Thickness | ASTM D2363 | ±20% of set value | All uses |
Wet Amount | Loss on Drying | ≤5% | Stay, flow traits |
Swap Level | HPLC or IR Spec | ±1% of told value | Work same |
Metal Bits | USP <231> | ≤20 ppm | Drug/food safe |
Bit Size | Laser Spread | Use-set | Mix rate |
Batch-to-batch same checks help keep product quality. Top makers use math work check to watch key points across making batches. Usual change limits are ±20% for thickness, ±1% for swap level, and ±5% for wet amount.
Store and use needs change between grades. Most grades should be kept in cool, dry spots away from sun. Drug grades need more strict checks, with heat watch and wet check. All grades should be kept from dirt and stored in closed bins.
Conclusion
Picking the right grade greatly changes your product’s work and making ease. The changes between grades—from thickness and swap pattern to bit size and pure state—change how the stuff works in your set use. By knowing these changes, you can make smart picks that boost product quality and cut mix problems. Data shows that right grade picks can cut growth time by up to 40% and boost product work by 15-30%. For help on picking the best grade for your set needs, call Morton’s tech team today. Our pros can tell you the best grade based on what you need and help you get the same, high-quality results in your making path.
FAQ
Q1: What is the difference between HPMC and MC (Methyl Cellulose)?
HPMC has both methyl and hydroxypropyl groups, while MC has only methyl groups. This change gives HPMC better mixing in cold water, more surface work, and better heat gel traits than MC. HPMC also stays more stable in base states, making it work better for building uses.
Q2: Can different grades of HPMC be mixed for custom applications?
Yes, you can mix grades to get custom traits. Makers often blend grades with changing thickness or swap levels to make goods with set work traits. But you need to test if they work well together and stay stable during storage and use.
Q3: How does temperature affect different grades of HPMC?
Heat changes how grades work based on their makeup. Lower-swapped grades often gel at lower heats (32-40°C), while higher-swapped grades gel at higher heats (60-90°C). All grades show reverse heat gelling, making gels when heated and mixing when cooled, but the exact change heat varies by grade.
Q4: What are the storage requirements for maintaining HPMC grade quality?
Keep it in cool, dry spots away from sun. The best storage heat is 10-30°C with wet level below 65%. Higher-grade drug goods need more strict storage to stay pure. When stored right, it often lasts 2-3 years, though drug grades may have more set end dates.
Q5: How do particle size differences between HPMC grades affect performance?
Bit size changes how fast it mixes, with smaller bits mixing faster but maybe clumping. Larger bits give slower, more even mixing but need more mix time. Fine-bit grades (20-80 mesh) work for fast-mix uses, while coarser grades (80-100+ mesh) work better for slow-release forms or uses needing slow wet growth.