HPMC E3 is a versatile cellulose derivative that plays a crucial role across multiple industries, from pharmaceuticals to construction. This article addresses the specific properties that make HPMC E3 valuable for industrial applications, helping purchasing managers and technical decision-makers select the right grade for their needs. By understanding the unique characteristics of HPMC E3, you can optimize formulations, improve product performance, and potentially reduce costs. The following comprehensive analysis draws on technical data and practical application experience to provide you with actionable insights for your HPMC E3 purchasing and implementation decisions.
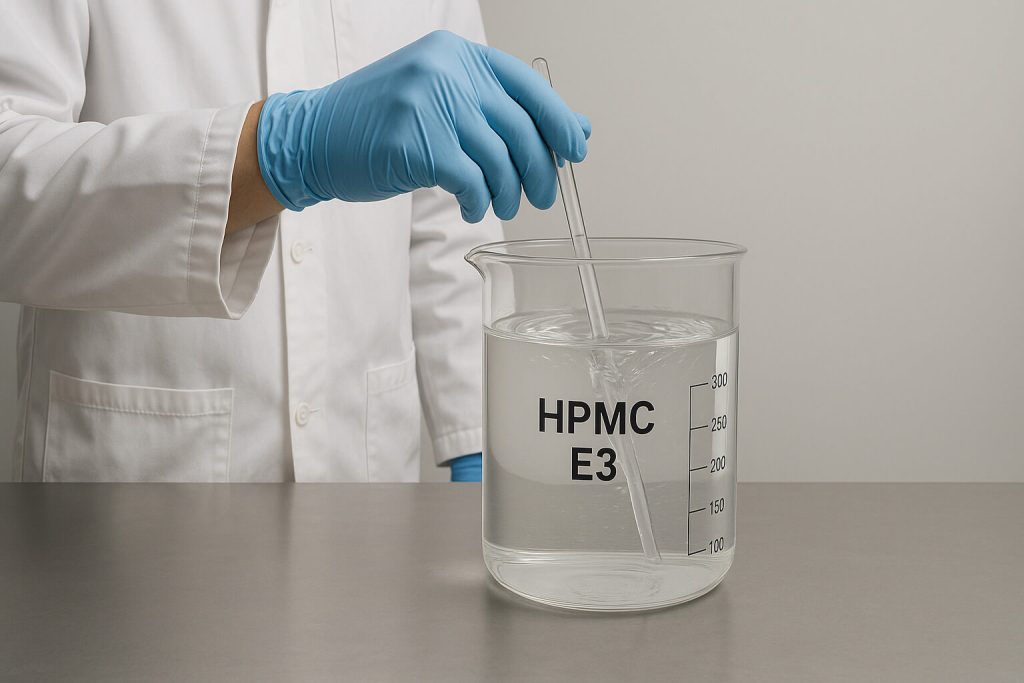
1. What Is HPMC E3 and How Does It Differ from Other Cellulose Derivatives?
HPMC E3 (Hydroxypropyl Methylcellulose E3) is a semi-synthetic polymer derived from cellulose through chemical modification. The “E3” designation refers to a specific viscosity grade within the HPMC family, indicating a low-viscosity product typically ranging from 2.4 to 3.6 mPa·s in a 2% solution at 20°C.
But what makes it truly stand out from other cellulose derivatives is its unique balance of methoxyl and hydroxypropyl substitution. HPMC E3 typically contains 28-30% methoxyl groups and 7-12% hydroxypropyl groups, creating a polymer with excellent film-forming capabilities and controlled solubility.
The manufacturing process involves treating alkali cellulose with methyl chloride and propylene oxide in carefully controlled ratios. This process determines the degree of substitution, which directly influences the final properties of the material. Quality manufacturers maintain strict control over reaction parameters to ensure batch-to-batch consistency.
When compared to other cellulose ethers like methylcellulose (MC), carboxymethylcellulose (CMC), or higher-viscosity HPMC grades, HPMC E3 offers distinct advantages:
Property | HPMC E3 | Other HPMC Grades | CMC | MC |
---|---|---|---|---|
Viscosity (2% solution) | 2.4-3.6 mPa·s | 4-100,000 mPa·s | 5-50,000 mPa·s | 4-100,000 mPa·s |
Gel Temperature | 58-64°C | 58-90°C | No thermal gelation | 50-55°C |
Salt Sensitivity | Low | Low | High | Low |
pH Stability Range | 2-12 | 2-12 | 4-10 | 3-11 |
The physical characteristics that define HPMC E3 include its white to off-white powder appearance, particle size distribution (typically 95% passing through 100-mesh screen), and bulk density of approximately 0.25-0.70 g/cm³. These properties make it easy to handle in industrial settings and contribute to its excellent dispersibility.
2. What Makes HPMC E3 Valuable in Pharmaceutical Formulations?
HPMC E3’s low viscosity grade makes it particularly suitable for pharmaceutical applications where precise control over drug release and manufacturing efficiency are paramount. Its film-forming properties enable the creation of thin, uniform coatings on tablets and capsules, providing protection against environmental factors while ensuring consistent drug release.
Here’s the remarkable thing about HPMC E3 in controlled release applications: it forms a gel layer when in contact with aqueous media, creating a diffusion barrier that regulates drug release. The low viscosity of E3 grade produces a less restrictive gel layer compared to higher viscosity grades, making it ideal for formulations requiring faster release profiles.
In tablet manufacturing, HPMC E3 serves as an effective binder in both wet and dry granulation processes. Its binding strength is sufficient to maintain tablet integrity while allowing for proper disintegration when required. Typical concentration ranges for different pharmaceutical applications include:
Application | HPMC E3 Concentration | Key Benefit | Processing Method |
---|---|---|---|
Film Coating | 2-10% w/w | Uniform, thin coatings | Spray application |
Binder in Wet Granulation | 2-5% w/w | Good cohesion, low viscosity | Addition to granulation liquid |
Dry Binder | 2-5% w/w | Improved compressibility | Direct blending |
Extended Release Matrix | 10-30% w/w | Controlled diffusion barrier | Direct compression |
From a regulatory perspective, HPMC E3 holds significant advantages. It is included in the FDA Inactive Ingredient Database, the European Pharmacopoeia, and the Japanese Pharmaceutical Excipients directory. This widespread regulatory acceptance streamlines the approval process for new pharmaceutical products incorporating this excipient.
Case studies demonstrate HPMC E3’s versatility in pharmaceutical applications. For instance, one generic drug manufacturer reported a 15% improvement in coating uniformity and a 20% reduction in coating time when switching from a higher viscosity HPMC to E3 grade for their enteric-coated tablets.
3. How Does HPMC E3 Perform in Construction Materials?
In construction applications, HPMC E3 serves as a critical additive that enhances the performance of mortars, cement-based renders, and tile adhesives. Its primary function is water retention, which prevents premature drying and ensures proper cement hydration, especially in hot or dry conditions.
You’ll be surprised by how effectively HPMC E3 improves workability in cementitious mixtures. By increasing the water retention capacity, it extends the open time of mortars and adhesives, giving workers more time to place and adjust tiles or other building materials. This property is particularly valuable in large-scale commercial projects where application efficiency directly impacts labor costs.
The impact of HPMC E3 on setting time and mechanical strength is significant and concentration-dependent:
HPMC E3 Dosage (% by weight of cement) | Water Retention (%) | Open Time Extension (minutes) | Impact on Final Strength |
---|---|---|---|
0.1% | 85-90% | +15-20 | Minimal reduction (<5%) |
0.3% | 92-96% | +30-40 | Slight reduction (5-10%) |
0.5% | 97-99% | +50-70 | Moderate reduction (10-15%) |
The adhesion enhancement provided by HPMC E3 in tile adhesives is particularly noteworthy. It increases the contact area between the adhesive and substrate by reducing slump and improving sag resistance. Testing has shown that properly formulated tile adhesives containing HPMC E3 can achieve tensile adhesion strengths exceeding 1 N/mm², meeting or surpassing international standards for both internal and external applications.
For different construction applications, dosage recommendations vary:
Application | Recommended HPMC E3 Dosage | Key Performance Benefit |
---|---|---|
Cement-based Renders | 0.1-0.3% | Improved workability and reduced cracking |
Tile Adhesives | 0.3-0.5% | Extended open time and enhanced adhesion |
Self-leveling Compounds | 0.05-0.15% | Improved flow without segregation |
Gypsum-based Plasters | 0.1-0.2% | Better workability and reduced water demand |
4. What Are the Rheological Properties of HPMC E3 Solutions?
The rheological behavior of HPMC E3 solutions is fundamental to its performance across various applications. As a low-viscosity grade, HPMC E3 provides functional benefits without excessively thickening formulations, making it ideal for applications where minimal viscosity impact is desired.
The fascinating aspect of HPMC E3 solutions is how their viscosity changes with concentration and temperature. At room temperature (20°C), the relationship between concentration and viscosity follows a power law relationship, with viscosity increasing exponentially as concentration increases:
HPMC E3 Concentration (w/w) | Approximate Viscosity at 20°C (mPa·s) | Approximate Viscosity at 50°C (mPa·s) |
---|---|---|
1% | 1.5-2.0 | 0.8-1.2 |
2% | 2.4-3.6 | 1.3-2.0 |
5% | 15-25 | 8-15 |
10% | 100-200 | Gel formation |
The temperature-dependent behavior of HPMC E3 solutions exhibits an inverse relationship with viscosity up to a certain point. As temperature increases from 5°C to approximately 55°C, viscosity gradually decreases. However, once the solution reaches its gel point (typically 58-64°C for HPMC E3), a dramatic increase in viscosity occurs as the polymer undergoes thermal gelation.
This thermal gelation phenomenon results from the dehydration of polymer chains and subsequent hydrophobic association. The gel formation temperature and mechanism have practical implications in applications like pharmaceutical capsule manufacturing, where thermal gelation is utilized to form stable structures.
HPMC E3 solutions also exhibit thixotropic behavior, meaning their viscosity decreases under shear stress and recovers when the stress is removed. This property is particularly valuable in coating applications, where the solution should flow easily during application but resist running or sagging afterward.
Rheological Property | HPMC E3 Characteristic | Practical Implication |
---|---|---|
Viscosity-Temperature Relationship | Inverse until gel point | Easier processing at elevated temperatures |
Thixotropy | Moderate | Good balance of flow and stability |
Shear Thinning | Present but limited | Predictable flow under varying shear conditions |
Gel Strength | Low to moderate | Suitable for applications requiring weak gel structure |
For quality control purposes, manufacturers typically measure the viscosity of HPMC E3 using rotational viscometers under standardized conditions (2% solution at 20°C).
5. How Does HPMC E3 Function in Food and Beverage Applications?
In food applications, HPMC E3’s low viscosity profile makes it an excellent functional ingredient that provides technical benefits without significantly altering the texture or mouthfeel of the final product. Its primary functions include emulsification, stabilization, and texture modification.
What you might not realize is that HPMC E3 acts as an effective emulsifier due to its amphiphilic nature, with hydrophilic hydroxypropyl groups and more hydrophobic methoxyl groups. This molecular structure allows it to position at oil-water interfaces, reducing interfacial tension and stabilizing emulsions. In salad dressings and sauces, HPMC E3 can maintain emulsion stability at concentrations as low as 0.1-0.3%, without significantly increasing viscosity.
The stabilization capabilities of HPMC E3 extend beyond emulsions to foams and suspensions. In whipped products, it enhances foam stability by forming a protective film around air bubbles, preventing coalescence. In fruit juice beverages, it keeps particulates in suspension without creating an overly thick consistency.
Food Application | HPMC E3 Concentration | Functional Benefit | Impact on Final Product |
---|---|---|---|
Bakery Products | 0.2-0.5% | Moisture retention, improved volume | Softer texture, extended shelf life |
Fried Foods | 0.5-2.0% (coating) | Oil barrier formation | Reduced oil absorption, crispier texture |
Sauces & Dressings | 0.1-0.3% | Emulsion stabilization | Improved stability without excessive thickening |
Dairy Alternatives | 0.2-0.4% | Fat mimetic, stabilizer | Creamy mouthfeel, reduced syneresis |
From a nutritional perspective, HPMC E3 contributes dietary fiber, as it is not digestible by human enzymes. While not metabolized for energy, it can have physiological effects similar to other soluble fibers, potentially contributing to satiety and helping to moderate glucose absorption.
Heat stability is a significant advantage of HPMC E3 in food processing. Unlike many natural hydrocolloids, it maintains functionality after high-temperature processing, including baking, retorting, and UHT treatment. This thermal stability makes it suitable for applications requiring heat sterilization or cooking.
Regulatory status favors HPMC E3 in food applications. It is approved as food additive E464 in the European Union and has GRAS (Generally Recognized As Safe) status in the United States.
6. What Technical Challenges Exist When Working with HPMC E3?
Despite its versatility, working with HPMC E3 presents several technical challenges that manufacturers must address to achieve optimal performance. Proper dissolution techniques are critical, as incorrect dispersion can lead to lumping, incomplete hydration, and inconsistent functionality.
The truth is that HPMC E3 requires specific dissolution methods to achieve complete hydration. The “hot/cold” technique is often most effective: dispersing the powder in one-third of the required water heated to 80-90°C (to prevent immediate hydration and lumping), followed by addition of the remaining water as cold water or ice to complete hydration as the temperature drops below the gel point.
Common processing issues and their solutions include:
Processing Issue | Cause | Solution |
---|---|---|
Lumping during dissolution | Too rapid hydration | Use hot/cold technique or high-shear mixing |
Incomplete hydration | Insufficient mixing time | Extend hydration period, optimize agitation |
Foam formation | Air incorporation during mixing | Reduce mixing speed, use defoamer if compatible |
Viscosity variation | Temperature fluctuations | Control process temperature, standardize mixing protocols |
Compatibility with other ingredients presents another challenge. HPMC E3 may interact with certain components in formulations, potentially affecting functionality:
Ingredient Type | Compatibility | Potential Interaction |
---|---|---|
Monovalent Salts (NaCl, KCl) | Good | Minimal effect on viscosity |
Divalent Salts (Ca²⁺, Mg²⁺) | Moderate | May reduce solution clarity and stability at high concentrations |
Strong Acids/Bases | Good | Stable across pH 2-12, but extreme pH may accelerate degradation |
Surfactants | Variable | Can enhance or interfere with surface activity depending on type |
Storage stability and shelf-life considerations are important for both the raw HPMC E3 powder and finished products containing it. The dry powder is relatively stable when stored in cool, dry conditions, with a typical shelf life of 2-3 years. However, factors like high humidity, elevated temperatures, and exposure to oxidizing agents can accelerate degradation.
7. How Should HPMC E3 Be Selected and Specified for Different Projects?
Selecting the appropriate HPMC E3 product for a specific application requires careful consideration of several key specification parameters. These parameters directly influence performance and should be clearly defined in purchasing specifications.
You need to understand that not all HPMC E3 products are identical, despite sharing the same general classification. Variations in substitution pattern, particle size distribution, and purity can significantly impact performance in specific applications. Developing comprehensive specifications is essential for consistent results.
Key specification parameters to consider include:
Specification Parameter | Typical Range for HPMC E3 | Importance |
---|---|---|
Viscosity (2% solution at 20°C) | 2.4-3.6 mPa·s | Critical for flow properties and functional performance |
Methoxyl Content | 28-30% | Affects solubility, thermal gelation, and surface activity |
Hydroxypropyl Content | 7-12% | Influences water retention and organic solubility |
Moisture Content | ≤5% | Impacts flow properties and microbial stability |
Particle Size Distribution | 95% through 100-mesh | Affects dissolution rate and dispersion quality |
Testing methods for quality verification should be standardized and agreed upon between supplier and purchaser. Common methods include rotational viscometry for viscosity determination, gas chromatography for substitution analysis, and laser diffraction for particle size measurement.
When conducting a cost-benefit analysis compared to alternatives, consider not only the raw material price but also processing efficiency, functional benefits, and potential formulation simplification. For example, while HPMC E3 may have a higher unit cost than some natural gums, its superior stability and consistent performance may reduce waste and quality issues, resulting in lower total cost of ownership.
Environmental impact and sustainability aspects are increasingly important considerations. Some manufacturers now offer HPMC E3 produced using wood pulp from certified sustainable forestry practices. Additionally, production processes with reduced solvent usage and improved energy efficiency are becoming available, potentially reducing the carbon footprint of the material.
Conclusion
HPMC E3 offers a unique combination of properties that make it invaluable across pharmaceutical, construction, food, and other industrial applications. Its low viscosity profile, excellent film-forming capabilities, and versatile functionality provide significant advantages in formulation development and process optimization. By understanding the specific properties discussed in this article, you can make informed decisions about incorporating HPMC E3 into your products.
For businesses seeking to optimize their formulations with HPMC E3, Morton provides comprehensive technical support, consistent quality, and sustainable sourcing options that ensure reliable performance. Contact Morton’s technical team today to discuss your specific application requirements and discover how our HPMC E3 products can enhance your manufacturing processes and end products. Partner with Morton for access to industry-leading expertise and innovative cellulose solutions that drive your business forward.
FAQ Section
Q1: What is the optimal dissolution method for HPMC E3?
The most effective dissolution method for HPMC E3 is the “hot/cold” technique. First, disperse the powder in one-third of the total water heated to 80-90°C while mixing vigorously. This prevents immediate hydration and lumping. Then add the remaining two-thirds as cold water or ice to complete hydration as the temperature drops below the gel point (approximately 58-64°C). For small quantities, pre-mixing with other dry ingredients before adding to water can also improve dispersion.
Q2: How does the viscosity of HPMC E3 compare to other HPMC grades?
HPMC E3 is among the lowest viscosity grades in the HPMC family, typically providing 2.4-3.6 mPa·s in a 2% solution at 20°C. By comparison, HPMC E5 yields 4-6 mPa·s, HPMC E15 provides 12-18 mPa·s, and HPMC E4M delivers 3,000-5,600 mPa·s under the same conditions. This low viscosity makes E3 ideal for applications requiring functional benefits without significant thickening, such as film coating, binding at low concentrations, and emulsion stabilization where flow properties must be maintained.
Q3: Can HPMC E3 be used in combination with other cellulose derivatives?
Yes, HPMC E3 can be effectively combined with other cellulose derivatives to achieve synergistic effects. Common combinations include HPMC E3 with higher viscosity HPMC grades to create tailored release profiles in pharmaceutical formulations, or with carboxymethylcellulose (CMC) to balance water retention and workability in construction applications. When combining with other cellulose derivatives, it’s important to consider potential competitive hydration, which may require adjustments to dissolution procedures.
Q4: What are the storage requirements for maintaining HPMC E3 quality?
HPMC E3 should be stored in its original sealed packaging in a cool, dry environment with temperatures below 30°C and relative humidity under 65%. Under these conditions, it typically maintains its quality for 2-3 years. Once opened, containers should be tightly resealed to prevent moisture absorption, which can cause agglomeration and affect flow properties. For production environments, implementing first-in-first-out inventory management is recommended.
Q5: How does HPMC E3 perform in extreme pH conditions?
HPMC E3 demonstrates remarkable stability across a wide pH range from 2 to 12, making it suitable for both acidic and alkaline formulations. In strongly acidic conditions (pH < 2), hydrolysis of the glycosidic bonds may gradually occur, leading to reduced molecular weight and decreased viscosity over time. In highly alkaline environments (pH > 12), deprotonation of hydroxyl groups can increase water solubility but may affect thermal gelation properties.