Selecting the correct Hydroxypropyl Methylcellulose (HPMC) grade presents a common challenge for many businesses. This choice directly impacts product performance, manufacturing efficiency, and ultimately, market success. Missteps can lead to costly reformulations, production delays, and compromised product quality, creating significant frustration. This article provides clear guidance on HPMC grades, helping you make informed decisions to optimize your product development and achieve superior results. This guide will cover HPMC fundamentals, classification methods, common grades, and selection criteria for various applications.
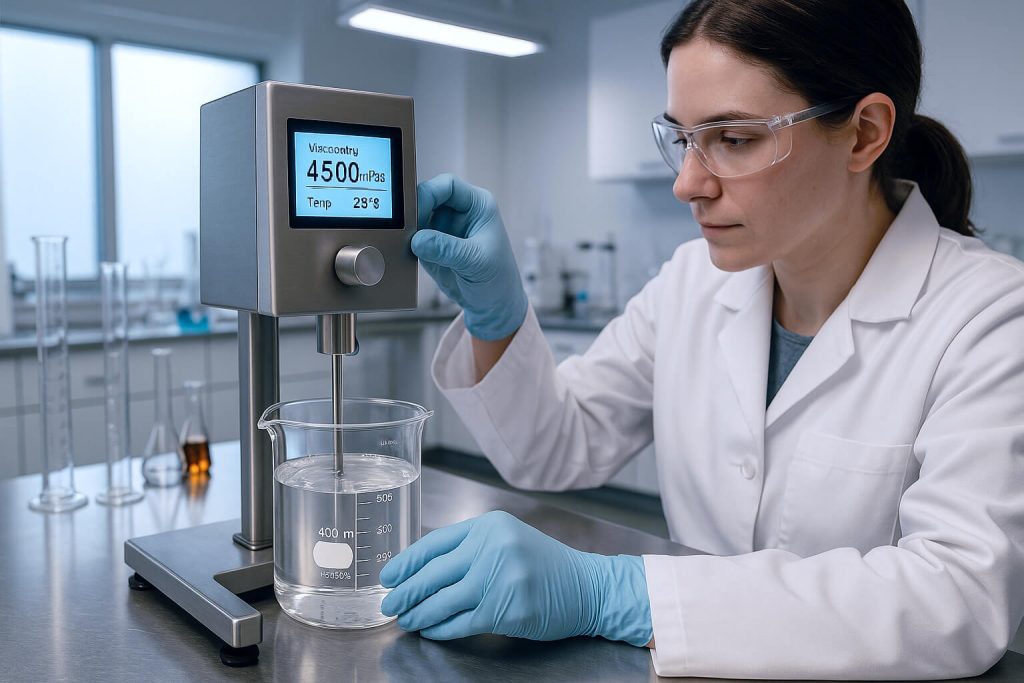
1. What is HPMC and why is it important?
HPMC is a versatile polymer derived from cellulose, a natural plant fiber. It undergoes chemical modification to enhance its properties, making it suitable for a wide array of industrial uses. This semi-synthetic compound is odorless and tasteless, appearing as a white to off-white powder. Its unique molecular structure allows it to dissolve in cold water, forming a clear solution that thickens upon heating. This thermal gelation property is particularly valuable in many applications. Here’s why it matters… HPMC serves as a thickener, binder, film-former, and water retention agent across diverse sectors.
Its importance stems from its ability to improve product stability, texture, and performance. For example, in construction, HPMC enhances workability and adhesion of mortars. In pharmaceuticals, it controls drug release rates. In food, it acts as a stabilizer and emulsifier. These varied functions make HPMC an indispensable ingredient in modern manufacturing processes. Understanding its basic composition helps in appreciating its broad utility.
Property | Description |
---|---|
Chemical Origin | Cellulose derivative |
Appearance | White to off-white powder |
Solubility | Soluble in cold water |
Thermal Behavior | Forms gel upon heating |
Key Functions | Thickener, binder, film-former, water retention agent |
2. How are HPMC grades classified?
HPMC grades are primarily classified by their viscosity, substitution types, and particle size. Viscosity is often the first characteristic considered, as it dictates the material’s thickening power in solution. Manufacturers measure viscosity at specific concentrations and temperatures, typically using a 2% solution at 20°C. Higher viscosity numbers indicate a thicker solution. This measurement provides a direct indicator of how the HPMC will perform in a given application. Different applications require different levels of thickening. For example, a coating application needs lower viscosity than a sustained-release tablet.
Substitution types refer to the degree and pattern of methoxyl and hydroxypropoxyl groups attached to the cellulose backbone. These groups influence properties like gelation temperature, solubility, and film flexibility. Particle size also plays a significant role, affecting dissolution rate and dispersion. Finer particles dissolve faster but can be harder to disperse without clumping. Coarser particles disperse more easily but take longer to hydrate fully. Each classification factor helps define the specific performance characteristics of an HPMC grade, guiding its selection for particular uses.
Classification Factor | Impact on Performance |
---|---|
Viscosity | Thickening power, flow properties |
Substitution Type | Gelation temperature, solubility, film properties |
Particle Size | Dissolution rate, dispersion behavior |
3. What are the common HPMC grades and their characteristics?
Common HPMC grades are tailored for specific industries, each with distinct characteristics. Pharmaceutical grades, often designated by letters like K, E, F, and P, vary in their methoxyl and hydroxypropoxyl content, which affects their gelation temperature and solubility. K-type HPMC, for instance, has a lower gelation temperature and is widely used for sustained-release applications due to its strong gelling properties. E-type HPMC has a higher gelation temperature and is common in film coatings and binders. These differences allow precise control over drug release and tablet integrity. But here’s the thing… selecting the right pharmaceutical grade ensures optimal drug delivery and patient safety.
Food grades, such as E464, meet strict regulatory standards for consumption. They function as thickeners, stabilizers, and emulsifiers in various food products. Construction grades are designed for high water retention and improved workability in cement-based materials. These often have higher viscosity and specific modifications to enhance adhesion and open time. Other industrial grades serve diverse purposes, from personal care products to paints and coatings. Each grade is engineered to deliver specific performance benefits within its intended application area.
HPMC Grade Type | Typical Characteristics | Primary Applications |
---|---|---|
Pharmaceutical (K-type) | Lower gelation temperature, strong gelling | Sustained-release tablets |
Pharmaceutical (E-type) | Higher gelation temperature, good film-forming | Film coatings, binders |
Food (E464) | High purity, thickening, stabilizing | Baked goods, dairy, dressings |
Construction | High water retention, improved workability | Tile adhesives, renders |
4. How does viscosity affect HPMC performance?
Viscosity is a critical parameter determining HPMC performance across applications. Low viscosity HPMC grades create thin solutions, making them ideal for film coatings on tablets or as ophthalmic solutions. They provide a smooth, uniform layer without excessive thickening. Medium viscosity grades act as effective binders in tablet formulations or as general thickeners in liquid products. They offer a balance between flowability and structural integrity. High viscosity HPMC grades form thick, viscous solutions, which are essential for sustained-release drug formulations, where they control the rate at which a drug dissolves and is absorbed. They also find use in cement mortars to improve water retention and prevent premature drying. Now, you might be wondering… how is this viscosity measured?
Viscosity is typically measured using a Brookfield viscometer at a specified concentration and temperature, often 2% solution at 20°C. This standardized test ensures consistent results and allows for accurate comparison between different HPMC grades. The choice of viscosity directly impacts the final product’s texture, stability, and functional properties. For instance, a high-viscosity HPMC in a paint formulation prevents sagging and improves brushability, while a low-viscosity HPMC in a liquid detergent ensures easy pouring.
Viscosity Range | Typical Applications | Performance Impact |
---|---|---|
Low | Film coatings, ophthalmic solutions | Thin, uniform layers, quick dissolution |
Medium | Tablet binders, general thickeners | Balanced flow and structural integrity |
High | Sustained release, cement mortars | Controlled release, water retention, anti-sag |
5. What role do substitution types play in HPMC selection?
Substitution types, specifically the methoxyl and hydroxypropoxyl content, profoundly influence HPMC properties and selection. Methoxyl content primarily dictates the gelation temperature of HPMC solutions. Higher methoxyl content generally leads to lower gelation temperatures. This is important for applications where thermal gelling is desired at specific temperatures, such as in certain food products or controlled-release systems. Hydroxypropoxyl content, on the other hand, largely determines the water solubility and surface activity of HPMC. Higher hydroxypropoxyl content enhances water solubility and can improve film formation and adhesion properties. Let me explain… these subtle chemical differences translate into significant functional variations.
The balance between these two substitution groups allows manufacturers to fine-tune HPMC grades for precise applications. For example, an HPMC with a specific methoxyl-hydroxypropoxyl ratio might be chosen for its ability to form a strong, flexible film in a pharmaceutical coating, while another ratio might be preferred for its superior water retention in a construction material. Understanding these substitution patterns helps in predicting how an HPMC grade will behave under different conditions and in various formulations. This chemical tailoring ensures optimal performance for diverse industrial needs.
Substitution Type | Primary Influence | Application Relevance |
---|---|---|
Methoxyl Content | Gelation temperature | Thermal gelling, controlled release |
Hydroxypropoxyl Content | Water solubility, surface activity | Film formation, adhesion, thickening |
6. How does particle size influence HPMC functionality?
Particle size significantly impacts HPMC functionality, particularly its dissolution rate and dispersion behavior. Fine HPMC powders dissolve more quickly, which is advantageous in applications requiring rapid hydration, such as instant beverage mixes or quick-setting construction materials. However, finer particles can also be more prone to clumping or forming lumps if not dispersed properly. This can lead to uneven hydration and inconsistent product performance. Coarser HPMC particles, conversely, disperse more easily without clumping but take longer to hydrate fully. They are often preferred in applications where a slower, more controlled dissolution is acceptable or even desired, such as in certain sustained-release formulations or dry-mix mortars. This is important because… the right particle size ensures efficient processing and consistent product quality.
The choice of particle size also affects the final texture and appearance of a product. For example, in pharmaceutical suspensions, a finer particle size might be chosen to ensure a smooth, uniform consistency and prevent sedimentation. In contrast, a coarser particle size might be used in a dry-mix construction product to improve its flowability and reduce dust during handling. Manufacturers often offer HPMC in various particle sizes, including standard, fine, and even ultra-fine grades, to meet diverse processing and application requirements. Selecting the appropriate particle size is a crucial step in optimizing HPMC performance.
Particle Size | Dissolution Rate | Dispersion Behavior | Typical Use Case |
---|---|---|---|
Fine | Fast | Prone to clumping | Instant mixes, quick hydration |
Coarse | Slow | Easy dispersion | Sustained release, dry-mix mortars |
7. What are the specific applications for different HPMC grades?
Different HPMC grades find specific applications across various industries due to their tailored properties. In the pharmaceutical industry, HPMC is a workhorse. It serves as a binder in tablets, ensuring their structural integrity. It also functions as a film-former for tablet coatings, protecting the active ingredients and facilitating swallowing. Crucially, HPMC is used as a matrix former in sustained-release formulations, controlling the rate at which a drug is released into the body. For example, a high-viscosity HPMC might be used to create a slow-release tablet for a chronic condition. In the food industry, HPMC acts as a thickener in sauces and dressings, a stabilizer in dairy products, and a gelling agent in baked goods. It improves texture and extends shelf life. Want to know the secret? HPMC helps maintain product consistency and appeal.
In the construction industry, HPMC is vital for improving the performance of cement-based materials. It enhances water retention in tile adhesives, preventing premature drying and improving bond strength. In renders and plasters, it improves workability and anti-sag properties. For self-leveling compounds, HPMC ensures a smooth, even surface. Personal care products also benefit from HPMC, where it functions as a thickener in shampoos and lotions, and a film-former in cosmetics. Each application leverages specific HPMC properties, from viscosity to thermal gelation, to achieve desired product characteristics and performance.
Industry | HPMC Application | Specific Function |
---|---|---|
Pharmaceutical | Tablets, coatings, sustained release | Binder, film-former, matrix former |
Food | Sauces, dairy, baked goods | Thickener, stabilizer, gelling agent |
Construction | Tile adhesives, renders, self-leveling compounds | Water retention, workability, anti-sag |
Personal Care | Shampoos, lotions, cosmetics | Thickener, film-former |
8. How do you select the correct HPMC grade for a project?
Selecting the correct HPMC grade involves a systematic approach, matching HPMC properties to specific application requirements. First, define the desired functional properties of your end product. Do you need thickening, binding, film-forming, or water retention? Consider the required viscosity range, dissolution rate, and thermal gelation properties. For instance, a pharmaceutical tablet requiring sustained release will need a high-viscosity HPMC with specific gelation characteristics. A paint formulation needing anti-sag properties will also require a high-viscosity grade. The bottom line? A clear understanding of your product’s needs guides the initial selection.
Next, consider regulatory compliance and industry standards. HPMC used in pharmaceuticals or food products must meet stringent purity and safety regulations. Always verify that the chosen grade complies with relevant pharmacopeias (e.g., USP, EP) or food additive regulations (e.g., E464). Finally, perform a cost-benefit analysis. While some specialized HPMC grades may offer superior performance, their higher cost might not be justified for all applications. Pilot trials and small-scale testing are crucial to validate the selected grade’s performance in your specific formulation and manufacturing process. This iterative process ensures both technical suitability and economic viability.
Selection Step | Key Considerations |
---|---|
Define Product Needs | Desired function (thickening, binding), viscosity, dissolution, gelation |
Regulatory Compliance | Pharmacopeias (USP, EP), food additive regulations (E464) |
Cost-Benefit Analysis | Performance vs. cost, economic viability |
Pilot Trials | Validate performance in specific formulation |
9. What are the quality control considerations for HPMC grades?
Quality control for HPMC grades is essential to ensure consistent product performance and safety. Purity and impurity profiles are paramount, especially for pharmaceutical and food applications. Manufacturers must verify that HPMC batches are free from contaminants and meet strict purity standards. This often involves testing for heavy metals, residual solvents, and microbial limits. Stability and shelf life are also critical considerations. HPMC should maintain its physical and chemical properties over its intended storage period. Proper storage conditions, such as temperature and humidity control, are necessary to preserve its quality. What does this mean for you? Consistent quality directly impacts your product’s reliability.
Batch consistency is another key aspect of quality control. Variations between batches can lead to inconsistencies in your final product, affecting performance and consumer acceptance. Manufacturers employ rigorous testing methods, including viscosity measurements, substitution analysis, and particle size distribution, to ensure each batch meets specifications. Certificates of Analysis (CoA) provide detailed information on a batch’s properties and confirm its compliance with quality standards. Regular audits of HPMC suppliers and in-house testing protocols are vital to maintain high quality. These measures help ensure that the HPMC you receive will perform as expected every time.
Quality Control Aspect | Importance | Testing Methods |
---|---|---|
Purity | Product safety, regulatory compliance | Heavy metals, residual solvents, microbial limits |
Stability | Shelf life, consistent performance | Accelerated aging tests, storage conditions |
Batch Consistency | Product reliability, uniform performance | Viscosity, substitution analysis, particle size |
10. What are the future trends and innovations in HPMC technology?
The future of HPMC technology focuses on sustainable production methods, new modification techniques, and emerging applications. There is a growing emphasis on developing more environmentally friendly manufacturing processes for HPMC, reducing energy consumption and waste. This includes exploring alternative raw materials and more efficient synthesis routes. Innovations in modification techniques aim to create HPMC derivatives with enhanced or novel properties. For example, researchers are developing HPMC with improved thermal stability, better film-forming capabilities, or specific functionalities for advanced drug delivery systems. These advancements promise to broaden HPMC’s utility even further. Here’s the deal… these innovations will drive new product development.
Emerging applications are also shaping the future of HPMC. In the biomedical field, HPMC is being explored for tissue engineering scaffolds and wound dressings due to its biocompatibility. In sustainable packaging, it is being investigated as a biodegradable film material. The demand for plant-based and sustainable ingredients continues to grow, positioning HPMC as a key component in various green initiatives. As industries seek more efficient, sustainable, and high-performing materials, HPMC technology will continue to evolve, offering new solutions for complex challenges. These trends highlight HPMC’s adaptability and its enduring relevance in a rapidly changing industrial landscape.
Future Trend | Description | Potential Impact |
---|---|---|
Sustainable Production | Eco-friendly manufacturing, alternative raw materials | Reduced environmental footprint, cost savings |
New Modifications | Enhanced thermal stability, specific functionalities | Advanced drug delivery, novel material properties |
Emerging Applications | Biomedical, sustainable packaging | New markets, expanded utility |
Conclusion
Understanding HPMC grades is vital for optimizing product performance and ensuring manufacturing success. We have covered HPMC fundamentals, detailed classification by viscosity, substitution, and particle size, and explored specific applications across pharmaceuticals, food, and construction. This knowledge empowers you to select the precise HPMC grade for your project, ensuring optimal functionality and compliance. The right HPMC choice leads to improved product quality and streamlined production processes. To gain a competitive edge and ensure your products meet the highest standards, consider partnering with Morton. We offer expert guidance and a comprehensive range of HPMC solutions tailored to your unique needs. Contact Morton today to discuss your specific HPMC requirements and elevate your product development.
FAQ
Q1: What is HPMC used for in pharmaceuticals?
HPMC is widely used in pharmaceuticals as a binder, film-former, disintegrant, and sustained-release agent in tablets and capsules. It also functions as a thickener and stabilizer in liquid formulations.
Q2: Can HPMC be used in food products?
Yes, HPMC is approved as a food additive (E464) and is used as a thickener, emulsifier, stabilizer, and gelling agent in various food products, including baked goods, dairy, and dressings.
Q3: How does HPMC affect cement-based materials?
HPMC improves the workability, water retention, and adhesion of cement-based materials like tile adhesives, renders, and self-leveling compounds. It also enhances their open time and anti-sag properties.
Q4: What is the difference between low and high viscosity HPMC?
Low viscosity HPMC is suitable for applications requiring thin films or quick dissolution, such as film coatings. High viscosity HPMC is used for sustained release, thickening, and water retention in applications like controlled-release tablets or cement mortars.
Q5: Is HPMC a natural or synthetic polymer?
HPMC is a semi-synthetic polymer derived from cellulose, a natural polymer found in plant cell walls. It undergoes chemical modification to enhance its properties for various industrial uses.