Are you looking for the right additive for your products? Low viscosity HPMC can make a big difference in your success. Many companies find it hard to pick and use this helpful polymer the right way. If you choose the wrong type or mix it poorly, your products might fail. You could waste money on a material that should help your products.
The good news? When you know how to use low viscosity HPMC the right way, it helps your products a lot. Tests show that companies who use the right HPMC make products 15% faster. Their products work much better too.
In this guide, we’ll show you what makes low viscosity HPMC special. We’ll explain how it works in many fields. We’ll also help you pick the best type for what you need.
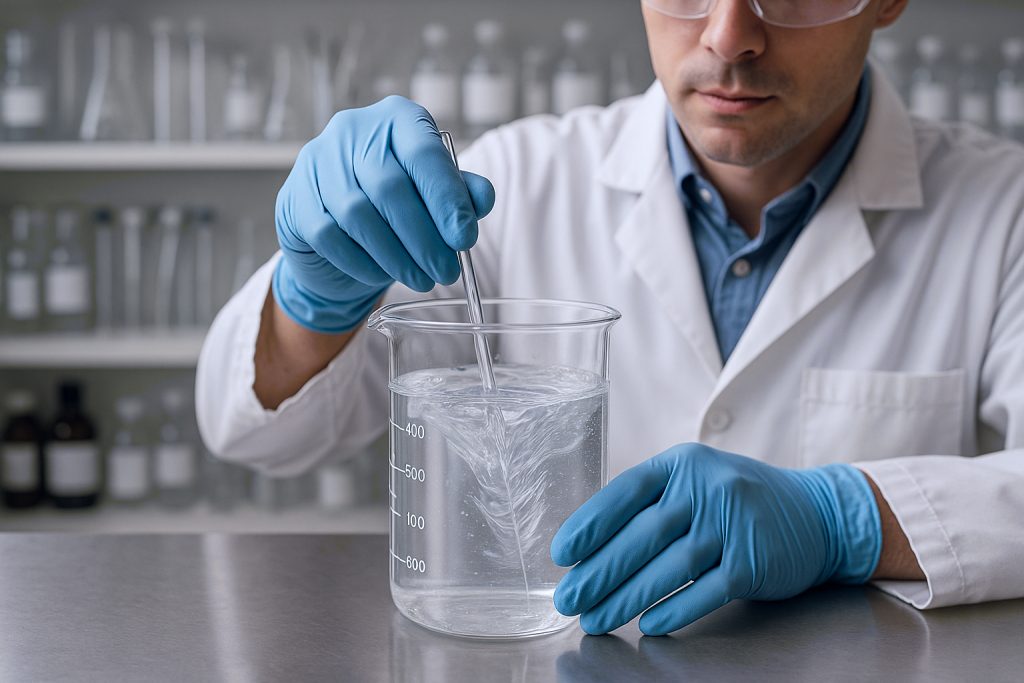
1. What Is Low Viscosity Hydroxypropyl Methylcellulose (HPMC)?
Low viscosity HPMC is a plant-based polymer. It comes from natural cellulose. When we say “low viscosity,” we mean it flows easily when mixed with water.
But what exactly makes it different? Low viscosity HPMC has shorter chains. This key feature changes how it acts in water. The shorter chains help it mix faster. They also make thinner mixtures compared to high viscosity HPMC.
The basic makeup of HPMC has a cellulose core. It has special groups added – hydroxypropyl and methyl groups. These extras make the polymer mix in cold water. They also give it useful traits for many products.
Low viscosity HPMC usually has flow ratings between 3 and 100 mPa·s. This is tested in a 2% mix at 20°C. This makes it great for uses where you don’t want much thickening. You still get other helpful traits.
Trait | Low Viscosity HPMC | High Viscosity HPMC |
---|---|---|
Flow Range | 3-100 mPa·s (2% mix) | 100-200,000 mPa·s (2% mix) |
Mixing Speed | Fast | Slower |
Gel Strength | Weaker, more bendy | Stronger, more stiff |
Typical Use Amount | 0.1-5% | 0.5-2% |
Film Thickness | Thinner | Thicker |
Low viscosity HPMC looks like a white to off-white powder. It has no smell or taste. It stays stable in a wide pH range (3-11). It doesn’t break down from enzymes. This makes it work well in many different product types.
Common types you can buy include HPMC E5, HPMC E15, and HPMC E50. The number roughly matches the flow rating in mPa·s of a 2% mix. Each type offers slightly different perks. They all keep the main good points of low viscosity HPMC.
The physical form of HPMC affects how it works in your products. Most sellers offer it as a fine powder. Some also make granules that mix more easily. The particle size can affect how fast it mixes. It also affects how well it spreads in your formula.
2. How Does Low Viscosity HPMC Work In Different Applications?
Low viscosity HPMC works in several key ways. These make it useful in many different products. When you know these methods, you can use this handy polymer better in your own products.
Want to know the science behind its success? When you add low viscosity HPMC to water, it goes through a special process. First, it forms a gel layer around each tiny bit. Then, as this gel slowly melts, the polymer spreads into the mix. The short chains in low viscosity types make this happen faster than with thicker types.
One of the most useful traits of low viscosity HPMC is how it forms films. When a mix with HPMC dries, the polymer chains line up. They create a smooth, even film. This film gives you several perks:
- Blocks air very well
- Has good strength even when thin
- Looks clear and shiny
- Keeps out oils and greases
Use | How It Works | Main Perk |
---|---|---|
Pill Coating | Forms smooth film around pill | Hides taste, keeps out water |
Building Glues | Bonds with wood-based stuff | Better sticking power, holds water |
Food Products | Creates gel when heated | Keeps food stable with better feel |
Skin Care | Makes shield on skin/hair | Delivers active parts, feels better |
Paints | Keeps color bits from sinking | Stops clumping, goes on more smoothly |
In heat-based uses, low viscosity HPMC shows unique traits. It mixes in cold water. But it forms a gel when heated above its gel point (about 65-80°C). This heat-based gelling makes it great for timed-release products.
Low viscosity HPMC stays stable in different pH levels. This is because it has no charge. Unlike many other polymers, it works well from pH 3 to 11. This makes it useful in products with different acid levels.
The binding power of low viscosity HPMC works through hydrogen bonds. The polymer chains form bonds with other stuff. This creates strong sticking even at low amounts. It makes it a good binder for many uses.
When used in mixes, low viscosity HPMC helps keep bits from sinking. It creates a light web in the liquid. This web holds bits in place. But it still lets the product flow when needed.
3. What Industries Use Low Viscosity HPMC And Why?
Low viscosity HPMC has found its way into many fields. It’s so handy that each field uses it for different reasons. Let’s look at how various areas gain from this polymer.
Did you know that HPMC is in products you use daily? In the drug field, low viscosity HPMC coats pills. It creates a shield that hides bad tastes. It controls water. It can be made for quick or slow release. For fast-melting coatings, types like HPMC E5 and E15 work best. They break down quickly.
The building field is one of the biggest users of low viscosity HPMC. It goes into cement products like tile glues, wall coatings, and floor mixes. The polymer helps keep water in the mix. It makes it easier to work with. It helps it stick to walls better. Tests show that mortars with HPMC hold 40-60% more water than those without it.
Field | Uses | Main Perks |
---|---|---|
Drug Making | Pill coating, binders, timed release | Taste hiding, melt control, stability |
Building | Mortars, tile glues, wall coats, joint fillers | Water holding, workability, sag stopping |
Food | Baked goods, sauces, dairy stand-ins | Texture change, stability, less fat needed |
Skin Care | Shampoos, lotions, creams, toothpaste | Film making, keeping stable, texture boost |
Paints | Water-based paints, primers | Flow control, stops settling, better use |
In food products, low viscosity HPMC works as a stabilizer and texture helper. It’s very useful in gluten-free baking. It helps trap air and give structure like gluten does. Food safety groups in the US and Europe have OK’d certain types of HPMC as food adds (E464). This shows it’s safe to eat.
The skin care field uses low viscosity HPMC in many products. You’ll find it in shampoos, lotions, and creams. Its film-making traits create a light, non-greasy feel on skin and hair. In toothpaste, it helps keep product form. It helps active parts work better.
Food Use | HPMC Job | User Perk |
---|---|---|
Gluten-free bread | Structure maker | Better texture and size |
Ice cream | Stops ice bits | Smoother feel, melts slower |
Sauces and dressings | Stabilizer | Stays mixed, feels better in mouth |
Plant-based meat stand-ins | Binding agent | Better texture, stays whole when cooked |
Fried foods | Film maker | Less oil soaked up, crispier texture |
The paint field gains from low viscosity HPMC’s ability to control flow. It doesn’t make paint too thick. It stops color bits from sinking. It allows good flow during painting. Water-based paints with HPMC splatter less. They cover walls better.
New uses for low viscosity HPMC keep coming up. In 3D printing, it helps control the flow traits of printing stuff. In farming, it’s used in seed coatings and as a soil helper. It breaks down and holds water well. The cloth field uses it in sizing agents and printing pastes. It forms good films on fibers without making cloth stiff.
4. What Are The Key Benefits Of Using Low Viscosity HPMC?
Low viscosity HPMC offers many perks. These help both your making process and your end products. These good points explain why so many fields choose to use it.
Here’s the real value offer: From a making standpoint, low viscosity HPMC works better than higher viscosity types. It works better than other polymers too. It mixes faster in water. This cuts mixing time and saves power. Factories report 30-50% shorter mixing times when switching from high to low viscosity types.
You also need less of it to get the same results. Low viscosity HPMC gets many perks at lower use levels than other stuff. For example, in building uses, you typically need only 0.2-0.5% amount. Other cellulose stuff needs 0.5-1.0% to get like water holding.
Perk Type | Specific Good Point | Measurable Impact |
---|---|---|
Making | Faster mixing | 30-50% cut in mixing time |
Making | Lower power use | 15-25% power savings in making |
Making | Less dust made | Safer for workers, less waste |
Money | Lower use levels | 20-40% cut in stuff costs |
Money | Longer shelf life | 6-12 months more product stability |
Cost savings is another big perk. The making gains plus lower usage amounts leads to direct stuff cost savings. Case studies from drug makers show 15-30% cost cuts. They changed to low viscosity HPMC. The product work stayed the same or got better.
End product gains vary by use. They include more even films in coatings. They include more exact timed release in drugs. They include better workability in building products. Food makers note better texture stability and mouth feel in products made with low viscosity HPMC.
From a green view, low viscosity HPMC offers several good points. It breaks down in nature. It comes from trees (wood pulp). Its good use means less stuff needed per use. Its non-toxic nature makes it safe for workers and end-users alike.
The shelf-life boost is another big perk. Products with low viscosity HPMC often show better stability during storage. For example, drug pills with HPMC coatings show better blocking of water and air. This makes shelf life 6-12 months longer in some cases.
5. How Do You Select The Right Low Viscosity HPMC Grade For Your Application?
Picking the best low viscosity HPMC type for your needs means looking at several key points. Making the right choice can greatly impact your product’s work and making gains.
Ready for some hands-on tips? The first step is to know what you need the HPMC to do in your product. Are you mainly looking for film making? Do you need binding? Are you looking for thickening or timed release? Each job may point to different best types within the low viscosity range.
Flow rate is the most clear factor. But it shouldn’t be the only one you think about. For film-making uses like pill coating, types in the 3-15 mPa·s range work best. HPMC E5 or E15 give the best mix of spray use traits and film quality. For binding uses, slightly higher flow rate types (15-50 mPa·s) often give better strength.
Use Type | Best Flow Rate Range | Suggested Types | Key Picking Points |
---|---|---|---|
Film Coating | 3-15 mPa·s | HPMC E5, E15 | Spray flow, film evenness |
Binding | 15-50 mPa·s | HPMC E15, E50 | Binding strength, melt rate |
Timed Release | 50-100 mPa·s | HPMC K100LV, E50 | Gel strength, wear rate |
Building | 15-50 mPa·s | HPMC E15, E50 | Water holding, workability |
Food Texturing | 25-100 mPa·s | HPMC F50, K100LV | Mouth feel, stability |
The side group pattern affects work. This means the methoxyl and hydroxypropoxyl content. E-type HPMC (higher methoxyl content) gives better oil mixing. It has lower gel temps. K-type (lower methoxyl, higher hydroxypropoxyl) offers better water mixing. It has higher gel temps.
Bit size spread impacts melt rate and mix quality. Finer types melt more quickly. But they may be more prone to lumping. Some sellers offer special made types. These have better mixing for hard uses.
Testing mix with your specific formula parts is key. HPMC works well with many parts. But mix with certain soaps, salts, or active parts can affect work. Simple lab tests can find issues early. Mix HPMC mixes with other formula parts to see how they act.
Common picking errors include focus only on price. You should think about total cost-in-use instead. Another error is missing how making states affect work. Some also fail to think about the whole product life. The cheapest type may need higher usage levels. It may cause making troubles. These problems kill any first savings.
6. What Are The Best Practices For Handling And Processing Low Viscosity HPMC?
Good handling and making of low viscosity HPMC can make a big change. It can mean smooth making instead of costly making problems. Using proven best ways helps you get the most from this handy polymer.
Let me share some pro tips: Storage states greatly impact HPMC quality over time. Store the stuff in its first sealed boxes. Keep it in a cool, dry place away from direct sun. HPMC soaks up water from the air. This can affect how it mixes and lead to clumping. The best storage states are temps below 30°C. Keep air water below 65%.
The right mix method is key for lump-free mixing into water-based systems. The most good method is the “hot/cold” method. Mix HPMC powder in hot water (above 80°C). At this temp, it won’t melt but wets evenly. Then cool the mix to allow full melting. This stops the making of a gel layer around bits. Such a layer can trap dry powder inside.
Storage Point | Best Way | Impact if Not Done |
---|---|---|
Temp | Below 30°C | Possible caking, shorter shelf life |
Air Water | Below 65% | Water soaking, lumping |
Box Type | First sealed or airtight | Dirt, water soaking |
Stacking | Max 3 pallets high | Physical pressing, caking |
Stock Turning | FIFO (First In, First Out) | Using older stuff with possible quality changes |
For dry mixing uses, think about using a special made mixable type. Or pre-mix HPMC with other dry parts before adding water. This helps split the bits. It cuts the risk of clumping. Adding HPMC to the mixer first, then other dry parts, then water, often gives the best results.
Making gear pick depends on your specific use. High-shear mixers work well for mixing HPMC in liquid systems. Ribbon mixers work well for dry mixes. For non-stop making, in-line mixing systems with good powder adding can be highly good.
Quality checks should include flow test of made mixes. This gives a good sign of proper melting and type match. For film uses, simple draw tests can check film making traits. In building uses, water holding tests help confirm work.
Making Issue | Cause | Fix |
---|---|---|
Lumping | Too fast adding, not enough stirring | Slower adding to swirl, more stirring |
Slow Melting | Cold water, high amount, big bits | Use hot/cold method, cut amount at first |
Air Adding | Too fast mixing speed, wrong mixer design | Cut speed, use different stirrer design |
Uneven Work | Changing raw stuff, uneven process | Seller check, process standard |
Foam Making | High-speed mixing, certain formula parts | Add anti-foam, change mixing points |
Common making issues include lumping during mixing. Uneven wetting can be a problem. Air adding is another issue. To stop lumping, add HPMC powder slowly to the swirl of a well-stirred liquid. For more even wetting, ensure enough mixing time after adding. To cut air bubbles, change mixer speed. Think about using vacuum mixing for touchy uses.
For spray uses like pill coating, proper mix making is key. Fully wet the HPMC before adding other parts. Strain the mix to remove any non-melted bits. Keep right mix temp during the process. This ensures even flow.
Conclusion
Low viscosity HPMC proves to be a handy and useful part across many fields. It offers a unique mix of work perks with making gains. In this guide, we’ve looked at its basic traits. We’ve checked its working ways. We’ve seen its hands-on uses. These make it a key part in many good mixes. By knowing how to pick the right type and using best handling ways, you can use the full power of this polymer. You can make your products work better while cutting costs. The facts show that good use of low viscosity HPMC can save up to 30% in costs. It can greatly boost end-product quality. For pro help on picking the perfect HPMC type for your specific use, call Morton’s special polymer team today. Our team work ensures you’ll get the most gain from this handy stuff in your unique making world.
FAQ
Q1: How does low viscosity HPMC differ from other cellulose derivatives?
Low viscosity HPMC differs from other cellulose stuff mainly in how it mixes and works. Unlike methylcellulose, it mixes in cold water and forms a gel when heated. Compared to CMC, HPMC has no charge. It stays stable across a wider pH range. It handles oils better than HEC. It still forms good films. The low viscosity types offer these perks without making the mix too thick. This makes them perfect for uses where other traits matter more than thickness.
Q2: Can low viscosity HPMC be used in combination with other polymers?
Yes, low viscosity HPMC works well with many other polymers. Together they create better effects. Common mixes include HPMC with PVA for stronger films in coating uses. It works with xanthan gum for better mix stability. It joins with MCC for timed release drug mixes. When mixed with ionic polymers like carbomers or sodium alginate, the no-charge nature of HPMC helps keep stability across pH changes. For building uses, mixes with re-mixable polymer powders boost flex and sticking.
Q3: What are the regulatory considerations for using low viscosity HPMC in different regions?
Rules status varies by use and region. For food uses, HPMC is OK’d as E464 in Europe. It is GRAS in the US under FDA rules 21 CFR 172.874. Drug types meet various standards. These include USP, Ph.Eur., and JP books. For building products, HPMC is not often ruled on its own. It may fall under wider chemical stock rules. When sending products with HPMC out of the country, check rules match with target country rules. These include China’s GB standards or Japan’s JHOSPA needs.
Q4: How stable is low viscosity HPMC in different environmental conditions?
Low viscosity HPMC shows great stability across many states. In mix, it keeps steady work from pH 3-11. This makes it good for acid and base mixes. It fights enzyme break down better than natural gums. Temp stability in dry form is great up to about 130°C. Long time in high temps can cause slow break down. In mix, it forms a gel around 65-80°C. This depends on the specific type. Freeze-thaw stability is mostly good. Many cycles may affect mix traits.
Q5: What innovations are happening in low viscosity HPMC manufacturing?
New ideas in low viscosity HPMC making focus on better work and green gains. New surface-fixed types mix better without lumping. This fixes a common making challenge. Some makers have made types with changed side group patterns. These give more bendy films or faster melting. Making steps are getting more green. They use less solvent and better power use. Special types for 3D printing uses show a new area of growth. There’s also more care in getting cellulose from farm waste rather than wood pulp. This helps green goals.